最终灭菌与非最终灭菌的区别
可灭菌与非最终灭菌分类指导原则
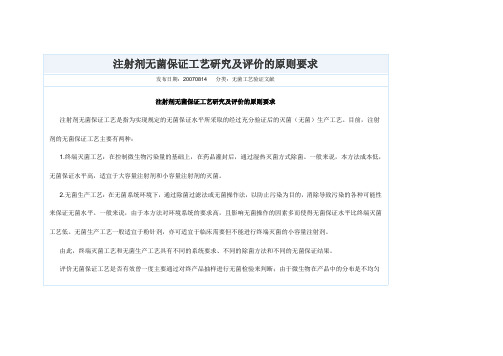
的,且抽检样品的数量有限,故抽检的结果不能真实代表整批产品的无菌状态。
国际上更为注重无菌保证工艺的设计是否合理、所用的设备与工艺是否经过充分的验证,在此基础上,切实按照验证后的工艺进行生产,这样才能保证灭菌(无菌)工艺的可靠性。
在业界,常用“无菌保证水平”(Sterility Assurance Level,SAL)概念来评价灭菌(无菌)工艺的效果,SAL的定义为产品经灭菌/除菌后微生物残存的概率。
该值越小,表明产品中微生物存在的概率越小。
为了保证注射剂的无菌安全性,国际上一致规定,采用湿热灭菌法的SAL不得大于10-6,即灭菌后微生物存活的概率不得大于百万分之一;而采用无菌生产工艺的产品,其SAL一般只能达到10-3,故仅限于临床必需注射给药而确实无法耐受终端灭菌的产品。
无菌生产工艺只适用于粉针剂或部分小容量注射剂。
一、注射剂剂型选择的原则注射剂包括大容量注射剂(50ml以上)、小容量注射剂(20ml以下)以及粉针剂三种剂型。
不同的剂型所采用的灭菌工艺可能不同,进而会影响产品的SAL,因此在评价无菌保证工艺时,需首先评价剂型选择的合理性。
在遵循剂型选择一般原则的基础上,从无菌保证水平的角度考虑,注射剂剂型选择的一般原则如下:1.首先要考虑被选剂型可采用的灭菌工艺的无菌保证水平的高低。
原则上首选剂型应能采用终端灭菌工艺(F0≥8),以保证SAL≤10-6。
2.对于有充分的依据证明不适宜采用终端灭菌工艺(F0≥8)且临床必需注射给药的品种,可考虑选择采用无菌生产工艺的剂型。
通常无菌生产工艺仅限于粉针剂或部分小容量注射剂。
3.注射剂中大容量注射剂、小容量注射剂和粉针剂之间的互改,如无充分的依据,所改剂型的无菌保证水平不得低于原剂型。
二、无菌保证工艺的技术要求1.大容量注射剂(1)应采取终端灭菌工艺,建议首选过度杀灭法(F0≥12),如产品不能耐受过度杀灭的条件,可考虑采用残存概率法(8≤F0<12),但均应保证产品灭菌后的SAL不大于10-6。
无菌技术概念

无菌原料药生产的无菌技术
• 工艺中的除菌过滤环节。
• 除菌过滤,利用直径0.22μm的精密过滤器过滤工 艺料液,达到除菌目的(过滤不能出去内毒素和 病毒)。
• 分装过程。无菌环境(A/B级),无菌包装材料, 密封。
无菌原料药生产的无菌技术
• 无菌技术是在生产中实现产品的无菌性。除此外, 洁净区的设计,施工,设施都是有别与一般厂房 的。比如气闸、缓冲,气锁,避免人流物流交叉 和不同级别区域间空气流通。
无菌原料药生产的无菌技术
• 人员管理。
• 洁净区主要的威胁来自于人,因为人不能灭菌、 除菌和消毒。所以只有通过穿洁净衣(无菌衣), 戴帽子、眼镜、口罩、手套来最大限度的减小这 种威胁。
• 更衣程序培训。进入洁净区的工作人员都是要经 过更衣程序培训,经验证合格后,才能进入洁净 区的。
无菌原料药生产的无菌技术
• 标准来源:微生物的杀灭遵循对数规则,达到这 个标准时。
无菌的意思
·2000版起的中国药典收藏了这个标准。 ·无菌验证方法:培养基模拟灌装实验。
无菌原料药生产的无菌技术
• 无菌技术是无菌原料药生产实现无菌的保证,有 三个重要环节:环境监控、人员管理、和工艺过 程的除菌环节。
