7步工作法 8D 模板
8D的八个步骤范文

8D的八个步骤范文8D是指八个步骤(Eight Disciplines),是一种持续改善的问题解决方法。
它最初是由福特汽车公司发展出来,旨在解决产品质量问题,现已广泛应用于各个领域。
以下是八个步骤的详细解释。
第一步:建立小组在问题解决的初期,首先需要建立一个由跨职能小组成员组成的小组。
这个小组应该包括与问题直接相关的人员,如质量工程师、生产经理、技术专家等。
成员之间应具备不同的技能和知识,以便能够从不同角度分析和解决问题。
第二步:描述问题在这一步骤中,小组成员需要共同讨论并详细描述问题。
描述问题时应尽量准确地说明问题的性质、范围和影响,以便更好地理解和解决问题。
此外,也应该收集和整理与问题相关的数据和信息。
第三步:立即应对问题在描述问题后,小组成员需要立即采取行动应对问题,以最大限度地减少对业务和客户的影响。
例如,可以采取暂停生产、调整工艺流程、修复设备以及提供临时解决方案等措施。
这一步骤的目标是尽快将问题封闭,减少损失和不良影响。
第四步:根本原因分析在根本原因分析阶段,小组成员需要深入分析问题,并确定导致问题的根本原因。
为了准确找到根本原因,可以运用常用的分析工具,如鱼骨图、五问法、因果关系图等。
这些工具可以帮助小组成员理解问题产生的各种因素,并找到可能的根本原因。
第五步:制定纠正措施在确定根本原因后,小组成员需要制定纠正措施来解决问题。
纠正措施应该具体、可执行和具有可衡量的效果。
例如,可以修改工艺流程、更新设备、加强培训等。
此外,纠正措施还应该考虑成本效益和可持续性。
第六步:实施纠正措施在纠正措施制定完成后,小组成员需要开始实施这些措施。
在实施过程中,应设定明确的目标、时间表和责任人,并监控和评估实施的进展。
如果在实施过程中发现任何问题或障碍,应及时进行调整并采取相应的措施。
第七步:预防措施在解决问题的同时,小组还应该考虑采取一些预防措施,以防止类似问题再次发生。
这些预防措施可以包括更新工艺流程、改进培训计划、完善检测设备等。
质量改进8D工作法介绍

1)应针对每一个末端故障进行因果分析;2)按照质量环对 所有环节进行分析,延伸到整车厂的装调、物流过程和维修 服务环节,找出所有可能因素;3)用因果分析图,直观列出 所有可能因素;4)对所有因素进行分析、验证、判断、确认 找出主要因素。
•未严格按工 艺文件装配
•密封性测 试工序安 排不合理, 试漏后酒 精浸渗到 触点部位
•法
•机
•料
•膜片工艺性差
•触片材料不耐腐蚀
•设备铆压力不够
•铆压力设计过小 •铆压力设计不合理
•铆压顺序不合理
•环
•膜片材质
•材质不符合要求
选择不合 理或结构 不合理
机
•触片结构不合理
油 压
•
力
报
警 器
•测试气密性时下接 触片与压片间的残
PPT文档演模板
质量改进8D工作法介绍
•2.2、2D:问题描述
•目的: • 用量化的术语详细说明与该问题有关的内/外部顾客抱 怨,如什么、地点、时间、程度、频率等。
• “什么东西出了什么问题”
PPT文档演模板
质量改进8D工作法介绍
•关键要点: •●收集和组织所有有关数据以说明问题,提供在顾客和小组 成员之间的充分理解,问题说明是所描述问题的特别有用的 数据的总结,并将贯穿于整个8D过程(如D3、D4、D5) •●审核现有数据,建立对问题共同理解,划定和问题有关范 围 •●细分问题,将复杂问题细分为单个问题 •●问题定义,找到和顾客所确认问题一致的说明,“什么东 西出了什么问题,而原因又未知。
•●质量分析报告中的故障率排序表; •●信息中心提供的质量信息; •●市场反馈的质量信息; •●部门或员工提出的建议; •●参观人员提出的改进建议; •●顾客或供应商提出的改进建议; •●相关领导的指令。
8D:解决问题的八大步骤

D1: ESTABLISH THE TEAM (成立小组)
• 1.让客户认为我们非常地重视他们所反应 的问题 • 2. • 3.G8D 要求要有成员的职称及联络分机 • 4.所有成员共同承担责任及后果, 但不要单 兵作业, 也不要写 Paperwork
31
成员包括:
●最高指导员(CHAMPION)
2
8D的本质: 问题解决程序
当我们观察到 或发现………时 这现象是否正常 跟标准或目标比较的差 异(偏离程度) 其差异是否不该在 为什么会发生异常 ?
