化工分离工程
化工分离工程
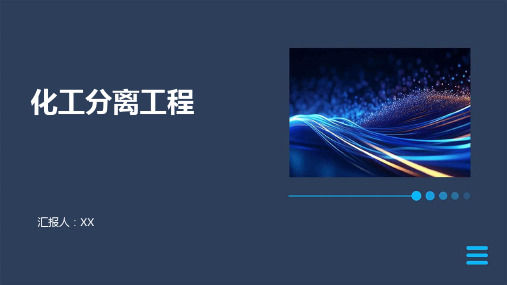
混合建模
结合机理建模和数据驱动建模 的优势,提高模型的精度和泛 化能力。
优化算法
应用遗传算法、粒子群优化等 智能优化算法,对分离过程进
行参数优化和操作优化。
先进控制技术应用
预测控制
基于模型预测控制(MPC)技术, 实现对分离过程的实时优化和控制。
化工分离工程
汇报人:XX
目 录
• 分离工程概述 • 化工分离原理与方法 • 化工分离设备与技术 • 化工分离过程优化与控制 • 典型案例分析 • 未来展望与挑战
01
分离工程概述
分离工程定义与重要性
分离工程定义
利用物理、化学或物理化学方法 ,将混合物中的各组分进行分离 、提纯或富集的过程。
重要性
膜分离法
01
02
03
原理
利用特定膜材料的选择性 透过性,使混合物中的某 些组分能够透过膜而实现 分离。
分类
微滤、超滤、纳滤、反渗 透等。
应用
海水淡化、废水处理、气 体分离等。
03
化工分离设备与技术
塔设备
蒸馏塔
用于多组分溶液的分离, 通过加热使不同组分在不 同温度下挥发,从而实现 分离。
吸收塔
用于气体吸收操作,将气 体中的某一组分通过液体 吸收剂吸收到液体中。
通过化工分离技术,将废弃物中的有用成分提取 出来,实现废弃物的资源化利用,减少环境污染 。
环保型分离剂的开发
研发环保型的分离剂,如生物可降解的分离剂、 无毒无害的分离剂等,以降低化工分离过程对环 境的污染。
化工行业面临的挑战与机遇
挑战
随着环保法规的日益严格和资源的日益紧缺,化工行业面临着越来越大的环保压力和成本压力。同时,新兴技术 的不断涌现也给传统化工行业带来了竞争压力。
化工分离工程01

化工分离工程 011. 引言化工分离工程是化工领域的重要分支之一,它涉及到物质的分离、净化和纯化等工艺过程。
本文将介绍化工分离工程的基本概念、分类、应用领域、工艺流程以及一些常用的分离技术。
2. 分离工程的基本概念分离工程是指根据物质的物理性质、化学性质或者两者的组合,将混合物中的组分进行分离的过程。
分离工程的基本任务是提高混合物中目标组分的纯度,并且尽可能地提高分离效率。
3. 分离工程的分类分离工程可以按照不同的分类标准来进行分类。
根据物质的性质,分离工程可以分为物理分离和化学分离两大类。
物理分离是根据物质的物理性质进行分离,包括蒸馏、吸附、萃取等技术;化学分离是根据物质的化学性质进行分离,如化学反应、化学析出等技术。
4. 分离工程的应用领域4.1 化工生产中的应用化工分离工程在化工生产中起着至关重要的作用。
通过分离工程,可以将原材料中的有用组分与杂质分离开来,从而提高产品的质量和产量。
例如,在石油炼制过程中,通过蒸馏工艺可以将原油中的轻质烃类和重质烃类分离出来,得到汽油、柴油等产品。
4.2 环境保护中的应用分离工程也广泛应用于环境保护领域。
例如,在废水处理过程中,可以通过吸附、离子交换等分离技术,将废水中的污染物与清水进行分离,从而净化废水,保护环境。
4.3 生物医药领域的应用化工分离工程在生物医药领域也有广泛的应用。
例如,在药物研发过程中,可以通过分离工程将混合物中的有效药物分离出来,提高药物的纯度和活性,从而提高药物的疗效。
5. 分离工程的工艺流程分离工程一般包括前处理、主分离和后处理等环节。
前处理是指对混合物进行预处理,如去除杂质、调整溶剂比例等;主分离是指将混合物中的目标组分与杂质分离开来;后处理是指对分离后的产物进行处理,如晶体过滤、溶剂回收等。
不同的分离工程可以采用不同的工艺流程,具体的流程可以根据混合物的特性和目标要求进行设计。
6. 常用的分离技术6.1 蒸馏蒸馏是一种基于组分的挥发性差异进行分离的技术。
化工分离工程

化工分离工程第一章绪论1.1概述1.1.1 分离过程的发展与分类随着世界工业的技术革命与发展,特别是化学工业的发展,人们发现尽管化工产品种类繁多,但生产过程的设备往往都可以认为是由反应器、分离设备和通用的机、泵、换热器等构成。
