金属大型锻件热处理论文
金属材料与热处理论文关于金属材料的论文
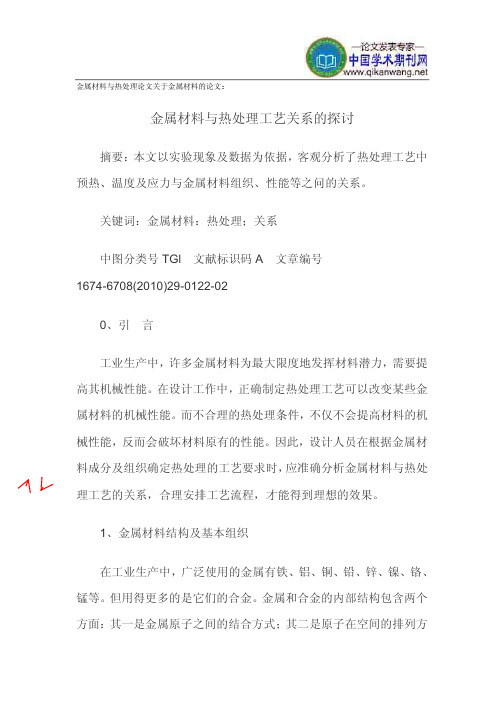
。的目的裂淬制抑终最和值力应小减 到达而从 �度速缩收的属金位部心中面截和差温面截小减量尽于在而
形变的来原替代来粒晶轴等的新生产域区的烈剧最形变在会 �后以度 温的高够足到热加属金形变冷当 。得获晶结再后理处热过通要主则化 细的织组属金而 。性韧强料材高提而从移滑错位碍阻而高增例比占所 界晶使粒晶化细过通是理原其 �法方要重种一的错位中体晶属金少减 是化强晶细。度强属金高提而从�降下度密错位的中料材属金使�错 位中体晶属金少减要是键关的性韧裂断属金高提。能性的展扩纹裂 抗抵下用作力外在料材的纹裂有含为解理以可际实性韧裂断 。纹裂的 寸尺同不、量数同不有含都际实料材何任�是点发出的学力裂断 系关的度温理处热与性韧裂断的料材属金 3.2
余残由是力应的裂开蚀腐力应起引分部大 。裂开蚀腐力应为称坏破裂 断性脆的生发下用作同共境环蚀腐定特和力应伸拉在料材属金 系关的力应理处热与裂开蚀腐力应抗料材属金 4.2
。性韧裂断的料材属金高提 以可�度温的理处热制控出得以可就们我�么那。行进能才程过晶结 再�时移迁行进能其使�子原活激以足�上之度温定一到热加属金形 变将须必此因�散扩的子原要需都大长与成形的核晶晶结再。段阶的 烈剧为最化变能性观宏的钢是�度温右左℃009�此因。大长始开粒 晶 �上以℃009 在 。级 2lBY 到达度粒晶 �粒晶轴等为部全乎几 �小细得 变然突粒晶�始开形变℃009 在。主为粒晶的长拉形变以然仍但�现 出量少有经已粒晶轴等中粒晶的形变℃008。化变状形的粒晶轴等 向渐逐始开粒晶的平扁�时℃007 在�为象现验实。貌形粒晶示显质 物学化用后光抛磨研�开剖割切线向轴沿样试的后缩压将再�理处火 退的)冷空(CAh6×℃086 行进再�温室至冷中气空在后然��05 形变 缩压 s03 温保率速形变的 1-01×5 以上机验试拟模热型 0051-elbeelC 在℃0011 和℃0001、℃009�℃008�℃007 在择选�后工 加机�柱圆小的当适割切线上料坯钢 YS 在�明证验实下以过通以可 。系关的显明有坏好果效晶结再的属金对度温同不 �此因 。晶结再态动 生发致导 �别级度密错位部局的高够足到累积会才中程过形变在料材 �下件条的度温形变和力应的定一在有只 。晶结再为称程过个这 �粒晶
锻件热处理技术
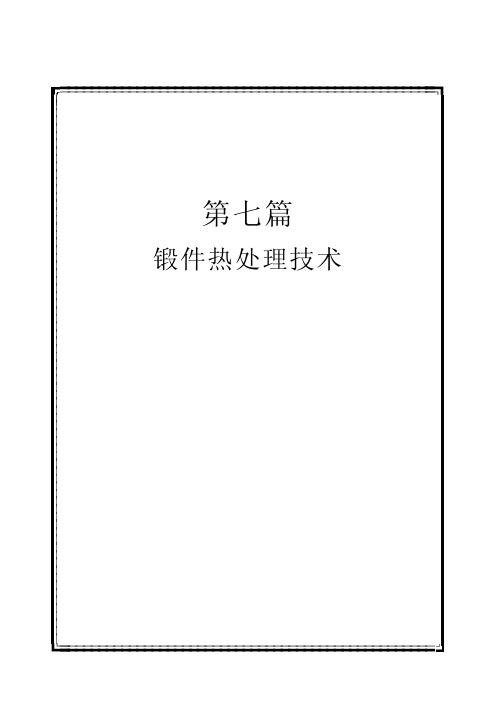
一、加热的目的和要求
(ÿ)加热的目的 提高金属的塑性,降低金属变形抗力,使之 易 于 成形,并 获 得良 好 的 锻后 组 织 和 力 学
差,以致造成过大的热应力,再叠加其它内应力,引起材料破裂。 ü准确实施给定的加热规 范,如 加 热 温 度、速 度、时 间 和 保 温 等 加 热 条 件,以 防 产 生
过热、过烧等缺陷。
二、加热方法
在锻压生产中,按采用热源不同,加热方法可分为燃料火焰加热和电加热两大类。 · ÿþüý ·
第七篇 锻件热处理技术
中小件
单件、成批
自由锻、 模锻
无炉门、多 采用 上排烟
中小件及 局部加热
成批
