回转窑的结构
第七讲 回转窑的结构及工作原理

• 2.轮带(又称滚圈)
• 轮带是一个坚固的大钢圈套装在筒体上,整个回 转窑(包括窑砖和物料)的全部重力,通过轮带传 给托轮,轮带随筒体在托轮上滚动,本身还起着 增加筒体刚性的作用。 • 轮带是以铸钢或锻钢制成,锻造轮带其截面为实 心结构,质量好使用年限长,但是散热差,刚性 差,制造工艺复杂。 • 截面尺寸较大的轮带,一般采用铸造,其截面有 实心矩形和空心箱形两种。
4.回转窑内的传热 • 在燃烧带内,火焰以辐射传热形式(包括对 流传热)把火焰中的热量传递给表层物料, 以传导传热形式把窑衬和窑皮吸收的热量传 给与其接触的物料。前者传递的热量约占整 个烧成带传热的90%,后者约占10%。
物料在窑内煅烧过程的控制
• 1、燃料煅烧及气流温度的控制; • 2、气固换热和物料升温的控制; • 3、物料在一定温度场内滞留时间及物理化 学反应的控制。
回转窑工作原理
1.窑内物料的运动 • 物料进入回转窑后,由于筒体以一定速度回转并 有一定斜度,物料逐渐由窑尾向窑头运动。 • 预分解窑将物料的预热和分解移到预热器和分解 炉,窑内只进行小部分分解反应,窑内一般可分 为过渡带、烧成带。 • 从窑尾起至物料温度1300℃为过渡带,主要任务 是物料升温及部分碳酸盐分解和固相反应;物料 温度1300~1450~1300℃区间为烧成带。
1、可加大窑头排风机挡 板; 2、视电收尘入口温度减 -20~-100Pa 小冷却机鼓风量; 3、视O2情况加大窑尾排 风。
窑 头 负 压
参数
意义及作用 1、反应窑内 燃料供给量及 总热量; 2、反应生料 的易烧性; 3、反应火焰 长短; 4、煤粉的燃 烧状况
控制方法 1、合理的用风比例; 2、合理的用煤比例, 炉:窑=60:40 3、改善煤粉质量; 4、提高二次风温,改 善燃烧环境; 5、保证正常的火焰形 状
回转窑工作原理及结构
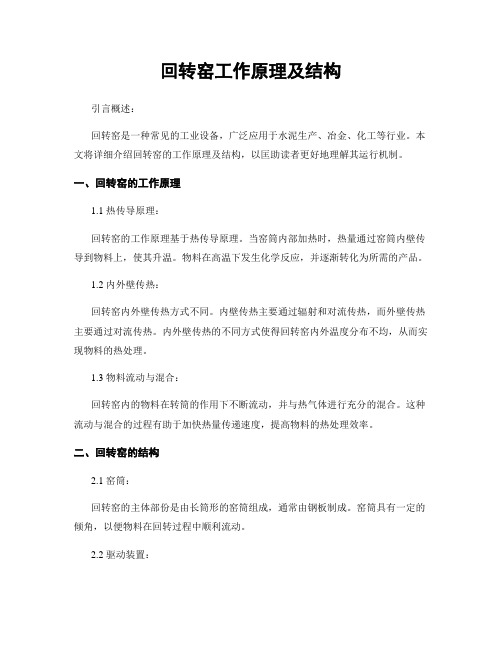
回转窑工作原理及结构引言概述:回转窑是一种常见的工业设备,广泛应用于水泥生产、冶金、化工等行业。
本文将详细介绍回转窑的工作原理及结构,以匡助读者更好地理解其运行机制。
一、回转窑的工作原理1.1 热传导原理:回转窑的工作原理基于热传导原理。
当窑筒内部加热时,热量通过窑筒内壁传导到物料上,使其升温。
物料在高温下发生化学反应,并逐渐转化为所需的产品。
1.2 内外壁传热:回转窑内外壁传热方式不同。
内壁传热主要通过辐射和对流传热,而外壁传热主要通过对流传热。
内外壁传热的不同方式使得回转窑内外温度分布不均,从而实现物料的热处理。
1.3 物料流动与混合:回转窑内的物料在转筒的作用下不断流动,并与热气体进行充分的混合。
这种流动与混合的过程有助于加快热量传递速度,提高物料的热处理效率。
二、回转窑的结构2.1 窑筒:回转窑的主体部份是由长筒形的窑筒组成,通常由钢板制成。
窑筒具有一定的倾角,以便物料在回转过程中顺利流动。
2.2 驱动装置:回转窑的转动是通过驱动装置实现的。
