常见缺陷产生的原因_预防措施及补救措施
焊接中常见的缺陷及防治措施
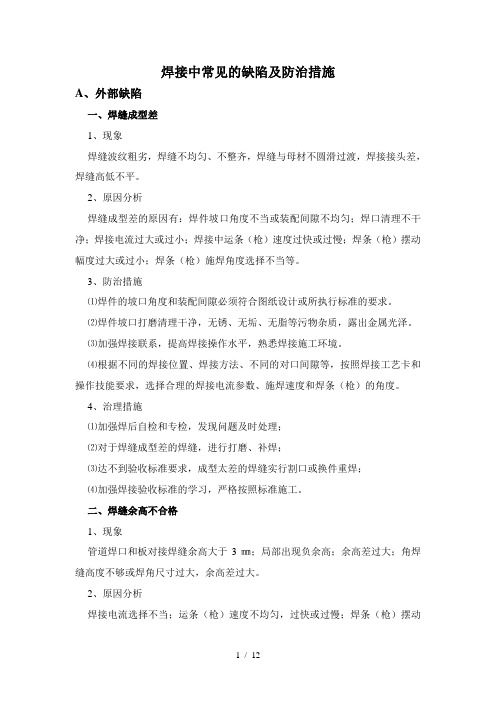
焊接中常见的缺陷及防治措施A、外部缺陷一、焊缝成型差1、现象焊缝波纹粗劣,焊缝不均匀、不整齐,焊缝与母材不圆滑过渡,焊接接头差,焊缝高低不平。
2、原因分析焊缝成型差的原因有:焊件坡口角度不当或装配间隙不均匀;焊口清理不干净;焊接电流过大或过小;焊接中运条(枪)速度过快或过慢;焊条(枪)摆动幅度过大或过小;焊条(枪)施焊角度选择不当等。
3、防治措施⑴焊件的坡口角度和装配间隙必须符合图纸设计或所执行标准的要求。
⑵焊件坡口打磨清理干净,无锈、无垢、无脂等污物杂质,露出金属光泽。
⑶加强焊接联系,提高焊接操作水平,熟悉焊接施工环境。
⑷根据不同的焊接位置、焊接方法、不同的对口间隙等,按照焊接工艺卡和操作技能要求,选择合理的焊接电流参数、施焊速度和焊条(枪)的角度。
4、治理措施⑴加强焊后自检和专检,发现问题及时处理;⑵对于焊缝成型差的焊缝,进行打磨、补焊;⑶达不到验收标准要求,成型太差的焊缝实行割口或换件重焊;⑷加强焊接验收标准的学习,严格按照标准施工。
二、焊缝余高不合格1、现象管道焊口和板对接焊缝余高大于3㎜;局部出现负余高;余高差过大;角焊缝高度不够或焊角尺寸过大,余高差过大。
2、原因分析焊接电流选择不当;运条(枪)速度不均匀,过快或过慢;焊条(枪)摆动幅度不均匀;焊条(枪)施焊角度选择不当等。
3、防治措施⑴根据不同焊接位置、焊接方法,选择合理的焊接电流参数;⑵增强焊工责任心,焊接速度适合所选的焊接电流,运条(枪)速度均匀,避免忽快忽慢;⑶焊条(枪)摆动幅度不一致,摆动速度合理、均匀;⑷注意保持正确的焊条(枪)角度。
4、治理措施⑴加强焊工操作技能培训,提高焊缝盖面水平;⑵对焊缝进行必要的打磨和补焊;⑶加强焊后检查,发现问题及时处理;⑷技术员的交底中,对焊角角度要求做详细说明。
三、焊缝宽窄差不合格1、现象焊缝边缘不匀直,焊缝宽窄差大于3㎜。
2、原因分析焊条(枪)摆动幅度不一致,部分地方幅度过大,部分地方摆动过小;焊条(枪)角度不合适;焊接位置困难,妨碍焊接人员视线。
常见缺陷分析
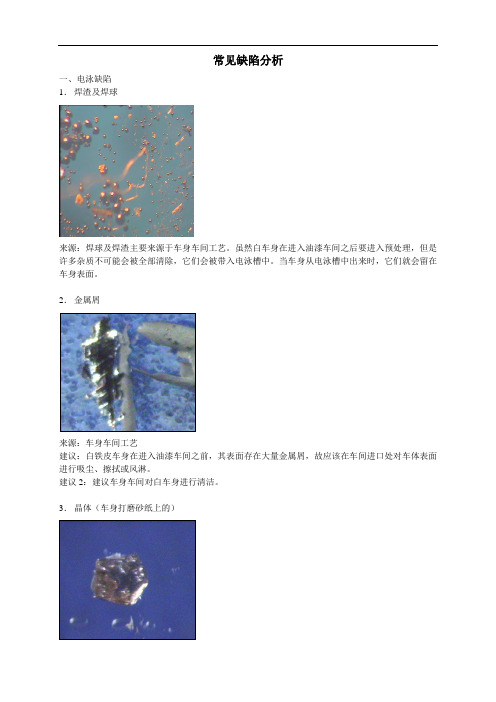
常见缺陷分析一、电泳缺陷1.焊渣及焊球来源:焊球及焊渣主要来源于车身车间工艺。
虽然白车身在进入油漆车间之后要进入预处理,但是许多杂质不可能会被全部清除,它们会被带入电泳槽中。
当车身从电泳槽中出来时,它们就会留在车身表面。
