浅谈提高电炉炉衬寿命的措施
浅谈延长中低碳铬铁炉衬寿命的措施
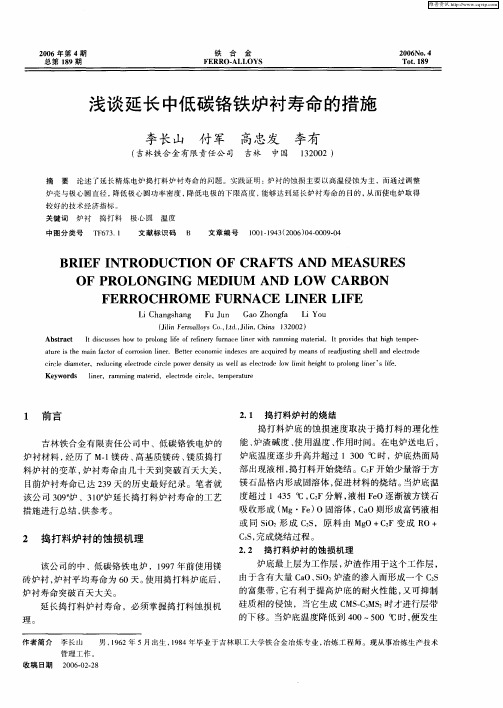
作者简介 李长 山
的下移 。当炉 底温 度降低 到 40~ 0 0 5 0℃ 时 , 发生 便
男 ,9 2年 5月 出 生 ,9 4年 毕业 于吉 林 职 工 大 学 铁 合 金 冶炼 专 业 , 16 18 冶炼 工程 师 。现 从 事 冶 炼 生 产 技术
管理 工 作 。 收稿 日期 2 0 .22 0 60 .8
墙 与 炉底 消耗 相 匹配 ,炉衬 寿命 就会 相应 延 长 。反 之, 炉衬 寿命 就会 相应 缩短 。 这是 影响炉 衬 寿命 的重
要因素。
自 20 0 0年开始 实现 中 、低铬 生产硅铬 热装工 艺
至 20 0 3年 , 实践证 明 , 随着料批 的增 加 , 生产能力 逐 步提 高 , 池 的直 径 、 熔 炉壳 直径偏 小 , 拆炉 时残余炉 墙 不 足 30mm。 要增 大熔 池 和炉壳直径 。 据 D膛= 0 需 根 2 5 心 计算 , . 圆 D垤 D膛= . . 3 5m, 2 5X14= . 比原炉膛 直 径增 加 30m 残余 炉墙 的厚度 应在 30mm左右 , 0 m, 0
料 炉衬 的变革 , 衬 寿命 由几十天 到 突破百 天大关 , 炉
目前炉 衬寿命 已达 2 9天 的历 史最 好纪 录 。笔者 就 3 该 公 司 3 9炉 、3 0炉 延 长捣 打 料炉 衬寿 命 的工 艺 0 1 措施 进行 总结 , 供参 考 。
镁石 晶格 内形 成 固溶体 , 促进 材 料 的烧 结 。 当炉底温
3 4 电极工 作端 长度 的影 响 .
极心 圆直径 是 电炉 的重要 参数 ,参 数选 择 的是 否 合理 , 直接影 响到 生产 指标 和炉衬 寿命 的长短 ( 见
图 1。 )
提高中频感应电炉炉衬寿命的解决方案

( 5 )无需补炉 ,维护简单 ( 仅以塑性料 勾抹 涂缝 ,即抹即熔无需等候 )。 ( 6 )炉龄更长 ,出液量 大 ( 炼钢 1 0 0 炉次 以
上 ,炼 铜2 0 0 炉次以上)。
( 7 )安全性高 ,避免 穿炉 ( 采用双 层炉衬复
合 结构
3 0 V 2 0
’
w w ̄ . r ne t o l w o r k l n ll g S O . c om
箩 期 热 孕簧 压 铸 造 ’ 参 霭 工 热 … 加 … 工 一
I l c !
