PDC钻头CAD系统研究与开发_鲁桂荣
定向井PDC钻头受力模型及优化设计研究的开题报告

定向井PDC钻头受力模型及优化设计研究的开题报告一、研究背景及意义随着石油工业的不断发展,定向井(包括水平井、斜井等)越来越被广泛应用,因其可以在较小的区域内获得更多的储层资源。
然而,定向井钻井难度较大,在钻井时需考虑钻头受力问题,以避免钻头磨损过快甚至失效。
因此,钻头的设计和优化在定向井钻井中显得尤为重要。
目前,钻头主要分为钻十字头和PDC钻头两种。
由于它们的结构和性能不同,导致受力情况和钻速不同,因此需要研究它们的受力特性,并对其进行优化设计,以提高钻进效率和降低钻井成本。
二、研究内容1. 建立定向井PDC钻头受力模型通过分析定向井钻井过程中的载荷、钻头结构和磨损机制等因素,建立PDC钻头在定向井钻井中的受力模型,揭示其受力分布、载荷分布、切削力分布等特征,为优化设计提供基础数据。
2. 优化设计PDC钻头基于受力模型,优化设计PDC钻头结构和参数,提高其钻进效率、降低其磨损率、延长其使用寿命,从而降低钻井成本。
3. 验证模型和设计的可行性通过实际定向井钻井试验,验证模型和设计的可行性和实用性,进一步提高优化设计的合理性和有效性。
三、研究方法1. 数值模拟法通过有限元方法和计算流体力学方法,建立PDC钻头在定向井钻井中的数值模型,分析其受力分析和动力学特性,进而揭示其磨损机制。
2. 实验验证法通过定向井钻井试验,采集实验数据,验证数值模拟方法的准确性和优化设计的可行性,进一步提高优化设计的实用性和可靠性。
四、预期成果1. 建立定向井PDC钻头受力模型,揭示其受力分布和切削特征。
2. 优化设计PDC钻头结构和参数,提高其钻进效率、降低其磨损率、延长其使用寿命,降低钻井成本。
3. 验证模型和设计的可行性和实用性,进一步提高模型和设计的准确性和可靠性。
五、研究难点1. 定向井钻头的受力模型建立较为复杂,需要考虑多种因素的影响。
2. PDC钻头结构和参数的优化需要同时考虑多个因素,因此具有较高的难度。
浅析小井眼高效PDC钻头在苏南区块的应用

210研究与探索Research and Exploration ·工程技术与创新中国设备工程 2021.06 (上)1 概述苏里格南区块为长庆油田公司与法国道达尔公司共同投资开发的合作项目,该区块位于内蒙古自治区鄂托克前旗南部地区,属于鄂尔多斯盆地天环坳陷构造。
为了减少建井成本,建设方在该区块全部采用小井眼钻井。
苏南区块二开井段的延长组底部、和尚沟组上部可能含有砾石,易对PDC 钻头造成崩齿失效;刘家沟组为砂泥岩互层,较为致密,地层压实强度高,影响机速;石盒子组上部以泥岩为主、下部以砂岩为主的砂泥岩互层,部分区域下部地层含有石英砂岩,研磨性较强;本溪组、马家沟组存在硬质泥岩、灰岩、白云岩地层,可钻性。
2 施工难点(1)二开井段为安定组-马家沟组,表层采用Φ215.9mm 钻头,二开使用Φ152.4mm 钻头,表层井深一般为650~750m,二开裸眼段长达3200~3400m,由于刘家沟组为砂泥岩互层,较为致密,地层压实强度高,PDC 钻头的磨损比较严重,机速影响较大。
(2)由于小井眼井环空比较小,如果岩屑上返不及时,容易造成钻头泥包,这与排屑槽的流量分配及流速分布与水眼的孔径及数量和排屑槽的面积等息息相关,需要对整个井底流场进行分析,避免大范围低速区域及可能会出现漩涡回流区,影响该区域的岩屑运移,避免钻头泥包。