2.金属屑来源:车身车间工艺建议:白铁皮车身在进入油漆车间之前,其表面存在大量金属屑,故应该在车间进口处对车体表面进行吸尘、擦拭或风淋。
建议2:建议车身车间对白车身进行清洁。
3.晶体(车身打磨砂纸上的)来源:车身车间对车身打磨的过程中,所使用的砂纸会磨损并落在车身表面。
建议:车身车间应该在打磨后擦拭车身表面4.纤维来源:车身使用抹布、手套,烘房过滤介质5.车身胶来源:车身车间原因:车身车间操作人员在操作时不规范,并未将多余的车身胶清洁干净6.电泳结块来源:电泳工艺原因:电泳漆中有细小杂质6.烘房灰粒来源:烘房建议:定期对烘房进行清洁二、中涂缺陷1.电泳灰来源:电泳打磨;铰链原因:电泳灰会落入车体内,然后在喷涂过程中会被吹到车身表面。
建议:用电泳湿打磨代替干打磨。
2.纤维来源:手套,连体服,无尘擦布,空气等。
原因:大部分纤维非常轻,故它可以漂浮于空气中或车身上。
所以这些纤维会在喷涂过程中被吹到车身表面。
3.PVC原因:1)密封线操作人员操作不当产生2)中涂TACK OFF人员擦拭不当4.焊渣焊球来源:车身缺陷原因:电泳打磨漏打建议:加强电泳打磨检查力度5.金属屑来源:车身缺陷原因:电泳打磨漏打磨建议:加强电泳打磨检查力度6.胶体来源:胶带,贴片等原因:操作完成后,操作时掉未将胶带印擦拭干净落在车身表面7.防震垫来源:防震垫原因:在安装防震垫的时候,防震垫上的细小颗粒掉落到车体表面三、面漆缺陷1.纤维来源:粘性抹布,手套,连体服,连体服袖口,鸵毛机,空气等,过滤顶棉。
原因:手套,连体服有破损;在使用粘性抹布擦车时,粘性抹布被车的棱边处钩破,并未察觉。
措施:1)加强连体服及手套的检查力度,发现有破损就即使更换,或采取短期措施,用胶带将破损处临时封好。
手工电弧焊常见焊接缺陷产生的原因及预防措施
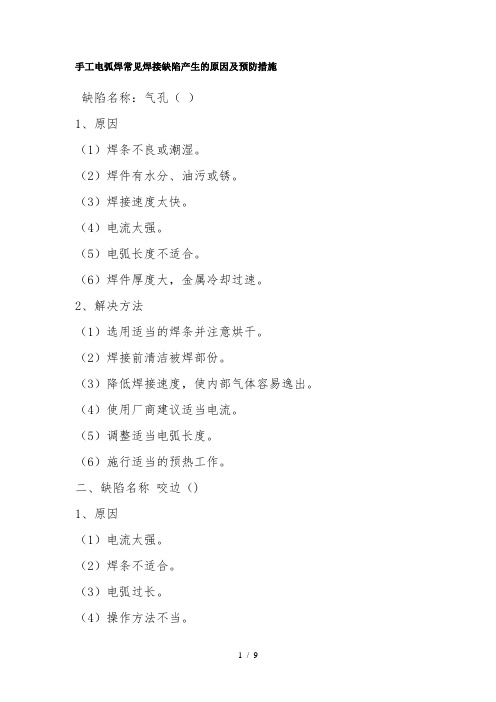
手工电弧焊常见焊接缺陷产生的原因及预防措施缺陷名称:气孔()1、原因(1)焊条不良或潮湿。
(2)焊件有水分、油污或锈。
(3)焊接速度太快。
(4)电流太强。
(5)电弧长度不适合。
(6)焊件厚度大,金属冷却过速。
2、解决方法(1)选用适当的焊条并注意烘干。
(2)焊接前清洁被焊部份。
(3)降低焊接速度,使内部气体容易逸出。
(4)使用厂商建议适当电流。
(5)调整适当电弧长度。
(6)施行适当的预热工作。
二、缺陷名称咬边()1、原因(1)电流太强。
(2)焊条不适合。
(3)电弧过长。
(4)操作方法不当。
(5)母材不洁。
(6)母材过热。
2、解决方法(1)使用较低电流。
