金属凝固组织的细化方法和机理
金属凝固组织的细化方法和机理-脉冲电场
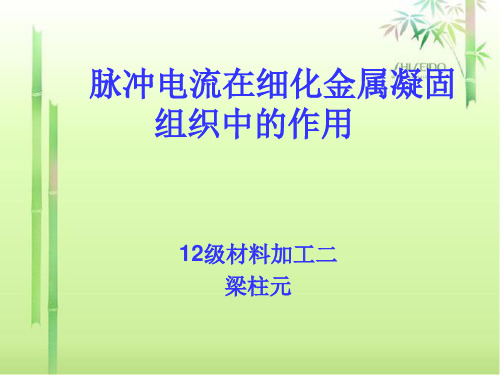
To find the best match to improve the refining efficiency.
I
II
III
IV
1— pulse generator; 2— digital oscillograph; 3 — copper strip; 4 — electrodes; 5 — sand mould; 6— sample.
熔融金属仍是一个电阻率为ρe的导 体,当电流通过时,电子与原子晶格发 生碰撞,产生热能,即焦耳热效应 Q=ρej2,从而导致熔体温度变 化:T=j2ρeτ/ρc 式中ρ—熔体密度; c—比热容; τ— 通电时间
• 产生两大作用:
• (1)对凝固体系来讲,焦耳热相当于内热源,它使 熔体整体冷速下降,过冷度减小。
• Barnak等对 Sn60%-Pb40% 合金进行了施加 电脉冲实验。 • 其研究结果表明, 随着电流密度的 增加和频率的减 小,共晶团尺寸 也大幅减小。
• Barnak.J.P 等人的研究 还表明随电 流密度增加, 过冷度ΔT也 随之增加 (如右图所 示)。
• 脉冲电流对金属凝固组织的研究是从低温合金 逐渐向高温合金过渡的。早期研究中,主要集 中在Pb - Sn 合金。
With Mode IV, the region of the equiaxed grains expanded further, and there are some fine equiaxed grains even near the top surface. The highest proportion (82%) of fine equiaxed grain area was obtained in Mode IV.
金属凝固理论原理及应用
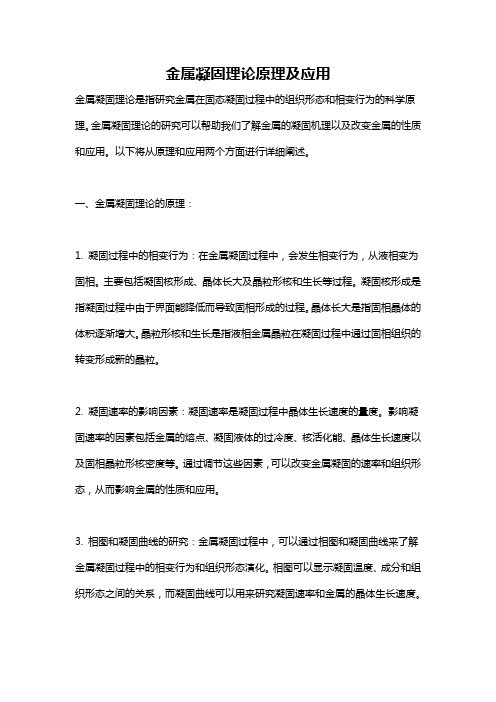
金属凝固理论原理及应用金属凝固理论是指研究金属在固态凝固过程中的组织形态和相变行为的科学原理。
金属凝固理论的研究可以帮助我们了解金属的凝固机理以及改变金属的性质和应用。
以下将从原理和应用两个方面进行详细阐述。
一、金属凝固理论的原理:1. 凝固过程中的相变行为:在金属凝固过程中,会发生相变行为,从液相变为固相。
主要包括凝固核形成、晶体长大及晶粒形核和生长等过程。
凝固核形成是指凝固过程中由于界面能降低而导致固相形成的过程。
晶体长大是指固相晶体的体积逐渐增大。
晶粒形核和生长是指液相金属晶粒在凝固过程中通过固相组织的转变形成新的晶粒。
2. 凝固速率的影响因素:凝固速率是凝固过程中晶体生长速度的量度。
影响凝固速率的因素包括金属的熔点、凝固液体的过冷度、核活化能、晶体生长速度以及固相晶粒形核密度等。
通过调节这些因素,可以改变金属凝固的速率和组织形态,从而影响金属的性质和应用。
3. 相图和凝固曲线的研究:金属凝固过程中,可以通过相图和凝固曲线来了解金属凝固过程中的相变行为和组织形态演化。
相图可以显示凝固温度、成分和组织形态之间的关系,而凝固曲线可以用来研究凝固速率和金属的晶体生长速度。
二、金属凝固理论的应用:1. 金属材料制备:金属凝固理论可以帮助我们了解金属材料制备过程中的相变行为和组织演化规律。
在铸造和凝固过程中,通过调节凝固速率和组织形态,可以获得不同性能和应用要求的金属材料。
