球墨铸铁常见缺陷的分析与对策
球墨铸铁常见缺陷的分析与对策
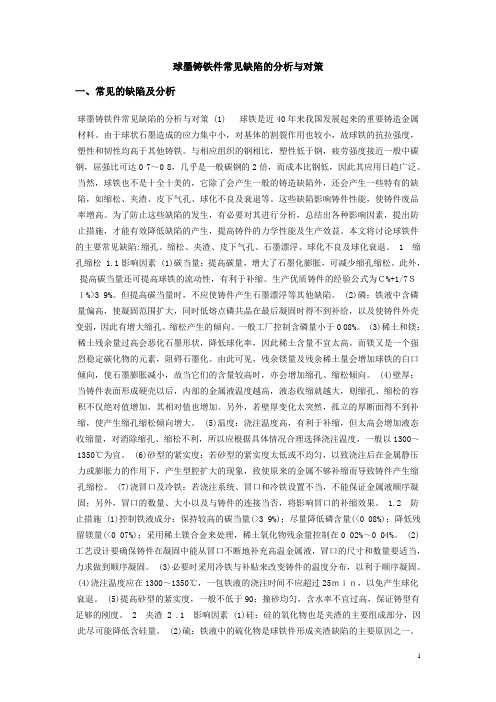
球墨铸铁件常见缺陷的分析与对策一、常见的缺陷及分析球墨铸铁件常见缺陷的分析与对策 (1) 球铁是近40年来我国发展起来的重要铸造金属材料。
由于球状石墨造成的应力集中小,对基体的割裂作用也较小,故球铁的抗拉强度,塑性和韧性均高于其他铸铁。
与相应组织的钢相比,塑性低于钢,疲劳强度接近一般中碳钢,屈强比可达0 7~0 8,几乎是一般碳钢的2倍,而成本比钢低,因此其应用日趋广泛。
当然,球铁也不是十全十美的,它除了会产生一般的铸造缺陷外,还会产生一些特有的缺陷,如缩松、夹渣、皮下气孔、球化不良及衰退等。
这些缺陷影响铸件性能,使铸件废品率增高。
为了防止这些缺陷的发生,有必要对其进行分析,总结出各种影响因素,提出防止措施,才能有效降低缺陷的产生,提高铸件的力学性能及生产效益。
本文将讨论球铁件的主要常见缺陷:缩孔、缩松、夹渣、皮下气孔、石墨漂浮、球化不良及球化衰退。
1 缩孔缩松 1.1影响因素 (1)碳当量:提高碳量,增大了石墨化膨胀,可减少缩孔缩松。
此外,提高碳当量还可提高球铁的流动性,有利于补缩。
生产优质铸件的经验公式为C%+1/7Si%>3 9%。
但提高碳当量时,不应使铸件产生石墨漂浮等其他缺陷。
(2)磷:铁液中含磷量偏高,使凝固范围扩大,同时低熔点磷共晶在最后凝固时得不到补给,以及使铸件外壳变弱,因此有增大缩孔、缩松产生的倾向。
一般工厂控制含磷量小于0 08%。
(3)稀土和镁:稀土残余量过高会恶化石墨形状,降低球化率,因此稀土含量不宜太高。
而镁又是一个强烈稳定碳化物的元素,阻碍石墨化。
由此可见,残余镁量及残余稀土量会增加球铁的白口倾向,使石墨膨胀减小,故当它们的含量较高时,亦会增加缩孔、缩松倾向。
(4)壁厚:当铸件表面形成硬壳以后,内部的金属液温度越高,液态收缩就越大,则缩孔、缩松的容积不仅绝对值增加,其相对值也增加。
另外,若壁厚变化太突然,孤立的厚断面得不到补缩,使产生缩孔缩松倾向增大。
球墨铸铁金相试样制备中的常见缺陷及其原因分析
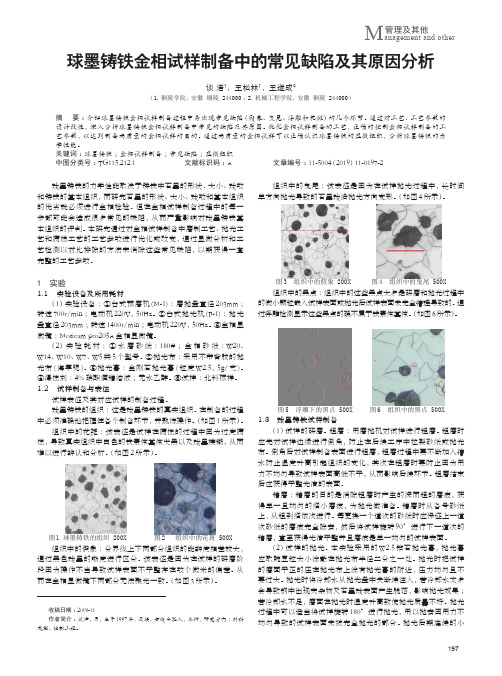
球墨铸铁金相试样制备中的常见缺陷及其原因分析
谈 浩¹,王松林¹,王继成²
(1. 铜陵学院,安徽 铜陵 244000 ;2. 机械工程学院,安徽 铜陵 244000)
摘 要 :介绍球墨铸铁金相试样制备过程中易出现常见缺陷(假象、曳尾、浮雕和花斑)的几个环节。通过对工艺、工艺参数的