(2)选用适当种类及大小之焊条。
(3)保持适当的弧长。
(4)采用正确的角度,较慢的速度,较短的电弧及较窄的运行法。
(5)清除母材油渍或锈。
(6)使用直径较小之焊条。
三:缺陷名称:夹渣( )1、原因(1)前层焊渣未完全清除。
(2)焊接电流太低。
(3)焊接速度太慢。
(4)焊条摆动过宽。
(5)焊缝组合及设计不良。
2、解决方法(1)彻底清除前层焊渣。
(2)采用较高电流。
(3)提高焊接速度。
(4)减少焊条摆动宽度。
(5)改正适当坡口角度及间隙。
四、缺陷名称:未焊透( )1、原因(1)焊条选用不当。
(2)电流太低。
(3)焊接速度太快温度上升不够,又进行速度太慢电弧冲力被焊渣所阻挡,不能给予母材。
(4)焊缝设计及组合不正确。
2、解决方法(1)选用较具渗透力的焊条。
(2)使用适当电流。
(3)改用适当焊接速度。
(4)增加开槽度数,增加间隙,并减少根深。
五:缺陷名称:裂纹()1、原因(1)焊件含有过高的碳、锰等合金元素。
(2)焊条品质不良或潮湿。
(3)焊缝拘束应力过大。
(4)母条材质含硫过高不适于焊接。
(5)施工准备不足。
(6)母材厚度较大,冷却过速。
(7)电流太强。
(8)首道焊道不足抵抗收缩应力。
2、解决方法(1)使用低氢系焊条。
(2)使用适宜焊条,并注意干燥。
(3)改良结构设计,注意焊接顺序,焊接后进行热处理。
常见铸造缺陷的产生原因及其预防措施
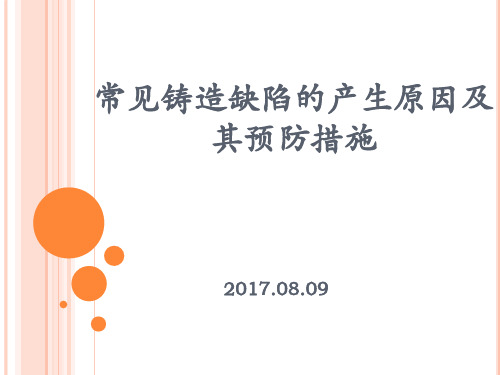
多肉产生的原因:
1、模具原因。 2、砂(芯)型起破。 3、砂(芯)型损坏 4、砂芯和砂型相接 表面不吻合
5、冷铁和模具不吻 合。
6、砂(芯)局部部 位未充满。
冷铁和模具不吻 合引起的铸件多
肉
多肉类缺陷的预防措施
(1) 提高铸型紧实度(下箱型砂的紧实度应高于 上箱的紧实度),避免局部过松;
(2)调整混砂工艺、控制水分,提高型砂强度; (3) 降低浇包的位置、降低浇注速度; (4) 铸型的分型面多压坭条或石棉绳; (5) 坭芯间的可见披缝尽量补死; (6) 需放置直接外冷铁时,外冷铁与铸件的接
根据GB/T 5611-1988《铸造术语》规定,将铸造缺陷 分为八大类。
① 多肉类缺陷 ② 孔洞类缺陷 ③ 裂纹、冷隔类缺陷 ④ 表面缺陷 ⑤ 残缺类缺陷 ⑥ 形状及重量差错类缺陷 ⑦ 夹杂类缺陷 ⑧ 性能、成分、组织不合格
分类(1)
大 类
序 号
缺陷名称
特征
1
飞翅(飞边、 产生在铸件分型面、坭芯间隙处、坭芯与
裂处金属表皮不氧化。
