甲烷化操作规程
甲烷化工艺
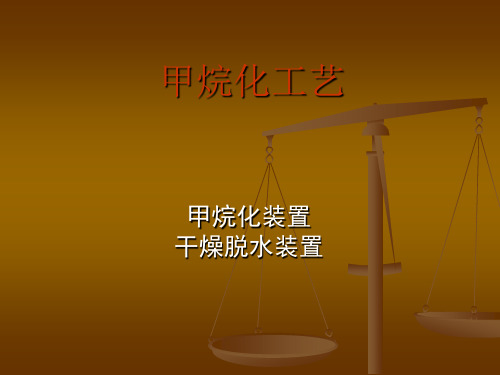
经净化后由甲烷化合成天然气的大型商业化工厂。
碎煤加压气化后净化煤气通过镍催化剂在 2.4~6MPa、300-700℃下,将H2、CO合成 天然气的技术,在美国大平原建成第一期 工程规模389万Nm3/d (相当于日产原油2 万桶)合成天然气工厂。于1980年7月破土 动工,1984年4月完工并投入试运转,1984 年7月28日生产出首批合成天然气并送入美 国的天然气管网。该厂至今还在正常运行。
b.从公用系统引出另一股净化空气经 自力式压力调节阀稳定阀后压力300kPag, 并经仪表风过滤器过滤后分配至各气动控 制仪表设备。 c. 过滤分离器、闪蒸罐均设置超压安 全泄放空系统。 d.从三甘醇再生塔塔顶排出的气体中 大部分为水蒸气,经过排出管线进入尾气 冷却器,冷取至环境温度后进入尾气焚烧 炉下部的气液分离腔,分离掉游离液体, 液体进入站内污水池后集中处理,分离出 的气体经焚烧炉燃烧后,转化成无污染环 境物质后排入大气。
此处加入高压蒸汽后温度为285℃和220℃ 的原料气汇合使得原料气被稀释,减弱放 热反应。混合后的气体温度255℃进入进入 R6002-1;R6002-1的另一股出口气和E6006 第一锅炉进料水预热器换热后温度为296℃ 和220℃的原料气汇合后温度为262℃进入 R6002-2(气体调节催化剂为GCC--2、 6×4mm、27.1m3;甲烷化催化剂为MCR、 11×5mm、17m3)主要反应为: CO+3H2=CH4+H2O CO+H2O=CO2+H4 CO2+4H2=CH4+2H2O C2H6+H2=2CH4,
2、在氨厂典型的甲烷化炉操作条件下,每 1% CO转化的绝热温升为72℃,每1% CO2转 化的绝热温升60℃,反应炉的总温升可由 下式计算: ΔT=72×[ CO]入+60×[ CO2]入 式中 ΔT--分别为进口气中CO、CO2的含 量,%(体积分数) (二)、甲烷化系统的主要设备有哪些?