胎模锻、 模锻
炉 底 可 进 出 运 大、中型坯 动,便于装出料 料及钢锭
单件、中 小批量
自由锻、 钢锭开坯
利用燃料不完全 燃烧形成保护气 氛
中小件
成批
精密模锻
推杆式炉 连 续 式 加 热
转壁炉
转底炉
液、气
液、气 液、气
用推 料 机 推 料,
ÿÿÿÿÿÿÿÿÿÿÿÿÿÿÿÿÿÿÿÿÿÿÿÿÿÿÿÿÿÿÿÿÿÿÿÿÿÿÿÿÿÿÿÿÿÿÿÿÿþ
第七篇
锻件热处理技术
ÿÿÿÿÿÿÿÿÿÿÿÿÿÿÿÿÿÿÿÿÿÿÿÿÿÿÿÿÿÿÿÿÿÿÿÿÿÿÿÿÿÿÿÿÿÿÿÿÿþ
第一章 金属的锻造温度与加热规范
第一章 金属的锻造温度与加热规范
第一节 加热目的和加热方法
ÿþ 燃料火焰加热法 燃料火焰加热法(简称火焰加热法)是利用固体(煤、焦炭等)、液体(重油、柴油等)或 气体(煤气、天然气等)燃料燃烧所发生的热能加热坯料的方法,是在加热炉内进行。 火焰加热炉通用性强,投资少,建造比较容 易;燃 料 来 源广 泛,费 用比 较 低,所 以 广 为 采用。但是,火焰加热炉炉温和气氛较难控制,加温工劳动条件差。 火焰加热和常用加热炉的特点及应用范围见表 ý ü ÿ ü ÿ。
大型锻件锻后热处理的研究及注意事项

河北汇 工机械设备有 限公 司 ( 巨鹿 0 5 5 2 5 0 ) 杨钟胜
大 型 锻 件 的 白点 和氢 脆 缺 陷 的危 害性 很 大 ,所
以 大 型锻 件 锻 后 热 处 理 要 求 防 止 白点 和 氢 脆 ,同
瞬 间 形成 ,而 是 逐 渐 形成 的 。从 停 锻到 出现 白 点 , 需 要 经 历一 段时 间 ,这 段时 间称 之 为 白 点形 成 的孕 育 期 或潜 伏 期 。孕 育 期 的长 短取 决 于钢 的含 氢量 , 同时 也取 决 于锻 件 的厚 度 。
力 ,重结 晶细 化 晶粒 ,同时 去 氢 。
1 . 有关钢 中白点 的基本概念
( 1 )白点的危害性 白点是过 高 时 ,钢 显著 变
脆 ,从 本 质来 看 , 白点也 属 于脆 性 破 坏 。 白点 的存 在 使 钢 的 力学 性 能 特 别 是 横 向 塑 性 和 韧 性 急 剧 降 低 ,成 为最 危 险 的断 裂源 ,严 重影 响 零件 的 使 用性 能 和 寿 命 。 因此 ,锻 件 中一 旦 发现 白点 ,则 该 锻件 必须 报 废 。 ( 2 ) 白点 的 形 貌 在 锻 件 的 纵 向断 裂 面 上 呈
中含有足够数量的氢是形成白点的必要条件,内应
力 的存 在具 有 促进 白点形 成 的作 用 。 ( 5 )白 点 的 三大 特 点 ① 白点 从 来 不 在 锻 件 的 表面 形 成 。根 据 有 关资 料表 明 ,其形 成 总是 在 锻 件 内部 ,含有 白点 的 区域 离锻 件 表 面有 相 当一 段 距 离 ,约 5 0 mm。② 白点是 在 锻 后 ,当 锻件 冷 却 到 比
即进 行 锻后 去 氢 退火 。
金属材料热处理学期论文
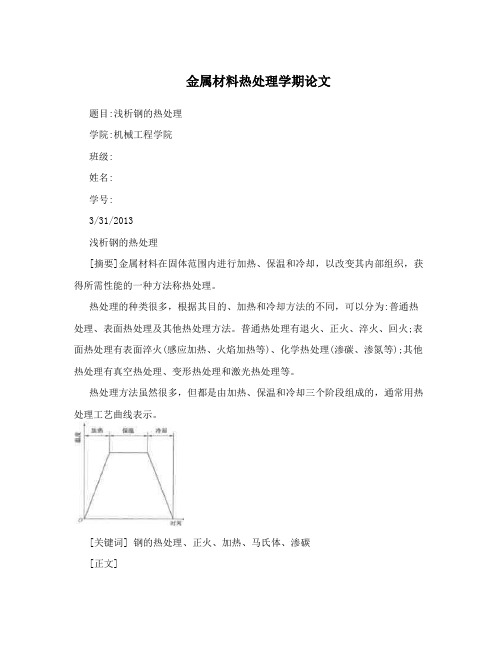
金属材料热处理学期论文题目:浅析钢的热处理学院:机械工程学院班级:姓名:学号:3/31/2013浅析钢的热处理[摘要]金属材料在固体范围内进行加热、保温和冷却,以改变其内部组织,获得所需性能的一种方法称热处理。