(3)小井眼井的井斜掌控难度比较大,对于钻头的稳定性要求比较高,需要对头型、布齿、保径等进行合理优化,在保证稳定性的情况下,提升机械钻速。
3 小井眼高效钻头设计针对苏南区块小井眼裸眼段长、地层可钻性差等特点,分别研制了152.4mm4刀翼PDC 钻头和5刀翼PDC 钻头。
4刀翼钻头设计:钻头为钢体设计,采用φ16mmZC-Ⅵ型主切削复合片,φ13mm 副切削齿结构,能够精准控制复合片吃入地层深度,提高滑动效率。
设计了中短抛物线平缓头型,综合力平衡设计和三维受力分析,提高钻头稳定性,适应配合螺杆钻具进行高转速钻进;针对小井眼井段段环空小,泥浆排量小的特点,采用中低密度布齿,减小复合片角度增强钻头攻击性,提高钻头切削效率;加密聚晶与倒划眼设计,预防缩径,保证井眼轨迹。
PDC钻头优化设计与CAD系统软件开发
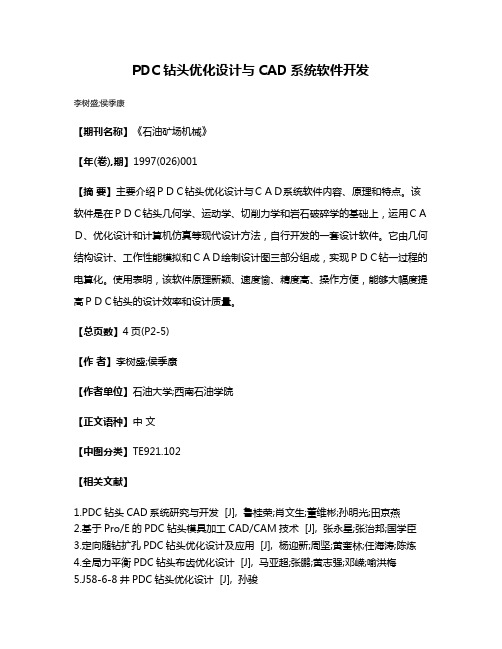
PDC钻头优化设计与CAD系统软件开发
李树盛;侯季康
【期刊名称】《石油矿场机械》
【年(卷),期】1997(026)001
【摘要】主要介绍PDC钻头优化设计与CAD系统软件内容、原理和特点。
该软件是在PDC钻头几何学、运动学、切削力学和岩石破碎学的基础上,运用CAD、优化设计和计算机仿真等现代设计方法,自行开发的一套设计软件。
它由几何结构设计、工作性能模拟和CAD绘制设计图三部分组成,实现PDC钻一过程的电算化。
使用表明,该软件原理新颖、速度愉、精度高、操作方便,能够大幅度提高PDC钻头的设计效率和设计质量。
【总页数】4页(P2-5)
【作者】李树盛;侯季康
【作者单位】石油大学;西南石油学院
【正文语种】中文
【中图分类】TE921.102
【相关文献】
1.PDC钻头CAD系统研究与开发 [J], 鲁桂荣;肖文生;董维彬;孙明光;田京燕
2.基于Pro/E的PDC钻头模具加工CAD/CAM技术 [J], 张永星;张治邦;国学臣
3.定向随钻扩孔PDC钻头优化设计及应用 [J], 杨迎新;周坚;黄奎林;任海涛;陈炼
4.全局力平衡PDC钻头布齿优化设计 [J], 马亚超;张鹏;黄志强;邓嵘;喻洪梅
5.J58-6-8井PDC钻头优化设计 [J], 孙骏
因版权原因,仅展示原文概要,查看原文内容请购买。
面向PDC钻头的三轴数控机床改进模块研究
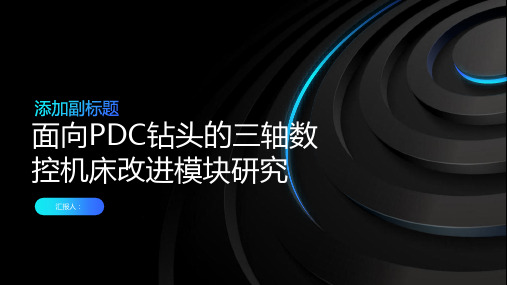
自动化:PDC钻 头加工需要自动化 的机床来降低人工 成本和提高生产效
率
添加标题
添加标题
添加标题
添加标题
改进模块的具体需求分析
提高加工精度:改进模块需要提高三轴数控机床的加工精度,以满足PDC钻头的高精 度要求。
提高加工效率:改进模块需要提高三轴数控机床的加工效率,以缩短PDC钻头的加工 时间。
降低成本:改进模块需要降低三轴数控机床的制造和维护成本,以降低PDC钻头的生 产成本。
提高可靠性:改进模块需要提高三轴数控机床的可靠性,以减少PDC钻头的废品率。
改进模块的设计 与实现
改进模块的整体设计方案
设计目标:提高 PDC钻头的加工
精度和效率
设计方案:采用三 轴数控机床进行加
工
模块组成:包括主 轴、进给系统、控
寿命
改进模块的局限性 在于需要更多的调 试和优化才能达到
最佳效果
添加标题
添加标题
添加标题
添加标题