(完整版)甲烷化操作规程

甲烷化操作规程甲烷化岗位作业指导书拟稿:审核:批准:公布日期:目录一、岗位任务 (2)二、工艺指标(2)三、工艺原理及流程 (2)四、主要设备 (3)五、正常开车步骤(4)六、正常停车步骤 (5)七、紧急停车步骤 (5)八、异常现象及处理方法(5)九、安全注意事项(6)一、本岗位任务甲烷化岗位的主要任务:在适当的压力、温度、催化剂的作用下把甲醇后的CO和CO2与H2合成为CH4和H2O,并把H2O分离下来,把CO+CO2含量控制在25ppm以下,送往合成岗位。
二、工艺指标(一)新鲜气温度30-40℃(二)催化剂热点温度250℃± 5 ℃(三)甲烷化塔一入温度≤130℃(四)塔壁温度≤150℃(五)甲烷化塔二入温度250℃-270℃。
(六)甲烷化塔二出温度≤190℃(七)出系统CO+CO2含量≤25PPM三、工艺原理及流程(一)工艺原理:本工段主要作用是脱除工艺气的CO和CO2。
在催化剂的作用下使少量CO、CO2加氢生成CH4和H2O,把工艺气的CO和CO2的含量脱除到25PPM 以下.由于该反应是放热反应,本工段充分利用其反应热以加热合成塔入口气体.甲烷化催化剂是以镍为活性组分,以稳定活性氧化铝为载体。
反应原理:CO+3H2= CH4+H2O +206.24kJ/molCO2+4H2= CH4+2H2O +165.4kJ/mol(二)流程:1、工艺介质主流程:从压缩机六段来的氢氮气进油分离器,油水分离后气体进入预热器与合成塔出口气体进行热量交换,加热后经合成塔环隙进塔底换热器与出口气体进一步换热,然后出合成塔进加热器,经蒸汽加热后再经合成塔心管到内件顶部进触媒层进行反应。
出口气体经塔底换热器换热后进预热器管内继续换热,然后进水冷排冷却,再进水分离器分离水后送合成。
注:(1)入工段阀门处增设旁路,主要目的是开停车时使用老系统的精练气。
(2)系统入口阀门前接循环机来气管线;增设放空管线。
(3)去合成阀门前增设去甲醇管线,为甲醇开车使用。
甲烷化岗位操作规程
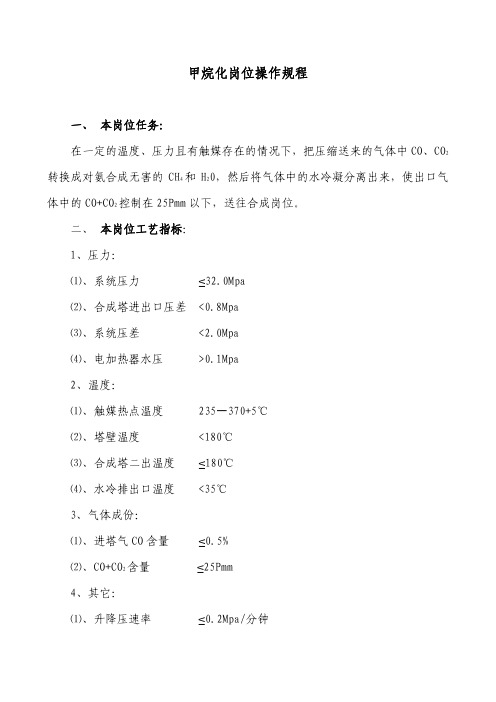
⑶活塞杆螺帽松动,连杆 车处理
轴瓦吻合不匀,十字头销 ⑵紧急停车处理
松动
⑶检修
⑷气缸余隙过小
9 循 环 机 油 泵 出 口 油 ⑴油过滤器堵塞
⑴清洗过滤器
⑵、合成塔进出口压差 <0.8Mpa
⑶、系统压差
<2.0Mpa
⑷、电加热器水压
>0.1Mpa
2、温度:
⑴、触媒热点温度
235—370+5℃
⑵、塔壁温度
<180℃
⑶、合成塔二出温度 ≤180℃
⑷、水冷排出口温度 <35℃
3、气体成份:
⑴、进塔气 CO 含量 ≤0.5%
⑵、CO+CO2 含量
≤25Pmm
⑴、打开付线阀,关闭出口阀,关闭进口阀,打开放空阀卸压。
⑵、停下循环机,关闭冷却水阀门。
七、本岗位常见事故及处理:
序号 发生现象
常见原因
处理方法
1 触 媒 层 温 度 增 高 过 醇后 CO、CO2 含量升高 ⑴加大副线流量,
快
调低电加热器电流
⑵启用循环机
⑶切气
2 触 媒 层 温 度 突 然 下 ⑴主线和副线气比例不 ⑴减少副线流量
