数控加工常用刀具的种类及选择
数控刀具选用培训教程

数控刀具选用培训教程在现代机械加工领域,数控刀具的选用是一项至关重要的工作。
正确选用数控刀具不仅能够提高加工效率和质量,还能降低生产成本和减少设备损耗。
本教程将为您详细介绍数控刀具选用的相关知识和技巧。
一、数控刀具的分类数控刀具种类繁多,常见的有以下几种:1、车削刀具包括外圆车刀、内孔车刀、螺纹车刀等。
外圆车刀用于加工外圆柱面和外圆锥面;内孔车刀用于加工内圆柱面和内圆锥面;螺纹车刀用于加工各种螺纹。
2、铣削刀具如立铣刀、面铣刀、球头铣刀等。
立铣刀适用于加工平面、台阶、沟槽等;面铣刀主要用于大面积平面的铣削;球头铣刀常用于曲面的加工。
3、钻削刀具有麻花钻、中心钻、深孔钻等。
麻花钻是最常见的钻孔刀具;中心钻用于加工中心孔;深孔钻用于加工深孔。
4、镗削刀具包括粗镗刀、精镗刀等,用于镗削内孔。
二、数控刀具的材料数控刀具的材料对其性能有着重要影响,常见的刀具材料有:1、高速钢具有较高的强度和韧性,但其耐热性和耐磨性相对较差,适用于低速切削。
2、硬质合金硬度高、耐磨性好、耐热性强,是目前应用最广泛的刀具材料之一。
3、陶瓷刀具具有极高的硬度和耐磨性,适用于高速切削,但韧性较差。
4、立方氮化硼(CBN)和金刚石刀具这两种刀具材料硬度极高,适用于加工高硬度材料,但价格昂贵。
三、数控刀具选用的基本原则1、加工工艺要求根据加工零件的形状、尺寸、精度和表面质量要求,选择合适的刀具类型和规格。
2、被加工材料不同的材料具有不同的切削性能,例如,加工钢件通常选用硬质合金刀具,而加工铝合金则可以选用高速钢刀具。
3、机床性能考虑机床的功率、转速、刚性等因素,确保选用的刀具能够在机床上正常工作。
4、刀具寿命在保证加工质量的前提下,尽量选择寿命较长的刀具,以降低刀具成本。
四、数控刀具选用的具体步骤1、分析零件图纸了解零件的形状、尺寸、精度要求以及材料等信息,确定加工工艺和刀具类型。
2、选择刀具材料根据被加工材料和切削速度等因素,选择合适的刀具材料。
数控刀具材料及选用技巧归纳

数控刀具材料及选用技巧归纳数控加工技术自推出以来已得到广泛应用,并逐渐成为了现代制造业的重要基础技术。
数控刀具则是其中的重要组成部分,是数控加工过程中直接参与的切削工具。
为了确保数控加工的准确性和高效性,刀具的材料与选用技巧显得尤为重要。
本文将对数控刀具材料及选用技巧做一些归纳总结。
一、数控刀具的分类及特点1. 按切削方式分类:钻头、铣刀、车刀、螺纹刀等;2. 按材料分类:高速钢刀具、硬质合金刀具、陶瓷刀具、普通钢刀具等;3. 按适用范围分类:铸铁刀具、钣金刀具、铜刀具等。
不同的数控刀具在使用时,具有不同的特点。
如高速钢刀具硬度较低,价格低廉,适合加工较易切削的材料;硬质合金刀具则硬度高、韧性好、适用于切削难加工的材料,但价格较高;陶瓷刀具的硬度最高,耐磨性好,但质量轻,容易折断等。
二、数控刀具材料的选择1. 选择耐磨系数高的材料,如硬质合金刀具与CBN刀片等;2. 选择好维护的材料,如钢铁类材料、碳化钨等;3. 选择体积小、质量轻的材料,能清晰观察加工过程,减小机床负重,如高温陶瓷刀具、钒钛合金刀具等。