常见的驱动装置有齿轮传动和液压传动两种形式。
齿轮传动通常用于较小的回转窑,而液压传动适合于较大的回转窑。
2.3 冷却装置:为了控制回转窑内部的温度,回转窑通常配备了冷却装置。
冷却装置可以通过喷淋水或者循环水的方式,将窑筒内的温度降低到所需的范围。
三、回转窑的应用3.1 水泥生产:回转窑在水泥生产中起着至关重要的作用。
它可以将石灰石和黏土等原料煅烧成水泥熟料,并通过冷却装置进行降温,最终得到水泥产品。
3.2 冶金行业:在冶金行业中,回转窑主要用于矿石的焙烧和还原。
通过回转窑的高温处理,可以使矿石中的有害物质得到去除,并提高矿石的还原率。
3.3 化工行业:化工行业中的一些反应需要在高温条件下进行,回转窑可以提供所需的高温环境。
例如,回转窑可用于有机物的燃烧、催化剂的制备等。
四、回转窑的优势与挑战4.1 优势:回转窑具有体积大、处理能力强、适应性广等优势。
回转窑简介

回转窑简介回转窑是一种用于煅烧原料的旋转设备,是干法水泥生产线中最重要的设备之一。
它特别适用于长时间连续煅烧,从而使原料充分发生化学反应,生产出高质量的水泥熟料。
回转窑的结构由筒体、支撑装置、驱动装置、轴承装置、密封装置和热交换设备等组成。
筒体通常为钢筋混凝土结构,内壁以耐火砖砌筑,以耐高温、耐磨和耐腐蚀的材料制成。
支撑装置通过轴承将筒体与基础连接,使其可以稳固地旋转。
驱动装置一般采用电动机和齿轮箱组成的传动装置,传递动力给筒体,使其顺时针或逆时针旋转。
轴承装置用于支撑和转动筒体,通常由滚动轴承和滑动轴承组成。
密封装置用于防止高温烟气和粉尘外泄,保证生产环境的清洁和安全。
热交换设备则用于将回转窑排出的烟气进行热能回收和利用,提高能源利用效率。
在回转窑的工作过程中,原料从入口处进入筒体,并随着筒体的旋转逐渐向出口处移动。
在煅烧过程中,原料经历一系列的物理和化学变化,最终转化为水泥熟料。
整个过程可以分为干燥区、预热区、煅烧区和冷却区四个阶段。
在干燥区,由于回转窑内部温度较低,原料中的水分得以蒸发,从而使原料脱水。
在预热区,高温烟气进入回转窑与原料进行热交换,使其逐渐升温。
在煅烧区,原料达到足够高的温度,使其发生化学反应,生成水泥熟料的主要成分。
在冷却区,较低温度的烟气冷却熟料,使其从高温状态恢复到室温。
最后,熟料从出口处排出,经过破碎和磨煤机加工后成为水泥成品。
回转窑具有许多优点,使其成为水泥生产线中不可或缺的设备。
首先,由于回转窑的连续运转特性,可以实现高效的大规模生产,提高生产能力。
其次,由于回转窑具有较大的热容量,能够有效地利用各种燃料的热能,降低能源消耗。
再者,回转窑内部温度和气氛可以进行精确控制,从而保证了水泥熟料的质量和稳定性。
最后,由于回转窑的结构紧凑,占地面积相对较小,可以适应各种场地条件。
然而,回转窑也存在一些问题和挑战。
首先,由于回转窑内部温度很高,对设备材料和热工性能要求较高,增加了设备的制造难度和成本。
回转窑工作原理及结构

回转窑工作原理及结构一、工作原理回转窑是一种重要的工业设备,广泛应用于水泥、冶金、化工等行业。
