经典_精益生产之均衡化生产
均衡化生产

决定混流装配线的产品顺序计划
月份需求预测
来自销售商的日订货
柔性设备
缩短生产过程时间
⑵第二个阶段是每日适应。因为每天的生产指示是由顺 序计划和看来实行的,所以使得每日适应成为可能。
2.均衡生产排产计划
⑴制定生产节拍 ⑵轮排图(品种较少为宜)
一.均衡化生产概念
杜绝浪费是精益生产方式的重心。
Muda 浪费 Mura 不均 衡 Muri Байду номын сангаас荷 过重 3M
不均衡:可以视为上述两种“M”的波动结果。
二.均衡生产实施
1.均衡生产实施阶段(见均衡生产的实施阶段图)
均衡生产的两个阶段:第一阶段是适应每个月的需求 变化,即每月适应;第二阶段是适应每天的需求变化, 即每日适应。 ⑴第一阶段是每月适应。按照每个月的需求预测制定月 度生产计划,即按照总量均衡的目标,制定生产计划,
确定并指示该厂各工序每天的平均产量。
迅速适应需求变化的生产
准时生产(仅按能销售的数量生产能销售的产品
每月的适应(对应于总量的销售速度<循 环时间的生产
每日的适应(对于分品种的销售速 度的生产) 按照当天分品种的循环时间的生产指示
通过看板方式(拉动方式)进行的对前工序每 天的生产指示
按工序的月份生产能力计划
⑶ABC分类法(排线品种较多的为宜) 品种数量比例排线
3.其他技巧
⑴装载均衡箱 ⑵指定座(对号入座) ⑶接棒区方式 ⑷分支方式(不同产品工时相差较大时,而暂时有无其他方法时
所用的方式)
均衡生产(精益生产)
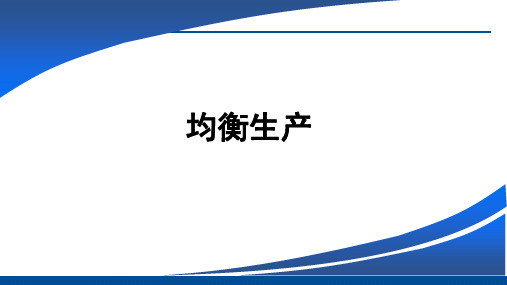
例题:某工厂某月有三种产品X、Y、Z需要生产,X产品的需求量为1000件,Y产品的需求量为600件,Z产品的需求 量为400件。 假若每月工作20天,则传统生产计划安排为10个工作日先将X产品生产完毕,再用6天生产Y产品,最后用4天生产Z产 品。 这是一种常见的型态,也称为分段生产。虽然这种传统的大批量生产的方法可以节省作业转换的时间。但是与市场需 求会出现很大的差异。在一个时间段内,会使一部分产品供大于求,造成积压;另一部分产品生产不出来,供不应求 ,发生缺货。无论哪种情况都会造成损失和浪费。
9
3、均衡生产的两大均衡
均衡的生产排程
某月生产计划
单位:个
品种 总量 1 2 3 4 5 6 7 8 9 10 11 12 13 14 15 16 17 18 19 20
X 1000
1000
Y 600
600
Z 400
400
• 从上表可以看出: X产品通常会导致较长时间的库存; 而Z产品却大半个月无货可供!!不能适应市场需求。
因为每天的生产指标是由顺序计划和看板来实行的,所以使得每日适应成为可能;
最终的装配线上的投入顺序计划则是进行看板管理的出发点,这个投入顺序计划是以品
种均衡为目标,根据它可以均衡地从零部件供应商和零部件生产线领取各种零部件。
14
谢谢大家!
