锻件的层状断口
锻件缺陷分析报告

锻造对金属组织、性能的影响与锻件缺陷锻件的缺陷包括表面缺陷和部缺陷。
有的锻件缺陷会影响后续工序的加工质量,有的则严重影响锻件的性能,降低所制成品件的使用寿命,甚至危及安全。
因此,为提高锻件质量,避免锻件缺陷的产生,应采取相应的工艺对策,同时还应加强生产全过程的质量控制。
概要介绍三方面的问题:锻造对金属组织、性能的影响与锻件缺陷;锻件质量检验的容和方法;锻件质量分析的一般过程。
(一)锻造对金属组织和性能的影响锻造生产中,除了必须保证锻件所要求的形状和尺寸外,还必须满足零件在使用过程中所提出的性能要求,其中主要包括:强度指针、塑性指针、冲击韧度、疲劳强度、断裂韧度和抗应力腐蚀性能等,对高温工作的零件,还有高温瞬时拉伸性能、持久性能、抗蠕变性能和热疲劳性能等。
锻造用的原材料是铸锭、轧材、挤材和锻坯。
而轧材、挤材和锻坯分别是铸锭经轧制、挤压及锻造加工后形成的半成品。
锻造生产中,采用合理的工艺和工艺参数,可以通过下列几方面来改善原材料的组织和性能:1)打碎柱状晶,改善宏观偏析,把铸态组织变为锻态组织,并在合适的温度和应力条件下,焊合部孔隙,提高材料的致密度;2)铸锭经过锻造形成纤维组织,进一步通过轧制、挤压、模锻,使锻件得到合理的纤维方向分布;3)控制晶粒的大小和均匀度;4)改善第二相(例如:莱氏体钢中的合金碳化物)的分布;5)使组织得到形变强化或形变——相变强化等。
由于上述组织的改善,使锻件的塑性、冲击韧度、疲劳强度及持久性能等也随之得到了提高,然后通过零件的最后热处理就能得到零件所要求的硬度、强度和塑性等良好的综合性能。
但是,如果原材料的质量不良或所采用的锻造工艺不合理,则可能产生锻件缺陷,包括表面缺陷、部缺陷或性能不合格等。
(二)原材料对锻件质量的影响原材料的良好质量是保证锻件质量的先决条件,如原材料存在缺陷,将影响锻件的成形过程及锻件的最终质量。
如原材料的化学元素超出规定的围或杂质元素含量过高,对锻件的成形和质量都会带来较大的影响,例如:S、B、Cu、Sn等元素易形成低熔点相,使锻件易出现热脆。
锻件的层状断口 -回复

锻件的层状断口-回复锻件的层状断口是指金属材料在受到外力作用下发生断裂时,在断口上呈现出一定的层状结构。
这种断口形貌的出现,是由于在金属材料的断裂过程中,包括晶界滑移、晶粒形变、相互间的变形差异等因素所导致的。
锻件是通过对金属材料进行锻造加工,使其在高温高压下通过压制,使材料的微观结构得以优化,提高材料的力学性能和物理性质。
然而,尽管锻造加工能够在一定程度上提高材料的综合性能,但是金属材料在实际使用中仍然存在着一定的断裂风险。
而锻件的层状断口正是这种断裂风险的一种表现形式。
为了更加深入地了解锻件的层状断口,我们需要从以下几个方面进行逐步解析。
首先,理解锻造过程中的变形特点对于理解层状断口的形成起到了关键作用。