若按平均送 电6 0 k W烘炉 l O h 计算可省电6 0 0 k W・ h , 以0 . 8 / k W・ h 元计算 ,合人民币4 8 0 元。 ( 3 )熔钢 量大 手工 捣制的炉衬熔钢 一般在 2 3 0 k g 左右 ( 使用后期 ,容量 稍大 )。而采用成型 炉 衬后第 一炉熔 钢就在 2 8 0 k g 以 上 ,每 炉多化 钢 5 0 k g 。一般熔炼 l t 钢需耗电8 0 0 k W・ h 。若 1 0 0 炉 多 熔炼5 t 钢 ,折算节省的 电为4 0 0 0 k W・ h ,节省人 民
几种典型的成型炉衬及相应 的中频 电炉感应线 圈尺寸情况见表 1 。
表1 成型炉衬型号及对应的感应线圈尺寸
型号/ k g 1 0 0 1 5 0 2 5 0 5 0 0 7 5 0 l O 0 0 1 5 0 0 2 O 0 0 3 0 o 0 5 o o 0
币3 2 0 0 元。
炼钢量和降低用电功率三项就节省电费1 8 0 0 0 元。 综上所述 ,使用成型炉衬仅节省的 电费就大于 购买成 型炉衬 的费用 。减 少 了筑 炉次数也 就减少 了原料 、人工 的投入 。使用次数越 多 ,效 果越 明 显。因此 ,成型炉衬是一种高效节电产 品。
延长中频炉炉衬使用寿命的措施

延长中频炉炉衬使用寿命的措施发表时间:2019-12-17T09:05:06.023Z 来源:《科学与技术》2019年第14期作者:李金帅[导读] 本文主要从生产实践中确定可行性分析和影响炉衬使命的原因,摘要:本文主要从生产实践中确定可行性分析和影响炉衬使命的原因,阐述了实施和步骤、措施实施的效果、和经济效益、巩固措施等方面对如何提高中频炉炉衬使用寿命进行了详细阐述,提出改进措施,以提高生产效率。
节约生产成本。
关键词:中频炉炉衬;使用寿命;措施前言:我公司是年产35万吨预焙阳极,其中配套两个组装车间。
组装工序是我公司预焙阳极生产中最后一道工序车间,其任务是向铝电解提供合格的成品阳极炭块组。
中频炉是整个生产链上的核心设备, 其炉衬的使用寿命直接影响生产能力。
一、概述我公司现在中频炉炉龄平均为90炉/次,按照要求,此次目标需要将中频炉炉龄提升至150炉/次以上。
可行性分析:1.对同行业企业的中频炉炉衬使用寿命进行了解,基本情况如下:与同行业其他企业比较,故有必要分析其中原因。
2.工序生产运行时间不长,各主体设备运行状态良好,在工艺改进工作方面能够提供坚实的硬件基础。
二、中频炉炉衬使用寿命短的原因针对中频炉炉衬使用寿命短的情况,我们进行了分析并对找到一些原因,绘制出鱼骨图如下:1.筑炉的质量差根据工艺技术标准,我们根据现场跟踪,检查了筑炉工艺,对与每层的振动和捣打,都不符合工艺标准要求,炉料铺设不均匀,这也是筑炉质量的问题,同时也是中频炉炉衬使用寿命缩短的重要因素。
2.新筑炉衬太薄根据标准规定,炉衬的厚度应该大于15CM才符合标准,根据现场对筑炉完成后的炉衬进行测量,我们发现新筑炉的炉衬太薄,不符合炉衬测量厚度的标准,实际情况的炉衬厚度小于15CM,这是中频炉炉衬使用寿命短的重要因素。
3.人员操作不规范工作人员必须严格按照设备操作规程进行,根据现场仪器仪表显示数据确定启动升温的速度快,我们发现在调查的过程中,人员未严格按照设备操作标准进行操作,所以人员操作不规范也是造成中频炉炉衬使用寿命短的主因素。
浅谈影响AOD炉龄的因素和改进措施罗冬云李良辉李国军李建庆李晨阳