其工作原理是通过回转窑的旋转运动,将原料在高温下进行热处理,实现物料的干燥、煅烧、还原等工艺过程。
回转窑的工作原理可以简单描述为:原料从窑尾进料口进入回转窑内,随着回转窑的旋转,原料在窑内逐渐向窑头挪移。
在回转窑内,原料受到高温燃烧气体和热风的作用,发生物理和化学变化。
最终,经过一段时间的处理,原料在窑头处排出,并完成热处理过程。
二、结构组成回转窑的结构组成主要包括以下几个部份:1. 窑筒:窑筒是回转窑的主体部份,通常由钢板焊接而成。
窑筒的内壁通常采用耐火材料,以承受高温和化学侵蚀。
2. 骨架:骨架是支撑和固定窑筒的重要组成部份,通常由钢材制成。
骨架的稳定性和强度对于回转窑的正常运行至关重要。
3. 驱动装置:回转窑的旋转是由驱动装置实现的。
常见的驱动装置包括机电、液压驱动系统等。
驱动装置通过传动装置将动力传递给回转窑,使其旋转。
4. 轴承支撑装置:轴承支撑装置用于支撑和固定回转窑的轴承,确保回转窑的旋转平稳。
轴承通常采用滚动轴承或者滑动轴承。
5. 燃烧装置:燃烧装置用于提供高温燃烧气体和热风,为回转窑提供所需的热能。
常见的燃烧装置包括燃烧炉、燃烧器等。
6. 冷却装置:冷却装置用于冷却回转窑内的物料和排出的热风。
常见的冷却装置包括冷却器、风机等。
7. 进料和排料装置:进料装置用于将原料送入回转窑,排料装置用于将处理后的物料从回转窑中排出。
进料和排料装置通常采用输送带、斗式提升机等。
三、工作参数回转窑的工作参数对于其正常运行和工艺效果具有重要影响。
常见的工作参数包括:1. 旋转速度:回转窑的旋转速度决定了物料在窑内停留的时间,对于不同工艺过程有不同的要求。
2. 倾角:回转窑的倾角决定了物料在窑内的运动轨迹和物料层厚度,对于热传导、物料均匀性等有影响。
3. 内径和长度:回转窑的内径和长度决定了窑的处理能力和物料的停留时间。
回转窑的结构及工作原理概述

回转窑的结构及工作原理概述回转窑的结构及工作原理概述回转窑的筒体由钢板卷制而成,筒体内镶砌耐火衬,且与水平线成规定的斜度,由3个轮带支承在各挡支承装置上,在入料端轮带附近的跨内筒体上用切向弹簧板固定一个大齿圈,其下有一个小齿轮与其啮合。
正常运转时,由主传动电动机经主减速器向该开式齿轮装置传递动力,驱动回转窑。
物料从窑尾(筒体的高端)进入回转窑内煅烧。
由于筒体的倾斜和缓慢的回转作用,物料既沿圆周方向翻滚又沿轴向(从高端向低端)移动,继续完成其工艺过程,最后,生成熟料经窑头罩进入冷却机冷却。
燃料由窑头喷入窑内,燃烧产生的废气与物料进行交换后,由窑尾导出。
本设计不含燃料的燃烧器。
该窑在结构方面有下列主要特点:1、简体采用保证五项机械性能(σa、σb、σ%、αk和冷弯试验)的 20g及Q235-B钢板卷制,通常采用自动焊焊接。
筒体壁厚:一般为25mm,烧成带为32mm,轮带下为65mm,由轮带下到跨间有38mm厚的过渡段节,从而使筒体的设计更为合理,既保证横截面的刚性又改善了支承装置的受力状态。
2、在筒体出料端有耐高温、耐磨损的窑口护板,筒体窑尾端由一米长1Cr18Ni9Ti钢板制作。