收稿日期 :2019-11 作者简介 :谈浩,男,生于 19ห้องสมุดไป่ตู้7 年,汉族,安徽合肥人,本科,研究方向 :材料 成型、控制工程。
组织中的曳尾 :该表征是因为在试样抛光过程中,长时间 单方向抛光导致的石墨球沿抛光方向变形。(如图 4 所示)。
图 3 组织中的假象 200X 图 4 组织中的曳尾 500X 组织中的黑点 :组织中的这些黑点大多是研磨和抛光过程中 的微小颗粒嵌入试样表面或抛光后试样表面未完全清理导致的。通 过浮雕检测显示这些黑点的确不属于铁素体基体。(如图 6 所示)。
2 结果及讨论 2.1 球墨铸铁试样制备中常见的缺陷及应对措施
文献标识码 :A
文章编号 :11-5004(2019)11-0197-2
球墨铸铁的力学性能取决于铸铁中石墨的形状、大小、球数 和铸铁的基本组织,而研究石墨的形状、大小、球数和基本组织 的优劣就必须进行金相检验。但在金相试样制备过程中的每一 步都可能会造成很多常见的缺陷,从而严重影响对球墨铸铁基 本组织的评判。本研究通过对金相试样制备中磨制工艺、抛光工 艺和腐蚀工艺的工艺参数进行优化或改变,通过显微分析和工 艺检测以对比排除的方法来消除这些常见缺陷,以期获得一套 完整的工艺参数。
试样表征及其对应试样的制备过程。 球墨铸铁的组织 :这是球墨铸铁的真实组织。在制备的过程 中必须准确地把握住各个制备环节,并熟练操作。(如图 1 所示)。 组织中的花斑 :该表征是试样在腐蚀的过程中因为过度腐 蚀,导致真实组织中白色的铁素体基体发黑以及球墨模糊,从而 难以进行辨认和分析。(如图 2 所示)。
球墨铸铁导盘常见缺陷分析与对策(下)
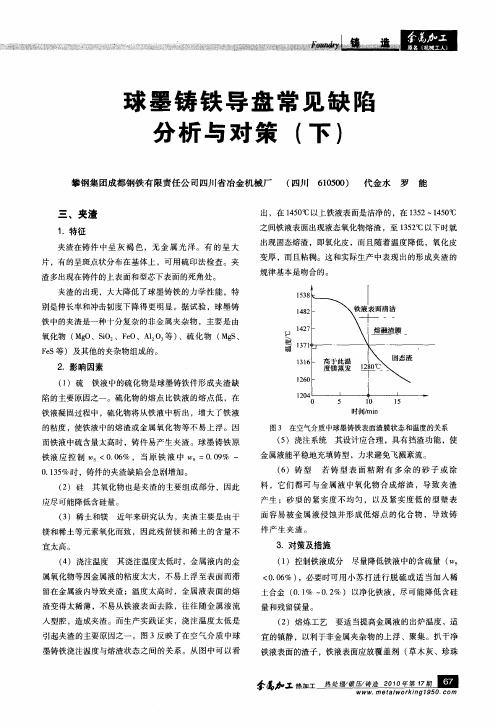
( )铸型 若铸 型表面粘附有多余 的砂子或涂 6
料 ,它们 都可 与金 属液 中氧化 物合 成熔 渣 ,导 致夹 渣
产生 ;砂 型 的紧实 度不 均匀 ,以及 紧实度 低的 型壁 表 面容 易被 金属 液侵 蚀并 形成低 熔点 的化合 物 ,导致 铸 件产 生夹 渣 。
应尽可能降低含硅量。 ( )稀 土和镁 3 近年 来研 究认 为 ,夹渣 主要 是 由于
3 1 断面应比灰铸铁增大 1% 一 5 ,以增加浇注速度,缩 0 1 %
短浇注时间。另外 ,还可采用挡渣性能较好的浇注系统。
注温度增高 ,铁液在 型腔 内保持 高温液态 的时 间增 长,
石墨有足够的时间上浮 ,石 墨漂浮就显得严重 。
四、石墨漂浮
1 特征 .
