精益均衡化排产
浅谈车间均衡生产

浅谈车间均衡生产摘要:本文主要介绍车间在面对生产量大幅度浮动情况下,如何有效管控,确保人员、场地、节奏、开工量对车间影响小,通过整体梳理生产流程,实施有效管理措施,与同期对比实现产量稳定递增,提高与外部工序生产节拍的准确性和及时性,以均衡生产为目标实现跨越式发展。
关键词:生产产量;生产节拍;均衡生产一现状分析均衡化生产是生产管理的最终目标,要使生产过程始终处在一个均衡的状态,确保产能利用率达到最佳效果。
目前在生产过程中,车间内部存在工序等待、生产速度时快时慢的现象;相对上下工序,存在转向架配台不及时、不准确的问题。
经过调研,对存在的问题进行了如下总结:(一)车间内部生产管理。
转向架分解属于第一道工序,工作8小时情况下,产能为50辆。
上下工序存在配件流转不及时、异常问题处理慢、工序间产品开工数不定量的问题,导致生产效率提升一直是个难题。
车间今年制定了“无异常情况下,上午落成要达到27辆,低于25辆就要考核相关调度和班组”的要求,仍存在员工配合度低问题。
该问题造成下工序上午时段垫车的需求不足。
(二)转向架分解顺序问题。
转向架分解顺序是根据上工序的分解顺序完成,当上工序车型搭配变化为先敞车后平车分解后,下工序上午排产计划相应受影响,本工序则须等分解完敞车后才能进行平车配件的分解检修,导致车间生产周转量不足,无法满足下工序垫车需求。
(三)各工序信息沟通滞后。
上下工序排产变化大,人员协调滞后,致使车间在没有下工序排产计划下生产。
导致下工序进行流水作业时需要垫车的转向架车型无法及时供给。
(四)日开工计划搭配不合理。
当开工计划中有特种车型转向架(K4、K5),并需在上午垫车时,由于车间特种车型转向架的检修作业方式存在人工组装落成,效率偏低,同时配件需倒运至外部车间完成检修,物流倒运、检修周期增长,车间不能在半天的周期内落成特种车型转向架;当开工平车数量大于25辆时,由于平车的骨架检修周期短,转向架的检修周期为固定模式,会产生节拍不一致,影响配台不及时。
精益生产(4--均衡化生产)
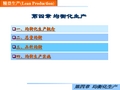
53% 67% 77% 83%
88% 92% 95% 98% 100%
尤其是在压缩在制品的情况下组织均衡生产难度更大、更 艰巨。
精益生产(Lean Production)
二、总量均衡
总量均衡是指将一个单位期间内的总订单量平均化,即
将连续两个单位期间的总生产量的波动控制到最小程度。 实施总量均衡之后,需求仍有可能发生波动:短期波动 靠加班就可以解决,而长期波动需要重新进行总量均衡配 置生产要素。 生产总量均衡可以防止两种浪费:工厂在不同时间不均 衡造成的浪费;不同工序之间不均衡产生的浪费。
Y
Z X Y Z
3
2 5 3 2
62
41
31
62
41
31
每个循环周期内各品种出现的比率是均等的,产品瞬时生产 数量波动控制到最小程度。
精益生产(Lean Production)
实现均衡化要注意以下的问题
不同的产品其作业多少会有不同的地方,所以事前的训练 是很重要的。 与前工序相对,小批量生产中的频繁物品取用是必要的, 但是由此增加了生产品种的切换次数,企业必须努力采用快 速转换技术补偿。 不同的零部件生产除了作业不同外,还可能使用的设备、 夹具、模具或工具也会有不同的地方,因此需要考虑设计通 用的工装、夹具来整合不同的产品,应用FMS和GT的生产 机器配置技术。 因市场的不稳定性,因此要提高预测数据的频率和精度, 其次要强化与供应商的关系。
精益生产(Lean Production)
ABC分类法
(1)进行ABC分析:A为50%以上的生产量,B为20%~ 50%的生产量,C为未满20%的生产量。 (2)决定生产批量。
(3)制作均衡化计划周期表。
(4)安排每天产品投入顺序计划:按照论排图或生产比 倒数法进行生产顺序安排。
均衡化生产

决定混流装配线的产品顺序计划
月份需求预测
来自销售商的日订货
柔性设备
缩短生产过程时间
⑵第二个阶段是每日适应。因为每天的生产指示是由顺 序计划和看来实行的,所以使得每日适应成为可能。