其中窑头护板与冷风套组成分格的套筒空间,从喇叭口向筒内吹冷风冷却窑头护板的非工作面,以有利该部分的长期安全工作,在筒体上套有三个矩形实心轮带。
轮带与筒体垫板间的间隙由热膨胀量决定,当窑正常运转时,轮带能适度套在筒体上,以减少筒体径向变形。
3、传动系统用单传动,由变频电动机驱动硬齿面三级圆柱齿轮减速器,再带动窑的开式齿轮副,该传动装置采用胶块联轴器,以增加传动的平稳性,设有连接保安电源的辅助传动装置,可保证主电源中断时仍能盘窑操作,防止筒体弯曲并便利检修。
4、回转窑窑头密封采用罩壳气封、迷宫加弹簧刚片双层柔性密封装置。
通过喇叭口吹入适量的冷空气冷却护板,冷空气受热后从顶部排走;通过交迭的耐热弹簧钢片下柔性密封板压紧冷风套筒体,保证在窑头筒体稍有偏摆时仍能保持密封作用。
「回转窑的结构及工作原理概述」
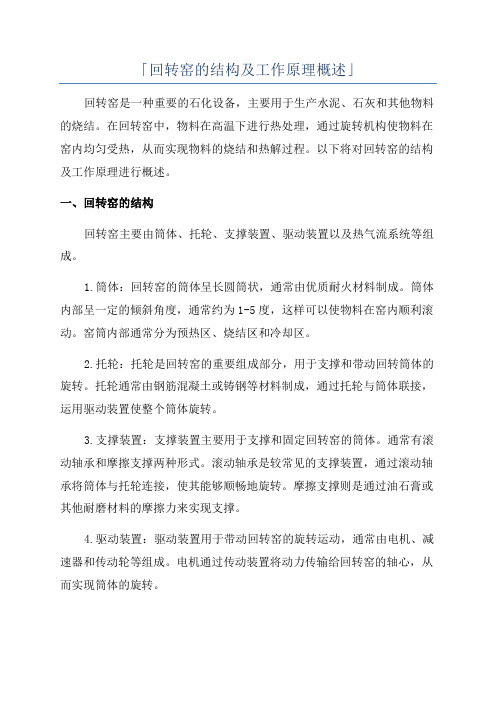
「回转窑的结构及工作原理概述」回转窑是一种重要的石化设备,主要用于生产水泥、石灰和其他物料的烧结。
在回转窑中,物料在高温下进行热处理,通过旋转机构使物料在窑内均匀受热,从而实现物料的烧结和热解过程。
以下将对回转窑的结构及工作原理进行概述。
一、回转窑的结构回转窑主要由筒体、托轮、支撑装置、驱动装置以及热气流系统等组成。
1.筒体:回转窑的筒体呈长圆筒状,通常由优质耐火材料制成。
筒体内部呈一定的倾斜角度,通常约为1-5度,这样可以使物料在窑内顺利滚动。
窑筒内部通常分为预热区、烧结区和冷却区。
2.托轮:托轮是回转窑的重要组成部分,用于支撑和带动回转筒体的旋转。
托轮通常由钢筋混凝土或铸钢等材料制成,通过托轮与筒体联接,运用驱动装置使整个筒体旋转。
3.支撑装置:支撑装置主要用于支撑和固定回转窑的筒体。
通常有滚动轴承和摩擦支撑两种形式。
滚动轴承是较常见的支撑装置,通过滚动轴承将筒体与托轮连接,使其能够顺畅地旋转。
摩擦支撑则是通过油石膏或其他耐磨材料的摩擦力来实现支撑。
4.驱动装置:驱动装置用于带动回转窑的旋转运动,通常由电机、减速器和传动轮等组成。
电机通过传动装置将动力传输给回转窑的轴心,从而实现筒体的旋转。
5.热气流系统:热气流系统用于提供燃料和空气等物质,使回转窑达到所需的高温。
燃料燃烧产生的高温烟气通过燃烧室喷入窑筒,与物料进行热交换。
二、回转窑的工作原理回转窑的工作原理主要是通过筒体的旋转和热气流的流动来实现物料的热处理。
1.物料进料:原料通过送料装置进入窑筒,从窑筒的一端加入。
2.预热区:物料在窑筒的进料端首先经过预热区,此时窑筒温度较低,物料开始升温,水分开始蒸发。
燃料燃烧产生的高温烟气经过预热区与物料进行热交换,从而使物料的温度逐渐升高。
3.烧结区:经过预热区后的物料进入烧结区,此时窑筒温度达到较高水平(约1300℃)。
物料在烧结区内进行热解和烧结过程,燃料燃烧产生的高温烟气通过烧结区与物料进行热交换,使物料逐渐烧结成球状颗粒。
回转窑工作原理及结构
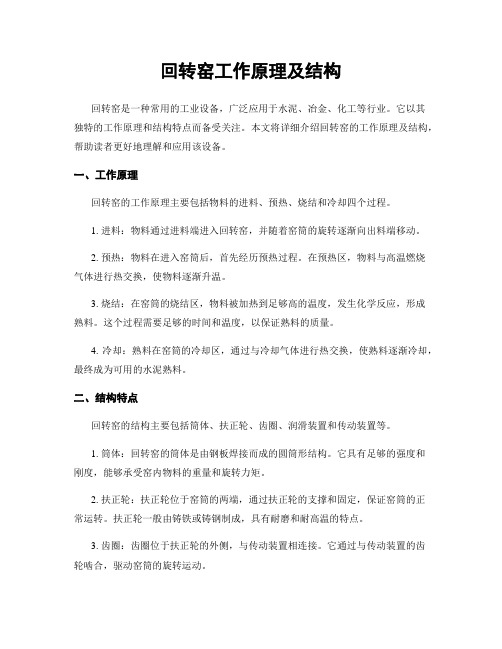