石墨漂浮是球墨铸铁所特 有的缺陷 ,出现在铸件 上
铁 中的夹渣是一种 十分复杂 的非金属 夹杂物 ,主要是 由
一
氧化 物 ( g M O、S : e i 、F O、A: , ) O 1O 等 、硫化 物 ( 、 M F S等 )及其他的夹杂物组成的 。 e
赠
J
一
1壁一 .堕 昼
。 、 \
固态 渣
2 .影响因素
多次扒渣 ,以免将非金属夹杂物留在铁液 中造成夹渣。 ( )浇注系统的设计 要使铁液平稳地充填型腔 ,浇 4
液中的溶解度会 降低 , 铁液将析 出大量石墨 ,从而加 重 石墨漂浮。残留镁量越高 ,石墨漂 浮就 越少 ,这是 因为
镁能阻止石墨化 ,使共晶点往右移的缘故 。 ( )浇注温度 4 在铸 型条件相 同的情况下 ,随着浇
量 和残 留镁量 。
属氧化物等 因金属液 的粘度 太大 ,不易上 浮至表 面而滞 留在金属液 内导致夹渣 ;温度 太高时 ,金属 液表 面的熔 渣变得太稀薄 ,不易从铁液 表面去 除,往 往 随金 属液 流 人型腔 ,造成夹渣 。而生产 实践证实 ,浇注温度 太低是 引起夹渣 的主要原 因之一 。图 3反映 了在空气介 质 中球 墨铸铁浇注温度与熔渣状态 之间的关 系。从 图中可 以看
浅析球墨铸铁件缺陷产生原因及防止措施

浅析球墨铸铁件缺陷产生原因及防止措施
1、坯料的缺陷:由于坯料的杂质含量过高,砂砾过大,沿铸缸边缘空隙较大等,都有可能导致炉内坯料缺陷大,从而产生球墨铸铁件缺陷。
2、成型工艺有问题:如砂芯型腔孔形不规则,型腔深度低,入型质量差,表面光洁度及粘结质量差等,都有可能产生球墨铸铁件缺陷。
3、浇注不合理:球墨铸铁件的浇注工艺过程中需要满足一定的条件,当不合理时,会导致溶质的不均匀分布,产生球墨铸铁件缺陷。
4、冷却不合理:冷却工艺是球墨铸铁件质量重要影响因素,冷却不合理,有可能使坯体结晶不良,从而产生球墨铸铁件缺陷。
二、防止球墨铸铁件缺陷的措施
1、提高坯料质量:在生产过程中,应加强原料检查,确保原料质量良好,并严格控制杂质含量,以减少成型过程中缺陷的发生。
2、改进成型工艺:应采用有利于消除和避免缺陷的成型工艺,如采用自动模具成型等技术,减少缺陷产生的可能性。
3、改善浇注工艺:采用有利于消除缺陷的浇注工艺,如采用连续浇铸或提高浇注压力,改善浇注品质,以减少球墨铸铁件缺陷。
4、优化冷却工艺:采用合理的冷却系统可以有效地控制坯体扩大速度,减少坯体内部残余应力,提高结晶度,以减少球墨铸铁件缺陷的产生。
三、结论
球墨铸铁件的缺陷的产生主要由坯料质量、成型工艺、浇注工艺以及冷却工艺不合理等原因引起。
因此,为防止球墨铸铁件缺陷的产生,应采取提高坯料质量、改进成型工艺、改善浇注工艺以及优化冷却工艺等措施。
只有这样,才能在生产过程中控制住缺陷,获得优良质量的球墨铸铁件。
浅析球墨铸铁件缺陷产生原因及防止措施
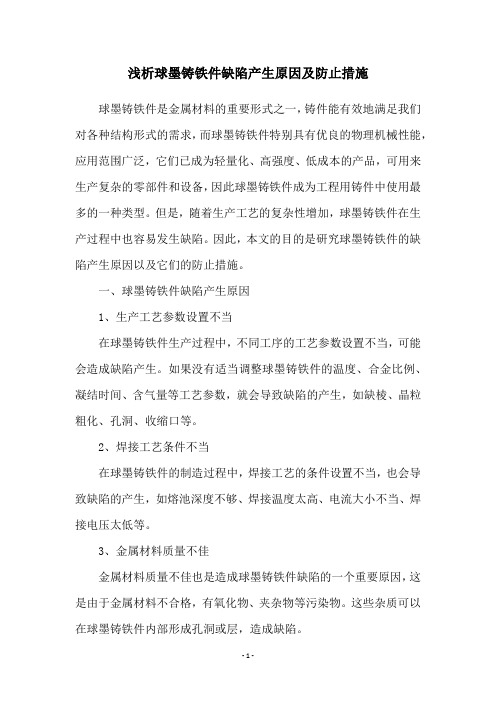
浅析球墨铸铁件缺陷产生原因及防止措施球墨铸铁件是金属材料的重要形式之一,铸件能有效地满足我们对各种结构形式的需求,而球墨铸铁件特别具有优良的物理机械性能,应用范围广泛,它们已成为轻量化、高强度、低成本的产品,可用来生产复杂的零部件和设备,因此球墨铸铁件成为工程用铸件中使用最多的一种类型。
但是,随着生产工艺的复杂性增加,球墨铸铁件在生产过程中也容易发生缺陷。
因此,本文的目的是研究球墨铸铁件的缺陷产生原因以及它们的防止措施。
一、球墨铸铁件缺陷产生原因1、生产工艺参数设置不当在球墨铸铁件生产过程中,不同工序的工艺参数设置不当,可能会造成缺陷产生。