• 我们十三车间采用除菌过滤技术,对药液除菌。
• FDA无菌工艺指南。
• 验证指南(2003)。
无菌原料药生产的简介
• 无菌药品按照生产工艺区分:最终灭菌产 品和非最终灭菌产品。
• 最终灭菌产品是指在最终容器中经受灭菌 的产品。此类产品能在受热或辐射时性质 稳定。
最终灭菌和非最终灭菌产品的工艺对比
非最终灭菌产品
• 除菌过滤产品
• 无菌工艺产品
无菌制剂生产关键的控制

无菌制剂生产关键的控制无菌药品一般指没有活体微生物存在的药品,具有无菌、无热原质、无不溶性微粒和高纯度等特性。
在药品制剂类别中,无菌药品也可称为无菌制剂。
无菌药品一般分为最终灭菌和非最终灭菌的药品。
最终灭菌和非最终灭菌的药品的根本区别是无菌性的过程或内容不同。
最终灭菌药品一般是在完成内包装工艺生产过程最终采取一个可靠的灭菌措施;非最终灭菌药品一般是在完成内包装工艺生产全过程始终未采取单独的灭菌措施。
非最终灭菌药品的生产过程可变因素较多,其生产条件、厂房装饰、生产设备、工艺用水、洁净环境(级别)、操作人员、检验等均有不同的特性要求,但必须保证无菌生产过程的时限性、操作性、完整性、真实性、追溯性,以达到无菌的目的。
无茵药品或无茵制剂主要有注射剂,其次为植入剂、冲洗剂、眼内注射溶液、眼内插入剂及供手术、伤口、角膜穿通伤用的眼用制剂,用于手术、创伤、烧伤或溃殇等的软膏剂、乳膏剂、气雾剂、喷雾剂、局部用散剂、耳用制剂、鼻用制剂、凝胶剂等。
为了加强对无菌药品生产过程的管理和监督,主要针对注射剂类风险产品的生产企业台帐管理,以及药品行政监督管理部门非现场监控.1培训1.1确保所有与药品生产有关的各级人员均经过与本岗位工作相适应的培训1.2对进入洁净区作业的人员还应进行微生物学基础知识、洁净区无菌控制、洁净区微粒控制、洁净区人员行为规范等内容的培训;1.3企业应及时对培训效果进行评估,对与药品生产有关的各级人员应进行持续的再培训。
2.物料2.1供应商确认2.1.1所有供应商均应经质量管理部门确认批准;2.1.2主要的原辅料及内包装材料供应商应进行现场审计。
现场审计内容可根据企业对物料的使用要求确定,但至少要包括对供应商的质量保证体系、工艺控制、卫生控制等内容进行审查;2.1.3质量管理部门应定期对供应商进行再评估,包括对供应商资质的变更情况、所供物料的质量情况等,并作为再确认的依据。
2.2物料购入从质量管理部门批准的供应商处采购。
最终灭菌与非最终灭菌的区别

无菌药品的普遍定义是要求没有活体微生物的存在,为了达到产品中没有活体微生物,无菌药品在制造过程中需要采取各种方法来去除制品中原有的微生物和防止制品受到微生物的污染[1]。
有许多方法可以用来控制微生物的生长、杀灭或去除微生物,通常在药品制造工艺过程中把这些方法分成化学和物理两大类。
其中,化学方法有化学消毒剂、气化双氧水、臭氧和环氧乙烷等;物理方法有湿热或干热灭菌、辐射灭菌和过滤除菌等。
在无菌药品的生产中,灭菌温度、灭菌时间、灭菌设施等诸多环节与药品质量和用药安全息息相关。
“欣弗”事件的主要原因是该公司在药品生产过程中的违规操作,即该公司未按批准的工艺参数灭菌,降低灭菌温度,缩短灭菌时间,增加灭菌柜装载量,影响了灭菌效果。
本文就如何合理选择灭菌方法,如何保证灭菌稳定、可靠,同时又不危害自然环境进行了阐述。