15
均衡生产
1
目录
一 • 均衡生产的定义 二 • 均衡生产的目的和意义 三 • 均衡生产中的两大均衡 四 • 均衡生产的实施条件 五 • 均衡生产的实施方法
精益生产之均衡化生产

精益生产之均衡化生产概述精益生产是一种以流程优化为核心的生产管理理念,旨在通过消除浪费,提高生产效率和质量,进一步提升企业的竞争力。
而均衡化生产则是精益生产的一个重要概念,它强调在生产过程中各个环节的平衡,以实现生产线的流程平稳和资源的有效利用。
均衡化生产的原则均衡化生产的核心原则是通过合理分配资源和优化生产流程来实现生产环节之间的平衡。
这里的资源包括人力、设备、原材料等,而生产流程则包括各个环节之间的工序、物料流动路径等。
为了实现均衡化生产,需要遵循以下原则:1. 根据客户需求进行生产计划均衡化生产的首要原则是以客户需求为导向。
只有充分了解客户需求,才能合理安排生产计划。
生产计划的制定应该考虑到不同产品的需求量、交货期限以及企业的生产能力,从而实现生产过程的平衡。
2. 平衡生产线的各个环节生产线上的各个环节应该在时间和能力上保持平衡。
通过合理地安排工序和物料流动路径,避免出现瓶颈环节或者空闲环节。
这样可以最大限度地提高生产线的效率。
3. 避免资源的浪费均衡化生产追求资源的最大化利用。
因此,需要避免资源的浪费,包括人力浪费、设备能力的浪费以及原材料的浪费。
通过优化生产流程,避免不必要的等待和运输时间,可以降低资源的浪费。
4. 强调持续改进均衡化生产是一个持续改进的过程。
通过不断地优化生产流程,改善生产环节之间的平衡,可以进一步提高生产效率和质量。
因此,企业应该建立持续改进的机制,不断寻找优化的空间,并进行相应的改进措施。
实施均衡化生产的关键步骤实施均衡化生产需要经过以下关键步骤:1. 分析生产过程首先需要对企业的生产流程进行分析,理清各个环节之间的关系和依赖。
通过绘制流程图或者价值流图,可以清楚地看到整个生产过程中的瓶颈环节和资源浪费的问题。
2. 识别问题和机会点在分析生产过程的基础上,需要识别问题和机会点。
问题包括生产线上的瓶颈、资源浪费以及质量问题等,而机会点则是指可以进一步优化的环节或者改进的措施。
均衡化生产

目录
1 2 3 4
精益生产的体系 一笔化的整体工厂布置
少人化
缩短作业切换时间
1.1精益生产理念
利润主义 以利润为中心,当市场售价降低时,成本也必须降低, 以便维持目标利润的经营思想。 成本=售价一利润 例如:公司的目标利润是200元,现在市场的售价 是1200元,那么目标成本就是1000元。如果市场 的售价降至1100元,为了维持200元的目标利润, 则必须降低成本至900元。很显然,采用这种经营 思想的企业就可以在竞争中立于不败之地。
4.2快速切换发展阶段
传统切换。切换作业没有标准,工人仅凭习惯和经验进行工作, 时间较长,通常需要数十分钟到数小时,甚至一天或几天的时 问。管理者也没有把切换作业列入改善工作范围之内。
单一作业切换。是指在10min之内完成作业切换。单一作业切 换应用在换模上称为快速换模。1969年在丰田,经过6个月的 改善成功将800t冲压机的作业切换时间由以前的4h降低1.5h, 再经3个月的时间,降为3min。单一作业切换是日本在IE领域 中的革新性方法之一,它给世界IE领域的理论和实践带来了思 路上的转变。 瞬间切换。指在1min之内完成作业切换,也就是“快餐式” 作业切换。现在许多世界一流的生产企业已进入到的瞬间切换 阶段。
多品种混流方式指多条专用生产线间的通用化和混流化,追 求1整数人工数。 专用生产线进行通用化
对B生产线进行通用化的改造,将A、C合理编排,使闲置的设备活用 和空间活用相联系起来,就可用5人生产。
通用生产线的负荷调整
如果从x生产线向y生产线转移0.5人工的工作量,从z生产线向y生产线 转移0.3人工的工作量,这时理论人工分别为4.2人工、3.2人工、3.2人 工,尾数较小,可以通过短时加班解决。这时实际需要配置人员可分别 为4人、3人、3人,在加班范围内就可以满足生产,节省了2名员工。
2024年《精益生产》学习心得(3篇)

