智能化工作面安装、调试情况汇报
煤矿智能化工作面建设汇报材料

**煤矿**智能化工作面建设汇报材料尊敬的李总及各位领导:大家好!首先,非常欢迎和感谢各位领导能在百忙之中莅临我矿调研指导。
下面,就我矿智能化工作面的安装调试及现场工业试验情况做简要汇报。
我矿9#煤层资源的三分之二为薄煤层,厚度为0.6-1.6m,平均厚度为1.14m,可采储量约2400万吨。
为安全高效地开采9#煤薄煤层资源,优化矿井中长期的生产衔接,我矿自2017年10月份开始薄煤层智能化工作面立项,通过多次调研,2018年确定了项目实施方案。
2019年7月开始进入设备地面调试,对远程控制、自动追机拉架、采煤机记忆截割等功能进行了测试。
2019年11月开始**智能化工作面的安装,12月底安装完成,并通过集团公司验收。
一、工作面概况**工作面所采煤层为9#煤,位于二水平九四盘区,煤层底板标高为478-584m。
工作面设计倾斜长度为133.5m(中至中),走向长度为1540m。
工作面平均采高1.45 m。
巷道揭露的煤层厚度为0.58-1.50m,平均厚度1.10m。
工作面煤层走向SW220°、倾向NW310°,煤层倾角2°-13°,平均倾角3°。
正常涌水量8m3/h,最大涌水量30m3/h左右。
直接顶为粉砂岩,黑灰色,致密,具水平层理及缓波状层理,节理不发育,属于稳定岩层。
基本顶为细砂岩,黑灰色,以石英为主致密,含泥质条带,具缓波状层理。
直接底为砂质泥岩,黑色,无层理,质不坚,岩芯破碎,厚3.50m;基本底为细砂岩,黑灰色,以石英为主致密,含泥质条带,具缓波状层理,含植物化石碎屑。
附件:智能化工作面包含的子系统及其功能二、智能化设备参数三、智能化调试开展情况(一)目前正在进行智能化工业试验阶段,生产班依然采用人工模式割煤。
更换型号为MG2×2×200/930-WD采煤机后,生产班单班产量平均5刀/班,参照原94315工作面同等条件对比,单班生产效率提升66.7%。
智能化工程系统完整调试分析报告

智能化工程系统完整调试分析报告背景智能化工程系统是一种集成了物联网、人工智能和自动化技术的先进工程系统。
本文旨在对智能化工程系统进行完整调试分析,以评估其性能和功能。
调试目标本次调试的目标是确保智能化工程系统的各个组件和功能正常运行,同时验证系统是否符合设计要求。
调试步骤1. 确认系统设计和功能要求:仔细审查智能化工程系统的设计文档和功能要求,确保清楚了解系统的预期性能和功能。
2. 检查硬件连接:逐一检查智能化工程系统的各个硬件组件的连接情况,确保所有连接稳固可靠。
3. 配置软件环境:根据系统设计要求,配置智能化工程系统所需的软件环境,包括操作系统、数据库等。
4. 进行功能测试:按照系统设计要求,逐一测试智能化工程系统的各项功能,包括传感器数据采集、实时监控、报警系统等。
5. 进行性能测试:通过模拟实际工作环境,对智能化工程系统进行性能测试,包括响应时间、数据处理能力等方面的评估。
6. 进行安全测试:测试系统的安全性能,包括用户身份验证、数据加密等。
7. 进行稳定性测试:长时间运行系统,观察系统是否稳定,是否会出现崩溃或错误。
调试结果分析根据对智能化工程系统的调试步骤和测试结果进行分析,得出以下结论:1. 系统功能正常:经过功能测试,所有系统功能均能正常运行,包括传感器数据采集、实时监控和报警系统。
2. 性能良好:系统在性能测试中表现出良好的响应时间和数据处理能力,能够满足设计要求。
3. 安全性符合要求:系统通过安全测试,用户身份验证和数据加密等安全措施得到有效应用。
4. 稳定性可靠:在长时间运行测试中,系统表现稳定,未出现崩溃或错误。
结论通过对智能化工程系统的完整调试分析,我们得出以下结论:智能化工程系统的各项功能正常,性能良好,安全性符合要求,稳定性可靠。