1 最终及非最终灭菌制剂产品的生产要求无菌药品的生产分为最终灭菌和非最终灭菌两种类型。
如无菌冻干粉针剂等制剂就属于非最终灭菌类型,在生产过程中需采用无菌作业以确保成品的无菌状态。
1.1 最终灭菌产品在最终灭菌注射剂(如大输液等)的生产过程中,配液、灌装可在非无菌环境中生产,而产品灌装后最终需通过灭菌措施达到灭菌要求。
比如,最终灭菌的容量为5OⅡlL以上的大容量注射剂由于直接输入血液,因此在其生产的全过程中应采取各种技术措施防止微粒、微生物、内毒素污染,以保证人体用药安全。
在药液配制过程中,应根据具体产品的要求,设置0.22~O.45 Il m的微孔滤膜过滤器对药液进行过滤,以降低药液中微生物、微粒的污染。
大输液所用包装容器,即玻璃瓶和胶塞应按规定进行清洗,包括粗洗、精洗等。
大输液的灭菌是在灌装后进行的,玻璃瓶经灌装、扎盖后,由专用小车运至双扉式灭菌柜。
灭菌设施一般可用水浴式灭菌器,以过热水为灭菌介质,采用水喷淋方式对灌装后药品加热升温和灭菌,灭菌后以循环水冷却。
大输液的灭菌一般应按配液批号进行安排,同一批号需要多个灭菌柜时,应编制亚批号。
无菌药品生产过程中的污染与控制

无菌药品生产过程中的污染与控制提纲132一、无菌药品生产简述◆无菌的定义:无菌指没有活的微生物。
◆无菌技术的定义:保持无菌物品、无菌区域不被污染、防止病原微生物侵入人体的一系列操作技术。
◆无菌物品的定义:经过物理或化学方法灭菌后,未被污染的物品的物品。
一、无菌药品生产简述◆无菌药品定义:无菌药品是指法定药品标准中列有无菌检查项目的制剂和原料药,包括无菌制剂和无菌原料药。
(2010版GMP无菌药品附录)◆常用的无菌药品一、无菌药品生产简述◆无菌生产工艺的基本特点无菌产品的质量不能完全依赖于对成品的无菌度测试。
◆取样检查不能保证支支的合格◆概率上的“无菌”理论上:无菌=没有任何活的微生物实际上:我们无法证明产品中没有活微生物存在实际我们无法明产品中没有活微物存在◆无法对整批产品进行100%检验一、无菌药品生产简述◆无菌制剂的生产工艺:-采用最终灭菌工艺的为最终灭菌产品;-部分或全部工序采用无菌生产工艺的为非最终灭菌产品。
一、无菌药品生产简述◆最终灭菌与非最终灭菌有着本质的区别◆最终灭菌:◆通常是在高质量的环境条件下进行灌装和密封产品容器。
产品在这类环境下灌装和封口是要最大一、无菌药品生产简述◆非最终灭菌的产品:◆在无菌生产工艺中,药品,容器及密封件首先要分别灭菌,然后把其组装起来。
由于在最终容器的产品不再经过灭菌处理,所以容器灌装及封口要在非常高质量的环境下进行。
无菌生产加工较最终灭菌方法有更多的变数。
◆在无菌组装成最终产品前,保证最终产品的各构成部分一一、无菌药品生产简述◆无菌产品生产涉及的内容示意图最终灭菌硬件厂房设施空调净化系统设备、仪器生产管理制约用水系统工艺用气系统物料无菌转运一、无菌药品生产简述◆控制生产过程中质量风险的目标:◆最终灭菌制剂:-灭菌前控制和最大程度减少产品的生物负荷-无菌保证水平为残存微生物污染概率≤10-6非最终灭菌制剂◆非最终灭菌制剂:一、无菌药品生产简述◆实施GMP管理是无菌药品质量保证的基础◆确保持续稳定地生产出合格的药品–适用于预定用途–符合注册要求–不仅限于质量标准最大限度减少药品生产过程中的风险交叉污染!二、无菌药品生产的污染源◆无菌药品GMP管理的基本原则◆2010版GMP无菌药品附录基本要求:◆第三条无菌药品的生产须满足其质量和预定用途的要求,应当最大限度降低微生物、各种微粒和热原的污染。