其中离不开两类关键操作:一是反应器,产生新物质的化学反应过程,其为化工生产的核心;-其中离不开两类关键操作:一是反应器,产生新物质的化学反应过程,其为化工生产的核心;-于是研究化学工业中具有共同性的过程和设备的规律,并将之运用于生产的“化学工程”这一学科应运而生。
分离过程可分为机械分离和传质分离两大类。
机械分离过程的对象都是两相或两相以上的非均相混合物,只要用简单的机械方法就可将两相分离,而两相间并无物质传递现象发生传质分离过程的特点是相间传质,可以在均相中进行,也可以在非均相中进行。
传统的单元操作中,蒸发、蒸馏、吸收、吸附、萃取、浸取、干燥、结晶等单元操作大多在两相中进行。
依据处于热力学平衡的两相组成不相等的原理,以每一级都处于平衡态为手段,把其他影响参数均归纳于效率之中,使其更符合实际。
它的另一种工程处理方法则是把现状和达到平衡之间的浓度梯度或压力梯度作为过程的推动力,而把其他影响参数都归纳于阻力之中,传递速率就成为推动力与阻力的商了。
上述两种工程处理方法所描述的过程,都称作平衡级分离过程。
分离行为在单级中进行时,往往着眼于气相或液相中粒子、离子、分子以及分子微团等在场的作用下迁移速度不同所造成的分离。
热扩散、反渗透、超过滤、电渗析及电泳等分离过程都属此类,称速率控制分离过程,都是很有发展潜力的新分离方法。
综上所述,分离过程得以进行的基础是在“场”的存在下,利用分离组分间物理或化学性质的差异,并采用工程手段使之达到分离。
显然,构思新颖、结构简单、运行可靠、高效节能的分离设备将是分离过程得以实施乃至完成的保证。
1.1.2 分离过程的地位广泛的应用、科技的发展、环境的需要都说明分离过程在国计民生中所占的地位和作用,并展示了分离过程的广阔前景:现代社会离不开分离技术,分离技术发展于现社会。
《化工分离工程》PPT课件大学课件
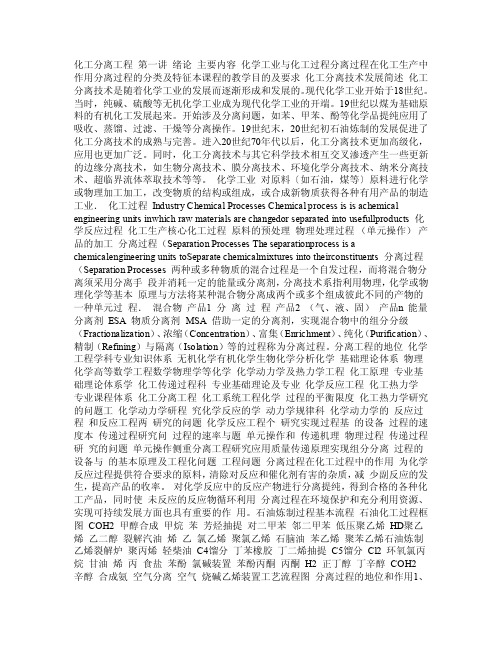
化工分离工程第一讲绪论主要内容化学工业与化工过程分离过程在化工生产中作用分离过程的分类及特征本课程的教学目的及要求化工分离技术发展简述化工分离技术是随着化学工业的发展而逐渐形成和发展的。
现代化学工业开始于18世纪。
当时,纯碱、硫酸等无机化学工业成为现代化学工业的开端。
19世纪以煤为基础原料的有机化工发展起来。
开始涉及分离问题,如苯、甲苯、酚等化学品提纯应用了吸收、蒸馏、过滤、干燥等分离操作。
19世纪末,20世纪初石油炼制的发展促进了化工分离技术的成熟与完善。
进入20世纪70年代以后,化工分离技术更加高级化,应用也更加广泛。
同时,化工分离技术与其它科学技术相互交叉渗透产生一些更新的边缘分离技术,如生物分离技术、膜分离技术、环境化学分离技术、纳米分离技术、超临界流体萃取技术等等。
化学工业对原料〔如石油,煤等〕原料进行化学或物理加工加工,改变物质的结构或组成,或合成新物质获得各种有用产品的制造工业.化工过程Industry Chemical Processes Chemical process is is achemical engineering units inwhich raw materials are changedor separated into usefullproducts 化学反应过程化工生产核心化工过程原料的预处理物理处理过程(单元操作)产品的加工分离过程(Separation Processes The separationprocess is a chemicalengineering units toSeparate chemicalmixtures into theirconstituents 分离过程(Separation Processes 两种或多种物质的混合过程是一个自发过程,而将混合物分离须采用分离手段并消耗一定的能量或分离剂,分离技术系指利用物理,化学或物理化学等基本原理与方法将某种混合物分离成两个或多个组成彼此不同的产物的一种单元过程.混合物产品1 分离过程产品2 (气、液、固)产品n 能量分离剂ESA 物质分离剂MSA 借助一定的分离剂,实现混合物中的组分分级(Fractionalization)、浓缩(Concentration)、富集(Enrichment)、纯化(Purification)、精制(Refining)与隔离(Isolation)等的过程称为分离过程。
