铝合金压铸模热处理PPT
《铝合金热处理》课件

在建筑领域的应用
总结词
美观耐用、绿色环保
详细描述
铝合金在建筑领域的应用广泛,如铝合金门窗、幕墙等。通过热处理技术,可以提高铝合金的硬度和耐磨性,使 其更加美观耐用。同时,铝合金材料可回收利用,符合绿色环保的理念。
在电子产品领域的应用
总结词
精密制造、小型化趋势
详细描述
随着电子产品向小型化、精密化方向发展,铝合金热处理技术在电子产品制造中发挥着越来越重要的 作用。通过热处理技术,可以提高铝合金的精度和稳定性,满足电子产品对材料高精度和高稳定性的 要求。
固溶处理可以提高铝合金的塑性和韧性,改善其加工性能,同时为时效处理提供良 好的基的性能有重要影响,需要严格控制 。
时效处理
时效处理是将经过固溶处理的铝 合金在室温或加热到一定温度下 保温一定时间,使过饱和固溶体
分解,析出强化相的过程。
时效处理可以提高铝合金的强度 和硬度,改善其耐磨性和耐腐蚀
THANKS
感谢观看
详细描述
铝合金因其高强度、轻量化和耐腐蚀等特性,在航空航天领域被广泛使用。通 过热处理技术,可以进一步提高铝合金的性能,满足航空航天领域对材料高强 度和轻量化的严格要求。
在汽车工业领域的应用
总结词
大规模生产、节能减排
详细描述
汽车工业是铝合金热处理应用的重要领域,铝合金零件的大规模生产能够降低汽 车重量,从而减少能源消耗和排放。热处理技术能够提高铝合金的力学性能和耐 腐蚀性,使其在汽车制造中更具竞争力。
提高材料使用寿命
通过合理的热处理工艺,可以显 著提高铝合金的使用寿命,减少 维修和更换的频率,降低成本。
铝合金热处理的历史与发展
早期铝合金热处理
未来发展趋势
早期的铝合金热处理主要采用退火和 淬火等简单工艺,以改善材料的塑性 和硬度。
铝合金压铸模热处理

• 模具零件热处理:在模具制造厂完成,或专业热
处理厂完成。特点是小批量或单件生产,工艺复杂 多样,设备精良。
• 热处理工艺方法,分预备热处理和最终热处 理。常用方法有:正火、退火、淬火、调质、 渗碳及氮化等,见表。
退火工艺:
• H13钢锻后碳化物带状偏析有时也较严重, 常规退火工艺(组织得到片状珠光体+少量 块状碳化物)不能满足。采用高温固溶— —段时间等温球化退火工艺(得到组织为 •退火工艺 球状珠光体+少量弥散分布粒状碳化物), 碳化物可以到超细化水平,碳化物带状偏 析可以得到均匀化,因此二次碳化物也较 少出现。使碳化物不均匀分布得到明显改 善,甚一直采用3Cr2W8V钢制 造,这种钢虽然具有良好的高温强度和热硬性, 但韧性和热疲劳抗性较差是一大弱点,致使使用 这种钢制造的模具因过早出现热疲劳裂纹并较快 扩展而影响产品质量。 4Cr5MoSiV(简称H13)是新型热模具钢,在国际 上广泛应用的一种空冷硬化热作模具钢。H13钢 有较高的热强性和热硬性,有相当高的韧性和耐 冷热疲劳性能,不容易产生热疲劳裂纹,即使出 现热疲劳裂纹也细而短,不容易扩展,用其制作 的模具使用寿命有较大提高。