热处理的种类很多,根据其目的、加热和冷却方法的不同,可以分为:普通热处理、表面热处理及其他热处理方法。
普通热处理有退火、正火、淬火、回火;表面热处理有表面淬火(感应加热、火焰加热等)、化学热处理(渗碳、渗氮等);其他热处理有真空热处理、变形热处理和激光热处理等。
热处理方法虽然很多,但都是由加热、保温和冷却三个阶段组成的,通常用热处理工艺曲线表示。
[关键词] 钢的热处理、正火、加热、马氏体、渗碳[正文]一、钢的普通热处理根据加热及冷却的方法不同,获得金属材料的组织及性能也不同。
普通热处理可分为退火、正火、淬火和回火四种。
普通热处理是钢制零件制造过程中非常重要的工序。
退火1(退火工艺及其目的退火是将工件加热到适当温度,保温一定时间,然后缓慢冷却的热处理工艺,实际生产中常采取随炉冷却的方式。
退火的主要目的:?降低硬度,改善钢的成形和切削加工性能;?均匀钢的化学成分和组织;?消除内应力。
2(常用退火工艺方法根据处理的目的和要求的不同,钢的退火可分为完全退火、球化退火和去应力退火等。
下表为主要退火工艺方法及其应用。
名称工艺目的应用将钢加热至Ac以上330,50?,保温一定时间,主要用于亚共细化晶粒,消除过热完全退炉冷至室温析钢的铸、锻组织,降低硬度和改善火 (或炉冷至600?以下,件,有时也用于切削加工性能出炉空冷) 焊接结构使钢中的渗碳体球状将钢加热至Ac以上化,以降低钢的硬度,120,40?,保温一定时改善切削加工性,并为间,炉冷至室温,或快以后的热处理做好组织球化退主要用于共析速冷至略低于Ar温度,准备。
若钢的原始组织1火钢和过共析钢保温后出炉空冷,使钢中有严重的渗碳体网,中碳化物球状化的退火则在球化退火前应进行工艺正火消除,以保证球化退火效果使钢的化学成分和组均匀化退将钢加热到略低于固相织均匀化主要用于质量火(扩散线温度(Ac或Ac以上要求高的合金3cm退火) 150~300?),长时间保温铸锭、铸件或锻(10~15h),随炉冷却。
金属材料热处理工艺论文
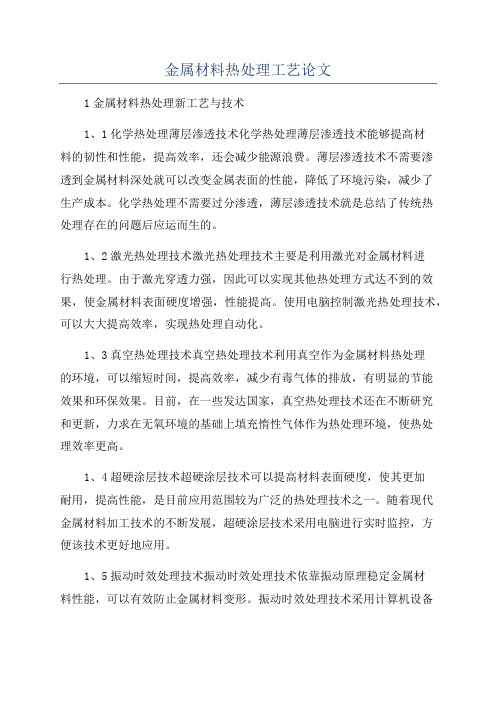
金属材料热处理工艺论文1金属材料热处理新工艺与技术1、1化学热处理薄层渗透技术化学热处理薄层渗透技术能够提高材料的韧性和性能,提高效率,还会减少能源浪费。
薄层渗透技术不需要渗透到金属材料深处就可以改变金属表面的性能,降低了环境污染,减少了生产成本。
化学热处理不需要过分渗透,薄层渗透技术就是总结了传统热处理存在的问题后应运而生的。
1、2激光热处理技术激光热处理技术主要是利用激光对金属材料进行热处理。
由于激光穿透力强,因此可以实现其他热处理方式达不到的效果,使金属材料表面硬度增强,性能提高。
使用电脑控制激光热处理技术,可以大大提高效率,实现热处理自动化。
1、3真空热处理技术真空热处理技术利用真空作为金属材料热处理的环境,可以缩短时间,提高效率,减少有毒气体的排放,有明显的节能效果和环保效果。
目前,在一些发达国家,真空热处理技术还在不断研究和更新,力求在无氧环境的基础上填充惰性气体作为热处理环境,使热处理效率更高。
