300mm单晶硅提拉法生长数值模拟案例报告
直拉法硅晶体生长中单晶炉坩埚内熔体的数值模拟
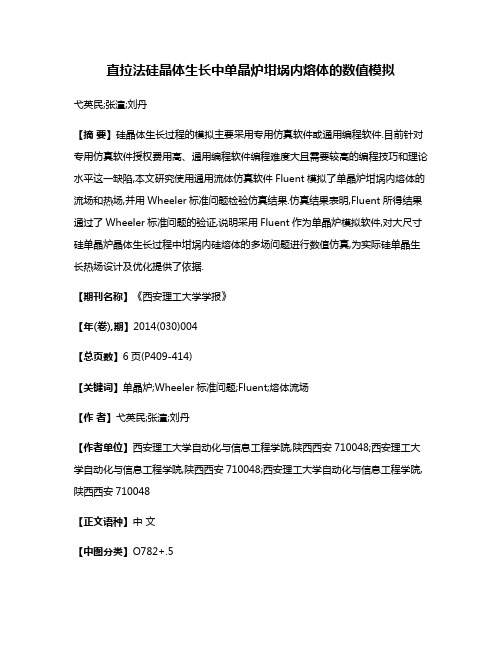
直拉法硅晶体生长中单晶炉坩埚内熔体的数值模拟弋英民;张潼;刘丹【摘要】硅晶体生长过程的模拟主要采用专用仿真软件或通用编程软件.目前针对专用仿真软件授权费用高、通用编程软件编程难度大且需要较高的编程技巧和理论水平这一缺陷,本文研究使用通用流体仿真软件Fluent模拟了单晶炉坩埚内熔体的流场和热场,并用Wheeler标准问题检验仿真结果.仿真结果表明,Fluent所得结果通过了Wheeler标准问题的验证,说明采用Fluent作为单晶炉模拟软件,对大尺寸硅单晶炉晶体生长过程中坩埚内硅熔体的多场问题进行数值仿真,为实际硅单晶生长热场设计及优化提供了依据.【期刊名称】《西安理工大学学报》【年(卷),期】2014(030)004【总页数】6页(P409-414)【关键词】单晶炉;Wheeler标准问题;Fluent;熔体流场【作者】弋英民;张潼;刘丹【作者单位】西安理工大学自动化与信息工程学院,陕西西安710048;西安理工大学自动化与信息工程学院,陕西西安710048;西安理工大学自动化与信息工程学院,陕西西安710048【正文语种】中文【中图分类】O782+.5大尺寸、高品质硅单晶是制造微细纳米级集成电路芯片的关键材料,目前我国全部依赖进口。
硅单晶炉作为生长电子级硅单晶材料的主要设备,其工艺复杂,技术集成度高,实现困难,在集成电路生产流程中处于首要地位。
因此,针对制备单晶硅的各种基础研究和仿真模拟成为了学者们研究的热点。
单晶硅按生长方法分有直拉法和区熔法等[1],直拉法也称CZ法,目前广泛应用于晶体制造领域。
在CZ法制备单晶硅的过程中,影响晶体质量的因素有坩埚内的硅熔体流动[2]、熔体内杂质分布[3]以及晶体生长面弯月面的形状[4]等。
使用计算机模拟晶体的生长环境在晶体制备的仿真中起到了重要的作用,为了衡量仿真算法的正确性,文献[5]提出了Wheeler标准问题,Wheeler标准问题是验证仿真算法正确与否的检验标准。
大尺寸单晶硅生长过程的数值模拟

Simulation,LES)在复杂湍流模拟中得到了许多研究者的青睐,各种亚格子涡粘模型也 逐渐被应用于晶体生长模拟的局部模型中 。
基金项目:国家自然科学基金项目(50876084),陕西省自然科学基础研究计划项目(SJ08E201),教育部 新世纪优秀人才支持计划(NCET-08-0443) 。
*
( 029-82663443,ljliu@) 摘要:利用块结构化网格对一典型工业用单晶硅结晶炉系统进行离散,对单晶炉内部硅熔体对流、所 有部件的传导换热和炉腔内的辐射换热进行整体耦合求解。针对大尺寸坩埚内的硅熔体湍流模拟,引 入了基于大涡数值模拟的 Smagorinsky 亚格子涡粘模型。 数值分析了单晶硅生长过程中不同阶段的传热 和流动特性,以及湍流输运对凝固相变界面形状的影响。 关键词:全局模拟;亚格子模型;单晶硅提拉法;湍流输运;熔体对流
2.4 等径拉晶过程中固液凝固界面形状的演变 图 4 给出了等径拉晶过程中凝固界面形状的演变情况。可以看出,凝固界面形状始 终呈凹状,在等径生长初始阶段,凝固界面的凹度最小,随着提拉过程的进行,凹度开 始变大,但自等径生长中间阶段到最后近收尾阶段,凝固界面形状变化不大。说明应该 通过工艺控制过程的动态优化来控制等径生长过程中凝固界面的形状。
[10]
+
u v u v
( ) ,其中 u
+
+
为无量纲速度,本文采用的壁面
,即
y +,y + ≤ 5 + u + = 5ln ( y + ) − 3.0472, 5 < y + < ybuff + + + ln ( y ) / 0.41 + 5.395, y ≥ ybuff
热屏和后继加热器对生长_300mm硅单晶热场影响的数值分析

第36卷第4期人 工 晶 体 学 报 V o.l 36 N o .4 2007年8月 J OURNAL O F S YNTHET IC CRY STA LS A ugust ,2007热屏和后继加热器对生长 300mm 硅单晶热场影响的数值分析高 宇1,2,周旗钢2,戴小林2,肖清华2(1.北京有色金属研究总院,北京100088;2.有研半导体材料股份有限公司,北京100088)摘要:本文采用有限体积元法软件C rys VU n 对直拉法生长直径300mm 硅单晶热场和热应力分布进行了模拟。
后继加热器通过补充晶体径向的热散失,使得沿生长界面径向的由熔体向晶体的热输运实现平衡,使晶体生长界面更加平坦。
随着热屏材料热辐射率的降低,晶体生长界面趋于平坦,生长界面上方热应力水平也随着热屏材料辐射率的减小而下降,使用内层高辐射率材料、外层低辐射率材料的复合式热屏结构进一步降低了晶体生长界面中心高度。
关键词:模拟;直径300mm 硅单晶;热屏;后继加热器中图分类号:TN304.1 文献标识码:A 文章编号:1000-985X (2007)04-0832-05N u m erical Anal ysis of the E ffects of H eat Shiel d and SuccessorH eater on H eat Fiel d of 300mm Si Si ngle CrystalGAO Yu 1,2,Z HOU Q i -gang 2,DAI X iao -lin 2,X IAO Q i n g-hua2(1.General Research Insti tute f or Nonferrou sM etals ,Beiji ng 100088,Ch i na ;2.GR I N M S e m iconductor M ateri als Co .,L t d,Beiji ng 100088,Ch i n a)(R eceive d 25F e bruary 2007,acce p t ed 12April 2007)Abst ract :A fi n ite vo lu m e so ft w are Crys VUn was used for the si m u lati o n of heat field and stress distri b u ti o n o f 300mm Si crysta.l The successor heater can be used to supp l y the radia lheat dissi p ation ,and the m e lt to crystal heat flo w is ba lanced by t h is process ,so that t h e crystal gro w th i n terface beca m e m ore flatted .Ther m al stress in the crystal upon the g r ow th i n terface decreasesw hen the e m issivity of hea t sh ield m ateria l decreases .The ther m al shie l d w ith h igh e m issi v ity m ateria l insi d e and lo w e m issiv ity m ateri a l outsi d e can greatly lo w er the interface he i g ht i n the center of t h e crysta.lK ey w ords :si m u lati o n ; 300mm Si si n g le crysta;l heat sh ield ;successor heater收稿日期:2007-02-25;修订日期:2007-04-12基金项目:科技部国际合作重点项目(No .2005DFA51050)作者简介:高宇(1981-),男,辽宁省人,硕士研究生。