结论与展望
研究结论总结
改进模块提高 了PDC钻头的 加工精度和效 率
改进模块降低 了PDC钻头的 加工成本
改进模块提高 了PDC钻头的 使用寿命
展望未来,改 进模块将在更 多领域得到应 用和发展
01
0 2
高精度:PDC钻头加工需要高 精度的机床和刀具,以保证钻 头的尺寸和形状精度。
高稳定性:PDC钻头加工需要 高稳定性的机床和刀具,以保
证钻头的质量和使用寿命。
环保性:PDC钻头加工需要环 保的机床和刀具,以减少环境
污染和符合环保要求。
三轴数控机床的 改进需求
三轴数控机床现有技术的不足
加工精度不足:现有技术 难以满足高精度加工需求
国标-》新型PDC钻头设计及应用

孙明光(|j9剂石油管哩国摘要P OC钻头在钻井破岩中所占的比蝌越来越大,但在软硬交错的多夹层地层钻进时效果却不理想,常常发生先期损坏。
本文针对胜利油田多夹层地层栈点进行了P DC钻头的优化设i十‟根据该设计制造的一种新型复合式P Dc钻头在多彳层挝L层中取得了轼好的应用竞贮果。
与牙轮钻头相比,复合PDC钻头机榭}阽速高,寿命长,进尺多等特点,对船∞由田勘探开发速度、降低钻井成本有积极的意义c主黝PDC钻头谢十桃嬲牙}徽谶作者简介孙明光,1965年生。
1994年毕业于石油大学北京研究生院石油工程专业,获硕士鞘立,1999年毕业于西南石浊学院机械谢十及理论专业,获博士前言早4E 80年f{=中期,胜乖蝣由田就开始试用P D C钻头,但只在渤南等少数地层岩|生柜对较为埝质的地因驭}导了鞍好的效果,在H烯0油阳大部分地区鼎卜一直没有好的指标和效益其主要原因在于胜利油田大多数I电l动电J犁i雯=勾复杂,夹层较多且软哽交瞧使常规P D c钻头钻进时,庄隆籍9躺坏而影响其使用寿命。
本文针对胜f蛐罔地层榻髓行了专题研究,设计了一种适合多夹层地层的新型复合PDc钻头,为提高胜利油田的钻井速度、降低钻井成本提供了有效的破岩二[具。
1常规PDc钻头的损坏特征从回收使用过PDC钻头来看,绝大部分I,DC钻头损坏的主要特征为齿柱折断、复合片碎裂、掉片、冲蚀、钻头基体冲蚀等现象,从POC钻头的损坏特征来看,POC 钻头在井下工作时,除了正常的切削地层而受到的反作用力和地层岩石磨损外,还受到了额外作用力的影响,这个额外作用力是造成P DC钻头非正常损坏的主要原因。
在统计和分析P OC钻头的使甩睛况后,结合P E C钻头使用的地区和地层层段,认为P OC钻头的损坏有下面几点原因:1)、地层硬夹层较多。
地层中硬夹层较多是P OC钻头上复合片碎裂、掉片或齿拄式切削齿断裂的主要原因,因为P Dc钻头在钻进过程中,从软地层钻至硬夹层时,由于PDC钻头冠部轮廓胗趺使得钻头表面的切削齿接触地层的硬度不一叶筝,造成切削齿切削地层时受力不均,造成钻头出现蹩钻跳钻现象,作用在钻头上的载荷大部分集中在切削硬夹层的几介切削齿上,蹩钻跳钻产生的瞬时载荷导致这几个切削齿因受力较大而碎裂或折断(特别是在切削硬地层中某些硬质点时,瞬时产生的载荷足队造成了切削齿的碎裂或切削齿折断)。
PDC钻头模具三维设计和数控加工技术研究与应用

PDC钻头模具三维设计和数控加工技术研究与应用摘要本文对PDC钻头模具三维设计和数控加工一体化技术的方法、步骤和相关工艺技术进行了研究。