例如,通过改变凝固速率可以获得细晶粒或均匀晶粒分布的材料,从而提高材料的强度和韧性。
2. 改善金属材料性能:金属凝固理论的研究可以帮助我们改善金属材料的性能。
例如,通过合适的添加剂和凝固工艺,可以改善金属材料的耐磨性、耐腐蚀性、高温稳定性等性能。
同时,金属凝固理论也可以指导材料加工过程中的热处理和冷处理,从而进一步提高金属材料的性能。
3. 金属合金设计:金属凝固理论是金属合金设计的重要基础。
通过研究金属合金的凝固机制和相图,可以合理地选择合金元素和调整合金成分,以达到特定的性能和应用要求。
金属的强化方法及机理
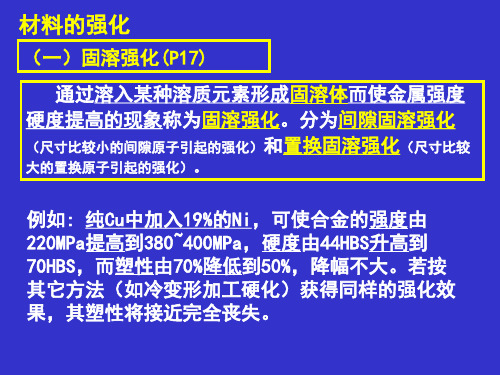
把某一成分的合金加热到固溶度曲线以B元 素析出,得到过饱和α固溶体,这就是固溶处理。
经固溶处理后的合金在室温下放置或加热到低于溶解度曲线的某 一温度保温,合金将产生脱溶析出,即B将以新相的形式从过饱和 α相中弥散析出,这个过程即是时效。通常将在室温下放置产生 的时效称为自然时效;将加热到室温以上某一温度进行的时效称 为人工时效。
金属材料经冷塑性变形后,其强度与硬度随变形 程度的增加而提高,而塑性、韧性则很快降低的 现象为加工硬化或形变强化。
例如:自行车链条板(16Mn钢板)
原始厚度3.5mm
150HB
五次冷轧后1.2mm 275HB
b=520MPa b>1000MPa
又如:冷拔高强度钢丝和冷卷弹簧是利用加工变 形来提高他们的强度和弹性极限;坦克和拖拉机 的履带、破碎机的颚板以及铁路的道叉等也都是 利用加工硬化来提高他们的硬度和耐磨性的。
实验证明,金属的屈服强度与其晶粒尺寸之 间有下列关系:
σs=σ0+ K/d1/2 此式称为霍耳-配奇公式。
式中:σ0 ——为常数,相当于单晶体的屈服强度; d——为多晶体中各晶粒的平均直径; K——为晶界对强度影响程度的常数, 与晶界结构有关。
σs ——开始发生塑性变形的最小应力
细晶强化机制:晶界是位错运动过程中的障碍。 晶界增多,对位错运动的阻碍作用增强,致使位 错在晶界处塞积(即位错密度增加),金属的强 度增加;在单个晶粒内部,塞积的位错群的长度 减小,应力集中较小,不足于使位错源开动,必 须增加外力。
2、加工硬化机制
金属的塑性变形是通过滑移进行的。在塑性变形 过程中,由于位错塞积(位错运动过程中遇到障 碍受阻)、位错之间的弹性作用、位错割阶等造 成位错运动受阻,从而使材料的强度提高。
金属凝固理论

20、液态金属的热速处理:
21、模数:折算厚度R=V1/S1,R又称为模数。
22、理想液态金属:指没有任何杂质及缺陷的纯金属熔体。
23、流动性:液态金属本身的流动能力,称为“流正常偏析相反的溶质分布情况,当k0<1时,表面或底部含溶质元素多,而中心部分或上部含溶质较少,这种现象称为逆偏折。
15、动态晶粒细化:动态晶粒细化方法主要是采用机械力或电磁力引起固相发生相对运动,导致枝晶破碎或与从型壁脱落,在液相中形成大量的晶核,达到细化晶粒的目的。
16、铸造应力:铸件在凝固及冷却过程中,由于线收缩及固态相变会引起体积的收缩或膨胀,而这种变化往往受到外界的约束或铸件各部分之间的相互制约而不能自由地进行,于是在产生变形的同时还产生应力。
30、规则共晶合金:也称非小面--非小面共晶,多由金属--金属或金属--金属间化合物相组成,该类合金在结晶过程中,共晶两相均具有非小面生长的粗糙界面。
8、成分过冷:这种由溶质再分配导致界面前方熔体成分及其凝固温度发生变化而引起的过冷称为成分过冷.