在材料选择的过程中,需要综合考虑切削加工的条件、材料特点、成本以及最终的质量要求等因素。
同时还要考虑机床和数控系统的技术参数,以选择适合的刀具材料。
三、数控刀具的选用技巧1. 根据不同切削加工作业选择不同的刀具;2. 根据数控机床的技术参数,避免选择易断裂的刀具;3. 考虑刀具的耐磨性和切削性,以便达到较高的加工效率。
选用数控刀具时,还需要注意一些基础的技巧,如:1.刀具的表面质量是选择刀具的关键因素之一;2. 避免深入切削,从而减少工具磨损;3. 建立合理的数控程序,以充分发挥刀具的潜力。
四、正确保养数控刀具切削刃的钝化往往源于不正确的保养,对其的保养维护是切削刃的使用条件。
下面我们介绍正确的保养技巧。
1. 避免使用含砂粒、粗糙或刮擦物品的清洗方法;2. 分别存放钻、铣、刨等刀具,不要放在一个盒子里;3. 刀具表面应涂上保养油等防锈剂;4. 切削刃失效后,刀具应及时刀磨、选配新刀片。
数控加工技术学习中的刀具选择指南

数控加工技术学习中的刀具选择指南随着科技的不断发展,数控加工技术在工业生产中得到了广泛应用。
而在数控加工过程中,刀具的选择是至关重要的一环。
本文将为大家介绍数控加工技术学习中的刀具选择指南,帮助大家更好地理解和掌握这一技术。
一、刀具材料选择刀具材料的选择直接影响着加工效果和刀具寿命。
常见的刀具材料有高速钢、硬质合金和陶瓷等。
在选择刀具材料时,需要考虑加工材料的硬度、韧性和热导率等因素。
1. 高速钢刀具:适用于加工低硬度材料,具有较好的韧性和耐磨性,价格相对较低。
但对于高硬度材料的加工,高速钢刀具的寿命较短。
2. 硬质合金刀具:适用于加工高硬度材料,具有较高的硬度和耐磨性。
但硬质合金刀具的韧性较差,容易断裂,价格也相对较高。
3. 陶瓷刀具:适用于加工高硬度和高温材料,具有优异的耐磨性和高温稳定性。
但陶瓷刀具易碎,加工过程需要注意避免冲击和振动。
二、刀具几何形状选择刀具的几何形状对加工效果和刀具寿命有着重要影响。
常见的刀具几何形状包括平头刀、球头刀和锥度刀等。
1. 平头刀:适用于平面加工和开槽等操作,具有较大的切削面积,能够提高加工效率。
但平头刀容易产生振动和噪音,需要注意加工过程中的稳定性。
2. 球头刀:适用于曲面加工和倒角等操作,能够实现复杂曲线的加工。
球头刀具有较小的切削力和较好的表面质量,但加工效率相对较低。
3. 锥度刀:适用于孔加工和倒角等操作,能够实现不同直径的孔加工。
锥度刀具有较好的切削刚度和切削稳定性,但需要注意加工过程中的刀具中心偏移问题。
三、刀具涂层选择刀具涂层能够有效提高刀具的耐磨性和耐高温性,延长刀具的使用寿命。
常见的刀具涂层包括涂层碳化物、涂层氮化物和涂层氧化物等。
1. 涂层碳化物:具有较高的硬度和耐磨性,能够有效减少切削力和热膨胀。
涂层碳化物适用于加工高硬度材料和高温材料。
2. 涂层氮化物:具有较好的耐磨性和耐高温性,能够提高刀具的切削速度和切削深度。
涂层氮化物适用于高速切削和重切削操作。
数控车削用刀具的常用分类
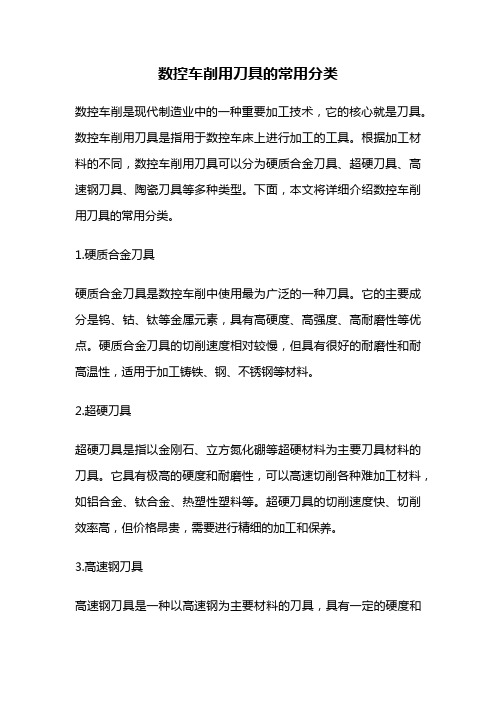
数控车削用刀具的常用分类数控车削是现代制造业中的一种重要加工技术,它的核心就是刀具。