解决了PDC钻头模具辅助设计二维数据的三维转化问题,提出了模具三维造型和参数化开发的方法,并应用CAD/CAM系统软件PRO/E建立了PDC钻头模具三维模型,应用PRO/PROGRAM(程序)开发模块进行PDC钻头模具造型的参数化开发,并编制了相应的参数化开发软件,提高了PDC钻头模具造型速度和准确性。
在建立PDC钻头模具三维造型的根底上,确定了模具数控加工工艺,摸索出一套利用PRO/E软件进行PDC钻头模具计算机辅助制造的方法和步骤,实现了PDC钻头模具一次装卡、一次成形的高精度自动化数控加工技术。
关键词 PDC钻头模具三维设计数控加工技术 CAD/CAM 聚晶金刚石复合片钻头(简称PDC钻头)由钻头体、接头组成,根据钻头体按材料的不同分为胎体PDC钻头和钢体PDC钻头。
胎体PDC钻头的钻头体是采用铸造碳化钨粉和浸渍料经无压浸渍烧结而成的。
钻头体形状是通过模具的形状而间接实现的。
模具由底模、中模和上模三局部组成。
模具的中模和上模的设计与加工都很容易实现。
但底模是具有复杂曲面特征的实体,PDC钻头的冠部形状参数、切削齿位置和方向参数、水力结构参数等都是通过底模的形状来实现的。
因此底模的设计和加工是模具设计和加工中最重要的一局部,其设计的好坏和加工的精度都直接关系到钻头的最终使用效果。
高质量的模具是保证PDC钻头质量的关键因素之一。
目前国内PDC钻头模具的形成主要有三种方法。
第一种(应用最多的,如以下列图)是利用普通车床车削形成钻头冠部形状,依靠分度头手工划线定位、普通万能铣床铣削完成切削齿和水眼的加工,再通过手工修模完成水力结构的造型等多道工序完成的。
这种加工方法的缺点是工人劳动强度大、加工精度低、人为误差大,难以控制和保证质量,很难到达设计的要求。
第二种是数控加工,利用数控机床加工形成钻头的冠部形状和切削齿的定位,然后再通过手工修模或者粘上相应形状成形的水力结构(粘上以后也要进行一定的手工修理)而最后形成模具的。
PDC钻头综合受力模型的试验研究
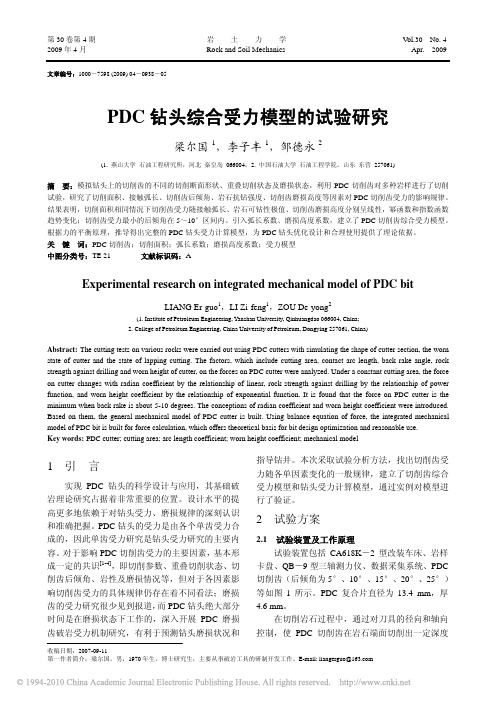
900
—切向力
750
—轴向力
600
450
300
150
0 0 5 10 15 20 25 30 A /mm2
图 6 磨损齿受力 F/μ f 与 切 削 面 积 A 关 系 Fig.6 The relationship between force of cutters worn
(F/μ f ) and cutting area (A)
摘 要:模拟钻头上的切削齿的不同的切削断面形状、重叠切削状态及磨损状态,利用 PDC 切削齿对多种岩样进行了切削
试验,研究了切削面积、接触弧长、切削齿后倾角、岩石抗钻强度、切削齿磨损高度等因素对 PDC 切削齿受力的影响规律。
结果表明,切削面积相同情况下切削齿受力随接触弧长、岩石可钻性极值、切削齿磨损高度分别呈线性,幂函数和指数函数
1引言
实现 PDC 钻头的科学设计与应用,其基础破 岩理论研究占据着非常重要的位置。设计水平的提 高更多地依赖于对钻头受力、磨损规律的深刻认识 和准确把握。PDC 钻头的受力是由各个单齿受力合 成的,因此单齿受力研究是钻头受力研究的主要内 容。对于影响 PDC 切削齿受力的主要因素,基本形 成一定的共识[1-4],即切削参数、重叠切削状态、切 削齿后倾角、岩性及磨损情况等,但对于各因素影 响切削齿受力的具体规律仍存在着不同看法;磨损 齿的受力研究很少见到报道,而 PDC 钻头绝大部分 时间是在磨损状态下工作的,深入开展 PDC 磨损 齿破岩受力机制研究,有利于预测钻头磨损状况和