在锻造过程中,金属材料受到了巨大的力学变形,通过压制使得晶粒重新排列,结晶界得到重新的形成,从而使得金属材料的力学性能得到提高。
然而,由于金属材料内部存在着晶界滑移和晶粒的形变,这些变形在金属的断裂过程中往往变得不均匀。
这种变形差异使得材料在断裂时发生局部应力集中,从而形成层状断口。
其次,断裂的产生和传播过程对于层状断口的形成也有着重要的影响。
在金属材料的断裂过程中,断裂的产生往往开始于材料中的缺陷、夹杂物或者应力集中点。
一旦断裂开始,则裂纹会随着应力场的变化不断扩展,最终导致材料的完全断裂。
而由于金属材料内部存在着晶界和晶粒的差异,这些差异会对断裂裂纹的传播路径产生一定的影响,从而使得断裂形成呈现出层状结构。
此外,材料的化学成分和热处理对于层状断口的形成也具有一定的影响。
在锻造过程中,材料内部的化学成分会影响晶界和晶粒的形变行为,从而影响应力场的分布。
而热处理则可以通过改变材料的显微组织,使得晶界和晶粒的差异得以减小,从而减少层状断口的形成。
综上所述,锻件的层状断口是金属材料在断裂过程中的一种特殊现象,其形成受到多种因素的影响。
通过深入研究金属材料的微观结构和断裂机制,可以更好地理解锻件的层状断口形成的原理,并采取相应的措施来减少断裂风险,提高锻件的可靠性和使用寿命。
常见锻造缺陷
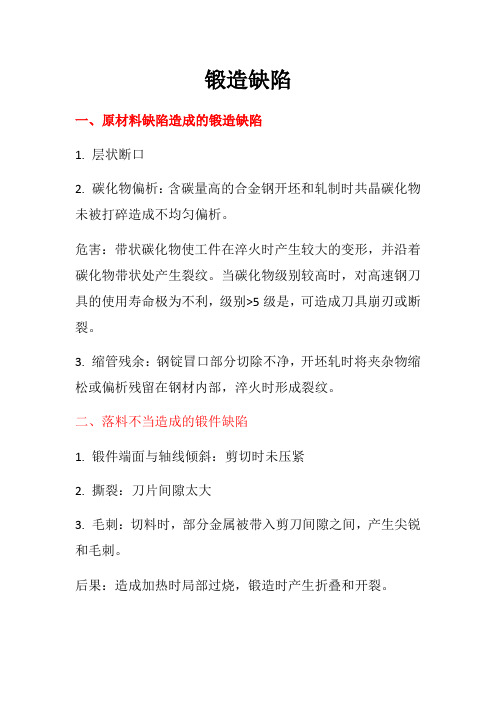
锻造缺陷一、原材料缺陷造成的锻造缺陷1. 层状断口2. 碳化物偏析:含碳量高的合金钢开坯和轧制时共晶碳化物未被打碎造成不均匀偏析。
危害:带状碳化物使工件在淬火时产生较大的变形,并沿着碳化物带状处产生裂纹。
当碳化物级别较高时,对高速钢刀具的使用寿命极为不利,级别>5级是,可造成刀具崩刃或断裂。
3. 缩管残余:钢锭冒口部分切除不净,开坯轧时将夹杂物缩松或偏析残留在钢材内部,淬火时形成裂纹。
二、落料不当造成的锻件缺陷1. 锻件端面与轴线倾斜:剪切时未压紧2. 撕裂:刀片间隙太大3. 毛刺:切料时,部分金属被带入剪刀间隙之间,产生尖锐和毛刺。
后果:造成加热时局部过烧,锻造时产生折叠和开裂。
4. 端部裂纹:剪切大断面坯料时,圆形端面变成椭圆形,材料中产生很大的内应力,引起应力裂纹。
另外,气割落料前,原材料没有预热,产生加工应力导致裂纹5. 凸芯开裂:车床下料时,棒料端面中心留有凸芯,锻造时凸芯冷却快,由于应力集中造成开裂。
三、锻造工艺不当造成的缺陷1. 过热:加热停留时间过长或加热温度过高引起材料晶粒粗大2. 过烧:过烧时,晶粒特别粗大,断口呈石状。
对碳钢,金相组织出现晶界氧化和熔化;工模具钢晶界因为熔化而出现鱼骨状莱氏体;铝合金出现晶界熔化三角区或复熔球。
3. 锻造裂纹1)加热裂纹:尺寸大的坯料快速加热造成内外温差大,热应力大造成开裂。
特征:由中心向四周辐射状扩展,多产生于高合金材料2)心部开裂:常在坯料的头部,开裂深度与加热和锻造有关,有事贯穿整个坯料。