9、枝晶间距::枝晶间距指的是相邻同次分枝之间的垂直距离,实际上则用金相视野下测得的各相邻同次分枝之间距离的统计平均值来表示。是树枝晶组织细化程度的表征,枝晶间距越小,组织就越细密,分布于其间的元素偏析范围也就越小。
25、密度偏析:密度偏析,也称重力偏析,是液体和固体共存或者是相互不混合的液相之间存在着密度差时产生的化学成分不均匀现象,一般形成于金属凝固前或刚刚开始凝固时。
26、变质处理:变质处理就是向金属液体中加入一些细小的形核剂(又称为孕育剂或变质剂),使它在金属液中形成大量分散的人工制造的非自发晶核,从而获得细小的铸造晶粒,达到提高材料性能的目的。变质是通过改变晶体的生长机理,从而影响晶体形貌。
液态金属al凝固过程中大团簇结构的形成与演变机理

液态金属al凝固过程中大团簇结构的形成与演变机理
液态金属al凝固过程中,大团簇结构形成的机理主要包括两种:超熔滴结构的固化,在形成过程中存在的最稳定的各种局部结构之间的竞争。
演变机理包括:大团簇结构的生长和繁殖,以及与周围物质的相互作用和溶解。
超熔滴结构的固化是指在液态金属al的固化过程中,形成超
熔滴结构,即超过固态晶格范围的同种金属分子的团簇结构。
这种结构的形成是由于高温下分子间的相互作用使得分子间形成“友好团”,多个团簇结构相互作用后就会形成超熔滴结构,
这种结构在凝固的过程中会保留下来。
在形成过程中存在的最稳定的各种局部结构之间的竞争是指在液态金属al凝固过程中,因为各种局部结构分别具有不同的
能量相互竞争,所以在液态金属al固化时会同时出现多种不
同类型的局部结构。
这些结构之间会相互竞争并演化成为最终的大团簇结构。
大团簇结构的生长和繁殖是指在液态金属al凝固的过程中,
大团簇结构因为整体能量更稳定而不断生长和扩散。
同时,液态金属al中还存在着其他种类的团簇结构,这些团簇结构不
同于大团簇结构,其内部成分不同,因此会与大团簇结构相互作用,并对其进行繁殖和衰减。
与周围物质的相互作用和溶解是指在液态金属al凝固过程中,大团簇结构和其他团簇结构会不断与周围物质相互作用和溶解,
与周围物质的相互作用和溶解会影响这些团簇结构的演化和繁殖,最终效果会在大团簇结构的形态和结构上产生影响。
液态金属成型原理
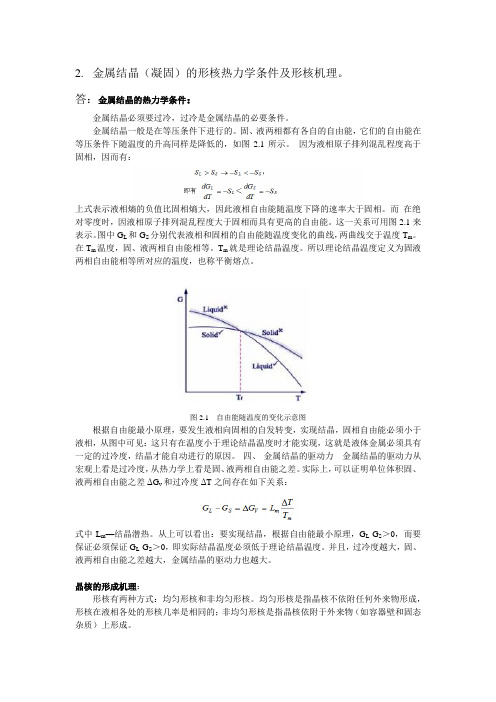
2. 金属结晶(凝固)的形核热力学条件及形核机理。
答:金属结晶的热力学条件:金属结晶必须要过冷,过冷是金属结晶的必要条件。
金属结晶一般是在等压条件下进行的。
固、液两相都有各自的自由能,它们的自由能在等压条件下随温度的升高同样是降低的,如图2.1所示。
因为液相原子排列混乱程度高于固相,因而有:上式表示液相熵的负值比固相熵大,因此液相自由能随温度下降的速率大于固相。
而在绝对零度时,因液相原子排列混乱程度大于固相而具有更高的自由能。
这一关系可用图2.1来表示。
图中G L和G S分别代表液相和固相的自由能随温度变化的曲线,两曲线交于温度T m。
在T m温度,固、液两相自由能相等。
T m就是理论结晶温度。
所以理论结晶温度定义为固液两相自由能相等所对应的温度,也称平衡熔点。
图2.1 自由能随温度的变化示意图根据自由能最小原理,要发生液相向固相的自发转变,实现结晶,固相自由能必须小于液相,从图中可见:这只有在温度小于理论结晶温度时才能实现,这就是液体金属必须具有一定的过冷度,结晶才能自动进行的原因。
四、金属结晶的驱动力金属结晶的驱动力从宏观上看是过冷度,从热力学上看是固、液两相自由能之差。
实际上,可以证明单位体积固、液两相自由能之差ΔG v和过冷度ΔT之间存在如下关系:式中L m—结晶潜热。
从上可以看出:要实现结晶,根据自由能最小原理,G L-G S>0,而要保证必须保证G L-G S>0,即实际结晶温度必须低于理论结晶温度。
并且,过冷度越大,固、液两相自由能之差越大,金属结晶的驱动力也越大。
晶核的形成机理:形核有两种方式:均匀形核和非均匀形核。
均匀形核是指晶核不依附任何外来物形成,形核在液相各处的形核几率是相同的;非均匀形核是指晶核依附于外来物(如容器壁和固态杂质)上形成。
形核时自由能的变化 在一定过冷度下,假设金属液相中形成一个圆形的固相小晶体(即晶胚),则其自由能的变化包括两个方面:一方面液相向固相转变,使自由能降低,这是结晶的驱动力;另一方面由于在液相中生成固相,出现液固界面,产生界面能,使自由能升高,这是结晶的阻力。
材料科学基础A习题答案第5章[1]解析