化工原理分离工程知识点

化工原理分离工程知识点化工原理分离工程是化学工程中的一个重要分支,涉及到物质的分离、提纯和纯化等工艺。
分离工程的目的是通过物理或化学手段,将混合物中的不同成分分开,以满足产品质量要求,并实现资源的合理利用。
下面将介绍一些关于化工原理分离工程的知识点。
1.分离工程的分类:-相平衡分离工程:利用物理性质(如沸点、溶解度等)不同的物质在相平衡时的差异进行分离,包括蒸馏、萃取、结晶、吸附等。
-膜分离工程:利用半透膜对混合物进行分离,包括逆渗透、超滤、气体渗透等。
-色谱分离工程:利用分子在固定相上的吸附与解吸作用的不同,进行分离,包括气相色谱、液相色谱等。
-离子交换分离工程:利用离子交换剂对混合物中的离子进行选择性吸附和解吸,包括离子交换层析、电渗析等。
-超临界流体分离工程:利用超临界流体对混合物进行溶解和脱溶,包括超临界流体萃取、疏水液相色谱等。
2.蒸馏:-原理:利用混合物中组分的不同沸点差异,将其在不同温度下从液相转变为蒸汽相,再通过冷凝收集纯净的成分。
-分类:常压蒸馏、减压蒸馏、精馏、萃取蒸馏等。
-应用:石油分馏、酒精提纯、药物合成等。
-原理:利用两个不相溶液体相之间的互溶性差异,将所需组分从一个相转移到另一个相中,实现分离和纯化。
-分类:液液萃取、固液萃取、溶剂萃取等。
-应用:食用油提取、天然产物提纯、有机物合成等。
4.结晶:-原理:利用溶液中物质浓度的变化,在适当的条件下使溶质以晶体形式析出,实现分离和纯化。
-分类:汽提结晶、真空结晶、冷结晶等。
-应用:糖类、盐类、有机物的制备和纯化等。
5.吸附:-原理:利用固体表面对一些组分的选择性吸附作用,实现分离和纯化。
-分类:气相吸附、液相吸附、离子交换等。
-应用:含油气分离、环保废气处理、污水处理等。
6.膜分离:-原理:利用半透膜对混合物进行分离,使其中的一些组分通过膜而其他组分被截留。
-分类:逆渗透、超滤、气体渗透等。
-应用:海水淡化、废水处理、气体分离等。
化工分离工程知识点

化工分离工程知识点化工分离工程是化工工程中的一个重要领域,其主要任务是将混合物中的不同物质按照一定的条件和方法进行分离,以得到纯净的物质。
分离工程在化工生产中起着至关重要的作用,可以帮助提高产品的纯度、品质和收率,同时也可以实现资源的高效利用。
在化工分离工程中,有许多重要的知识点,下面将对其中的一些重要知识点进行详细介绍。
1.分离原理在化工分离工程中,常用的分离原理包括蒸馏、结晶、吸附、萃取、膜分离、离子交换等。
其中,蒸馏是最常用的一种分离方法,它利用不同物质的沸点差异将混合物中的成分进行分离。
结晶则是通过溶解度的差异将混合物中的成分分离出来。
吸附是利用吸附剂对混合物中的组分进行吸附而实现分离。
萃取是利用两种不相溶的溶剂将混合物中的成分进行分离。
膜分离是利用半透膜将混合物中的成分进行分离。
离子交换则是通过离子交换树脂将混合物中的离子进行分离。
2.蒸馏工程蒸馏是常用的分离方法之一,其主要原理是根据物质的沸点差异将混合物中的成分进行分离。
在蒸馏工程中,常见的设备包括塔式蒸馏塔、板式蒸馏塔、换热器、冷凝器等。
蒸馏工程的优点是操作简单、技术成熟、分离效果好,适用于对物质纯度要求较高的情况。
3.结晶工程结晶是将溶液中的溶质通过结晶过程沉淀出来的分离方法,其主要原理是通过温度变化或添加结晶剂来控制溶质的溶解度,从而实现溶质的分离。
在结晶工程中,通常使用的设备包括结晶槽、结晶釜、过滤机等。
结晶工程的优点是生产操作简单、设备投资较小、适用于对纯度和晶体形态要求较高的情况。
