轴承套实验报告
轴承实验报告

轴承实验报告轴承实验报告引言在机械工程领域中,轴承是一种重要的机械元件,用于支撑旋转机械的轴。
它们承载着重要的机械负荷,同时也承受着摩擦和磨损。
为了确保轴承的可靠性和寿命,轴承的性能评估和实验测试是必不可少的。
本实验旨在通过测试不同类型的轴承,评估它们的性能和可靠性。
实验设计本次实验使用了两种常见的轴承类型:滚动轴承和滑动轴承。
滚动轴承是通过滚动元件(如钢球或滚子)来减小摩擦的,而滑动轴承则是通过润滑剂来减小摩擦。
实验过程中,我们将分别测试这两种轴承的摩擦系数、寿命和可靠性。
实验步骤1. 准备工作:清洁实验台面,确保实验环境清洁无尘。
2. 安装滚动轴承:将滚动轴承安装在实验设备上,并确保其能够自由旋转。
3. 测量摩擦系数:通过施加一定的力矩,使滚动轴承旋转,并使用力传感器测量所需的力。
根据所施加的力矩和测得的力,计算出滚动轴承的摩擦系数。
4. 测试寿命:通过连续施加一定的力矩和转速,观察滚动轴承的运行时间,直到其失效。
记录下滚动轴承的寿命。
5. 安装滑动轴承:将滑动轴承安装在实验设备上,并确保其能够自由旋转。
6. 测量摩擦系数:通过施加一定的力矩,使滑动轴承旋转,并使用力传感器测量所需的力。
根据所施加的力矩和测得的力,计算出滑动轴承的摩擦系数。
7. 测试寿命:通过连续施加一定的力矩和转速,观察滑动轴承的运行时间,直到其失效。
记录下滑动轴承的寿命。
实验结果与讨论通过实验,我们得到了滚动轴承和滑动轴承的摩擦系数和寿命数据。
根据数据分析,我们可以得出以下结论:1. 滚动轴承的摩擦系数较低,这是由于滚动元件的存在,可以减小接触面积和摩擦力。
2. 滚动轴承的寿命较长,这是由于滚动元件的分布,可以均匀分担负荷,减小磨损。
3. 滑动轴承的摩擦系数较高,这是由于润滑剂的存在,无法完全消除接触面积和摩擦力。
4. 滑动轴承的寿命较短,这是由于摩擦和磨损的积累,导致轴承失效。
结论通过本次实验,我们对滚动轴承和滑动轴承的性能和可靠性有了更深入的了解。
滑动轴承实验报告答案

滑动轴承实验报告答案滑动轴承实验报告答案引言:滑动轴承是一种常见的机械元件,广泛应用于各种机械设备中。
通过实验,我们可以了解滑动轴承的工作原理、性能特点以及影响其工作性能的因素。
本报告将对滑动轴承实验进行分析和总结,以期加深对滑动轴承的理解。
实验目的:1. 掌握滑动轴承的工作原理和结构特点;2. 了解滑动轴承的性能指标及其测试方法;3. 分析滑动轴承工作时的摩擦特性及其影响因素。
实验装置和方法:本次实验采用了滑动轴承实验装置,包括轴承座、轴承套、轴承外壳、轴承盖等组成部分。
实验方法是在轴承内壁涂抹润滑油,然后在轴上施加不同的负荷,通过测量轴承温度和摩擦力来分析轴承的工作情况。
实验结果与讨论:通过实验,我们得到了一系列数据,包括轴承温度和摩擦力的变化情况。
根据这些数据,我们可以得出以下结论:1. 轴承温度与负荷大小成正比:实验结果表明,随着负荷的增加,轴承温度也随之升高。
这是因为负荷增加会导致轴承内部的摩擦增加,从而产生更多的热量。
因此,在实际应用中,需要根据负荷大小来选择适当的润滑方式和材料,以保证轴承的正常工作温度。