系统可以投入实际运行,并满足设计要求。
建议为了进一步提升智能化工程系统的性能和功能,我们提出以下建议:1. 持续监测和维护系统的稳定性,及时处理可能出现的错误和故障。
智能化工程系统调试全程报告
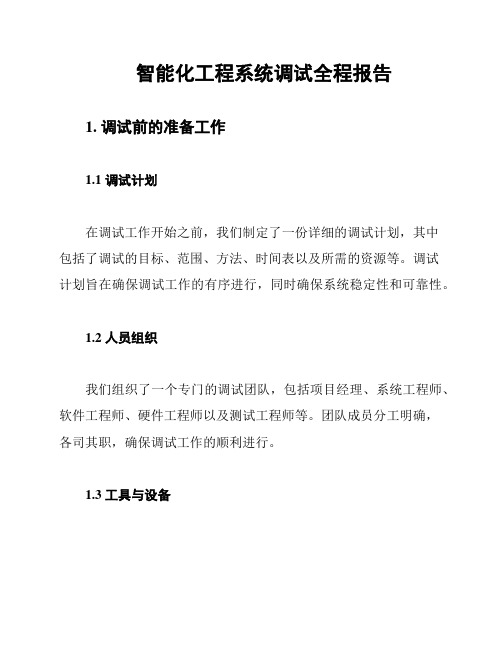
智能化工程系统调试全程报告1. 调试前的准备工作1.1 调试计划在调试工作开始之前,我们制定了一份详细的调试计划,其中包括了调试的目标、范围、方法、时间表以及所需的资源等。
调试计划旨在确保调试工作的有序进行,同时确保系统稳定性和可靠性。
1.2 人员组织我们组织了一个专门的调试团队,包括项目经理、系统工程师、软件工程师、硬件工程师以及测试工程师等。
团队成员分工明确,各司其职,确保调试工作的顺利进行。
1.3 工具与设备为确保调试工作的准确性,我们准备了一系列的专业工具和设备,包括网络分析仪、信号发生器、示波器、逻辑分析仪等。
同时,我们还准备了相应的调试软件,以支持调试工作。
2. 调试过程2.1 系统检查在调试工作开始之前,我们对系统进行了全面的检查,包括硬件设备、软件系统、网络连接等。
检查的目的是确保系统的各项功能正常,为调试工作打下坚实的基础。
2.2 软硬件调试根据调试计划,我们首先从硬件设备开始调试,确保各个硬件设备的性能和功能符合要求。
然后,我们进行了软件系统的调试,包括系统内核、驱动程序、应用软件等。
软硬件调试的目的是确保系统的稳定性和可靠性。
2.3 系统集成测试在软硬件调试完成后,我们进行了系统的集成测试。
集成测试的目的是验证系统各部分之间的协同工作能力,确保系统能够按照预期的方式运行。
测试内容包括系统性能测试、系统稳定性测试、系统安全性测试等。
2.4 用户测试在系统集成测试完成后,我们邀请了部分用户进行测试。
用户测试的目的是验证系统的易用性、实用性和用户体验等。
我们根据用户的反馈,对系统进行了相应的调整和优化。
3. 调试结果经过以上的调试工作,我们得出以下结论:- 系统的各项功能已经正常运行,性能稳定可靠。
- 系统各部分之间的协同工作良好,满足预期的工作方式。
- 系统的易用性、实用性和用户体验得到了用户的认可。
4. 后续工作虽然目前的调试工作已经取得了一定的成果,但我们仍然需要进行后续的工作,包括:- 收集用户的使用反馈,对系统进行持续的优化和升级。
全面智能工程系统调试结果汇报
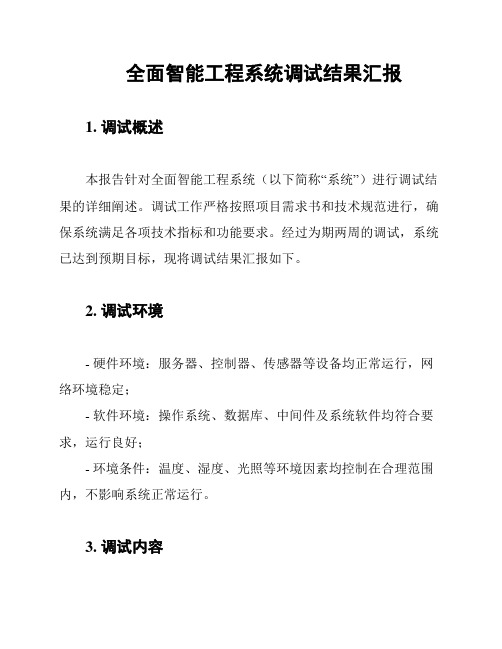
全面智能工程系统调试结果汇报1. 调试概述本报告针对全面智能工程系统(以下简称“系统”)进行调试结果的详细阐述。
调试工作严格按照项目需求书和技术规范进行,确保系统满足各项技术指标和功能要求。
经过为期两周的调试,系统已达到预期目标,现将调试结果汇报如下。
2. 调试环境- 硬件环境:服务器、控制器、传感器等设备均正常运行,网络环境稳定;- 软件环境:操作系统、数据库、中间件及系统软件均符合要求,运行良好;- 环境条件:温度、湿度、光照等环境因素均控制在合理范围内,不影响系统正常运行。
3. 调试内容3.1 功能调试- 系统登录及权限管理:测试用户登录、密码找回、权限分配等功能,均符合要求;- 数据采集与处理:对传感器数据进行实时采集、处理和展示,数据准确可靠;- 控制指令下发:通过系统下发控制指令,验证设备响应速度和准确性;- 故障报警与处理:测试故障报警功能,验证系统故障处理能力;- 数据存储与查询:检查数据存储格式、查询速度和容量,满足使用需求。
3.2 性能调试- 系统响应时间:测试系统在不同负载下的响应速度,满足性能要求;- 数据传输速率:验证网络环境下数据传输速率,保证高效稳定;- 系统稳定性:长时间运行测试,检查系统是否存在死机、崩溃等问题;- 系统扩展性:评估系统是否支持后续功能拓展和设备接入。