2024年《精益生产》学习心得《精益生产》是由詹姆斯·P·温姆克勒和丹尼尔·T·琼斯合著的一本关于生产管理的经典著作。
该书介绍了精益生产的概念和原则,指导企业如何通过精益的方法来提高生产效率和质量。
阅读这本书对我来说是一次重要的学习经历。
下面是我对该书学习的心得体会。
首先,精益生产强调的是价值流的观念。
作者指出,企业的生产过程是一条价值流,而非孤立的生产环节。
通过对整个价值流进行分析和优化,企业能够发现生产过程中的浪费和瓶颈,从而不断提高生产效率。
在我工作的过程中,我也深刻体会到了这一点。
以前我只注重自己的工作环节,只关注自己的任务完成情况。
但是通过阅读《精益生产》,我逐渐认识到,只有将整个生产过程作为一个整体来考虑,才能找到真正的问题,并采取相应的措施来解决。
其次,精益生产提出了许多实用的工具和方法,帮助企业实现生产流程的优化。
其中,价值流图是一种重要的工具。
通过绘制价值流图,企业可以清晰地看到每个工序的价值添加和浪费的情况,从而有针对性地进行改进。
我在实际工作中也尝试过使用价值流图。
通过与同事共同绘制价值流图,我们发现了一些生产过程中的浪费和低效环节,并提出了相应的改进方案。
这些改进措施确实带来了明显的效果,提高了生产效率,降低了成本。
此外,精益生产还强调了持续改进的重要性。
作者指出,只有不断地挖掘潜在问题,找到改进的机会,并采取相应的措施,企业才能在竞争激烈的市场中立于不败之地。
我深深认同这一观点。
在实际工作中,我们经常会遇到各种问题和困难。
但是如果我们能够保持积极的改进心态,不断地寻找问题,找到解决问题的办法,就能够不断提高自己和团队的能力,并逐步达到卓越的业绩。
综上所述,阅读《精益生产》是一次十分有价值的学习经历。
通过学习这本书,我不仅对精益生产的理念和原则有了更深入的理解,而且学到了许多实用的工具和方法,可以帮助我更好地管理和提高生产效率。
我相信,在今后的工作中,我将能够应用这些知识和技巧,不断改进自己的工作,实现更好的业绩。
精益生产之均衡化生产

精益生产之均衡化生产均衡化是丰田生产方式的大前提均衡化是与市场需求同步,同时将生产量与机种平均。
翻译成英文是"level(拉平)"的意思。
但为了强调并理解『同时将生产量与机种平均』,建议直接使用日语发音的"Heijunka"作为专业术语。
均衡化生产是丰田生产方式的大前提,和说明其它手法时一样,均衡化生产是在理解了丰田生产方式的目标与两大支柱之后的进一步研究的课题。
什么是均衡化?均衡化是将生产量与机种在一定的时间内加以平均的意思,例如并不是早上只生产"A",下午只生产"B",而是将"A、B"切割成小批量,交错地生产。
为什么要实施均衡化?如果实施了均衡化就可以不必批量生产,而可以和市场需求同步,结果就是没有浪费地生产,在整个物料流动范围内就能以最少的库存、资金、工种和前置时间来营运了。
批量生产与均衡化生产■批量生产效率在装配部门几乎所有的人都认为要尽可能地、持续地制造同种机种的产品,避免机种的频繁切换,但是这种方法会带来比较高的成本。
■批量生产前置时间延长批量生产会延长前置时间,顾客需要的产品若不进行批量生产,就无法满足客户的需求。
若提前为顾客准备好各自机种的库存,就必须增加完成品的库存。
■批量生产的材料与零件批量制造的话则需要批量地使用材料与零件,这也加大了半成品的库存。
■批量生产的品质批量生产会隐蔽不良品,如果在该批量生产期间未被发现,不良品就会不断地被制造出来,所以品质无法保障。
■批量生产和团队在批量生产过程中你会看到即使某生产线的人很忙,但其他生产线的人却很悠闲。
这种方式会有许多的浪费,同时工作的『不均匀』也会产生『不合理』,而『不合理』则会影响生产安全和折损员工士气。
精益生产之均衡化生产

绿色生产的融合
环保理念:注重环境保护减少 污染排放
绿色技术:采用环保技术和工 艺提高生产效率
循环经济:实现资源的循环利 用降低资源消耗
绿色供应链:建立绿色供应链 实现上下游企业的协同发展
定制化生产的趋势
个性化需求:消费者对个性化产品的需求日益增长 技术进步:3D打印、智能制造等技术的发展为定制化生产提供了可能 供应链管理:供应链管理技术的提升使得定制化生产更加高效和灵活