如果没有适当调整球墨铸铁件的温度、合金比例、凝结时间、含气量等工艺参数,就会导致缺陷的产生,如缺棱、晶粒粗化、孔洞、收缩口等。
2、焊接工艺条件不当在球墨铸铁件的制造过程中,焊接工艺的条件设置不当,也会导致缺陷的产生,如熔池深度不够、焊接温度太高、电流大小不当、焊接电压太低等。
3、金属材料质量不佳金属材料质量不佳也是造成球墨铸铁件缺陷的一个重要原因,这是由于金属材料不合格,有氧化物、夹杂物等污染物。
这些杂质可以在球墨铸铁件内部形成孔洞或层,造成缺陷。
4、操作人员技术素养不足操作人员的技术素养也是产生缺陷的一个重要原因,如果操作人员缺乏技术素养,他们就不能熟练掌握工艺流程,也会导致生产过程中的缺陷。
二、防止球墨铸铁件缺陷的措施以上是球墨铸铁件缺陷的原因,那么如何防止缺陷产生呢?1、优化工艺参数设置在球墨铸铁件生产过程中,加强对工艺参数的监控,优化工艺参数设置,确保金属材料在加工上能满足一定的质量要求。
2、严格控制焊接工艺条件焊接是一项技术复杂的任务,因此我们应该在焊接工艺中严格控制各项工艺参数,确保球墨铸铁件能获得良好的焊接性能,从而防止缺陷的产生。
3、挑选优质金属材料在球墨铸铁件生产中,应该重视金属材料的质量,仅选用合格的金属材料,这样可以减少出现缺陷的概率。
4、提升操作人员技术素养提升操作人员的技术素养是防止球墨铸铁件缺陷的重要措施之一,建立科学的操作流程,以此来提高操作人员的技术水平,减少因技术不足而导致的缺陷。
球墨铸铁缺陷产生原因及应对措施
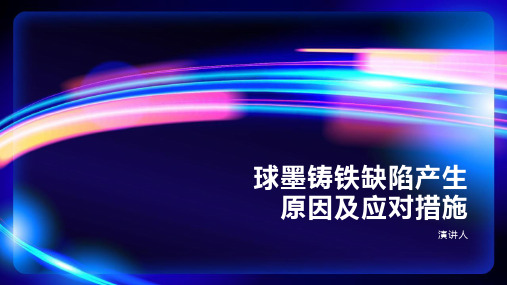
改进生产工艺
优化浇铸工艺:控 制浇铸温度、速度、
压力等参数,提高 1
铸件质量
加强质量控制:建 4
立完善的质量管理 体系,确保生产过
程符合标准要求
改进模具设计:优 化模具结构、尺寸、
2 材料等,提高铸件
成型精度
3
采用先进技术:如
快速凝固技术、电
磁搅拌技术等,提
高铸件性能
维护设备性能
01
定期检查设备,确保 其正常运行
设备维护不当:设备维护不及时,导致设备 性能下降,影响铸件质量
设备设计不合理:设备设计不合理,导致 生产过程中容易出现缺陷
球墨铸铁缺陷应对措 施
优化原材料选择
选择优质生 铁,降低杂
质含量
选用合适的 球化剂和孕 育剂,提高
球化效果
控制合金元 素含量,保 证化学成分
稳定
选用合适的 铸造工艺, 减少缺陷产
球墨铸铁缺陷产生 原因及应对措施
演讲人
目录
01. 球墨铸铁缺陷产生原因 02. 球墨铸铁缺陷应对措施 03. 球墨铸铁缺陷预防措施
球墨铸铁缺陷产生原 因
原材料质量
01 铁水成分:铁水中的碳、硅、锰等元素含 量对球墨铸铁的缺陷产生有很大影响
02 球化剂:球化剂的质量和加入量对球墨铸 铁的缺陷产生有很大影响
04
加强员工培训,提高员工的质量 意识和技能水平
定期检查设备
01
定期检查设备,确保设 备正常运行
02
定期更换磨损部件,避 免设备故障
03
定期清洁设备,保持设 备清洁
04
定期校准设备,确保设 备精度
05
定期培训员工,提高员 工操作技能
06
球墨铸铁件表面缺陷

球墨铸铁件表面缺陷清华大学于震宗引言球墨铸铁件的缺陷分为表面缺陷和内在缺陷两大类,后者即有关金属材质方面的缺陷,不属于本文范围内。
本文内容重点是砂型铸件的表面缺陷,包括用湿型砂、水玻璃砂、树脂砂等砂型和砂芯生产的铸件。
砂型球墨铸件的表面缺陷有多种,本文仅选择①粘砂,②砂孔和渣孔,③夹砂,④气孔,⑤胀砂、缩孔和缩松等缺陷进行讨论。
有的缺陷如灰班虽然发生在铸件表面上,而产生原因完全属于材质方面,则不包括在本文内:一. 球墨铸件气孔缺陷气孔是最难分析其形成原因和最难找出防治方法的铸件缺陷。
