高炉热平衡计算
高炉炼铁计算

炼铁工艺计算2 物料平衡计算物料平衡计算是炼铁工艺计算中的重要组成部分,它是在配料计算的基础上进行的。
物料平衡计算包括鼓风量、煤气量以及物料收支总量等项内容的计算。
物料衡算有助于对高炉过程进行全面定量的分析和深入研究,并为热平衡计算做准备。
2.1 物料平衡计算的准备进行物料衡算应具备以下资料:各种物料的全分析成分,各种物料的实际用量;生铁成分、炉渣成分和数量;鼓风含氧量及鼓风湿度等。
2.2 物料平衡计算内容与方法2.2.1 鼓风量的计算对于炼铁设计,作物料平衡计算时,应首先计算每吨生铁的鼓风量。
每吨生铁的鼓风量用V b (m3,一般均为标准立方米)表示,它是由风口前燃烧碳量与鼓风含氧量计算的。
(1)风口前燃烧碳量C b的计算由碳素平衡图(图2-4)可知b O da dFe C C C C =-- (kg/t ,下同) (2-1)式中 C O ——氧化碳量,kg/t ;C da ——合金元素还原耗碳,kg/t ;C dFe ——铁的直接还原耗碳,kg/t 。
要计算风口前燃烧碳量b C ,则需先计算式中其他各项碳量,它们的计算是1)氧化碳量O C 计算4O f C CH C C C C =--[]410K M CH K C M C C C =⨯+⨯-- (2-2)式中,C C 为生铁渗碳量,由生铁成分计算;4CH C 为生成CH 4碳量,按燃料带入碳量f C 的0.5% ~ 1.2%取值计算;在作炼铁设计时,选定的焦比K 是参加炉内冶炼过程的实际数值,进入炉尘的碳量不包括在内。
2)合金元素还原耗碳da C 的计算()[][][][][])(375.0273.0882.55677.9182.2571.832/)(1244/12102/60][48/24][62/60][55/12][28/24][1022S U CO V Ti P Mn Si S U CO V Ti P Mn Si C da ⨯⨯+⨯⨯Φ⨯+++++=⨯⨯+⨯⨯Φ⨯+⨯+⨯+⨯+⨯+⨯⨯=ΦΦαα式中 []Si ,[]Mn ,[]P ,[]Ti ,[]V ——生铁中相应元素含量,%;Φ ——每吨生铁的石灰石用量,kg ;2CO φ——石灰石中CO 2含量;α——石灰石在高温区分解率,通常取α = 0.5;U —— 每吨生铁的渣量,kg ;()S ——渣中硫含量。
高炉炼铁热过程热平衡计算过程
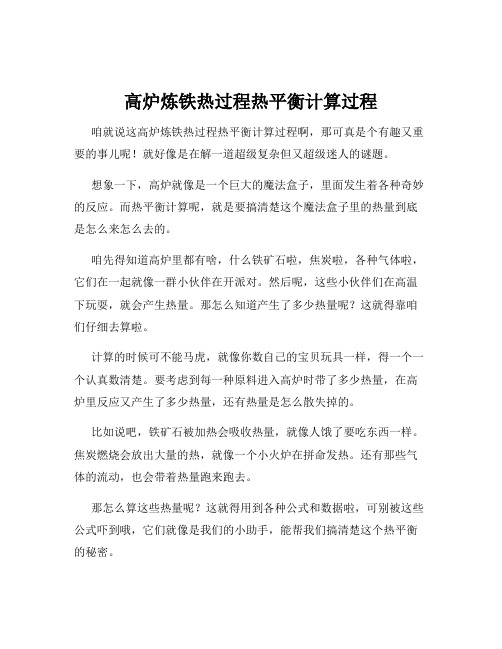
高炉炼铁热过程热平衡计算过程咱就说这高炉炼铁热过程热平衡计算过程啊,那可真是个有趣又重要的事儿呢!就好像是在解一道超级复杂但又超级迷人的谜题。
想象一下,高炉就像是一个巨大的魔法盒子,里面发生着各种奇妙的反应。
而热平衡计算呢,就是要搞清楚这个魔法盒子里的热量到底是怎么来怎么去的。
咱先得知道高炉里都有啥,什么铁矿石啦,焦炭啦,各种气体啦,它们在一起就像一群小伙伴在开派对。
然后呢,这些小伙伴们在高温下玩耍,就会产生热量。
那怎么知道产生了多少热量呢?这就得靠咱们仔细去算啦。
计算的时候可不能马虎,就像你数自己的宝贝玩具一样,得一个一个认真数清楚。
要考虑到每一种原料进入高炉时带了多少热量,在高炉里反应又产生了多少热量,还有热量是怎么散失掉的。
比如说吧,铁矿石被加热会吸收热量,就像人饿了要吃东西一样。
焦炭燃烧会放出大量的热,就像一个小火炉在拼命发热。
还有那些气体的流动,也会带着热量跑来跑去。
那怎么算这些热量呢?这就得用到各种公式和数据啦,可别被这些公式吓到哦,它们就像是我们的小助手,能帮我们搞清楚这个热平衡的秘密。
