磷化膜的形成
磷化钝化膜形成原理
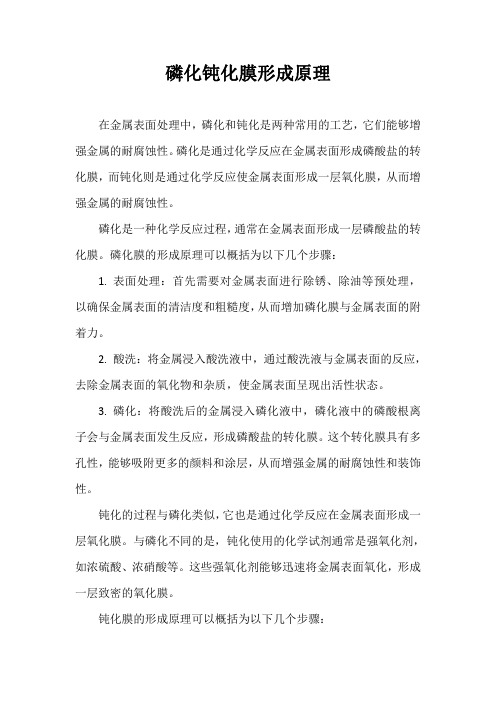
磷化钝化膜形成原理在金属表面处理中,磷化和钝化是两种常用的工艺,它们能够增强金属的耐腐蚀性。
磷化是通过化学反应在金属表面形成磷酸盐的转化膜,而钝化则是通过化学反应使金属表面形成一层氧化膜,从而增强金属的耐腐蚀性。
磷化是一种化学反应过程,通常在金属表面形成一层磷酸盐的转化膜。
磷化膜的形成原理可以概括为以下几个步骤:1.表面处理:首先需要对金属表面进行除锈、除油等预处理,以确保金属表面的清洁度和粗糙度,从而增加磷化膜与金属表面的附着力。
2.酸洗:将金属浸入酸洗液中,通过酸洗液与金属表面的反应,去除金属表面的氧化物和杂质,使金属表面呈现出活性状态。
3.磷化:将酸洗后的金属浸入磷化液中,磷化液中的磷酸根离子会与金属表面发生反应,形成磷酸盐的转化膜。
这个转化膜具有多孔性,能够吸附更多的颜料和涂层,从而增强金属的耐腐蚀性和装饰性。
钝化的过程与磷化类似,它也是通过化学反应在金属表面形成一层氧化膜。
与磷化不同的是,钝化使用的化学试剂通常是强氧化剂,如浓硫酸、浓硝酸等。
这些强氧化剂能够迅速将金属表面氧化,形成一层致密的氧化膜。
钝化膜的形成原理可以概括为以下几个步骤:1.表面处理:同样需要对金属表面进行除锈、除油等预处理,以提高钝化膜与金属表面的附着力。
2.酸洗:将金属浸入酸洗液中,去除金属表面的氧化物和杂质,使金属表面呈现出活性状态。
3.钝化:将酸洗后的金属浸入钝化液中,钝化液中的强氧化剂会迅速将金属表面氧化,形成一层致密的氧化膜。
这个氧化膜能够阻挡腐蚀介质对金属的侵蚀,从而提高金属的耐腐蚀性。
通过磷化和钝化处理,金属表面的耐腐蚀性能得到了显著提高。
同时,这两种处理方法还可以增强金属的装饰性能,使其具有更美观的外观。
在实际应用中,应根据不同的需求选择合适的处理方法。
总的来说,磷化、钝化都是通过化学反应在金属表面形成一层保护膜,从而提高金属的耐腐蚀性。
虽然它们的化学反应机理和所用试剂有所不同,但它们的表面处理和反应过程是相似的。
磷化成膜机理

磷化成膜机理1、化学转化过程所用的磷化液都是由磷酸、碱金属或重金属的磷酸二氢盐及氧化性促进剂组成的酸性溶液。
因此,整个磷化过程都包括含有基体金属的溶解反应、难溶磷酸盐结晶沉积的成膜过程及氧化性促进剂的去极化作用。
①基体金属的溶解磷化液的PH 值一般都在2~5.5之间,呈酸性。
因此当金属和此酸性溶液接触时,必然发生由局部阳极和局部阴极反应组成的金属溶解过程:局部阳极 Me Me 2++2e 局部阴极 2H ++2e H 2↑ ②成膜反应由于局部阴极区域H +被还原而消耗,酸度下降,使得在第一阶段形成的可溶性二价金属磷酸二氢盐离解成溶解度较小的磷酸一氢盐:Me (H 2PO 4)2 MeHPO 4+H 3PO 4只要PH 上升到一定程度,则主要离解成不溶性二价金属磷酸盐。