在铸件表面有未完全融合的缝隙或 洼坑,其交接边缘是光滑的。
热裂和冷裂(1) 热裂
图6-1 铸钢件的外热裂
冷裂
热裂和冷裂(2)
冷隔(1)
局 部 放 大
叶片机座 冷隔缺陷
冷隔(2)
典型的冷隔特 征
裂纹冷隔类缺陷的预防措施
(1) 严格按照化学成分的要求,控制钢水中的 S、 P含量;
触面一定要打磨平整; (7) 合箱后,注意保证上、下箱连接位置的紧固,
需放置压铁时上、下箱之间要用冷铁尖死。
分类(2-1)
大 类
序 号
缺陷名称
特征
孔 洞
焊接常见缺陷产生的原因及其预防措施
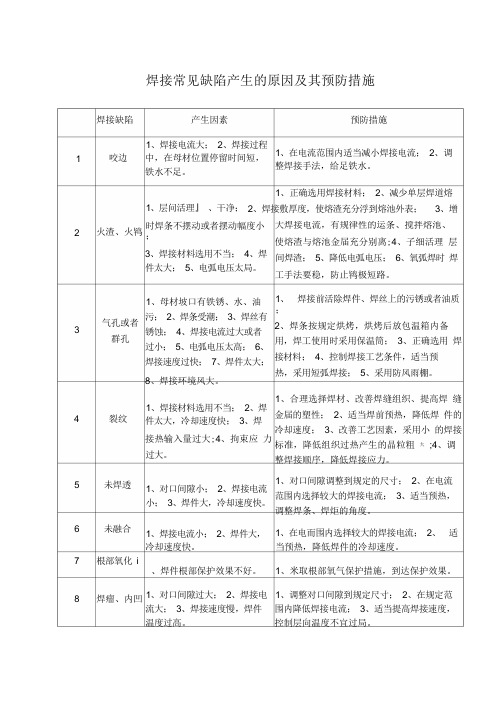
焊接常见缺陷产生的原因及其预防措施1 2 3 45 6 7 8 焊接缺陷咬边火渣、火鸨气孔或者群孔裂纹未焊透未融合根部氧化i焊瘤、内凹产生因素1、焊接电流大;2、焊接过程中,在母材位置停留时间短,铁水不足。
预防措施1、在电流范围内适当减小焊接电流;2、调整焊接手法,给足铁水。
1、正确选用焊接材料;2、减少单层焊道熔1、层问活理』、干净;2、焊接敷厚度,使熔渣充分浮到熔池外表;3、增时焊条不摆动或者摆动幅度小;3、焊接材料选用不当;4、焊件太大;5、电弧电压太局。
1、母材坡口有铁锈、水、油污;2、焊条受潮;3、焊丝有锈蚀;4、焊接电流过大或者过小;5、电弧电压太高;6、焊接速度过快;7、焊件太大;8、焊接环境风大。
1、焊接材料选用不当;2、焊件太大,冷却速度快;3、焊接热输入量过大;4、拘束应力过大。
1、对口间隙小;2、焊接电流小;3、焊件大,冷却速度快。
1、焊接电流小;2、焊件大,冷却速度快。
、焊件根部保护效果不好。
1、对口间隙过大;2、焊接电流大;3、焊接速度慢,焊件温度过高。
大焊接电流,有规律性的运条、搅拌熔池、使熔渣与熔池金届充分别离;4、子细活理层间焊渣;5、降低电弧电压;6、氧弧焊时焊工手法要稳,防止鸨极短路。
1、焊接前活除焊件、焊丝上的污锈或者油质;2、焊条按规定烘烤,烘烤后放包温箱内备用,焊工使用时采用保温筒;3、正确选用焊接材料;4、控制焊接工艺条件,适当预热,采用短弧焊接;5、采用防风雨棚。
1、合理选择焊材、改善焊缝组织、提高焊缝金届的塑性;2、适当焊前预热,降低焊件的冷却速度;3、改善工艺因素,采用小的焊接标准,降低组织过热产生的晶粒粗大;4、调整焊接顺序,降低焊接应力。
1、对口间隙调整到规定的尺寸;2、在电流范围内选择较大的焊接电流;3、适当预热,调整焊条、焊炬的角度。
1、在电而围内选择较大的焊接电流;2、适当预热,降低焊件的冷却速度。