意义:均衡化生产可以 提高生产效率降低生产 成本提高产品质量增强 企业的竞争力。同时也 可以减少生产过程中的 浪费和环境污染符合可 持续发展的理念。
实现方式
采用先进的生产技术提高生产 效率
合理安排生产计划避免生产瓶 颈
加强供应链管理确保原材料供 应稳定
提高员工技能水平减少生产过 程中的浪费
适用范围
利实施
调整生产流程
确定生产瓶颈:分析生产过程中 的瓶颈环节找出影响生产效率的 因素
引入自动化设备:引入自动化设 备减少人工操作提高生产效率
添加标题
添加标题
添加标题
添加标题
优化生产流程:对瓶颈环节进行 优化提高生产效率
培训员工:对员工进行培训提高 他们的技能和素质提高生产效率
优化资源配置
确定生产目 标:明确生 产任务和生 产目标
环保意识:消费者对环保产品的需求增加定制化生产可以减少浪费降低环境影响
全球化生产的挑战与机遇
挑战:全球市场竞争激烈需要不断提高产品质量和降低成本 机遇:全球市场广阔可以扩大销售范围提高利润 挑战:全球供应链管理复杂需要加强供应链管理能力 机遇:全球供应链管理可以降低库存成本提高生产效率
THEME TEMPLATE
感谢观看
精益生产名词解析:均衡化与库存

精益生产名词解析:均衡化与库存Heijunka(均衡化)
在固定的生产周期内,平衡产品的类型与数量。
这样可以在避免大量生产的同时,有效的满足顾客的需求,最终带来整条价值流中的最优化的库存、投资成本、人力资源以及产品交付期。
举例说明“按照客户需求的产品数量来均衡生产”:假设一个制造商每周都收到500个产品的订单,但是每天收到的订单的产品数量却有着显著的差别:周一要运送200个,周二100个,周三50个,周四100个,周五再运送50个。
为了平衡产量,制造商可能会把少量的已经完工的产品储存在装运处,作为一种缓冲来满足周一的高需求量,并按照每天生产100个产品的产量,来平衡整个一周的生产。
通过在价值流终点库存少量成品,制造商可以平衡顾客的需求,同时,更有效地利用整条价值流的资源。
Inventory(库存)
沿着价值流各工序之间存在的成品或半成品。
库存通常按照其在价值流中所处的位置及用途来进行分类。
原材料,在制品和成品都是用来描述库存位置的术语。
而缓冲库存,安全库存,以及装运库存则是用来描述库存用途的术语。
库存可能发生在价值流中的某一个位置和某一种用途。
因此,“成品”和“缓冲库存”极可能指的是同样的产品。
类似的,“原材料”和“安全库存”也有可能指代相同的产品。
为了避免混淆,仔细地定义每一类的库存是十分重要的。
- 1、下载文档前请自行甄别文档内容的完整性,平台不提供额外的编辑、内容补充、找答案等附加服务。
- 2、"仅部分预览"的文档,不可在线预览部分如存在完整性等问题,可反馈申请退款(可完整预览的文档不适用该条件!)。
- 3、如文档侵犯您的权益,请联系客服反馈,我们会尽快为您处理(人工客服工作时间:9:00-18:30)。
产量/台
20
30
0 1 2 3 4 5 n
1 2 3 4 5 m 日期
长期波动
如果完全按照准时化生产,则会产生生产要素配置的浪费; 如果不按准时化生产,则会产生库存浪费。 因而要权衡产能损失与库存浪费的最佳平衡点。根据经验,日产量允 许存在着一定的变化幅度,但为保持人员和设备的稳定性,应把振幅控制 在20%之内。
例如,X、Y、Z三种产品各由A、B、C三种零件组成,如下表: 各产品零件构成
产品名称 X产品 Y产品 Z产品 A零件 10 2 3 B零件 2 5 8 C零件 3 2 5
下表为X、Y、Z批量分别为50件、30件、20件时需要的各种零件数量。 改进前每天各产品零件消耗数量
产品 批量 A零件 B零件 C零件
• 均衡生产排产计划 1、制定生产节拍 定义:生产节拍是指连续生产出2个产品所需要的时间间隔。
一天正常生产时间 生产节拍= 一天生产数量
生产数量并不一定是固定的 ,每天的生产节拍也不是固定 不变的,它们随生产任务而变 化。
均衡生产是指每天要以一定的节拍循环地生产多个品种