area in general cutting
940
岩土力学
2009 年
3.1.2 接触弧长对切削齿受力的影响 重叠切削状态下切削齿切削岩样产生各种不规
PDC_钻头钻井提速关键影响因素研究
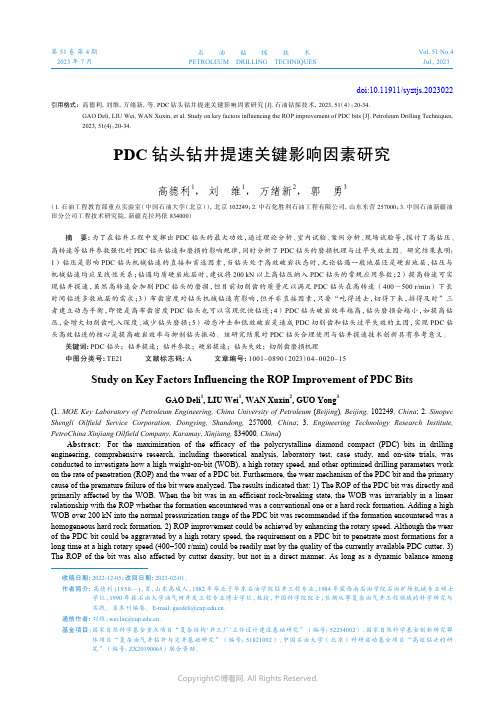
第 51 卷 第 4 期石 油 钻 探 技 术Vol. 51 No.4 2023 年 7 月PETROLEUM DRILLING TECHNIQUES Jul., 2023doi:10.11911/syztjs.2023022引用格式:高德利,刘维,万绪新,等. PDC钻头钻井提速关键影响因素研究[J]. 石油钻探技术,2023, 51(4):20-34.GAO Deli, LIU Wei, WAN Xuxin, et al. Study on key factors influencing the ROP improvement of PDC bits [J]. Petroleum Drilling Techniques,2023, 51(4):20-34.PDC钻头钻井提速关键影响因素研究高德利1, 刘 维1, 万绪新2, 郭 勇3(1. 石油工程教育部重点实验室(中国石油大学(北京)),北京 102249;2. 中石化胜利石油工程有限公司,山东东营 257000;3. 中国石油新疆油田分公司工程技术研究院,新疆克拉玛依 834000)摘 要: 为了在钻井工程中发挥出PDC钻头的最大功效,通过理论分析、室内试验、案例分析、现场试验等,探讨了高钻压、高转速等钻井参数强化对PDC钻头钻速和磨损的影响规律,同时分析了PDC钻头的磨损机理与过早失效主因。
研究结果表明:1)钻压是影响PDC钻头机械钻速的直接和首选因素,当钻头处于高效破岩状态时,无论钻遇一般地层还是硬岩地层,钻压与机械钻速均应呈线性关系;钻遇均质硬岩地层时,建议将200 kN以上高钻压纳入PDC钻头的常规应用参数;2)提高转速可实现钻井提速,虽然高转速会加剧PDC钻头的磨损,但目前切削齿的质量足以满足PDC钻头在高转速(400~500 r/min)下长时间钻进多数地层的需求;3)布齿密度对钻头机械钻速有影响,但并非直接因素,只要“吃得进去,切得下来,排得及时”三者建立动态平衡,即便是高布齿密度PDC钻头也可以实现优快钻进;4)PDC钻头破岩效率越高,钻头磨损会越小,如提高钻压,会增大切削齿吃入深度、减少钻头磨损;5)动态冲击和低效破岩是造成PDC切削齿和钻头过早失效的主因,实现PDC钻头高效钻进的核心是提高破岩效率与抑制钻头振动。
- 1、下载文档前请自行甄别文档内容的完整性,平台不提供额外的编辑、内容补充、找答案等附加服务。
- 2、"仅部分预览"的文档,不可在线预览部分如存在完整性等问题,可反馈申请退款(可完整预览的文档不适用该条件!)。
- 3、如文档侵犯您的权益,请联系客服反馈,我们会尽快为您处理(人工客服工作时间:9:00-18:30)。
收稿日期:2007-11-12作者简介:鲁桂荣(1982-),女,湖南常德人,硕士,现主要从事钻井设备的CAD 设计及仿真分析等方面的研究,E -mail :lg r0811@163.co m 。