4.吸附工程吸附是利用吸附剂对混合物中的组分进行吸附而实现分离的方法,其主要原理是通过吸附剂表面的吸附作用将目标成分从混合物中吸附出来。
在吸附工程中,常用的设备包括吸附塔、吸附柱、吸附剂等。
吸附工程的优点是操作简单、分离效果好、适用于对成分含量要求较高的情况。
5.膜分离工程膜分离是利用半透膜将混合物中的成分进行分离的方法,其主要原理是根据分子大小、形状、电荷等特性使得不同的成分通过膜的选择性渗透从而实现分离。
化工分离工程
根据分子间作用力不同,汽相可分为以下三类 (1) 理想气体的混合物 此时,P-V-T关系服从理想气体定律
ˆV p fi i
ˆV 1 fi
(2-24)
pi Pyi
二、汽液平衡的分类与计算
⑴ 汽液平衡的分类
2.2 相 平 衡 关 系 的 计 算
(2) 实际气体的理想溶液(实际气体的理想 混合物)
x g x ( 2 11) gi i i i
二、相平衡常数和分离因子 yi 定义:K i xi
精馏、吸收:称汽液相平衡常数
液液萃取:液液相平衡常数(或分配系数)
Ki xi ij — i对j的相对挥发度 K j yj xj (或分离因子)
yi
三、用 Ki ,ij 表示平衡关系
ˆV f V fi i
ˆ V f V y f V Py fi i i i i
(3) 实际气体
(2-25)
Hale Waihona Puke 二、汽液平衡的分类与计算⑴汽液平衡的分类 与此类似,液相也可分为理想溶液和实际 溶液(与实际气体对应)两类,但不存在理 想气体那样的溶液。 对理想溶液 g i 1 则: ˆ L f 0 x p 0f 0 x (2-26) fi i i i i i 三类不同汽相和两类不同液相可以组合成 以下五类汽-液平衡系统,它们的平衡常数计 算如下:
fiL
fiV
Vi L ( P pi0 ) g i pi0fi0 化简得: K i exp V fi P RT
即
Ki g i fi
L
f (T , P , xi )
V i
二、汽液平衡的分类与计算
化工分离工程概述
化工分离工程概述1. 引言化工分离工程是化学工程中一项重要的技术领域,旨在通过各种分离技术将混合物中的组分分离出来,以获得纯度较高的化学品或纯净的溶剂。
分离工程在各个化工过程中起到关键作用,广泛应用于石油、化工、食品、医药等行业。
本文将对化工分离工程的概念、分类和常见的分离技术进行概述。
2. 化工分离工程的概念化工分离工程是指通过物理或化学方法,将化学反应或物理混合造成的组分相互分离的过程。
其目的是将混合物中的有用组分或纯度较高的物质分离出来,以满足工业生产中对纯净产品的需求。
化工分离技术不仅可以分离混合物中的两种或多种组分,还可以进行多级分离,使得产品的纯度更高。
3. 化工分离工程的分类化工分离工程根据不同的分离原理和应用领域可以分为多个分类,常见的分类包括以下几种:3.1 蒸馏分离蒸馏分离是化工中常用的分离技术之一,基于组分的汽液平衡和挥发性的差异,利用液体的汽化和冷凝过程实现组分的分离。
根据不同的蒸馏方式,可以将蒸馏分离分为常压蒸馏、减压蒸馏和精馏。
蒸馏分离广泛应用于石油精制、石油化工、化学制药等领域。
3.2 溶剂萃取分离溶剂萃取分离是利用两种不相溶的液体之间的亲疏性差异,将目标成分从一种溶液中分离出来的分离技术。
溶剂萃取分离通常涉及两个相,即萃取相和被萃取相。
常见的溶剂萃取方法有液液萃取、气液萃取和固液萃取。
溶剂萃取广泛应用于化工中的萃取、提纯和纯化过程。
3.3 结晶分离结晶分离是利用溶质在溶剂中的溶解度随温度变化的特点,通过控制温度和压力的变化,使溶质从溶液中结晶出来的分离技术。
结晶分离通常包括普通结晶、循环结晶和反溶剂结晶等方法。
结晶分离广泛应用于食品加工、医药制造等行业。
3.4 吸附分离吸附分离是一种将混合溶液中的目标物质吸附到固体吸附剂表面从而分离的技术。
吸附分离常见的方法有吸附柱、吸附塔和吸附床等。
吸附分离广泛应用于环保领域的废气处理、废水处理以及精细化工过程中。