回转窑工作原理及结构回转窑是一种常用的工业设备,广泛应用于水泥、冶金、化工等行业。
它以其独特的工作原理和结构特点而备受关注。
本文将详细介绍回转窑的工作原理及结构,帮助读者更好地理解和应用该设备。
一、工作原理回转窑的工作原理主要包括物料的进料、预热、烧结和冷却四个过程。
1. 进料:物料通过进料端进入回转窑,并随着窑筒的旋转逐渐向出料端移动。
2. 预热:物料在进入窑筒后,首先经历预热过程。
在预热区,物料与高温燃烧气体进行热交换,使物料逐渐升温。
3. 烧结:在窑筒的烧结区,物料被加热到足够高的温度,发生化学反应,形成熟料。
这个过程需要足够的时间和温度,以保证熟料的质量。
4. 冷却:熟料在窑筒的冷却区,通过与冷却气体进行热交换,使熟料逐渐冷却,最终成为可用的水泥熟料。
二、结构特点回转窑的结构主要包括筒体、扶正轮、齿圈、润滑装置和传动装置等。
1. 筒体:回转窑的筒体是由钢板焊接而成的圆筒形结构。
它具有足够的强度和刚度,能够承受窑内物料的重量和旋转力矩。
2. 扶正轮:扶正轮位于窑筒的两端,通过扶正轮的支撑和固定,保证窑筒的正常运转。
扶正轮一般由铸铁或铸钢制成,具有耐磨和耐高温的特点。
3. 齿圈:齿圈位于扶正轮的外侧,与传动装置相连接。
它通过与传动装置的齿轮啮合,驱动窑筒的旋转运动。
4. 润滑装置:润滑装置用于保证回转窑的正常运转和减少摩擦损失。
常见的润滑方式包括油脂润滑和油气润滑等。
5. 传动装置:传动装置用于提供足够的动力,驱动回转窑的旋转运动。
常见的传动方式包括电动机驱动、液压驱动和齿轮传动等。
三、应用领域回转窑广泛应用于水泥生产、冶金和化工等行业。
具体应用领域包括:1. 水泥生产:回转窑是水泥生产过程中的核心设备之一。
它能够将原料烧结成熟料,用于水泥生产。
2. 冶金行业:回转窑在冶金行业中主要用于焙烧矿石和精矿,以提取有用的金属元素。
3. 化工行业:回转窑在化工行业中主要用于石油焦的生产和处理,以及有机化合物的热解和煅烧等。
回转窑的结构与工作原理-PPT文档资料

考虑冷空和热窑轮带 的位置不同,同时移
动轮带使托轮整个表
面受到均匀的磨损, 否则会留下沟纹,无
பைடு நூலகம்
法正常工作。
托轮轴承结构 1---瓦衬;2---球面瓦;3、轴承座;4、顶丝
为使托轮磨损均匀:
窑体每班上下移动 13 次,每次移动幅度 约 50mm 。上下移动可
通过托轮的倾斜液压
挡轮完成
4、液压挡轮
1 、液压挡轮是围绕纵向轴运动的滚轮,安装在窑尾轮带靠近 窑头侧的平面上。 2 、作用:及时指出窑体在托轮轮上的运转位置是否合理,并 限制或控制窑体轴向窜动。
主要内容及要求
一、回转窑的结构 理解回转窑的构造由哪些部件组成,有何作用。 二、回转窑的工作原理(重点) 掌握回转窑内物料的运动、燃料的燃烧、气体的流 动和传热过程的影响因素,掌握喷煤管的工作原理和调
节。
一、回转窑的结构
●筒体 ●轮带 ●筒体 ●托轮 ●挡轮 ●密封装置
●传动装置
●附属设备
1、筒体
●
回转窑的斜率与窑的转速和填充率有关。 回转窑的斜率 β ↑ Vm ↑; 物料的填充率应越大,窑的转速应越大。