原因:加热时保温不足,坯料未热透,外部温度高,塑性好,变形大,内部温度低变形小,内外产生不均匀变形3)材质缺陷开裂:锻造时在缩孔夹渣碳化物偏析等材料缺陷处形成锻造裂纹4. 脱碳和增碳1)脱碳:钢材表面在高温下,碳被氧化发生脱碳,使表层组织含碳量下降,硬度下降,强度下降,脱碳层的深度与钢的成分、炉内气氛、温度有关。
通常高碳钢易氧化脱碳,氧化性气氛中易脱碳。
锻件缺陷 标准
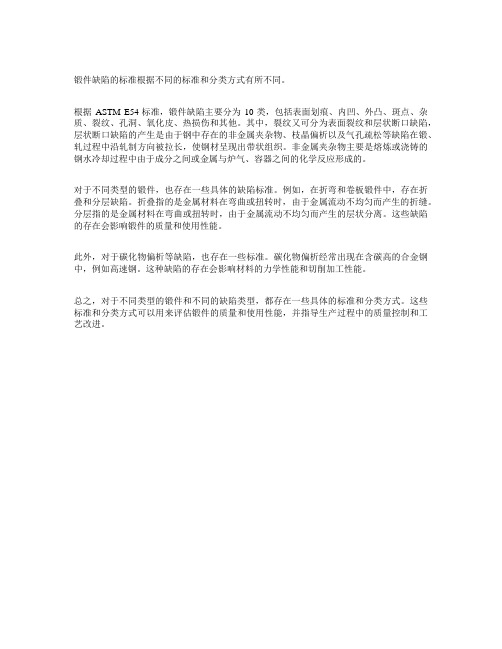
锻件缺陷的标准根据不同的标准和分类方式有所不同。
根据ASTM E54标准,锻件缺陷主要分为10类,包括表面划痕、内凹、外凸、斑点、杂质、裂纹、孔洞、氧化皮、热损伤和其他。
其中,裂纹又可分为表面裂纹和层状断口缺陷,层状断口缺陷的产生是由于钢中存在的非金属夹杂物、枝晶偏析以及气孔疏松等缺陷在锻、轧过程中沿轧制方向被拉长,使钢材呈现出带状组织。
非金属夹杂物主要是熔炼或浇铸的钢水冷却过程中由于成分之间或金属与炉气、容器之间的化学反应形成的。
对于不同类型的锻件,也存在一些具体的缺陷标准。
例如,在折弯和卷板锻件中,存在折叠和分层缺陷。
折叠指的是金属材料在弯曲或扭转时,由于金属流动不均匀而产生的折缝。
分层指的是金属材料在弯曲或扭转时,由于金属流动不均匀而产生的层状分离。
这些缺陷的存在会影响锻件的质量和使用性能。
此外,对于碳化物偏析等缺陷,也存在一些标准。
碳化物偏析经常出现在含碳高的合金钢中,例如高速钢。
这种缺陷的存在会影响材料的力学性能和切削加工性能。
总之,对于不同类型的锻件和不同的缺陷类型,都存在一些具体的标准和分类方式。
这些标准和分类方式可以用来评估锻件的质量和使用性能,并指导生产过程中的质量控制和工艺改进。
锻件的常见缺陷及原因分析

锻件的常见缺陷及原因分析(2007/07/05 10:58)锻件的缺陷很多,产生的原因也多种多样,有锻造工艺不良造成的,有原材料的原因,有模具设计不合理所致等等。
尤其是少无切削加工的精密锻件,更是难以做到完全控制。
1.大晶粒大晶粒通常是由于始锻温度过高和变形程度不足、或终锻温度过高、或变形程度落人临界变形区引起的。
铝合金变形程度过大,形成织构;高温合金变形温度过低,形成混合变形组织时也可能引起粗大晶粒,晶粒粗大将使锻件的塑性和韧性降低,疲劳性能明显下降。
2.晶粒不均匀晶粒不均匀是指锻件某些部位的晶粒特别粗大,某些部位却较小。
产生晶粒不均匀的主要原因是坯料各处的变形不均匀使晶粒破碎程度不一,或局部区域的变形程度落人临界变形区,或高温合金局部加工硬化,或淬火加热时局部晶粒粗大。
耐热钢及高温合金对晶粒不均匀特别敏感。
晶粒不均匀将使锻件的持久性能、疲劳性能明显下降。
3.冷硬现象变形时由于温度偏低或变形速度太快,以及锻后冷却过快,均可能使再结晶引起的软化跟不上变形引起的强化(硬化),从而使热锻后锻件内部仍部分保留冷变形组织。