在计算过程中,要特别注意细节,就像你拼图的时候不能放过任何一个小角落一样。
一个小小的数据错误,可能就会让整个计算结果都不对啦。
而且啊,这个热平衡计算可不是一次性就能搞定的,就像你搭积木,可能搭到一半发现不对,就得重新开始。
我们可能要反复计算,不断调整,才能找到最准确的答案。
这还没完呢,知道了热平衡,我们就能更好地控制高炉的运行啦。
可以根据计算结果来调整原料的比例呀,控制温度呀,让高炉这个魔法盒子运行得更顺畅。
总之,高炉炼铁热过程热平衡计算过程虽然有点复杂,但真的很有意思呀!它就像是一个神秘的宝藏,等着我们去挖掘,去发现其中的奥秘。
难道你不想去试试解开这个谜题吗?别犹豫啦,快来和我一起探索这个神奇的世界吧!。
高炉热风炉热平衡测定与计算方法

高炉热风炉热平衡测定与计算方法1 范围本标准规定了炼铁高炉热风炉热平衡测定与计算基准、测定准备、测定内容与方法、测定步骤及计算方法、测定报告。
本标准适用于高炉顶燃式、外燃式和内燃式热风炉热平衡测定与计算,其他类型热风炉热平衡测定与计算也可参考。
”2 规范性引用文件下列文件对于本文件的应用是必不可少的。
凡是注日期的引用文件,仅所注日期的版本适用于本文件。
凡是不注日期的引用文件,其最新版本(包括所有的修改单)适用于本文件。
GB/T 2587 用能设备能量平衡通则GB/T 2588 设备热效率计算通则GB/T 13338 工业燃料炉热平衡测定与计算基本规则3 术语和定义GB/T 2587界定的以及下列术语和定义适用于本文件。
3.1操作周期 operation cycle在高炉正常生产及热风炉工况稳定情况下,由热风炉本次燃烧期开始,至下次燃烧期开始为止的时间,包括燃烧期、送风期和换炉时间。
4 测定与计算基准4.1 基准温度采用环境温度,取热风炉周围1m处的空气温度。
4.2 燃料发热量采用实际燃料的低(位)发热量。
对于一般热风炉,采用湿煤气的低(位)发热量。
4.3 热平衡测定范围热风炉包括热风炉本体、热风管道、空气-煤气预热装置和烟道余热回收利用装置等,热平衡测定范围可分为:a)热风炉本体:即燃烧期由燃烧器至烟道阀,送风期由冷风阀至热风阀的热风炉的本体及其内部连接管路部分;b)热风炉:热风炉本体加外围热风管路部分;c)热风炉系统:除热风炉外,还包括助燃空气、煤气预热装置和烟道余热回收利用装置等部分。
4.4 测定时间和频次热平衡测定限定连续8h内完成,测定次数不能少于2次,每次包括热风炉的一个完整的操作周期,温度、压力和流量等测定参数在每个操作周期内测定4次~6次,然后取平均值。
4.5 计算单位以单位体积热风的热量为计算单位,即kJ.m-3。
5 测定准备5.1 热风炉设备概况及近期生产运行情况了解设备已经运行的时间和历程,熟悉热风炉及高炉等相关设备的结构、性能、操作、运行及生产工艺等情况,并按以下要求填写热风炉设备概况和近期生产运行情况:a) 热风炉设备概况:按附录A中表A.1填写;b) 近期生产运行情况:按附录A中表A.2填写被测热风炉前一个月平均生产参数。
4.4高炉能量利用计算

4.4.1
高炉能量利用计算
计算以冶炼1t生铁为基准。根据生铁成分、炉渣碱度和Fe、Mn及CaO的平衡, 分别求出铁矿石(锰矿石)及熔剂的需要量。这样便可按照它们的化学成分,分别求出其 带入炉内的各种化学组分含量,再根据各种元素在渣、铁、煤气中的分配率,便可求得 最终渣、铁成分。根据相图可初步了解这种炉渣的物理性能是否能满足要求。 为了编制物料平衡必须进行风量和煤气量的计算。 计算风量是根据碳平衡原理,首先计算出风口前被鼓风中的氧所燃烧的碳量(C风)