压铸模具材料我国铝合金压铸模多年来一直采用3cr2w8v钢制造这种钢虽然具有良好的高温强度和热硬性但韧性和热疲劳抗性较差是一大弱点致使使用这种钢制造的模具因过早出现热疲劳裂纹并较快扩展而影响产品质量
铝合金压铸模热处理
压铸模具概述
• 压铸模具的失效形式有热疲劳开裂、热磨 损和热熔蚀。 • 对压铸模具的性能要求是:具有较高的 耐热性和良好的高温力学性能;具有优良 的耐冷热疲劳性和较高的导热率;具有良 好的抗氧化性和耐蚀性;具有较高的淬透 性。凹模的硬度为56~60HRC,但要求韧性 较高。
金属热处理铝合金的热处理课件

铝合金的时效处理
时效处理是铝合金热处理的另一个重要环节 ,通过在室温或低温下长时间放置,使过饱 和固溶体发生分解,形成弥散分布的强化相 ,进一步提高材料的强度和硬度。
时效处理过程中,过饱和固溶体在室温或低 温下长时间放置,会发生分解。随着时间的 推移,强化相逐渐从过饱和固溶体中析出, 形成弥散分布的状态。这种弥散分布的强化 相可以有效地阻碍位错运动,提高材料的强 度和硬度。时效处理是铝合金热处理中不可 或缺的一环,对于提高铝合金的性能具有重
02 铝合金热处理原理
铝合金特性
密度低
铝合金的密度远低于钢铁,具有更好的轻量化 效果。
良好的塑性
铝合金在加工过程中具有良好的塑性,容易形 成各种形状。
良好的导电性和导热性
铝合金具有优良的导电和导热性能,广泛应用于电子和散热器行业。
铝合金热处理原理
加热
01Biblioteka 将铝合金加热到一定温度,使其原子TDM活跃度增加。
加热时间控制
根据铝合金的厚度和热处 理工艺要求,控制加热时 间,确保铝合金材料均匀 受热。
冷却方式选择
根据铝合金的种类和热处 理要求,选择适当的冷却 方式,如风冷、水冷等, 以获得所需的机械性能。
铝合金热处理的质量检测与控制
硬度检测
通过硬度测试,检测铝合金材料的硬度是否达到 要求。
金相组织观察
通过金相显微镜观察,检测铝合金材料的金相组 织是否符合要求。
金属热处理铝合金的热处理课件
• 金属热处理概述 • 铝合金热处理原理 • 铝合金热处理工艺 • 铝合金热处理设备与工艺控制
• 铝合金热处理的发展趋势与未来 展望
• 案例分析:某铝合金产品的热处 理工艺流程
01 金属热处理概述
压铸工艺ppt课件

压铸工艺可获得高精度 、高质量的金属零件, 尺寸精度可达IT6-IT8级 。
压铸机生产效率高,可 实现自动化生产,提高 生产效率。
压铸工艺可节约原材料 ,减少加工余量,降低 生产成本。
压铸工艺可应用于各种 金属材料的成型,如铝 合金、锌合金、铜合金 等。
压铸工艺发展历程
01 早期阶段
压铸工艺起源于19世纪初,最初用于制造印刷机 零件和钟表零件等小型精密零件。
采用真空压铸、挤压铸造等先进压铸技术 ,提高金属液的充型能力和补缩能力,减 少气孔、缩松等缺陷的产生。
提高压铸件质量途径
加强原材料控制
选用优质合金材料,严格控制金属液的化学成分和物理性能,确保原 材料质量符合要求。
优化压铸工艺设计
根据压铸件的结构和性能要求,合理设计浇注系统、排气系统和冷却 系统等,确保金属液在型腔内的流动和凝固过程稳定可靠。
冷却系统设计