此离解则比较迅速:Me (H 2PO 4)2 MeHPO 4+4H 3PO 4同时 MeHPO 4 Me 3(PO 4)2+H 3PO 4难溶的Me 3(PO 4)2在金属表面的阴极区域沉积析出。
当整个阴极区域都被沉积物覆盖时,成膜反应结束,从而在金属表面形成完整的磷化膜覆盖。
由于成膜反应的可溶性二价金属磷酸二氢盐可以是金属溶解生成的,也可以是溶液中原有的配方组成。
除磷酸铁盐膜外,其他所有的磷化膜的成膜物质都是添加配方中的原料。
难溶性磷酸盐的溶积度如表:氧化性促进剂的去极化作用和对金属溶解的促进金属溶解时产生的氢气易吸附于阴极的金属表面,从而阻碍水解产生的二价金属磷酸盐在阴极区域的沉积,不能形成磷化膜。
水解产物则于溶液中析出成为渣,即浪费成膜原料,也使渣量大大增加。
这样在工艺方面将造成困难,对膜的性能也不能保证,因为孔隙率很大。
氧化剂的去极化作用是将还原形成的初生态氢氧化成水;2[H]+[O] H2O与去极化作用密切相关的是促进剂对金属溶解的促进。
它是通过促进剂对H2的氧化和沉积作用,导致阳极电流密度增加而提高溶解速率,即提高可溶性二价金属磷酸二氢盐的生成速率。
钢板的磷化
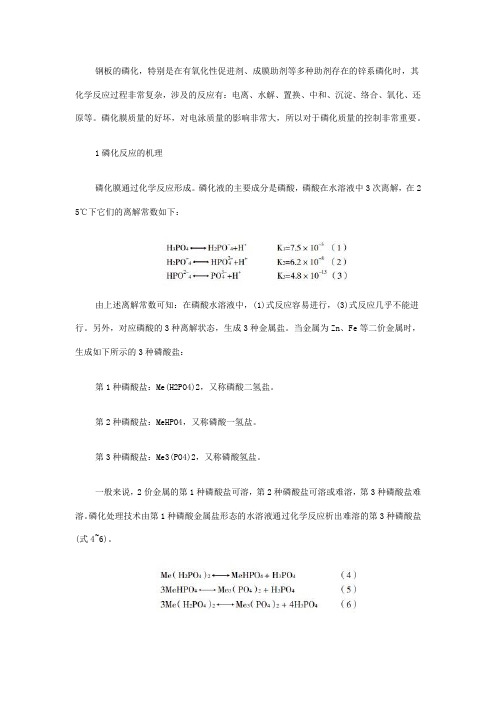
钢板的磷化,特别是在有氧化性促进剂、成膜助剂等多种助剂存在的锌系磷化时,其化学反应过程非常复杂,涉及的反应有:电离、水解、置换、中和、沉淀、络合、氧化、还原等。
磷化膜质量的好坏,对电泳质量的影响非常大,所以对于磷化质量的控制非常重要。
1磷化反应的机理磷化膜通过化学反应形成。
磷化液的主要成分是磷酸,磷酸在水溶液中3次离解,在2 5℃下它们的离解常数如下:由上述离解常数可知:在磷酸水溶液中,(1)式反应容易进行,(3)式反应几乎不能进行。
另外,对应磷酸的3种离解状态,生成3种金属盐。
当金属为Zn、Fe等二价金属时,生成如下所示的3种磷酸盐:第1种磷酸盐:Me(H2PO4)2,又称磷酸二氢盐。
第2种磷酸盐:MeHPO4,又称磷酸一氢盐。
第3种磷酸盐:Me3(PO4)2,又称磷酸氢盐。
一般来说,2价金属的第1种磷酸盐可溶,第2种磷酸盐可溶或难溶,第3种磷酸盐难溶。
磷化处理技术由第1种磷酸金属盐形态的水溶液通过化学反应析出难溶的第3种磷酸盐(式4~6)。
汽车涂装前的磷化处理以锌盐磷化处理为代表。
(7)式和(8)式所示的是生成锌盐磷化膜的平衡反应:(7)式反应在被处理物上进行,钢板界面上的Fe(H2PO4)2浓度增高。