1、4超硬涂层技术超硬涂层技术可以提高材料表面硬度,使其更加耐用,提高性能,是目前应用范围较为广泛的热处理技术之一。
随着现代金属材料加工技术的不断发展,超硬涂层技术采用电脑进行实时监控,方便该技术更好地应用。
1、5振动时效处理技术振动时效处理技术依靠振动原理稳定金属材料性能,可以有效防止金属材料变形。
振动时效处理技术采用计算机设备进行监控,既可以减少生产时间,提高效率,还能够降低成本,节能减耗,克服了传统热处理技术的不足。
2金属材料热处理工艺与技术展望随着金属材料热处理工艺与技术的不断发展,诞生了许多热处理技术。
其中,可控气氛热处理就是较为成熟的热处理技术之一。
可控气氛,顾名思义,就是一种可以控制和保护的气氛,是一种保护金属材料的气体介质。
可控气氛可以有效保护金属材料的表面性能,使热处理过程更为完善。
对于钢制工件而言,可控气氛热处理极为适合,可以给钢材料提供更为妥善的保护。
这是因为钢在热处理高温中很容易被氧化,表面破坏较为严重,但可控气氛热处理却能够避免钢被氧化。
钢的热处理原理与方法论文
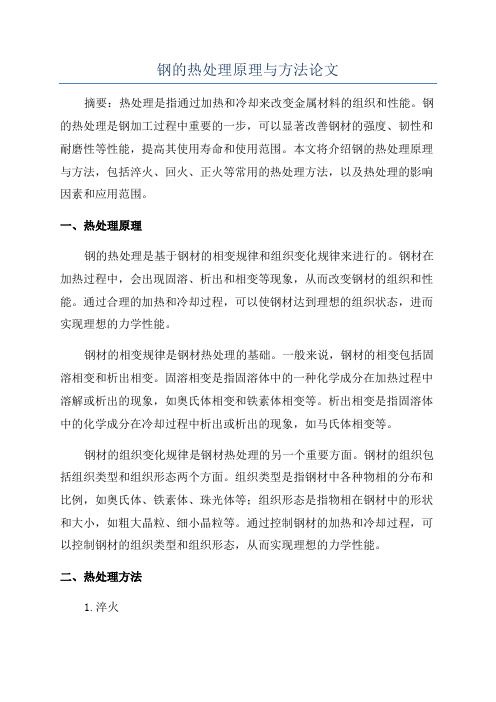
钢的热处理原理与方法论文摘要:热处理是指通过加热和冷却来改变金属材料的组织和性能。
钢的热处理是钢加工过程中重要的一步,可以显著改善钢材的强度、韧性和耐磨性等性能,提高其使用寿命和使用范围。
本文将介绍钢的热处理原理与方法,包括淬火、回火、正火等常用的热处理方法,以及热处理的影响因素和应用范围。
一、热处理原理钢的热处理是基于钢材的相变规律和组织变化规律来进行的。
钢材在加热过程中,会出现固溶、析出和相变等现象,从而改变钢材的组织和性能。
通过合理的加热和冷却过程,可以使钢材达到理想的组织状态,进而实现理想的力学性能。
钢材的相变规律是钢材热处理的基础。
一般来说,钢材的相变包括固溶相变和析出相变。
固溶相变是指固溶体中的一种化学成分在加热过程中溶解或析出的现象,如奥氏体相变和铁素体相变等。
析出相变是指固溶体中的化学成分在冷却过程中析出或析出的现象,如马氏体相变等。
钢材的组织变化规律是钢材热处理的另一个重要方面。
钢材的组织包括组织类型和组织形态两个方面。
组织类型是指钢材中各种物相的分布和比例,如奥氏体、铁素体、珠光体等;组织形态是指物相在钢材中的形状和大小,如粗大晶粒、细小晶粒等。
通过控制钢材的加热和冷却过程,可以控制钢材的组织类型和组织形态,从而实现理想的力学性能。
二、热处理方法1.淬火淬火是指将高温钢材迅速冷却到室温以下,使其产生马氏体相变。
马氏体具有高硬度和脆性的特点,可以显著提高钢材的硬度和强度,但降低了韧性。
因此,淬火一般需要进行回火处理来改善钢材的韧性。
2.回火回火是指将淬火后的钢材加热到较低温度并保温一段时间,然后冷却到室温。
回火可以消除淬火时产生的内应力和组织不均匀性,通过分解马氏体改善钢材的韧性,同时适当降低硬度和强度。
3.正火正火是指将低碳钢材加热到临界温度以上,保温一段时间,然后冷却至室温。
正火可以使铁素体相变为奥氏体,改善钢材的塑性和韧性,适用于需要保持一定塑性和耐久性的工件。
三、热处理的影响因素钢材的热处理效果和性能会受到多种因素的影响。
金属材料与热处理论文关于金属材料的论文