例:仍以X、Y、Z三种产品为例。假设一天工作时间为8小时,则产品X、 Y、Z节拍分别为9.6min, 16min ,24min,各产品平均节拍为4.8min。可以 看出,均衡生产可以理解为在当月里,用与各种产品的平均销售速度同步 进行生产。 均衡化生产的生产节拍
总量均衡就是将一个单位期间内的总订单量平均化,即将 连续两个单位期间的总生产量的波动控制到最小程度。
生产总量不均衡 产品产量出现波动 人和设备要依照生产 量的高峰期做准备 产量减少时,容易产 生人员、库存等浪费
总量均衡的重要性
总量均衡案例分析
某月某产品的实际需求量为400台,一月生产20天,每日生产量的需 求不同,最高日30台/日,最低日10台/日,如图所示。
4
均衡化生产
本章要点
4.1 均衡化生产概念 4.2 总量均衡 4.3 品种均衡 4.4 均衡生产实施
4.1 均衡化生产概念
浪费、负载过重与不均衡概念 杜绝浪费是精益生产方式的核心。在日语中浪费用“Muda”表示, 在精益生产方式中,“Muri”(负荷过重)和“Mura”(不均衡)也 与Muda同等重要。
a)均衡前
对装配线生产进行配种均衡即采用混流生产如b)所示。
b)均衡后
采用品种均衡后,通常把所需工时 多的产品、所需工时一般的产品、 所需工时少的产品合理地搭配,均 衡的进行流水混流生产,可有效解 决装配线平衡问题。
据美国有关资料统计,即使在 美国这样工业发达的国家,在 工业装配生产中平均要有5%10%的生产时间是浪费在平衡 延迟上。
这种以天为单位的生产安排,每天将依旧按照批量生产的方式, 即先生产50件X产品,其次是30件Y产品,最后是20件Z产品。
某日生产计划
产品 X Y Z 产量 1000 600 400 8:00 9:00 10:00 11:00 12:00 13:00 14:00 15:00 16:00
50 30 20 改进后的日生产安排
品种 X Y Z 总量 1000 600 400
1
2
3
4
5
6
7
8
9 10 11 12 13 14 15 16 17 18 19 20
1000 600 400
由表中可以看出,X产品通常会导致较长时间的库存,而Z产品 却大半个月无货可供。
传统的大批量生产的方法可以节省作业转换时间,但是,与 市场需求会出现很大差异。为满足需求多样性,进行如下改进: 每天生产X产品50件,Y产品30件,Z产品20件,改进后的月生 产排程如表所示: 某月生产计划
产品 X Y Z X Y Z X Y Z 批量 5 3 2 5 3 2 5 3 2 62 41 31 62 41 31 62 41 31 A零件 B零件 C零件
以这样的思路改进下去,不断细化生产单位,直到可以按照“X—Y —X—Z—X—Y—X—Z—X—Y”的顺序重复生产,达到最小的观察时间 单位,满足精益生产倡导的以小时、分钟为单位进行安排的要求,实现 均衡化生产。
案例:
某工厂某月有三种产品X、Y、Z需要生产。X产品的需求数为1000 件,Y产品为600件,Z产品为400件。假若每月工作日为20天,则传 统生产计划安排为前10个工作日先将X产品生产完毕,然后6天生产 Y产品,最后4天生产Z产品。这是一种常见的型态,也称分段生产。
传统的生产排程
(单位:个)
某月生产计划
产生中间库存
(4)若对后工序进行品种均衡,按照“A—B—A—B—A…”循环顺序 进行生产,这样可消除库存和等待,同时生产能力配置可减少50%。
实行品种均衡的混流生产
案例二: 下图为生产a、b、c三种车型的装配线。a车型作业时间是4.2min,b车 型3.8min,c车型4.0min。根据生产需求,装配线的平均节拍是4min,如 果采取连续生产方式,如图a)所示。整个装配线需要按最大节拍4.2min (生产a车型)配置人员,但当最小节拍3.8min(生产b车型)时则会产生 等待,从而造成人员浪费。
月合计:400台
仍以某月生产400台产品为例, 如在当天需求量稍大于20台时,靠 加班即可解决;需求小于20台时, 提前结束生产。
平均
20
10 17 10 配置生产要素
提前结束
0 1 2 3 4 5 6
日期
短期波动