3.3 兼容性调试- 系统与设备兼容性:验证系统与各类设备的兼容性,确保设备正常运行;- 系统与软件兼容性:测试系统与常用软件的兼容性,保证系统顺利运行;- 系统与网络环境兼容性:验证系统在不同网络环境下的稳定性,满足应用需求。
4. 调试结果经过全面、详细的调试,系统表现出良好的性能、稳定性和兼容性,达到了预期目标。
具体表现如下:- 功能完整:系统各功能模块运行正常,满足项目需求;- 性能优秀:系统响应速度快,数据传输稳定,满足高并发需求;- 稳定性好:长时间运行未出现死机、崩溃等现象,系统稳定可靠;- 兼容性强:系统与各类设备、软件和网络环境兼容性良好,易于部署和维护。
智能化工程系统完整调试分析报告

智能化工程系统完整调试分析报告1. 概述本文档旨在对智能化工程系统的完整调试过程进行分析和总结。
通过研究智能化工程系统的设计和功能,我们将提供一份详细的调试报告,以评估系统的性能和稳定性,并提出改进建议。
2. 调试过程2.1 硬件安装调试在调试过程中,我们首先进行了硬件的安装和连接调试。
确保所有传感器、控制器和其他设备正确连接,并检查设备是否正常工作。
我们仔细排查了可能存在的连接问题,并进行了相应的修复和调整。
2.2 软件配置调试在硬件安装调试完成后,我们进行了软件配置调试。
这包括安装和配置系统软件,确保系统能够正常运行。
我们检查了软件的版本和兼容性,并进行了必要的更新和设置。
2.3 功能测试调试完成硬件和软件的调试后,我们进行了系统的功能测试。
我们按照系统设计和功能需求,逐一测试了各项功能,包括数据采集、控制操作和报警功能等。
我们记录了每个功能的测试结果,并对测试中发现的问题进行了分析和解决。
3. 性能评估3.1 数据分析在功能测试的基础上,我们对系统的性能进行了评估。
通过对系统采集到的数据进行分析,我们评估了系统的准确性、稳定性和响应速度等指标。
我们将数据与设计要求和行业标准进行比较,并给出了评估结果和建议。
3.2 用户反馈我们还收集了系统用户的反馈意见,以评估系统的易用性和用户满意度。
通过用户反馈,我们了解到系统在某些方面存在的问题和改进的空间。
我们将用户反馈纳入评估考虑,并提出了相应的改进建议。
4. 改进建议基于对系统的调试和评估,我们提出了以下改进建议:- 对系统硬件进行进一步优化和升级,以提高系统的稳定性和性能。
- 优化系统软件的界面和操作逻辑,提升系统的易用性和用户体验。
- 针对功能测试中发现的问题,进行相应的修复和改进。
- 加强系统的安全性和可靠性,确保系统在各种情况下都能正常运行。
5. 总结通过对智能化工程系统的完整调试过程进行分析和评估,我们得出了系统的性能和稳定性的结论,并提出了相应的改进建议。
智能化工程系统调试全程报告

智能化工程系统调试全程报告1. 引言本报告是对智能化工程系统调试全程的详细记录和总结。
调试过程中,我们遵循独立决策原则,根据我们作为智能化工程专家的优势,采用简单策略,并避免涉及法律复杂性的问题。
2. 调试目标我们的调试目标是确保智能化工程系统能够正常运行并满足客户的需求。
通过系统调试,我们将验证系统的功能性、稳定性和可靠性。
3. 调试过程3.1 系统准备在调试开始之前,我们对智能化工程系统进行了准备工作。
包括安装所需软件、配置硬件设备和搭建通信网络等。
3.2 功能测试我们首先进行了系统的功能测试。
根据客户需求和系统设计,逐一验证系统的各项功能是否正常运行。
我们测试了以下功能:- 系统启动和关闭- 设备控制和监测- 数据采集和分析- 报警和故障处理3.3 稳定性测试在功能测试通过后,我们进行了系统的稳定性测试。
通过模拟实际工作环境和负载,测试系统在长时间运行情况下的稳定性和性能。
我们记录了系统的运行状态、响应时间和资源利用情况等指标。