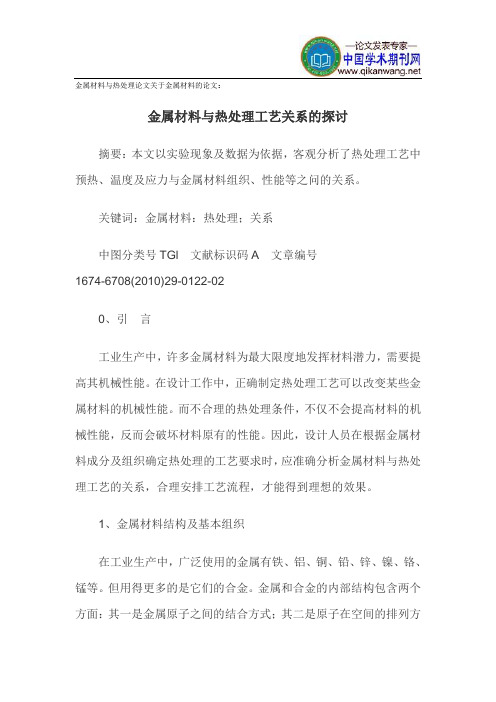
金属材料与热处理论文关于金属材料的论文:金属材料与热处理工艺关系的探讨摘要:本文以实验现象及数据为依据,客观分析了热处理工艺中预热、温度及应力与金属材料组织、性能等之问的关系。
关键词:金属材料:热处理;关系中图分类号TGl文献标识码A文章编号1674-6708(2010)29-0122-020、引言工业生产中,许多金属材料为最大限度地发挥材料潜力,需要提高其机械性能。
在设计工作中,正确制定热处理工艺可以改变某些金属材料的机械性能。
而不合理的热处理条件,不仅不会提高材料的机械性能,反而会破坏材料原有的性能。
因此,设计人员在根据金属材料成分及组织确定热处理的工艺要求时,应准确分析金属材料与热处理工艺的关系,合理安排工艺流程,才能得到理想的效果。
1、金属材料结构及基本组织在工业生产中,广泛使用的金属有铁、铝、铜、铅、锌、镍、铬、锰等。
但用得更多的是它们的合金。
金属和合金的内部结构包含两个方面:其一是金属原子之间的结合方式;其二是原子在空间的排列方式。
金属的性能和原子在空间的排列配置情况有密切的关系,原子排列方式不同,金属的性能就出现差异。
金属材料热处理过程是将金属工件放在一定的介质中加热到适宜的温度,并在此温度中保持一定时间后,又以不同速度在不同的介质中冷却,通过改变金属材料表面或内部的显微组织结构来改变其性能的一种工艺。
因此,对某些金属或合金来说,可以用热处理工艺来改变它的原子排列,进而改变其组织结构,控制其机械性能,以满足工程技术的需要。
不同的热处理条件会产生不同的材料性能改变效果,下面就金属的材料的某些性能来分析其与热处理工艺的关系,以便更好的提高材料的机械性能。
2、金属材料与热处理工艺的关系2.1金属材料的切削性能与热处理预热的关系金属材料加工的整个工艺流程中,如果切削加7-7-艺与热处理工艺之间能相互沟通,密切配合,对提高产品质量将有很大好处。
在金属切削过程中,由于被加工材料、切削刀具和切削条件的不同,金属的变形程度也不同,从而产生不同程度的光洁度。
大型锻件热处理过程的数值模拟研究
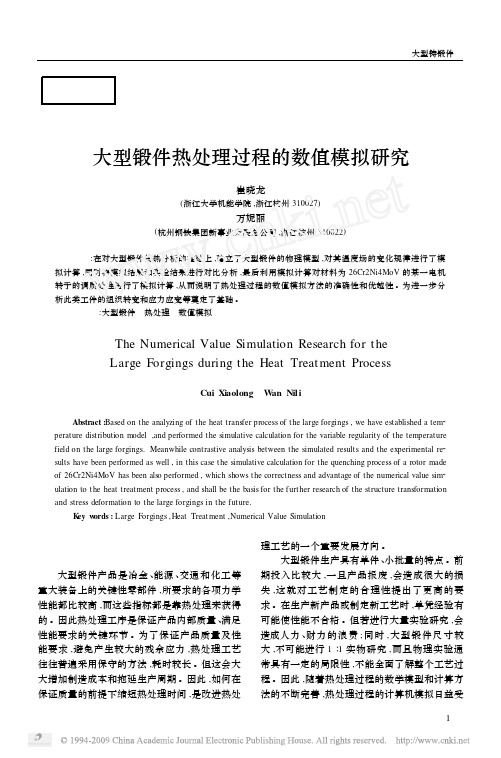
时间 (
8
10
12
14
16
18
20
无风
模拟值 实验值 绝对差值
724. 7 723. 3
1. 4
679. 1 682. 3
3. 2
646. 3 649. 8
3. 5
619. 5 617. 2
2. 3
595. 5 594. 0
1. 5
572. 7 574. 2
2
图 2 工件断面的几何形状
大型铸锻件
2. 2 建立差分方程
为了具体说明数值模拟在热处理过程中的
优越性 ,我们以图 2 所示的 L 形工件为例 ,用数
值模拟方法求解热处理时工件内温度场的变化
情况 ,然后和实验数据进行对比 。从而说明数值
模拟方法的准确性和优越性 。
用有限差分法求解 ,对内节点采用中心差
1. 5
550. 6 553. 4
2. 8
528. 7 525. 8
2. 9
507. 2 508. 8
1. 6
486. 1 487. 4
1. 3
A 向风
模拟值 实验值 绝对差值