高拉速对300_mm单晶硅点缺陷分布及生产能耗的影响

第52卷第4期2023年4月人㊀工㊀晶㊀体㊀学㊀报JOURNAL OF SYNTHETIC CRYSTALSVol.52㊀No.4April,2023高拉速对ϕ300mm单晶硅点缺陷分布及生产能耗的影响徐尊豪1,李㊀进2,何㊀显2,安百俊2,周春玲2(1.宁夏大学物理与电子电气工程学院,银川㊀750021;2.宁夏大学宁夏光伏材料重点实验室,银川㊀750021)摘要:大尺寸直拉单晶硅的 增效降本 是当前光伏企业急需解决的问题㊂本文采用有限元体积法对ϕ300mm直拉单晶硅生长过程分别进行稳态和非稳态全局模拟,研究提高拉晶速率对直拉单晶硅生长过程中的固液界面㊁点缺陷分布以及生长能耗的影响㊂结果表明:拉晶速率提高为1.6mm/min时固液界面的偏移量为33mm,不会影响晶体的稳定生长;拉晶速率对晶体中点缺陷的分布起决定性作用,提高拉晶速率不仅能降低自间隙点缺陷的浓度,而且使晶棒内V/G始终高于临界值;且拉晶速率对功率消耗影响较大,提高拉晶速率后晶体生长时间减少了46.4%,单根晶体生长消耗功率降低了约4.97%㊂优化和控制适宜的拉晶速率有利于低成本地生长特定点缺陷分布甚至无点缺陷单晶硅,为提高大尺寸直拉单晶硅质量㊁降低生产能耗提供一定的理论支持㊂关键词:直拉单晶硅;有限元体积法;拉晶速率;固液界面;点缺陷;生产能耗中图分类号:TQ127.2㊀㊀文献标志码:A㊀㊀文章编号:1000-985X(2023)04-0562-09 Effect of High Pulling Rate on the Distribution of Point Defects and Energy Consumption inϕ300mm Monocrystalline SiliconXU Zunhao1,LI Jin2,HE Xian2,AN Baijun2,ZHOU Chunling2(1.School of Physics and Electronic-Electrical Engineering,Ningxia University,Yinchuan750021,China;2.Ningxia Key Laboratory of Photovoltaic Materials,Ningxia University,Yinchuan750021,China)Abstract:The efficiency and cost reduction of large size Czochralski monocrystalline silicon is an urgent problem for photovoltaic enterprises.In this paper,the finite element volume method was used to simulate the growth process ofϕ300mm Czochralski monocrystalline silicon in both steady and unsteady state,respectively,to study the change rule of crystal-melt interface,point defect distribution and growth energy consumption during the growth process of Czochralski monocrystalline silicon by increasing the pulling rate.The results show that the shift of crystal-melt interface is33mm when the pulling rate increases to1.6mm/min,which would not affect the stable growth of crystals.The pulling rate plays a decisive role in the distribution of point defects in the crystal.Increaseing the pulling rate could not only reduce the concentration of self-interstital defects,but also make the V/G in the crystal bar always higher than the critical value.And the pulling rate has a great influence on the power consumption.After increasing the pulling rate,the crystal growth time is reduced by46.4%,and the power consumption for monocrystalline silicon growth is reduced by4.97%.Optimization and control of appropriate pulling rate is conducive to low cost growth of specific point defect distribution or even point defect free monocrystalline silicon,which provides some theoretical support for improving the quality of large size Czochralski monocrystalline silicon and reducing production energy consumption.Key words:Czochralski monocrystalline silicon;finite element volume method;pulling rate;crystal-melt interface;point defect;energy consumption㊀㊀收稿日期:2022-11-05㊀㊀基金项目:国家自然科学基金(51962030);直拉法单晶硅低能耗关键制备技术研究(2022XQZD006)㊀㊀作者简介:徐尊豪(1997 ),男,宁夏回族自治区人,硕士研究生㊂E-mail:xuzunhao123@㊀㊀通信作者:李㊀进,博士,教授㊂E-mail:li-jin@㊀第4期徐尊豪等:高拉速对ϕ300mm 单晶硅点缺陷分布及生产能耗的影响563㊀0㊀引㊀㊀言在全球绿色低碳转型的大方向和我国 双碳 目标的趋势下,通过直拉(Czochralski)法生长的单晶硅以转换效率和电池组件发电量高等优点,在新能源产业中占据着主导地位[1-2]㊂随着单晶炉投料量增加,单晶硅片直径突破到如今的210mm [3],大尺寸单晶硅 增效降本 的瓶颈问题成为研究重点,提升拉晶速率变得尤为重要㊂而直拉过程是一个热量㊁质量输运和界面移动的非平衡热力学耦合过程,热处理过程中的点缺陷集群化很大程度上决定了晶体的质量,直接影响太阳能电池转换效率㊂Abe 等[4]通过降低直拉晶体的生长速率改变热梯度,比较ϕ150mm 和ϕ250mm 的直拉晶体中固液界面的形状变化,结果表明热梯度是生长速率的递减函数,来自固液界面的空位与由热梯度产生的间隙的比率最终决定了单晶硅的性质㊂年夫雪等[5]通过改变12英寸(1英寸=2.54cm)直拉单晶硅恒定及连续变化的拉速(0.2~0.45mm /min)研究点缺陷分布规律,结果表明:拉速较大时,晶体中以空位点缺陷为主;逐步降低拉速时,自间隙点缺陷区域逐渐增大㊂Mukaiyama 等[6]通过改变0.2~0.8mm /min 的拉晶速率探究ϕ400mm 晶体中的热应力和C V -C I 的关系,研究表明,固液界面形状决定热应力和点缺陷的分布㊂Sabanskis 等[7]研究了ϕ50㊁ϕ100和ϕ200mm 晶体在拉速恒定以及逐步减小时,晶体中热应力㊁点缺陷和加热器功率的变化,研究得出长晶初期没必要保持恒定的拉速,热应力使C I 减小,而C V 增大㊂综上所述,有关拉晶速率对点缺陷的研究已经有了一定基础,但所研究的拉晶速率限制在0.85mm /min 以内,无法满足光伏市场对硅棒尺寸和生产效率的需求,对大尺寸单晶硅全局生长过程进行非稳态研究以及关于拉晶速率对生产能耗影响的研究较少㊂本文将温度场㊁流场和应力场耦合,对ϕ300mm 单晶硅等径阶段(300㊁500㊁800和1200mm)进行稳态模拟,探究不同高拉晶速率对固液界面变化的影响;又对单晶硅生长过程进行全局非稳态模拟,研究了拉晶速率对缺陷分布规律以及生产能耗的影响,为单晶硅大规模应用与工业生产中提高质量和降低能耗提供理论支持㊂1㊀计算方法与理论模型1.1㊀计算方法直拉过程中的传热㊁质量输运㊁磁场的控制微分方程为[8]:∂ρ∂t +Δ㊃(ρu )=0(1)∂(ρu )∂t +(u ㊃Δ)ρu =-Δp +Δ㊃τ+(ρ-ρ0)g +j ˑB +S u (2)∂(ρc p T )∂t +Δ㊃(ρc p u T )=Δ㊃(λeff ΔT )-Δ㊃q rad (r )+S T (3)∂(ρφi )∂t +Δ㊃(ρu φi )=Δ㊃(D φ,eff Δφi )+S φi (4)ρ=p 0m R g T (5)τij =μeff ∂u i∂x j +∂u i ∂x i ()-23μeff δij Δ㊃u (6)式中:ρ为密度;ρ0为参考密度;u 为速率;τ为应力张量;g 为重力向量;p 为压强;c p 为比热容;φi 为被动核素;T 为温度㊂μeff =μmolecular +μt 为有效动态黏度,μmolecular 为分子黏度,μt 为湍流黏度;λeff =λ+c p μt Pr t为有效热传导率;q rad (r )=ʏɕ0ɥ4πΩI λ(r ,Ω)dΩd λ为辐射热流矢量,I λ(r ,Ω)为点r 在Ω方向的辐射强度;δij 为克罗内克函数;D φ,eff 是动态扩散系数;S φi =S u ϕi +ϕi S p ϕi 代表体积i th 源(公式(2)㊁(3)中的源项具有相同的结构);j 为电流;B 为磁感应;p 0为基准压力;m 为分子量;R g =8314J㊃mol -1㊃K -1是通用气体常数㊂564㊀研究论文人工晶体学报㊀㊀㊀㊀㊀㊀第52卷长晶时固液界面结晶速率垂直分量可表示为[9]:V crys =1n x ρΔHéëêêλcrys ∂T crys ∂n -λmelt ∂T melt ∂n +(Q in rad -Q out rad )melt ùûúú(7)式中:V crys 为结晶速率;n 为固液界面法线矢量;ΔH 为结晶潜热;λcrys 为晶体中的热导率;λmelt 为熔体中的热导率;∂T crys ∂n 和∂T melt ∂n分别为界面处晶体和熔体的法向温度梯度;(Q in rad )crys /melt 和(Q out rad )crys /melt 分别为传入和传出的辐射通量㊂空位缺陷和自间隙缺陷进入晶体及其在结晶前缘附近的热区复合的控制方程可表示为[10-11]:∂C x ∂t +V ㊃ΔC x =Δ㊃(D x ΔC x )+4πa r (D i +D v )exp -ΔG kT ()(C eq i C eq v -C i C v )(8)式中:C eq x 为平衡缺陷浓度(x =i㊁v 分别为自间隙和空位);C x 为实际缺陷浓度;D x 为缺陷扩散系数;V 为拉晶速率;a r 为复合半径;ΔG 为重组自由能垒㊂图1㊀直拉炉体结构示意图Fig.1㊀Schematic diagram of Czochralski furnace structure 1.2㊀理论模型本文运用专业晶体生长模拟软件CGSim 进行数值模拟分析,通过对单晶硅生长炉结构进行合理的简化和改进,对基本热场构造进行保留,建立ϕ300mm 直拉单晶硅炉体模型,单晶炉由石墨加热器㊁石英坩埚㊁保温件㊁热屏㊁水冷装置等构件组成,炉体结构如图1所示㊂对于大尺寸单晶硅热场,提升拉晶速率容易引起固液界面附近热量攀升,导致后续晶体生长的不稳定,所以需增强晶体及熔体表面的散热效果,即降低固液界面与自由液面附近的温度㊂本文在创建炉体结构时设计了合理结构的热屏,通过对热量的导流增强散热,如图2(a)所示,并且在晶体与热屏处设计水冷装置,通过冷却水的不断循环释放热量,如图2(b)所示㊂炉内构建呈对称分布,考虑到硅熔体处网格划分对后续影响较大,在硅熔体处细化网格且均为矩形网格,将其划分为三块区域,如图3所示㊂靠近晶棒处的区域①化为25ˑ40块,靠近坩埚侧壁的区域②及靠近坩埚底部区域③分别为70ˑ40块和25ˑ70块,即将硅熔体划分为11100个单元格㊂对单晶硅生长过程进行全局数值模拟,具体生长工艺条件如下:石英坩埚内径为1520mm,侧壁厚度25mm㊂多晶硅填料量320kg,单晶硅棒直径300mm,总长度1460mm,炉体外壁温度恒定室温为300K,炉中充氩气气氛,流速为12.5L /min㊂固液界面温度为多晶硅熔点,设为1685K㊂主加热器功率为90000W,底部加热器功率为3000W㊂单晶硅弹性模量设为1.653ˑ1011Pa,泊松比设为0.217,晶体转速为10r /min,坩埚与晶体反方向旋转,转速为7r /min㊂图2㊀热屏(a)与水冷系统(b)结构图Fig.2㊀Structure diagram of heat screen (a)and cooling system (b)图3㊀硅熔体网格划分图Fig.3㊀Mesh division at silicon melt㊀第4期徐尊豪等:高拉速对ϕ300mm 单晶硅点缺陷分布及生产能耗的影响565㊀㊀㊀稳态模拟研究1.4~1.9mm /min 六种高拉速对等径阶段四种不同晶体高度的固液界面的影响,为非稳态模拟的工艺设置提供理论依据;非稳态模拟贯穿放肩与等径阶段,为研究高拉速对点缺陷浓度㊁分布以及生长能耗的影响,等径阶段的模拟研究拉速分别设定为目前研究的最高拉速(0.8mm /min)与提高拉速(1.6mm /min)两种工艺,且均为恒定拉速㊂研究两种工艺下晶体缺陷分布㊁浓度以及长晶所需能耗的变化㊂其他物性参数如表1所示㊂表1㊀物性材料参数Table 1㊀Physical parameters of material propertiesMaterial Heat conductivity /(W㊃m -1㊃K -1)Heat capacity /(J㊃kg -1㊃s -1)Emissivity Density /(kg㊃m -3)Latent heat /(J㊃kg -1)Silicon(melt)66.59150.32530 1.8ˑ106Silicon(crystal)110.612-0.1507T +0.000109T 2-4.0094ˑ10-8T 3+5.668ˑ10-12T 310000.9016-0.0026208T 2330 1.8ˑ106Quartz crucible 49000.852650 Graphite146.8885-0.17687T +0.000127T 2-4.6899ˑ10-8T 3+6.665ˑ10-12T 47100.81950 Water 0.642000.51000 Argon 0.01520 2000 Insulation 0.51000.8500 2㊀结果与讨论2.1㊀高拉晶速率对固液界面的影响固液界面是晶体与熔体热量传输与物质输运的媒介,关乎着单晶硅质量㊂等径阶段不同高度在不同拉速下的固液界面如图4所示(x r 为单晶硅径向长度,δ为固液界面偏移量)㊂图4㊀四种晶体高度下不同拉速的固液界面形貌图Fig.4㊀Interface shape of crystal-melt under different pulling rates at four crystal heights 由图4可看出固液界面形状在四种高度下存在相同规律,固液界面中心部位都随着拉晶速率的增大呈566㊀研究论文人工晶体学报㊀㊀㊀㊀㊀㊀第52卷上移趋势,固液界面形状逐渐上凸㊂拉晶高度为300mm 时,界面中心点由1.4mm /min 时的23.79mm 逐步增大到1.9mm /min 时的50.50mm,上升高度Δδ约为26.7mm;拉晶高度500mm 时Δδ约为25.2mm;拉晶高度800mm 时Δδ约为26.5mm;拉晶高度1200mm 时Δδ约为27.0mm㊂同一拉速在不同拉晶高度时的界面中心点最大偏移量基本相同,四种拉晶高度下六种拉速分别使固液界面中心点最大偏移量稳定在23㊁28㊁33㊁38㊁44和49mm 左右㊂固液界面前端和三向点位置的结晶速率并不相同,且同一拉速对固液界面偏移量的改变随着拉晶高度增大呈现先减小后增大的趋势,出现这一现象的原因是晶体高度较低时,硅熔体体积较大,固液界面轴向温度梯度较大,界面附近热量聚集较多,随着拉晶高度的增长,固液界面轴向温度梯度随着硅熔体体积减小而降低㊂而且,拉晶速率较小时,固液界面中心处界面偏移量较小,界面较为平坦㊂但随着拉晶速率的提高,固液界面逐渐上凸㊂出现此现象的原因是拉晶速率偏高,由公式(7),V crys 增大使固液界面温度梯度增大,且沿着晶棒径向逐渐减小,热量聚集不易散去㊂图5为晶体等径阶段不同高度在不同拉速下的自由液面温度变化图(x t 为自由液面边长,T 为自由液面温度)㊂由图5可以看出,四种高度下三相点区域及硅熔体自由界面的温度随拉晶速率上升而下降,以拉晶高度800mm 为例,三相点区域温度由1686.6K 降为1684.5K㊂说明在晶体周围的硅熔体向晶体的传热效率增加,这导致了三相点附近晶体生长速率大于晶体中心区域,而为了保证长晶的稳定,三相点在炉体中的位置不会随着坩埚的上升而变化㊂由固液界面形状和自由液面温度的变化规律可以看出,固液界面上凸的趋势会随着拉晶速率的提高而增强,所以拉晶速率提升的前提是晶体生长的稳定㊂发现拉晶速率为1.6mm /min 时,等径阶段各高度的固液界面较稳定,且自由液面轴向温度和三相点附近熔体平均温度稳定㊂图5㊀四种晶体高度下不同拉速的自由液面温度Fig.5㊀Temperature of free melt surface under different pulling rates at four crystal heights 2.2㊀高拉晶速率对晶体中点缺陷分布机理的影响图6为放肩阶段到等径阶段生长时(0.8㊁1.6mm /min)两种拉晶速率下晶体的生长特性图,为达到除拉晶速率外两种晶体生长工艺的一致性,模拟时采用同一热场,其他工艺参数相同㊂由图6可看出两种拉晶速率下晶体高度最终都为1400mm,晶体直径在放肩结束后都保持为300mm,晶棒和硅熔体的质量随着长晶的进行稳定增㊁减㊂截止到等径阶段结束,拉晶速率为0.8mm /min 时的长晶㊀第4期徐尊豪等:高拉速对ϕ300mm 单晶硅点缺陷分布及生产能耗的影响567㊀耗时约28.83h,拉晶速率为1.6mm /min 的长晶耗时约14.46h,提升拉晶速率使晶体生长时间减少了46.4%㊂图6㊀不同拉晶速率下晶体特性Fig.6㊀Crystal characteristics under different pulling rates 图7为晶体高度为800mm 时,两种拉晶速率下晶体内点缺陷分布图,C V -C I 表示晶体中空位与自间隙浓度差,点缺陷的分布以零等值线为分界线,正值(图中黑色字体数值)代表此处点缺陷以空位型为主,负值(图中白色字体数值)代表此处点缺陷以自间隙型为主㊂由图7可以看出,拉速为0.8mm /min(左)的晶体固液界面形状比拉速为1.6mm /min(右)的晶体固液界面平坦,证实了高拉晶速率是引起固液界面上凸的因素㊂但两种拉晶速率下,晶体中C V -C I 的最大值相同,为1.5366ˑ1014cm 3,且都位于固液界面中心处,表明靠近固液界面处以空位型缺陷为主㊂沿着晶体径向方向,两种拉速条件下点缺陷分布不同:拉速为0.8mm /min 时,出现零等值线,即晶体中点缺陷沿径向由空位型缺陷逐渐向自间隙型缺陷转变,呈现出晶体内侧以空位型缺陷为主,外侧以点缺陷自间隙型缺陷为主的特点㊂拉速为1.6mm /min 时,C V -C I 沿径向有相同规律,但在靠近固液界面附近区域未出现零等值线,而出现在远离晶体底部的晶体中,即晶体下半部点缺陷全部以空位型为主,沿法向向自间隙型缺陷过渡㊂这与文献[7]的研究结果一致㊂为进一步分析拉晶速率对固液界面处点缺陷的影响,对两种拉晶速率下固液界面处V /G (V 是晶体结晶处生长速率,G 是固液界面出轴向温度梯度)进行研究,该理论[12-14]提出V /G 低于临界值(1.3ˑ10-3cm 2㊃min -1㊃K -1)时,自间隙原子会从固液界面向晶体扩散补偿复合引起的自间隙原子减少,晶体中缺陷为自间隙原子聚集形成的A /B 型缺陷,即自间隙缺陷;若V /G 高于临界值,晶体中缺陷为空位聚集而成的D 型缺陷,即空位型缺陷㊂图8为两种拉晶速率下晶体高度800mm 时的V /G 图㊂由图8可看出,两种拉晶速率下,V /G 曲线都从固液界面中心沿径向逐渐降低,且曲线斜率基本维持不变㊂V /G 最大值均超过了临界值,拉速为0.8mm /min 时逐步减小到临界值以下,而在1.6mm /min 拉速下始终保持在临界值以上,G 也保持着随拉晶速率增大而变大的趋势㊂出现此现象的原因是晶㊁熔体间热量交换没有产生足够大的温度梯度,致使V /G 变化主要由长晶速率决定㊂上述结果表明,若降低拉晶速率,晶体中点缺陷以自间隙型缺陷为主,而提高拉晶速率后,不仅568㊀研究论文人工晶体学报㊀㊀㊀㊀㊀㊀第52卷可以得到较高的V /G ,同时自间隙型浓度减少,空位型缺陷浓度较高有效地降低了氧化环的生成,提高单晶硅的质量㊂图7㊀晶体高度为800mm,两种拉速条件下晶体中自间隙与空位缺陷分布图(左:拉晶速率为0.8mm /min;右:拉晶速率为1.6mm /min)Fig.7㊀Distribution