在X、Y平面上,线段AB及其投 影∆X(或x)和∆Y(或y),代表 一种特定类型的氧的迁移。相应 的氧的流量no与沿着x轴的煤气 中的碳量nc有关,也与沿着Y轴 的固体炉料中的铁量nFe有关。
线段AB的斜率:
4.4.2
高炉操作线图及其应用
由于x,y均为正值,所以斜率u亦为正值。斜率等于碳同铁的产物 量的比值,即nc/nFe,实际就是用c/Fe原于比表示的单位原于铁 的碳量消耗,也就是以比值(分子co/原子Fe)表示的单位原子铁的还 原气体消耗量。 可见,斜率的意义在实际上与焦比(或燃料比)是完全一致的。当原 料和冶炼条件一定时,焦比或c/Fe原子比是一个定值。由于u=c/ Fe原子比一定,故o/Fe与O/C原于比或Y与X呈直线关系。 当表示若干氧的迁移过程时所有的线段都具有同一斜率u,而且可 按一定顺序在斜率为u的同一条直线AE上互相衔接起来,就构成了操 作线(图4—12),由于是以原子比为计量单位,所以操作线AE是一条 直线,其斜率u=c/Fe原子比。实际代表了焦比或燃料比。
4.4.1
高炉能量利用计算
4.4.1
高炉能量利用计算
由热平衡计算可得高炉热量利用系数(Kr):
此值一般为80%-85%,个别高达90%。上例中:
高炉煤气锅炉的热平衡计算
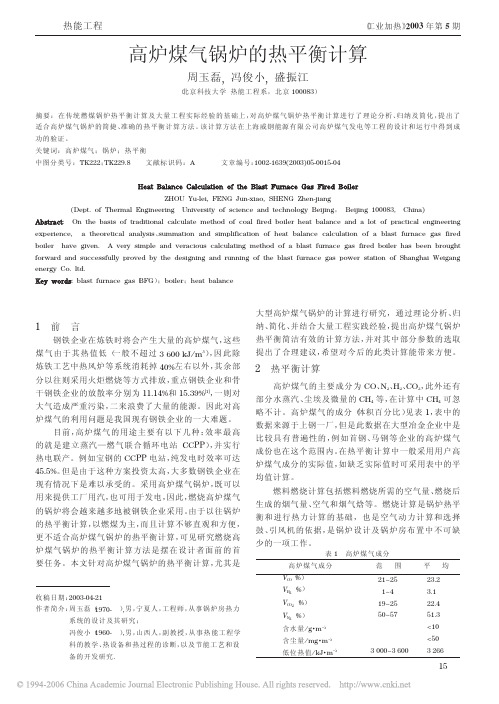
式中: AK4 为排烟的焓, %C ( 01; AJ%& 为进入锅炉的冷空气的 焓, %C ( 01; !K4 为排烟处的过量空气系数。
"9
热能工程
排烟热损失的大小取决于排烟的焓值,即主要决 定于排烟温度和烟气容积。排烟热损失是锅炉各项热 损失较大的一项, 一般为 !"#$%"。排烟温度 !&’ 每增加 故 !&’ 应尽量降低。一般大、 中 $%#$! (, )% 约增加 $" , 型锅炉的排烟温度为 $$*#$+* (。 炉膛出口过量空气系 数 "$,以及沿烟气流程各处烟道的漏风使 )% 增大的原 因,一是增大了排烟容积,二是漏风也使排烟温度升 高。因为漏入烟道的冷空气使烟温降低, 使漏风点以后 所有受热面的传热量都减少, 故使 !&’ 升高。
空气和烟气的焓是表示每立方米燃料所需理论空 气量或生成的烟气量在等压下从 & @ 加热到某一温度 需要的热量。
!)#锅炉的热效率
锅 炉 热 效 率 $<J 是 指 锅 炉 有 效 利 用 的 热 量 占 燃 烧 带入锅炉热量的百分数
!"#理论空气焓 AB& 的计算
$<J’H"’"&&>!H).H1.H7#
$%&’" ( )"!&*+,-.&*+/)#
!)# 实际空气量 $%
01 ( 01 01 ( 01
( ") ( ))
$%’!$%&
式中: ! 为过量空气系数。
"A%’!!>"#A%&
& 4
%C ( 01
高炉常用计算公式

炼铁用计算公式1、根据焦炭负荷求焦比焦比=1000/(负荷×综合品位)=矿批/(负荷×理论焦比)2有效容积利用系数=每昼夜生铁产量/高炉有有效容积3焦比=每昼夜消耗的湿焦量×(1-水分)/每昼夜的生铁产量4理论出铁量=(矿批×综合焦比)/0.945=矿批×综合品位×1.06不考虑进去渣中的铁量因为焦炭也带入部分铁5富氧率=(0.99-0.21)×富氧量/60×风量=0.013×富氧量/风量6煤比=每昼夜消耗的煤量/每昼夜的生铁含量7综合焦比=焦比+煤比×0.88综合燃料比=焦比+煤比+小块焦比9冶炼强度=每昼夜消耗的干焦量/高炉有效容积10矿比=每昼夜加入的矿的总量/每昼夜的出铁量11风速=风量(1-漏风率)/风口总面积漏风率20%12冶炼周期=(V有-V炉缸内风口以下的体积)/(V球+V烧+V矿)×88%=719.78