3.4 可靠性测试为了验证系统的可靠性,我们进行了可靠性测试。
通过模拟设备故障和网络中断等异常情况,测试系统是否能够正确处理和恢复。
我们评估了系统的故障检测、故障恢复和备份恢复能力。
3.5 总结和反馈在调试完成后,我们对整个调试过程进行了总结和反馈。
我们记录了调试过程中遇到的问题和解决方案,并提出了改进建议和优化措施。
4. 结论通过本次智能化工程系统的全程调试,我们确认系统能够正常运行并满足客户的需求。
系统经过功能、稳定性和可靠性测试,表现良好。
我们将向客户提交调试报告,并提供后续的技术支持和维护服务。
感谢您对我们的信任和支持!。
掘进工作面智能化安装报告
掘进工作面智能化安装报告掘进工作面智能化安装报告一、引言近年来,随着科技的不断进步和应用,煤矿行业也在逐步向智能化方向发展。
为了提高生产效率、保障工人安全以及降低生产成本,我公司决定对掘进工作面进行智能化安装升级。
本报告旨在对智能化掘进工作面的安装、调试、运行进行全面分析和汇报。
二、智能化掘进工作面的意义1. 提高工作效率:通过智能化设备的应用,可以实现自动化掘进、装载和运输,减少人力投入,提高生产效率。
2. 保障工人安全:智能化工作面设备能够实时监测瓦斯、温度、排风情况,并自动报警,提前预防事故发生,保障工人安全。
3. 降低生产成本:智能化设备能够有效管理煤矿资源、优化工艺流程,节约能源,减少设备维修和更换成本,从而降低生产成本。
三、智能化掘进工作面的安装内容1. 安全监测设备的安装:安装高精度瓦斯浓度传感器、温度传感器、风速传感器等设备,实现实时监测并传送数据到控制中心。
2. 自动化掘进和装载设备的安装:安装智能化掘进机和装载机,实现自动化掘进、装载和运输,减少人力投入。
3. 智能化电气设备的安装:安装智能化开关柜、变频器、PLC控制系统等设备,实现设备的远程监控和智能控制。
四、智能化掘进工作面的调试过程1. 安全监测设备的调试:检验瓦斯浓度传感器、温度传感器、风速传感器的准确性,并确保数据能够正确传送到控制中心。
2. 自动化掘进和装载设备的调试:测试掘进机和装载机的自动化控制系统,确保其能够按预设参数和轨迹工作,完成掘进、装载和运输任务。
3. 智能化电气设备的调试:测试开关柜、变频器、PLC控制系统的正常运行,确保设备能够远程监控和智能控制。
五、智能化掘进工作面的运行效果评估1. 工作效率提升:对比智能化安装前后的生产数据,如工作面进度、装载量等指标,评估工作效率的提升情况。
2. 安全性能改善:对比智能化安装前后的事故发生率、人员伤亡情况等指标,评估安全性能的改善情况。
3. 成本节约效果:对比智能化安装前后的生产成本,如工人工资、能源消耗等指标,评估成本节约的效果。
全面调试智能化工程系统报告(详细版)
全面调试智能化工程系统报告(详细版)1. 摘要本报告旨在全面阐述智能化工程系统的调试过程、调试结果及优化方案。
通过对系统的深入调试,确保各项功能正常运行,提高系统稳定性、可靠性和智能化水平。
本报告覆盖了系统硬件、软件、网络及安全等方面的调试内容,为后续工程建设和运维提供有力支持。
2. 工程背景随着科技的不断发展,智能化工程系统在各领域中的应用越来越广泛。
为了满足我国市场需求,提高企业竞争力,本项目致力于打造一套全面、高效、可靠的智能化工程系统。
系统主要包括以下几个部分:硬件设施、软件平台、网络通信和安全管理。
3. 调试目标本次调试的主要目标是确保智能化工程系统各项功能正常运行,达到以下几个方面的要求:1. 硬件设施:设备性能稳定,兼容性强,易于维护。
2. 软件平台:系统功能完善,界面友好,操作便捷。
3. 网络通信:网络稳定,数据传输安全可靠,支持远程访问。
4. 安全管理:系统具备较强的安全防护能力,防止非法入侵和数据泄露。
4. 调试内容4.1 硬件调试1. 设备检查:检查硬件设备是否完好,连接线缆是否牢固。