of self-interstitials and vacancies in crystal at crystal length of 800mm under different pulling rate (left:pulling rate is 0.8mm /min;right:pulling rate is 1.6mm /min)图8㊀不同拉晶速率下V /G 的变化曲线Fig.8㊀Change curves of V /G under different pulling rates㊀第4期徐尊豪等:高拉速对ϕ300mm 单晶硅点缺陷分布及生产能耗的影响569㊀2.3㊀高拉晶速率对晶体生长能耗的影响直拉工艺中,提高拉晶速率不仅改变晶体质量,而且对晶体生长的功率消耗有着重要影响㊂图9为两种拉晶速率下晶体生长整个过程实际拉晶速率与功率的变化图㊂图9㊀不同拉晶速率下时间与功率的关系曲线Fig.9㊀Relationship between time and power under different crystal pulling rates 由图9可以看到,晶体生长的实际拉晶速率和目标拉晶速率是有一定偏差的,因为硅熔体热量不能快速达到目标拉速所需值,实际拉速呈现滞后性㊂等径阶段前两种拉晶条件下的实际拉晶速率与功率的变化趋势大致相同:放肩阶段拉速较小,功率变化范围小,当需要提升拉晶速率进行转肩时,功率迅速提升㊂晶体等径阶段的实际拉速与目标拉速保持一致,并延续至晶体生长完成,但功率呈现逐步上升的趋势,是因为随着长晶的持续,硅熔体逐渐减少,坩埚为保持三相点位置不发生改变持续上移,导致加热器与坩埚的相对受热面积减少,所以需要不断加大功率以达到结晶条件㊂两种拉晶速率条件下的功率消耗差别较大,拉速为1.6mm /min 的晶体共消耗功率126.99kW 且等径阶段功率曲线斜率较小,而拉晶速率为0.8mm /min 时晶体生长缓慢,需要持续加大功率维持晶体生长所需热量,所以完成长晶共消耗功率133.63kW 且等径阶段功率曲线斜率较大㊂3㊀结㊀㊀论本文利用有限元法对直拉单晶硅的生长过程分别进行局部稳态和全局非稳态模拟,分析了提升拉晶速率对单晶硅生长过程中固液界面形状㊁晶体中点缺陷浓度与分布以及生长能耗的影响㊂得出以下结论:1)高拉晶速率时固液界面偏移量的改变随着拉晶高度增大呈现先减小后增大的趋势,且拉晶速率为1.6mm /min时,固液界面中心点最大偏移量稳定在33mm,等径阶段各高度的固液界面较稳定,不影响晶体的稳定生长;2)拉晶速率对晶体生长时的缺陷分布有决定性因素,拉晶速率提升后,固液界面上V /G 始终大于临界值且晶棒内不存在C V -C I 零等值线,晶体内部点缺陷全部以空位型为主,即通过提高拉晶速率可以有效降低自间隙型浓度,有效提高单晶硅的质量;3)长晶时间和功率消耗随拉晶速率的提高明显减少,拉晶速率由0.8mm /min 提升到1.6mm /min 后,拉晶时间减少了46.4%,功率消耗降低了约4.97%,不仅增大了企业时570㊀研究论文人工晶体学报㊀㊀㊀㊀㊀㊀第52卷间效益,更降低了生产能耗㊂通过提升拉晶速率,为解决生产大尺寸直拉单晶硅提高品质和降低成本的问题提供一定的理论支持㊂参考文献[1]㊀江㊀华.未来光伏发电技术的发展趋势预测[J].太阳能,2022(1):5-13.JIANG H.Forecast of development trend of pv power generation technologies in the future[J].Solar Energy,2022(1):5-13(in Chinese).[2]㊀陈俊帆,赵生盛,高㊀天,等.高效单晶硅太阳电池的最新进展及发展趋势[J].材料导报,2019,33(1):110-116.CHEN J F,ZHAO S S,GAO T,et al.High-efficiency monocrystalline silicon solar cells:development trends and prospects[J].Materials Reports,2019,33(1):110-116(in Chinese).[3]㊀董梓童.硅片尺寸之争硝烟再起[N].中国能源报,2021-12-13(9).TONG Z T.The battle over the size of silicon wafers is raging again[N].China Energy News,2021-12-13(9)(in Chinese).[4]㊀ABE T,TAKAHASHI T.Intrinsic point defect behavior in silicon crystals during growth from the melt:a model derived from experimental results[J].Journal of Crystal Growth,2011,334(1):16-36.[5]㊀年夫雪,黄嘉丽,邓㊀康,等.拉速对12英寸单晶硅点缺陷分布影响的动态模拟仿真研究[J].稀有金属,2018,42(6):634-639.NIAN F X,HUANG J L,DENG K,et al.Pulling rate on point-defect distribution in12-inch silicon single crystal by dynamical simulations[J].Chinese Journal of Rare Metals,2018,42(6):634-639(in Chinese).[6]㊀MUKAIYAMA Y,SUEOKA K,MAEDA S,et al.Numerical analysis of effect of thermal stress depending on pulling rate on behavior of intrinsicpoint defects in large-diameter Si crystal grown by Czochralski method[J].Journal of Crystal Growth,2020,531:125334.[7]㊀SABANSKIS A,VIRBULIS J.Modelling of thermal field and point defect dynamics during silicon single crystal growth using CZ technique[J].Journal of Crystal Growth,2019,519:7-13.[8]㊀STR GROUP.CGSim flow module theory manual,v.8.12[DB/OL].St.Petersburg,Russia:Richmond VA,2008[2009-7-17].㊀http://.[9]㊀HIRTH J P.Theory of dislocations[M].2nd ed.Malabar,Fla:Krieger Publishing Company,1983.[10]㊀KULKARNI M S,VORONKOV V,FALSTER R.Quantification of defect dynamics in unsteady-state and steady-state Czochralski growth ofmonocrystalline silicon[J].Journal of the Electrochemical Society,2004,151(10):G663.