浅谈影响AOD炉龄的因素和改进措施罗冬云李良辉李国军李建庆李晨阳发布时间:2022-01-17T04:02:48.425Z 来源:《基层建设》2021年第29期作者:罗冬云李良辉李国军李建庆李晨阳[导读] AOD炉衬寿命是一个综合性的指标,它不仅与炉型结构设计、耐火材料的选择和使用工艺有关,而且与冶炼工艺水平、各操作参数的控制、设备状况等密切相关。
本文结合AOD炉的操作特点及损毁特征广西柳钢中金不锈钢有限公司炼钢厂摘要:AOD炉衬寿命是一个综合性的指标,它不仅与炉型结构设计、耐火材料的选择和使用工艺有关,而且与冶炼工艺水平、各操作参数的控制、设备状况等密切相关。
本文结合AOD炉的操作特点及损毁特征,介绍了柳钢中金公司围绕以下几方面在提高AOD炉衬寿命上改进措施。
关键词:AOD、炉龄、改进1、前言在国际上,氩氧脱碳法(AOD炉法)是生产不锈钢的主要工艺。
AOD炉以其成本低、易操作、效率高等特点而受青睐,但AOD炉法耐火材料消耗高,炉衬寿命低,一直困扰着AOD炉的生产。
随着柳钢发展不锈钢战略的不断深入,AOD炉衬寿命及其耐火材料成为制约柳钢中金公司发展的一大难题,根据AOD炉的操作条件及炉衬材料的损毁机理,柳钢中金公司AOD炉自投产以来一直在不断地探索提高AOD炉衬寿命的方法。
经过不懈努力,终于在AOD炉龄方面有了重大突破,平均炉龄由此前的47炉左右提高到目前的92炉,最高可达到111次。
2、AOD炉的操作特点及损毁机理AOD炉是向钢水熔池吹氧的同时,吹入惰性气体(Ar,N2),通过降低CO分压,达到假真空的效果,从而去除钢水中的有害气体和夹杂,并使S、P等有害元素含量降到很低的指标,抑制钢水中铬的氧化。
由于采用氩、氧和氮的混合气体或纯氩气进行精炼,气体搅拌钢液产生涡流现象,造成钢液和熔渣的剧烈搅动,熔池衬砖受到严重的冲刷和侵蚀,并受到高温、强碱性熔渣的影响。
AOD炉的冶炼经历了氧化脱碳,还原精炼的过程,炉内气氛发生从氧化到还原的改变,使用条件十分苛刻,炉衬毁损严重,图一为耐火材料的侵蚀状况。
提高转炉炉龄的措施
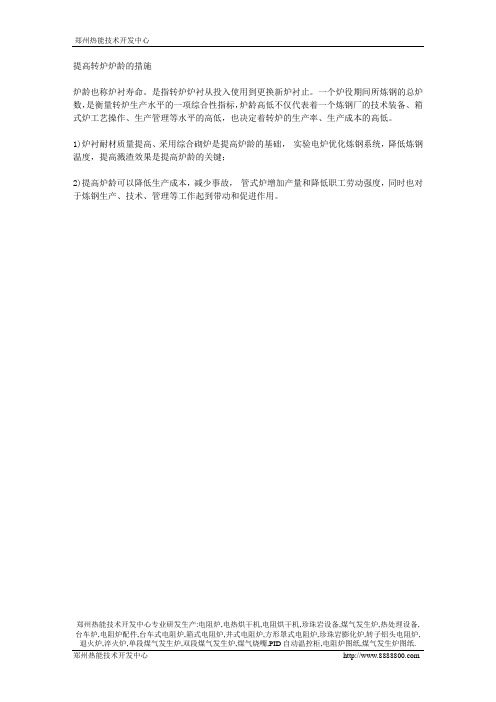
郑州热能技术开发中心
提高转炉炉龄的措施
炉龄也称炉衬寿命。
是指转炉炉衬从投入使用到更换新炉衬止。
一个炉役期间所炼钢的总炉数,是衡量转炉生产水平的一项综合性指标,炉龄高低不仅代表着一个炼钢厂的技术装备、箱式炉工艺操作、生产管理等水平的高低,也决定着转炉的生产率、生产成本的高低。
1)炉衬耐材质量提高、采用综合砌炉是提高炉龄的基础,实验电炉优化炼钢系统,降低炼钢温度,提高溅渣效果是提高炉龄的关键;
2)提高炉龄可以降低生产成本,减少事故,管式炉增加产量和降低职工劳动强度,同时也对于炼钢生产、技术、管理等工作起到带动和促进作用。
郑州热能技术开发中心专业研发生产:电阻炉,电热烘干机,电阻烘干机,珍珠岩设备,煤气发生炉,热处理设备,台车炉,电阻炉配件,台车式电阻炉,箱式电阻炉,井式电阻炉,方形罩式电阻炉,珍珠岩膨化炉,转子铝头电阻炉,退火炉,淬火炉,单段煤气发生炉,双段煤气发生炉,煤气烧嘴,PID自动温控柜,电阻炉图纸,煤气发生炉图纸. 郑州热能技术开发中心。
提高电炉炉衬使用寿命的探讨

2 炉 衬 侵 蚀 原 因 分 析
衬 的侵蚀 原 理进 行 分 析 :
1 O吨工 频 感应 电炉 其 结 构 最外 层 是 感应 线 圈 ,往 里