1、米取根部氧气保护措施,到达保护效果。
焊接质量缺陷原因分析及预防、治理措施
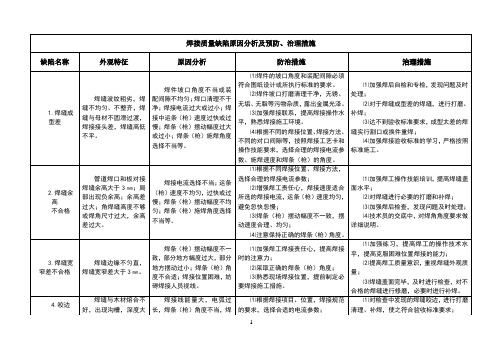
⑷根据自己的操作技能,选择合适的线能量、焊接速度和操作手法。
厚度符合标准要求;
⑵加强打底练习,熟练掌握操作手法以及对应的焊接线能量及焊接速度等。
18.管道焊口根部焊瘤、凸出、凹陷
⑷注意周围焊接施工环境,搭设防风设施,管子焊接无穿堂风;
⑸氩弧焊时,氩气纯度不低于%,氩气流量合适;
⑹尽量采用短弧焊接,减少气体进入熔池的机会;
⑺焊工操作手法合理,焊条、焊枪角度合适;
⑻焊接线能量合适,焊接速度不能过快;
⑼按照工艺要求进行焊件预热。
⑴严格按照预防措施执行;
⑵加强焊工练习,提高操作水平和责任心;
⑴严格按照规程和作业指导书的要求准备各种焊接条件;
⑵提高焊接操作技能,熟练掌握使用的焊接方法;
⑶采取合理的焊接顺序等措施,减少焊接应力等。
⑴针对每种产生裂纹的具体原因采取相应的对策;
⑵对已经产生裂纹的焊接接头,采取挖补措施处理。
11.焊缝表面不清理或清理不干净,电弧擦伤焊件
焊缝焊接完毕,焊接接头表面药皮、飞溅物不清理或清理不干净,留有药皮或飞溅物;焊接施工过程中不注意,电弧擦伤管壁等焊件造成弧疤。
⑶发现问题及时采取必要措施。
14.气孔
在焊缝中出现的单个、条状或群体气孔,是焊缝内部最常见的缺陷。
根本原因是焊接过程中,焊接本身产生的气体或外部气体进入熔池,在熔池凝固前没有来得及溢出熔池而残留在焊缝中。
⑴焊条要求进行烘培,装在保温筒内,随用随取;
⑵焊丝清理干净,无油污等杂质;
⑶焊件周围10~15㎜范围内清理干净,直至发出金属光泽;
⑴焊件的坡口角度和装配间隙必须符合图纸设计或所执行标准的要求。
浅谈水工混凝土常见质量缺陷及预防处理措施

1概述水利工程施工中,由于机械、材料、施工人员素质、施工方法、气象环境等各种原因,难免出现一些施工瑕疵、质量缺陷,常见质量缺陷有麻面、蜂窝、露筋、孔洞、错台、缺棱掉角、缝隙等。
本文结合长期积累的施工经验及施工规范、设计要求,探讨了不同质量缺陷产生的原因、预防措施以及处理方法。
2水工混凝土质量缺陷的预防处理措施2.1表面气泡2.1.1形成原因模板面积较大,仓内混凝土气泡不易排除;浇筑分层过厚,振捣时气体未排出仓外。
混凝土振捣不密实,没有排出混凝土中的气泡,气泡在模板表面停留。
2.1.2预防措施选用模板时尽量使用表面平整、光滑的模板。
使用已经用过的模板时要把模板表面的混凝土残渣及各种杂物清理干净。
将脱模剂均匀地涂刷在模板表面,不能涂刷过厚,也不能用动植物油、柴油等代替脱模剂。
