热镀锌工艺助镀剂中铁含量分析及除铁工艺对比
热镀锌的助镀液中除铁方法

热镀锌的助镀液中除铁方法(摘自热镀锌的节锌技术)除铁的重要性经常测定助镀液中Fe2+离子的含量并加以除去,控制在l g/L以内(国外控制在0.5 g/L以下)。
因为生成锌铁合金的因素是一份铁和25份锌。
这就是说生成锌铁合金所造成锌的消耗是大量的,因此除铁就显得格外重要。
经常分析助镀液中的Zn、NH4、Fe2+的含量并调整。
除铁技术除铁常用的方法有两种:一是将助镀液吸入除铁处理系统,通过加H2O2,将Fe2+氧化为Fe3+后再加入NH3·H2O中和到pH>5,然后由板框压滤机,滤清液回到助镀液槽中,滤饼集中存放处理。
这样的系统有搅拌器槽、双氧水槽、氨水槽和压滤机等设施组成。
另一种也可以定期在空槽中进行除铁作业。
通过分析铁的含量后,根据铁的含量多少加入H2O2和NH3·H20进行除铁作业。
如果暂时没有分析手段时,可首先取出少量助镀液在不断搅拌下加入选择量的H2O2 (30%),用NH3·H2O调节pH 为5以上,进行沉淀后将上清液再加入H2O2,如不发生浑浊现象则铁基本除完,然后计算H202加入助镀液中的数量。
一般情况下,H202(30%)的加入量为l2kg 左右可处理lT助镀液。
有时候一次处理完后分析或作试验时仍然有铁存在,要根据铁的多少,再次实施除铁处理,直至达到除铁效果Fe<lg/L。
如果铁的含量能够控制在0·5g/L时除铁效果将达到最佳状态。
NH2·H20的加入主要是靠测量助镀液的pH值而定量,如果处理前助镀液的pH值己超过5,那就可以不加NH3·H2O。
另外中和后一定要充分沉淀,使固液彻底分离,然后将上清液滤入助镀液槽中,并调节pH值4~5。
这项技术可使产生锌碴、锌灰的量减少,可达到平均节锌0·8%左右,对年产量大的热浸锌单位具有非凡的节锌意义。
除铁工艺流程:助镀液+氧化(30%H2O2)+中和(NH3·H2O)→静止→过滤→调节pH值→再生后循环使用。
钢铁工艺材料成份对热镀锌高强钢锌层影响

【钢铁工艺】材料成份对热镀锌高强钢锌层影响高强钢热镀锌产品的生产中,经常出现锌层附着力差的问题。
为解决这一问题,尤其在钢卷的头尾部位表现特别明显。
某机组在退火炉段配置了预氧化设备。
下面我们就预氧化设备的使用来给大家介绍一下预氧化工艺对热镀锌高强钢锌层附着力的影响:锌层脱落的材料类型和缺陷形貌折弯时发生镀锌层脱落的1OOO和800MPa级高强钢板如图1所示。
图1表明,钢板经不同程度折弯变形后锌层几乎完全脱落,1000MPa级钢板不仅弯曲变形的部位镀锌层脱落,相邻未变形区也发生了锌层脱落。
800MPa级钢板锌层脱落后的表面较光滑,而且仅弯曲变形区发生镀锌层脱落。
图1锌层脱落的IOoO(a)和800MPa(b破钢板采扫描光学显微镜/电子显微镜和能谱仪对镀锌层脱落的钢板表面和截面形貌及成分进行检测分析。
首先来看IOOOMpa级别高强钢的缺陷分析。
IOOOMPa 级钢板1)镀锌层脱落区的表面形貌和成分采用导电胶将锌层脱落区锌层剥离,检验钢板的表面形貌和成分。
图2(a)为钢板锌层脱落区的表面微观形貌,表面光滑;图2(b)为背散射电子图,钢板镀锌层脱落区的表面有疏松。
能谱分析表明,钢板镀锌层脱落区的表面除含有少量Mn 、A1外,还含有较多的Fe 和少量的O,说明该区域除形成Fe2AI5抑制层外还形成了还原铁层。
图2钢板镀锌层脱落区表面的二次电子图(a)、背散射电子图(b)和能谱分析(C,:々钢变工业技才 2)镀锌层脱落区的截面形貌钢板镀锌层脱落区的截面形貌如图3所示。