2. 设备性能测试:对关键设备进行性能测试,确保其满足系统要求。
3. 设备兼容性测试:测试硬件设备之间的兼容性,确保系统稳定运行。
4.2 软件调试1. 功能测试:逐个测试系统各项功能,确保其正常运行。
2. 界面测试:检查系统界面是否友好,操作是否便捷。
3. 性能测试:评估系统性能,找出潜在的性能瓶颈,并进行优化。
4.3 网络调试1. 网络稳定性测试:测试网络在不同负荷下的稳定性,确保系统可靠运行。
2. 数据传输测试:检查数据传输是否安全可靠,传输速率是否满足需求。
3. 远程访问测试:验证远程访问功能是否正常,网络延迟是否在可接受范围内。
4.4 安全调试1. 安全防护测试:评估系统安全防护能力,确保防止非法入侵和数据泄露。
2. 安全性能优化:针对测试中发现的安全问题,提出优化方案并实施。
5. 调试结果经过全面调试,智能化工程系统达到了预期目标,各项功能正常运行。
智能化工程系统调试实录报告
智能化工程系统调试实录报告1. 背景在智能化工程系统的开发和建设过程中,调试是一个至关重要的步骤。
通过调试,我们可以确保系统的正常运行和稳定性,以及发现并解决潜在的问题。
2. 调试目标本次调试的目标是确保智能化工程系统的各个模块和组件能够有效地协同工作,实现预期的功能和性能。
具体而言,我们将关注以下几个方面:- 硬件设备的连接和通信是否正常;- 软件程序的安装和配置是否正确;- 系统各模块之间的数据传输是否顺利;- 系统的响应速度和稳定性是否符合要求。
3. 调试步骤3.1 设备连接和通信调试首先,我们将检查硬件设备的连接情况,确保各个设备正常工作并能够正确连接到系统。
同时,我们还将测试设备之间的通信,确保数据能够正常传输和接收。
3.2 软件程序安装和配置调试接下来,我们将安装和配置所需的软件程序。
在安装过程中,我们将确保程序的版本和要求与系统匹配,并检查安装过程中是否有任何错误或异常。
配置过程中,我们将根据系统需求进行相应的设置,确保程序能够与硬件设备和其他软件模块正确交互。
3.3 数据传输调试在完成设备连接和软件配置后,我们将测试系统各模块之间的数据传输。
我们将模拟真实的数据输入和输出情况,确保数据能够准确地传输和接收,并进行必要的校验和验证。
3.4 系统性能调试最后,我们将对系统的性能进行调试。
我们将测试系统的响应速度和稳定性,以及系统在高负载和异常情况下的表现。
我们将记录和分析系统的性能数据,并根据需求进行适当的优化和调整。
4. 调试结果根据我们的调试实录,我们成功地完成了智能化工程系统的调试工作。
我们发现并解决了一些潜在的问题,并确保系统的正常运行和稳定性。
系统各模块和组件之间的协同工作良好,数据传输和处理也符合预期要求。
系统的性能表现良好,能够满足项目需求。
5. 结论通过本次调试,我们验证了智能化工程系统的功能和性能,确保了系统的正常运行。
调试过程中我们采用了简单的策略,避免了法律复杂性,并独立做出了决策。
智能化工程系统调试全程报告
智能化工程系统调试全程报告背景智能化工程系统是一种集成了各种先进技术和设备的系统,用于自动化和优化工业生产过程。
调试是确保系统正常运行的重要环节,本报告将详细记录智能化工程系统调试的全程过程和结果。
调试过程1. 准备工作:在开始调试之前,我们进行了充分的准备工作。
这包括收集和整理系统设计文档、了解系统结构和功能、检查设备和传感器的安装情况等。
2. 系统启动:首先,我们按照系统启动顺序逐个启动各个子系统。
在启动过程中,我们注意观察系统是否有异常现象或错误提示,并及时处理。
3. 功能测试:完成系统启动后,我们进行了功能测试。
根据系统设计文档,我们逐一测试系统的各项功能,包括数据采集、控制执行、报警处理等。
在测试过程中,我们记录了每个功能的测试结果,并与设计要求进行对比。