2. 润滑油的选择对轴承性能有重要影响:实验中我们使用了不同种类的润滑油进行测试,发现不同润滑油的摩擦力和温度变化情况有所不同。
这说明润滑油的选择对轴承的工作性能有重要影响。
在实际应用中,需要根据轴承的工作条件和要求选择适当的润滑油,以提高轴承的工作效率和寿命。
3. 轴承摩擦力与轴承材料和表面处理方式有关:实验中我们使用了不同材料和表面处理方式的轴承进行测试,发现它们的摩擦力存在差异。
这是因为不同材料和表面处理方式会影响轴承与轴之间的接触面积和摩擦系数。
因此,在设计和选择轴承时,需要考虑材料和表面处理方式对轴承摩擦力的影响。
结论:通过本次实验,我们对滑动轴承的工作原理、性能特点以及影响因素有了更深入的了解。
我们发现轴承温度与负荷大小成正比,润滑油的选择对轴承性能有重要影响,轴承摩擦力与轴承材料和表面处理方式有关。
微型滚动轴承装配及质检实验报告

微型滚动轴承装配及质检实验报告微型滚动轴承是具有精度高、性能稳定、尺寸小、体积小,重量轻、重量不足或无轴承的微型零件,广泛用于传动机械中。
轴承根据结构可分为平面轴承、圆柱形轴承和滚子滚动轴承三种。
微型滚动轴承一般有四个轴,可以旋转180°角度进行旋转,这种结构的精度很高,并且可以方便地更换为圆柱形或球形。
在装配微型滚动轴承时如何保证其达到要求呢?我们通过对微型滚油润滑套及滚子的组装质量进行检测,确保其装配质量达标。
我们按照要求分别安装了小型球面滚子滚道式微型滚动轴承5套、圆锥形式微型滚油润滑套滚道式微型滚动轴承4套共计9只小球作为检验重点,同时装配人员根据检测结果对设备进行了保养、维修及检查。
实验方法:将10个小球放入1号圆孔内(距圆孔表面5 mm),然后将其放入3个直径为100~200 mm的圆柱形滚油润滑套内,分别用压板将之压紧或挤压即可。
1、选择合适的轴承和轴承座,在保证良好润滑的情况下,尽量减小摩擦阻力。
微型滚动轴承的磨损是不可避免的,在使用过程中其磨损会不断地积累,造成轴系精度降低、输出轴精度不高、运行阻力增大,影响使用寿命。
因此要选择合适的轴承座来支撑微型滚动轴承。
轴颈材质选用低合金精密工具钢(HRB400)制作而成,在保证高强度、耐磨性和承载能力的情况下,减小轴颈尺寸大小与内径的偏差,以提高机械产品的使用寿命。
此外还要考虑轴承座本身性能是否达标、配合是否可靠等,以免造成因配合不合适而发生轴系精度降低和运行阻力增大的现象。
对微型滚动轴承而言为了降低摩擦阻力可以选用有密封作用或防尘作用的轴承座来结构;还要根据轴系及载荷选择合适类型的零件(如滚针轴承、圆锥形轴承以及球面滚子轴承等)。
根据微型滚动轴承型号和负荷大小选择合适大小规格、质量较轻的轴来保证其承载能力及使用寿命;避免负荷增大而发生轴系及滚针轴承失效。
例如对于微型滚动轴承而言,应避免由于负荷增大而使其滚针轴承与滑动摩擦表面受损或是因轴系过热造成润滑不均匀引起故障。
中南大学——滚动轴承综合性能测试分析 实验报告
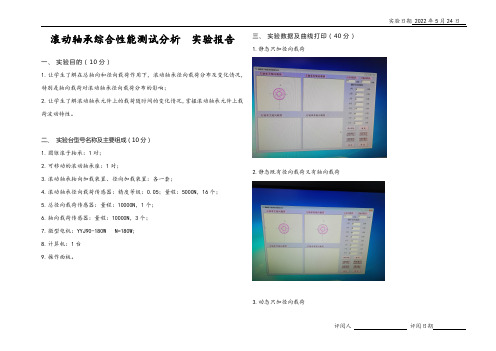
滚动轴承综合性能测试分析 实验报告一、 实验目的(10分)1. 让学生了解在总轴向和径向载荷作用下,滚动轴承径向载荷分布及变化情况,特别是轴向载荷对滚动轴承径向载荷分布的影响;2. 让学生了解滚动轴承元件上的载荷随时间的变化情况,掌握滚动轴承元件上载荷波动特性。