这是因为气孔的形成原因很多,从外观上又不易分清气孔是属于那种类型的。
虽然采用扫描电镜和能谱等微观分析方法有助于估计气孔的产生原因,但是这些先进的技术都还处于研究阶段,大多数铸造工厂尚难在生产中利用。
根据气孔发生机理,可分为裹入、侵入、析出和反应四类气孔。
其中裹入气孔是浇注时金属液中裹带着空气泡,随着液流进入型腔中而产生的气孔缺陷。
侵入气孔是铸件表面凝固成壳以前,砂型、砂芯等造型材料受热产生的气体侵入金属液中,形成气泡而产生的气孔球铁铸件最常遇到的气孔缺陷是反应气孔和析出气孔。
以下将分别讨论:1. 析出气孔金属液中溶解的原子态氢、氮气体元素,随金属温度下降而溶解度逐渐减小。
下降至结晶温度或凝固温度时,溶解度突然变小,氢、氮以分子态气相析出形成气泡,使铸件产生气孔,称为析出气孔。
生产铸铁的工厂中,最常见的析出气孔是使用树脂砂型和砂芯造成氨氮气孔,也有来自炉料和增碳剂的氮气孔。
①氨氮酚醛树脂覆膜砂的硬化剂为乌洛托平(六亚甲基四胺(CH2)6N4)。
铸铁件用热芯盒呋喃树脂含有尿素(CO(NH2)2)。
硬化剂用含有尿素和NH4Cl的水溶液。
冷芯盒和自硬砂用酚醛脲烷树脂的聚异氰酸酯组分中含有-RNCO基团。
上述树脂砂都含有多少不等的氨或胺,都是引起析出气孔的根源。
所含氮不同于空气中的氮,大气中78%是由氮组成,并不引起析出气孔缺陷。
铸铁件缺陷分析及对策
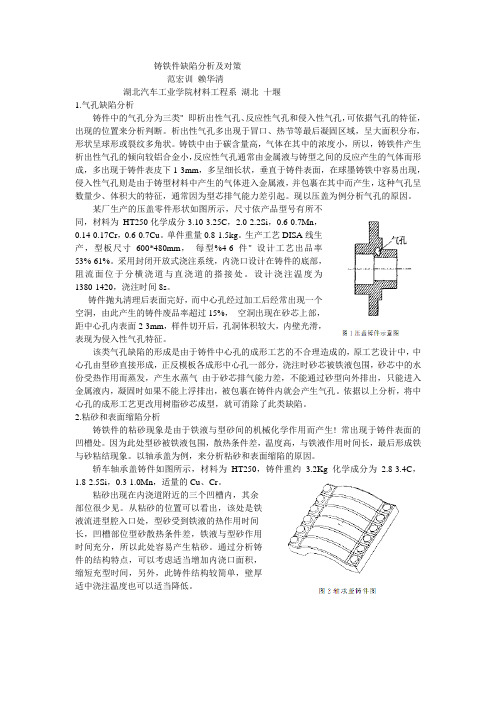
铸铁件缺陷分析及对策范宏训赖华清湖北汽车工业学院材料工程系湖北十堰1.气孔缺陷分析铸件中的气孔分为三类" 即析出性气孔、反应性气孔和侵入性气孔,可依据气孔的特征,出现的位置来分析判断。
析出性气孔多出现于冒口、热节等最后凝固区域,呈大面积分布,形状呈球形或裂纹多角状。
铸铁中由于碳含量高,气体在其中的浓度小,所以,铸铁件产生析出性气孔的倾向较铝合金小,反应性气孔通常由金属液与铸型之间的反应产生的气体而形成,多出现于铸件表皮下1-3mm,多呈细长状,垂直于铸件表面,在球墨铸铁中容易出现,侵入性气孔则是由于铸型材料中产生的气体进入金属液,并包裹在其中而产生,这种气孔呈数量少、体积大的特征,通常因为型芯排气能力差引起。
现以压盖为例分析气孔的原因。
某厂生产的压盖零件形状如图所示,尺寸依产品型号有所不同,材料为HT250化学成分3.10-3.25C,2.0-2.2Si,0.6-0.7Mn,0.14-0.17Cr,0.6-0.7Cu。
单件重量0.8-1.5kg。
生产工艺DISA线生产,型板尺寸600*480mm,每型%4-6件" 设计工艺出品率53%-61%。
采用封闭开放式浇注系统,内浇口设计在铸件的底部,阻流面位于分横浇道与直浇道的搭接处。
设计浇注温度为1380-1420,浇注时间8s。
铸件抛丸清理后表面完好,而中心孔经过加工后经常出现一个空洞,由此产生的铸件废品率超过15%,空洞出现在砂芯上部,距中心孔内表面2-3mm,样件切开后,孔洞体积较大,内壁光滑,表现为侵入性气孔特征。
该类气孔缺陷的形成是由于铸件中心孔的成形工艺的不合理造成的,原工艺设计中,中心孔由型砂直接形成,正反模板各成形中心孔一部分,浇注时砂芯被铁液包围,砂芯中的水份受热作用而蒸发,产生水蒸气由于砂芯排气能力差,不能通过砂型向外排出,只能进入金属液内,凝固时如果不能上浮排出,被包裹在铸件内就会产生气孔。
依据以上分析,将中心孔的成形工艺更改用树脂砂芯成型,就可消除了此类缺陷。
- 1、下载文档前请自行甄别文档内容的完整性,平台不提供额外的编辑、内容补充、找答案等附加服务。