/(V球+V烧+V矿)×88%13综合品位=(m烧×烧结品位+m球×球品位+m矿×矿品位)/每昼夜加入的矿的总量14安全容铁量=0.6×ρ铁×1/4πd2hh取风口中心线到铁口中线间高度的一半15圆台表面积=π/2(D+d)体积=π/12×h×(D2+d2+Dd)16正方角锥台表面积S=a2+b2+4(a+b/2)hV=h/3(a2+b2+ab)=h/3(S1+S2+√S1S)17、圆锥侧面积M=πrl=πr√r2+h2体积V=1/3πr2h18、球S=4πr2=πd2V=4/3πr3=π/6d319、风口前燃烧1kg碳素所需风量(不富氧时)V风=22.4/24×1/(0.21+0.29f)f为鼓风湿度20、吨焦耗风量V风=0.933/(0.21+0.29f)×1000×85%f为鼓风湿度85%为焦炭含碳量21、鼓风动能(1)E=(764I2-3010I+3350)dE-鼓风动能I-冶炼强度(2)E=1/2mv2=1/2×Q×r风/(60gn)v风实2Q-风量r风-风的密度g=9.8n-风口数目22、石灰的有效容剂性CaO有效=CaO熔-SiO2×R23、洗炉墙时,渣中CaF2含量控制在2%-3%,洗炉缸时可掌控在5%左右,一般控制在4.5% 每批料萤石加入量X=P矿×TFe×Q×(CaF2)/([Fe]×N)P矿-矿批重TFe-综合品位[Fe]-生铁中含铁量Q-吨铁渣量(CaF2)-渣中CaF2含量N-萤石中CaF2含量24、风口前燃烧1kg碳素的炉缸煤气量V煤气=(1.21+0.79f)/(0.21+0.29f)×0.933×C风C风-风口前燃烧的碳素量,kg25、理论出渣量渣量批=QCaO批/CaO渣渣量批-每批炉料的理论渣量,tQCaO批-每批料带入的CaO量,tCaO渣-炉渣中CaO的含量,%25、喷吹煤粉热滞后时间t=V总/(V批×n)V总-H2参加反应区起点处平面(炉身温度1100℃~1200℃处)至风口平面间的容积,m3V批-每批料的体积,m3n-平均每小时的下料批数,批/h26、高炉某部位需要由冷却水带走的热量称为热负荷,单位表面积炉衬或炉壳的热负荷称为冷却强度Q=CM(t-t0)×103Q-热负荷kJ/hM-冷却水消耗量,t/hC-水的比热容,kJ/(kg.℃)t-冷却水出水温度℃t0-冷水进水温度,℃。
gsc的物料平衡和热平衡计算

gsc的物料平衡和热平衡计算GSC(高炉煤气干燥除尘系统)是一种用于高炉喷吹系统的煤气清洁设备,它的物料平衡和热平衡计算是非常重要的。
1. 物料平衡计算GSC中的物料平衡计算主要是指干燥、粉碎、输送和回收等过程中各种物料的量的计算。
其计算方法如下:(1)4种物料的流量计算GSC中的4种物料分别是煤气、煤粉、水分和粉尘。
它们的流量应分别进行计算,其中煤气和煤粉的计算方法为:煤气和煤粉流量 =煤气和煤粉的质量控制 + 称量误差校正。
而水分和粉尘的计算方法为:水分和粉尘流量 = 流速测量器读数× 面积。
(2)各物料的贮存计算GSC中的各种物料都需要进行贮存,它们的贮存时间应进行计算。
计算公式为:贮存物料的总质量 = 流量× 时间。
(3)水分的蒸发计算GSC中的水分会随着煤气一起被带出去,需要进行计算。
计算公式为:水分的蒸发量 = 含水量× 煤气的质量。
2. 热平衡计算GSC中的热平衡计算主要是指煤气、煤粉和水分等热量的计算。
其方法如下:(1)煤气的热量计算煤气的热量可以通过其温度、压力和流量进行计算。
计算公式为:煤气的热量 = 煤气流量× 煤气的热值。
(2)煤粉的热量计算煤粉的热量可以通过其温度和质量进行计算。