将氧化促进剂亚硝酸盐添加到锌盐磷化液中后,(7)式中Fe(H2PO4)2就成为FePO4,H2变成H2O除去。
根据(7)式的反应,在磷化槽液内的钢板表面上,靠促进剂的作用,氢离子浓度下降,引发(9)式的反应:Fe的浓度高时就生成磷酸二锌铁:2磷化的加速反应2.1磷化反应的加速(1)磷化反应是一个吸热过程,加热有利于反应的进行。
(2)加入氧化性物质(如NO2-、H2O2等)作为去极化剂,其作用是使晶核能够暴露,而不被氢气覆盖;在有氧化性促进剂时,氢原子直接被氧化成水,不影响离子的扩散,形成磷化膜。
2.2磷化膜沉积过程的加速实现反应加速的方法一般是引入结晶晶核。
磷化前的钛盐表面调整,在工件表面形成晶核活性中心,使磷化结晶能够沿晶核生长。
关于磷化工序的浅解

关于钢丝〔盘条〕磷化的浅解1.0磷化的目的和基本原理:1.1钢丝表面涂着物的特性:钢丝的加工和使用,要求材料在保存或加工过程和加工结束后的一定时间段内,材料表面不产生锈蚀或表面涂着物不产生潮解;在加工过程中得到低的摩擦系数。
钢丝因再加工和使用的需要,钢丝表面选择的涂着物有:涂石灰、涂硼砂或其类似物、电镀金属、磷化等。
电镀金属仅是在一些特殊产品的要求而使用。
涂石灰是早期钢丝生产工艺中广泛使用的方式,它成本低;但是这种方式在再加工时产生粉尘有害健康且不适应高速拉拔。
涂硼砂是适用于高速拉拔且成本低廉的方式。
虽然它易于潮解,但对涂后的中间品有适当的管理措施是可以避免的。
且特别在涂后直接拉拔的工艺是被广泛选用。
目前国外虽开始限制使用硼砂产品,因此出现其类似物。
但是这种涂层只适用于中间产品的表面而不适用于最终产品的表面;因为它抗锈蚀能力差,但强于石灰涂层。
磷化的涂着层具有一定的抗锈蚀能力,和具有一定的电抗;在后加工过程中得到低的摩擦系数。
好的磷化膜本身具有很好的塑性,在变形中能够很好地保持其连续性;同时,它不仅能和皂——硬脂酸钠,发生反应产生更有利于润滑的金属皂类,而且其表面又可以很好地附着皂液和润滑剂;这有利减小变形摩擦因数、减少模具磨损。
1.2 磷化膜的形成和特性:1.2.1 磷化技术的机理:磷化处理过程是化学与电化学反应过程,主要是由下述步骤组成:a.酸的浸蚀使基体金属表面 H+ 离子浓度降低。
当金属表面与酸性磷化液接触时,钢丝表面被溶解,使金属与溶液中酸反应产生氢,从而使界面的 PH 值上升,以致磷酸锌〔以锌系为例〕沉积于钢丝表面。
由于亚铁在溶液中的存在,不论因酸后的带入还是在槽内反应产生,磷酸铁锌也同时沉积于钢丝表面。
其总反应方程如下:5Zn(H2P04)2+Fe(H2P04)2+8H20--+ Zn 3(P04)2。
4H20+ Zn 2Fe(P04)2。