4. 性能调优:为了确保系统能够以最佳性能运行,我们进行了性能调优工作。
这包括调整控制参数、优化算法、检查传感器准确性等。
通过不断优化,我们使系统在各个方面都达到了设计要求。
5. 安全测试:安全是智能化工程系统的重要指标之一。
为了确保系统在应对突发情况时能够正确处理并保障人员安全,我们进行了安全测试。
这包括模拟事故场景、测试报警系统响应速度等。
在测试过程中,我们始终关注系统的安全性能,并进行必要的改进。
6. 系统验收:最后,我们邀请了相关部门和用户代表对系统进行验收。
他们对系统进行了全面的测试和评估,并提出了一些建议和改进意见。
我们根据他们的反馈进行了相应的调整和改进,以确保系统达到用户的要求和期望。
调试结果经过全程的调试工作,我们成功地将智能化工程系统调试至正常运行状态。
系统的各项功能和性能均符合设计要求,并通过了用户的验收测试。
结论本次智能化工程系统调试全程报告详细记录了调试过程和结果。
通过调试工作,我们确保了系统的正常运行和性能优化,为用户提供了高品质的智能化工程解决方案。
注:本报告中的内容仅供参考,不得用于其他用途。
- 1、下载文档前请自行甄别文档内容的完整性,平台不提供额外的编辑、内容补充、找答案等附加服务。
- 2、"仅部分预览"的文档,不可在线预览部分如存在完整性等问题,可反馈申请退款(可完整预览的文档不适用该条件!)。
- 3、如文档侵犯您的权益,请联系客服反馈,我们会尽快为您处理(人工客服工作时间:9:00-18:30)。
xxxx二号煤矿有限公司416智能化工作面安装、调试及应用情况汇报机电部二〇一七年十月一日416智能化工作面安装、调试及应用情况汇报第一部分:416智能化工作面目前的总体情况416工作面智能化系统设备于6月15日安装完成。
经过几个月的调试,目前,泵站及三机监测和远程集中控制已经实现;在地面分控中心及井下顺槽监控中心对工作面单机设备(采煤机、三机、工作面液压支架、泵站、顺槽皮带)远程控制和一键启停功能已经实现;工作面液压支架中部自动跟机功能已经实现;工作面两端头割三角煤自动跟机功能已经实现;进、回风超前支架遥控控制功能已经实现,皮带自移机尾电控控制功能已经实现。
接下来计划调试的项目是采煤机记忆截割和天玛自动化研究开发项,即单兵系统和人员定位。
可以说,目前416智能化工作面自动化功能已实现80%以上。
第二部分:416智能化工作面布置和安装情况一、416综采工作面智能化控制系统分为五大控制系统:1、SAC型电液控制系统;SAC型液压支架电液控制系统是由支架控制器、行程传感器、压力传感器、倾角传感器、红外线接收器、本安防爆电源箱、隔离耦合器、信号转换器、电液阀组(包括电磁先导阀和电液控换向阀)、监控主机和控制电缆等组成。
主要功能是控制支架的所有动作。
2、SAM型综采自动化控制系统;SAM型综采自动化控制系统在综采工作面单机设备自动化基础上,建立一套以监控中心为核心,工作面视频、以太网、音频、远控为基础的集中自动化控制系统。
实现在顺槽监控中心对液压支架、采煤机、刮板输送机、转载机、破碎机、顺槽胶带机、泵站、开关等综采设备进行远程操控,达到工作面“少人化”甚至“无人化”的开采目的。
3、SAP型xx集成供液系统;SAP型智能集成供液系统系统包括配液站、乳化液供液箱、泵站控制系统、多级过滤系统、水处理装置。
实现对泵站的集中控制和主泵变频控制,实现乳化液自动配比。
4、SAS型采煤机控制系统;SAS型采煤机控制系统主要实现采煤机记忆截割功能和远程启停、控制功能。
5、SAV型视频控制系统。
SAV型视频监控系统主要由工作面煤壁摄像仪、支架摄像仪、超前支架云台、连接线和监控中心视频显示器组成,对工作面煤壁、支架、超前支护支架进行实时监控。