是耐 火 砖 , 再往 里 是 报警 电极 、 云母 板 、 石棉 板 、 棉 布 等 石 隔热 材 料 ,最里 面 直 接 与铁 水 接 触 的 是 坩埚 ,也 就 是 炉 衬 。烘 炉烧 结 后 , 衬一 般 形 成 烧 结 层 , 炉 过渡 层 及 松 散 层
( ) 高 炉 衬 材 料 的热 强 度 ( 别 是 烧 结 层 ) 提 高 1提 特 以
炉 衬 抗 冲刷 性能 ;
( ) 高 炉衬 材 料 的物 理化 学 稳 定 性 能 , 加 炉 衬 抗 2提 增
侵 蚀性 能 。
重 制 约 了铸 管 生产 的组 织 , 频繁 的停 、 、 、 炉 使 炉子 拆 筑 烘 的利 用率 下 降 , 水 的处 理 能力 不 足 , 铁 无法 保 证 离 心 浇注 多台 离心 机 同 时生 产 的 铁水 供 应 , 约 了产量 、 制 质量 的进
炉料 的冲刷 等 。
我 公 司是 我 国最 早 引 进 离 心 球 墨铸 铁 管生 产 设 备 及 工 艺 的厂 家 之 一 ,采 用 水 冷 金 属 型法 生 产 离 心球 墨铸 铁
管 ,现 具 有 2 O万 吨 / 铸 管 生 产 能 力 ,产 品 最 小 规 格 年
D 8 , 大规 格 D 10 。 N 0最 N 2 0 熔 炼 采 用双 联 熔 炼 , 装 高 炉 铁 水 运 至 厂 房 内 , 先 罐 首 倒 人 混铁 炉 保 温均 衡 铁 水 , 后倒 人 电炉 调 质 、 温 。 在 然 调
生 产 过 程 中我 们 发 现 , 由于 以下 原 因 , 衬 使 用 寿 命 低 , 炉 成 为制 约 了铸 管 生产 的瓶 颈 因 素 。
提高炉衬寿命的原理措施

图 1 生产率、成本与炉龄的关系A 一炉衬费用;B 一喷补费用; A +B 一综合成本;C 一炉子生产率;D —最佳炉龄提高转炉炉衬寿命的原理及相应措施转炉从开新炉到停炉,整个炉役期间炼钢的总炉数称为炉衬寿命,简称炉龄。
它是炼钢生产的一项重要技术经济指标。
炉龄,特别是平均炉龄在很大程度上反映出炼钢车间的管理水平和技术水平。
炉龄延长可以增加钢的产量和降低耐火材料消耗,并有利于提高钢的质量。
但对于一定的生产条件和技术水平的车间,存在着一个技术经济效果最好的最佳炉龄,图-1为某厂的一例。
因此,应该努力改善生产条件和提高技术水平,将最佳炉龄不断提高到新的水平。
同时应该反对不顾技术经济效果而盲目追求最高炉龄的倾向。
1 转炉用耐火材料1.1 转炉用耐火材料的演变自氧气转炉问世以来,其炉衬的工作层都是用碱性耐火材料砌筑。
曾经用过白云石质耐火材料,制成焦油结合砖,在高温条件下砖内的焦油受热分解,残留在砖体内的碳石墨化,形成碳素骨架。
它可以支撑和固定白云石材料的颗粒,增强砖体的强度,同时还能填充耐火材料颗粒间的空隙,提高了砖体的抗渣性能。
为了进一步提高炉衬砖的耐化学侵蚀性和高温强度,也曾使用过高镁白云石砖和轻烧油浸砖,炉衬寿命均有提高,炉龄一般在几百炉。
直到20世纪70年代兴起了以死烧或电熔镁砂和碳素材料为原料,用各种碳质结合剂,制成镁碳砖。
镁碳砖兼备了镁质和碳质耐火材料的优点,克服了传统碱性耐火材料的缺点,镁碳砖的抗渣性强,导热性能好,避免了镁砂颗粒产生热裂;同时由于有结合剂固化后形成的碳网络,将氧化镁颗粒紧密牢固地连接在一起。
用镁碳砖砌筑转炉内衬,大幅度提高了炉衬使用寿命,再配合适当维护方式,炉衬寿命可达到万炉以上。