根据模具温度和产品要求,设计合理的冷 却水道和冷却方式
模具材料及热处理
01 常用模具材料
热作模具钢、冷作模具钢、塑料模具钢等
02 热处理工艺
淬火、回火、表面强化处理等,提高模具的硬度 、耐磨性和抗疲劳性能
03 模具寿命与维护
通过合理的使用和维护,延长模具使用寿命,降 低生产成本
03
压铸合金与熔炼
强化过程监控和检验
采用先进的检测手段和工艺控制方法,对压铸过程中的关键参数进行 实时监控和调整,确保压铸件质量稳定可靠。
加强人员培训和管理
提高压铸操作人员的技能水平和质量意识,加强生产现场的管理和调 度,确保生产过程的顺利进行和产品质量的有效控制。
06
压铸工艺发展趋势与展望
新型压铸技术及应用前景
02 中期阶段
铝合金的热处理
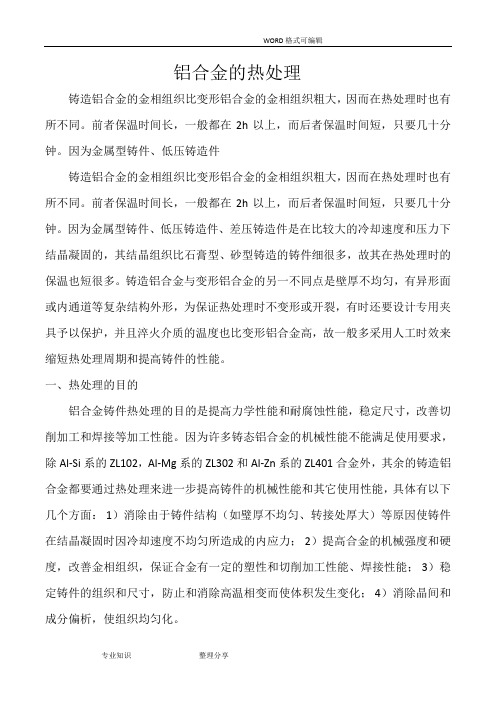
铝合金的热处理铸造铝合金的金相组织比变形铝合金的金相组织粗大,因而在热处理时也有所不同。
前者保温时间长,一般都在2h以上,而后者保温时间短,只要几十分钟。
因为金属型铸件、低压铸造件铸造铝合金的金相组织比变形铝合金的金相组织粗大,因而在热处理时也有所不同。
前者保温时间长,一般都在2h以上,而后者保温时间短,只要几十分钟。
因为金属型铸件、低压铸造件、差压铸造件是在比较大的冷却速度和压力下结晶凝固的,其结晶组织比石膏型、砂型铸造的铸件细很多,故其在热处理时的保温也短很多。
铸造铝合金与变形铝合金的另一不同点是壁厚不均匀,有异形面或内通道等复杂结构外形,为保证热处理时不变形或开裂,有时还要设计专用夹具予以保护,并且淬火介质的温度也比变形铝合金高,故一般多采用人工时效来缩短热处理周期和提高铸件的性能。
一、热处理的目的铝合金铸件热处理的目的是提高力学性能和耐腐蚀性能,稳定尺寸,改善切削加工和焊接等加工性能。
因为许多铸态铝合金的机械性能不能满足使用要求,除Al-Si系的ZL102,Al-Mg系的ZL302和Al-Zn系的ZL401合金外,其余的铸造铝合金都要通过热处理来进一步提高铸件的机械性能和其它使用性能,具体有以下几个方面: 1)消除由于铸件结构(如璧厚不均匀、转接处厚大)等原因使铸件在结晶凝固时因冷却速度不均匀所造成的内应力; 2)提高合金的机械强度和硬度,改善金相组织,保证合金有一定的塑性和切削加工性能、焊接性能; 3)稳定铸件的组织和尺寸,防止和消除高温相变而使体积发生变化; 4)消除晶间和成分偏析,使组织均匀化。
二、热处理方法 1、退火处理退火处理的作用是消除铸件的铸造应力和机械加工引起的内应力,稳定加工件的外形和尺寸,并使Al-Si系合金的部分Si结晶球状化,改善合金的塑性。
其工艺是:将铝合金铸件加热到280-300℃,保温2-3h,随炉冷却到室温,使固溶体慢慢发生分解,析出的第二质点聚集,从而消除铸件的内应力,达到稳定尺寸、提高塑性、减少变形、翘曲的目的。
铝合金压铸工艺基础知识培训PPT课件

二、压铸过程主要工艺参数
3. 3 快压射速度的作用和影响