二、 实验台型号名称及主要组成(10分) 1. 圆锥滚子轴承:1对; 2. 可移动的滚动轴承座:1对;3. 滚动轴承轴向加载装置、径向加载装置:各一套;4. 滚动轴承径向载荷传感器:精度等级:0.05;量程:5000N ,16个;5. 总径向载荷传感器:量程:10000N ,1个;6. 轴向载荷传感器:量程:10000N ,3个;7. 微型电机:YYJ90-180W N=180W;8. 计算机:1台9. 操作面板。
三、 实验数据及曲线打印(40分) 1.静态只加径向载荷2.静态既有径向载荷又有轴向载荷3.动态只加径向载荷四、思考题(40分)1、圆锥滚子轴承受径向载荷后,本实验台为什么就可测出它受有轴向力?(10分提示:从书本内容和实验台相关内容两方面来回答)答:书本内容:圆锥滚子轴承受径向载荷后,由于存在接触角,轴承本身会产生一个轴向力实验台:由于实验台已知接触角,并且有轴向和径向载荷的力传感器,即可以通过受的径向载荷,来计算测出它所受的轴向力。
2、本实验台一对正装的圆锥滚子轴承支撑的轴系受外部轴向载荷后,左右圆锥滚子轴承承受的轴向载荷将怎样变化?(20分提示:先通过派生轴向力及外加轴向载荷的计算与分析,判定被“放松”或被“压紧”的轴承;然后确定被“放松”轴承的轴向力仅为其本身派生的轴向力,被“压紧”轴承的轴向力则为除去本身派生的轴向力后其余轴向力的代数和。
)答:(1)画出本实验台轴向力示意图(F S1表示左轴承内部轴向力,F S2表示右轴承内部轴向力,Fa 表示轴向外载荷方向向左)。
(2)F S2+Fa<F S1 ,则左 被放松(被放松,被压紧),右 被压紧(被放松,被压紧), 则Fa 1= F S1 (用计算式表达) ,则Fa 2= F S1-Fa (用计算式表达) 。
轴承应用技术实训报告

一、实训目的通过本次轴承应用技术实训,旨在提高学生对轴承应用技术的认识,掌握轴承的基本结构、性能、选用原则、安装调试和维护保养方法,培养学生在实际工程中的轴承应用能力。
二、实训内容1. 轴承基本知识(1)轴承的定义:轴承是用于支承轴、减少运动部件间的摩擦、承受载荷的机械元件。
(2)轴承的分类:根据承受载荷的方式,轴承可分为滚动轴承和滑动轴承;根据承受载荷的方向,轴承可分为向心轴承和推力轴承。
(3)轴承的结构:轴承主要由内圈、外圈、滚动体、保持架和密封件等组成。
2. 轴承性能(1)轴承的载荷能力:轴承的载荷能力是指轴承在承受载荷时所能承受的最大载荷。
(2)轴承的旋转精度:轴承的旋转精度是指轴承在旋转过程中,内外圈之间的相对位置变化程度。
(3)轴承的耐磨性:轴承的耐磨性是指轴承在使用过程中,抵抗磨损的能力。
3. 轴承选用原则(1)根据载荷性质选择轴承类型:如承受纯径向载荷,可选择向心轴承;承受轴向载荷,可选择推力轴承。
(2)根据载荷大小选择轴承型号:载荷越大,所选轴承型号越大。
(3)根据转速选择轴承型号:转速越高,所选轴承型号越大。
4. 轴承安装与调试(1)轴承安装:轴承安装时应注意以下几点:①保持轴承清洁;②轴承与轴配合良好;③轴承间隙合适。
(2)轴承调试:轴承调试时应注意以下几点:①轴承间隙调整;②轴承轴向定位;③轴承旋转精度检查。
5. 轴承维护保养(1)定期检查轴承的磨损情况,发现异常及时更换。