2.均衡生产排产计划
⑴制定生产节拍 ⑵轮排图(品种较少为宜)
一.均衡化生产概念
杜绝浪费是精益生产方式的重心。
Muda 浪费 Mura 不均 衡 Muri Байду номын сангаас荷 过重 3M
不均衡:可以视为上述两种“M”的波动结果。
二.均衡生产实施
1.均衡生产实施阶段(见均衡生产的实施阶段图)
均衡生产的两个阶段:第一阶段是适应每个月的需求 变化,即每月适应;第二阶段是适应每天的需求变化, 即每日适应。 ⑴第一阶段是每月适应。按照每个月的需求预测制定月 度生产计划,即按照总量均衡的目标,制定生产计划,
确定并指示该厂各工序每天的平均产量。
迅速适应需求变化的生产
准时生产(仅按能销售的数量生产能销售的产品
每月的适应(对应于总量的销售速度<循 环时间的生产
每日的适应(对于分品种的销售速 度的生产) 按照当天分品种的循环时间的生产指示
通过看板方式(拉动方式)进行的对前工序每 天的生产指示
按工序的月份生产能力计划
⑶ABC分类法(排线品种较多的为宜) 品种数量比例排线
3.其他技巧
⑴装载均衡箱 ⑵指定座(对号入座) ⑶接棒区方式 ⑷分支方式(不同产品工时相差较大时,而暂时有无其他方法时
所用的方式)
公司精益生产总体方案

精益供应链
设备管理 成本管理
5S、目视化
持续改善
现场TPM
三级核算体系 3S
TPM职能强化
全员TPM
构建标准成本
全面预算 固化投入
产出系统
5S
维持、优化
改善培训及现场改善
改善体制建立
人力资源
基础精益化
生产省人化
管理柔性化
变经 营 结 果 改
时间
I(导入+扩展+深化) 20个月(6+6+8)
II(流程优化) 8个月
■信息处理类
支撑环境改善
■供应链
■整体精益供应链形成
生产部
生产部
采购部 生产部
8/6/2021 15
品质管理专项方案
1期
现场品质改善
目标设定
外
防止不良品流出 减少客户投诉抱怨
内
减少作业内不良发生 降低废品损失 降低品质成本
2期
品管能力强化
目标设定
品管职能优化 品管技能提升 品保能力提高
3期
品质体系高效
➢第二阶段:用8个月完成流程优化 ➢第三阶段:用12个月完成机制改革 ➢第四阶段:供应链持续优化
2021/8/6 3
精益愿景规划
精益供应链
扩展到参与方
66--1220个个月月
大规模培训,初步改
精益企业:
精 改变机制
益
文
化
形 成
精益工厂: 优化流程
的
过
程
精益现场: 奠定基础
变意识,完善基础管 理。 主要工具: 5S、标准化、目视化 、现场改善等。 主要成果: 初步形成自律的现场 改变员工意识 遵守规则
均衡生产(精益生产)
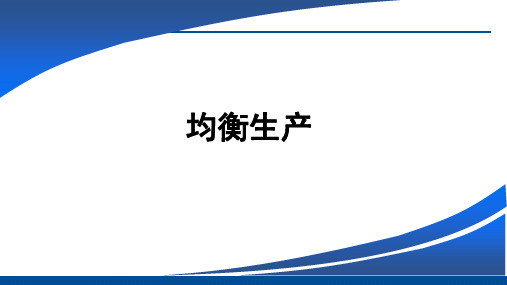
例题:某工厂某月有三种产品X、Y、Z需要生产,X产品的需求量为1000件,Y产品的需求量为600件,Z产品的需求 量为400件。 假若每月工作20天,则传统生产计划安排为10个工作日先将X产品生产完毕,再用6天生产Y产品,最后用4天生产Z产 品。 这是一种常见的型态,也称为分段生产。虽然这种传统的大批量生产的方法可以节省作业转换的时间。但是与市场需 求会出现很大的差异。在一个时间段内,会使一部分产品供大于求,造成积压;另一部分产品生产不出来,供不应求 ,发生缺货。无论哪种情况都会造成损失和浪费。
9
3、均衡生产的两大均衡
均衡的生产排程
某月生产计划
单位:个
品种 总量 1 2 3 4 5 6 7 8 9 10 11 12 13 14 15 16 17 18 19 20
X 1000
1000
Y 600
600
Z 400
400
• 从上表可以看出: X产品通常会导致较长时间的库存; 而Z产品却大半个月无货可供!!不能适应市场需求。
因为每天的生产指标是由顺序计划和看板来实行的,所以使得每日适应成为可能;
最终的装配线上的投入顺序计划则是进行看板管理的出发点,这个投入顺序计划是以品
种均衡为目标,根据它可以均衡地从零部件供应商和零部件生产线领取各种零部件。
14
谢谢大家!