- 2、"仅部分预览"的文档,不可在线预览部分如存在完整性等问题,可反馈申请退款(可完整预览的文档不适用该条件!)。
- 3、如文档侵犯您的权益,请联系客服反馈,我们会尽快为您处理(人工客服工作时间:9:00-18:30)。
球墨铸铁件常见缺陷的分析与对策一、常见的缺陷及分析球墨铸铁件常见缺陷的分析与对策 (1) 球铁是近40年来我国发展起来的重要铸造金属材料。
由于球状石墨造成的应力集中小,对基体的割裂作用也较小,故球铁的抗拉强度,塑性和韧性均高于其他铸铁。
与相应组织的钢相比,塑性低于钢,疲劳强度接近一般中碳钢,屈强比可达0 7~0 8,几乎是一般碳钢的2倍,而成本比钢低,因此其应用日趋广泛。
当然,球铁也不是十全十美的,它除了会产生一般的铸造缺陷外,还会产生一些特有的缺陷,如缩松、夹渣、皮下气孔、球化不良及衰退等。
这些缺陷影响铸件性能,使铸件废品率增高。
为了防止这些缺陷的发生,有必要对其进行分析,总结出各种影响因素,提出防止措施,才能有效降低缺陷的产生,提高铸件的力学性能及生产效益。
本文将讨论球铁件的主要常见缺陷:缩孔、缩松、夹渣、皮下气孔、石墨漂浮、球化不良及球化衰退。
1 缩孔缩松 1.1影响因素 (1)碳当量:提高碳量,增大了石墨化膨胀,可减少缩孔缩松。
此外,提高碳当量还可提高球铁的流动性,有利于补缩。
生产优质铸件的经验公式为C%+1/7Si%>3 9%。
但提高碳当量时,不应使铸件产生石墨漂浮等其他缺陷。
(2)磷:铁液中含磷量偏高,使凝固范围扩大,同时低熔点磷共晶在最后凝固时得不到补给,以及使铸件外壳变弱,因此有增大缩孔、缩松产生的倾向。
一般工厂控制含磷量小于0 08%。
(3)稀土和镁:稀土残余量过高会恶化石墨形状,降低球化率,因此稀土含量不宜太高。
而镁又是一个强烈稳定碳化物的元素,阻碍石墨化。
由此可见,残余镁量及残余稀土量会增加球铁的白口倾向,使石墨膨胀减小,故当它们的含量较高时,亦会增加缩孔、缩松倾向。
(4)壁厚:当铸件表面形成硬壳以后,内部的金属液温度越高,液态收缩就越大,则缩孔、缩松的容积不仅绝对值增加,其相对值也增加。
另外,若壁厚变化太突然,孤立的厚断面得不到补缩,使产生缩孔缩松倾向增大。
(5)温度:浇注温度高,有利于补缩,但太高会增加液态收缩量,对消除缩孔、缩松不利,所以应根据具体情况合理选择浇注温度,一般以1300~1350℃为宜。
(6)砂型的紧实度:若砂型的紧实度太低或不均匀,以致浇注后在金属静压力或膨胀力的作用下,产生型腔扩大的现象,致使原来的金属不够补缩而导致铸件产生缩孔缩松。
(7)浇冒口及冷铁:若浇注系统、冒口和冷铁设置不当,不能保证金属液顺序凝固;另外,冒口的数量、大小以及与铸件的连接当否,将影响冒口的补缩效果。
1.2 防止措施 (1)控制铁液成分:保持较高的碳当量(>3 9%);尽量降低磷含量(<0 08%);降低残留镁量(<0 07%);采用稀土镁合金来处理,稀土氧化物残余量控制在0 02%~0 04%。
(2)工艺设计要确保铸件在凝固中能从冒口不断地补充高温金属液,冒口的尺寸和数量要适当,力求做到顺序凝固。
(3)必要时采用冷铁与补贴来改变铸件的温度分布,以利于顺序凝固。
(4)浇注温度应在1300~1350℃,一包铁液的浇注时间不应超过25min,以免产生球化衰退。
(5)提高砂型的紧实度,一般不低于90;撞砂均匀,含水率不宜过高,保证铸型有足够的刚度。
2 夹渣 2 .1 影响因素 (1)硅:硅的氧化物也是夹渣的主要组成部分,因此尽可能降低含硅量。
(2)硫:铁液中的硫化物是球铁件形成夹渣缺陷的主要原因之一。