计算公式为:煤粉的热量 = 煤粉的质量× 煤粉的比热× 煤粉的温度。
(3)水分的热量计算水分的热量可以通过其水份含量、温度和质量进行计算。
计算公式为:水分的热量 = 水分的质量× (水分的温度 - 煤气的温度)×水的比热。
综上所述,GSC的物料平衡和热平衡计算是其正常运行的基础和保障,这也说明物料和热量的平衡管理对于高炉的稳定和效率非常重要。
高炉物料平衡和热平衡的计算
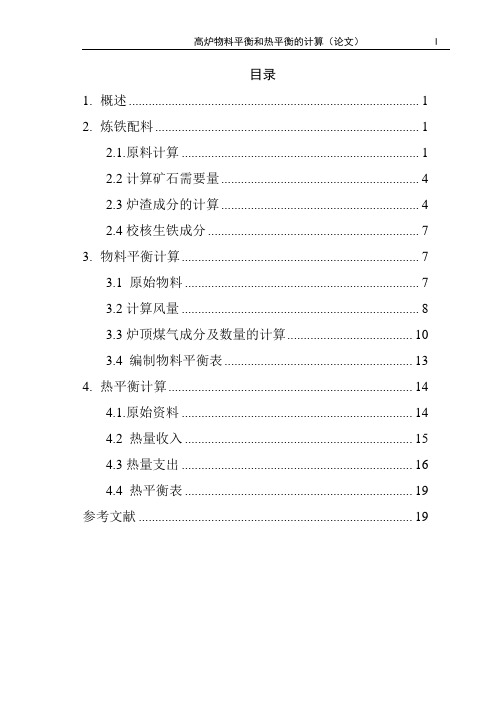
目录1.概述 (1)2.炼铁配料 (1)2.1.原料计算 (1)2.2计算矿石需要量 (4)2.3炉渣成分的计算 (4)2.4校核生铁成分 (7)3.物料平衡计算 (7)3.1 原始物料 (7)3.2计算风量 (8)3.3炉顶煤气成分及数量的计算 (10)3.4 编制物料平衡表 (13)4.热平衡计算 (14)4.1.原始资料 (14)4.2 热量收入 (15)4.3热量支出 (16)4.4 热平衡表 (19)参考文献 (19)高炉物料平衡和及平衡的计算1.概述在计算物料平衡和热平衡之前,首先必须确定主要工艺技术参数。
对于一种新的工业生产装置,应通过实验室研究、半工业性试验、以致于工业性试验等一系列研究来确定基本工艺技术参数。
高炉炼铁工艺已有200余年的历史,技术基本成熟,计算用基本工艺技术参数的确定,除特殊矿源应作冶炼基础研究外,一般情况下都是结合地区条件、地区高炉冶炼情况予以分析确定。
例如冶炼强度、焦比、有效容积利用系数等。
计算用的各种原料、燃料以及辅助材料等必须作工业全分析,而且将各种成分之总和换算成100%,元素含量和化合物含量要相吻合。
配料计算是高炉操作的重要依据,也是检查能量利用状况的计算基础。
配料计算的目的,在于根据已知的原料条件和冶炼要求来决定矿石和溶剂的用量,以配置合适的炉渣成分和获得合格的生铁。
通常以一吨生铁的原料用量为基础进行计算。
物料平衡是建立在物质不灭定律的基础上,以配料计算为依据编算的。
计算内容包括风量、煤气量、并列出收支平衡表。
物料平衡有助于检验设计的合理性,深入了解冶炼过程的物理化学反应,检查配料计算的正确性,校核高炉冷风流量,核定煤气成分和煤气数量,并能检查现场炉料称量的准确性,为热平衡及燃料消耗计算打基础。
热平衡计算的基础是能量守恒定律,即供应高炉的热量应等于各项热量的消耗;而依据是配料计算和物料平衡计算所得的有关数据。
热平衡计算采用差值法,即热量损失是以总的热量收入,减去各项热量消耗而得到的,即把热量损失作为平衡项,所以热平衡表面上没有误差,因为一切误差都集中掩盖在热损失之重。
- 1、下载文档前请自行甄别文档内容的完整性,平台不提供额外的编辑、内容补充、找答案等附加服务。
- 2、"仅部分预览"的文档,不可在线预览部分如存在完整性等问题,可反馈申请退款(可完整预览的文档不适用该条件!)。
- 3、如文档侵犯您的权益,请联系客服反馈,我们会尽快为您处理(人工客服工作时间:9:00-18:30)。
4 高炉热平衡计算4.1热平衡计算的目的热平衡计算的目的,是为了了解高炉热量供应和消耗的状况,掌握高炉内热能的利用情况,研究改善高炉热能利用和降低消耗的途径。
通过计算调查高炉冶炼过程中单位生铁的热量收入与热量支出,说明热量收支各项对高炉冶炼的影响,从而寻找降低热消耗与提高能量利用的途径,达到使高炉冶炼过程处于能耗最低和效率最高的最佳运行状态。
同时还可以绘制热平计算表研究高炉冶炼过程的基本方法[2]。
4.2热平衡计算方法热平衡计算的量论依据是能量守恒定律,即单位生铁投入的能量总和应等于中位个铁各项热消耗总和。