15
均衡生产
1
目录
一 • 均衡生产的定义 二 • 均衡生产的目的和意义 三 • 均衡生产中的两大均衡 四 • 均衡生产的实施条件 五 • 均衡生产的实施方法
什么是均衡生产

均衡生产是精实生产制度的最终目标。
将产量的高低起伏减至最低,确保产能利用率达到最佳状态,并使完全生产时间(亦即从头到尾的生产时间,throughput time)缩至最短。
从企业角度而言,在每个工作站和流程步骤的工作量均衡分配下,利用率达到最大,而总体周期时间维持在最少状态。
精益生产:自动化,准时生产制,标准作业,一个流。
核心思想:消除一切浪费,长期持续化发展。
我们完全可以抛开日本式的“看板”“全员生产管理”“全员质量管理”这些工具,我们从这个精益的思想出发,如何去运用深入中国人心理的传统文化来实现精益企业。
如果客户的定单波动很大,你们公司是否可以承受建立成品超市的压力。
如果供应商材料提供波动很大,他们是否愿意建立安全库存生产管理最主要的就是进行过程控制,而在过程控制中我们需要考虑的因素有:产量、质量、成本、安全、设备等等,而如果仅仅只顾着某方面,另一方面就可能有失,那么最终可能是产量出来了,质量却没有了,质量上来了,成本却又上升了,成本费用控制住了,却又可能安全、设备的可靠性又没有了。
因此如此有效的兼顾各方面,就是我们如何进行均衡生产的关键。
?均衡生产是精实生产制度的最终目标,即将产量的高低起伏减至最低,确保产能利用率达到最佳状态,并使完全生产时间(亦即从头到尾的生产时间,thr oughput time)缩至最短。
均衡生产一直是企业管理者追求的理想状态。
实现了均衡生产,意味着企业的所有资源均在有条不紊地运转,很少出现加班及等待现象,企业的生产成本也会处在较低的状态下。
影响均衡生产的主要因素有合同交货期、设备生产能力、劳动力工时、零部件的配套性、用于生产的流动资金。
实际解决办法是否可以从以下几个方面考虑(仅作参考):1.在宏观生产计划、主生产计划、零部件计划的编制过程中,均要进行生产能力的平衡分析,包括:工时能力平衡、工作中心生产能力分析、关键材料的需求能力、工装模具的能力分析等。
2.对于物料仓库,通用物料库存上下限的确定应考虑到生产的配套性。
精益生产:准时化生产(JIT)
1 混线生产:排产的混线排产(物流) 工艺的混线装配工艺(总装)
目标:统一线速(降低节拍时间)
2 停线管理:真正的停线记录, 彻底的停线原因分析(各部门)
明确停线权限人,停线标准
生产管理
3 岗位优化:不在4%,等待14%,走动15%
社会
↑
手艺人 预测生産 社会 PUSH【作坊型】
多品種少量个性生产
运用IT技术 订单确定式生産 产品 + 服务 个性定制产品,短交期
多品种小批量生产
市场导向(顾客对应) 库存、时间、空间、工时 质量等志在消灭浪费 小批量化、缩短品种切换时间 代表例 丰田生産方式
分工:传送带 生产线平衡 生产线设计能力 代表例 福特方式
JIT 准时生产 流程均衡化计划 同期拉动式生产 可视化管理式
自働化
过程质量 人员:3N 设备:防错 组织:QC活动
自主改善
现场改善 提高生产性 成本最适化 OJT人员培养
手工 生产方式
熟练・柔性・通用
D
Q
C
以消除浪费为重点 以现场改善为核心 以改善为基础的标准化
在竞争激烈化中、保持生产效率(D)、保持高品质(Q)的同 时、如何以最少的投入获得最大限度的利益是重要的课题。
関田鉄洪(T.kanda) 日本国家资格 IE士 / 中科院 IE首席专家(人才交流开发中心)
4. 准时化的混流生产和均衡生产 混流工艺
11
工序N
工序N+1
工序N+2
B、 、
1200