数控车削用刀具是指用于数控车床上进行加工的工具。
根据加工材料的不同,数控车削用刀具可以分为硬质合金刀具、超硬刀具、高速钢刀具、陶瓷刀具等多种类型。
下面,本文将详细介绍数控车削用刀具的常用分类。
1.硬质合金刀具硬质合金刀具是数控车削中使用最为广泛的一种刀具。
它的主要成分是钨、钴、钛等金属元素,具有高硬度、高强度、高耐磨性等优点。
硬质合金刀具的切削速度相对较慢,但具有很好的耐磨性和耐高温性,适用于加工铸铁、钢、不锈钢等材料。
2.超硬刀具超硬刀具是指以金刚石、立方氮化硼等超硬材料为主要刀具材料的刀具。
它具有极高的硬度和耐磨性,可以高速切削各种难加工材料,如铝合金、钛合金、热塑性塑料等。
超硬刀具的切削速度快、切削效率高,但价格昂贵,需要进行精细的加工和保养。
3.高速钢刀具高速钢刀具是一种以高速钢为主要材料的刀具,具有一定的硬度和耐磨性。
它的切削速度相对较快,适用于加工较软的材料,如铝、铜、铁等。
高速钢刀具价格相对便宜,但需要定期进行磨刃和更换。
4.陶瓷刀具陶瓷刀具是指以氧化锆、碳化硅等陶瓷材料为主要材料的刀具。
它具有极高的硬度和耐磨性,可以用于高速切削各种难加工材料,如镁合金、钛合金等。
陶瓷刀具的切削速度快、寿命长,但价格昂贵,需要进行精细的加工和保养。
5.刀柄刀柄是刀具的支撑部分,也是数控车削中的重要组成部分。
根据使用方式的不同,刀柄可以分为直柄、切削柄、内螺纹柄、外螺纹柄等多种类型。
直柄适用于较小的切削力,切削柄适用于较大的切削力,内螺纹柄适用于内孔加工,外螺纹柄适用于外圆加工。
数控车削用刀具的分类有很多种,每种刀具都有其特点和适用范围。
在实际应用中,需要根据加工材料和工件形状等因素选择合适的刀具。
同时,需要注意刀具的保养和更换,以提高加工效率和质量。
数控刀具材料与选择

普通刀具材料
三、数控刀具的材料
硬质合金 硬质合金是由难熔金属碳化物(如TiC、WC、NbC等)
和金属粘结剂(如Co、Ni等)经粉末冶金方法制成。 硬质合金的性能特点:硬质合金中高熔点、高硬度碳化物 含量高,因此硬质合金常温硬度很高,达到78~82 HRC, 热熔性好,热硬性可达800℃~1000℃以上,切削速度比 高速钢提高4~7倍。硬质合金缺点是脆性大,抗弯强度和 抗冲击韧性不强。抗弯强度只有高速钢的1/3~1/2,冲击 韧性只有高速钢的1/4~1/35。硬质合金力学性能主要由 组成硬质合金碳化物的种类、数量、粉末颗粒的粗细和粘 化剂的含量决定。碳化物的硬度和熔点越高,硬质合金的 热硬性也越好。粘结剂含量大,则强度与韧性好。碳化物 粉末越细,而粘结剂含量一定,则硬度高。
涂层刀具有四种:涂层高速钢刀具,涂层硬质合金 刀具,以及在陶瓷和超硬材料(金刚石或立方氮化硼)刀 片上的涂层刀具。
三、数控刀具的材料
涂层方式: TiN涂层:在高温时能产生氧化膜,与铁基材料摩擦 系数较小,抗粘结性能好,并能有效降低切削温度。
TiC—TiN复合涂层: 第一层涂TiC,与刀具基体粘牢不易脱落。第二层 涂TiN,减少表面层与工件间的摩擦。 TiC-Al203复合涂层: 第一层涂TiC, 与刀具基体粘牢不易脱落。第二层涂 Al203可使刀具表面具有良好的化学稳定性和抗氧化性 能。 目前单涂层刀片已很少应用,大多采用TiC-TiN复 合涂层或TiC-Al2O3-TiN三复合涂层。