648. 2 644. 8
3. 4
566. 1 567. 2
1. 1
512. 2 514. 5
2. 3
471. 7 473. 8
表 2 N 点温度变化过程( ℃)
6
8
10
12
765. 4 765. 8
0. 4
736. 0 733. 0
热微分方程[5 ] :
ρc
5T 5τ
=
λ(
52 T 5 x2
- 1、下载文档前请自行甄别文档内容的完整性,平台不提供额外的编辑、内容补充、找答案等附加服务。
- 2、"仅部分预览"的文档,不可在线预览部分如存在完整性等问题,可反馈申请退款(可完整预览的文档不适用该条件!)。
- 3、如文档侵犯您的权益,请联系客服反馈,我们会尽快为您处理(人工客服工作时间:9:00-18:30)。
小论大型锻件热处理
大型锻件是指用1000t或更大吨位水压机生产的锻件。
随着大型锻件的尺寸和重量的增加,热处理时有效厚度也随之发生变化。
由于截面的增大,不可避免地存在成分偏析、非金属夹杂、显微空隙等冶金缺陷,再加上相变潜热的影响,在加热和冷却过程中产生的应力较大,极易引工件的畸变和开裂,本文对大型锻件的热处理工艺参数进行了优化,并取得了显著经济效果。
一、大型锻件热处理可以解决的缺陷通常有以下几种
1.大晶粒
大晶粒通常是由于始锻温度过高和变形程度不足、或终锻温度过高、或变形程度落人临界变形区引起的。
铝合金变形程度过大,形成织构;高温合金变形温度过低,形成混合变形组织时也可能引起粗大晶粒,晶粒粗大将使锻件的塑性和韧性降低,疲劳性能明显下降。
2.晶粒不均匀
晶粒不均匀是指锻件某些部位的晶粒特别粗大,某些部位却较小。
产生晶粒不均匀的主要原因是坯料各处的变形不均匀使晶粒破碎程度不一,或局部区域的变形程度落人临界变形区,或高温合金局部加工硬化,或淬火加热时局部晶粒粗大。
耐热钢及高温合金对晶粒不均匀特别敏感。
晶粒不均匀将使锻件的持久性能、疲劳性能明显下降。
3.冷硬现象
变形时由于温度偏低或变形速度太快,以及锻后冷却过快,均可能使再结晶引起的软化跟不上变形引起的强化(硬化),从而使热锻后锻件内部仍部分保留冷变形组织。
这种组织的存在提高了锻件的强度和硬度,但降低了塑性和韧性。
严重的冷硬现象可能引起锻裂。
4.裂纹
裂纹通常是锻造时存在较大的拉应力、切应力或附加拉应力引起的。
裂纹发生的部位通常是在坯料应力最大、厚度最薄的部位。
如果坯料表面和内部有微裂纹、或坯料内存在组织缺陷,或热加工温度不当使材料塑性降低,或变形速度过快、变形程度过大,超过材料允许的塑性指针等,则在撤粗、拔长、冲孔、扩孔、弯曲和挤压等工序中都可能产生裂纹。
5.龟裂
龟裂是在锻件表面呈现较浅的龟状裂纹。
在锻件成形中受拉应力的表面(例如,未充满的凸出部分或受弯曲的部分)最容易产生这种缺陷。
引起龟裂的内因可能是多方面的:①原材料合cu、sn等易熔元素过多。
②高温长时间加热时,钢料表面有铜析出、表面晶粒粗大、脱碳、或经过多次加热的表面。
③燃料含硫量过高,有硫渗人钢料表面。
6.飞边裂纹
飞边裂纹是模锻及切边时在分模面处产生的裂纹。
飞边裂纹产生的原因可能是:①在模锻操作中由于重击使金属强烈流动产生穿筋现象。
②镁合金模锻件切边温度过低;铜合金模锻件切边温度过高。