图3表明,钢板镀锌层脱落区的上、下d) (a)能HzkCV表面均有还原铁层,使镀层与基体明显分离,这就是钢板镀锌层脱落的原因。
图3钢板镀锌层脱落区域截面的上(a)和下(b)部的电子背;方豺窗工3)镀锌层脱落区表面抑制层形貌热浸镀锌过程中,钢板与锌液中的A1首先形成均匀致密的Fe2AI5抑制层,这是确保热镀锌钢板镀层不脱落的关键。
抑制层越均匀致密,镀锌层与钢板的结合力越大,越不易脱落。
PAM对热镀锌助镀液中铁离子去除效果研究

PAM对热镀锌助镀液中铁离子去除效果研究于梦琦;党康飞;李顺义【摘要】热镀锌助镀液中铁离子含量过高会严重影响镀层质量.本文采用化学沉淀法处理热镀锌助镀液原水中过量的铁离子.采用双氧水氧化法氧化水样中的Fe2+离子,调节pH到4.5 ~5.0,使铁离子生成Fe(OH)3沉淀,分别加入不同类型的聚丙烯酰胺(PAM)絮凝.结果表明:投加过氧化氢15 mL/L时对水样中的Fe2+离子氧化效果最好,离子度为40的阳离子型PAM在浓度为0.06 g/L时对氢氧化铁的絮凝效果最好,絮体粒径为67.3 μm,铁离子去除效率为95.4%.【期刊名称】《广州化工》【年(卷),期】2018(046)019【总页数】3页(P78-80)【关键词】热镀锌;亚铁离子;过氧化氢氧化法;PAM【作者】于梦琦;党康飞;李顺义【作者单位】郑州大学化工与能源学院,河南郑州450001;郑州大学化工与能源学院,河南郑州450001;郑州大学化工与能源学院,河南郑州450001【正文语种】中文【中图分类】TQ电镀产业的生产是利用化学法或电化学法,在金属或其他材料的表面镀上金属[1]。
助镀液中的亚铁离子对镀锌工艺有消极影响,当助镀液中Fe2+含量过高,会使锌镀层发黑,镀液的分散能力下降,影响镀层质量,严重时使镀锌助镀液完全失效[2-3]。
研究表明,只有当铁离子的含量稳定维持在2000 mg/L以下时,才能保证镀锌取得较好的效果。
为了提高镀锌质量,实现最大限度的节锌,需要及时去除助镀液中的铁离子[4]。
目前,对助镀液中亚铁离子的去除方法有很多,主要有化学沉淀法、离子交换法、吸附法、电渗析、微电解法等方法[5]。
其中,微电解法、离子交换法等新型方法由于成本较高、操作时间长、设备复杂以及选择性低等缺点限制了这些方法的推广应用[6]。
化学沉淀法试剂来源广,成本低,金属离子去除率高,在实际操作中被广泛应用,但化学沉淀法产生的氢氧化铁沉淀量大,沉淀速度慢,不易从沉淀池中分离,沉淀时间过长会严重干扰后续镀锌,因此沉淀过程中需投加絮凝剂使氢氧化铁沉淀快速从助镀液中分离。
热镀锌的助镀理论及相关工序生产注意事项 唐山鑫德 2011

溶剂助镀剂是热浸镀前处理中一道重要处理工序,它不仅可以弥补前面几道工序可能存在的不足,还可以进一步活化钢铁表面,提高镀锌质量。
这是其他钢铁防腐工艺中所没有的。
它不仅直接影响镀层质量,还对锌耗,成本有很大影响。
如不采用溶剂助镀,会容易产生漏镀,而且会产生较多的锌渣,造成锌耗增加,影响镀锌质量。
现在最常用的采用氯化锌和氯化铵混合溶液作为溶剂来助镀。
所谓助镀就是将酸洗后的制件再浸入一定成分的氯化锌铵助镀液中,提出后在制件表面形成一层薄的氯化锌铵盐膜的过程。
一.助镀的作用机理:1助镀的作用㈠对钢铁表面起到清洁的作用,去除酸洗清洗后残留在制件表面的铁盐或氧化物,使钢铁件在进入锌浴时具有更大的表面活性。
㈡在制件表面沉积上一层盐膜,可防止制件从助镀池到进入锌锅这一段时间内在空气中锈蚀。
㈢净化制件使浸入液体锌时能与液体锌快速浸润并反应。