三、数控刀具的材料
陶瓷刀具的特点:有很高的硬度和耐磨性,刀具寿命 比硬质合金高;具有很好的热硬性,摩擦系数低,切削力 比硬质合金小,用该类刀具加工时能提高表面质量。 缺 点是脆性大,抗冲击性能很差。
模具数控加工的刀具选购与使用管理指导

模具数控加工的刀具选购与使用管理指导一、目的:为规范公司的刀具管理和使用,控制刀具耗用成本,提高刀具的使用寿命,减少刀具不合理使用导致加工精度或工件异常问题,提高工作效率,特制定本指导书。
二、适用范围:适用于公司各加工工序使用刀具的管理及采购刀具、刀具仓储管理。
包括:刀具供应商开发、刀具选择、计划、采购、入库保管、领出、使用、车间刀具管理及退库的整个过程。
三、刀具述语与品牌简述:1.刀具定义:广义的刀具包括以下几种:●CNC铣削刀具:包括通用立铣刀(分平底立铣刀、圆鼻立铣刀、球头立铣刀)、非标立铣刀、刀盘、刀粒、刀片、刀头、刀杆等。
●车床刀具:车刀杆、车刀片、装夹卡盘等;●钻床刀具:钻头(分钨钢、高速钢、含钴高速钢、粉末冶金含钴高速钢四种)、枪钻、钻咀、铰刀(分钨钢、高速钢、含钴高速钢三种)等。
●攻丝螺纹刀具:丝攻丝锥(镍基高温合金及钛合金专用丝锥)、螺纹锥等。
●夹具、热装夹头:夹头、刀柄、热胀刀柄、刀把、弹簧筒夹、BIG刀具装夹工具等。
可以根椐不同的加工工件尺寸和工艺方法,按需要组合成铣、钻、镗、铰、攻丝等各类工具进行切削加工。
2.刀具寿命:从开始加工到刀尖报废整个过程中,刀尖切削工件的时间或切削过程中在工件表面实际的长度。
刀尖加工时间为每个刀具公司计算刀具寿命的主要考核指标。
刀具质量、正确选择、合理使用、优化编程、正确操作等因素,对工件加工精度的控制至关重要的,也关系到了刀具的使用寿命,所以,在使用刀具时,了解程式和零件的加工要求,根据加工中心机床的特点,根据工件材料的特性,正确安排加工工艺、优化编程参数(主轴转速、进给量、进给速度、切削速度等)、正确选用刀具夹具、合理使用刀具,发挥刀具最大效果,制造出高精密的零件,降低刀具使用成本;CNC工序的刀具使用量大,故CNC组长是刀具的使用与管理的主要责任人。
3.刀具成本与加工成本的关系:刀具成本:是指在生产过程中,每年采购所有刀具工具的费用,是生产成本的一部分。
数控机床刀具的选择
(2)硬质合金(Cemented Carbide)
1)普通硬质合金
①钨钴类(YG)
WC+Co,强度好,硬度和耐磨性较差, 用于加工脆性材料、有色金属和非金属 材料。常用牌号:YG3、YG6、YG8、 YG6X。数字表示Co的百分含量, Co多 韧性好,用于粗加工; Co少用于精加 工。
2)新型硬质合金 ①钨钛钽(铌)钴类
在YG类中添加 TaC 或 NbC,可提高 高温硬度、强度、耐磨性。用于加工 难切削材料和断续切削。
②通用合金(YW)
在YT类中添加合金,可提高抗 弯强度,冲击韧性,耐热性及高 温强度,抗氧化性等。
(3)新型刀具材料
① 涂层刀具
刀具基体材料上涂一薄层耐磨性 高的难熔金属化合物而得到的刀具材 料.