②、立即与压缩岗位联系,停止送气。迅速关闭补气阀门。按紧急停车步 骤停循环机(如电加热器在用时,须先停用电加热器)。
③、迅速关闭系统进、出口阀门。 ④、按短期停车方法处理。 四、 本岗位安全操作规程: 1、严格按工艺开停车程序,不得超指标操作。 2、严格按工艺指标进行,不得超指标操作。 3、系统放空要缓慢,以免产生静电着火。 4、电机启动前注意盘车,并注意各电机电流、温升。 5、注意检查安全装置、压力表是否灵敏可靠。 6、严格按升降温速率升降温。 7、严格按升降压速率升降压。 8、加强岗位间联系,确保信号准确无误。 9、加强巡回检查。 五、本岗位正常操作要点: 1、触媒层温度的调节,使温度控制在指标以内,稳定其操作。 2、塔壁温度的控制,绝对不允许超指标操作。 3、CO+CO2 含量的控制。 4、系统压力的控制。 5、系统压差的控制。 六、本岗位主要运转设备的操作规程: 1、循环机开车:
甲烷化工艺流程

甲烷化工艺流程
《甲烷化工艺流程》
甲烷化工艺是一种将甲烷转化为更有用化学物质的过程。
甲烷是一种富含碳和氢的简单有机化合物,是天然气的主要成分。
甲烷化工艺可以将甲烷转化为甲烷醇、甲醛、丙烷等更有用的化学品。
甲烷化工艺通常包括以下几个步骤:
1. 蒸汽重整:甲烷和水蒸汽经过反应生成一氧化碳和氢气。
这一步骤是甲烷化工艺的起始阶段,产生的一氧化碳和氢气可作为后续反应的原料。
2. 甲烷蒸氨:甲烷和氨气在催化剂的作用下发生反应,生成甲胺。
甲胺可以用于生产甲胺醛等化学品。
3. 碳氢化合物的加氢:甲烷和氢气通过催化剂反应,生成其他碳氢化合物,如丙烷、丁烷等。
4. 甲基化反应:甲烷和一氧化碳在高温下发生反应,生成甲醇。
这是甲烷化工艺中的重要步骤,因为甲醇是一种重要的工业原料。
以上是甲烷化工艺的基本流程,通过不同的反应组合可以得到各种不同的化学品。
甲烷化工艺在化工领域具有广泛的应用,
不仅可以提高甲烷的利用率,还可以生产出更多有用的化学品,为化工行业的发展做出贡献。
甲烷化技术
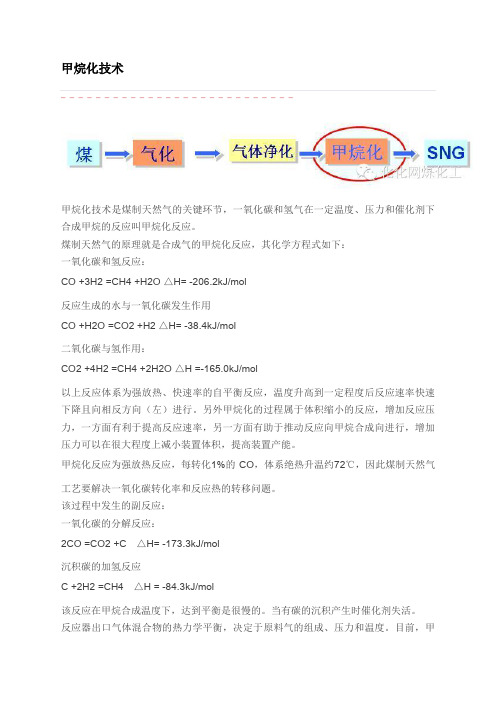
甲烷化技术¯ ¯ ¯ ¯ ¯ ¯ ¯ ¯ ¯ ¯ ¯ ¯ ¯ ¯ ¯ ¯ ¯ ¯ ¯ ¯ ¯ ¯ ¯ ¯ ¯ ¯ ¯甲烷化技术是煤制天然气的关键环节,一氧化碳和氢气在一定温度、压力和催化剂下合成甲烷的反应叫甲烷化反应。
煤制天然气的原理就是合成气的甲烷化反应,其化学方程式如下:一氧化碳和氢反应:CO +3H2 =CH4 +H2O △H= -206.2kJ/mol反应生成的水与一氧化碳发生作用CO +H2O =CO2 +H2 △H= -38.4kJ/mol二氧化碳与氢作用:CO2 +4H2 =CH4 +2H2O △H =-165.0kJ/mol以上反应体系为强放热、快速率的自平衡反应,温度升高到一定程度后反应速率快速下降且向相反方向(左)进行。
另外甲烷化的过程属于体积缩小的反应,增加反应压力,一方面有利于提高反应速率,另一方面有助于推动反应向甲烷合成向进行,增加压力可以在很大程度上减小装置体积,提高装置产能。