(2)定期给轴承加注润滑油,保持轴承润滑良好。
(3)保持轴承清洁,防止异物进入轴承。
(4)定期检查轴承的安装情况,确保轴承安装牢固。
三、实训过程1. 实训前准备:了解轴承的基本知识、性能、选用原则、安装调试和维护保养方法。
2. 实训操作:根据实训指导书,进行轴承的选用、安装、调试和维护保养。
(1)选用轴承:根据载荷性质、载荷大小和转速,选用合适的轴承型号。
(2)安装轴承:按照轴承安装步骤,将轴承安装在轴上。
浙师大 滚动轴承实验报告

如图 1 所示, 把派生轴向力的方向与外加轴向载荷 Fae 的方向一致的轴承标 为 2,另一端标为轴承 1。取轴和与其相配合的轴承内圈为分离体,如达到轴向 平衡时,应满足:
Fae Fd 2 Fd 1
如果按表 3 中的公式求得的 Fd1 和 Fd2 不满足上面的关系式时,就会出现下面 两种情况: 当 Fae Fd 2 Fd 1 时,则轴有向左窜动的趋势,相当于轴承 1 被“压紧” ,轴承 2 被“放松” ,但实际上轴必须处于平衡位置(即轴承座必然要通过轴承元件施加 一个附加的轴向力来阻止轴的窜动),所以被“压紧”的轴承 1 所受的总轴向力 Fa1 必须与 Fae Fd 2 相平衡,即 Fa1 Fae Fd 2 而被“放松”的轴承 2 只受其派生的轴向力 Fd2,即 (10)
Fa Fd Fr tan
(3)
图 5 轴承中受载滚动体数目的变化
(二)滚动轴承元件上载荷动态分析 通过电脑直接测量滚子对外圈的压力及变化情况,绘制滚动体内、外圈载荷 变化曲线。 轴承工作时, 各个元件上所受的载荷及产生的应力是随时间变化的。根据上 面的分析,当滚动体进入承载区后,所受载荷即由零逐渐增加到 FN2、FN1 直到 最大值 FN0, 然后再逐渐降低至 FNI, FN2 直至零(图 5)。 就滚动体上某一点而言, 它的载荷及应力是周期性地不稳定变化的(图 5a)。 滚动轴承工作时,可以是外圈固定、内圈转动,也可以是内圈固定、外圈转 动。对于固定套圈,处在承载区内的各接触点,按其所在位置的不同,将受到不 同的载荷。 处于 Fr 作用线上的点将受到最大的接触载荷。 对于每一个具体的点, 每当一个滚动体滚过时,便承受一次载荷,其大小是不变的,也就是承受稳定的 脉动循环载荷的作用,如图 6b 所示。载荷变动的频率快慢取决于滚动体中心的 圆周速度,当内圈固定外圈转动时,滚动体中心的运动速度较大,故作用在固定 套圈上的载荷的变化频率也较高。
加工套类零件实训报告
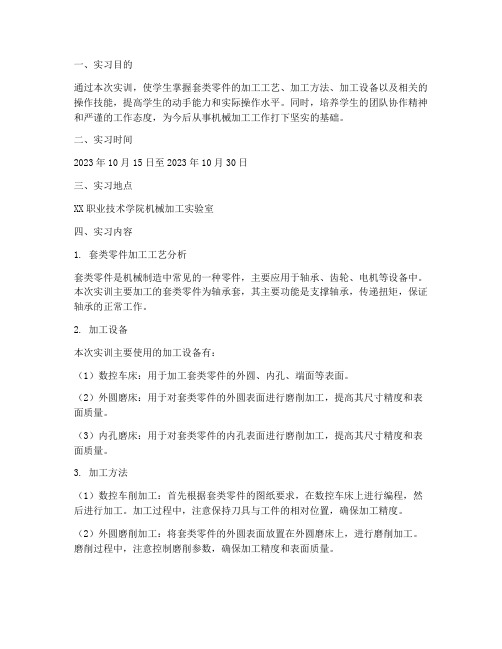
一、实习目的通过本次实训,使学生掌握套类零件的加工工艺、加工方法、加工设备以及相关的操作技能,提高学生的动手能力和实际操作水平。
同时,培养学生的团队协作精神和严谨的工作态度,为今后从事机械加工工作打下坚实的基础。
二、实习时间2023年10月15日至2023年10月30日三、实习地点XX职业技术学院机械加工实验室四、实习内容1. 套类零件加工工艺分析套类零件是机械制造中常见的一种零件,主要应用于轴承、齿轮、电机等设备中。
本次实训主要加工的套类零件为轴承套,其主要功能是支撑轴承,传递扭矩,保证轴承的正常工作。