1.2 转炉内衬用砖顶吹转炉的内衬是由绝热层、永久层和工作层组成。
绝热层一般用石棉板或耐火纤维砌筑;永久层是用焦油白云石砖或者低档镁碳砖砌筑;工作层都是用镁碳砖砌筑。
转炉的工作层与高温钢水和熔渣直接接触,受高温熔渣的化学侵蚀,受钢水、熔渣和炉气的冲刷,还受到加废钢时的机械冲撞等,工作环境十分恶劣。
浅谈中频炉炉龄的提高
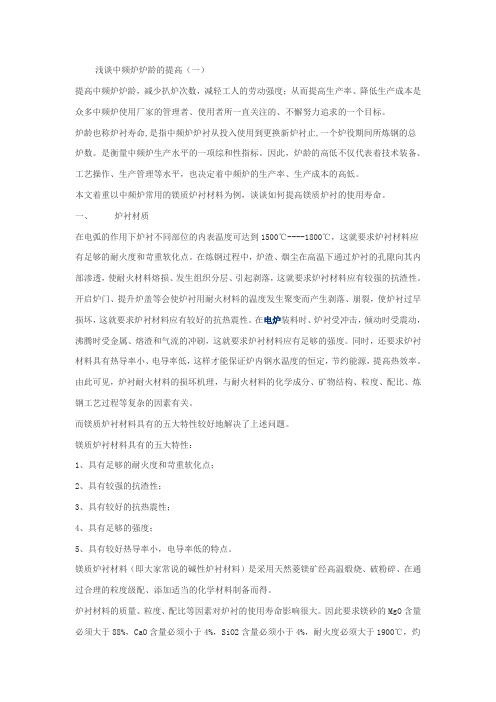
浅谈中频炉炉龄的提高(一)提高中频炉炉龄,减少扒炉次数,减轻工人的劳动强度;从而提高生产率、降低生产成本是众多中频炉使用厂家的管理者、使用者所一直关注的、不懈努力追求的一个目标。
炉龄也称炉衬寿命,是指中频炉炉衬从投入使用到更换新炉衬止,一个炉役期间所炼钢的总炉数。
是衡量中频炉生产水平的一项综和性指标。
因此,炉龄的高低不仅代表着技术装备、工艺操作、生产管理等水平,也决定着中频炉的生产率、生产成本的高低。
本文着重以中频炉常用的镁质炉衬材料为例,谈谈如何提高镁质炉衬的使用寿命。
一、炉衬材质在电弧的作用下炉衬不同部位的内表温度可达到1500℃----1800℃,这就要求炉衬材料应有足够的耐火度和苛重软化点。
在炼钢过程中,炉渣、烟尘在高温下通过炉衬的孔隙向其内部渗透,使耐火材料熔损、发生组织分层、引起剥落,这就要求炉衬材料应有较强的抗渣性。
开启炉门、提升炉盖等会使炉衬用耐火材料的温度发生聚变而产生剥落、崩裂,使炉衬过早损坏,这就要求炉衬材料应有较好的抗热震性。
在电炉装料时、炉衬受冲击,倾动时受震动,沸腾时受金属、熔渣和气流的冲刷,这就要求炉衬材料应有足够的强度。
同时,还要求炉衬材料具有热导率小、电导率低,这样才能保证炉内钢水温度的恒定,节约能源,提高热效率。
由此可见,炉衬耐火材料的损坏机理,与耐火材料的化学成分、矿物结构、粒度、配比、炼钢工艺过程等复杂的因素有关。
而镁质炉衬材料具有的五大特性较好地解决了上述问题。
镁质炉衬材料具有的五大特性:1、具有足够的耐火度和苛重软化点;2、具有较强的抗渣性;3、具有较好的抗热震性;4、具有足够的强度;5、具有较好热导率小,电导率低的特点。
镁质炉衬材料(即大家常说的碱性炉衬材料)是采用天然菱镁矿经高温煅烧、破粉碎、在通过合理的粒度级配、添加适当的化学材料制备而得。
炉衬材料的质量、粒度、配比等因素对炉衬的使用寿命影响很大。
因此要求镁砂的MgO含量必须大于88%,CaO含量必须小于4%,SiO2含量必须小于4%,耐火度必须大于1900℃,灼减必须小于0.6%。
- 1、下载文档前请自行甄别文档内容的完整性,平台不提供额外的编辑、内容补充、找答案等附加服务。
- 2、"仅部分预览"的文档,不可在线预览部分如存在完整性等问题,可反馈申请退款(可完整预览的文档不适用该条件!)。
- 3、如文档侵犯您的权益,请联系客服反馈,我们会尽快为您处理(人工客服工作时间:9:00-18:30)。
浅谈提高电炉炉衬寿命的措施王刚摘要:本文通过介绍电炉炉衬的侵蚀机理、电炉炉衬材料、合理的炉衬烘烤烧结工艺以及良好的工艺操作等方面分析了影响炉衬寿命的主要因素,并简要地提出了提高电炉炉衬寿命的几项措施。
关键词:电炉炉衬寿命措施1 前言电炉炉衬的使用寿命对于需要连续大规模生产的冶金、铸造企业来说具有重大意义。
由于炉龄是一项综合性指标,炉龄的高低直接影响到钢产量的提高和原材料消耗,因此提高电炉炉衬寿命、降低耐火材料消耗、提高电炉炉龄己引起人们的普遍关注。