材料科学基础A习题第五章材料的变形与再结晶1、某金属轴类零件在使用过程中发生了过量的弹性变形,为减小该零件的弹性变形,拟采取以下措施:(1)增加该零件的轴径。
(2)通过热处理提高其屈服强度。
(3)用弹性模量更大的金属制作该零件。
问哪一种措施可解决该问题,为什么?答:增加该零件的轴径,或用弹性模量更大的金属制作该零件。
产生过量的弹性变形是因为该金属轴的刚度太低,增加该零件的轴径可减小其承受的应力,故可减小其弹性变形;用弹性模量更大的金属制作该零件可增加其抵抗弹性变形的能力,也可减小其弹性变形。
2、有铜、铝、铁三种金属,现无法通过实验或查阅资料直接获知他们的弹性模量,但关于这几种金属的其他各种数据可以查阅到。
请通过查阅这几种金属的其他数据确定铜、铝、铁三种金属弹性模量大小的顺序(从大到小排列),并说明其理由。
答:金属的弹性模量主要取决于其原子间作用力,而熔点高低反映了原子间作用力的大小,因而可通过查阅这些金属的熔点高低来间接确定其弹性模量的大小。
据熔点高低顺序,此几种金属的弹性模量从大到小依次为铁、铜、铝。
3、下图为两种合金A、B各自的交变加载-卸载应力应变曲线(分别为实线和虚线),试问那一种合金作为减振材料更为合适,为什么?答:B合金作为减振材料更为合适。
因为其应变滞后于应力的变化更为明显,交变加载-卸载应力应变回线包含的面积更大,即其对振动能的衰减更大。
4、对比晶体发生塑性变形时可以发生交滑移和不可以发生交滑移,哪一种情形下更易塑性变形,为什么?答:发生交滑移时更易塑性变形。
因为发生交滑移可使位错绕过障碍继续滑移,故更易塑性变形。
5、当一种单晶体分别以单滑移和多系滑移发生塑性变形时,其应力应变曲线如下图,问A、B中哪一条曲线为多系滑移变形曲线,为什么?应力滑移可导致不同滑移面上的位错相遇,通过位错反应形成不动位错,或产生交割形成阻碍位错运动的割阶,从而阻碍位错滑移,因此其应力-应变曲线的加工硬化率较单滑移高。
金属合金Bi-Te的介绍
第一章绪论液固遗传性在很久以前已经被认识[1]。
人们经过广泛地研究发现作为母相的液体结构和性质对凝固所形成的固体材料的结构和性能有重要影响[2, 3]。
生产中广泛应用的熔体过热处理能在很大程度上细化合金组织、提高力学性能[4-10],与此同时,熔体过热处理细化组织的机理也得到了较大的发展。
但不可否认的是,从控制熔体结构的角度来改善凝固组织仍然是经验性的,远远没有形成较为系统的理论。
众多科学家一致认为今后应该加强熔体过热对液态合金结构的影响和液态合金结构与凝固组织之间联系的研究,为制定更合理更有效的熔体过热处理工艺提供理论依据。
因此,作为涉及多学科交叉,有广泛应用背景的液态结构研究成为凝聚态物理在工业和理论领域中最热的课题之一[11-13]。
近来,对液态结构的研究已经取得重大进展,发现在一些纯金属和液态合金中存在液态结构转变[14-17],但结构转变对合金凝固影响的研究相对较少,本文从液态结构转变的角度出发,研究熔体热历史及相关处理工艺对凝固的影响。
鉴于本文工作内容主要针对液态合金结构与凝固的相关性,本章主要从熔体热历史及相关处理工艺对凝固影响的进展,包晶合金凝固的研究,物理场磁场在凝固过程控制中的应用及由此带来的一系列理论问题,以及热电材料的热电效应等几个方面来综述有关研究背景与进展,以阐明本文的研究内容及意义。
1.1液态金属的结构理论和研究方法到目前为止,人们对物质液态结构的认识远远落后于对固态和气态结构的认识。
几个世纪前,人们已经知道结晶固体是由在三维空间周期性(长程有序性)排列的原子所组成,并且晶体中的原子位置可以用X射线等衍射方法予以确定。
同样,气体热力学理论也早已解决了完全无序的气体本质。
而对长程无序短程却短程有序的液体结构的确定与描述目前仍不很成熟,直至今天关于液态结构的本质仍然存在很多不同的说法[18] 。
由于液态具有特殊的结构、性质和变化规律,众多研究学者开展了液态金属结构这方面的工作。
炼钢过程的物理化学基础
炼钢过程的物理化学基础
炼钢是将生铁或生铁合金通过冶炼、熔炼和精炼等过程,去除杂质和调整合金元素含量,制得具有一定化学成分和性能的钢材。
这个过程涉及多种物理和化学原理,其中一些重要的物理化学基础包括:
1.熔炼原理:
熔融与溶解:高温条件下金属原料被熔化,形成熔体。
在熔体中,不同金属元素能够相互溶解,形成合金体系。
相平衡与相图:钢铁冶炼中考虑不同金属之间的相平衡关系,例如铁碳相图,用于预测在不同温度下金属间的相变情况,指导生产实践。
2.去除杂质与精炼原理:
氧化还原反应:在炼钢过程中,通过氧化还原反应去除杂质。