1000
800
600
400
200
均衡化生产PPT课件
该企业采用均衡化生产方式,将产品线划分为若干个系列,每个系列按照市场需求进行 排产。同时,企业加强了生产计划的管理,根据市场趋势和客户需求调整生产计划,确 保生产和销售的平衡。通过这些措施,企业减少了库存积压,提高了生产效率,降低了
库存成本。
某零售企业的库存管理与均衡化生产
总结词
某零售企业通过实施均衡化生产,优化 了库存管理,提高了库存周转率,提升 了客户满意度。
强化生产现场管理和调度
现场管理标准化
制定现场管理标准,如5S管理、 定置管理、目视化管理等,提高
现场管理水平。
调度指挥科学化
建立科学的调度指挥体系,确保 生产计划的顺利实施。
现场问题及时处理
建立问题反馈和处理机制,及时 发现并解决生产现场出现的问题。
04 均衡化生产的优势与挑战
提高生产效率和资源利用率
06 均衡化生产的未来发展与 展望
智能制造与均衡化生产
1 2
智能制造
通过引入先进的信息技术,实现生产过程的自动 化、智能化,提高生产效率和产品质量。
实时监控与预测
通过物联网技术,实时监控生产设备状态,预测 设备故障,提前采取措施,减少生产中断。
3
定制化生产
利用大数据和人工智能技术,分析消费者需求, 实现定制化生产,满足市场多样化需求。
均衡化生产起源于日本丰田汽车公司的准时制生产方式(Just-In-Time,JIT),该方式旨在通过减少库存、优化 资源配置和提高生产效率来降低成本和提高产品质量。
均衡化生产的推广与发展
随着全球市场竞争的加剧和制造业的不断升级,均衡化生产逐渐成为主流的生产方式,被广泛应用于汽车、电子、 机械、化工等制造业领域。同时,随着信息技术和智能制造的发展,均衡化生产也在不断升级和完善,逐渐向数 字化、智能化方向发展。
精益生产项目实施步骤及其效果
物品、人员、作业、仓库、设备等的目视化管理,使各级人员到达现场后都可以判断出正常与否。使人获得整洁、有序的工厂之第一印象。夯实生产管理之基础,不断寻找且消除浪费的根源。节约场地,提高工作效率。提高设备的可动率。目标的明确化与目视化,增强团队精神养成员工良好的工作习惯。2小批量生产内部转换转化为外部转换,并将外部转换标准化。把模具等与设备的联接部分标准化,制定作业指导书。使用快速紧固件使用辅助用具,如转换台架等在全生产线推进同步转换模具摆放和维护。作业转换由专人负责线上作业转换时间缩短70%。因作业转换时间长而引起的中间在库减少70%实现小批量生产,增加生产柔性度。3同步生产线上实现单个流根据工序顺序安排的机械布局工序之间的连接优化,减少搬运距离定制搬运器具和搬运量U型生产线的编排多能工进行多工序操作由坐姿作业变为站姿作业生产节拍一致化,让高速设备慢下来生产线上所有工序的加工节拍一致,中间在制品积压为零加工产品均衡地流到下工序,实现有效的可追溯性一个流作业给100%全数检验提供了可能任何加工中的异常都能及时发现,避免了批量不合格。多能工训练提高操作人员的技能,为紧急事件储备人力资源操作工人在移动中工作,疲劳度降低节约现场加工面积,减少作业面积20%最少距离的工件搬运,缩短产品加工周期针对顾客需求变化,积压产品最少。4标准作业依据一人多机的多能工安排生产核定多能工的移动时间、手作业时间和机器加工时间根据作业顺序计算标准在工量依据顾客需求,计算作业节拍,安排相应数量操作人员制定标准作业组合票和标准作业票生产线上操作人员充满式工作,现场操人数最少。依据顾客需求调整标准作业组合,生产柔性进一步加强5生产均衡化总量均衡品种均衡数量均衡以通用设备适应产品的多样性制造现场所有的生产线,按顾客的需求,成组配套地加工、进料装配形成合理的生产计划和生产节拍。