2 电炉炉衬侵蚀机理及对其性能的要求2.1 电炉炉衬侵蚀机理1) 炼钢电弧炉的炉顶、炉墙热点部位(如渣线)、及炉底是电弧炉的薄弱环节。
炉顶耐火材料损毁的原因:一是飞溅物、炉尘的侵蚀作用;二是由于电极周围温度高,炉顶温差较大造成的熔蚀和热震作用。
常用的耐火材料有高铝砖、镁铬砖、白云石砖、硅砖等及相应材质的耐火浇注料或捣打料。
炉墙热点部位的内衬容易蚀损,其原因是温度过高,熔渣、钢水侵蚀严重,装料时的冲击作用等。
常用的耐火材料主要是各种碱性耐火材料砌筑,损坏时常进行喷补或铲补。
炉底损毁的主要原因是化学侵蚀和机械冲击。
常用碱性耐火捣打料或浇注料。
电炉各部位炉衬损毁的原因,如表2-1所示。
表2-1电炉各部位炉衬损毁的原因2) 电炉中耐火材料最普遍的损毁机理是侵蚀、冲刷、熔融、剥落和水化,五种因素中最主要的是侵蚀。
电炉耐火材料承受两种类型的侵蚀。
①化学侵蚀。
氧化铁(FeO)或渣中的酸性组分,例如二氧化硅与氧化钙和氧化镁之间的化学反应如下式所示:FeO + MgO= FeO·MgOSiO2 + 2MgO= 2MgO·SiO2CaO + SiO2 + MgO= CaO·MgO·SiO2所有这些反应使炉衬变为熔渣而导致耐火材料损毁。
氧化是经常发生在电炉炉衬中耐火材料侵蚀的一种特殊形式,在此侵蚀机理中耐火材料的碳成分由氧化铁或氧气而被侵蚀。
FeO + C=Fe + COO2 + 2C = 2CO渣中的氧化铁与砖衬的热面中的石墨或焦油/树脂反应,或氧气侵蚀砖衬冷面的石墨或碳粘结剂。
在这两种情况下,砖的强度降低,并可能被熔渣或钢水冲蚀。
②冲刷是第二位的耐火材料损毁机理由于钢水或熔渣流过耐火材料表面并物理地磨损或冲刷炉衬而导致了物理损毁。
在电炉的出钢口、渣线、电极口或排气口平台等处冲刷蚀损机理是最普遍的。
一个更为错综复杂的耐火材料损毁机理称之为剥落。
这是由于炉衬耐火材料遭受迅速加热和冷却导致耐火材料产生应力而造成的。
该应力常常超过耐火材料的强度,因而导致裂纹的相交贯穿,炉衬的碎片将会剥落或完全脱落,这种情况普遍发生在电炉炉顶上。
水化也是电炉耐火材料损毁的一个因素。
假如水渗入炉盖或炉墙,水或水蒸汽能侵蚀耐火材料炉衬,其中的氧化镁和其它碱性氧化物与水或水蒸汽发生如下反应而被水化。
MgO + H2O= Mg(OH)2水化的耐火材料衬耐熔渣和钢水的渗透性差。
2.2 电炉炉衬对耐火材料性能的要求1) 耐火度电弧温度高达3000℃以上,炼钢温度常在1550—1650℃之间。
在返回吹氧冶炼不锈钢时,吹氧末期钢液温度在短时期内高达1800℃以上,因此耐火材料的耐火度必须高。
2) 荷重软化温度电炉熔炼是在高温负荷和经受钢水冲刷的恶劣条件下进行的,因此耐火材料要有高的荷重软化温度。
3) 热稳定性电炉熔炼时温度高,而出钢后,开出炉体(或旋转炉盖)进料时,温度由1600℃左右骤然降至900℃以下,因此要求耐火材料有良好的热稳定性。
4) 抗渣性电炉熔炼是一个复杂多变的物理化学反应过程,为抵抗高温时不同性质、不同成分的炉渣和钢液以及炉气的化学侵蚀,耐火材料必须有良好的抗渣性(化学稳定性)。
5) 耐压强度耐火材料经常受炉料冲击,必须有高的耐压强度。
6) 导热率和导电率为减少电炉熔炼时的热损失,以降低电耗,因此耐火材料的导热率和导电率必须低。