现
象
确认并定义问题 WHAT, WHEN, WHERE, WHO, WHY, HOW, HOW MUCH
例如: 人员出勤率93%
问
题
分析原因 WHY
12
%
异常
Quality Improvement
v } ² £ ¨ ¤
Quality Control
Quality Control
É ¶ ® ¡
13
二、如何挖掘问题?
14
把问题想象成一座冰山
现象
现在
看得到的, 可感觉 , 可测量
why
问题
why
紧急处理
真因
一次因 (近因)
why
治标对策 (暂时)
• 答1:因为机器超载, 保 险丝烧断了 • 答2: 因为轴承的润滑 不足 • 答3: 因为润滑帮浦失 灵了 • 答4: 因为帮浦的轮轴 耗损了 • 答5: 因为杂质跑到里 面去了
21
5 Why的分布层次
现象
为什么机器停了? 现在 为什么机器会超载? 为什么轴承会润滑不足? 为什么润滑帮浦会失灵?
– 一般为主管阶层,对小组的进度有 监督, 支持及决策决定权力.
8个步骤改善手法(8D)
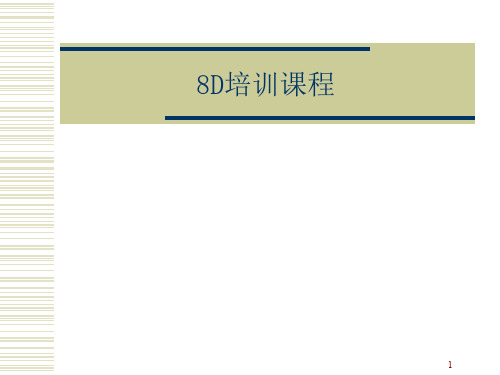
37
1.成立小组
按问题涉及范围确定小组成员: 责属单位:
生管课、销售课、库管课、品保课 责属人员:
贾正羽、庄卫年、赵晓明、许 丽
38
2.问题描述
何时 : 1999年11月4日; 何人 : 浙江精密机械厂; 何地 : 浙江精密机械厂—包装车间; 何事 : 包装ALT-5检测器时,使用20μMHT
27
针对根本原因
群策群力、脑力激荡 提出所有可能的纠正
措施
必要时,考慮選擇 方案所涉及的風險
生产前小批试验 纠正措施
选择最佳方案
确定可行有效的 糾正措施
28
執行永久對策
执行永久性的纠正措施,应注意持续实施 控制,以确保根本原因已经消除.并应监视 纠正措施的长期效果;必要时采取补救措 施。
当验证永久对策有效后,即可以停止临时 措施。
為什麼樣會泄漏?
焊接密封不好。
為什麼焊接的密封不好?
在毛細管內有沉積物。
為什麼在毛細管內有沉積物?
清洗管子時沒有清洗掉。
11
解決根本性問題
為什麼清洗不掉?
使用的洗滌劑效果不好。
為什麼洗滌劑效果不好?