4. 常见的化工分离技术除了以上提到的蒸馏、溶剂萃取、结晶和吸附分离技术外,化工分离工程还涉及其他常见的分离技术,例如萃取、析出、过滤、离心、膜分离等。
化工分离工程PPT课件
7.1.1 分离用膜和膜分离设备
一、膜种类
二
天然膜 生物膜
、
天然物质改性膜 人工膜 无机膜 金属膜
设 备
非金属膜 有机膜 均质膜
微孔膜
管卷板 式式框
式
非对称性膜
复合膜
离子交换膜
➢ 膜性能:
1.分离透过性
a. 透过通量
单位时间通过单位膜面积的物理量。
b. 分离效率 用截留率表示: (R)
截留率:表示膜对溶质的截留能力,可用
操作中:
阳膜中带负电荷的基团“R SO3 ” 吸引溶液中带正电荷的离子,排斥带负电荷 的离子;
阴膜中带正电荷的基团“R N (CH3 )3 ” 吸引带负电荷的离子,排斥带正电荷的 离子
这种现象称:反粒子迁移
即:与膜所带电荷相反的离子穿过膜的现象 称反粒子迁移。
+++++++++++
1
Na
新型分离技术
第一节 膜分离技术 第二节 吸附分离 第三节 反应精馏
第一节 膜分离技术
➢ 膜的作用:
选择渗透
➢ 适用:
1.热敏性物质 ——可常温操作
2.特殊溶液 ——可用于大分子、无机盐、蛋
白质溶液等
第一节 膜分离技术
7.1.1 7.1.2 7.1.3 7.1.4 7.1.5
分离用膜和膜分离设备 反渗透 超滤与微滤 电渗析 其它膜分离
J — 时间时的渗透通量 kg / m 2 h m — 率减系数(小数)
2. 物化稳定性
强度、耐温、耐压性等
二、分离设备 (1)板框式膜具
↑↑
(2)卷式膜具 由四层组成
化工分离工程正文
绪论一:分离工程在工业生产中的地位和作用:1.分离工程定义:将混合物分成组成互不相同的两种或几种产品的操作2.化工生产装置:反应器+分离设备+辅助设备(换热器、泵)3.分离工程重要性:(1)纯化原料:清除对反应或催化剂有害的杂质,减少副反应、提高收率。
(2)纯化产品:使未反应物质循环。
(3)环境治理工程:去除污染物。
4.分离工程发展现状:5.分离过程在清洁生产中的地位和作用:废物减少(分离系统有效分离和再循环)废物直接再循环+进料提纯+除去分离过程中加入的附加物质+附加分离与再循环系统二:传质与分离过程的分类和特征:1.过程:(1)机械分离:两相以上的混合物分离(过滤、沉降、离心分离、旋风分离、静电分离)(2)传质分离:均相混合物分离(精镏、吸收、结晶、膜分离、场分离、萃取、干燥、浸取、升华)△平衡分离过程:分离媒介(热、溶剂、吸附剂)使均相混合物变为两相体系,再以混合物中各组分在处于平衡的两相分配关系的差异实现分离。
(精镏、吸收、结晶、萃取、干燥、浸取、升华)△速率分离过程:推动力(浓度差、压力差、温度差、电位差),组分选择性透过膜,各组分扩散速度的差异实现分离(膜分离、场分离)三:分离过程的集成化:新型1.反应过程与分离过程的耦合:化学吸收、化学萃取、催化精镏、膜反应器2.分离过程与分离过程的耦合:萃取结晶、吸附蒸馏、电泳萃取3.过程的集成:传统分离过程的集成(共沸精镏—萃取、共沸精镏—萃取精镏)传统分离过程与膜分离的集成(渗透蒸发—吸附、渗透蒸发—吸收、渗透蒸发—催化精镏)膜过程集成(微滤—超滤—纳滤—反渗透)第一章蒸馏与精馏§1—1 概述一:蒸馏定义和特点:1.定义:混合物中各组分挥发度差异进行分离提纯。
2.特点:工艺流程短、使用范围广、工艺成熟;但能耗大(汽相再冷凝)二:分类:1.蒸馏方式:闪蒸、简单蒸馏、精馏、特殊精馏、反应精馏2.操作压力:加压蒸馏、常压蒸馏、真空蒸馏3.混合物组分:两组分精馏、多祖分精馏4.操作流程:间歇蒸馏、连续蒸馏三:精馏操作流程:精馏段精馏段提馏段图:连续精馏操作流程图:间歇精馏操作流程1—精镏塔 2—再沸器 3—冷凝器 1—精镏塔 2—再沸器 3—全凝器 4—观察罩 5—贮槽§1—2 简单蒸馏和闪蒸组分挥发度相差较大、分离要求低——预分离一:工艺流程:图:简单蒸馏图:平衡蒸馏(闪蒸)1—蒸馏釜 2—冷凝器 3—接受器 1—加热器 2—节流阀 3—分离器1.