几种灭菌法的优缺点及技术参数

几种常用 灭菌法 的优缺点及技术参数灭菌法系指用适当的物理或化学手段将物品中活的微生物杀灭或除去,从而使物品残存活微生物的概率下降至预期的无菌保证水平的方法。
本法适用于制剂、原料、辅料及医疗器械等物品的灭菌。
无菌物品是指物品中不含任何活的微生物。
对于任何一批灭菌产物品来说而言,绝对无菌既无法保证也无法用试验来证实。
一批物品的无菌特性只能相对地通过物品中活微生物的概率低至某个可接受的水平来表述,即无菌保证水平(Sterility assurance level,简称SAL)。
实际生产过程中,灭菌是指将物品中污染微生物的残存概率下降至一定水平,以无菌保证水平SAL(sterility assurance level)表示预期的无菌保证水平。
最终灭菌的产物品微生物存活概率,即无菌保证水平不得高于10-6。
已灭菌产物品达到的无菌保证水平可通过验证确定。
灭菌产物品的无菌保证不能依赖于最终产品的无菌检验,而是取决于生产过程中采用合格的灭菌工艺、严格的GMP管理和良好的无菌保证体系。
灭菌工艺的确定应综合考虑被灭菌物品的性质、灭菌方法的有效性和经济性、灭菌后物品的完整性和稳定性等因素。
灭菌程序的验证是无菌保证的必要条件。
灭菌程序经验证后,方可交付正式使用。
验证内容包括:(1)撰写验证方案及制定评估标准。
(2)确认灭菌设备技术资料齐全、安装正确,并能处于正常运行(安装确认)。
(3)确认关键控制设备和仪表灭菌设备、关键控制和记录系统能在规定的参数范围内正常运行(运行确认)。
(4)采用被灭菌物品或模拟物品按预定灭菌程序进行重复试验,确认灭菌效果各关键工艺参数符合预定标准,确定经灭菌物品的无菌保证水平符合规定(性能确认)。
(5)汇总并完善各种文件和记录,撰写验证报告。
日常生产中,应对灭菌程序的运行情况进行监控,确认关键参数(如温度、压力、时间、湿度、灭菌气体浓度及吸收的辐照剂量等)均在验证确定的范围内。
灭菌程序应定期进行再验证。
最终灭菌与非最终灭菌的区别

无菌药品的普遍定义是要求没有活体微生物的存在,为了达到产品中没有活体微生物,无菌药品在制造过程中需要采取各种方法来去除制品中原有的微生物和防止制品受到微生物的污染[1]。
有许多方法可以用来控制微生物的生长、杀灭或去除微生物,通常在药品制造工艺过程中把这些方法分成化学和物理两大类。
其中,化学方法有化学消毒剂、气化双氧水、臭氧和环氧乙烷等;物理方法有湿热或干热灭菌、辐射灭菌和过滤除菌等。
在无菌药品的生产中,灭菌温度、灭菌时间、灭菌设施等诸多环节与药品质量和用药安全息息相关。
“欣弗”事件的主要原因是该公司在药品生产过程中的违规操作,即该公司未按批准的工艺参数灭菌,降低灭菌温度,缩短灭菌时间,增加灭菌柜装载量,影响了灭菌效果。
本文就如何合理选择灭菌方法,如何保证灭菌稳定、可靠,同时又不危害自然环境进行了阐述。
1 最终及非最终灭菌制剂产品的生产要求无菌药品的生产分为最终灭菌和非最终灭菌两种类型。
如无菌冻干粉针剂等制剂就属于非最终灭菌类型,在生产过程中需采用无菌作业以确保成品的无菌状态。