热平衡计算采用差值法,即热损失是以总的热量收入减去各项热量的消耗而得到的,即把热量损失作为平衡项,所以热平衡表面上没有误差,因为一切误差都集中掩盖在所有热损失之中。
根据计算的目的和分析的需要,热平衡可分为全炉热平衡与区域热平衡。
全炉热平衡是把整个高炉作为研究对象、计算它的各项热收入与支出,用来分析高炉冶炼过程令的能量利用情况。
而区域热平衡是把高炉的某一个区域作为研究对象,计算和分析这个区域内的能量利用情况。
虽然计算热平衡的部位与方法不向,但计算的目的都是为寻找降低能耗的途径和确定一定冶炼条件下的能耗指标。
理论上可以以把高炉内的任何一个部位当作区域热平衡的计算对象,但由于决定向炉冶炼能耗指标的主要因素存在于高炉下部的高温区。
因此,常用高炉下部属温区热平衡进行计算。
本例采用第一热平衡法计算进行热平衡计算。
第一种热平衡法,亦称热工法热平衡。
它是根据羔斯定则,不考虑炉内的实际反应过程.耍以物料最初与最终状态所具有的热力学参数为依据,确定高炉内的过程中所提供和消耗的热量。
它的热收入规定为焦炭和喷吹物的热值(即全部C完全燃烧成CO2和H2全部燃烧成H2O时放出的热量)、热风与炉料带入的物理热及少量成渣热。
而热支出为氧化物、硫化物和碳酸盐的分解热,喷吹燃料的分解热,水分分解热。
脱S反应耗热,渣铁和炉顶煤气热焓与热值,冷却水代走的热量和炉体散热损失等项。
这种热平衡计算法中,把焦炭和喷吹的燃料完全燃烧时放出的热量当作热收入。
而实际上高炉冶炼过程中有相当一部分C并没有完全燃烧,以CO的形态离开了高炉。
还有一部分进入生铁中和炉守中的C则完全权有燃烧,因此,必须把炉顶煤气与未燃烧C的热值当作热支出来处理。
另外,这种计算中,把炉内还原反向看成两步完成的,即硫化物的分解和还原剂的氧化,把还原剂氧化放热(即C 和CO 的燃烧)当作热收入项。
而把氧化物的分解吸热当作热支出项。
这就不符实际地夸大热量收入与支出从邑,热平衡总量中各项所占比例失真,难以通地热平衡总量与各项的比例来直观地判断炉内能量利用情况及各种因素对冶炼指标的影响。
同时,在热平衡计算中看不出炉内各热效应的作用,这也是此种热平彻计算法们缺点[2]。
4.3热平衡计算过程需要补充的原始条件:鼓风温度1100℃;炉顶温度200℃;入炉矿石温度为80℃。
4.3.1 热量收入(1)碳素氧化热由C 氧化1m³ 成CO 2放热1222.433410.66⨯=17898.43 KJ/m³由C 氧化成1m³ 的CO 放热1222.49797.11⨯=5250.50 KJ/m ³碳素氧化热=288.45×19878.43+(435.04-2.22)×5250.50=8006454.54 KJ(2)热风带入热1100 ℃时干空气的比热容为1.429kJ / m 3·℃ ,水蒸气的比热为1.753 kJ / m 3·℃,热风带入热=[(1238.89-18.58)×1.429+18.58×1.753]×1100=1954033.10 KJ(3)成渣热炉料中以碳酸盐形式存在的CaO 和MgO ,在高炉内生成钙铝酸盐时,1kg 放出热量1130.49 kJ混合矿的CaO=1666.82×0.0154×4456=32.67 KJ 成渣热=32.67×1130.49=36933.10 kJ (4)混合矿带入的物理热80 ℃时混合矿的比热容为1.0 KJ/Kg·℃混合矿带入的物理热=1666.82×1.0×80=133345.60 kJ (5)H 2氧化放热1m³ H 2氧化成H 2O 放热10806.65 KJ H 2氧化放热=51.81×10806.65=559892.53 kJ(6)CH 4生成热1Kg CH 