例如,将氧气通过熔融金属,氧气与不纯净金属反应生成氧化物,再被去除,使金属中杂质减少。
渗碳原理:通过加入碳源(如石墨、焦炭等)来调整钢铁的碳含量,使其满足特定的技术要求。
3.结晶与晶体生长:
凝固过程:当熔体冷却至凝固温度以下时,金属开始凝固成晶体结构。
晶体的形成和排列方式直接影响钢材的力学性能。
晶粒粗化与细化:控制熔体冷却速率,可以影响晶粒的尺寸和形态,从而调节钢材的组织结构和性能。
4.热力学与动力学:
热力学平衡:针对炼钢过程中的温度、压力和化学反应等参数,
进行热力学平衡分析,确保炉内反应能够朝着预期的方向进行。
动力学控制:炼钢过程中,不仅需要考虑热力学平衡,还需考虑动力学控制,即控制熔体的流动和传热,以便有效地去除杂质、调整合金成分。
炼钢过程是一个复杂的物理化学过程,其中涉及多种物质相互作用和反应过程。
理解这些物理化学基础是确保钢铁冶炼过程高效、稳定和品质可控的关键。
快速凝固铝合金的组织与性能
快速凝固铝合金的组织与性能摘要:速凝固技术;过去对凝固过程的模拟只考虑在熔融状态下的热传导和凝固过程中潜热的释放,很少考虑金属熔体在型腔内必然存在的流动以及金属熔体在凝固过程中存在的流动,目前,快速凝固技术作为一种研制新型合金材料的技术一开始研究合金在凝固时的各种组织形态的变化以及如何控制才能到符合实际生活,生产要求的合金着重研究高的温度梯度和快的凝固速度的快速凝固技术正在走向逐步完善阶段。
快速凝固原理及凝固组织:快速凝固是指通过对合金熔体的快速冷却(≥104-106k/s)或非均质形核备遏制,是合金在很大过冷度下,发生高生长速率(≥1-100cm/s)凝固。
由于凝固过程的快冷,起始形核过冷度大,生长速率高是古冶界面偏离平衡,因而呈现出一系列于常规合金不同的组织和结构特征,加快冷却速度和凝固速率所应起的组织及结构特征可以近似用表来表示。
本实验利用真空系统下的金属熔液快速凝固装置,获得高真空后,充入一定压力的惰性气体,熔炼铝合金在熔融状态下以细直径金属液柱方式喷射到铜模具中,液流发生横向铺展并在纯铜模具中快速凝固。
由于整个过程的浇注时间在很大程度上被分散、延迟,热耗散可以快速、充分进行,从而可获得层状铝合金。
关键词:铜模具;射流沉积;亚稳块体材料;层状复合材料The Study on the Aluminum Alloy by Rapid Solidification Based on Reciprocate MotionCooling ModelAbstract:Rapid solidification is the way to get the non-steady state metal by the rapid cooling much more fast than the cooling rate for the equilibrium materials, and amorphous, nano-crystalline and some limiting structural or functional materials can be obtained.In this work, jet solidification in the cooling model with the computer controlled reciprocating motion protected under vacuum or inert gas was used to obtain the layer Al alloys. After the Al alloy was molten in a quartz tube, the alloy liquid was jet out ofa little hole under the tube inside a copper die by high pressure Ar gas, and alloy liquid lateral spread and solidify in the model. The process were repeated foe many times, and accumulation like a wall growing up. Since the pouring time of the entire process was delay and dispersed, heat was quickly and fully dissipated, so the bulk