洗滌劑的配方對毛細管內的這種沉積物無效。
跟蹤和分析問題的一種有效的方法是使用4階段 圖表,如圖所示。4階段圖表的優點是對問題和 改正行動的敘述簡明而又全面。必須記住的是 當你能夠“產生又消除”時,也就是說能夠隨 意地重現一個問題,然後又能使其解決時,你 就能确定已經找到了這個問題的根本原因。
如:某一问题发生及团队组成时,可能制造人员 已经先行采取临时对策,惟其永久解决方案,则 可能尚需小组人员的共同参与,经多方研讨后才 能产生。
七步工作法标准模板

07 优化改进
分析优化点
确定优化目标
明确优化的目的和期望结果,为后续步骤提供指 导。
识别瓶颈
分析当前工作流程中的瓶颈和低效环节,找出需 要优化的关键点。
收集数据
收集相关数据和信息,以便对现状进行深入分析 和评估。
制定优化方案
制定方案
根据分析结果,制定具体的优化方案,包括改进措施、时间计划 和责任人。
03
对实施过程进行监控,及时发现问题并进行调整。评估优化改
进的效果,总结经验教训,为后续工作提供借鉴。
THANKS FOR WATCHING
感谢您的观看
重新分配任务
根据实际情况重新分配任务,确保 项目顺利进行。
04
06 检查效果
评估效果
目标完成情况
对照预设目标,评估实际完成情 况,包括数量、质量、时间等方
面的达标情况。
客户反馈
收集客户对产品或服务的反馈意 见,了解满意度、改进建议等方
面的情况。
内部评估
组织内部团队对工作成果进行评 估,分析优点和不足,提出改进
将整理好的信息存储在合适的 媒介中,便于随时查阅和使用
。
03 分析问题
识别问题
总结问题
明确问题的核心,将问题 简化为可解决的形式,避 免过于复杂或模糊。
收集信息
收集与问题相关的所有信 息,包括数据、事实、观 察结果等,以便更好地理 解问题的背景和影响。
确定问题范围
明确问题的具体领域或方 面,以便更有针对性地分 析。
七步工作法标准模板
目录
• 明确目标 • 收集信息 • 分析问题 • 制定计划 • 执行计划 • 检查效果 • 优化改进
01 明确目标
确定目标
8D和七步工作法

• D5:确定永久性纠正措施
在生产前测试方案,并对方案进行评 审以确定所选的校正措施能够解决客 户问题,同时对其它过程不会有不良 影响。
• 主要工具:因果图、FMEA
• 关键要点:重新审视小组成员资格;决策,选择最 佳措施;重新评估临时措施,如必要重新选择;验 证;管理层承诺执行永久纠正措施 。
是通用机型的故障还是专有机型的故障?
是否就措施方案的目的进行了针对性的试验验证?
是否充分收集并分析了典型的失效零件?
是否进行了符合设计标准的可靠性试验验证?
通过分析是否完全确定了失效故障模式?
是否进行过定点用户使用的验证?
识别的失效原因是否为根本原因?
验证数据是否对验证结论有充分的支持?
是否对相关的零件和过程进行了符合性的排查? 是否确定了小批投放(服务更换)的样本跟踪方案 ?
措施方案是否考虑了远近结合?
是否考虑了其它类似机型的采用问题?
是否考虑了在用、库存产品的临时措施?
是否确认了改进措施文件化的范围?
首先要分清楚什么是:
现象 问题 原因 什么是纠正措施 什么是临时措施 什么是长期措施
8D方法常用工具:
• 头脑风暴 • 推移图(目标达成情况、PPM) • 查检表 • 因果图(鱼刺图)、5why方法 • 帕累托图(排列图) • 控制图 • FMEA
Discipline 8
总结和激励
做好详细跟踪,趋势不理想,及时调整,重复上述过程
通过上述的工作过程回答: 1、问题是什么?(2D);2、问题如何解决?(3D~6D);3、将来该问题如何预防?(7D)
质量改进项目关键阶段控制评审内容
失效原因确认评审点
改进措施采用评审点
如何正确在工作中使用“8D”工作法
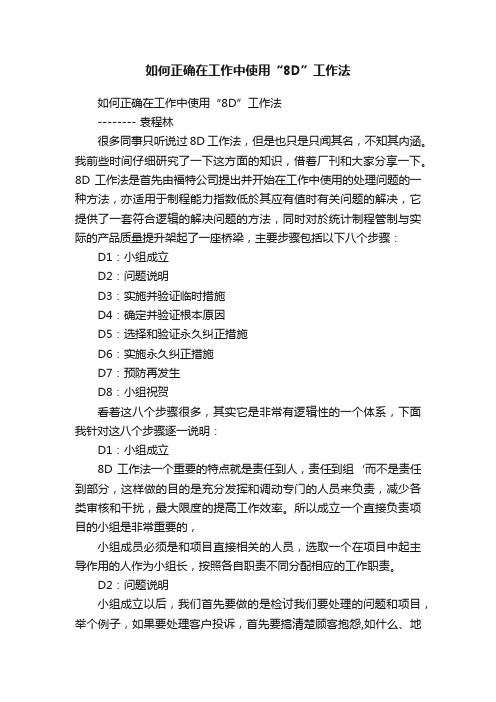