7.铸造组织残留
铸造组织残留主要出现在用铸锭作坯料的锻件中。
铸态组织主要残留在锻件的困难变形区。
锻造比不够和锻造方法不当是铸造组织残留产生的主要原因,
铸造组织残留会使锻件的性能下降,尤其是冲击韧度和疲劳性能等。
8.碳化物偏析级别不符要求
碳化物偏析级别不符要求主要出现于莱氏体工模具钢中。
主要是锻件中的碳化物分布不均匀,呈大块状集中分布或呈网状分布。
造成这种缺陷的主要原因是原材料碳化物偏析级别差,加之改锻时锻比不够或锻造方法不当。
具有这种缺陷的锻件,热处理淬火时容易局部过热和淬裂。
制成的刃具和模具使用时易崩刃等。
13.带状组织
带状组织是铁素体和珠光体、铁素体和奥氏体、铁素体和贝氏体以及铁素体和马氏体在锻件中呈带状分布的一种组织,它们多出现在亚共折钢、奥氏体钢和半马氏体钢中。
这种组织,是在两相共存的情况下锻造变形时产生的带状组织能降低材料的横向塑性指针,特别是冲击韧性。
在锻造或零件工作时常易沿铁素体带或两相的交界处开裂。
14.局部充填不足
局部充填不足主要发生在筋肋、凸角、转角、圆角部位,尺寸不符合图样要求。
产生的原因可能是:①锻造温度低,金属流动性差;②设备吨位不够或锤击力不足;③制坯模设计不合理,坯料体积或截面尺寸不合格;④模膛中堆积氧化皮或焊合变形金属。
二、大型锻件热处理工艺
1.1 正火和淬火的加热
大型锻件特别是合金钢锻件,在加热方式上应采用阶梯升温方式加热。
有关资料表明l2 J大型锻件在350℃~500℃以及600℃~800℃时工件表面与心部存在最大温差,差值在300℃~400℃左右。
因此采用在450℃与650℃保温一段时间,然后再升温的加热方法是比较合适的。
大型锻件正火和淬火加热温度的选择,理论上与小型锻件是一致的,应取理论加热温度的上限,以保证偏析区也能达到相应的正火或淬火温度,使工件充分奥氏体化。
装炉温度≤400℃,并在450℃保持一定时间,以进一步减小锻件在蓝脆温度范围(250℃~350℃)内的温差。
在450℃保温之前由于锻件温度低,仍处于线弹性状态,如果表面与心部温差引起的热应力过大,可致锻件在加热过程中早期开裂。
因此,保温前加热速度一般控制在30℃/h-70℃/h;450℃保温后可适当加快升温速度但不能超过100℃/h~15012/h。
锻件经过650℃保温后,心部与表面还可能存在温差,但由于锻件处于塑性状态,尤其是当锻件加热到临界点温度以上时,相变超塑性伴随产生,因而导致开裂的可能性极小,此时可按设备功率升温。
均温时间凭经验目测决定,锻件表面温度均匀一致并和炉墙颜色相同时为止,工艺不做要求。
均温结束即开始保温,保温时间可根据公式(1)计算:
t=a·K·D (1)
式中t为加热时间(min);a为加热系数(rain/ram),碳素结构钢与低合金结构钢取0.40~0.50,中、高合金钢取0.50-0.60;K 是装炉系数;D是工件有效加热厚度。
1.2 回火加热
锻件在回火装炉的初始阶段,表面温度回升,心部温度进一步降低,以完成心部过冷奥氏体完全转变。
入炉温度应<400℃,并且在400℃左右保温一段时间。
为保证锻件表面与心部温差较小且无较大的应力,升温速度不应超过30℃/h~100℃/h。