3 提高电炉炉衬寿命的措施3.1 耐火材料的选用筑炉用耐火材料的性能直接影响着炉衬的使用寿命。
水晶石英砂具有较高的耐火度,较小的膨胀系数以及较低的导热性,有足够高的强度和化学稳定性,能抵抗熔渣的侵蚀,能承受加料时固体金属炉料的冲击和融化后液体金属的静压力,有较好的耐急冷急热性,能反复承受金属液融化的高温以及出炉后的降温过程,其化学成分和使用性能如下表3-1所示。
表3-1 石英砂的化学成分和使用性能化学成分SiO2CaO Fe2O3+FeO Al2O3 软化温度耐火度数值99.89% <0.01% <0.004% <0.01% ≥1650℃1750℃保证石英砂质量,除了严把进料关外,在打结炉衬前还需对石英砂做如下处理:①过筛或手选,去除块状物及其他杂质;②磁选,完全去除磁性杂质;③一般要求石英砂中的水分含量应小于0.5%,对其应缓慢烘干处理,烘干温度为210—280℃,时间在4h。
3.2 粘结剂的选用选用硼酸(H2BO3)作为粘结剂。
硼酸在石英砂混合料中主要起粘结作用。
硼酸的加入量在2%~3%之间比较合适,但在生产过程中发现,当炉衬中硼酸的含量大于2.5%时,随硼酸加入量的增加,炉龄显著下降,且在熔炼后,炉壁表面有液体晶体向下流动,其侵蚀速度随硼酸含量的增加而增大。
因此,在烧制炉衬过程中硼酸的加入量的选择为2.0%~2.5%。
3.3 粒度配比炉衬材料中粗细颗粒各起不同的作用。
一粗颗粒起骨架作用,它抗冲击性强,高温性能好,抗渣性能强且能改善炉子的隔热性能。
但打结密度差,在与金属接触的表面上难以形成稳固、完整的烧结层,膨胀较大,容易引起炉衬松散、破裂。
细颗粒用来填充粗颗粒之间的空隙,增加接触表面,以得到较致密的炉衬。
但细砂易烧蚀,若含量太高,耐火度及抗浸蚀能力会降低。
同时由于细砂表面活性大,形成的大量玻璃态物质将与铁水和炉渣积极反应,促使炉衬过快侵蚀。
此外由于高温,细砂粒容易融合,使炉衬收缩产生裂纹。
石英砂的粒度配比及捣固方法影响炉衬的使用寿命,其主要影响炉衬的耐蚀性能和抗高温冲击性能。
经试验,炉衬的抗侵蚀能力与其基体密度成正比,炉衬密度越大,基体组织越密,炉衬的抗侵蚀能力越强。
石英砂配方如表3-2所示。
表3-2炉衬石英砂配方石英砂的粒度(目)8~10 10~20 20~40 70~140 270新工艺11 24 20 20 25 配比(%)旧工艺10 25 25 10 303.4 制定合理的炉衬烘烤烧结工艺炉衬材料中的水分来源有:①硼酸转变时析出的水分;②石英砂中的残余水分和隔热层中石棉板等材料的少量水分;③修补耐火砖层、炉体时带入的水分。
根据水分来源,可预先脱水。
在打结前,除了对石英砂进行烘干外,需对硼酸进行部分脱水处理,可放在电烤箱中烘烤,炉温控制在160—200℃之间,1小时后取出,冷却到60℃时就可以与石英砂搅拌。
经此方法处理后,可减少15%—18%的水分。
烘炉初期,由于炉衬含水量较大,水分又不易排除,这就要求升温缓慢,否则,水蒸汽排不出去,使炉口上涨,造成炉衬松散,水蒸汽残留在烧结层中形成峰窝状孔洞,极易渗漏铁水。
在随后的烘炉过程中,石英砂将发生晶形转变。
600℃前,完成α—β—γ晶形转变,体积急剧膨胀。
870℃—900℃,完成α石英—α鳞石英转变,体积变化较大。
1200℃后石英变成磷石英和方石英的速度加快,体积膨胀较明显。
因此,在600℃前和1200℃后要特别控制升温速度。