[11]㊀KULKARNI M S.Defect dynamics in the presence of oxygen in growing Czochralski silicon crystals[J].Journal of Crystal Growth,2007,303(2):438-448.[12]㊀VORONKOV V V.The mechanism of swirl defects formation in silicon[J].Journal of Crystal Growth,1982,59(3):625-643.[13]㊀FALSTER R,VORONKOV V V,QUAST F.On the properties of the intrinsic point defects in silicon:a perspective from crystal growth and waferprocessing[J].Physica Status Solidi(b),2000,222(1):219-244.[14]㊀DORNBERGER E,VON AMMON W.The dependence of ring-like distributed stacking faults on the axial temperature gradient of growingczochralski silicon crystals[J].Journal of the Electrochemical Society,1996,143(5):1648-1653.。
大直径直拉硅单晶炉热场的数值模拟

大直径直拉硅单晶炉热场的数值模拟王学锋3,翟立君,周旗钢,王 敬,戴小林,吴志强(北京有色金属研究总院国家半导体工程研究中心,北京100088)摘要:数值模拟技术已经成为分析和发展工业化晶体生长工艺必不可少的工具。
提出了直拉硅单晶生长过程温度分布的有限元模拟,通过对300mm单晶炉内热场的数值模拟计算,得出了晶体生长不同阶段的单晶炉内温度分布及相应的温度梯度和热流密度分布。
关键词:直拉硅单晶;热场;数值模拟中图分类号:TN304.1 文献标识码:A 文章编号:0258-7076(2004)05-0890-04 随着半导体集成电路技术的不断发展,硅材料的应用也越来越广泛。
半导体硅作为现代电子工业的基础材料,已有50~60年的历史,随着IC 集成度的提高,给硅片质量提出了更高的要求,这就要求半导体材料行业能够提供直径更大、质量更好的单晶硅[1]。
然而,随着制备单晶硅直径的不断加大,单晶制备的每次装料量也随之增多,使得实验费用越来越高;而且,一些数据很难通过直接测量获得。
因此,人们想出用数值模拟的方法来模拟单晶硅生长过程的热场。
从1965年Billig采用一维片状近似的方法,获得了晶体半径和晶体拉速平方成反比的关系[2],现在人们进行的数值模拟向着瞬态、全系统的方向转变。
可以说,人们对于单晶炉热场进行数值计算经历了一个由简单到复杂、由局部到整体的过程。
随着计算机技术的发展,人们可以利用计算机运行更加复杂的大运算量的数值计算。
计算方法多采用差分法和有限元法[3]。
国内有学者曾经对晶体生长建立过局部的模型,并进行过相关的研究,得到了一些有益的结论。
本文运用有限元的方法对生长的硅单晶和晶体生长的热场作为整体进行研究,得到了不同条件下单晶炉内的热场分布。
对晶体实际生产有一定的指导作用。
1 计算模型根据热动力学第一定律即热能守恒定律和热扩散定律[4],可以得到(1)式:ρc(5Tt+{V}T{L}T)={L}T([D]{L}T)+q(1)将(1)式进行展开得到其常见形式:ρC(5T5t+V X5T5X+V Y5T5Y+V Z5T5Z=q+55X(K X5T5X)55Y(K Y5T5Y)+55Z(K Z5T5Z)(2)(2)式是有限元计算中用到的偏微分方程。
直径300mm硅单晶生长过程的热场模拟
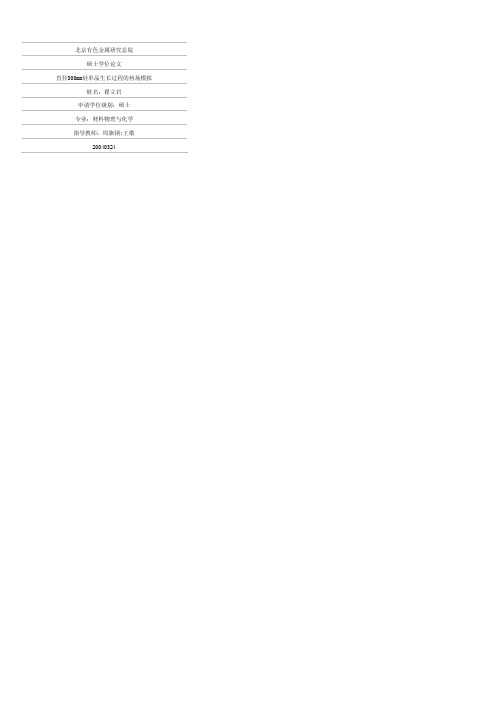
北京有色金属研究总院硕士学位论文直径300mm硅单晶生长过程的热场模拟姓名:翟立君申请学位级别:硕士专业:材料物理与化学指导教师:周旗钢;王敬20040324摘要摘要本文对直径300mm.晶体生长热场进行了数值模拟,并模拟计算了晶体生长过程中单晶炉内的氩气流动情况。
热场的模拟计算结果与实验测量的结果基本一致,较好地模拟了单晶炉内的热场分布情况。
通过对氩气流动情况的模拟分析,更好地了解了单晶炉内氩气流场的分布情况,这有利于我们更好地控制单晶炉内的氨气流的流速和流向,以及单晶中氧含量。
通过对有热屏和无热屏两种状态下的热场分布和晶体质量的比较,我们得出;单晶炉内施加热屏,可以很好地改进单晶炉内的热场分布,从而改善CZ硅单晶的生长条件,可以较好地控制晶体中的各种缺陷;同时,通过加装热屏,可以改进熔体内的温度分布,增大晶体生长的稳定性,从而获得更大的晶体生长速度,这样有利于提高生产效率;加装热屏还可以减少单晶炉内的热量损失,从而降低加热功率,减少了熔体与坩埚壁的反应,从而有利于控制晶体中的氧含量。
关键词:直拉硅晶体,热屏,300mm,热场,氩气流,数值模拟_—__——,—_——_-—_。
_‘-。
__。
●__-_●__。
●。
1。
_’’—‘‘-‘。
_。
‘-。
_。
_-。
’—’————一一一.垒!!塑璺———AbstractInthispaper,thehotzoneandtheargonflowdistributionduring300mmsinglecrystalgrowthprocessweresimulated.Thehotzonenumericalsimulationresultswereessentiallyinaccordancewitllexperimentalresuas.DifferentargonflowdistributionsinCZ—Sicrystalfurnacewereanalyzed,whichcanhelpUSunderstandtheargonflowdistributionsinCZ-Sicrystalfi瑚aceeffectivelyandadjusttheoxygenconcentrationbyanddirectioninCZ—Sicrystalfurnace.controllingargonflowvelocityComparingthehotzoneconfigurmionswithandwithoutheatshield,wefoundthatheatshieldcouldimprovethehotzoneconfiguration,crystalgrowthconditionsanddefectsintheCZ-Sicrystal.Simultaneously,throughadoptinghemshield,themelttemperaturedistributionswereimproved,thestabilityofcrystalgrowthWasenhancedandtheproductionefficiencyWaSincreaSedbyincreasingcrystalgrowthvelocity.ThehealersupplyingpowerWasreducedbyapplyingheatshieldbecauseofthereductionofheatloss,andtheinterstitialoxygeninthecrystalcanbedecreasedbecauseoftherestraintofthereactionbetweenthecrucibleandmelt,whichwasthemainsourceofoxygen.KeyWords:CZ-Sicrystal,heatshield,300mm,hotzone,argonflow,numericalsimulation.11.原创性声明本人郑重声明:所呈交的论文是我个人在导师指导下进行的研究工作及取得研究成果。