2.制件表面覆盖的氯化锌铵盐膜的活化作用㈠低于200oC时,在制件表面会形成一种复合盐酸,这种强酸保证了在干燥过程中制件表面无法形成氧化膜而保持活化状态。
㈡在200oC以上时,制件表面的助镀液盐膜中的NH4CL会在较高温度下分解成NH3和HCL,此时HCL对钢基体的侵蚀占了主导,使钢基体表面不能形成氧化物,保持钢基体的活化状态。
故在热浸镀锌时正确使用含有NH4CL的助镀剂是很重要的。
二.助镀剂的成分范围及工艺参数对于助镀液,除了对其质量浓度需要控制外,氯化铵和氯化锌的比例,溶液中的二价铁盐含量,PH值,温度以及杂质含量等因素均会对助镀效果产生较大效果。
因此助镀液的成分和工艺参数是衡量其质量和效果的重要因素。
三.助镀剂成份及工艺参数的影响1.助镀剂质量浓度。
助镀液质量浓度的高低对助镀效果影响很大。
当助镀液质量浓度过低(低于80g/L)时,镀件浸锌时容易产生“漏镀”;当助镀液质量浓度偏低(80-150g/L)时,由于制件表面附着的盐膜量少,不能有效活化制件表面,难以获得平滑均匀的镀层;当助镀液质量浓度偏高(300-500g/L)时,由于制件表面盐膜过厚,不易干透,在浸锌时将引起锌的飞溅,产生更多的锌灰,更浓的烟尘,以及更厚的镀层;当助镀液质量浓度过高(超过500g/L)时,制件表面形成的盐膜层将分成内外两层,外层薄而干,内层潮湿且呈糊状。
湿法炼锌过程中除铁工艺的进展报告
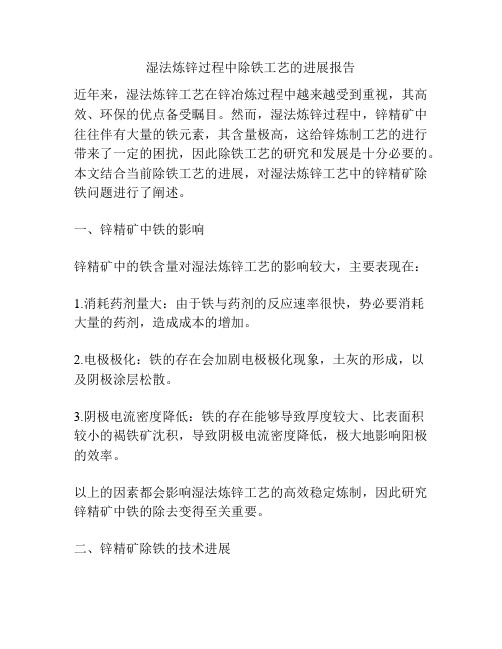
湿法炼锌过程中除铁工艺的进展报告近年来,湿法炼锌工艺在锌冶炼过程中越来越受到重视,其高效、环保的优点备受瞩目。
然而,湿法炼锌过程中,锌精矿中往往伴有大量的铁元素,其含量极高,这给锌炼制工艺的进行带来了一定的困扰,因此除铁工艺的研究和发展是十分必要的。
本文结合当前除铁工艺的进展,对湿法炼锌工艺中的锌精矿除铁问题进行了阐述。
一、锌精矿中铁的影响锌精矿中的铁含量对湿法炼锌工艺的影响较大,主要表现在:1.消耗药剂量大:由于铁与药剂的反应速率很快,势必要消耗大量的药剂,造成成本的增加。
2.电极极化:铁的存在会加剧电极极化现象,土灰的形成,以及阴极涂层松散。
3.阴极电流密度降低:铁的存在能够导致厚度较大、比表面积较小的褐铁矿沈积,导致阴极电流密度降低,极大地影响阳极的效率。
以上的因素都会影响湿法炼锌工艺的高效稳定炼制,因此研究锌精矿中铁的除去变得至关重要。
二、锌精矿除铁的技术进展锌炼制过程中,锌精矿除铁的技术虽然较为成熟,但是目前仍然面临一些技术难题,如精度不够高,药剂耗用等问题。
当前,锌精矿除铁技术主要有以下几种:1.浮选法:针对铁含量较高的锌矿石,锌矿石浮选中磨矿时顺便将铁矿物中的铁和锌分离,但此方法没有办法将铁从已经浸出成为锌精矿中除去。
2.磁选法:常温常压下利用磁性差异将铁矿石中的铁和锌分离,但在自然条件下除铁效果不及磁性强的高温、高压除铁法。
3.高温、高压除铁法:该方法是通过高温、高压反应使得铁矿物中的铁和锌分离,且是目前比较有效的一种除铁方法。
四、结论综上所述,随着工业技术的不断提高,湿法炼锌工艺在锌炼制中的占有率逐渐提高,但锌炼制过程中锌精矿中铁的影响和铁的除去问题一直是制约炼锌技艺的关键技术难点。
当前的技术手段虽然较为成熟,但还存在精度不够高、药剂耗用等技术问题,为此,今后的技术改进和研发将继续推进,以逐步实现高效稳定的湿法炼锌工艺,为锌炼制行业的发展注入新鲜的活力。
湿法炼锌工艺中除铁工艺是锌炼制制约的重要因素之一,以下是相关数据的分析。
助镀液铁离子检验

助镀液中铁离子含量检测