过快,会使炉衬厚度方向温度不均,易造成膨胀不一致引起开裂,而且石英砂膨胀过快,在炉衬各层间易形成较大的剪切力,引起裂纹及剥落。
3.5 减少炉渣对炉衬的影响炉料中的铁锈、回炉料带入的型砂以及加料、出钢水时钢水溅在炉口和炉壁上被氧化等,产生大量的FeO炉渣,这些FeO与炉衬中的SiO2、炉渣中的SiO2、Al2O3等氧化物形成FeO—SiO2—Al2O3系熔渣。
在温度较低时,这些炉渣挂在炉壁上,温度较高时,又易于上浮,严重浸蚀时,粘结在炉壁上的炉渣冷却后不易清除,特别是大量炉渣不早扒除,或生成粘糊状的炉渣过多,会结成一体,像锅盖一样盖在熔化的钢水表面,造成钢水过热,加速对炉衬的浸蚀。
挂在炉壁上的炉渣冷却会掩盖炉衬的真实裂纹,导致因没有早期发现而造成钢水渗人或漏炉。
为了减少炉渣对炉衬的影响,可采用如下措施:①熔炼过程中勤扒渣,避免炉渣沉积在炉壁上;②不可同时使用含有SiO2和Al2O3的材料,回炉料应清理干净,生铁和废钢需经除锈处理;③在熔渣附着较多时,可加一些石灰石除渣;④熔化切屑时,应保持切屑干燥、清洁、无锈无杂质。
3.6 优化操作工艺在引用新材料和新技术的同时,还要对操作工艺进行优化,主要有以下几个方面:(1)合理热装铁水考虑到电炉的配碳量,供氧强度和脱碳速率对炉衬寿命的影响,在满足工艺要求的前提下,配加占装入量30~40%的铁水代替生铁,铁水随第一批料装入,由于相对减少了装料次数,同时铁水带入大量的物理·化学热,使冶炼时间相对缩短,从而减少了高温钢水对炉衬的浸蚀时间,提高了炉体寿命。
(2)采用泡沫渣操作氧化期造泡沫渣的工艺参数最佳值如下:碱度1.8—2.1时泡沫渣高度达250mm,此时当渣中FeO n为20%—25%时泡沫渣持续时间最长为40秒,合适的加发泡剂的温度为1530—1600℃。
根据某厂实际情况,确定在装第一批钢铁料时炉底垫入350—450Kg石灰,在熔池形成后,均匀加入C粉使其发泡。
在还原期,该厂造泡沫渣操作的经验值为:石灰20—27公斤/吨,萤石4—6公斤/吨,Si-C粉分两批,每次75Kg均匀撒开,发泡效果仍然良好。
如新建电炉时,采用碳氧枪喷吹造泡沫渣,效果更好。
采用泡沫渣操作后,降低了炉衬的侵蚀速度,同时由于渣层厚,埋弧送电,也减少了高温电弧对炉衬和炉盖的烧损,改善了耐火材料的工作环境,相应延长了耐火材料的使用寿命。
(3)合理装料首先严把配料关,将形状不规则的料进行切割,尽量减少装料次数,减少因多次旋转炉盖造成的热损失,配料时做到好次料重轻料合理搭配,料斗内布料应达到下密上疏松,中间高四周低,穿井快不搭桥。
同时,根据不同的炉役采用不同的装入量,避免因装入量不合理造成升温速度慢,炉衬侵蚀加剧。
(4)控制吹氧控制吹氧压力在0.4~0.6MPa,严禁大氧压吹氧,吹氧时以割料为主,不得压管子吹氧和深插钢水吹氧,确保氧末碳受控率,防止出现过氧化现象。
(5)温度控制冶炼全过程注意温度控制,确保氧化温度,扒渣温度的合理,避免出现后期升温,稳定出钢温度。
4 结束语通过采用新材料,新技术及改善操作工艺等措施后,电炉炉衬的寿命得以提高,同时也提高了炉子的作业率,提高了钢产量,降低了冶炼成本。
相信随着工人操作的熟练和对新工艺认识的不断深入,炉龄还有望进一步提高。
因此,要提高电炉的使用寿命,除了严格控制炉衬原材料质量外,尤其要注意平时的操作,合理配料,精心称量、打结、烘烤、烧结,细心加料熔化,做到勤观察、勤加料、勤扒渣,对于炉衬出现的裂纹和缺材,及时进行修补。