4H20+ 8 H3P04磷酸盐沉淀的副反应将形成磷化沉渣,即亚铁离子被氧化后同磷酸反应生成磷酸铁在溶液中沉淀:Fe³¯+ P04³¯==FeP04但是在这钢丝表面的二种磷膜沉积物有不同的特性;称前者Zn 3(P04)2。
磷化膜主要成分

磷化膜主要成分
磷化膜是一种常见的防腐涂层,主要成分是磷化物。
磷化物是由磷和金属元素组成的化合物,可以在金属表面形成一层致密的磷化膜,起到防腐、耐磨、导电等作用。
磷化膜的形成是通过磷化反应实现的。
磷化反应是将金属表面暴露在含磷化合物的气氛中,使磷元素与金属表面发生反应,生成磷化物。
磷化反应可以通过多种方法实现,如热浸磷化、气相磷化、电化学磷化等。
磷化膜的主要成分是磷化物,但其它元素的存在也会对磷化膜的性能产生影响。
例如,镁、锌等元素可以促进磷化反应的进行,提高磷化膜的质量和厚度;铜、银等元素可以提高磷化膜的导电性能;而铁、铬等元素则会降低磷化膜的质量和耐腐蚀性能。
磷化膜的性能与其成分和结构密切相关。
一般来说,磷化膜的成分越纯,结构越致密,其防腐、耐磨、导电等性能就越好。
此外,磷化膜的厚度也是影响其性能的重要因素。
磷化膜的厚度越大,其防腐、耐磨性能就越好,但过厚的磷化膜也会影响金属件的尺寸精度和表面质量。
总之,磷化膜的主要成分是磷化物,但其它元素的存在也会对其性能产生影响。
磷化膜的性能与其成分、结构和厚度密切相关,因此在实际应用中需要根据具体要求选择合适的磷化方法和工艺参数,以获得最佳的防腐、耐磨、导电等性能。
磷化成膜机理
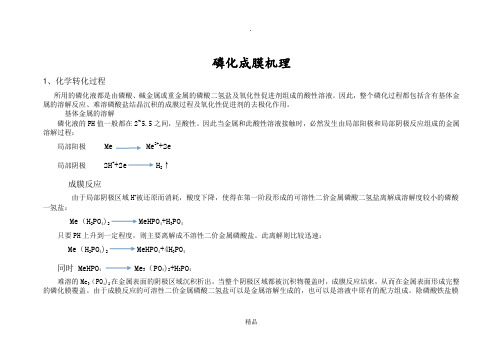
精品磷化成膜机理1、化学转化过程所用的磷化液都是由磷酸、碱金属或重金属的磷酸二氢盐及氧化性促进剂组成的酸性溶液。
因此,整个磷化过程都包括含有基体金属的溶解反应、难溶磷酸盐结晶沉积的成膜过程及氧化性促进剂的去极化作用。
基体金属的溶解磷化液的PH 值一般都在2~5.5之间,呈酸性。
因此当金属和此酸性溶液接触时,必然发生由局部阳极和局部阴极反应组成的金属溶解过程:局部阳极 Me Me 2++2e 局部阴极 2H ++2e H 2↑成膜反应由于局部阴极区域H +被还原而消耗,酸度下降,使得在第一阶段形成的可溶性二价金属磷酸二氢盐离解成溶解度较小的磷酸一氢盐:Me (H 2PO 4)2 MeHPO 4+H 3PO 4只要PH 上升到一定程度,则主要离解成不溶性二价金属磷酸盐。
此离解则比较迅速: Me (H 2PO 4)2 MeHPO 4+4H 3PO 4同时 MeHPO 4 Me 3(PO 4)2+H 3PO 4难溶的Me 3(PO 4)2在金属表面的阴极区域沉积析出。
当整个阴极区域都被沉积物覆盖时,成膜反应结束,从而在金属表面形成完整的磷化膜覆盖。