具 装三面刃铣刀
装面铣刀
M
装有扁尾莫氏锥柄刀具
TQW
倾斜式微调镗刀
XDZ
装直角端铣刀
G C 规格
攻螺纹夹头
TQC
倾斜式粗镗刀
XD
装端铣刀
切内槽工具
TZC
直角形粗镗刀
用数字表示工具的规格,其含义随工具不同而异。有些工具该数字为轮廓尺寸D-L;有些工具 该数字表示应用范围。还有表示其他参数值的,如锥度号等。
②钨钛钴类(YT)
TiC+WC+Co类(YT):常用牌号有YT5、 YT14、YT15、YT30等。此类硬质合金硬度、 耐磨性、耐热性都明显提高,但韧性、抗冲 击振动性差,主要用于加工钢料,不宜加工脆 性材料。含TiC量多,含Co量少,耐磨性好, 适合精加工;含TiC量少,含Co量多,承受 冲击性能好,适合粗加工。
数控车床常用刀具及选择
数控车床常用刀具及选择1. 数控刀具的结构数控车床刀具种类繁多,功能互不相同。
根据不同的加工条件正确选择刀具是编制程序的重要环节,因此必须对车刀的种类及特点有一个基本的了解。
在数控车床上使用的刀具有外圆车刀、钻头、镗刀、切断刀、螺纹加工刀具等,其中以外圆车刀、镗刀、钻头最为常用。
数控车床使用的车刀、镗刀、切断刀、螺纹加工刀具均有整体式和机夹式之分,除经济型数控车床夕卜,目前已广泛使用可转位机夹式车刀。
(1) 数控车床可转位刀具特点数控车床所采用的可转位车刀,其几何参数是通过刀片结构形状和刀体上刀片槽座的方位安装组合形成的,与通用车床相比一般无本质的区别,其基本结构、功能特点是相同的。
但数控车床的加工工序是自动完成的,因此对可转位车刀的要求又有别于通用车床所使用的刀具,具体要求和特点如下表所示。
(2) 可转位车刀的种类可转位车刀按其用途可分为外圆车刀、仿形车刀、端面车刀、内圆车刀、切槽车刀、切断车刀和螺纹车刀等,见表2-3。
表2-3可转位车刀的种类刀具材料切削性能的优劣直接影响切削加工的生产率和加工表面的质量。
刀具新材料的岀现,往往 端面车刀900、 450、 750 普通车床和数控车床 内圆车刀450、600、750、900、910、930、 950、107.50 普通车床和数控车床 切断车刀普通车床和数控车床 螺纹车刀普通车床和数控车床切槽车刀普通车床和数控车床 (3) 可转位车刀的结构形式① 杠杆式:结构见图2-16,由杠杆、螺钉、刀垫、刀垫销、刀片所组成。
这种方式依靠螺钉旋紧压靠杠杆,由杠杆的力压紧刀片达到夹固的目的。
其特点适合各种正、负前角的刀片,有效的前角范围为 -60°〜 +180°;切屑可无阻碍地流过,切削热不影响螺孔和杠杆;两面槽壁给刀片有力的支撑,并确保转位精度。
② 楔块式:其结构见图2-17,由紧定螺钉、刀垫、销、楔块、刀片所组成。
这种方式依靠销与楔块的挤压力 将刀片紧固。
数控加工常用刀具及参数选择
数控加工常用刀具及加工参数刀具的选择和刀具参数的设置是数控加工工艺中的重要内容,合理地选用刀具和设置刀具参数不仅可以影响数控机床的加工效率,而且可以直接影响加工质量。
1.数控铣削加工常用刀具铣削用刀具通常称为铣刀,普通铣床上的刀具可以用于数控铣床和加工中心上。