4生成热=1677874.4=4865.29 KJCH 4的生成热=10.78×22.416×4865.29=37462.73 KJ冶炼1t 生铁总热为以上各热量的总和Q总收=8006454.54+1954033.10+36933.10+133345.60+559892.53+37462.7 3=10728121.6KJ4.3.2 热量支出(1) 氧化物分解与脱硫耗热1)铁氧化物分解热:设焦炭和煤粉中FeO 以硅酸铁形态存在,烧结矿中FeO 有20%以硅酸铁形态存在其余以Fe 3O 4,铁氧化物分解热由FeO 、Fe 3O 4和 Fe 2O 3三部分组成。
m (FeO )硅酸铁=1666.82×0.87×0.0718×0.2+360×0.0074+160×0.0045=24.21 kg去除进入渣中的FeO ,它也以硅酸铁形式存在,计3.68 kg 余下的m (FeO )硅酸铁=24.21-3.68=20.53 kgm (FeO )四氧化三铁=1666.82×0.0915-1666.82×0.87×0.0718×0.2 =152.51-20.82=131.69kgm (Fe 2O 3)四氧化三铁=131.69×72160=292.64 kgm (Fe 2O 3)自由=1666.82×0.7099-292.64=890.63 kg 依据1kg 铁氧化物分解热,即可算出总的分解热。
FeO 硅酸铁分解热=20.53×4075.21=83664.06KJ , (4075.2 KJ /kg FeO 硅酸铁) Fe 4O 3分解热=(131.69+292.64)×4799.98=2036775.51 KJ(4799.98 KJ /kg Fe 4O 3)Fe 2O 3分解热=890.63×5152.94=4589362.95 KJ ,(5152.94 KJ /kg Fe 2O 3) 铁氧化物分解总热=83664.06+2036775.51+4589362.95 =6709802.52KJ 2)锰氧化物分解热锰氧化物分解热包括MnO 2 分解为MnO 和MnO 分解为Mn 放出的热量; MnO 2→Mn 分解热=1666.82×0.0002×2629.44=876.56 KJMnO→Mn 分解热=0.7×7362.84=5153.98 KJ , (7362.84 KJ/KgMn) 锰氧化物分解总热=876.56+5152.98=6030.54KJ3)SiO 2分解热=3.5×30288.76=106010.65 KJ ,(30288.76 KJ/Kg Si ) 4)Ca 3(PO 4)2分解热=0.7×35756.98= 25029.88 KJ ,(35756.98KJ/KgMn ) 5)脱S 耗热由于CaO 脱硫耗热5401.23 KJ/ Kg·S ,MgO 脱硫耗热为8039.4 KJ/ Kg·S ,二者差别较大,故取其渣中成分比例(39.84:10.95≈4:1)来计算平均脱硫耗热。
1 Kg 硫的平均耗热=(5401.23*4/5+8039.04*1/5)=5928.79 KJ 脱S 耗热=3.64×5928.79=21580.8 KJ氧化物分解和脱硫总热为上述1)~5)项热耗之和,即Q 总=6709802.52+6030.54+106010.65+2\5029.88+21580.8=6868454.39 KJ (2)碳酸盐分解热由CaCO 3分解出1 Kg 的CO 2需热4044.64 KJ ,由M gCO 3分解出1 Kg CO 2需热2487.08 KJ ,混合矿石CO 2量=1666.82×0.0154=25.67 Kg 。