由于成膜反应的可溶性二价金属磷酸二氢盐可以是金属溶解生成的,也可以是溶液中原有的配方组成。
除磷酸铁盐膜外,其他所有的磷化膜的成膜物质都是添加配方中的原料。
难溶性磷酸盐的溶积度如表:精品精品氧化性促进剂的去极化作用和对金属溶解的促进金属溶解时产生的氢气易吸附于阴极的金属表面,从而阻碍水解产生的二价金属磷酸盐在阴极区域的沉积,不能形成磷化膜。
水解产物则于溶液中析出成为渣,即浪费成膜原料,也使渣量大大增加。
这样在工艺方面将造成困难,对膜的性能也不能保证,因为孔隙率很大。
氧化剂的去极化作用是将还原形成的初生态氢氧化成水;2[H]+[O] H 2O与去极化作用密切相关的是促进剂对金属溶解的促进。
它是通过促进剂对H 2的氧化和沉积作用,导致阳极电流密度增加而提高溶解速率,即提高可溶性二价金属磷酸二氢盐的生成速率。
钢铁锌系磷化常见问题及处理方法
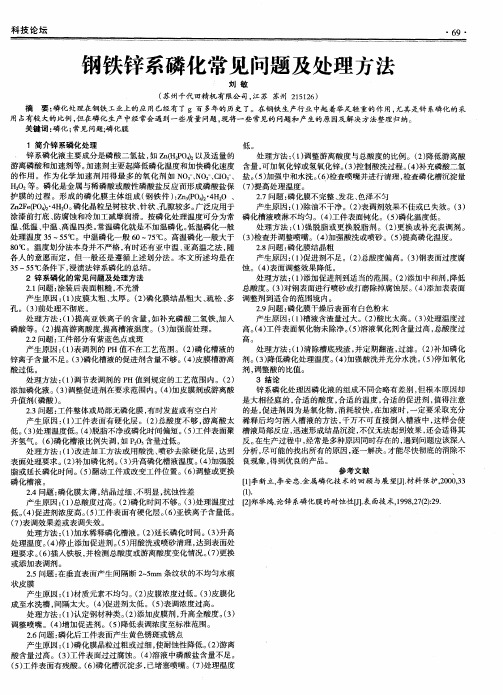
・ 6 9・
钢铁锌系磷化常见问题及处理方法
刘 敏
( 苏州千代田精机 有限公 司, 江 苏 苏州 2 1 5 1 2 6 )
摘 要: 磷 化处理在钢铁 工业上的应 用已经有 了 g百 多年 的历 史了。在钢铁 生产行业 中起 着举足轻重的作用 , 尤其是锌 系磷, I t  ̄ g j 采 用 占有较 大的比例 , 但在磷化 生产 中经 常会遇到一些质量 问题 , 现将一些常见的 问题 和产 生的原 因及解决方法整理 归纳。 关键词 : z a化 ; 常见 问题 ; 磷化膜
1简介锌系磷化 处理 低。 锌 系磷化液 主要 成分是磷 酸二氢盐 , 如 Z n ( H2 P 0 4 ) 以及适量 的 处理方法 : ( 1 ) 调整游离酸度与总酸度的 比例 。( 2 ) 降低游 离酸 游离磷酸和加速剂等 。 加 速剂 主要起 降低磷化温度和加快磷化速度 含量 , 可加氧化锌或氢氧化锌 。 ( 3 ) 控制 酸洗过程 。 ( 4 ) 补充磷酸二氢 的作 用 。作 为化学 加速剂 用得 最多 的氧化 剂如 N O  ̄ 、 N O  ̄ 、 C 1 0  ̄ 、 盐。 ( 5 ) 加强中和水洗 。 ( 6 ) 检查喷嘴并进行清理 , 检查磷化槽沉淀量 H 0 等 。磷 化是金属与稀磷 酸或酸性磷酸盐反应 而形成磷酸盐保 ( 7 ) 提高处理温度。 护膜 的过程 。形成 的磷化 膜主体 组成 ( 钢铁 件 ) : z n ( P 0 4 ) : ・ 4 H : 0 、 2 . 7问题 : 磷化膜不完整 、 发花 、 色泽不匀 Z n 2 F e ( P 0 4 ) 2 " 4 H 0。 磷化晶粒呈树枝状 、 针状 、 孔 隙较多 。 广泛应 用于 产生原 因: ( 1 ) 除油不干净。