一般立式数控加工用铣刀的种类可以有很多种划分方法,既可以从刀具的材料上划分,也可以从刀具的外形上划分,还可以从刀具的用途等方面来划分。
依刀具的外形,数控加工常用的刀具有平刀、圆鼻刀(飞刀)、球刀三种。
(1)平刀平刀底面是平面,平刀是一种以侧刃切削的刀具,所以使用平刀加工时应尽量避免切入底面的工件表面,一般平刀用作开粗和加工平面。
常用平刀大小有D1、D2、D4、D6、D8、D10、D12、D16、D20。
(2)圆鼻刀(飞刀)圆鼻刀底面是平面,每刃都带有圆角,因为底面是平面,所以加工时也应尽量避免切入底面的工件表面,一般圆鼻刀用作开粗,圆鼻刀开粗效果比平刀好。
常用圆鼻刀(飞刀)大小有D25R5、D3OR5。
(3)球刀球刀的切削刃有180°,所以球刀一般用作精加工,球刀切削时较稳定,但球刀不能用作开粗。
常用球刀大小有R1、R2、R3、R4、R5、R6、R8。
2.加工参数的选择随着模具制造技术的高速发展,刀具的加工参数的设置对加工的效率和加工质量的影响越来越大。
熟练掌握刀具加工参数的设置有利于提高加工的效率和加工质量。
刀具加工参数包括切削速度、进给量、背吃刀量(切削深度)和切削宽度。
(1)切削速度v切削速度是指铣刀刀齿切削处的线速度。
v=πDn/1000式中v—切削速度(m/min);D—铣刀直径(mm),周铣时为圆柱铣刀外圆直径;n—主轴转速(rmin)(2)进给量a,f铣削进给量有三种形式:铣刀每转过一个刀齿相对工件移动的距离称为每齿进给量a,其大小决定着一个刀齿的负载,a越大,切削力越大,刀齿的负载也越大。
铣刀每转相对工件移动的距离称为每转进给量f。
数控车床刀具的选择及应用方法
数控车床刀具的选择及应用方法
数控车床刀具的选择及应用方法包括以下几点:
1. 刀具材质选择:根据数控车床的加工材料和加工工艺要求选择合适的刀具材料。
常见的刀具材料有硬质合金,高速钢,陶瓷刀具等。
2. 刀具类型选择:根据具体的加工任务选择合适的刀具类型。
常见的数控车床刀具类型有车刀、铣刀、钻孔刀具等。
3. 刀具尺寸选择:根据工件的尺寸和形状确定刀具的尺寸。
刀具尺寸要与工件的加工要求相匹配,包括刀具长度、刀尖半径、刀具直径等。
4. 刀具刃口选择:根据加工要求选择合适的刀具刃口类型,如单刃刀具、双刃刀具、倒角刀具等。
5. 刀具涂层选择:对于高速切削和长时间连续加工的任务,可以选择带有涂层的刀具,以提高切削性能和刀具寿命。
刀具应用方法:
1. 安装刀具:在安装刀具之前,要确保刀具和刀座的匹配性。
安装时要注意刀具和刀座的固定方式,确保刀具稳定不松动。
2. 刀具调试:在加工之前,要对刀具进行调试。
调试包括刀具的位置、刀具的刃口与工件的间距、切削速度、进给速度等参数的调整。
3. 切削过程中的刀具监控:在切削过程中,要及时监控刀具的磨损情况。
一旦刀具出现磨损或断刃等情况,应及时更换或修复刀具。
4. 刀具保养:刀具在使用过程中要注意保养和清洁。
保持刀具的干燥和清洁,定期进行润滑和维护,以延长刀具的使用寿命。