layer Al alloy was obtained. The alloy be with the high density and fine structure.Microstructure observation, hardness testing, tensile test were carried out for the alloy. The aluminum alloyBy precise control of the working parameter, the test was adjust to obtained the needed materials. The interface of multi-layer homogeneous composite was studied, such as superheat of the molten metal, the relationship between the liquid jetting parameters and solidification process, metallurgical complex process, heat dissipation process and control of the materials deposition growth process were also analyzed. The experiences was obtained for the fabrication of multi-layer deposition composites of high melting point metals and alloys.Keywords:reciprocating motion; jetting sediment; metestable bulk materials;composite materials目录第1章绪论 (1)1.1 引言 (1)1.2 铝合金及其主要分类 (1)1.2.1 铝合金的分类 (1)1.2.2 变形铝合金 (2)1.2.3 铸造铝合金 (2)第2章实验方法 (2)2.1实验原理 (2)2.2实验设备 (3)2.3实验过程 (4)第3章实验结果与讨论 (5)3.1铝合金试样的制备 (5)3.2层状铝合金的组织 (6)3.3硬度测试实验结果 (6)3.4快速凝固的冷速 (6)第4章结论 (7)第1章绪论1.1非晶材料简介非晶合金具有长程无序、短程有序的结构,与晶态合金相比,具备许多特有的性能,如高硬度、高强度、高电阻、耐蚀及耐磨等,为材料科研工作者开发高性能的功能材料和结构材料提供了巨大的潜力。
- 1、下载文档前请自行甄别文档内容的完整性,平台不提供额外的编辑、内容补充、找答案等附加服务。
- 2、"仅部分预览"的文档,不可在线预览部分如存在完整性等问题,可反馈申请退款(可完整预览的文档不适用该条件!)。
- 3、如文档侵犯您的权益,请联系客服反馈,我们会尽快为您处理(人工客服工作时间:9:00-18:30)。
课程名称:金属凝固指导老师:宋长江,翟启杰教授金属凝固组织的细化方法和机理摘要:金属组织细化细化是提高材料性能的一种有效手段。
在材料科学领域里,控制金属的凝固过程以细化金属凝固组织是提高铸件性能的重要途径之一,在已有的研究中,控制金属凝固过程以细化凝固组织的方法主要有两类:一是物理细化法,如低温浇注、电磁搅拌、机械振动、超声波细化等,二是化学细化法,如添加形核剂和长大抑制剂等。
物理细化方法处理材料纯净度高,不会对金属熔体带来外来夹杂,细化效果好;化学添加剂法细化效果稳定、作用快、操作方便、适应性强,是目前最普遍的细化方法。
关键词:组织细化;细化方法;细化剂;变质剂Refinement methods and mechanism of solidification structure of metalsAbstract: Metal microstructure refinement is an effective means to improve the properties of materials.In the field of meterial science, To contol the metal solidification process to refine the metal solidification structure is an important way of improving the