文章编号:1001-3482(2008)05-0022-06PDC 钻头CAD 系统研究与开发鲁桂荣1,肖文生1,董维彬2,孙明光3,田京燕3(1.中国石油大学(华东)机电工程学院,山东东营257061;2.武汉市江汉石油机械有限公司,武汉430040;3.胜利石油管理局钻井工艺研究院,山东东营257017)摘要:借助Visual C ++6.0软件和Pro /ENGIN EE R 二次开发工具Pro /TOO LKIT 开发了集参数化设计、自动装配和数据管理于一体的PDC 钻头CAD 系统。
介绍了面向对象———PDC 钻头CAD 系统的总体技术,给出了其体系结构,建模、装配、数据管理等子系统的构成和功能,分析了PDC 钻头参数化和智能布齿设计的关键技术及解决方案。
该系统将有助于改变国内钻头产品的设计研制思路,缩短开发周期,提高国内钻头产品的设计水平。
关键词:Pro /ENGINEER ;PDC 钻头;参数化设计;布齿设计;CAD中图分类号:T E921.102 文献标识码:A Study and Development of PDC Bit C AD S ystemLU Gui -rong 1,XIAO Wen -sheng 1,DONG Wei -bin 2,S UN M ing -g uang 3,TIAN Jing -yan3(1.College o f Mechanical and E lectronic Engineering ,China University of Petroleum ,Dongy ing 257061,China ;2.Wuhan J ianghan Petroleum Machinery Co .,Ltd ,Wuhan 430040,China ;3.D ri lling T echnology ResearchI nstitute ,S hengli Petroleum Ad ministration ,Dongy ing 257017,China )A bstract :A n CAD sy stem fo r PDC Bit is developed using Visual C ++6.0and Pro /TOOLKIT ,the system is integrated with paramete r design ,autom atic assembly and data management .The structures o f PDC bit CAD sy stem are introduced .This sy stem co nsists of some subsy stem s in -cluding g eneral project desig n sy stem ,m odule desig n system ,assem bly sy stem and data manage -m ent system .The structures and functions of these subsy stems a re presented .The key tech -nique s and metho ds o f PDC bit 's parame ter desig n and intelligent too th arrangement a re dis -cussed .Key words :Pro /ENGIN EER ;PDC Bit ;parameter desig n ;CAD 我国的PDC 钻头生产技术与国外相比有很大差距,基础设计基本上还停留在二维设计阶段,设计过程繁琐、效率低,极大地制约了国产PDC 钻头的产品质量和进一步发展[1]。