1.1 最终灭菌产品在最终灭菌注射剂(如大输液等)的生产过程中,配液、灌装可在非无菌环境中生产,而产品灌装后最终需通过灭菌措施达到灭菌要求。
比如,最终灭菌的容量为5OⅡlL以上的大容量注射剂由于直接输入血液,因此在其生产的全过程中应采取各种技术措施防止微粒、微生物、内毒素污染,以保证人体用药安全。
在药液配制过程中,应根据具体产品的要求,设臵0.22~O.45 Il m的微孔滤膜过滤器对药液进行过滤,以降低药液中微生物、微粒的污染。
大输液所用包装容器,即玻璃瓶和胶塞应按规定进行清洗,包括粗洗、精洗等。
大输液的灭菌是在灌装后进行的,玻璃瓶经灌装、扎盖后,由专用小车运至双扉式灭菌柜。
灭菌设施一般可用水浴式灭菌器,以过热水为灭菌介质,采用水喷淋方式对灌装后药品加热升温和灭菌,灭菌后以循环水冷却。
大输液的灭菌一般应按配液批号进行安排,同一批号需要多个灭菌柜时,应编制亚批号。
最终灭菌
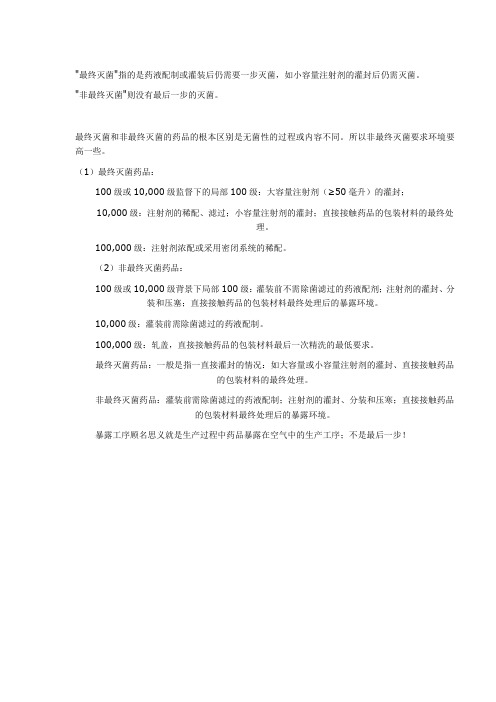
"最终灭菌"指的是药液配制或灌装后仍需要一步灭菌,如小容量注射剂的灌封后仍需灭菌。
"非最终灭菌"则没有最后一步的灭菌。
最终灭菌和非最终灭菌的药品的根本区别是无菌性的过程或内容不同。
所以非最终灭菌要求环境要高一些。
(1)最终灭菌药品:
100级或10,000级监督下的局部100级:大容量注射剂(≥50毫升)的灌封;
10,000级:注射剂的稀配、滤过;小容量注射剂的灌封;直接接触药品的包装材料的最终处
理。
100,000级:注射剂浓配或采用密闭系统的稀配。
(2)非最终灭菌药品:
100级或10,000级背景下局部100级:灌装前不需除菌滤过的药液配剂;注射剂的灌封、分装和压塞;直接接触药品的包装材料最终处理后的暴露环境。
10,000级:灌装前需除菌滤过的药液配制。
100,000级:轧盖,直接接触药品的包装材料最后一次精洗的最低要求。
最终灭菌药品:一般是指一直接灌封的情况:如大容量或小容量注射剂的灌封、直接接触药品
的包装材料的最终处理。
非最终灭菌药品:灌装前需除菌滤过的药液配制;注射剂的灌封、分装和压寒;直接接触药品
的包装材料最终处理后的暴露环境。
暴露工序顾名思义就是生产过程中药品暴露在空气中的生产工序;不是最后一步!。
- 1、下载文档前请自行甄别文档内容的完整性,平台不提供额外的编辑、内容补充、找答案等附加服务。
- 2、"仅部分预览"的文档,不可在线预览部分如存在完整性等问题,可反馈申请退款(可完整预览的文档不适用该条件!)。
- 3、如文档侵犯您的权益,请联系客服反馈,我们会尽快为您处理(人工客服工作时间:9:00-18:30)。
无菌药品的普遍定义是要求没有活体微生物的
存在,为了达到产品中没有活体微生物,无菌药品在制造过程中需要采取各种方法来去除制品中原有的
微生物和防止制品受到微生物的污染[1]。
有许多方法可以用来控制微生物的生长、杀灭或去除微生物,通常在药品制造工艺过程中把这些方法分成化学和物
理两大类。
其中,化学方法有化学消毒剂、气化双氧水、臭氧和环氧乙烷等;物理方法有湿热或干热灭菌、辐射灭菌和过滤除菌等。
在无菌药品的生产中,灭菌温度、灭菌时间、灭菌
设施等诸多环节与药品质量和用药安全息息相关。
“欣弗”事件的主要原因是该公司在药品生产过程中的违规操作,即该公司未按批准的工艺参数灭菌,降低灭菌温度,缩短灭菌时间,增加灭菌柜装载量,影响