●
填充系数:窑内物料的体积占筒体窖的百分比。用正式
表示:
m — 单位时间通过某带的物料量 t/s
Vm — 某带物料的运动速度 m/s
●
物料的休止角 α ↑ Vm ↓ 物料的粘度越大,流动性困难,则 Vm ↓ 易烧性好的物料,在窑内煅烧时间短,则Vm ↑
2、回转窑内的燃料燃烧
2、回转窑内的燃料燃烧
( 1 )煤的燃烧过程是怎样的? 0 ~100- 150℃燃料中水分蒸发; 0.30-0.05S ~450- 500℃逸出挥发份
- 1、下载文档前请自行甄别文档内容的完整性,平台不提供额外的编辑、内容补充、找答案等附加服务。
- 2、"仅部分预览"的文档,不可在线预览部分如存在完整性等问题,可反馈申请退款(可完整预览的文档不适用该条件!)。
- 3、如文档侵犯您的权益,请联系客服反馈,我们会尽快为您处理(人工客服工作时间:9:00-18:30)。
回转窑的结构
回转窑是有:筒体、支承装臵、传动装臵、密封装臵组成。
一、筒体
生产实践表明,回转窑运转率的高低,运转时间的长短,主要决定于耐火砖(也称窑衬)寿命,而窑衬寿命除取决于耐火砖及其镶砌质量、原料性能、挂好、保护好窑皮外,还与筒体的弯曲变形和径向变形(特别是径向变形)有直接的关系。
另外,就回转窑发生轮带断裂、托轮断轴、传动装臵运动不平稳以及电机过负载等故障来看,也主要是由于筒体不直所引起的。
因此,在设计、制造、安装、操作和维护过程中保证筒体直线性公差和减少径向变形是非常重要的。
1、筒体形状
回转窑筒体的形状有直筒形、热端扩大型、冷端扩大型以及两端扩大(哑玲)型。
2、筒体的材质与厚度
回转窑的筒体一般是用不同厚度的Q235(A3)钢板,通常采用18、20、25、28、29、32毫米等几种规格。
在支承轮带处筒体除用厚钢板外,还在圆周上加装有数十块均布的垫板,这样使筒体受力更为均匀、防筒体被轮带磨损同时也为筒体提供了较好的散热条件。
3、筒体的热变形及影响因素
(1)、筒体的热膨胀
尽管在筒体内衬以很厚的耐火砖,在工作时筒体内腔由于受高温热气流的作用,筒体的温度仍较冷窑时高很多,烧成带筒体高达
300~400℃。
温度向窑的两端逐渐降低。
在出料端达300℃左右,加料端200℃左右。
因此,运转中窑筒体的长度和直径要比冷窑时有所伸长和扩大,由于安装在筒体外周轮带的温度低,其径向热膨胀远较筒体小,因此轮带与筒体之间在安装时一般要预留间隙。
由于筒体的轴向热膨胀,轮带和托轮以及大小齿轮的相对位臵都要改变。
安装时应仔细地检查各部分尺寸并预留出由热膨胀而产生的移动量。
筒体沿轴线方向因热膨胀而产生的位移量是这样考虑的,夹在挡轮间的轮带因受挡轮的限制,其轴向移动量不大,故把档轮轮带的位臵作为中立断面,即该处筒体不移动。
当筒体工作受热时,在中立断面左右方面的轮带各向其左右方向移动,其移动数值计算如下:Δl=α(t平均-t环境)l(㎜)
式中 l——由中立面至所要计算的那一挡的筒体长度(㎜)
t平均——在计算的这段筒体上平均温度(℃)
t环境——窑所在的环境温度(℃)