浇筑混凝土过程中要正确地选择骨料,粗骨料最好是三级配料,严格执行实验配合比。
要分层浇筑混凝土,每层铺料厚度不能超过50cm,靠近模板处要谨慎振捣,保证振捣密实直到气泡翻到混凝土上方为止。
2.1.3处理措施根据气泡直径大小进行处理,直径小于2mm的气泡不需要处理;直径大于2mm的气泡,先用高压水枪将气泡内的污垢冲洗干净,烘干后再将预缩砂浆均匀地刮抹在有气泡混凝土的表面。
如果气泡十分密集,将气泡密集区打磨平整,用黑水泥和白水泥按1∶1的比例配制水泥浆进行刮抹,边刮抹边压实。
如果刮抹后的混凝土颜色和原混凝土颜色差别很大,要调整两种水泥的比例。
2.2麻面2.2.1形成原因模板表面本身就非常粗糙,没有进行处理;有一些杂物或者混凝土残渣没有清理干净粘在模板表面上;拆模时间过早混凝土表面被粘坏;浇筑混凝土前木模板没有浇水,木模板的表面吸走了混凝土中的水份,导致混凝土因失水产生麻面。
2.2.2预防措施不能选用表面扭曲、粗糙的模板,使用前要把模板表面的水泥砂浆清除干净。
木模板在浇筑混凝土前应充分浇水保持湿润,拆模时间应根据当地气温、混凝土强度而定。
手工电弧焊常见焊接缺陷产生的原因及预防措施
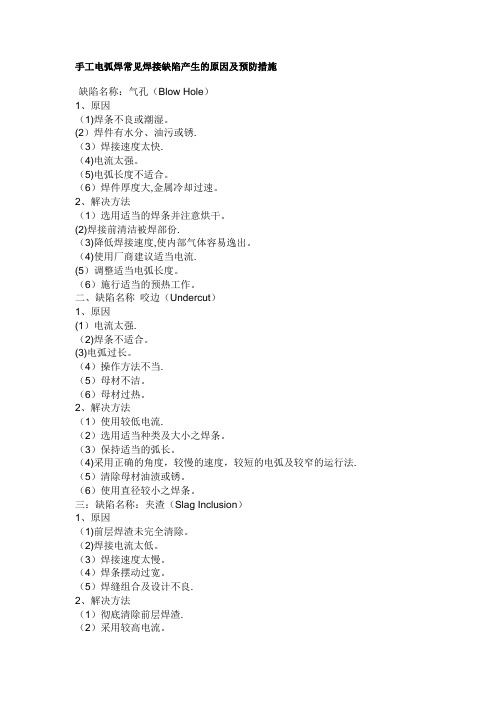
手工电弧焊常见焊接缺陷产生的原因及预防措施缺陷名称:气孔(Blow Hole)1、原因(1)焊条不良或潮湿。
(2)焊件有水分、油污或锈.(3)焊接速度太快.(4)电流太强。
(5)电弧长度不适合。
(6)焊件厚度大,金属冷却过速。
2、解决方法(1)选用适当的焊条并注意烘干。
(2)焊接前清洁被焊部份.(3)降低焊接速度,使内部气体容易逸出。
(4)使用厂商建议适当电流.(5)调整适当电弧长度。
(6)施行适当的预热工作。
二、缺陷名称咬边(Undercut)1、原因(1)电流太强.(2)焊条不适合。
(3)电弧过长。
(4)操作方法不当.(5)母材不洁。
(6)母材过热。
2、解决方法(1)使用较低电流.(2)选用适当种类及大小之焊条。
(3)保持适当的弧长。
(4)采用正确的角度,较慢的速度,较短的电弧及较窄的运行法. (5)清除母材油渍或锈。
(6)使用直径较小之焊条。
三:缺陷名称:夹渣(Slag Inclusion)1、原因(1)前层焊渣未完全清除。
(2)焊接电流太低。
(3)焊接速度太慢。
(4)焊条摆动过宽。
(5)焊缝组合及设计不良.2、解决方法(1)彻底清除前层焊渣.(2)采用较高电流。
(3)提高焊接速度.(4)减少焊条摆动宽度。