勾形磁场下提拉法生产单晶硅的数值模拟

第33卷第2期 人 工 晶 体 学 报 V ol.33 N o.2 2004年4月 JOURNA L OF SY NTHETIC CRY ST A LS April,2004 勾形磁场下提拉法生产单晶硅的数值模拟宇慧平1,隋允康1,张峰翊2,王学锋2(1.北京工业大学机电学院,北京100022;2.北京有色金属研究总院,北京100088)摘要:本文给出了提拉单晶硅时,勾形磁场强度的计算公式,并对单晶硅在有无勾形磁场情况下熔体内流场和氧的浓度分布进行了数值模拟,计算出磁场作用下磁场强度和洛伦兹力及有无磁场时流函数、垂直截面处的速度场和氧的浓度分布。
通过分析表明,勾形磁场能使流动更为平稳,能有效地降低熔体内及生长界面氧的浓度,并对产生这一现象的机理作了理论分析。
关键词:提拉法;勾形磁场;单晶硅中图分类号:O78 文献标识码:A 文章编号:10002985X(2004)022******* Numerical Simulation in Czochralski Si Melt under a Cusp Magnetic FieldYU Hui2ping1,SUI Yun2kang1,ZH ANG Feng2yi2,WANG Xue2feng2(1.C ollege of M echanical Engineering&Applying E lectronic T echnique,Beijing University of T echnology,Beijing100022,China;2.G eneral Research Institute for N on ferrous M etals,Beijing100088,China)(Received10September2003,accepted25December2003)Abstract:The equations used to calculate the cusp magnetic field strength in the crystal silicon growth were given.Numerical calculation was carried out to investigate the melt convection and oxygen transportation in aC zochralski growth system with and without a cusp magnetic field.The cusp magnetic filed strength and Lorentzforce at a vertical cross section were calculated and the stream function,velocity at a vertical cross section, oxygen concentration were als o calculated.Numerical result shows that the melt flow is dramatically suppressed and the oxygen concentration at the growth interface decreases with the application of the cusp magnetic field.The mechanism of the reductions of the convection and the concentration of oxygen was analyzed.K ey w ords:C zochralski method;cusp magnetic field;crystal silicon1 引 言提拉法是工业上生产单晶硅的重要方法。
定拉速生长对Φ300 mm直拉硅单晶生长影响分析

第49卷第5期人工晶体学报'cl.49No.5 202°年5月JOURNAL OF SYNTHETIC CRYSTALS Mvy,2°2°定拉速生长对!V00mm直拉硅单晶生长影响分析高宇1,朱亮1,张俊1,娄中士2(1浙江晶盛机电股份有限公司,绍兴312300;2.内蒙古中环领先半导体材料有限公司,呼和浩特010070)摘要:作为集成电路制备的衬底材料,对硅单晶的均匀性以及微缺陷的尺寸、密度要求极高。
传统直拉法生长硅单晶过程中,通过拉速变化控制晶体直径,因此拉速始终处于波动状态。
恒定拉速对晶体均匀性及缺陷密度、尺寸的影响研究较少&本研究实现了在35±0.7mm/h的拉速范围内生长出直径30°mm硅单晶,对晶体片间和片内电阻率分布以及FPD缺陷分布进行了检测,结果显示,在更小拉速波动阶段,晶体的电阻率均匀性得到改善,FPD缺陷密度降低。
关键词:硅单晶;直拉法;提拉速度中图分类号:078;0613.72文献标识码:A文章编号:1°°°-985X(2°2°)°5-°8n rd Analysis of0300mm Cz Silicon Single Crystal Growthwith Constanh Growth RateG$O Yu,ZHU Liang1,ZHANG Jun1,LOU Zhongshi2(1.Zhe soang J ongsheng Mechn oca aand EaectoocaaCo.,Ltd.,Shao cong312300,Chona;2.Inne oMongo aoa Zhonghuan Longcoan SemoconductooMateooaaCo.,Ltd.,Hohhot010070,Chona)Abstract:As the substrate material for IC fabrication,the uniformity of silicon single cestal and the size and density of micro defects are highly required.In the process of growing silicon single cestal by tradiConai CzochraNki(Cz)method,the cestal diameter is controWed by the growth-rate,so the growth-rate is always in a Cuctuating state.The eTects of constant growth-rate on cestal uniformity and defect density and size were still rarely studied.In this research,a30°mm diameter silicon cestal