这种组织的存在提高了锻件的强度和硬度,但降低了塑性和韧性。
严重的冷硬现象可能引起锻裂。
4.裂纹裂纹通常是锻造时存在较大的拉应力、切应力或附加拉应力引起的。
裂纹发生的部位通常是在坯料应力最大、厚度最薄的部位。
如果坯料表面和内部有微裂纹、或坯料内存在组织缺陷,或热加工温度不当使材料塑性降低,或变形速度过快、变形程度过大,超过材料允许的塑性指针等,则在镦粗、拔长、冲孔、扩孔、弯曲和挤压等工序中都可能产生裂纹。
5.龟裂龟裂是在锻件表面呈现较浅的龟状裂纹。
在锻件成形中受拉应力的表面(例如,未充满的凸出部分或受弯曲的部分)最容易产生这种缺陷。
引起龟裂的内因可能是多方面的:①原材料合Cu、Sn等易熔元素过多。
②高温长时间加热时,钢料表面有铜析出、表面晶粒粗大、脱碳、或经过多次加热的表面。
③燃料含硫量过高,有硫渗人钢料表面。
锻件的层状断口 -回复

锻件的层状断口-回复什么是锻件的层状断口?锻件的层状断口是在金属锻造过程中产生的一种特殊的断口形貌。
通常情况下,金属经过锻造过程后,常常会呈现出一种层状的结构形态。
这种结构形态是由于金属在不同方向上的应力分布不均所导致的。
当金属受到外力作用时,会经历塑性变形,而不同方向上的应力分布则会导致这种层状结构的形成。
金属的层状结构是由多个层片状的金属晶粒组成的,这些晶粒之间常常会存在一定的间隙或裂纹。
这也是层状断口形成的主要原因之一。
在金属锻造过程中,金属在受到外力作用时,会经历塑性变形和流动。
当金属内部存在缺陷或晶粒边界处出现滑移时,金属会沿晶界或缺陷处发生断裂。
而这种断裂常常会呈现出一种层状的形态。
金属锻造过程中的层状断口具有以下特点:1. 层状结构:金属的层状断口呈现出多个层片状的结构形态,这些层片之间常常会存在一定的空隙或裂纹。
2. 断裂沿晶界或缺陷处发生:金属的层状断口是由金属内部的缺陷或晶界处的滑移引起的断裂。
这种断裂往往是在金属内部的某个特定区域发生的。
3. 反映金属内部力学性能:金属的层状断口可以反映金属内部的力学性能。
通过观察层状断口的形态和特征,可以了解金属的塑性变形和断裂性能。
4. 与金属的锻造工艺有关:金属的层状断口与金属的锻造工艺密切相关。
不同的锻造工艺会导致不同形态和特征的层状断口。
通过观察金属的层状断口,可以获得关于金属的结构和力学性能的信息。
而这些信息对于锻造工艺的优化和产品质量的控制具有重要意义。
因此,准确理解和分析金属的层状断口是金属锻造研究的重要内容之一。
总结:金属的层状断口是金属锻造过程中产生的一种特殊的断口形貌。
它是由金属内部的缺陷或晶界处的滑移引起的断裂形态,呈现出多个层片状的结构。
通过观察层状断口的形态和特征,可以了解金属的塑性变形和断裂性能。
金属的层状断口与金属的锻造工艺密切相关,通过分析层状断口可以获得关于金属结构和力学性能的信息,对于锻造工艺的优化和产品质量的控制具有重要意义。
大型锻件中常见的缺陷与对策