月排产改为日排产没有因组件短缺造成的停线和在制品库存积压降低成品库存为最低依据顾客的需求实现拉动式生产(JIT)。6自働化能停止的生产线防错装置目视化管理的ANDON系统由机械装置和人工共同控制生产线产品质量不良率接近零缺陷防止不合格品流入下道工序防止批量报废如果完成了必要的数量或作业,设备自动停止,只供给下序必要的数量减少生产监视人员数量生产线上的异常表面化及时发现异常,及时对策减少专职检验人员数量贯彻质量是制造出来的思想,实现过程质量控制7看板管理导入定义看板种类和使用方法:如生产指数看板、纳入看板等计算看板枚数建立看板管理系统,利用看板微调生产节拍定时、巡回混载搬运方式只对最终工序进行计划安排,其他工序依据看板信息进行拉动式生产消除原来意义上的库存管理方法定制库存(每一枚看板,代表一定的零件数量)优化库存,实现库存最少化应对突然的需求变化依据看板的传递,控制工序间物流状况。为生产作业建立信息指示系统和监控系统
精益生产推行五阶段法
精益生产推行五阶段法
精益生产推进的五阶段界定法
LPS的推进效果由五阶段界定法来体现,并以此评价、判断企业的精益生产系统所处的水平。
一、稳定性生产,即企业过程的自我完善,在这个阶段使企业具有稳定的过程能力,确保产品和生产流程的一致性。
二、连续流生产,即企业的自我改善,在这个阶段企业达到工序间的连续生产。
三、同步化生产,即在生产过程中各个工位的生产能力与负荷基本平衡,物料供应能力与实际需求量基本平衡的前提下,生产系统各环节能够按照产品生产的速度进行成比例同步调整的生产管理方式。
同步化生产在连续性流动生产的基础上,特别强调各制造环节能力与负荷的整体平衡。
四、拉动式生产,即在供应链后端(供应、生产)各环节储备少量的零部件、工序在制品、成品,通过对供应商的整合,确保物料供应能够满足工序要求的前提下,由订单需求向前层层拉动每道工序进行生产,最终能够按时保质保量提供用户需要的产品。
拉动式生产在同步化生产的基础上特别强调生产系统各环节的生产进度及调整信号由订单需求(实际订单+预测)发出并进行拉动。
五、均衡化生产,即在供应链整体(包括前端销售和后端供应、生产)各环节仅有少量储备的前提下,通过对经销商的整合,提高市场需求预测准确度,确保在既能满足顾客订单数量、配比、顺序要求的基础上,又能保证生产管理环节的整体均衡。
均衡化生产在拉动式生产的基础上特别强调整个(内部和外部)供应链的整体均衡。
- 1、下载文档前请自行甄别文档内容的完整性,平台不提供额外的编辑、内容补充、找答案等附加服务。
- 2、"仅部分预览"的文档,不可在线预览部分如存在完整性等问题,可反馈申请退款(可完整预览的文档不适用该条件!)。
- 3、如文档侵犯您的权益,请联系客服反馈,我们会尽快为您处理(人工客服工作时间:9:00-18:30)。
批量 50 30 20
A零件 500 60 60
B零件 100 150 160
C零件 150 60 100
从表中可知,每天按X、Y、Z各自批量生产,则各个零件波动较大。例如,当生产 X产品时需要A零件为500个,当生产Y产品时需要A零件为60个,这样容易产生库存和人 员的浪费。
均衡化排产
按品种均衡就是要在一定的周期内各ห้องสมุดไป่ตู้种出现比率是均等的,并且时间、周期尽可能缩 短,尽量细化观察标准,如下图,这样使产品瞬时生产数量波动尽可能控制到最小程度。
如果采用总量均衡的办法,是日产量保持一致,即每天生产20台,则可以按这个产量准 备人员以及生产要素。这样,总产量没有减少,人员以及生产要素却可以减少1/3,成本也 就随之降低。
产量/台
月合计:400台