参数化设计实现了驱动零件尺寸的设计修改,通过变动某些约束参数就能设计出一簇产品模型,对加快产品开发周期,提高设计效率有极大的影响。
PDC 钻头属于标准化、系列化和通用化程度较高的定型产品,可通过开发CAD 系统来实现其参数化设计[2],达到提高设计效率和产品质量的目的。
近年来,国内开始涉及计算机辅助PDC 钻头设计的研究[3-5],并开发了一些用于PDC 钻头设计的软件系统[6],但系统功能大都比较简单,智能化程度低,且不具备参数化设计功能,实用性不强。
基于 2008年第37卷 石油矿场机械 第5期第22页 OIL FIELD EQUIPMENT 2008,37(5):22~27 此,借助Visual C ++6.0软件和Pro /ENGINEER 二次开发工具Pro /TOOLKI T 开发了PDC 钻头CAD 系统,实现了PDC 钻头的参数化设计。
1 PDC 钻头设计流程PDC 钻头冠部轮廓曲线的设计一般采用如下过程:首先,确定钻头冠顶半径尺寸和布齿原则,得到具体的理论冠部轮廓曲线;然后,根据钻头总体结构设计的需要,选用某一种实用冠部轮廓曲线进行曲线拟合,并给出内锥角及冠部高度等有关几何参数,即可设计出实际总体冠部轮廓曲线形状。
理论冠部轮廓曲线一般由布齿原则:等切削原则、等功率原则和等磨损原则来确定。
这3种设计原则可统一为通式h =∫RR(R /R 0)2/n-1d R (R >R 0)式中,h 为外锥高度;R 为钻头公称外半径;R 0为冠顶半径;n 为指数,由试验测定,与切削齿和岩石性质有关。
为了便于设计和类比,令R 0=f 0R ,f 0为冠顶半径综合系数,根据经验或类比同型钻头确定,一般在0.2~0.8之间取值,f 0越大,所设计钻头适应的地层越硬;f 0越小,所设计钻头适应的地层越软。
实用冠部轮廓曲线主要有单圆弧、双锥、双圆弧、抛物线、圆弧抛物线、球型、平顶圆弧、平顶抛物线等类型。
以Pro /ENGINEER 为开发平台,利用其二次开发工具Pro /TOOLKIT ,结合VC ++编程,开发了PDC 钻头CA D 系统,该系统集参数化设计、自动装配和数据管理于一体,支持完整的PDC 钻头设计,设计流程如图1。
2 PDC 钻头C AD 系统体系结构PDC 钻头CAD 系统体系结构及各子项目之间的关系如图2,由4个子系统组成。
2.1 总体方案设计子系统PDC 钻头总体方案设计是指根据钻头设计任务,确定钻头总体结构、切削齿大小、数目、布齿方式、水眼数目等[7]。
按照模块化设计思想,将PDC 钻头的概念设计转化为结构设计,结合设计任务,把PDC 钻头抽象成一组相互连接的功能模块的集合,建立功能模块之间的关系。
在功能分析的基础上,确定PDC 钻头总体结构型式和所需模块的种类、数目以及主要性能参数、结构参数值。
在进行方案设计时,考虑到以前的设计数据或模型对拓宽设计思路有一定的帮助,总体方案设计系统为用户提供了2种设计途径。
a ) 参考钻头参数库中的设计数据,确定总体方案。
b ) 参考钻头模型库中的参数化模型,通过对模型的修改、调整,确定总体方案。