取1ml的助镀液,加入3ml的30%的过氧化氢(H2O2)再加入10ml水,加热至沸,冷却后加10ml(1+1)的氨水,过滤,并用10ml的(1+1)氨水洗涤沉淀,弃去滤液,把带有沉淀的漏斗置于一干净的250ml锥形瓶上,用10ml热的(1+1)盐酸洗涤于锥形瓶中,加热至沸。
加入6滴1g/L的甲基橙。
趁热边摇边滴加SnCl2溶液还原Fe3+至溶液变为粉红色,停止加SnCl2溶液,再摇几下至粉色褪去。
然后加入50ml水,15ml硫磷混酸(15+15+75),2-4滴二苯胺磺酸钠(5g/L),立即用K2Cr2O7标准溶液滴定至紫红色为终点。
c(铁离子)=C*V*55.85/a (g/L)
C---K2Cr2O7标准溶液的浓度mol/L。
V---消耗K2Cr2O7标准溶液的体积ml。
a---取样量ml。
热镀锌工艺化验方法
热镀锌工艺化验方法1、实验目的:测定助镀剂中氯化锌的含量2、实验方法:用EDTA(乙二胺四乙酸二钠盐)标准溶液进行滴定,根据滴定时消耗EDTA标准溶液体积可求出氯化锌的含量。
3、实验仪器:容量瓶、移液管、三角瓶、碱式滴定管、洗耳球、洗瓶4、实验试剂:EDTA标准溶液0.05mol/L、NH3--NH4CL缓冲溶液(PH=10)、蒸馏水、铬黑T指示剂0.5%5、实验步骤:5.1、从助镀剂槽中取样,用5mL移液管吸取试液5mL,置于100mL容量瓶中;5.2、用水稀释至规定的刻度后摇匀;5.3、自100mL容量瓶中,吸取稀释液5mL于三角瓶中加水50mL。
5.4、再加缓冲溶液10mL,再加铬黑T指示剂2-3滴。
5.4、用0.05mol/L的EDTA标准溶液滴至纯蓝色为终点。
5.5、准确读数。
计算公式:ZnCl2 (g/L). = C*V1/V2×136.38其中:C—用于滴定的标准EDTA溶液的浓度mol/L;V1—实际滴定中消耗标准EDTA溶液的体积,mL;136.38——氯化锌的摩尔质量;V2—稀释液的实际体积,mL。
1、实验题目:测定助镀剂中氯化铵的含量2、实验方法:用NaOH标准溶液进行滴定,根据滴定时消耗的NaOH 标准溶液体积可求出氯化铵含量。
3、实验仪器:移液管、三角瓶、碱式滴定管、酸度计、磁力搅拌器、容量瓶、洗耳球、洗瓶4、实验试剂:NaOH标准溶液0.1mol/L 甲醛、甲基红指示剂0.2% 蒸馏水5实验步骤:5.1、从助镀锌剂槽中取样;5.2、用移液管吸取试液5mL置于100mL容量瓶中,用水稀释刻度摇匀。
5.3、自100mL容量瓶中吸取稀释液5mL于三角瓶中,加水50mL。
加甲醛溶液20mL,再加甲基红指示剂2-3滴。
5.4、打开酸度计,将复合电极插入被测试液中。
同时开启磁力搅拌器,然后用NaOH标准溶液进行滴定,酸度计读数为6.2时,即为终点。
5.5准确读数。
计算公式: NH4CL(g/L)= 4cv×53.5其中:C—用于滴定的标准NaOH溶液的浓度,mol/L;V—实际滴定中消耗标准NaOH的体积,mL;53.5—氯化铵的摩尔质量。
热镀锌钢管助镀剂的成分分析及影响
热镀锌钢管助镀剂的成分分析及影响作者:陈国强张红田来源:《商品与质量·建筑与发展》2014年第05期【摘要】热镀锌层质量及热镀锌过程中的锌耗成本与热镀锌的助镀工艺密切相关,通过对热镀锌助镀工艺的研究,阐述了热镀锌助镀作用机理,给出了钢铁制件热镀锌时助镀液的有效成分范围及工艺参数为氯化铵和氯化锌的总质量浓度、铵锌比、PH值、温度。
并分析了助镀液浓度、成分配比、铁盐含量、除铁方法、PH值和温度等因素对热镀锌的影响。
结果表明,要获得良好的镀锌质量及较低的生产成本,必须对热镀锌助镀液成分及工艺条件进行严格控制。