20
据此配置生
产要素
0
1
2
3
4
5
6 日期
实行总量均衡
均衡化排产
实施总量均衡后,虽然每天按照相同的数量准备人员及生产要素,但需求仍有可能产生 波动,可分为短期波动和长期波动两种情况。
均衡化排产
传统的大批量生产的方法可以节省作业转换时间,但是,与市场需求会出现很大 差异。为满足需求多样性,进行如下改进:
每天生产X产品50件,Y产品30件,Z产品20件,改进后的月生产排程如表所示:
某月生产计划
品种 总量 1 2 3 4 5 6 7 8 9 10 11 12 13 14 15 16 17 18 19 20
A零件 10 2 3
B零件 2 5 8
C零件 3 2 5
下表为X、Y、Z批量分别为50件、30件、20件时需要的各种零件数量。
改进前每天各产品零件消耗数量
产品 X产品 Y产品 Z产品
批量 50 30 20
A零件 500 60 60
B零件 100 150 160
C零件 150 60 100
从表中可知,每天按X、Y、Z各自批量生产,则各个零件波动较大。例如,当生产 X产品时需要A零件为500个,当生产Y产品时需要A零件为60个,这样容易产生库存和人 员的浪费。
总量
均衡化生产
品种
均衡
均衡
实现准时化的前提条 件,实现看板管理的
均衡化排产
总量均衡
定义:
总量均衡就是将一个单位期间内的总订单量平均化,即将连续两个单位期间的总生产 量的波动控制到最小程度。
生产总量不均衡
产品产量出现波动
人和设备要依照生产 量的高峰期做准备
总量均衡的重要性
产量减少时,容易产 生人员、库存等浪费
重新进行总量平衡
产量/台
30
20
提前结束
01 23456
短期波动
日期
0 1 2 3 4 5 n 1 2 3 4 5 m 日期
长期波动
均衡化排产
如果完全按照准时化生产,则会产生生产要素配置的浪费; 如果不按准时化生产,则会产生库存浪费。 因而要权衡产能损失与库存浪费的最佳平衡点。根据经验,日产量允许存在着一定的
均衡化排产
按不同时间单位均衡的实
均衡化和多重每日循环
传统的月排程
Leveled by Month
25 20 15 Units 10
5 0
1 3 5 7 9 11 13 15 17 19 Days
每周的批量生产
Leveled by Week
25 20 15 Units 10 5 0
1 3 5 7 9 11 13 15 17 19 Days
变化幅度,但为保持人员和设备的稳定性,应把振幅控制在20%之内。
产量/台
20
振幅20%
1 2 34 5 n 总量均衡允许的产量波动幅度
日期
均衡化排产
• 品种均衡的概念 品种均衡就是在一个单位期间内生产的产品组合平均化,是各种产品在不同单位期间不
产生波动,在生产各种产品时所需前工序的零部件数量不产生波动。 案例: 某工厂某月有三种产品X、Y、Z需要生产。X产品的需求数为1000件,Y产品为600件,Z
X 1000
Y 600
Z
400
50个/日 30个/日 20个/日
一个月20天每天重复1次,共20次,就可以每天生产出X、Y、Z产品,产品积压与短缺 的情况将大大减少生产资源利用率也将提高。但是应当设法减少每天作业转换的辅助时间。
均衡化排产
这种以天为单位的生产安排,每天将依旧按照批量生产的方式,即先生产 50件X产品,其次是30件Y产品,最后是20件Z产品。
设法将变动的幅度控制在20%以内。 如果要结束某种特定类型产品的生产,必须事先 通知供应商,并对相关损失进行补偿。
生
X 1000
1000
产
Y 600
排
600
程
Z
400
400
分段式生产
均衡化排产
分段式生产会产生哪些问题?