快压射速度对合金机械性能的作用和影响,提高压射 速度,动能转化为热能,提高了合金熔液的流动性,有利 于消除流痕,冷隔等缺陷,提高了机械性能和表面质量, 但速度过快时,合金熔液呈雾状和气体混合,产生严重裹 包气,机械性能下降。
第33页/共49页
C
椭圆中心详见局部视图
椭圆 2 (长轴 22mm,短轴 21.4mm) 椭圆 1 (长轴 15.6 mm,短轴 14.6mm)
第34页/共49页
三、压铸件设计
7.压铸件设计中的嵌入嵌件设计 压铸件中能铸入金属或非金属嵌件,主要为了提高局部的强度耐磨性或
形成难以成型的内腔,嵌件埋入金属的部分要设计防转和防止轴向移动的形 状同时要考虑嵌件放入模具的方便性和承受金属液冲击的稳定性
第22页/共49页
二、压铸过程主要工艺参数
4. 1 浇注温度的作用和影响
➢ 合金温度对铸件机械性能的影响。随着合金温度的提高 。机械性能有所改善,但超过一定限度后,性能恶化, 主要原因是:
➢ 气体在合金中的溶解度,随温度的升高而增大,虽然溶 解在合金中的气体,但在压铸过程中难以析出,影响机 械性能
3. 1 冲头速度与内交口速度的关系
➢ 根据连续性原理,在同一时间内金属流以速度V1流过 压室截面积为F1的合金液体积,应等于以速度V2流过 内浇口截面积为F2的合金液体积 F1室V1射=F2内V2内
➢ 因此,压射锤头的压射速度越高,则金属流经内浇口的 速度越高。
第17页/共49页
二、压铸过程主要工艺参数
三、压铸件设计
3.压铸件的圆角设计 铸件除有特殊配合要求的地方,尽量所有的部位都设计圆角,
铝合金压铸件表面热处理的方法
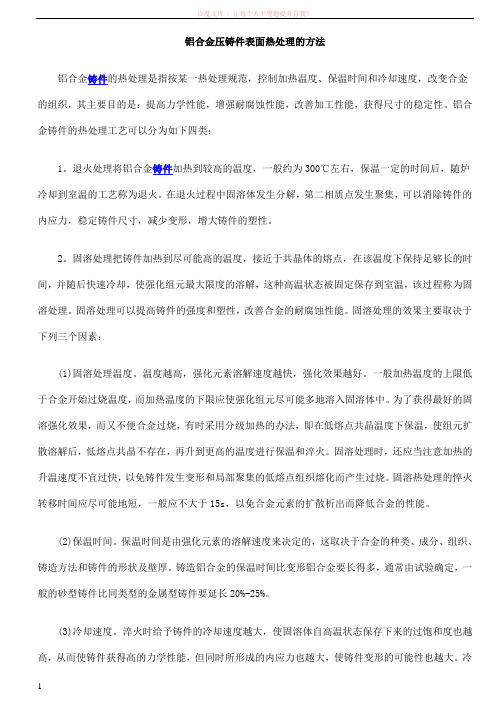
铝合金压铸件表面热处理的方法铝合金铸件的热处理是指按某一热处理规范,控制加热温度、保温时间和冷却速度,改变合金的组织,其主要目的是:提高力学性能,增强耐腐蚀性能,改善加工性能,获得尺寸的稳定性。
铝合金铸件的热处理工艺可以分为如下四类:1。
退火处理将铝合金铸件加热到较高的温度,一般约为300℃左右,保温一定的时间后,随炉冷却到室温的工艺称为退火。
在退火过程中固溶体发生分解,第二相质点发生聚集,可以消除铸件的内应力,稳定铸件尺寸,减少变形,增大铸件的塑性。
2。
固溶处理把铸件加热到尽可能高的温度,接近于共晶体的熔点,在该温度下保持足够长的时间,并随后快速冷却,使强化组元最大限度的溶解,这种高温状态被固定保存到室温,该过程称为固溶处理。
固溶处理可以提高铸件的强度和塑性,改善合金的耐腐蚀性能。
固溶处理的效果主要取决于下列三个因素:(1)固溶处理温度。
温度越高,强化元素溶解速度越快,强化效果越好。
一般加热温度的上限低于合金开始过烧温度,而加热温度的下限应使强化组元尽可能多地溶入固溶体中。
为了获得最好的固溶强化效果,而又不便合金过烧,有时采用分级加热的办法,即在低熔点共晶温度下保温,使组元扩散溶解后,低熔点共晶不存在,再升到更高的温度进行保温和淬火。
固溶处理时,还应当注意加热的升温速度不宜过快,以免铸件发生变形和局部聚集的低熔点组织熔化而产生过烧。
固溶热处理的悴火转移时间应尽可能地短,一般应不大于15s,以免合金元素的扩散析出而降低合金的性能。