【关键词】热镀锌;钢管;助镀剂;成分;除铁【Abstract】 The quality of hot dip galvanized coating and the cost of zinc consumption during the hot galvanizing, are closely connected with the galvanizing fluxing technology. Based on the research about the galvanizing fluxing technology, the present paper has explained the mechanism of hot galvanizing fluxing, indicted the effective composition and technological parameters of the steelwork galvanizing, which including the total mass concentration, An/Zn ratio, pH,temperature of ammonium chloride and zinc chloride. Moreover, this paper also has analyzed the effect on the hot galvanizing by concentration of flux, composition proportion, molysite content,method of removing molysite, pH and temperature, etc. The research results show that, we must strictly controll the composition of flux and technology conditio.,if we expect to obtain the good quality as well as the low output cost of hot dip galvanized coating.【Key Words】 hot-dip galvanizing;Steel pipe;plating auxiliary;composition;Removing ferric ion1 概述熱镀锌钢管生产工艺中助镀剂的应用,在浸锌前处理工序中是非常重要的工序,目前,国内外研究和应用的是溶剂助镀法、盐酸助镀、氧化还原法和热浸渗铝法。
热镀锌工艺助镀剂中除铁工艺对比
热镀锌助镀剂除铁工艺助镀剂除铁主要是除去助镀剂中的二价铁离子。
将二价铁离子氧化成三价铁离子,三价铁离子被水解生成氢氧化铁。
氢氧化铁不溶于水,经沉淀在助镀剂中被分离。
除铁的方法有很多。
有用压缩空气氧化,有用臭氧氧化,有用化学氧化剂氧化等。
在此只介绍化学法氧化除铁的原理和方法。
目前国内大多采用氧化提纯法除铁,其工艺为:调整PH值——氧化除铁——过滤(分离)。
1、调整PH值:助镀剂中的铁离子一般以Fe2+即氯化亚铁状态存在,Fe2+在PH值很大(PH=8.5)时,或锌含量不大而Fe2+很大时才能水解析出沉淀。
因此必须将Fe2+经氧化成为Fe3+,Fe3+在PH=1.7时即可发生水解,形成氢氧化锌沉淀后很容易被除去。
锌水解时PH值为5.0—5.5,因此在除铁工艺中为便于控制PH值,一般将PH值调整在3—4。