( 2 ) 表调剂效果不佳或 已失效 。( 3 ) 涂漆前打底 、 防腐蚀 和冷加工减摩润滑 。按磷化处理温度可分 为常 磷化槽液喷淋不均匀。( 4 ) 工件表面钝 化。( 5 ) 磷化 温度低 。 温、 低温、 中温 、 高温 四类 。 常温磷化就是不加温磷化。 低温磷化一般 处理 方法 : ( 1 ) 强 脱脂或更 换脱脂剂 。( 2 ) 更换 或补充表调 剂 。 处理温度 3 5 ~5 5 ℃。中温磷化一般 6 0 —7 5 %。高温磷化一般大 于 ( 3 ) 检查并 调整 喷嘴 。( 4 ) 加强 酸洗或喷砂 。( 5 ) 提高磷化温度 。 8 0  ̄ C 。温度划分法本身并不严格 , 有时还有亚 中温 、 亚高温之法 , 随 2 . 8问题 : 磷化膜结晶粗 各人 的意愿 而定 ,但 一般还是遵循上述 划分法 。本文所 述均是在 产生原 因: ( 1 ) 促进剂不 足。( 2 ) 总酸度偏 高。( 3 ) 钢表面过度腐 3 5~5 5  ̄ C 条件下 , 浸渍法锌系磷化的总结。 蚀 。( 4 ) 表 面调整效果降低。 2锌 系磷化 的常见 问题及处理方法 处理方法 : ( 1 ) 添加促进 剂到适 当的范 围。( 2 ) 添加 中和剂 , 降低 2 . 1问题 : 涂装后表面粗糙 , 不光滑 总酸度 。( 3 ) 对 钢表 面进行喷砂或打磨除掉腐蚀层 。( 4 ) 添加表表 面 产生原 因 : ( 1 ) 皮膜太粗 、 太厚 。( 2 ) 磷化膜结 晶粗大 、 疏松 、 多 调整剂到适合的范围境内。 孔 。( 3 ) 前处理不彻底 。 2 . 9问题 : 磷化膜干燥后表 面有 白色粉末 处理方 法 : ( 1 ) 提 高亚铁离 子的含量 , 如补 充磷酸二 氢铁, 加入 产生原因 : ( 1 ) 槽液含渣量过大 。( 2 ) 酸 比太高 。( 3 ) 处理温 度过 磷酸等 。( 2 ) 提 高游离酸度, 提高槽液温度 。( 3 ) 加强前处理 。 高。 ( 4 ) 工件 表面氧化物未除净 。 ( 5 ) 溶液氧化剂含量过 高, 总酸度过 2 . 2问题 : 工件部分有紫蓝 色点或斑 高。 处理方法 : ( 1 ) 清除槽底残渣 , 并定期翻渣 , 过滤。( 2 ) 补加磷化 产生原 因 : ( 1 ) 表调剂 的 P H值不 在工 艺范 围。( 2 ) 磷化槽液 的 锌离子含量不足。( 3 ) 磷化槽液 的促进剂含量不够 。( 4 ) 皮膜槽游离 剂 。 ( 3 ) 降低磷化处理 温度 。 ( 4 ) 加强酸洗并充分水洗 。 ( 5 ) 停加 氧化 酸过低 。 剂, 调整酸 的比值 。 3 结 论 处理方法 : ( 1 ) 调节表 调剂 的 P H值 到规定 的工艺范 围内。