简单蒸馏:一次进料,馏出液连续出料(出料浓度逐渐降低),釜残液一次排放——压力恒定、温度变化2.平衡蒸馏:连续进料,连续出料(出料浓度恒定)——压力、温度恒定混合液→加热器→温度>料液泡点(分离器压力下)→节流阀(降压)→分离器→料液部分汽化、并在分离器中汽液分离(相平衡)二:原理:1.前提条件:理想物系——液相为理想溶液(拉乌尔定律);汽相为理想气体(道尔顿分压定律)2.原理:汽液共存区饱和蒸汽线(露点线)过热蒸汽区饱和液体线(泡点线)液相区图:苯—甲苯混合液的t—x—y图图:苯—甲苯混合液的x—y图图:简单蒸馏t—x—y图图:平衡蒸馏t—x—y图(1)简单蒸馏:任何瞬间,蒸汽与液相处于平衡。
- 1、下载文档前请自行甄别文档内容的完整性,平台不提供额外的编辑、内容补充、找答案等附加服务。
- 2、"仅部分预览"的文档,不可在线预览部分如存在完整性等问题,可反馈申请退款(可完整预览的文档不适用该条件!)。
- 3、如文档侵犯您的权益,请联系客服反馈,我们会尽快为您处理(人工客服工作时间:9:00-18:30)。
化工分离工程第一章绪论1.1概述1.1.1 分离过程的发展与分类随着世界工业的技术革命与发展,特别是化学工业的发展,人们发现尽管化工产品种类繁多,但生产过程的设备往往都可以认为是由反应器、分离设备和通用的机、泵、换热器等构成。
其中离不开两类关键操作:一是反应器,产生新物质的化学反应过程,其为化工生产的核心;-其中离不开两类关键操作:一是反应器,产生新物质的化学反应过程,其为化工生产的核心;-于是研究化学工业中具有共同性的过程和设备的规律,并将之运用于生产的“化学工程”这一学科应运而生。
分离过程可分为机械分离和传质分离两大类。
机械分离过程的对象都是两相或两相以上的非均相混合物,只要用简单的机械方法就可将两相分离,而两相间并无物质传递现象发生传质分离过程的特点是相间传质,可以在均相中进行,也可以在非均相中进行。
传统的单元操作中,蒸发、蒸馏、吸收、吸附、萃取、浸取、干燥、结晶等单元操作大多在两相中进行。
依据处于热力学平衡的两相组成不相等的原理,以每一级都处于平衡态为手段,把其他影响参数均归纳于效率之中,使其更符合实际。
它的另一种工程处理方法则是把现状和达到平衡之间的浓度梯度或压力梯度作为过程的推动力,而把其他影响参数都归纳于阻力之中,传递速率就成为推动力与阻力的商了。
上述两种工程处理方法所描述的过程,都称作平衡级分离过程。
分离行为在单级中进行时,往往着眼于气相或液相中粒子、离子、分子以及分子微团等在场的作用下迁移速度不同所造成的分离。
热扩散、反渗透、超过滤、电渗析及电泳等分离过程都属此类,称速率控制分离过程,都是很有发展潜力的新分离方法。
综上所述,分离过程得以进行的基础是在“场”的存在下,利用分离组分间物理或化学性质的差异,并采用工程手段使之达到分离。
显然,构思新颖、结构简单、运行可靠、高效节能的分离设备将是分离过程得以实施乃至完成的保证。
1.1.2 分离过程的地位广泛的应用、科技的发展、环境的需要都说明分离过程在国计民生中所占的地位和作用,并展示了分离过程的广阔前景:现代社会离不开分离技术,分离技术发展于现社会。
1.2 分离分子组分i和J的通用分高因一fαl11为二组分在严品l中的摩尔分率的比値除以在产品2中的比值。
显然,,r的单位可以用组分的质量分率、摩尔流量或质量流量,其所得的分离因子值不变。
1.3过程开发及方法(1)开发基础研究:针对项目的应用性基础研究和工艺特征研究,以实验室研究为主体(2)过程研究:进行工艺、产品、设备等的工程放大试验,包括模型试验、徽型中试、中间试验、原型装置试验及工业试验的全部过程或部分过程。
(3)工程研究:包括技术经济评价、概念设计、数学模型、放大技术及基础设计等所以,化工新技术开发不外乎三个关键环节:概念形成到课题的选定、技术与经济论证(可行性)和放大技术。
其中,放大技术是研究开发的核心。