如何正确在工作中使用“8D”工作法如何正确在工作中使用“8D”工作法-------- 袁程林很多同事只听说过8D工作法,但是也只是只闻其名,不知其内涵。
我前些时间仔细研究了一下这方面的知识,借着厂刊和大家分享一下。
8D工作法是首先由福特公司提出并开始在工作中使用的处理问题的一种方法,亦适用于制程能力指数低於其应有值时有关问题的解决,它提供了一套符合逻辑的解决问题的方法,同时对於统计制程管制与实际的产品质量提升架起了一座桥梁,主要步骤包括以下八个步骤:D1:小组成立D2:问题说明D3:实施并验证临时措施D4:确定并验证根本原因D5:选择和验证永久纠正措施D6:实施永久纠正措施D7:预防再发生D8:小组祝贺看着这八个步骤很多,其实它是非常有逻辑性的一个体系,下面我针对这八个步骤逐一说明:D1:小组成立8D工作法一个重要的特点就是责任到人,责任到组‘而不是责任到部分,这样做的目的是充分发挥和调动专门的人员来负责,减少各类审核和干扰,最大限度的提高工作效率。
所以成立一个直接负责项目的小组是非常重要的,小组成员必须是和项目直接相关的人员,选取一个在项目中起主导作用的人作为小组长,按照各自职责不同分配相应的工作职责。
D2:问题说明小组成立以后,我们首先要做的是检讨我们要处理的问题和项目,举个例子,如果要处理客户投诉,首先要搞清楚顾客抱怨,如什么、地点、时间、程度、频率等,“什么东西出了什么问题” 等等。
只有明确了我们要处理问题的细节,才可能更好的对症下药处理好下面的工作。
在这个步骤中有以下关键要点:1、收集和组织所有有关数据以说明问题2、问题说明是所描述问题的特别有用的数据的总结3、审核现有数据,识别问题、确定范围4、细分问题,将复杂问题细分为单个问题处理,详细分类明确问题的细节。
D3:实施并验证临时措施我们面对的问题有可能在很短的时间内不能得到彻底的解决,所以在处理问题的时候我们必须要先对要处理的问题做一个临时的对应措施,比如如果是客户投诉,我们在了解清楚客户投诉的内容后,首先要做的是尽量满足客户眼前的需求,比如给客户换货呀,全检库存等等。
8D工作法标准版本时间
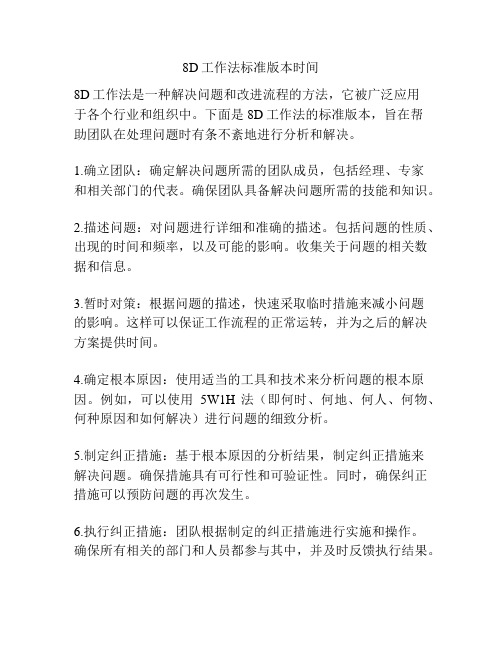
8D工作法标准版本时间8D工作法是一种解决问题和改进流程的方法,它被广泛应用于各个行业和组织中。
下面是8D工作法的标准版本,旨在帮助团队在处理问题时有条不紊地进行分析和解决。
1.确立团队:确定解决问题所需的团队成员,包括经理、专家和相关部门的代表。
确保团队具备解决问题所需的技能和知识。
2.描述问题:对问题进行详细和准确的描述。
包括问题的性质、出现的时间和频率,以及可能的影响。
收集关于问题的相关数据和信息。
3.暂时对策:根据问题的描述,快速采取临时措施来减小问题的影响。
这样可以保证工作流程的正常运转,并为之后的解决方案提供时间。
4.确定根本原因:使用适当的工具和技术来分析问题的根本原因。
例如,可以使用5W1H法(即何时、何地、何人、何物、何种原因和如何解决)进行问题的细致分析。
5.制定纠正措施:基于根本原因的分析结果,制定纠正措施来解决问题。
确保措施具有可行性和可验证性。
同时,确保纠正措施可以预防问题的再次发生。
6.执行纠正措施:团队根据制定的纠正措施进行实施和操作。
确保所有相关的部门和人员都参与其中,并及时反馈执行结果。
7.验证纠正效果:对纠正措施的执行结果进行验证。
可以采用实验、测试或观察的方法来评估纠正措施是否有效。
如果发现还有问题存在,需要重新制定纠正措施。
8.预防措施:基于之前的经验和结果,制定预防措施来防止同类问题的再次出现。
确保先前发现的根本原因得到解决,并且相关的流程和规范得到更新。
这是8D工作法的标准版本。
团队在解决问题时,可以根据该方法的步骤进行分析和决策。
通过逐步追踪问题,找出根本原因,并制定纠正和预防措施,可以有效地解决问题并改进工作流程。
同时,团队成员的协作和沟通也是成功应用8D工作法的关键因素。