甲烷化反应为强放热反应,每转化1%的CO,体系绝热升温约72℃,因此煤制天然气工艺要解决一氧化碳转化率和反应热的转移问题。
该过程中发生的副反应:一氧化碳的分解反应:2CO =CO2 +C △H= -173.3kJ/mol沉积碳的加氢反应C +2H2 =CH4 △H = -84.3kJ/mol该反应在甲烷合成温度下,达到平衡是很慢的。
当有碳的沉积产生时催化剂失活。
反应器出口气体混合物的热力学平衡,决定于原料气的组成、压力和温度。
目前,甲烷化技术已经用在大规模的合成气制天然气上,最大的问题是催化剂的耐温和强放热反应器的设计制作上。
甲烷化工艺有两步法和一步法两种类型。
低变及甲烷化
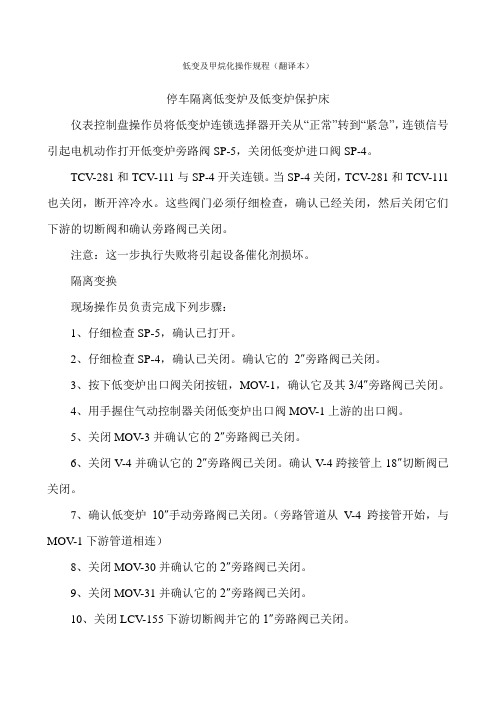
低变及甲烷化操作规程(翻译本)停车隔离低变炉及低变炉保护床仪表控制盘操作员将低变炉连锁选择器开关从“正常”转到“紧急”,连锁信号引起电机动作打开低变炉旁路阀SP-5,关闭低变炉进口阀SP-4。
TCV-281和TCV-111与SP-4开关连锁。
当SP-4关闭,TCV-281和TCV-111也关闭,断开淬冷水。
这些阀门必须仔细检查,确认已经关闭,然后关闭它们下游的切断阀和确认旁路阀已关闭。
注意:这一步执行失败将引起设备催化剂损坏。
隔离变换现场操作员负责完成下列步骤:1、仔细检查SP-5,确认已打开。
2、仔细检查SP-4,确认已关闭。
确认它的2″旁路阀已关闭。
3、按下低变炉出口阀关闭按钮,MOV-1,确认它及其3/4″旁路阀已关闭。
4、用手握住气动控制器关闭低变炉出口阀MOV-1上游的出口阀。
5、关闭MOV-3并确认它的2″旁路阀已关闭。
6、关闭V-4并确认它的2″旁路阀已关闭。
确认V-4跨接管上18″切断阀已关闭。
7、确认低变炉10″手动旁路阀已关闭。
(旁路管道从V-4跨接管开始,与MOV-1下游管道相连)8、关闭MOV-30并确认它的2″旁路阀已关闭。
9、关闭MOV-31并确认它的2″旁路阀已关闭。
10、关闭LCV-155下游切断阀并它的1″旁路阀已关闭。
11、关闭LCV-263下游切断阀并它的11/2″旁路阀已关闭。
在变换炉被隔离后应放空泄压并用氮气保护催化剂。
低温变换炉放空与氮气吹扫1、低温变换炉可以用三种方式放空。
前两种最有效。
a、慢开低变炉进口管接出的2″放空管线上的两个放空阀。
(一个阀大开度,另一个慢开以控制放空的量)这样气体放空到位于103-C上方管架的小放空罐。
b、打开V-4下游的两个2″导淋阀(一个阀大开度,另一个慢开以控制放空的量)这样气体放空到103-C与104-C之间的放空烟囱。
c、打开位于低变炉出口管上4″和6″两个放空阀。
这样气体放空到PIC-5放空消音器。
(一个阀大开度,另一个慢开以控制放空的量)确认到102-J进口的4″阀门已关闭。
甲烷化操作规程

1)减少循环量
2)调整补入原料气中CO+CO2含量
3)减少循环量或增加生产负荷
4)加强油分排油水
5)减少生产负荷
6)停车检修
7)精心调节,调节电炉功率,维持温度
3
甲烷化塔塔壁温度升高