大型锻件中常见的缺陷与对策大型锻件中常见的缺陷与对策大型锻件中的缺陷,从性质上分为化学成分、组织性能不合格,第二相析出,类孔隙性缺陷和裂纹五大类。
从缺陷的产生方面可分为,在冶炼、出钢、注锭、脱模冷却或热送过程中产生的原材料缺陷及在加热、锻压、锻后冷却和热处理过程中产生的锻件缺陷两大类。
大型锻造中,由于锻件截面尺寸大,加热、冷却时,温度的变化和分布不均匀性大,锻压变形时,金属塑性流动差别大,加上钢锭大冶金缺陷多,因而容易形成一些不同于中小型锻造的缺陷。
如严重偏析和疏松,密集性夹杂物,发达的柱状晶及粗大不均匀结晶,敏感开裂与白点倾向,晶粒遗传性与回火脆性,组织性能的严重不均匀性,形状尺寸超差等等。
大型锻件中常见的主要缺陷有:1.偏析钢中化学成分与杂质分布的不均匀现象,称为偏析。
一般将高于平均成分者,称为正偏析,低于平均成分者,称为负偏析。
尚有宏观偏析,如区域偏析与微观偏析,如枝晶偏析,晶间偏析之分。
大锻件中的偏析与钢锭偏析密切相关,而钢锭偏析程度又与钢种、锭型、冶炼质量及浇注条件等有关。
合金元素、杂质含量、钢中气体均加剧偏析的发展。
钢锭愈大,浇注温度愈高,浇注速度愈快,偏析程度愈严重。
(1)区域偏析它属于宏观偏析,是由钢液在凝固过程中选择结晶,溶解度变化和比重差异引起的。
如钢中气体在上浮过程中带动富集杂质的钢液上升的条状轨迹,形成须状∧形偏析。
顶部先结晶的晶体和高熔点的杂质下沉,仿佛结晶雨下落形成的轴心∨形偏析。
沉淀于锭底形成负偏析沉积锥。
最后凝固上部区域,碳、硫、磷等偏析元素富集,成为缺陷较多的正偏析区。
图1为我国解剖的55t34CrMolA钢锭纵剖面硫印低倍图片及区域偏析示意图。
图1 钢锭区域偏析硫印示意图①“∧”型偏析带②“∨”型偏析带③负偏析区防止区域偏析的对策是:1)降低钢中硫、磷等偏析元素和气体的含量,如采用炉外精炼,真空碳脱氧(VCD)处理及锭底吹氩工艺。
2)采用多炉合浇、冒口补浇、振动浇注及发热绝热冒口,增强冒口补缩能力等措施。
锻件缺陷的主要特征及其产生的主要原因
锻造件缺陷是指锻造过程中锻件上产生的外在的和内在的质量不合要求的各种毛病。
锻件缺陷如按其表现形式来区分,可分为:外部的、内部的和性能的三种。
外部缺陷如几何尺寸和形状不符合要求。
表面裂纹、折叠、缺肉、错差、模锻不足、表面麻坑、表面气泡和橘皮状表面等。
这类缺陷显露在锻件的外表面上,比较容易发现或观察到。
内部缺陷又可分为低倍缺陷和显微缺陷两类。
前者如内裂、缩孔、疏松、白点、锻造流纹紊乱、偏析、粗晶、石状断口、异金属夹杂等;后者如脱碳、增碳、带状组织。
铸造组织残留和碳化物偏析级别不符合要求等。
内部缺陷存在于锻件的内部,原因复杂,不易辨认,常常给生产造成较大的困难。
反映在性能方面的缺陷,如室温强度、塑性、韧性或疲劳性能等不合格;或者高温瞬时强度,持久强度、持久塑性、蠕变强度不符合要求等。
性能方面的缺陷,只有在进行了性能试验之后,才能确切知道。