继续写相关内容:9. 定期复审:定期回顾和复审已经实施的纠正措施和预防措施的效果。
确保问题的解决是可持续的,并跟踪潜在的新问题。
10. 持续改进:将学到的知识和经验应用于其他领域和流程中,实现持续改进的目标。
- 1、下载文档前请自行甄别文档内容的完整性,平台不提供额外的编辑、内容补充、找答案等附加服务。
- 2、"仅部分预览"的文档,不可在线预览部分如存在完整性等问题,可反馈申请退款(可完整预览的文档不适用该条件!)。
- 3、如文档侵犯您的权益,请联系客服反馈,我们会尽快为您处理(人工客服工作时间:9:00-18:30)。
Section E: Failure Scenario失效分析
Worst Case Failure Scenario最差的失效情况: Is this an Emissions Related Failure 是排放 相关的失效: Estimated Cost per Engine for most likely failure估计单台成本
Section C: Start of Problem 问题开始时间
When did problem start in the mfg. process 问题什么时候在生 产过程发现 If a supplier problem, when was material first received at 如果是 供应商问题, 什么时候发现? Supporting logic for the start date 开始时间 If a Engine problem, when was engine first received at customer 如果是发动机问题,客户什么时候 发现?
Section G: Recommended Action 建议行动
For IN-HOUSE Engines 库 存发动机处理 For PARTS DISTRIBUTION Inventory 零件库存 For OEM Engines OEM 发动机处理 Finished Date and Responsibility 计划检验完成时间及责 任人
Section H: Follow-up/Interim Action Assignments Action Resp. Plan Date
Section D: End of Problem问题结束时间
When was condition corrected in production 问题什么时候解决? What action was taken 采取了什么行动? ESN First: 第一个ESN
PIC Report
Team Member: 小组成员 Prepared by: 起草人
PIC No: Date: 时间
Section A :Problem Description 问题描述
Part Number (s) affected 影响的零 件号: Problem Description (Word) 问题文字描述: Part or Process Name零件或过程 名称 Part Batch or Engine No. 零件批 次或发动机号
F08-077A0
Most Likely Failure Scenario最可能的失效:
Section F: Possible Reasons可能原因
Pictures Description 图片描述
Байду номын сангаас
Section B: First Noted 第一次发现
When was the problem found 问题什么时候发现? If supplier identified, when was notified 如果供应商发现的, 何 时被通知 Who identified the problem 谁发 现问题? If Customer identified, when was notified 如果客户抱怨的, 何时被 通知