1.逐级经验放大其基本步骤是:进行小试,确定操作条件和设备形式,以及可望达到的技术经济指标。
确定的依据是最终产品质量、产量和成本,并不考虑过程的机理。
小试之后进行规模稍大的中试,以确定设备尺寸放大后的影响(放大效应),然后才能放大到工业规模的大型装置。
2.数学模型方法此法基于对过程本质的深刻理解,将复杂过程分解为多个较简单的子过程,再根据研究的目的进行合理简化,得出物理模型。
1.4分离方法的选择1可行性要选择合适的分离方法,首先应考查它的可行性。
也就是说,应用该方法是否可能获得所期望的结果。
通过可行性判断,可以筛选合适的分离方法。
第二章精馏蒸馏(Distillation):借助液体混合物中各组分挥发性的差异而进行分离的一种操作方法。
简单蒸馏(simple distillation):混合液受热部分汽化,产生的蒸汽进入冷凝器种冷凝,分批收集不同组成的馏出液产品。
平衡蒸馏(equilibrium distillation):釜内液体混合物被部分汽化,使气相与液相处于平衡状态,然后将气相与液相分开,是一种单级蒸馏操作。
精馏(rectification):液体混合物多次进行部分冷凝或部分汽化后,最终可以在气相中得到较纯的易挥发组分,而在液相中得到较纯的难挥发组分。
精馏计算:物料衡算,热量衡算,相平衡关系计算方法:双组份常用图解法;多组分常用简捷法、严格计算法 普通精馏不适用下列物料的分离:(1)待分离组分间的相对挥发度很接近于1。
此时,它们的分离需要很多理论板数和很大的回流比,因此设备投资和操作费用很大,不经济。
一般认为,当分离所需的理论板数大于100时,精馏已不适用。
(2)待分离组分形成恒沸物,此时相对挥发度等于1,平衡的汽液两相组成一样,普通精馏无法实现分离。
(3)待分离物料是热敏性的,或是在高温下易发生聚合、结垢、分解等不良反应的。
(4)待回收的组分是难挥发组分,且在料液中含量很低。
此时能量消耗太大,不经济。
理论板、板效率和填料的理论板当量高度理论板:进入该板的不平衡的物流发生了充分的接触传质,离开了两相的物流间达到了平衡;在该板上发生传质接触的汽液两相各自完全混合,板上各点的汽相和液相浓度各自一样;该板上充分接触后的汽液两相实现了机械上的完全分离,离开该板的汽流中不夹带雾滴,液流中不夹带气泡,也不存在漏液。
板效率: 1*1++--=j jj j MV y y y y E式中,分子为汽相经实际板接触传质后的增浓值;分母则为经理论板后的增浓值;效率为两者之比值。
点效率、莫夫里板效率(干板效率)、湿板效率、总板效率理论板数只与相平衡关系、规定的分离要求和精馏操作参数(进料热状况、回流比和液气比)有关,表征物料达到规定分离要求的难易。
系统物性对板效率的影响液相粘度:粘度高产生的气泡大,两相接触差,液相扩散系数小,效率低; 相对挥发度:相对挥发度大则气相溶解度低,液相阻力大,板效率低; 表面张力:表面张力对板效率影响相当小。
二元精馏计算图解法:在x -y 图上作出平衡线和操作线、对角线和曲,精馏段在 精馏段操作线与平衡线之间画得的梯级即为精馏段的理论板数,在提馏段操作线与平衡线画出的梯级数为提馏段的理论板数。
汽液平衡关系;相邻两板之间汽液两相组成的操作关系;原料液的组成;进料热状况;操作回流比;分离程度精馏段各组分的摩尔汽化焓相等; 气液接触时因温度不同而交换的的显热可以忽略不计;塔的热损失可以忽略不计操作线方程 D x R x R R y )11()1(+++= 提馏段操作线方程 B BB B x V x V V y )1()1(-+= Feed stage considerations冷液进料、饱和液体、气液混合进料、饱和蒸汽进料、过热蒸汽进料 进料热状态参数q :和液体的摩尔焓饱和蒸汽的摩尔焓-饱料的摩尔焓饱和蒸汽的摩尔焓-原=qq 线方程:)1()1(---=q zx q q y F 平衡级与进料板位置的确定精馏的简捷计算(多组分精馏)关键组分:进料中按要求选取的两个组分(大多是挥发度相邻的两个组分它们对物料的分离起控制作用。