若PH值小于3:KClO3+2HCl=KCl+O2↑+H2O+Cl2↑4KMnO4+4HCl=4KCl+4MnO2+3O2↑+2H2O2H2O2=2H2O+O2↑(酸性条件)Ca(ClO)2+4HCl=2Cl2↑+ CaCl2+2H2O这时会使氧化剂与酸反应会造成氧化剂的消耗,可以用氨水、锌、氧化锌调整PH值。
NH4OH+HCl=H2O+NH4ClZn+2HCl=ZnCl2+H2↑ZnO+2HCl=ZnCl2+H2O若PH值大于4:ZnCl2+2H2O=Zn(OH)2↓+2HCl这时会使氯化锌水解生成氢氧化锌沉淀,造成氯化锌浪费,此时可用盐酸调整。
在测试PH值时可采用如下方法:取一份过滤好的助镀剂与同体积的水在试管中混合后摇匀,若产生白色的絮状混合物即为合格;若产生白色的胶状体则说明PH值超过4,需加酸调整;若加水后溶液仍然澄清说明酸度大,需加氨水或锌粉或氧化锌调整。
2、氧化除铁处理在助镀剂中加入氧化剂,将二价铁氧化成三价铁,使之水解沉淀分离。
化学法除铁通常是用高锰酸钾、氯酸钾、氯酸钠、次氯酸钠、次氯酸钙、过氧化氢等作为氧化剂。
助镀剂铁离子浓度对镀锌锌耗的影响研究
第9期 收稿日期:2020-03-03作者简介:陆梅鹏(1993—),江苏宝应人,大学本科学历,助理工程师,职务为江苏华电铁塔制造有限公司镀锌车间技术员。
助镀剂铁离子浓度对镀锌锌耗的影响研究陆梅鹏,朱小明,王 亮(江苏华电铁塔制造有限公司,江苏徐州 221131)摘要:热浸镀锌是输电铁塔行业必不可少的生产工序,镀锌工序中仅锌锭成本占整个铁塔生产成本10%以上。
从以往生产数据分析,按当前锌价行情18000元/t计算,以3.9%锌耗为基准,锌耗每降低0.1%,每吨黑件镀锌可节约成本为18元。
而助镀剂铁离子含量对于镀锌锌渣的产生具有重大影响,所以降低助镀剂中铁离子含量具有重大意义,能够极大的降低整体镀锌锌耗,是十分可观的利润提升空间。
本研究将围绕镀锌助镀剂中铁离子含量对锌耗的影响为切入点,展开数据研究。
关键词:助镀剂;氯化亚铁离子;锌耗中图分类号:TQ153.1+5 文献标识码:A 文章编号:1008-021X(2020)09-0029-02 工业中应用最广泛的钢铁材料,在大气、海水、土壤及建筑材料等环境中使用时,均会发生不同程度的腐蚀。
据统计,全世界每年因腐蚀而损失的钢铁材料大约可占到其总产量的1/3。
为了保证钢铁制品的正常使用,延长其使用寿命,钢铁的防腐蚀保护技术一直受到人们的普遍重视。
热浸镀锌是延缓钢铁材料环境腐蚀的最有效手段之一,它是将表面经清洗、活化后的钢铁制品浸于熔融的锌液中,通过铁锌之间的反应和扩散,在钢铁制品表面镀覆附着性良好的锌合金镀层。
与其他金属防护方法相比,热浸镀锌工艺在镀层的物理屏障与电化学保护相结合的保护特性上,镀层与基体的结合强度上、镀层的致密性、耐久性、免维护性和经济性及其对制品形状与尺寸的适应性上,具有无可比拟的优势。
目前热浸镀锌产品主要有钢板、钢带、钢丝、钢管等,其中热浸镀锌钢板所占比例最大。
长期以来,热浸镀锌工艺因其低廉的施镀成本,优良的保护特性和漂亮的外观而备受人们的青睐,广泛应用于汽车、建筑、家电、化工、机械、石油、冶金、轻工、交通、电力、航空和海洋工程等领域。
- 1、下载文档前请自行甄别文档内容的完整性,平台不提供额外的编辑、内容补充、找答案等附加服务。
- 2、"仅部分预览"的文档,不可在线预览部分如存在完整性等问题,可反馈申请退款(可完整预览的文档不适用该条件!)。
- 3、如文档侵犯您的权益,请联系客服反馈,我们会尽快为您处理(人工客服工作时间:9:00-18:30)。