图1 P DC 钻头设计子流程2.2 三维造型设计子系统该系统由参数化设计模块和数据转换接口组成,包括PDC 钻头组成模块的三维实体造型设计以及与ANSYS 、FLUEN T 等分析软件的数据转换,主要完成刀翼、切削齿、水眼、接头及其他辅助结构的三维造型设计,并结合参数化设计思想和人机界面,实现了所有结构的智能建模,其中,刀翼设计模块支持单圆弧、双圆弧、抛物线、单锥、圆弧抛物线、双锥6种拟合方式下的刀翼实体参数化设计。
该系统通过人机交互界面,为用户提供PDC 钻头各组成模块的查询、添加、删除、修改等功能,支持完整的钻头设计流程,设计过程中产生的数据将自动保存,并传递给数据管理系统,构建PDC 钻头参数库。
PDC 钻头刀翼的智能建模及修改如图3。
·23· 第37卷 第5期 鲁桂荣,等:P DC 钻头CA D 系统研究与开发图2 PDC钻头CA D系统体系结构图3 P DC钻头刀翼的智能建模及修改2.3 装配设计子系统该系统主要完成PDC钻头切削齿和水眼的布置设计、装配以及钻头的自动装配任务。
布齿和水眼布置设计是关系钻头工作性能的关键。
系统能为用户提供良好的人机交互界面,借助这些交互界面,用户可以选择合适的布齿和水眼布置方式,可以调整切削齿和水眼的位置,修改切削齿和水眼的尺寸,添加新的切削齿,删除不满意的切削齿以及对切削齿进行排序。
除此之外,还能为用户提供批量布齿及批量布置水眼的功能,为方便、快捷地完成设计提供了崭新的计算机平台。
最后,借助自动装配定位技术,系统获取切削齿、水眼、刀翼、钻头体在装配体中的相对位置,完成自动装配,生成PDC钻头装配体,如图4。
2.4 数据管理子系统图4 P DC钻头装配体 数据管理系统管理PDC钻头设计过程中产生的数据,以面向对象为思想,对数据归纳、分组,利用M FC类库构建PDC钻头参数库。
设计过程中产生的数据主要有钻头组成模块的设计参数、二维工程图和三维模型3类。
设计参数以文本文件的格式(.txt)存储,文件名统一为PDC设计行为冠部编号。
例如,对单圆弧钻头进行切削齿添加操作时产生的设计数据文件为:PDC jiachi01.tx t,该文件记录了切削齿的设计参数及位置参数;二维工程图包括钻头的径向、周向布齿图,钻头刀翼剖面图,以dwg格式存储;三维模型包括:钻头各组成模块的参数化零件模型,以prt格式存储;装配体模型,以·24·石油矿场机械 2008年5月 asm格式存储。
3 系统实现的关键技术3.1 基于Pro/Toolkit的参数化设计技术基于Pro/To olkit的参数化设计关键技术包括:建立参数化模型;确定主要参数;编辑Pro gram 文件中模型相关尺寸与主要参数的关系式;编制人机交互的参数输入对话框;编写计算机程序。
其中计算机程序代码的关键部分就是参数的传递过程,一般包括5个部分。
a) 将参数化模型调入内存,初始化模型特征,初始化各参数,在Pro/Toolkit中,参数的数据类型为Pro Parameter。
b) 读取对话框各编辑框的输入数值。
c) 定义ProParam value型的数据变量,把编辑框的输入数值赋给它。
d) 设置各参数值,即将上一步的Pro Param-v alue型数据变量值传递给对应的参数。
e) 模型再生。
3.2 PDC钻头参数库的设计和管理PDC钻头参数库的设计原则为:查询简单;具有良好的可扩充性;层次清楚;支持多级表结构。