硫化物的熔点比铁液熔点低,在铁液凝固过程中,硫化物将从铁液中析出,增大了铁液的粘度,使铁液中的熔渣或金属氧化物等不易上浮。
因而铁液中硫含量太高时,铸件易产生夹渣。
球墨铸铁原铁液含硫量应控制在0 06%以下,当它在0 09%~0 135%时,铸铁夹渣缺陷会急剧增加。
(3)稀土和镁:近年来研究认为夹渣主要是由于镁、稀土等元素氧化而致,因此残余镁和稀土不应太高。
(4)浇注温度:浇注温度太低时,金属液内的金属氧化物等因金属液的粘度太高,不易上浮至表面而残留在金属液内;温度太高时,金属液表面的熔渣变得太稀薄,不易自液体表面去除,往往随金属液流入型内。
而实际生产中,浇注温度太低是引起夹渣的主要原因之一。
此外,浇注温度的选取还应考虑碳、硅含量的关系。
(5)浇注系统:浇注系统设计应合理,具有挡渣功能,使金属液能平稳地充填铸型,力求避免飞溅及紊流。
(6)型砂:若型砂表面粘附有多余的砂子或涂料,它们可与金属液中的氧化物合成熔渣,导致夹渣产生;砂型的紧实度不均匀,紧实度低的型壁表面容易被金属液侵蚀和形成低熔点的化合物,导致铸件产生夹渣。
2.2 防止措施 (1)控制铁液成分:尽量降低铁液中的含硫量(<0 06%),适量加入稀土合金(0 1%~0 2%)以净化铁液,尽可能降低含硅量和残镁量。
(2)熔炼工艺:要尽量提高金属液的出炉温度,适宜的镇静,以利于非金属夹杂物的上浮、聚集。
扒干净铁液表面的渣子,铁液表面应放覆盖剂(珍珠岩、草木灰等),防止铁液氧化。
选择合适的浇注温度,最好不低于1350℃。
(3)浇注系统要使铁液流动平稳,应设有集渣包和挡渣装置(如滤渣网等),避免直浇道冲砂。
(4)铸型紧实度应均匀,强度足够;合箱时应吹净铸型中的砂子。
3 石墨漂浮 3. 1 影响因素 (1)碳当量:碳当量过高,以致铁液在高温时就析出大量石墨。
由于石墨的密度比铁液小,在镁蒸汽的带动下,使石墨漂浮到铸件上部。
碳当量越高,石墨漂浮现象越严重。
应当指出,碳当量太高是产生石墨漂浮的主要原因,但不是唯一原因,铸件大小、壁厚也是影响石墨漂浮的重要因素。
(2)硅:在碳当量不变的条件下,适当降低含硅量,有助于降低产生石墨漂浮的倾向。
(3)稀土:稀土含量过少时,碳在铁液中的溶解度会降低,铁液将析出大量石墨,加重石墨漂浮。
(4)球化温度与孕育温度:为了提高镁及稀土元素的吸收率,国内试验研究表明,球化处理时最适当的铁液温度是1380~1450℃。
在此温度区间,随着温度升高,镁和稀土的吸收率增加。
(5)浇注温度:一般情况下,浇注温度越高,出现石墨漂浮的倾向越大,这是因为铸件长时间处于液态有利于石墨的析出。
A.P.Druschitz与W.W.Chaput研究发现,若缩短凝固时间,随着浇注温度升高,石墨漂浮倾向降低。
(6)滞留时间:孕育处理后至浇注完毕之间的停留时间太长,为石墨的析出提供了条件,一般这段时间应控制在10min以内。
球墨铸铁件常见缺陷的分析与对策 (2) 3 2 防止措施 (1)控制铁液成分:严格控制碳当量,不得大于4 6%;铁液的含碳量不得大于4 0%,可用废钢来调整铁液的含碳量;采用低硅(<1 2%)生铁;改进孕育处理,增强孕育效果,这样可降低孕育硅铁量。
(2)控制稀土的加入量:在保证球化的前提下,加入量要少。
(3)改进铸件的结构,使壁厚尽量均匀,且小于60mm;若壁厚相差很大、热节很大,可在厚壁或者热节处加放冷铁;若是热节或厚壁位置在铸件顶部,可在此处加冒口。
(4)严格控制温度:通常要求在1380~1450℃进行球化处理,1360~1400℃进行浇注。
同时,尽量缩短铁液出炉到浇注之间的滞留时间。