热镀锌工艺助镀剂中铁含量分析及
除铁工艺对比
近几年,由于热浸镀行业迅猛发展,原来酸洗之后不浸助镀剂直接镀锌的传统工艺逐渐已被摒弃。
这样已经使用助镀剂的企业越来越多的开始重视助镀剂的除铁工艺。
由于酸洗后铁盐被带到锌锅,1公斤铁可产生25公斤锌渣,不但造成锌耗增加、镀锌成本增高,而且还会使锌液中氧化物和其他杂质增加,这样会造成锌液老化、锌液黏度增加,使热浸镀锌质量下降。
原来干法镀锌工艺规程要求,助镀剂中铁盐含量不大于30g/l,现在很多企业控制铁盐含量不大于5g/l,甚至有些企业在助镀工序采用连续除铁,连续过滤的方法控制铁盐含量。
然而现在还有的企业不了解助镀剂除铁的有关原理,认为助镀剂直接用过滤泵或压滤机过滤就是除铁了。
还有的企业随便加一些氨水和双氧水经过滤后就认为是除铁了,实际根本达不到除铁的目的。
2、助镀剂的种类。
目前国热浸镀锌企业采用多种助镀剂配比方式,但广泛使用的助镀剂是氯化锌和氯化铵混合而成的复盐。
基本都是根据企业的实际使用情况进行配比,有的是纯氯化铵溶液,有的是氯化锌和氯化铵混合而成的复合盐。
复合盐有高氯化锌低氯化铵的复合盐,也有低氯化锌高氯化铵的复合盐。
还有些企业为了使用助镀添加剂而特殊制定氯化锌与氯化铵的复合盐的比例,它的比例是氯化锌80-100g/l,氯化铵120-150g/l,这是由于氯化锌吸水性决定的。
如果在高氯化锌配比的
溶剂中加入助镀添加剂,而且预镀件存放时间较长时,氯化锌吸水会使助镀添加剂起不到防爆作用。
因此说,氯化铵氯化锌含量高低主要是取决于预镀件存放时间长短和有无烘干来决定的。
氯化锌含量越高形成的助镀膜越厚,储存时间越长,但吸水性越强。
氯化铵含量越高,崩锌虽然减小,但氯化铵分解后烟气增大。
现在大部分企业都采用助镀剂加热的方式,加入助镀添加剂后预镀件可短时间存放,在生产中浸助镀剂后马上进行镀锌作业,取消了干燥工序。
3、助镀剂除铁工艺
助镀剂除铁主要是除去助镀剂中的二价铁离子。
将二价铁离子氧化成三价铁离子,三价铁离子被水解生成氢氧化铁。
氢氧化铁不溶于水,经沉淀在助镀剂中被分离。
除铁的方法有很多。
有用压缩空气氧化,有用臭氧氧化,有用化学氧化剂氧化等。
在此只介绍化学法氧化除铁的原理和方法。
目前国大多采用氧化提纯法除铁,其工艺为:调整PH值——氧化除铁——过滤(分离)。
3.1、调整PH值:
助镀剂中的铁离子一般以Fe2+即氯化亚铁状态存在,Fe2+在PH值很大(PH=8.5)时,或锌含量不大而Fe2+很大时才能水解析出沉淀。
因此必须将Fe2+经氧化成为Fe3+,Fe3+在PH=1.7时即可发生水解,形成氢氧化锌沉淀后很容易被除去。
锌水解时PH值为5.0—5.5,因此在除铁工艺中为便于控制PH值,一般将PH值调整在3—4。
●若PH值小于3:
KClO3+2HCl=KCl+O2↑+H2O+Cl2↑
4KMnO4+4HCl=4KCl+4MnO2+3O2↑+2H2O
2H2O2=2H2O+O2↑(酸性条件)
Ca(ClO)2+4HCl=2Cl2↑+ CaCl2+2H2O
这时会使氧化剂与酸反应会造成氧化剂的消耗,可以用氨水、锌、氧化锌调整PH值。
NH4OH+HCl=H2O+NH4Cl
Zn+2HCl=ZnCl2+H2↑
ZnO+2HCl=ZnCl2+H2O
●若PH值大于4:
ZnCl2+2H2O=Zn(OH)2↓+2HCl
这时会使氯化锌水解生成氢氧化锌沉淀,造成氯化锌浪费,此时可用盐酸调整。
在测试PH值时可采用如下方法:取一份过滤好的助镀剂与同体积的水在试管中混合后摇匀,若产生白色的絮状混合物即为合格;若产生白色的胶状体则说明PH值超过4,需加酸调整;若加水后溶液仍然澄清说明酸度大,需加氨水或锌粉或氧化锌调整。