(5)改正适当坡口角度及间隙。
四、缺陷名称:未焊透(Incomplete Penetration)1、原因(1)焊条选用不当。
(2)电流太低.(3)焊接速度太快温度上升不够,又进行速度太慢电弧冲力被焊渣所阻挡,不能给予母材.(4)焊缝设计及组合不正确。
2、解决方法(1)选用较具渗透力的焊条。
(2)使用适当电流。
(3)改用适当焊接速度。
(4)增加开槽度数,增加间隙,并减少根深.五:缺陷名称:裂纹(Crack)1、原因(1)焊件含有过高的碳、锰等合金元素。
(2)焊条品质不良或潮湿。
(3)焊缝拘束应力过大。
(4)母条材质含硫过高不适于焊接.(5)施工准备不足。
(6)母材厚度较大,冷却过速。
(7)电流太强。
- 1、下载文档前请自行甄别文档内容的完整性,平台不提供额外的编辑、内容补充、找答案等附加服务。
- 2、"仅部分预览"的文档,不可在线预览部分如存在完整性等问题,可反馈申请退款(可完整预览的文档不适用该条件!)。
- 3、如文档侵犯您的权益,请联系客服反馈,我们会尽快为您处理(人工客服工作时间:9:00-18:30)。
主题:常见缺陷产生的原因,预防措施及补救措施
适用对象:
嘉丰公司全体人员
课时
版次
教官:柯于伟
日期
一.起泡:
原因: .电镀工艺配方有缺陷
.电镀溶液有污梁
.电镀前除油不彻底(前处理不干净)
.工序不完整.
预防: .选择证明良好的配方
.严格管理维护镀液
.加强控制前处理
.完善工序.
其中基材原因:选用不合适的材料,氢气量增加,氢脆造成.
预防.生产过程加强控制.
.保护好产品
十.局部无络层:
原因:镀铬工艺溶液分散能力较差.
预防:改善结构形状,采取辅助电极措施.
十一.点焊缝夹溶液:
原因:结构设计不当造成
预防.改善结构计设计
.在点焊时.
第页,共页
主题:常见缺陷产生的原因,预防措施及补救措施
适用对象:嘉丰公司全体人员
十五.包装气泡印:
原因:包材不适当.
预防.选择不含腐蚀性成份的材料.
.选择透水率低的材料.
.控制贮存环境.
十六.镀锌钢板切边腐蚀:
原因:材料特点的决定(无法避免)
预防.涂漆保护
.磷化
.改善所处的环境.
十七.孔内无涂层:
原因:深孔内涂料很难进入,导致无保护产生腐蚀.
预防:进行手工补漆
十八.涂层附着力不良
2.钝化膜质量不良.
3.表面处理后因素: ).环境恶劣. ).污染(汗液,胶水,气体腐蚀).
4.搬运过程中划碰伤.
预防:
1.选用合格的基体材料
2.机械加工过程中有保护措施.
3.处理后避免污染,选择良好的环境.
4.加强电镀工艺,使钝化良好.