casting performance. There are two main ways in the previous study: the first one is Physical refining method,such as cast cold, electromagnetic stirring, mechanical vibration, ultrasonic Refining and so on. The other one is chemical method, like the addition of nucleating agents and growth inhibitors. Physical refining method can make the material more pure,and there is no inclusion along with. The chemical method is the most common method of refinement because it’s faster and more stable and easy to operate.Key words:structure refinement; refine method; refiners; modifier1前言金属的性能在很大程度上取决于其凝固组织,因此细化凝固组织一直是材料科学领域的重要研究容,而控制金属凝固过程以细化金属凝固组织是改善铸件性能的重要手段之一。
在材料科学领域里,控制金属的凝固过程以细化金属凝固组织是提高铸件性能的重要途径之一,在现有的研究中,控制金属凝固过程以细化凝固组织的方法主要有两类: 一是物理细化法,如低温浇注、电磁搅拌、机械振动、超声波细化等;二是化学细化法,如添加形核剂和长大抑制剂等。
1984年,印度学者A K Misra[1~2]在三元合金Pb-15%Sb-7%Sn凝固过程中施加直流电,电流密度为30~40 mA/cm2,电压约为30 V,结果发现凝固后的组织得到了细化,并且第二相分布均匀1990年,M Nakada[3]等首次使用脉冲电流作用于Sn-Pb合金的凝固过程,试验发现,凝固后的组织大部分为球状等轴晶。
2007年,翟启杰等[4]研究了脉冲电流对纯铝凝固组织的影响,认定在凝固形核阶段施加脉冲电流可以显著细化纯铝凝固组织,而在液相线以上或晶粒长大阶段施加脉冲电流则没有明显细化效果。
目前人们采用了许多办法细化金属的晶粒。
细化晶粒的方法按照细化手段可以分为物理和化学两大类。
物理方法主要包括形变处理细化法、物理场细化、快速冷却法、机械物理细化法;化学方法可分为添加细化剂与添加变质剂方法。
2.物理细化法2.1 形变处理细化法形变处理细化利用各种塑形变形工艺,如轧制、挤压、锻造等,在加工过程中,通过温度、应变、应变速率等参数的配合,利用再结晶或者相变来控制变形态晶粒的尺寸。
由于传统的机械变形方法生产微米晶和微米晶材料往往受工件尺寸的限制,不能获得很大的变形量,例如,要求产品厚度为1mm , 则最大真应变量仅能达到3 ~4 mm,当制备亚微米细晶材料时就更加困难了。
为了突破总应变量的限制,很多不改变工件形状而获得大变形量的方法被开发出来,并得到了越来越多人的关注。
2.1.1 轧制细化轧制过程除了使轧件获得一定形状和尺寸之外,还必须使轧件具有一定的组织和性能。
温度是金属轧制过程中重要的工艺参数,然而轧制温度偏高,晶粒容易长大而使板材热脆倾向增大。
轧制温度偏低,高的应力集中可导致切变断裂;所以轧制温度应保证合金具有最大的塑性而不使其发生碎裂。
比如通过控制轧制快速冷却(TMCP)处理低碳钢,得到约5μm的细小α晶粒。
TMCP工艺由再结晶γ区轧制、未再结晶γ区轧制、( α +γ ) 二相区轧制和加速冷却4个阶段组成。
如图1所示TMCP各阶段是将α晶粒细化法妙地组合在一起,即在第一阶段(再结晶γ 区轧制),粗大的初始γ晶粒经反复轧制,再结晶细化;第二阶段(未再结晶γ区轧制)获得含位错和形变带的加工硬化状态γ组织;第四阶段通过加速冷却,使α相变在尽可能低的温度下进行。
其中,能最有效细化α晶粒的方法是在第二阶段的9 00~950 ℃轧制,以获得加工硬化的γ 组织。
TMCP 在热轧状态也能获得细小的α晶粒,然而,最小的α晶粒直径也在5 μ m左右。