2、长期波动 对于周期性的大幅波动,则需要重新进行总量均衡配置生产 要素,而进行产品总量均衡的周期由产品特点及工厂管理能力而 定:产品需求量波动频繁则调整也应频繁进行, 工厂管理能力强则可以在需要的时候及时调整; 如果不强则只能允许浪费的存在或供不应求。
混流生产的均衡化
均衡化生产概念
均衡化生产也称平准化生产,各种产品的生产节拍与对应产 品的平均销售节拍一致。
采取混流生产、缩短作业转换时间、一个流生产、准时采购、 全面品质管理等管理手段和方法来实现。
总量 均衡
均衡化生产
品种 均衡
实现准时化的前提 条件,实现看板管 理的基础。
4.2 总量均衡
定义:
X产品
Y产品 Z产品
50
30 20
500
60 60
100
150 160
150
60 100
从表中可知,每天按X、Y、Z各自批量生产,则各个零件波动 较大。例如,当生产X产品时需要A零件为10个,当生产Y产品时需要 A零件为2个,这样容易产生库存和人员的浪费。
如果1天内产品X、Y、Z按照5:3:2的比例进行轮番生产,1/10个 工作日重复1次,则1/10个工作日内各个零部件的消耗速率就相同。 改进后的零部件消耗数量
按品种均衡就是要在一定的周期内各品种出现比率是均等的,并 且时间、周期尽可能缩短,尽量细化观察标准,如下图,这样使产品 瞬时生产数量波动尽可能控制到最小程度。
品种观察细化观察时间单位
按不同时间单位均衡的实例
• 品种均衡的作用 案例一: 某汽车装配线装配A、B两种车型,装配顺序是4个A型车和2个B型 车循环。装配线和部件线的生产节拍都是4min,生产部件A和B的工序都 需要两名操作工。由于车型的不同而需要不同的部件,即装配A型车需 要用到A部件,装配B型车需要用到B部件,如下图所示。
设法将变动的幅度控制在10%以内。 如果要结束某种特定类型产品的生产,必须事先 通知供应商,并对相关损失进行补偿。
4.4 均衡生产实施
• 均衡生产实施阶段
迅速适应需求变 化的生产 准时生产(仅能销售的数量生产 能销售的物品) 每月的适应 每日的适应 (对应于总 (对于分品 量的销售速度< 种的销售速度 循环时 的产生) 按照当天分品 各工序的月份生产 间的生产) 种的 能力计划 循环时间的生 内示各工序品 通过看板方式 通过看板方式 产指示 种的月份 进行+10% (拉动方式) 生产量和每天 进行的对前工序 左右的微调 决定各品种的月生产计划(基本生产计划) 的平均生 每天的生 决定混流装配线的产品顺序计划 产量 产指示 月份需求预测 均衡生产 来自销售商的日订货 柔性设备 缩短生产过程时间
20
据此配置生产要素
0
1
2
3
4
5
6
日期
实行总量均衡
实施总量均衡后,虽然每天按照相同的数量准备人员及生产 要素,但需求仍有可能产生波动,可分为短期波动和长期波动两 种情况。 1、短期波动 对于短期内需求有小幅度波动,当需求量增大时可以采取加 班方式,需求量减少时则提早结束生产。
加班
产量/台
30 22 24
品种 X Y Z 总量 1000 600 400 1 2 3 4 5 6 7 8 9 10 11 12 13 14 15 16 17 18 19 20
50个/日 30个/日 20个/日
一个月20天每天重复1次,共20次,就可以每天生产出X、Y、Z 产品,产品积压与短缺的情况将大大减少生产资源利用率也将提高。 但是应当设法减少每天作业转换的辅助时间。
Muda 浪费
可视为上述两“M” 的波动结果, 其来自 不合理的生产日程, 或是由于内部问题 而导致的产量波动
未能创造价值,不 增值的活动
Mura 不均衡
Muri 负荷过重
员工或设备的负荷 过重
工厂中生产线工位生产能力不均衡示例:
瓶颈 能力 平均 9.7 11 10 10 8
不平衡时产生库存
10 10 10.5 8.5
产量/台
30
22 24 月合计:400台
平均 20 10
17 10
0
1
2
3
4
5
6
日期
实行总量均衡前
如果采用总量均衡的办法,是日产量保持一致,即每天生产20台, 则可以按这个产量准备人员以及生产要素。这样,总产量没有减少, 人员以及生产要素却可以减少1/3,成本也就随之降低。