3.2、氧化除铁处理
在助镀剂中加入氧化剂,将二价铁氧化成三价铁,使之水解沉淀分离。
化学法除铁通常是用高锰酸钾、氯酸钾、氯酸钠、次氯酸钠、次氯酸钙、过氧化氢等作为氧化剂。
高锰酸钾除铁的反应原理:
5FeCl2+KMnO4+8HCl=MnCl2+5FeCl3+4H2O+KCl
FeCl3+3H2O=Fe(OH)3↓+3HCl
氯酸钾(钠)除铁的反应原理:
6FeCl2+KClO3+6HCl=6FeCl3+KCl+3H2O
FeCl3+3H2O=Fe(OH)3↓+3HCl
次氯酸钙除铁的反应原理:
4FeCl2+Ca(ClO)2+4HCl=4FeCl3+CaCl2+2H2O
FeCl3+3H2O=Fe(OH)3↓+3HCl
过氧化氢除铁的反应原理
2FeCl2+2H2O2+2HCl=2FeCl3+2H2O
FeCl3+3H2O=Fe(OH)3↓+3HCl
在除铁过程中,首先根据化验得出的铁盐含量计算出氧化剂的用量,将氧化剂用水制成饱和溶液后放入助镀槽中,这时助镀槽温度应控制在60℃—80℃。
若温度过低则造成反应速度变慢。
在加入氧化剂时特别要注意:要加饱和溶液,不要加固体。
因为加入的固体氧化剂颗粒在溶解时容易被水解后的Fe(OH)3包裹,使之不再继续溶解而沉入底渣中,造成氧化剂大量浪费。
3.3、过滤(分离)
目前除铁后分离方式主要有过滤泵过滤、板块压滤机过滤、自然沉降过滤三种方式。
自然沉降过滤所需温度要控制在80℃以上,将已制成饱和溶液的絮凝剂(聚丙烯酰胺)放入助镀槽中均匀搅拌,使Fe(O
H)3迅速沉降。
沉降后,上部为清液,下部为底渣。
最后可将混液和底渣排放,而清液可用酸泵抽出使用。
4、经济性分析
氧化剂的选择应根据其来源、价格、使用量等条件来确定。
1、高锰酸钾:
5FeCl2+KmnO4+8HCl=MnCl2+5FeCl3+4H2O+KCl
根据方程式计算得出:除掉1公斤氯化亚铁需使用高锰酸钾0.19公斤。
2、氯酸钾(钠):
6FeCl2+KClO3+6HCl=6FeCl3+KCl+3H2O
根据方程式计算得出:除掉1公斤氯化亚铁需使用氯酸钾0.16公斤或需氯酸钠0.14公斤。
3、次氯酸钙(钠):
4FeCl2+Ca(ClO)2+4HCl=4FeCl3+CaCl2+2H2O
根据方程式计算得出:除掉1公斤氯化亚铁需使用次氯酸钙0.57公斤或需次氯酸钠0.29公斤。
4、过氧化氢:
2FeCl2+2H2O2+2HCl=2FeCl3+2H2O
根据方程式计算得出:除掉1公斤氯化亚铁需使用过氧化氢0.13公斤。
从上表可以看出,每除去1公斤氯化亚铁所需氧化剂的费用从高到低排序为:高锰酸钾——次氯酸钙——次氯酸钠——氯酸钾——过氧化氢——氯酸钠。
因为过氧化氢是最洁净的氧化剂,所以目前很多企业使用过氧化氢除铁。
但由于其为液体,浓度低、体积大,不便于运输和贮存,而且过氧化氢存放一年浓度还会下降约3%,造成了成本加大。
另外过氧化氢在使用过程中对人体危害较大,其蒸汽对眼睛、鼻子、喉咙造成强烈的刺激,最终可能导致慢性呼吸器官疾病,皮肤接触也会造成疼痛及腐蚀,迸入眼睛有可能致盲。
而氯酸钠除铁费用最低,且相对安全,因此从安全和经济性角度考虑,氧化剂一般应选择氯酸钠。
5、结束语
在热浸镀锌助镀剂除铁工艺中,氧化剂无论选择哪一种都要以经济性和安全性综合考虑,但更主要的是除铁工艺的选择,只有在正确的除铁工艺指导下,才能达到最好的除铁效果,使热浸镀锌企业获得更高的经济效益。