了灭菌效果。
本文就如何合理选择灭菌方法,如何保证灭菌稳定、可靠,同时又不危害自然环境进行了阐述。
1 最终及非最终灭菌制剂产品的生产要求
无菌药品的生产分为最终灭菌和非最终灭菌两
种类型。
如无菌冻干粉针剂等制剂就属于非最终灭菌类型,在生产过程中需采用无菌作业以确保成品的无
菌状态。
1.1 最终灭菌产品
在最终灭菌注射剂(如大输液等)的生产过程中,
配液、灌装可在非无菌环境中生产,而产品灌装后最终需通过灭菌措施达到灭菌要求。
比如,最终灭菌的容量为5OⅡlL以上的大容量注射剂由于直接输入血液,因此在其生产的全过程中应采取各种技术措施防止微粒、微生物、内毒素污染,以保证人体用药安全。
在药液配制过程中,应根据具体产品的要求,设置0.22~O.45 Il m的微孔滤膜过滤器对药液进行过滤,以降低药液中微生物、微粒的污染。
大输液所用包
装容器,即玻璃瓶和胶塞应按规定进行清洗,包括粗洗、精洗等。
大输液的灭菌是在灌装后进行的,玻璃瓶
经灌装、扎盖后,由专用小车运至双扉式灭菌柜。
灭菌
设施一般可用水浴式灭菌器,以过热水为灭菌介质,采用水喷淋方式对灌装后药品加热升温和灭菌,灭菌后以循环水冷却。
大输液的灭菌一般应按配液批号进行安排,同一批号需要多个灭菌柜时,应编制亚批号。
1.2 非最终灭菌产品
采用非最终灭菌方式生产的无菌分装注射剂一
般是不耐热且不能进行成品灭菌的药品,所以必须特别强调药品生产过程中的无菌操作。
其生产作业区的无菌操作与非无菌操作应严格分开,所有从非无菌操作区进入无菌操作区的物料器具必须经过严格灭菌,生产人员应按无菌作业要求进行人净程序。
如在冻干粉针剂的生产洁净室,原辅料需称量后被送入药液配制(包括浓配、稀配)问按药品的要求配制好药液,药液经过设在配液间内的2级或3级过滤,其中必须经过过滤精度为0.22 u m的除菌过滤器后才能送入灌
装机被灌装入包装容器(如西林瓶等)。
用于包装冻干粉针的西林瓶须从进瓶间转入洗瓶灭菌间,先由纯水和注射用水清洗后,经灭菌(一般采用干热灭菌法,隧道灭菌装置或灭菌柜)再送入灌装机用于灌装。
而西林瓶的瓶塞在洗塞间,经饮用水、纯水和注射用水清洗后,采用蒸汽灭菌、硅化和干燥后待用。
近年来,胶
塞清洗、硅化、灭菌联动的设备,如自动湿法超声波胶
塞清洗机等常用于胶塞的灭菌处理。
西林瓶的铝盖在铝盖灭菌间经清洗、灭菌后被送入压盖机压盖。
无菌洁净生产区存在多种可能导致污染和交叉
污染的因素,如空气、各类介质、生产设施、原辅材料
包装材料、反应物、人员等。
进入无菌生产区的操作人
员应在经过手消毒和更换无菌洁净工作服后才能进入;人员退出时,同样应经过手消毒和更换无菌工作服为一般洁净工作服。
无菌区与外无菌区之间运送物料或工器具用的传递柜(窗)均应设有灭菌装置嘲。
2 合理选择灭菌方法及设备
2.1 灭菌方法
无菌制剂药品生产常用的灭菌方式有物理灭菌
和化学灭菌两种方式。
物理灭菌有加热、辐射、过滤等,化学灭菌是用化学品的气体或蒸气对药品、材料进行灭菌的方法。
选择灭菌设备,要根据无菌药品采用的制造工艺进行确定,如制造无菌药品有采用无菌制造和最终灭菌制造两种工艺。
制造工艺不同,采用的灭菌工艺也有所不同。
2.1.1 湿热灭菌
灭菌能力强,最有效,应用也最广。