值得注意的是内外部和性能方面的缺陷这三者之间,常常有不可分割的联系。
例如过热和过烧表现于外部常为裂纹的形式:表现于内部则为晶粒粗大或脱碳,表现在性能方面则为塑性和韧性的降低。
因此,为了准确确定锻件缺陷的原因,除了必须辨明它们的形态和特征之外,还应注意找出它们之间的内在联系。
锻造过程产生的缺陷和热处理过程产生的缺陷。
按照锻造过程中各工序的顺序,还可将锻造过程中产生的缺陷,细分为以下几类:由下料产生的缺陷;由加热产生的缺陷:由锻造产生的缺陷:由冷却产生的缺陷和由清理产生的缺陷等。
不同工序可以产生不同形式的缺陷,但是,同一种形式的缺陷也可以来自不同的工序。
由于产生锻件缺陷的原因往往与原材料生产过程和锻后热处理有关,因此在分析锻件缺陷产生的原因时,不要孤立地来进行。
锻件的热处理种类及应用
“蛤蟆皮” 铝合金、铜合金的坯料,在镦粗时表
由于坯料过热,晶粒粗大而引起
表面 面形成“蛤蟆皮”,或者出现类似秸 有粗晶环的铝合金毛坏,在镦粗时也会出现这种现象
皮的粗糙表面,严重时还要开裂
魏氏 α 相或 (α+β)钛合金坏料过热后,其显微由于加热温度超过了(α+β)钛合金的 β 转变温度而
(普通正火) 钢和过共析钢加热到 Acm+30-50℃, 氏组织或过共析钢的网状 钢和过共析钢的热
保温一定时间后空冷,得到珠光体型碳化物,减小应力,改善切
处理
组织的热处理
削加工性能
二段正火 按普通正火加热保温后,先把工件快 减少变形和消除非正常组 用于形状复杂或断
冷到 Ar1 以下 550℃左右,然后再放入
白点在合金结构钢中常见,在普通碳
钢中也有发现
缩孔残余 在锻件低倍检查时,出现不规则的皱 由于钢锭冒口部分产生的集中缩孔未切除干净,开坯
折状缝隙,形似裂纹,呈现深褐色或
和轧制时残留在钢坯内部而产生的
灰白色;高倍检查缩孔残余附近有大
量非金属夹杂物,质脆易剥落
铝合金挤压 经热处理后供应的铝合金挤压棒材, 主要是由于铝合金中 Mn、Cr 等元素以及挤压时金属
热处理工艺
将时效强化合金或不锈钢、耐热钢加 改善锻态时的强化相不均匀分 用于不锈钢、耐
热到一定高温(不锈钢、耐热钢为 布,降低硬度、提高塑性、抗 热钢和时效强化
1000-1150℃)使强化相全部或大部 蚀性及导电性或为以后的时效
合金
分溶入固溶体,并调整晶粒尺寸,然
处理进行准备
后以较快速度(水、空气等)冷却
棒材上的粗 在其横断面外层环形内出现粗大晶 与挤压筒壁之间的摩擦,使棒材表面层变形剧烈所致
层状撕裂断口及其形成机理
层状撕裂断口及其形成机理一、层状撕裂断口的定义层状撕裂断口是指材料在拉伸或剪切载荷作用下,出现沿其断面呈现出层状剥离的现象。
这种断口通常表现为多个平行的层状裂纹,断面呈现出明显的层状结构。
二、层状撕裂断口的形成机理层状撕裂断口的形成机理主要涉及以下几个方面:1.剪切力的作用:当材料受到剪切力作用时,材料内部的层状结构容易发生滑动,从而引发层状裂纹的形成。