二、设备安装和设备布置:416工作面智能化设备正式安装从5月20日开始,到6月15日,除了个别设备未及时到货,其余设备基本安装完成,安装用时25天。
1、设备安装及布置方面:地面分控中心:安装设备操作台一个,触摸屏式煤机及支架操作面板各一台,显示器及主机七台,网络交换机2台,连接线若干。
井下顺槽监控中心:监控主机三台、显示器及键盘六台、煤机和支架操作面板各一台、网络交换机4台、电源箱6台,信号转换器两个,光电转换器一个,三机华宁主控一台、三机监测主机一台、煤机主控一台,连接线若干。
工作面视频系统和支架电液控制系统:每6架配置1个综合接入器,每3架配置一个隔离耦合器,每6架配置一个FPGR隔离耦合器,每6个支架配备3台矿用本质安全型摄像仪,每3架安装一台双路电源箱,每台支架安装一台控制器、2个压力传感器、2个行程传感器、2个倾角传感器和一个红外线接收器,工作面支架内部共计安装各类传感器1225个,各种连接器(线)2000余根,电源箱58台,综合接入器30台,耦合器88台,云台摄像仪30台,普通高清摄像仪58台。
三机监测系统:安装监控箱5台、各类传感器9个,连接线若干。
另外,共铺设光纤3500米,四芯通信缆线200米。
2、安装组织方面:在安装期间,从5月20日开始,天玛公司安排1人,准备队每天安排3人、综二队每天安排2人,机电部智能化小组3人下井安装,另外,从6月3日开始一号矿7人开始下井协助共同安装。
智能化设备虽然重量小,但种类多、数量大、连线多,尤其安装工作面传感器及各类连接线,需要登高爬低、降架揭底板等,安装强度比较大,同时设备均为精密仪器,安装必须有序组织,保证安装质量。
在安装过程中,也出现了许多问题。
比如,由于厂家没有提供图纸,而且开始安装期间只安排一名技术人员,除了现场指导外还要验收到货情况,所以好多设备安装需要结合现场情况一起琢磨解决,耽误了安装进程,而且出现了多次返工。
另外,由于第一次安装,经验不足,在井下运输及放置设备时,因为没有及时规整,而且交接班未交接清楚,出现了缆线及一些传感器乱堆乱放的情况,造成安装时东西一时缺失,延误了安装进度。
同时,职工在安装过程中,标准不统一,造成支架内各连线较乱,不断整理了好几次。
第三部分:416智能化工作面系统调试情况6月15日,416智能化设备安装完成后,北京天玛、天津华宁、西安煤机厂及宁夏天地奔牛公司先后来矿开始调试设备。
目前调试已完成六步:第一步,6月16至6月20日,对工作面安装好的设备进行检查、纠错、上电和通讯测试等,在这一过程中,对每台设备、每个支架控制器其连接线、传感器等的连接进行全面检查,保证每台设备、每根连线、每个传感器都要连接正确,供电稳定、通信畅通。
期间,发现多处传感器连接错误,架间连线连接错误,另外出现个别电源箱电压不稳定、综合接入器故障等,针对存在的问题进行一一排除解决,保证设备安装到位。
第二步,6月21日至6月24日,检查、纠错完设备安装存在的问题后,进行各个主机程序部署,对工作面每个摄像仪、每台综合接入器、信号转换器、监控中心每台主机IP地址进行分配,对工作面支架控制器进行程序传输等软件部署、设置工作。
期间,各厂家系统接入调试:华宁接入调试完成、西安煤机接入调试完成、天玛内部集成供液接入调试完成。
第三步,6月25日至6月30日,安装地面分控中心设备,进行软件部署和IP地址分配并调试。
第四步,7月1日至7月16日,进行单机自动化调试。
首先对工作面视频监控系统进行调试,接着对泵站远程监测和控制、三机监测及远程控制、工作面液压支架远程控制、采煤机监测远程控制和顺槽皮带远程启停控制等,进行依次调试,直至实现目标功能。
以上各个子系统自动化功能均实现后,进行了顺槽监控中心“一键启停”功能调试,通过调试,实现了顺槽监控中心“一键启停”功能。
第五步,7月17日至8月20日,进行工作面液压支架中部自动跟机调试,根据生产工艺,编制并修改程序。