2. 加工设备本次实训主要使用的加工设备有:(1)数控车床:用于加工套类零件的外圆、内孔、端面等表面。
(2)外圆磨床:用于对套类零件的外圆表面进行磨削加工,提高其尺寸精度和表面质量。
(3)内孔磨床:用于对套类零件的内孔表面进行磨削加工,提高其尺寸精度和表面质量。
3. 加工方法(1)数控车削加工:首先根据套类零件的图纸要求,在数控车床上进行编程,然后进行加工。
加工过程中,注意保持刀具与工件的相对位置,确保加工精度。
(2)外圆磨削加工:将套类零件的外圆表面放置在外圆磨床上,进行磨削加工。
磨削过程中,注意控制磨削参数,确保加工精度和表面质量。
(3)内孔磨削加工:将套类零件的内孔表面放置在内孔磨床上,进行磨削加工。
磨削过程中,注意控制磨削参数,确保加工精度和表面质量。
4. 加工过程(1)数控车削加工过程:1)装夹:将套类零件毛坯放置在数控车床上,采用三爪卡盘进行装夹。
2)编程:根据套类零件的图纸要求,编写数控车床加工程序。
3)加工:启动数控车床,按照编程指令进行加工。
(2)外圆磨削加工过程:1)装夹:将套类零件的外圆表面放置在外圆磨床上,采用支撑爪进行装夹。
2)磨削:启动外圆磨床,进行磨削加工。
(3)内孔磨削加工过程:1)装夹:将套类零件的内孔表面放置在内孔磨床上,采用支撑爪进行装夹。
2)磨削:启动内孔磨床,进行磨削加工。
轴承实训报告

一、实训目的通过本次轴承实训,旨在加深对轴承结构、原理及维修保养等方面的理解,提高动手实践能力,为今后从事相关行业打下坚实基础。
二、实训环境实训地点:XXX机械设备维修实训室实训设备:轴承、拆卸工具、安装工具、润滑油、检测仪器等三、实训原理轴承是一种用于支撑旋转轴的机械元件,具有减少摩擦、降低磨损、提高旋转精度等作用。
本次实训主要涉及轴承的拆卸、安装、检测和保养等基本操作。
四、实训过程1. 轴承拆卸(1)观察轴承外圈,确认拆卸工具是否适用。
(2)根据拆卸顺序,将轴承外圈与内圈分离。
(3)拆卸过程中,注意保持轴承的清洁,防止异物进入。
(4)使用专用工具拆卸轴承,避免损坏轴承。
2. 轴承安装(1)检查轴承是否损坏,确认安装位置。
(2)根据安装要求,将轴承安装在相应位置。
(3)安装过程中,注意轴承内外圈的平行度,避免偏斜。
(4)使用专用工具安装轴承,确保轴承紧固。
3. 轴承检测(1)使用检测仪器检测轴承内外圈的磨损情况。
(2)检测轴承间隙,确保轴承运转平稳。
(3)检测轴承润滑情况,判断是否需要添加润滑油。
4. 轴承保养(1)定期检查轴承润滑情况,确保轴承运转顺畅。
(2)根据实际情况,添加适量润滑油。
(3)定期检查轴承磨损情况,必要时进行更换。
五、实训结果通过本次实训,我掌握了以下技能:1. 轴承拆卸、安装、检测和保养的基本操作。
2. 了解轴承的结构、原理及维修保养要点。
3. 提高动手实践能力,为今后从事相关行业打下坚实基础。
六、实训总结1. 轴承是机械设备中的重要组成部分,掌握轴承的拆卸、安装、检测和保养等基本操作对于机械设备维护具有重要意义。
2. 在实训过程中,要注重安全操作,避免因操作不当造成人身伤害。
3. 提高动手实践能力,通过实际操作加深对理论知识的学习。
4. 加强团队合作,共同完成实训任务。
5. 积极参加实训,不断提高自己的综合素质。