was grown at the rate of35±0.7mm/h.The resistivity distribution between wBers and within a wBer,and the distribution of FPD in the wBer were detected,the results show that the resistivity uniformity of the centals was improved and the density of FPD are reduced at the lower growth-rate CuctuaBon stage.Key words:siCcon single cestal;CzochraNki method;growth rate°引言直拉硅单晶生长过程中微缺陷形成是生长前沿空位和自间隙原子的产生、复合及扩散的结果&由于间隙型缺陷对集成电路的致命性且生长速度偏低,通常直拉硅单晶会偏向微空洞型晶体生长,甚至生长出无空洞型缺陷单晶&根据检测方法不同,空洞型缺陷又被称为cop[1],l std[2],fpd[3]等&但空洞型缺陷尺寸超过集成电路线宽1/3仍会造成器件失效,因此不断降低空洞型缺陷的尺寸和密度是半导体级硅单晶生长需要解决的重要问题&业内以Voenkva等屮+提出的缺陷理论来解释微缺陷形成过程,当Y晶体生长速度)/G(生长界面处轴向温度梯度)大于临界值时形成空位型缺陷,"G小于临界值时形成间隙型缺陷,这一临界值约为1.3x 10-3cm2-min-1-K-1®10〕&余学功等[11]综述了直拉硅单晶中空洞型缺陷的基本性质,包括空洞型缺陷的八面体结构及内部氧化层形成机理,详细解释了Voenkva提出的缺陷形成动力学模型和空位原子、间隙原子富集区关系理论,以及硼、氧、氮、碳、氢*12A4+等源于与空洞缺陷的相互作用&常规直拉硅单晶生长过程通过调整晶体提拉速度来控制晶体直径,晶体提拉速度波动较大不利于V/G 控制,阻碍了晶体质量提高&通过改变直拉硅单晶提拉速度,WLfced等[15]研究显示,晶体中的微缺陷从空作者简介:高宇(1981-),男,辽宁省人,工程师。
- 1、下载文档前请自行甄别文档内容的完整性,平台不提供额外的编辑、内容补充、找答案等附加服务。
- 2、"仅部分预览"的文档,不可在线预览部分如存在完整性等问题,可反馈申请退款(可完整预览的文档不适用该条件!)。
- 3、如文档侵犯您的权益,请联系客服反馈,我们会尽快为您处理(人工客服工作时间:9:00-18:30)。
300mm单晶硅提拉法生长数值模拟案例报告
一、模型背景
案例演示了基于FEMAG/CZ生长考虑磁场的300mm单晶硅的工艺过程,目标是模拟评估全局热场,优化加热系统,模拟晶体热应力等分布,最终改善热场和生长工艺,提高晶体质量。
FEMAG/CZ软件是专业化的CZ法晶体生长的模拟软件,也是2015年11月举办的IWMCG-8第八届国际生长模型化会议公认的求解性能和精度最好的晶体生长模拟软件。
国内以新昇半导体公司为代表的优秀企业,成功的应用FEMAG 软件,为300mm单晶硅提拉法生长工艺研发提供了建设性的帮助。
FEMAG/CZ的模拟可以是反向模拟或直接模拟。
前者通过定义晶体形状和单晶生长速度来计算加热器功率和其它未知变量,如温度场、流场、应力和掺杂和杂质等的分布。
后者通过定义加热器功率和单晶生长速度来预测晶体生长形状和上述未知场变量。
二、模型设置
FEMAG晶体生长模拟过程包括以下几个部分:几何模型的绘制、网格划分、模拟参数的设定、求解、结果分析。
2.1几何模型
几何模型采用实际用于生长300mm单晶硅的工业晶体炉构建,模型可以通过CAD文件导入,也可以在FEMAG中自行建模。
图1. 几何模型
2.2 网格划分
绘制完成几何模型后,划分网格,全模型网格剖分结果如下:
图2 全局网格
图3 弯液面计算与局部边界层网格
FEMAG 可以自动计算弯液面,对熔体、气体交界面进行修正,并考虑表面张力的作用,最终生成更符合真实物理模型的Melt/Gas 弯液面,如上图(1)区域。
对于固液界面以及液相和坩埚界面,存在明显的边界层效应,对于考虑磁场的提拉法生长过程,边界层效应将会更加显著,为了更好地表征该界面区域的速度场分布,也为了模型更好的收敛,软件提供了定制化的界面边界层网格功能,用户可以选择启用。
如上图(2)和(3)区域:
2.3 模拟参数的设定
2.3.1 工艺条件设定
可以在FEMAG 中设定工艺操作条件,如下所示:
提拉速率:0.5 mm/h;
晶转:-10 RPM ;
埚转:5 RPM ;
1 2 3
外部边界条件(炉子外壁温度): 300 K。
加热器功率:自适应
图4 工艺条件设置
图5 各部分材料显示
采用自适应加热器功率设置,生长预定义几何的晶体。
2.3.2材料参数设定
材料参数按照下图的界面进行设置,FEMAG提供半导体材料和单晶炉热场部件的所有物理属性,同时也可以在界面进行修改。
图6 材料参数设置
2.3.3 磁场设定:
FEMAG目前支持四种类型的加热器的外加磁场计算,分别是水平磁场、垂直磁场、CUSP以及Ovoid这四种类型。
这里选择是的Horizontal Magnetic field,磁感应强度参照实际工艺设置为0.3 T。
图7 磁场设置界面
2.4、模型结果
计算完成后,加热器总加热功率为92800 W,其中侧部加热器为9510 W,底部加热器为83290 W。
温度场分布结果如下:
图8 温度场分布
图9 温度场分布(XZ YZ截面)
晶体和熔体区域(M/C)温度场分布结果如上图,分别是XZ和YZ平面切片图,可以看到,在外加磁场的作用下,温度场分布不再满足轴对称,结果表明对于考虑磁场提拉法求解有必要使用3D全局模型而非简单的2D轴对称。
图10 速度场分布
图11 速度场分布(XZ YZ截面)
晶体和熔体区域(M/C)速度场分布结果如上图。
从XZ和YZ放大的切片图,可以看到,外加磁场对熔体速度场影响很大。
固液界面形状计算结果如下:
图12 固液界面形状
沿着界面的温度梯度如下:
图13 沿着界面的温度梯度分布
下图显示的是假定为<100>晶向的单晶硅热应力分布云图。
可以看到晶体接近于三相点的位置,热应力较为显著,热屏的存在导致此处温度变化显著,温度梯度诱发了显著的热应力分布。
改变热屏几何形状和材料参数,可以用于优化晶体的热应力分布。
图14 热应力分布
可以计算得到O、C等杂质原子在晶体和熔体中的分布情况,下图分别显示的是O原子在晶体和熔体的中分布情况。
图15 O原子在晶体中的分布
图16 O原子在熔体中的分布
下图显示的是电势分布以及熔体内的洛伦兹力的分布情况。
图17 电势分布
图18 电势分布和洛伦兹力分布
三、结论
采用FEMAG/CZ软件,分析考虑磁场的300mm单晶硅提拉法生长数值模拟,:
1. 能够考虑液相和气相内部的辐射、传导和对流的全局传热模拟,全局意味着考虑到所有的单晶炉单元,并且模拟结果是相互联系的;
2. 很容易控制的液流和气流计算的流体动力学模型;
3. 精确地预测晶体前沿生长形状;
4. 全自动化的动态模拟工具,能自动模拟从融化后的稳定、引晶、放肩、转肩、等径生长、收尾及后冷的完整单晶生长过程;
5. 预测晶体生长和冷却的热弹性应力、晶体生长的点缺陷、微缺陷及液相的氧分布等;
6. 优化单晶炉热场温度分布的工具;
使用FEAMG/CZ数值模拟工具,能够更好的了解结晶过程细节,预测晶体生长过程,优化晶体生长炉和生长工艺。