α——线膨胀系数,对于钢α=0.000012(开-1)
(2)、筒体的热弯曲
筒体受热不均匀而发生弯曲。
多发生在:点窑时没有定期转窑;如传动机械的损坏或停止供电等。
此时,下面筒体由于受到热熟料作用温度升高,而上面的筒体则由于散热及空气流的冷却作用温度降低,因而筒体下部较上部伸长很多,致使筒体发生弯曲。
二、支承装臵
支承装臵由轮带、托轮组和档轮组等部分组成
1、轮带
轮带支承回转窑筒体,承受全部回转质量,加强筒体的刚性。
(1)轮带在托轮上滚动时,其工作表面要逐渐磨损。
如果使托轮轴线安装成平行于窑筒体中心线,则轮带与托轮在整个宽度上的磨损是均匀的,此时接触面保持圆柱形状。
当托轮轴线对窑筒体中心线发生歪斜时,轮带与托轮表面的磨损就不均匀,长期运转之后以致变成畸形,就会使窑筒体在运转时失去稳定性,这就需要修理或更换轮带与托轮。
一般托轮受滚压次数为轮带的3~4倍。
在保证轮带经久耐用的前提下,应尽量提高两者的耐磨性能,延长双方使用寿命。
从这一点出发,采用45号铸钢轮带和55号铸钢托轮是比较舒适的。
(2)轮带的断面型式
实心矩形:实心矩形断面轮带,具有制造简单,温度应力小的优点,但利用材料不合理,刚度小,散热条件差。
中空箱形两种形式:箱形断面轮带,材料利用合理,刚度大,运转时散热条件好,但制造较复杂。
(3)轮带的安装方式
主要两种方法:固装和活装目前活装应比较广泛
2、托轮组
托轮组由托轮、托轮轴及轴承所组成
要求每对托轮安装在窑筒体断面中心线的对称位臵,且其距离等于托轮与轮带半径之和,此时,通过托轮中心和筒体断面中心连
线的夹角等于60°。
托轮这样安装时,可以保证筒体稳定性而不致向两侧移动,也不会被托轮挤紧。
并要求每个托轮轴都与窑中心线平行,以保证轮带与托轮表面均匀接触。
轮带与托轮直径之比一般为3~4。
托轮宽度稍宽于轮带是保证回转窑在运转中轮带始终与托轮全面接触;停窑时,任一轮带在托轮上的接触宽度不小于轮带宽度的75﹪,以免过载。
轮带与托轮中心的最大偏量Δl发生在靠窑头第一挡支承上。
托轮的最小宽度按下式计算。
轮带与托轮的偏移B-b≥50㎜并且当Δl≥b/4+25时可用下式求托轮宽度B
B/2≥b/4+Δl
即 B≥b/2+2Δl
托轮与轴的装配多用热装法,将它们牢固地联接在一起。
托轮轴承一般是滑动轴承,瓦衬镶在球面瓦上,运转中能自动调心。
油勺带油润滑,球面瓦通水冷却。
轴端设有止推盘,或轴肩设有止推环,用以承受轴向推力。
轴承固定在底座上,其上设有调整托轮
用的顶丝。
三、窑体窜动及其调整
保持回转窑筒体中心线正直,使回转窑窑体沿其轴线方向作上下往复有规律地移动,是维护回转窑长期安全运转的关键问题之一。
1、回转窑筒体轴向窜动的原因
回转窑筒体是与水平面成一定倾斜角度支承在托轮上的,其斜度一般为2.5~5﹪(一线为4﹪,二线为3.5﹪)现在就托轮轴线平行于窑筒体中心线和托轮轴线与筒体中心线歪斜两种情况进行讨论.
(1)托轮轴线平行于窑筒体中心线时情况
对于静止回转窑,由于窑体自重产生的向下的轴向分力能否使窑体下滑?分析如下.