- 1、下载文档前请自行甄别文档内容的完整性,平台不提供额外的编辑、内容补充、找答案等附加服务。
- 2、"仅部分预览"的文档,不可在线预览部分如存在完整性等问题,可反馈申请退款(可完整预览的文档不适用该条件!)。
- 3、如文档侵犯您的权益,请联系客服反馈,我们会尽快为您处理(人工客服工作时间:9:00-18:30)。
数控加工常用刀具的种类及选择1.数牲加工常用刀具的种类及特点
数控加工刀具必须适应数控机床高速、高效和自动化程度高的特点,一般应包括通用刀具、通用连接刀柄及少量专用刀柄。
刀柄要联接刀具并装在机床动力头上,因此已逐渐标准化和系列化。
2.1数控刀具的分类有多种方法
a.根据刀具结构可分为
(1)整体式;
(2)镶嵌式,采用焊接或机夹式联接,机夹式又可分为不转位和可转位两种;
(3)特殊型式,如复合式刀具、减震式刀具等。
b.根据制造刀具所用的材料可分为:
(1)高速钢刀具;
(2)硬质合金刀具;
(3)金刚石刀具;
(4)其他材料刀具,如立方氮化硼刀具、陶瓷刀具等。
c.从切削工艺上可分为:
(1)车削刀具,分外圆、内孔、螺纹、切割刀具等多种;
(2)钻削刀具,包括钻头、铰刀、丝锥等;
(3)镗削刀具;
(4)铣削刀具等。
为了适应数控机床对刀具耐用、稳定、易调、可换等的要求,近几年机夹式可转位刀具得到广泛的应用,在数量上达到整个数控刀具的30%一40%,金属切除量占总数的80%~90%。
2.2数控刀具与普通机床上所用的刀具相比,有许多不同的要求,主要有以下特点:
(1)刚性好(尤其是粗加工刀具)、精度高、抗振及热变形小;互换性好,便于快速换刀;
(2)寿命高,切削性能稳定、可靠;
(3)刀具的尺寸便于调整,以减少换刀调整时间;
(4)刀具应能可靠地断屑或卷屑,以利于切屑的排除;
(5)系列化标准化以利于编程和刀具管理。
2.数控加工刀具的选择
刀具的选择是在数控编程的人机交互状态下进行的。
应根据机床的加工能力、工件材科的性能、加
工工序切削用量以及其它相关因素正确选用刀具及刀柄。
刀具选择总的原则是:安装调整方便、刚性好、耐用度和精度高。
在满足加工要求的前提下,尽量选择较短的刀柄,以提高刀具加工的刚性。
(1)选取刀具时,要使刀具的尺寸与被加工工件的表面尺寸相适应。
生产中,平面零件周边轮廓的加工,常采用立铣刀;铣削平面时,应选硬质合金刀片铣刀,加工凸台、凹槽时,选高速钢立铣刀;加工毛坯表面或粗加工孔时,可选取镶硬质合金刀片的玉米铣刀;对一些立体型面和变斜角轮廓外形的加工,常采用球头铣刀、环形铣刀、锥形铣刀和盘形铣刀。
(2)在进行自由曲面(模具)加工时,由于球头刀具的端部切削速度为零,因此,为保证加工精度,切削行距一般采用顶端密距,故球头常用于曲面的精加工。
而平头刀具在表面加工质量和切削效率方面都优于球头刀,因此,只要在保证不过切的前提下,无论是曲面的粗加工还是精加工,都应优先选择平头刀。
另外,刀具的耐用度和精度与刀具价格关系极大,必须引起注意的是,在大多数情况下,选择好的刀具虽然增加了刀具成本,但由此带来的加工质量和加工效率的提高,则可以使整个加工成本大大降低。