第页,共页
主题:常见缺陷产生的原因,预防措施及补救措施
适用对象:嘉丰公司全体人员
十二.死边夹缝腐蚀:
原因:结构设计不当造成:
预防.改善结构设计
.加工时给予留适当缝隙让溶液自由进出.
.表面处理加强清洗.
十三.针孔:
原因:一般属手电镀工艺问题
预防:加强工艺溶液管理,加强基材使用控制.
十四.凹坑:
原因:表面处理前的基材表面缺陷.
预防.选择合格材料
2.定合适的工艺方法,加强工序间操作运输控制.避免损伤.
.可以在没有出现白色粉状物之前进行涂漆覆盖.
六.凹坑:无法补救(前处理之前补救)
七.挂耳印:该处没有保护层,基体被腐蚀.
1.手工涂漆
2.镀彩锌采用金色漆修补
3.银色漆作修补(其它金属)
八.裂纹,缝隙:无法补救.
表面处理前进行补救,封严或扩大开口.
九.晶粒粗大,无法补救.
由于材料轧制时的工艺参数控制不良而产生的此种现象,导致性能发生变化.
十.局部无铬层:无需补救(仅有碍于外观还在,对腐蚀性甚微)
十一.水印:一般无需补救.
清洁水对防护性无影响,不干净水有可能对膜层造成损害.
十二.孔内无涂层:手工补涂尽量减少腐蚀性,防腐蚀扩散.
十三.涂层附着不良:易脱落,有空气进入发腐蚀.
1.局部不附着,当面程小时可以作局部重新涂覆.
2.当面积大时,必须重涂覆.
2.因磨擦磨损导致.
预防:
1.控制焊缝质量及夹缝大小。
2.控制压铆缝隙(控制镀后压铆)
3.各包装,运输必须采取保护措施.
八.手印:
原因:操作不当,手直接触摸或手套用时间过长,脏,未更换.
预防:加强防护意思,配戴防护用品,脏即时更换.
九.水印:
原因.表面处理后水未吹干净.
.表面外来水未及时处理干净而留下的痕迹.
五.基材晶粒粗大:
原因:金属材料(铝板)在轧制过程中出现问题
预防:加强材料来料质量控制.
六.裂纹:
原因:多是因为材料本身的性能较差所决定或者折弯前材料表面有微小裂纹.
预防.严格按照设计要求,采用性能延伸良好材料.
.避免微小深划痕迹(拉丝)
.尽量避免拉丝、拉丝纹路与拆弯直线方向一致.
七.露白:
1.溶液截留而滞后腐蚀导致,如缝隙,微孔,裂纹,压铆缝隙,盲孔.
原因.喷涂或前处理不干净,操作有问题.
.涂料本身不良.
预防.选用合格之涂料
.加强过程控制(包括返工过程)
十九.基体腐蚀:
第页,共页
主题:常见缺陷产生的原因,预防措施及补救措施
适用对象:嘉丰公司全体人员
原因.膜厚不够
.附着力不良
.表面膜层耐蚀性不合格.
.涂料不合适.
预防.使用合格涂料
.加强过程中控制
失效机理及补求措施:
一.起泡,针孔:无法补救,必须重镀
二.黑点:钝化膜出现黑点,斑点,表面已开始发生腐蚀变化(重镀).
三.手印.汗液含盐份对金属产生腐蚀作用.
.立即用干净布或无水乙醇擦除()
四.基材花斑.基材粗糙而易镀层中产生微小缺陷.
.镀后无法补救,镀前可用机械方法消除(拉丝,打磨).
五.露白.锌钝化膜已不存在,锌层表面没有了保护,直接与大气接触而导腐蚀.
第页,共页
二.基材花斑:
原因:电镀前基材料产生严重锈蚀而出现,电镀后形成花斑.
预防:对基材采取良好有效的工序间进行防腐蚀性措施.
三.挂印:
原因:表面处理生产的必然的印迹现象.
预防:补救是必然进行的,在挂印位置在工件内表面和面必曾时增加工艺孔.
四.黑点:
原因:有多种,各环节都有可能导致.
1.基材中有不允许的杂质,有裂纹或小针孔.