1)内件保温脱落,塔内同平面温差太大
2)内件筒体椭圆,气体偏流
停车检修,消除同平面温差;校正
4
系统出口CO+CO2含量超标
≤180℃
3
氨冷器出口气体温度
<15℃
4
水冷器出口气体温度
<35℃
5
甲烷化塔壁温度
<120℃
6
循环机进口温度
≤40℃
7
循环机出口温度
≤50℃
三
气体成份
1
进塔气:
CO+CO2≤0.5%
2
出塔气:
CO+CO2≤25ppm
四
电流
1
循环机电机电流
<336A
2
电炉丝最大电流
<1200A
第四节开、停车操作要点及注意事项
3)内件保温层脱落
1)降低生产负荷,待机停车更换催化剂
2)停车检修清理换热器
3)停车修理
6
电炉短路
1)中心管有异物
1)停车吹除中心管
7
断水、断电
紧急停车处理
2008-6-26
3.2防止有毒物质进入合成塔,其措施主要是提高原料气的脱硫效率,控制原料气中的总硫含量小于0.1PPM。同时加强除油效率,确保原料气的质量。
3.3由于甲烷化反应中要消耗H2生成CH4,造成进氨合成工段的补充气CH4含量增加,从而加大氨合成工段的放空量,因此,在一般情况下保证进塔原料气成分CO+CO2≤0.5%.
甲烷化操作实操

1、甲烷合成反应器的反应机理?在甲烷化反应器中主要进行的是甲烷的合成反应,即一氧化碳、二氧化碳与氢在催化剂的作用下转化成甲烷。
甲烷合成反应是个强放热反应,伴随甲烷合成反应同时还发生了一氧化碳的氧化还原。
总反应方程式如下:CO + 3H2 = CH4 + H2OCO2 + 4H2 = CH4 + 2H2OCO + H2O = CO2 + H22.在氨厂典型的甲烷化炉操作条件下,毎1%CO转化的绝热温升为72℃,每1%CO2转化的绝热温升60℃,反应炉的总温升可由下式计算:ΔT=72╳[CO]入+60╳[CO2]入式中:ΔT----分别为进口气中CO、CO2的含量,%(体积分数)3甲烷化设备主要有哪些?甲烷化设备主要有硫吸收器、甲烷化反应器、高压废热锅炉、低压废热锅炉、甲烷化换热器、高压蒸汽过热器、开车加热器、循环压缩机、水冷器、水分离器等设备。
4、甲烷化催化剂的组成及主要组分的作用是什么?甲烷化催化剂是以镍为活性组分在载体上,为获得催化剂的活性和热稳定性有添加了一些促进剂。
主要组分有Ni、Al2O3、MgO、Re2O3等Al2O3是一种普遍使用的载体。
Al2O3具有多种结构形态,用于甲烷化的是具有大孔的Al2O3。
MgO是一种良好的的结构稳定剂。
Re2O3为稀土氧化物,具有良好的活性与稳定性。
5、为什么要对甲烷化催化剂进行还原?还原过过程中有哪些化学反应?①甲烷化催化剂使用前,是以镍(Ni)的氧化物形式纯在,所以使用时,必须还原活化。
在还原剂(H2、CO)被氧化的同时,多组分催化剂中的NiO被还原具有活性的金属镍(Ni),并在还原过程中形成了催化剂的孔道。
而Al2O3不会被还原,起着间接支持催化剂结构的助构作用,使镍处于均匀分散的微晶状态,使催化剂具有较大的比表面、较高的活性和稳定性。