图1 低碳钢TMCP(控轧、加速冷却)四个阶段及各阶段的组织Fig.1 Four stages during TMCP(controlled rolling accelerated colling) and their microstructures for low carbon steel长瑞等人[ 5 ]研究了AZ31镁合金板材在常温下的塑性变形行为,通过挤压-轧制方法获得了晶粒尺寸5 . 2 μ m的镁板。
研究结果表明:随着冷轧变形量的增加,晶粒尺寸减小;反之,晶粒的细化也可以使冷变形程度增加,两者存在相互依赖关系。
同时他们还发现小变形量、多道次冷轧可以提高板材两次退火间的总变形程度。
平等人[ 6 ]研究了利用道次间退火改善AZ31 镁合金的成形性,在变形速率0 . 0 1 /s 的实验条件下,确定合理的终轧温度为180 ~260℃,并获得了晶粒尺寸为6 . 9 μ m的A Z31镁合金。
2.1.2 挤压细化法挤压是对放在挤压模的锭坯一端施以挤压力,在强烈的三向压应力作用下,使之从挤压模孔中流出,从而成为具有一定形状、尺寸和性能的金属制品的一种压力加工方法。
挤压可以按金属的流向、挤压制品的形状、挤压时锭坯的温度以及挤压金属的种类进行分类。
按照在挤压时金属的流动方向与挤压杆的运动方向的关系,挤压主要分为正向挤压和反向挤压两种。
黄光胜[ 7 ]等在研究AZ 31 镁合金挤压工艺时发现在挤压过程中均发生了动态再结晶,组织以绝热剪切条纹和细小的α再结晶等轴晶为基本特征,呈现出良好的力学性能,其抗拉强度为2 75 ~285 N/mm2,屈服强度为220 ~225 N/ mm2伸长率为15 %~17 %。
大学的汪凌云[ 8 ]等人研究表明再结晶晶粒大小除了与温度有关,还与应变速率有关。
随着应变速率增高,变形过程中产生的位错来不及抵消,增加了再结晶形核位置,即位错的增加是晶粒细化的原因。
2.1.3 锻造细化影响产品韧性的重要因素之一是材料部的微观组织结构。
当成分确定之后,在生产过程中,锻造是能够有效细化晶粒的重要途径。
充分利用锻造高温形变的再结晶软化机制,利用合适的变形温度、均匀的变形分布以及其它热力学参数,可以获得满足产品性能要求的均匀细晶。
王淑云[ 9 ]等将T i - 47A l - 2Cr - 1 N b 经两次等温锻造和退火处理,使显微组织显著细化,得到晶粒尺寸为15 ~20 μ m 的细小、均匀的组织将7075[ 10 ]合金经多向反复热锻后可使7075铝合金的晶粒尺寸细化到1~2 μ m,由于晶粒的细化,锻件的力学性能有很大提高。
退火状态,其室温强度的增幅较大;淬火时效状态,塑韧性的提高十分显著,在保持较高强度的情况下,室温拉伸伸长率高于标准规定值的2倍,接近退火态水平。
X ing J 等[ 11 ]利用逐步降温多向锻造( multi -direction forging , MDF) 技术,在3 × 10-3s S-1的应变速率条件下,锻造温度从350 ℃ 逐步降低到150 ℃,使晶粒细化到了230 nm,得到了组织均匀的高性能AZ 31镁合金。
2.2 物理场细化法物理场对金属凝固作用的研究始于20世纪30年代,但由于当时物理、电子、材料技术的落后,物理场细化凝固组织的研究没有太大的发展。
20世纪末期后,随着科技的进步,特别是物理、电子、材料等领域的快速发展,使得大功率电流、磁场、超声波的产生变成可能,目前利用物理场控制凝固组织、细化铸件晶粒、提高铸件质量的研究主要在三个方面:( 1 ) 脉冲电流处理;( 2 ) 磁场处理;( 3 ) 超声波处理。
2.2.1 脉冲电流处理脉冲电流可有效地促进金属液生核(装置如图2所示),脉冲电流可以减少形核势垒而增大形核率,从而细化凝固组织。
脉冲电流的充放电过程还可以在金属液中造成收缩力,而且在金属液的不同位置,这种收缩力大小不一样,从而使得熔体不同位置的流动速度不同。
根据牛顿粘性定律,速度梯度的形成会导致产生剪切应力,当对凝固过程中的金属液施加高压脉冲电流或高频脉冲电流时,产生的剪切力将会撕裂凝固过程中出现的柱状晶,使其成为等轴晶的晶核[ 12 ]。
速度梯度形成的对流作用会使其弥散分布于熔体中,从而得到细小均匀的晶粒组织。
试验表明,脉冲电流的频率和电压对凝固细晶效果均有影响,且凝固细晶效果随着脉冲电流频率和电压的提高而增强,但是二者哪个起主导作用,因合金材料及频率和电压围的不同而异。
图2 电脉冲实验装置示意图Fig.2 Schematic diagram of experimental apparatus electropulsing回顾以往研究者对脉冲电流作用下的金属凝固研究,对于凝固组织细化的现象和规律的认识已取得长足进展。