(3)在加工中心上,各种刀具分别装在刀库上,按程序规定随时进行选刀和按刀动作。
因此必须采用标准刀柄,以便使钻、镗、扩、铣削等工序用的标准刀具迅速、准确地装到机床主轴或刀库上去。
编程人员应了解机床上所用刀柄的结构尺寸、调整方法以及调整范围,以便在编程时确定刀具的径向和轴向尺寸。
目前我国的加工中心采用TSG工具系统,其刀柄有直柄(3种规格)和锥柄(4种规格)2种,共包括16种不同用途的刀柄。
(4)在经济型数控机床的加工过程中,由于刀具的刃磨、测量和更换多为人工手动进行,占用辅助时间较长,因此,必须合理安排刀具的排列顺序。
一般应遵循以下原则:①尽量减少刀具数量;②一把刀具装夹后,应完成其所能进行的所有加工步骤;粗精加工的刀具应分开使用,即使是相同尺
寸规格的刀具;④先铣后钻;⑤先进行曲面精加工,后进行二维轮廓精加工;
⑥在可能的情况下,应尽可能利用数控机床的自动换刀功能,以提高生产效率等。
3.加工过程中切削用量的确定
合理选择切削用量的原则是:粗加工时,一般以提高生产率为主,但也应考虑经济性和加工成本;半精加工和精加工时,应在保证加工质量的前提下,兼顾切削效率、经济性和加工成本。
具体数值应根据机床说明书切削用量手册,并结合经验而定。
具体要考虑以下几个因素:
(1)切削深度ap。
在机床、工件和刀具刚度允许的情况下,ap就等于加工余量,这是提高生产率的一个有效措施。
为了保证零件的加工精度和表面粗糙度,一般应留一定的余量进行精加工。
数控机床的精加工余量可略小于普通机床。
切削宽度L。
一般L与刀具直径d成正比,与切削深度成反比。
经济型数控机床的加工过程中,一般L的取值范围为L=(~)d。
(2)切削速度V。
提高V也是提高生产率的一个措施,但v与刀具耐用度的关系比较密切。
随着v的增大,刀具耐用度急剧下降,故v的选择主要取决于刀具耐用度。
另外,切削速度与加工材料也有很大关系,例如用立铣刀铣削合金刚30CrNi2MoVA时,V可采用8m/min左右;而用同样的立铣刀铣削铝合金时,V可选200m/min以上。
主轴转速n(r/min)。
主轴转速一般根据切削速度v来选定。
计算公式为:V=pnd/1000。
数控机床的控制面板上一般备有主轴转速修调(倍率)开关,可在加工过程中对主轴转速进行整倍数调整。
(3)进给速度Vf。
Vf应根据零件的加工精度和表面粗糙度要求以及刀具和工件材料来选择。
Vf的增加也可以提高生产效率。
加工表面粗糙度要求低时,Vf可选择得大些。
在加工过程中,Vf也可通过机床控制面板上的修调开关进行人工调整,但是最大进给速度要受到设备刚度和进给系统性能等的限制。
结束语
随着数控机床在生产实际中的广泛应用,量化生产线的形成,数控编程已经成为数控加工中的关键问题之一。
在数控程序的编制过程中,要在人机交互状态下即时选择刀具和确定切削用量。
因此,编程人员必须熟悉刀具的选择方法和切削用量的确定原则,从而保证零件的加工质量和加工效率,充分发挥数控机床的优点,提高企业的经济效益和生产水平。