(2)保温时间。
保温时间是由强化元素的溶解速度来决定的,这取决于合金的种类、成分、组织、铸造方法和铸件的形状及壁厚。
铸造铝合金的保温时间比变形铝合金要长得多,通常由试验确定,一般的砂型铸件比同类型的金属型铸件要延长20%-25%。
(3)冷却速度。
淬火时给予铸件的冷却速度越大,使固溶体自高温状态保存下来的过饱和度也越高,从而使铸件获得高的力学性能,但同时所形成的内应力也越大,使铸件变形的可能性也越大。
铝合金压铸技术ppt课件
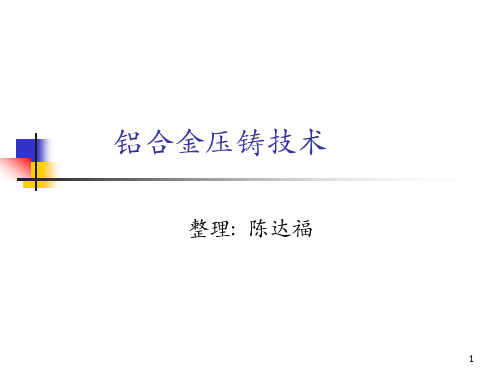
7.0 7.5
8.1
8.5 9.0
% 80 4.6 5.2
5.7 6.1
6.6
7.0 7.3
85 3.6 4.0
4.4 4.7
5.0
5.4 5.6
90 2.5 2.8
3.0 3.3
3.5
3.7 3.9
95 1.3 1.5
1.6 1.8
1.9
2.0 2.1
15Biblioteka 压铸制程条件>合金熔解
>射出速度 >高速切换位置 >铸造压力 >温度控制
铝合金压铸技术
整理: 陈达福
1
课程内容
>压铸概论与压铸铝合金 >压铸制程条件与设定 >模具方案设计 >实例研讨
2
压铸铝合金
压铸用铝合金全世界超过3000种型号
3
压铸铝合金的基本要求
1.流动性好 2.收缩率.龟裂倾向小 3.等温凝固比率大,如此方可产生致密之表面化铸
肌,避免缩孔之危害 4.有一定之高温强度,顶出时才不致变形 5.常温下有足够强度,以利生产薄壁件 6.不易与模具起化学或物理反应,否则粘模,影响量
27
THE END
28
GD-AlSi12(Cu) GD-AlSi10Mg GD-AlMg9 ----GD-AlSi9Cu3 GD-AlSi9Cu3 -------------
6
压铸铝合金材料成份规范
编号
ADC-1
Cu
1.0
ADC-3 0.6max
ADC-5 0.2max
ADC-6 0.1max
ADC-10 2.0~4.0
份 Zn
0.5max 0.5max 0.1max 0.4max 1.0max 3.0max
- 1、下载文档前请自行甄别文档内容的完整性,平台不提供额外的编辑、内容补充、找答案等附加服务。
- 2、"仅部分预览"的文档,不可在线预览部分如存在完整性等问题,可反馈申请退款(可完整预览的文档不适用该条件!)。
- 3、如文档侵犯您的权益,请联系客服反馈,我们会尽快为您处理(人工客服工作时间:9:00-18:30)。
退火工艺:
H13钢锻后碳化物带状偏析有时也较严重, 常规退火工艺(组织得到片状珠光体+少量块 状碳化物)不能满足。采用高温固溶——段 时光间体等+少温量球弥化散退分火布工•退粒艺火状(工碳得艺化到物组)织,为碳球化状物珠可 以到超细化水平,碳化物带状偏析可以得到 均匀化,因此二次碳化物也较少出现。使碳 化物不均匀分布得到明显改善,甚至消除。
我国铝合金压铸模多年来一直采用3Cr2W8V钢制造, 这种钢虽然具有良好的高温强度和热硬性,但韧性 和热疲劳抗性较差是一大弱点,致使使用这种钢制 造的模具因过早出现热疲劳裂纹并较快扩展而影响 产品质量。