( 2 ) 锌 系磷化处理 因磷化液 的组 成不 同会 略有 差别 , 但根本原 因却 添加磷化液 。( 3 ) 调整促进剂在要求范 围内。( 4 ) 加皮膜剂 或游离酸 是大相 径庭 的 , 合 适的酸度 , 合适 的温度 , 合适 的促进剂 , 值得 注意 升值剂 ( 磷 酸) 。 的是 , 促进剂 因为是氧化物 , 消耗较快 , 在加液 时, 一定要采取充分 2 _ 3问题 : 工件整体或局部无磷化膜 , 有时发 蓝或有空 白片 产生原 因 : ( 1 ) 工件表 面有硬化层 。( 2 ) 总酸度 不够 , 游离酸太 稀 释后 均匀洒人槽液 的方法 , 千 万不可直接倒人槽液 中 , 这样会使 迅速形成结晶沉淀 , 不仅无法起到效果 , 还会适得其 低。 ( 3 ) 处理温度低。( 4 ) 脱脂不净或磷化时 间偏短。( 5 ) 工件表 面聚 槽液局部反应 , 反。 在生产过程中 , 经常是多种原因同时存在 的, 遇到 问题应该深入 齐氢气 。( 6 ) 磷 化槽 液比例失调 , 如P 2 0 含量过低 。 尽可能的找出所有 的原 因, 逐一解决 。 才能尽快彻底 的消除不 处理方 法 : ( 1 ) 改进加 工方法或用酸洗 、 喷砂去 除硬化层 , 达 到 分析 , 表面处理要求 。 ( 2 ) 补加磷化剂 。 ( 3 ) 升高磷化槽液温度 。 ( 4 ) 加强脱 良现象 , 得 到优 良的 产 品 。 参 考 文 献 脂或延长磷化时 间。( 5 ) 翻动工件或改变工件位置 。( 6 ) 调整或更换
钢板的磷化
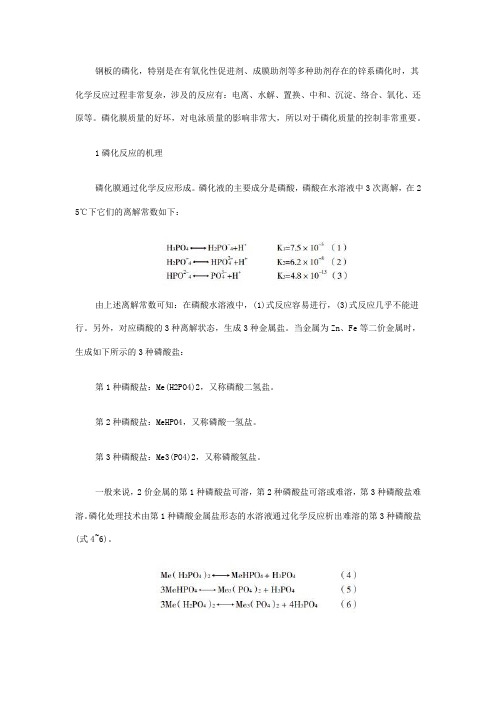
钢板的磷化,特别是在有氧化性促进剂、成膜助剂等多种助剂存在的锌系磷化时,其化学反应过程非常复杂,涉及的反应有:电离、水解、置换、中和、沉淀、络合、氧化、还原等。
磷化膜质量的好坏,对电泳质量的影响非常大,所以对于磷化质量的控制非常重要。
1磷化反应的机理磷化膜通过化学反应形成。
磷化液的主要成分是磷酸,磷酸在水溶液中3次离解,在2 5℃下它们的离解常数如下:由上述离解常数可知:在磷酸水溶液中,(1)式反应容易进行,(3)式反应几乎不能进行。
另外,对应磷酸的3种离解状态,生成3种金属盐。
当金属为Zn、Fe等二价金属时,生成如下所示的3种磷酸盐:第1种磷酸盐:Me(H2PO4)2,又称磷酸二氢盐。
第2种磷酸盐:MeHPO4,又称磷酸一氢盐。
第3种磷酸盐:Me3(PO4)2,又称磷酸氢盐。
一般来说,2价金属的第1种磷酸盐可溶,第2种磷酸盐可溶或难溶,第3种磷酸盐难溶。
磷化处理技术由第1种磷酸金属盐形态的水溶液通过化学反应析出难溶的第3种磷酸盐(式4~6)。