本次轴承实训让我受益匪浅,我将以此为契机,继续努力学习,提高自己的专业技能。
- 1、下载文档前请自行甄别文档内容的完整性,平台不提供额外的编辑、内容补充、找答案等附加服务。
- 2、"仅部分预览"的文档,不可在线预览部分如存在完整性等问题,可反馈申请退款(可完整预览的文档不适用该条件!)。
- 3、如文档侵犯您的权益,请联系客服反馈,我们会尽快为您处理(人工客服工作时间:9:00-18:30)。
轴承套实验报告
由生产现场回馈的信息表明,轴承套在焊接后装配轴承时会出现轴承无法安装和轴承脱落等装配不良现象。
一、实验目的:
为检查轴承套焊接后所产生装配不良现象的原因,并制定消除这种装配不良现象方案。
图1.0轴承套外协图纸
二、实验步骤:
1.测量轴承套JGL-48-10-1焊接前内径尺寸。
2.焊接轴承套测试部件及制造镜面滚压机加工装。
3.测量轴承套JGL-48-10-1焊接后内径尺寸。
4.轴承套镜面滚压机加工。
5.测量轴承套JGL-48-10-1镜面滚压机加工后内径尺寸。
6.将轴承6205和轴承套测试部件进行试安装,评审装配效果。
三、实验过程:
1.测量轴承套JGL-48-10-1焊接前内径尺寸。
轴承套JGL-48-10-1焊前内径尺寸测量数据;
表格1
2.焊接轴承套测试部件及制造镜面滚压机加工装。
图2.0轴承套测试部件焊接图
图3.0 镜面机加工装 图4.0 轴承套测试部件实物图
3. 测量轴承套JGL -48-10-1焊接后内径尺寸。
轴承套JGL -48-10-1焊后内径尺寸测量数据;
表格2
4. 轴承套镜面滚压,机加工。
图5.0 镜面滚压加工现场情况
5. 测量轴承套JGL -48-10-1镜面滚压机加工后内径尺寸。
表格3 镜面滚压加工注意事项:
1. 加工时需用润滑油,淋浴滚刀;
2. 加工转速不易过高,参照350r/min ;
3. 滚刀纵向进给不宜太快;
4. 滚刀纵向加工到位时,保持15-20秒持续加工。
6.将轴承6205和轴承套测试部件进行试安装,评审装配效果。
图6.0 轴承套测试部件轴承装配情况
图7.0转轴与轴承装配效果 图8.0 转轴JGL -48-09
四、数据处理
1.对比表格1,表格2,均值一项数据;可以评判焊接前后轴承套JGL -45-10-1的变形量为∆=±0.1。
五、结论
1.轴承套JGL -48-10-1在焊接时,焊接处受热膨胀焊接层间温度短时间内集聚升高;使得轴承套JGL -48-10-1焊接处内径产生塑性变形。
2.轴承套JGL -48-10-1在焊接时内径产生的形变,而导致的装配不良;是可以通过对焊后轴承套JGL -48-10-1内径进行镜面滚压机加工,校正其内径变形量;从而消除五通管在焊接后装配轴承时,所产生的轴承无法安装及轴承脱落等装配不良现象。
3.基于测试验证结果是(无氧和路径):
a) 轴套焊接前间歇配合公差采用∅52+0.015+0.03,焊接变形后用镜面滚压进行滚压到
∅52+0.015+0.03;
b) 轴的加工工艺公差采用∅25−0.0050.02。
批准: 审核: 报告人:
轴承与轴承套测试部件装配效果良好, 且轴承易于安装。
轴承6205与转轴JLG -48-09 的装配效果良好,且装配同 心度良好;转轴可自由转动。