②甲烷化催化剂还原时发生如下反应:NiO + H2 = Ni + H2O - 2.55KJ/molNiO + CO = Ni + CO2 - 30.25 KJ/mol这些都不是强放热反应,还原过程本身不会引起催化剂床层大的温升。
- 1、下载文档前请自行甄别文档内容的完整性,平台不提供额外的编辑、内容补充、找答案等附加服务。
- 2、"仅部分预览"的文档,不可在线预览部分如存在完整性等问题,可反馈申请退款(可完整预览的文档不适用该条件!)。
- 3、如文档侵犯您的权益,请联系客服反馈,我们会尽快为您处理(人工客服工作时间:9:00-18:30)。
甲烷化岗位作业指导书
拟稿:
审核:
批准:
公布日期:
目录
一、岗位任务 (2)
二、工艺指标 (2)
三、工艺原理及流程 (2)
四、主要设备 (3)
五、正常开车步骤 (4)
六、正常停车步骤 (5)
七、紧急停车步骤 (5)
八、异常现象及处理方法 (5)
九、安全注意事项 (6)
、本岗位任务
甲烷化岗位的主要任务:在适当的压力、温度、催化剂的作用下把甲醇后
的CO和CO2与H2合成为CH4和战0,并把出0分离下来,把CO+CO2含量控制在25ppm 以下,送往合成岗位。
二、工艺指标
(一)新鲜气温度30- 40C
(二)催化剂热点温度250C 士5 C
(三)甲烷化塔一入温度W 130C
(四)塔壁温度w 150C
(五)甲烷化塔二入温度250C —270 C o
(六)甲烷化塔二出温度w 190C
(七)出系统CO+C2C含量W 25PPM
三、工艺原理及流程
(一)工艺原理:
本工段主要作用是脱除工艺气中的CO和C02。
在催化剂的作用下使少量
CO、CO2加氢生成CH4和出0,把工艺气中的CO和CO2的含量脱除到25PPM 以下。
由于该反应是放热反应,本工段充分利用其反应热以加热合成塔入口气体。
甲烷化催化剂是以镍为活性组分,以稳定活性氧化铝为载体。
反应原理:CO+3H2= CH4+H2O+206.24kJ/mol
CO2+4H2= CH4+2H2O+165.4kJ/mol
(二)流程:
1、工艺介质主流程:
从压缩机六段来的氢氮气进油分离器,油水分离后气体进入预热器与合成
塔出口气体进行热量交换,加热后经合成塔环隙进塔底换热器与出口气体进一
步换热,然后出合成塔进加热器,经蒸汽加热后再经合成塔中心管到内件顶部进触媒层进行反应。
出口气体经塔底换热器换热后进预热器管内继续换热,然后进水冷排冷却,再进水分离器分离水后送合成。
注:(1)入工段阀门处增设旁路,主要目的是开停车时使用老系统的精练气。
(2)系统入口阀门前接循环机来气管线;增设放空管线。
(3)去合成阀门前增设去甲醇管线,为甲醇开车使用。
(4)去合成阀门前接去循环机管线,增设放空。
2、蒸汽流程:
过热蒸汽总管来蒸汽经调节阀进甲烷化加热器上部,对工艺气起加热后回蒸汽管网。
3、水流程:
循环水来自氨合成凉水塔,经冷排后,通过水池底部连通管回到合成冷排水池。
四、主要设备
五、正常开车步骤
当系统处于保温保压状态且催化剂温度仍然在正常范围内时,接到开车通知后,可以通知压缩送气然后开启补充气进口阀门,缓慢向塔内送气,微量合格后向氨合成送气,如果送气温度下降,可以开启电炉维持温度。