挥发度大的称为轻关键组分(LK ),它在塔釜中的浓度必须加以控制,不能大于某个规定值;两组分中挥发度大的称为重关键组分(HK ),为达到分离要求,它在塔顶产品中的含量必须加以控制。
料液中比轻关键组分更易挥发的组分为轻非关键组分(LNK ),简称为轻组分;比重关键组分更难挥发的组分称为重非关键组分(HNK ),简称为重组分。
在多组分精馏中,只在塔顶或塔釜出现的组分为非分配组分;而在塔顶和塔釜均出现的组分则为分配组分。
LK 和HK 肯定同时在塔顶和塔釜出现,是当然的分配组分。
多组分精馏过程特性:对二组分精馏,设计变量值被确定后,很容易用物料衡算式,汽液平衡式和热量衡算式从塔的任何一端出发作逐板计算,无需进行试差。
但在多组分精馏中,由于不能指定馏出液和釜液的全部组成,要进行逐板计算,必须先假设一端的组成,然后通过反复试差求解。
精馏塔的分离要求通常有两个,它们可以是产品的纯度和流量(或回收率),但至少有一个应是纯度。
多组分精馏与二组分精馏在含量分布上的区别:在多组分精馏中,关键组分的含量分布有极大值;非关键组分通常是非分配的,即重组分通常仅出现在釜液中,轻组分仅出现在馏出液中;重、轻非关键组分分别在进料板下、上形成几乎恒浓的区域;全部组分均存在于进料板上,但进料板含量不等于进料含量,塔内各组分的含量分布曲线在进料板处是不连续的。
在精馏塔中,温度分布主要反映物流的组成,而总的级间流量分布则主要反映了热量衡算的限制。
最小理论板数N min :精馏塔在操作过程中,将塔顶蒸气全部冷凝,其凝液全部返回塔顶作为回流,称此操作为全回流 (total reflux),回流比R 为无穷大 (R=∞)。
此时通常不进料,塔顶、塔底不采出。
故精馏塔内气、液两相流量相等,L = V ,两操作线斜率均为1,并与对角线重合。
由于全回流操作时,使每块理论板分离能力达到最大,完成相同的分离要求,所需理论板数最少,并称其为最小理论板数N min 。
芬斯克方程ABW BA DB A x xx x N αlg ])/()lg[(min =最小回流比Rmin :ee eD x y y x R --=m in恩特伍德方程(估算最小回流比):11--=-=-∑∑i iB DiiB m i iBFiiB x R q x θααθαα,,,,minlg[](1)(1)lg LK D HK WLK D HK W LK HKN ϕϕϕϕα*---=适宜回流比吉利兰关联式:⎥⎥⎦⎤⎢⎢⎣⎡⎪⎭⎫ ⎝⎛+--=+-5668.0min min1175.01R R R N N N多组分精馏的FUG 简捷计算方法①首先用芬斯克方程计算最少理论板数;②计算给定条件下的最小回流比;③应用吉利兰经验关联式估算所需理论板数。
FUG 法适合于新塔的设计计算,习惯需要指定以下三个变量:实际回流流率与最小回流流率之比;参考组分(通常是重关键组分)的切割程度;另一组分(通常为轻关键组分)的切割程度。
精馏的简捷计算例题-见课件严格的多组分精馏计算 精馏的定态数学模型MESH 方程:组分物料衡算(M ),相平衡关联(E ),摩尔分率加和归一(S ),热量衡算(H ) 组分物料衡算(M )方程: uij+wij+lij+vij-vi,j+1-li,j-1-fij=0 (i=1,…,c; j=1,…,N )相平衡关联(E 方程): (i=1,…,c; j=1,…,N )摩尔分率加和归一(S )方程: (j=1,…,N )热量衡算(H )方程:(j=1,…,N )为进行精馏的严格计算,除MESH 模型方程组外,K ij ,h j 和H j 的关联式必须知道。
ij jij ijjK V v l L =1ijij ij iiijjjl v f LV F ===∑∑∑1111()()0j j j j j j j j j j j Fj j U L h W V H V H L h F h Q ++--+++----=基于上述定态数学模型的操作型算法可归并为两大类:1)分块求解;2)联列解。