一般适用于耐热药品、容器、培养基、无菌衣、胶塞以及其他遇高温
和潮湿不发生变化或损坏的物品灭菌。
成型设备有立式灭菌锅、台式压力蒸汽灭菌器、脉动真空灭菌柜、中
成药灭菌柜、多功能安瓿检漏灭菌柜、大输液水浴灭菌柜等。
2.1.2 干热灭茵
可去除热原物质,适用于耐高温但不宜用湿热灭
菌法灭菌的物品,如金属容器、纤维制品、固体试药、液状石蜡及玻璃仪器等。
成型设备有净化双扉干燥烘箱、西林瓶隧道灭菌器等。
2.1.3 辐射灭菌法
最常用的为60Co—Y射线辐射灭菌。
适宜于医疗
器械、容器、生产辅助用品、不受辐射破坏的原料药及
成品等。
要控制辐射剂量。
2.1.4 气体灭菌法
常用的化学消毒剂有环氧乙烷、气态过氧化氢、
甲醛、臭氧等。
适用于在所选气体中稳定的物品消毒灭菌。
还需要注意灭菌气体的可燃可爆性、致畸性和残留毒性。
采用环氧乙烷时,还应考虑泄露实验。
成型
设备有臭氧、环氧乙烷灭菌柜及甲醛、臭氧熏蒸。
2.1.5 过滤除菌法
常用于热不稳定的药品溶液或原料的除菌。
如无
菌原料药、冻干粉针生产除菌。
可根据被灭菌无菌制剂的特性采用一种或多种
方法组合灭菌,尽可能选用最终灭菌法灭菌。
若产品不适合采用最终灭菌法,可选用过滤除菌法或无菌生产工艺达到无菌保证要求,如可能应对非最终灭菌的产品做补充性灭菌处理(如流通蒸汽灭菌)。
2.2 灭菌设备
选用灭菌设备应本着节能、灭菌均匀、速度快、安全性好、操作简单、性能稳定、可靠性好的原则。
所有
的灭菌方法都应经过验证[3],同样,无论采用何种灭菌设备,最后都要验证其灭菌除热原的效果,来确认设备的适宜性。
根据灭菌工艺要求选择无菌制剂药品生产用灭
菌设备的方法:(1)设备的设计和安装应有利于避免交叉污染、避免差错并便于清洁及日常维护。
全部材料应采用优质不锈钢制作。
氩弧焊焊接,焊缝必须平整光滑,弯角应圆弧过渡,材料折边不能有死角和缝隙。
结构上无盲区,便于清洗和防止尘埃粒子沉积。
(2)工艺设备应在生产工艺规定的参数范围内运行。
如隧道式灭菌干燥机,各段温度根据生产工艺要求可独立控制和任意设定,灭菌加热段温度可在300~380℃内控制,350℃高温灭菌段运行时间一般≥
5 min。
灭菌后抗生素玻璃瓶的微粒达到100级洁净度要求、细菌内毒素降3个对数单位以及微生物不得检出。
又如湿热和干热灭菌箱,胶塞和铝盖灭菌箱位于两个不同洁净区的双扇门应配置电气或PLC电脑控制,保证各洁净区之间的隔离,防止由于误操作而引起的不符合GMP的事故发生。
另外,干热灭菌箱的
进、出风口需安装高效过滤器,防止外界对内部的污染。
3 结束语
无菌制剂原则上是制剂中不含任何活的微生物,
但绝对无菌既是无法保证也是无法用实验来证实的。
实际生产过程是将制剂中微生物存活率下降至
SAL≤10 。
良好的灭菌工艺是无菌制剂的重要保证。
确定灭菌工艺时应把无菌制剂的性质、灭菌方法的有效性和经济性、灭菌后物品的完整性、灭菌介质的残留量等因素综合考虑。
[参考文献]
[1]李龙迪,李敏,李小燕.关于无菌制剂无菌检查方
法验证的探讨
[J].新疆中医药,2OlO,(01):34-36.
[2]霍秀敏.注射剂无菌安全存在的问题及对策思考[J].中国执业药
师,2009,(10):37—39.
[3]吕慧侠,周建平.灭菌和无菌制剂及其制各技术发展概况[J].机电
信息。
2004,(o6):54—58.。