回火工艺过程的温度较淬火的温度低(<650℃),所以均温时间难以用目测确定,因此回火工艺规程中没有规定均温时间,而是适当延长保温时间。
回
火保温时间也可按公式(1)计算,其中碳素钢、低合金钢a为1.0~1.5,高、中合金钢为1.2~1.7;工件有效厚度每100ram 回火保温时间不能少于4h。
1.3 正火和淬火冷却工艺
大型锻件正火冷却通常采用空冷、不同部位采用强力风冷或先进行短时间喷雾冷却后再采用强力风冷的冷却方式。
针对大型锻件的材料及要求,淬火冷却分别采用油冷、水冷、水一油双介质等冷却方法。
①油冷:3号锭子油,该介质的技术参数是运动粘度(50℃)为:17X 10 m2/s~23 X 10一m2/s,闪点为170℃,凝点为一15℃,淬火温度范围为一15℃~170℃。
为了缓解运动粘度大的缺点,可以安装冷却循环装置和加热装置。
冷却时间按公式(2)计算:
r=a·D (2)
式中r为冷却时间(S),D为工件有效厚度(mm),a为系数(s/mm),对45CrMo、3Cr13钢a一般为9~13。
②水冷:针对大型锻件水冷淬火后工件存在硬度不足的问题,采用15%的CaC12水溶液取代以前使用的自来水,并且安装冷却循环装置。
两种冷却介质的性能指标可知15%的CaC12水溶液与水相比,具有使用温度区间宽,最大冷速大,特性温度高,100"C~300~2的平均冷速小和适用范围广的优点。
冷却时间按公式(2)计算,其中a为1.5~2。
③水一油双介质冷却:对于40Cr、35CrMo、42CrMo等淬透性差和淬透性中等的低合金结构钢大型锻件,由于单纯的油冷淬火已不满足设计要求,而采用水冷工件开裂的倾向较大,在没有专用淬火液的条件下,采用水一油双介质淬火冷却工艺,冷却时间按公式(2)计算,其中水冷a为1~2,油冷a 为7~10。
在具体操作时应注意以下几点:水冷淬火之前要有较短时间的预冷,以减小热应力,使工件畸变和开裂倾向减小,而且还可以增加大型锻件的淬硬层,提高零件的综合力学性能;严格控制水油转换时的空冷时间,不宜超过20s。
1 .4 回火冷却工艺
一般在400℃以上的冷却速度应控制在50℃/h~高温回火(≥450℃)后必须采用水冷或油冷等冷却较5℃/h,对于40Cr、3Cr13等钢具有明显可逆回火脆性的材料,该种方法将使该材料的冲击韧性显著降低。
回火冷却时应考虑以下两点:①对无高温回火脆性材料,如45、35CrMo、42CrMo、45CrMo钢等,采用随炉冷却或空冷的缓慢冷却方式。
②对具有高温回火脆性的材料,如40Cr、3Cr13、Crl2钢等,在低温回火快的方式进行冷却,以避免出现回火脆性,为了进一步消除由于回火冷却带来的应力,然后补充进行一次400C左右的去除内应力退火。
热处理工艺对于去除大型锻件的缺陷有着越来越重要的作用,对提高锻件质量已经是不可缺少的工艺过程,进一步研究有效的热处理工艺变得至关重要。
参考文献:
1.机械工业职业技能鉴定指导中心.热处理工技术[M].北京:机械工业出版社
2.刘胜.浅谈连续式渗碳炉予处理炉的作用[j] 机械工人
3.孙宝兴.SrL连续式渗碳自动线的特点及应用[J].金属热处理
4.内滕武志.渗碳淬火实用技术[M].北京:机械工业出版社。