由图3-54可知,如果回转窑的回转部分重力为G,促使窑体下滑的轴向分力G2为
G2=Gsinα=(0.025~0.05)G (3-23)
式中α---窑体中心线与水平面的倾斜角,一般取sinα=0.025~0.05 回转窑回转部分重力G分解为作用于托轮接触表面上的正压力G1为 G1=Gcosα/sinβ(3-24)
式中β---一对托轮的夹角之半,一般2β=60°,因此,轮带与托轮之间的磨擦力F为
F= G1f (3-25)
式中 f=轮带与托轮间和磨擦系数.
将(3-24)式代入(3-25)式得
F= Gfcosα/sinβ(3-26)如取β=30°、α=2°,代入(3-26)式则得
F = 1.16Gf
当轮带与托轮间为干摩擦时,其磨擦系数f=0.15~0.2,则
F = 1.16(0.15~0.2)
G = (0.174~0.232)G (3-27)
当轮带与托轮间有油润滑时,其摩擦系数f = 0.1~0.12,则
F = 1.16(0.1~0.12)
G = (0.116~0.1392)G (3-28)
比较(3-23)和(3-27)、(3-28)式可知,G2<F。
因此,当窑静止时窑体是不会向下滑动的,事实也是如此。
当窑回转时,其受力情况如图3-55所示,轮带除受窑体回转部分重力产生的下滑力G2作用外,垂直于下滑力G2沿轮带圆周表面切线方向还作用着由窑体齿轮传动而产生的圆周力P。
可以经过计算分析得知G2与P的合力Q,仍远远小于磨擦力F。
但运转着的回转窑,事实上是往低端缓慢滑动的。
这可用弹性理论来解释。
分析得出,托轮的平均圆周速度事实上已落后于轮带的圆周速度。
把由于轮带和托轮接触处产生的弹性变形所引起的滑动,叫做弹性滑动。
上述为圆周力P的作用下产生周向滑动速度V圆周,同理在轴向分力G2作用下,由于弹性滑动现象产生轴向下滑速度V下滑,这就是窑体下滑的原因。
V圆周与V下滑都与其作用力成比例,因此可写出下列关系式
V下滑= V圆周 G2/P (3-29)
圆周弹性滑动速度为托轮丢失速度,即
V圆周 = εV托轮(3-30)
式中ε——滑动率,对于两轮都是金属时,
ε=(0.001~0.005)P/fG1(3-31)
由此可知,滑动率与圆周力P成正比,而与轮带和托轮间不产生相对滑动所能允许的最大摩擦力G1成反比。
将(3-31)式代入(3-30)式然后再代入(3-29)式,以及把G2 = G1tgα代入整理后得
V下滑 = (0.001~0.005)V托轮tgα/f (3-32)因为弹性滑动速度值很小,可以近似认为轮带和托轮的圆周速度相等,即V下滑 = V托轮,则
V下滑 = (0.001~0.005)V轮带tgα/f (3-33)(2)托轮轴线歪斜的情况
如果托轮轴线与窑体中心线
不平行,如图3-57所示。
当窑体
回转时,托轮与轮带接触处的圆周
速度V托轮可以分解为两个分速度,
即V1和V2。
V2与轮带的圆周速度在
方向和大小上都一致的,而V1则
是沿轴向的分速度,这就产生了所谓“螺旋效应”。
在托轮与轮带间的摩擦力作用下,迫使窑筒体以V1的速度向上移动。
显然,托轮轴线歪斜角β越大,则轴向分速度V1也就越大,推窑体向上移动的速度也就越快。
如果推窑体向上移动的速度大大超过其弹性下滑的速度,则将使托轮和轮带表面产生相对滑动,使托轮和轮带表面、大小齿轮表面产生轴向刻痕,加速其磨损。
因此,应使窑体上移的速度等于其弹性下滑的速度,以此来确定托轮轴线的歪斜角,即
V1 = V下滑而 V1 = V2 tgβ= V轮带tgβ
因此(0.001~0.005)V轮带tgα/f = V轮带tgβ(3-34)将上式整理后可得出托轮轴线需要歪斜的角度
β = tg-1[(0.001~0.005)V轮带tgα/f] (3-35)2、窑体窜动的调整。