汽车涂装前的磷化处理以锌盐磷化处理为代表。
(7)式和(8)式所示的是生成锌盐磷化膜的平衡反应:(7)式反应在被处理物上进行,钢板界面上的Fe(H2PO4)2浓度增高。
将氧化促进剂亚硝酸盐添加到锌盐磷化液中后,(7)式中Fe(H2PO4)2就成为FePO4,H2变成H2O除去。
根据(7)式的反应,在磷化槽液内的钢板表面上,靠促进剂的作用,氢离子浓度下降,引发(9)式的反应:Fe的浓度高时就生成磷酸二锌铁:2磷化的加速反应2.1磷化反应的加速(1)磷化反应是一个吸热过程,加热有利于反应的进行。
(2)加入氧化性物质(如NO2-、H2O2等)作为去极化剂,其作用是使晶核能够暴露,而不被氢气覆盖;在有氧化性促进剂时,氢原子直接被氧化成水,不影响离子的扩散,形成磷化膜。
2.2磷化膜沉积过程的加速实现反应加速的方法一般是引入结晶晶核。
磷化前的钛盐表面调整,在工件表面形成晶核活性中心,使磷化结晶能够沿晶核生长。
- 1、下载文档前请自行甄别文档内容的完整性,平台不提供额外的编辑、内容补充、找答案等附加服务。
- 2、"仅部分预览"的文档,不可在线预览部分如存在完整性等问题,可反馈申请退款(可完整预览的文档不适用该条件!)。
- 3、如文档侵犯您的权益,请联系客服反馈,我们会尽快为您处理(人工客服工作时间:9:00-18:30)。
磷化膜的形成
现代电镀网3月3日讯:
当金属浸人热的稀磷酸溶液中,会生成一层磷酸亚铁(锌、铝)膜。
但这种膜防护性能差,通常的磷化处理是在含有Zn2+、Mn2+、Ca2+、Fe2+等离子的酸性溶液中进行的。
以假转化型磷化为例,其形成过程分为如下两个阶段。
第一阶段,将钢铁件仔细清洗干净浸人酸性磷化液中,金属表面在溶液中发生溶解,发生反应:
第二阶段,金属与溶液界面处升高,使得此处可溶性的磷酸(二氢〉盐向不溶性的磷酸盐转化,并沉积在金属表面成为磷化膜:
其中,他代表Me代表Zn2+、Mn2+、Ca2+、Fe2+等二价金属离子。
对膜层成分进行分析,发现磷化膜中除含有溶液中的金属离子和磷酸根外,还含有铁,基体金属铁也可与磷酸二氢盐发生反应:
整个成膜过程可以写成如下反应式:
此类磷化过程中,虽然被处理金属发生溶解并参与反应,但磷化膜的金属离子主要由溶液提供,一般为 Zn2+、Mn2+、Ca2+ 中的一种或两种,所以称为“假转化型磷化”。
按处理液成分不同,假转化型磷化可分为锌系、锰系、锌-猛系、锌-钙系磷化等。
转化型磷化膜的形成过程与上述不同,处理液成分是磷酸的碱金属盐或铵,沉积的膜层是基体金属的磷酸膜或氧化物,其中的金属离子是由基体转化而来的,称为“转化型磷化”,或者“铁系”磷化。
当对铝等进行处理时,并无“铁”参与成膜,习惯上仍称为“铁系”磷化。