若停车时间较长,催化剂床层温度已降至活性温度以下,应首先联系电工开启循环机,电炉通电后升温,当炉温升至活性温度时通知送气,待微量合格后开始向合成系统送气。
六、正常停车步骤
(一)短期停车:接到通知后,关闭系统进口出口阀门,系统保温保压。
(二)长期停车:接到停车通知后,关闭进口出口阀门,然后开启循环机,用
循环量来控制降温速率每小时w 40C,当温度降至150C时,可以停循环机,
让其自然降温,根据需要确定系统保压或卸压。
七、紧急停车步骤立即关死系统进出口阀门和付线阀,视情况做好保温保压或卸压处
理。
八、异常现象及处理方法
(一)压力对甲烷化反应有何影响? 答:甲烷化反应为体积收缩的反应,提高压力有利于反应的进行,提高压力
也相应增大反应物分压而加快反应的进行。
因而随反应压力的提高,有利于提高催化剂活性,使用空速也可加大反应物压力。
(二)操作空速对甲烷化反应有何影响?
答:操作空速应大于设计空速会引起塔出口微量超指标以及催化剂活性衰退的加快,并不可取。
降低空速一般是在前面工序出现事故引起甲烷化催化剂.
(三)气体组分对甲烷化反应有何影响?
答: 入塔气中CO、CO2 含量增加,加重了催化剂的负荷,加快了催化剂的活性衰退,提高了氢耗与惰性气甲烷含量,特别是CO 甲烷化比较困难,应入口气中CO 难度增大,有可能导致出塔CQ含量增加,应适当提高进口温度,保证出口CQ含量符合指标。
(四)温度、压力、空速、气体成分对甲烷化催化剂的还原有何影响?
A. 温度:温度是影响还原过程的主要因素。
温度过低,还原速度很慢,还原过程拖的
时间太长。
温度过高,由于热老化以及还原过程中生成的水不能及时从催化剂空隙中排出,而引起镍的反复氧化还原会导致镍晶长大,同样也不能获得最大的镍表面而影响催化剂的活性。
根据试验,在还原温度350—400 范围内,可获得镍表面积的最大值。
在400 下还原,催化剂还原
完全,活性液明显提高。
B. 压力:压力对还原反应影响不大。
单还原阶段,若用工艺气作还原介质时,适当提前
提压至正常操作压力,将有利于甲烷化反应的进行,可提早供应合格的合成,缩短非生产时间。
C. 空速:加大空速有利于还原过程生成的水及时排出,使催化剂有较大的接触表面
积,而且也可缩小催化剂床层轴向温差,使催化剂充分还原,因此采用较高空速是有益的。
但考虑到加热设备的能力及气体的来源,还原空速一般采用正常操作空速的25%—50%。
D. 气体成分:合格的工艺气、N2—H2 混合气以及纯氢,均可选为还原剂。
操作人员
应希望气体中氢浓度比较高,水蒸气浓度竟可能低。
若气体中水蒸气浓度高于3%,将使催化剂丧失部分活性,即使以后用干气操作其活性液不能恢复。
九、安全注意事项本工段的主要有毒有害物质及防护措施: (一)主要有毒有害物质:氢气、一氧化碳
(二)主要防护措施
1、严禁有跑冒滴漏现象。
2、所有设备、管道及管件安装均符合安全规程。
3、岗位上要备有CO 防毒面具。
4、岗位上要备有消防器具。
5、操作人员认真阅读升温还原方案,并严格执行。
6、各部位温度、压力要严格按照工艺指标控制。