4Cr5MoSiV(简称H13)是新型热模具钢,在国际上 广泛应用的一种空冷硬化热作模具钢。H13钢有较 高的热强性和热硬性,有相当高的韧性和耐冷热疲 劳性能,不容易产生热疲劳裂纹,即使出现热疲劳 裂纹也细而短,不容易扩展,用其制作的模具使用 寿命有较大提高。
目前压铸模具型块材料多采用H13 H13退火模坯,硬度为192~229HBS H13钢的化学成份 C 0.32—0.45 Mn
0.20—0.50 Si 0.80—1.20 Gr 4.75—55 Mo 1.10—1.75 V 0.80—1,20 (%)
热作模具常用热处理工艺
模具热处理包括模具材料热处理和模具零件热处理 。
铝合金压铸模热处理
压铸模具概述
压铸模具的失效形式有热疲劳开裂、热磨损 和热熔蚀。
对压铸模具的性能要求是:具有较高的耐 热性和良好的高温力学性能;具有优良的耐 冷热疲劳性和较高的导热率;具有良好的抗 氧化性和耐蚀性;具有较高的淬透性。凹模 的硬度为56~60HRC,但要求韧的主要性能之一,它反 映了模具钢在高的工作温度下抵抗软化的能力, 它关系到钢的高温硬度、高温强度、及热疲劳抗 力等等。提高回火稳定性有助于延长模具的使用 寿命。为了防止开裂,模具淬火后冷却至100℃ 左右应立即回火(特别是形状复杂的模具淬火后 应立即回火)。根据模具的工作情况,回火一般 却550℃——650℃。在500℃附近获得二次硬化, 回火硬度最高,为55HRC左右,钢的冲击韧性显 著降低,出现回火脆性,应避免。
淬火工艺:
据热作模具的服役特点,淬火温度选在1020℃.选择 淬火温度目的在于获得最紧要的性能。高温强度随 淬火温度升高而增高,但强度的增高是牺牲韧性的 条件下得到的,淬火温度越高,钢对晶粒长大越敏 感。粗晶粒比细晶粒钢韧性差,容易产生裂纹而损 坏。冷却速度低导致冲击韧性差,容易产生裂纹而 损坏。冷却速度低导致冲击韧性低,要使H13钢获 得尽可能的冲击韧性就应该把高的淬火温度和高的 冷却速度恰当地结合起来
铝合金压铸模的升温速度,以每小时200℃ 左后为最理想。也可以快速进行预热,预 热的目的在于防止升温中因热应力或相变 应力而产生的变形,以及800℃左右由相变 引起的收缩变形,因此采用二次预热。第 一次预热温度为550℃,第二次预热温度为 800℃,最终加热到1020℃。
采用空冷和一级淬火,铝合金压铸模容易 产生开裂,使用寿命低。采用二级分级淬 火,较为理想。现将分级淬火工艺相比较, 一级盐浴分级淬火用的中性盐浴温度为 500℃和200℃。
模具材料热处理:在钢厂内完成,保证钢材质量,
如基本力学性能,金相组织要符合国家标准或行业 标准。特点是大型工业炉中大批量生产。
模具零件热处理:在模具制造厂完成,或专业热
处理厂完成。特点是小批量或单件生产,工艺复杂 多样,设备精良。
热处理工艺方法,分预备热处理和最终热处 理。常用方法有:正火、退火、淬火、调质、 渗碳及氮化等,见表。
淬火后回火曲线 :
去应力回火:
℃ 随炉冷 400℃
小时
空冷