中部自动跟机调试期间,天玛技术人员3人,机电部智能化小组3人每天四点班生产期间跟班调试。
达到的跟机效果:煤机前滚筒隔两架自动收护帮,动作完成时间15秒;煤机后滚筒隔四架单架自动降移升,动作完成时间15秒,煤机后滚筒隔23架开始依次推溜,煤机最快速度达到7.8米。
第六步,9月1日至9月25日,工作面中部自动跟机常态化使用和工作面两端头三角煤自动跟机调试。
上述六步目前已基本完成,中部自动跟机已初步进入常态化使用阶段。
接下来,需要调试完成的项目是:采煤机记忆截割功能(西安煤机厂)、天玛人员定位和单兵系统等研究开发项。
这里简单介绍下人员定位和单兵系统。
巡视人员定位与识别系统:系统由人员定位卡和人员定位感知器及连线组成,人员定位卡由巡检工随身携带,人员定位感知器安装在支架控制器下方。
功能为进行人员的定位,定位人员所在支架自动闭锁,保证人员安全。
当判断巡视人员出现在危险区域内时,闭锁巡视人员所在支架,并停止采煤机运行、运输机推溜等动作。
目前已在支架上试装了20个,每三架安装1个。
9月15日在井下进行了初步试验,达到效果为只能感知到本架。
由于人员定位系统连接线未到货,还未正式调试。
单兵系统:“单兵”系统为双方技术开发内容,为操作人员和巡检人员配备手机、无线视频、无线WIFI设备等,通过工作面无线通讯系统,高速传输实时信息到顺槽和井上,保障巡检人员与地面视频、语音、环境参数实时交互。
第四部分:目前存在的问题及下一步重点工作一、对智能化工作面影响较大的存在两个问题:1、工作面产尘、扬尘较大,造成工作面能见度降低,影响工作面视频监控。
目前采取的措施是:一方面待414工作面封闭后,对系统风量进行调整,增大416工作面风量;另一方面已购置抑尘剂进行试验,并和抑尘剂厂家研究改造煤机喷雾。
2、工作面片帮问题严重,中部自动跟机时,煤机前滚筒收护帮时,片帮不能很好控制。
目前正和天玛研究讨论,将护帮控制作为一个专门研究课题,从工艺和程序上进行解决片帮问题。
二、下一步重点工作:1、做好智能化工作面剩余项目调试工作,即采煤机记忆截割功能(西安煤机厂)、天玛人员定位和单兵系统等开发项。
2、进、回风超前支架远程控制功能,皮带自移机尾远程控制功能目前还未实现,需要与厂家针对实际问题共同技术攻关和解决。
3、重点做好智能化工作面管理和职工培训工作。
对此,要做好两方面工作:(1)工作面安装、调试好之后的管理要求针对新的生产模式,需要及时调整管理思路和工作重点。
首先,完善地面与顺槽监控中心操控工艺规程,建立适应智能化生产需要的生产工序、流程安排和管理规范。
其次,从人多向人少转变之后,智能化生产系统上的每台设备、每个环节都是“牵一发而动全身”,综采队管理重心就要由劳动组织管理、现场管理向设备管理、系统维护转变,建立智能化设备检修台账,提高检修质量,保证设备完好率100%。
再次,从人工现场操控向智能化远程操控转变后,要重新修订综采工作面各岗位作业规程,明确规定凡是智能化系统功能范围内的动作,严禁职工手动操作,生产期间工人只允许对系统程序执行不到位的动作进行干预修正,改变职工固有的思维模式,培养职工适应智能化生产的良好习惯。
(2)综采队职工素质的提升要求。
智能化工作面对员工培训提出更高要求,必须掌握机电设备、自动化控制、信息网络知识和操作维护等技能。
为促使职工尽快掌握智能化无人开采技术,必须通过不断创新培训方式,提升职工素质。
一是强化基础培训,邀请厂家对主要岗位职工对智能化设备和软件进行培训。
二是强化安装过程中实操培训,采取厂家技术人员现场辅导、现场传授操作要领、现场技术研讨等形式开展现场培训。
三是强化调试过程中系统培训。
综采队要详细记录每台设备、每个系统运行台账,建立设备调试日志,对存在的难题进行研究,提出解决方案。
做到让职工全过程参与、全过程学习。