(5)必要情况下,可以加入钼等反石墨化元素,提高碳在铁液中的溶解度,从而减少石墨析出。
4 皮下气孔 4. 1 影响因素 (1)碳当量:适当增加含硅量有助于皮下气孔的减少。
同时,在硅量保持不变的情况下,随着含碳量的增加,球铁中皮下气孔的个数呈现出单峰曲线,且峰值点总保持在共晶点左右,因此,最好将碳硅含量选择得高一些,以使球铁的碳当量稍大于共晶点。
(2)硫:硫高会引起皮下气孔等缺陷,这是因为产生H2S气体而形成。
当含硫量超过0 .094%时就会产生皮下气孔,含硫量越高,情况越严重。
(3)稀土:铁液中加入稀土元素能脱氧、脱硫,提高铁液表面张力,因此有利于防止产生皮下气孔。
但稀土含量太高,会增加铁液中氧化物的含量,使气泡外来核心增加,皮下气孔率增加。
残余稀土量应控制在0. 043%以下。
(4)镁:过高的镁将会加剧铁液的吸氢倾向,大量的镁气泡和氧化物进入型腔,增加气泡的外来核心;此外镁蒸汽直接与砂型中的水分作用,产生MgO烟气及氢气,也会产生皮下气孔。
试验表明,残镁量大于0 .05%后便易出现皮下气孔,残镁越高越严重。
因此在保证球化基础上,尽量降低残留镁量。
(5)铝:铁液中的铝是铸件产生氢气孔的主要原因。
据报道,当湿型铸造球墨铸铁的残留铝量为 0.030%~0 .050%时,将产生皮下气孔。
E.R.Kaczmarek等人研究认为,铁液与铸型中的水反应生成FeO与H2,由于铝的脱氧作用,又生成Al2O3,其即为气泡生成的核心而又能吸附一定的气体,增加了球铁产生皮下气孔的倾向。
但是在减少渣中的FeO成分时,镁的存在使得铝显得多余,故铝的敏感含量是有一定范围的。
(6)壁厚:皮下气孔还有“壁厚效应”特征,即气孔的产生在一定壁厚范围内,实际上这与铸件的凝固速度有关。
铸件壁厚大时,其凝固结皮时间推迟,有利于气泡逸出。
因此,一般来说壁厚小于6mm或大于25mm时不易产生皮下气孔。
(7)浇注温度:浇注温度类似于壁厚效应,也有一个温度范围,在1285~1304℃时,皮下气孔相当严重。
笔者进一步研究认为,不同的壁厚其危险温度也不相同,因此,应根据铸件壁厚共同确定浇注温度。
当然,提高浇注温度能延缓氧化膜的生成,防止熔渣进入型腔,同时对砂型烘烤时间加长使水分向外迁移。
(8)型砂含水率:铸型产生皮下气孔的倾向按下列顺序依次减小:湿型、干型、水玻璃型、壳型。
司乃潮的研究也证明了这一点,即随着型砂水分的提高,球铁产生皮下气孔的倾向增大,而当型砂水分小于4 .8%时,皮下气孔率接近于零。
(9)型砂紧实度与透气性:型砂的透气性太低,导致型壁所产生的气体不能排出型外,而向金属侵入,致使铸件产生气孔;随着型砂紧实度的增加,皮下气孔的倾向也加大,但当紧实度相当高时,倾向又减小,这可能是由于表层砂紧实度高,增大了水分向铸件方向的迁移阻力,但若型砂水分也高,将使水蒸气爆炸的可能性增加。
(10)浇冒口:合理设计浇冒口,使铁液平稳浇注,并具有较强的挡渣功能;同时,适当增加直浇道和冒口的高度,以增加金属液的静压力。
4 2 防止措施 (1)严格控制铁液化学成分,使碳当量稍大于共晶点成分,含硫量不大于0 .094%;残余稀土小于0.043%;残留镁含量不大于0.05%;铝含量在0.03%~0.05%范围以外。
(2)合理设计铸件结构,使壁厚不小于25mm;根据壁厚确定浇注温度,薄壁小件不得小于1320℃;中件不得小于1300℃;大件不得小于1280℃。
(3)金属炉料、孕育剂和所用工具应干燥,表面无锈蚀和油污。
同时型砂水分不宜过高,尽量小于4.8%,煤粉、重油等发气物质的含量要适当控制,减少粘土含量,并可附加一些增加透气性的物质,如木屑等。