假定CaCO 3和M gCO 3是按比例分配的。
其中以CaCO 3分解的CO 2为25.67× 2.268.218.21 =20.12 Kg ;故以MgCO 3形式分解的CO 2量=25.67-20.12=5.55 Kg 。
碳酸盐分解总热=20.12×4044.64+5.55×2787.08=96846.45 KJ(3)水分分解热=18.58×10806.65=200787.56 KJ (10806.65 KJ/Kg.H 2O) (4)喷吹物分解热=160×1256.1=200976 kJ (1256.1 KJ/Kg 煤粉) (5)炉料游离水的蒸发热1Kg 水由20℃升温到100℃吸热334.94 KJ ,再变成100℃水蒸气吸热2261 KJ 总吸热为2595.96 KJ游离水蒸发热=360×0.048×2595.96=44858.19 KJ (6)生铁带走热表4.1各种生铁的热焓值[2]生铁热焓值 炼钢生铁 铸造生铁 锰铁 KJ /Kg1130.44-1172.36 1256.04-1297.91 1172.3-1214.17炼钢生铁焓值=1172.36 KJ/kg ,铁水带走热=1000×1172.36=1172360 KJ (7)炉渣带走热表4.2各种炉渣的热焓值[2]炉渣热焓值 炼钢铁渣 铸造铁渣 锰铁铁渣 KJ /Kg1716.59-1758.54 1884.06-2009.66 1842.192-1967.79炼钢铁渣焓值=1758.54 KJ/kg ,炉渣带走热=352.02×1758.54=619041.25 KJ (8)炉顶煤气带走热,炉顶温度为200℃时煤气各成分比热容见表4.3表4.3 200℃时炉顶煤气比热容[2]CO 2 CO N 2 H 2 CH 4 H 2O 1.787 1.313 1.313 1.302 1.82 1.159干煤气比热容=0.1701×1.787+(0.5470+0.2450)×1.313+0.0316×1.302+0.006×1.82=1.396 KJ/ m 3·℃干煤气带走热=1775.13×1.396×200=495616.29 KJ水蒸气带走热=60.17×1822.4×1.519×(200-100)=11374.01 KJ炉尘带走的热=8.87×0.8374*200=1485.54 KJ(炉尘比热容0.8374 KJ/Kg·℃)煤气带走总热=495616.29+11374.01+1485.54 =508475.85 KJ 前8项总和6868454.39+96846.45+200787.56+200976+44858.19+1172360+619041.25+508475.85=9711799.69KJ(9)外部热损失=10728121.6-9711799.69=1016321.91 KJ (包括散热和冷却水带走热)根据热收入与热支出数值列表于4.44.3.3 热平衡指标计算(1)碳素热能利用系数K c%100CO CO CO K 22⨯=所放出的热量燃烧生成除进入生铁外的碳全部放出的热量)和生成碳的氧化热(包括燃烧c=%18.5517.434334218006454.54=⨯ (2)热量有效利用系数KK t =(高炉总热量收入-煤气带走热-外部热损失)%=(100-5.77-9.47)%=84.76%K t =高炉总热量收入外部热损失)(煤气带走热—高炉总热量收入+*100%=10728121.61016321.91508475.8510728121.6)(—+=85.79%从上述指标可以看出,K c 值一般在50%~60%之间,个别可高达65%。