积压缺货
大批量的分段生产必然造 成部分产品一时供大于求, 销售不出去,造成积压。 同时另一部分产品供不应 求,发生缺货。这两种情 况都会造成损失和浪费。
闲忙不均
由于面临多种产品生产,企业 必然会配置多种设备与多种不 同类型技能的工人。同一段时 间只生产一种产品可能会造成 部分车间 部分设备超负荷运转, 部分工人加班加点,相反另一 部分的车间设备符合不足,甚 至空闲。
产品为400件。假若每月工作日为20天,则传统生产计划安排为前10个工作日先将X产品生产 完毕,然后6天生产Y产品,最后4天生产Z产品。这是一种常见的型态,也称分段生产。
传 统
某月生产计划
(单位:个)
的
品种 总量 1 2 3 4 5 6 7 8 9 10 11 12 13 14 15 16 17 18 19 20
均衡化排产
如果1天内产品X、Y、Z按照5:3:2的比例进行轮番生产,每小时重复一次,则每小 时内各个零部件的消耗速率就相同。
改进后的零部件消耗数量
产品 X Y Z X Y
批量 5 3 2 5 3
A零件 62
62
B零件 41
41
Z
2
X
5
Y
3
62
41
Z
2
C零件 31 31 31
以这样的思路改进下去,不断细化生产单位,直到可以按照“X—Y—X—Z— X—Y—X—Z—X—Y”的顺序重复生产,达到最小的观察时间单位,满足精益生产 倡导的以小时、分钟为单位进行安排的要求,实现均衡化生产。
终极目标:多重每日循环(小时均衡)
Four Intervals per Day
Day 1
Day 2
Day 3
Day 4
Day 5
初步目标:每天平均化生产
Leveled by Day
25 20 15 Units 10
5 0
1 3 5 7 9 11 13 15 17 19 Days
均衡化排产
定义:
“牛鞭效应”是经济学上的一个术语,指供应链上的一种需求变异放大现象,是信息流从最终客户端向 原始供应商端传递时,无法有效地实现信息共享,使得信息扭曲而逐级放大,导致了需求信息出现越来越 大的波动,此信息扭曲的放大作用在图形上很像一个甩起的牛鞭,因此被形象地称为牛鞭效应。
均衡化排产
均衡化生产也称平准化生产,是指企业采购、制造以及配送的整个过程都与市场需求相符合。采用均衡化 意味着最终供货与需求相适应,同时从需求开始进行拉动,总装配线在向前工序领取零部件时应均衡地使用各种 零部件,生产各种产品。
采取混流生产、SMED、一个流、准时采购、TQM、 TPM等管理手段和方法来实现。
某日生产计划
产品
产量
8:00
9:00
10:00
11:00
12:00
13:00
14:00
15:00
16:00
X
1000
50X
Y
600
30Y
Z
400
20Z 改进后的日生产安排
这样安排生产对前工序带来的影响?
均衡化排产
例如,X、Y、Z三种产品各由A、B、C三种零件组成,如下表:
各产品零件构成
产品名称 X产品 Y产品 Z产品
减少供应链波动
因每日生产产品及产 量均衡,可降低供应 商生产压力及库存。 使供应商准时化生产
均衡化排产
实现均衡化生产需要注意的几个问题
重视事前训练,避免实际操作中错误的出现。 企业必须采用快速装换技术补偿因切换次数增加而产生的时间损失。 考虑设计通用的工装、夹具来整合不同的产品,以配合适当的机器设备,一般以 引入应用柔性生产系统(FMS)和成组技术(GT)的生产机器配置技术为宜。 针对市场需求量与生产量差异较大的问题,可采用两种方法;
1、短期波动
对于短期内需求有小幅度波动,当 需求量增大时可以采取加班方式,需求 量减少时则提早结束生产。
2、长期波动
对于周期性的大幅波动,则需要重新进行总 量均衡配置生产要素,而进行产品总量均衡的周 期由产品特点及工厂管理能力而定
产量/台
平均
20
加班
30 22
月合计:400台
24
10
17
10 配置生产要素
均衡化排产
例如,X、Y、Z三种产品各由A、B、C三种零件组成,如下表:
各产品零件构成
产品名称 X产品 Y产品 Z产品
A零件 10 2 3
B零件 2 5 8
C零件 3 2 5
下表为X、Y、Z批量分别为50件、30件、20件时需要的各种零件数量。
改进前每天各产品零件消耗数量
产品 X产品 Y产品 Z产品
均衡化排产
总量均衡案例分析
某月某产品的实际需求量为400台,一月生产20天,每日生产量的需求不同,最高 日30台/日,最低日10台/日,如图所示。