这种情况通常发生在具有层状结构的复合材料中,比如纤维增强复合材料。
2.拉伸载荷的作用:在拉伸载荷作用下,材料内部的层状结构会受到拉伸力的拉伸和撕裂,从而导致层状裂纹的形成。
这种情况通常发生在纤维增强塑料等材料中。
3.界面强度的影响:层状撕裂断口的形成还与界面强度有关。
当材料内部的界面强度较低时,容易发生层状裂纹的形成。
而当界面强度较高时,层状撕裂断口的形成则相对困难。
4.材料的结构和性能:不同材料的结构和性能差异也会影响层状撕裂断口的形成。
例如,纤维增强塑料中纤维的分布和排列方式,以及塑料基体的性能等因素都会对层状撕裂断口的形成产生影响。
三、层状撕裂断口的实际应用层状撕裂断口在实际应用中具有重要意义,主要体现在以下几个方面:1.材料性能评估:通过观察层状撕裂断口的形貌特征,可以评估材料的韧性、强度和断裂机制等性能指标。
这对于材料的选用和设计具有重要意义。
2.故障分析:层状撕裂断口的形貌特征可以提供有关材料的断裂原因和机理的重要线索,从而有助于进行故障分析和失效预测。
3.材料改进:通过对层状撕裂断口的分析研究,可以为材料的改进和优化提供指导。
例如,通过改变材料的结构和处理工艺,可以减少层状撕裂断口的形成,提高材料的韧性和强度。
4.产品质量控制:层状撕裂断口的形貌特征还可以用于产品质量的控制。
通过对层状撕裂断口的观察和分析,可以判断产品是否存在材料缺陷和工艺问题等。
层状撕裂断口是材料在拉伸或剪切载荷作用下出现的一种断口形貌,其形成机理主要与剪切力、拉伸载荷、界面强度以及材料的结构和性能等因素有关。
- 1、下载文档前请自行甄别文档内容的完整性,平台不提供额外的编辑、内容补充、找答案等附加服务。
- 2、"仅部分预览"的文档,不可在线预览部分如存在完整性等问题,可反馈申请退款(可完整预览的文档不适用该条件!)。
- 3、如文档侵犯您的权益,请联系客服反馈,我们会尽快为您处理(人工客服工作时间:9:00-18:30)。
锻件的层状断口
锻件的层状断口是指在金属材料的拉伸、压缩或弯曲等力学加工过程中,材料发生断裂时,断口呈现出层状结构。
这种断口形貌类似于木材的剖面,由多条平行的层状裂缝组成。
锻件的层状断口形成的原因主要有以下几点:
1.金属材料在受到外力作用时,会在应力集中区域发生局部塑性变形。
当应力超过材料的屈服强度时,就会形成裂纹。
随着外力的继续作用,裂纹会逐渐扩展,形成层状断口。
2.金属材料的微观结构和组织也会影响层状断口的形成。
如果材料的结晶粒度较大,裂缝扩展路径较长,就容易形成层状断口。
3.材料的纯度、含气等也会影响层状断口的形成。
锻件的层状断口会导致钢的横向力学性能严重下降,特别是延伸率和断面收缩率。
这种层状断口在形变结构钢中经常出现,会显著降低钢的强度和韧性。
因此,在金属材料的加工过程中,应采取措施避免层状断口的形成,如优化加工工艺、控制材料纯度和组织结构等。