铝合金讲义压铸模
铝合金压铸模

• 在等温球化退火工艺的制定过程中,奥氏体化温度及等温 转变温度十分重要。奥氏体化温度较高时,未溶碳化物数 量较少,奥氏体晶粒较大,而且其中的碳含量的分布也比 较均匀,因而有利于球化过程的进行。等温转变温度较低 时,碳(及合金元素)在奥氏体中扩散较困难,也不利于 球化过程的进行。只有当奥氏体温度较低,等温转变温度 较高的处理规程下,才能得到球化组织。 等温球化退火 规范:首先毛坯入炉,随炉升温缓慢加热,加热至Ac1+ (20~30℃),保 • 温3~4h,经查表,H13钢的Ac1为860℃,故升温加热至 880℃~890℃并保温3~4h;然后随炉缓冷至Ar1-(20~ 30℃)保温4~5h,经查表H13钢的Ar1为775℃,故升温加 热至745℃~755℃并保温4~5h;然后再随炉缓冷至550℃, 空冷至室温。经硬度检测,硬度可达229HBW,共晶碳化物 等级≤3级。如果钢中的原始组织网状碳化物较严重,则 需要加热到略高于Acm的温度,使碳化物网溶入奥氏体, 然后再较快地冷却到Ar1一下温度进行等温球化退火。 • 经过球化退火,可使可切削性能大大提高;在淬火时,溶 入奥氏体的碳化物较均匀; • 淬火开裂和淬火变形减轻;而韧性有所增加等等多方面有 所改善。
一般把热作模具钢分为三类:
• (1)高韧性热作模具钢 5CrMnMo、5CrNiMo、 4Cr5MoVSi(H11)等,适宜制作一般的锻造模具; • (2)高热强钢 3Cr2W8V、Y4、Y10、以及基体 钢5Cr4Mo2W2SiV等,宜用作热挤压模、压铸模 等; • (3)强韧兼备的热作模具 钢 4Cr5MoV1Si(H13)、HM3、4Cr5W2SiV等,宜 用作热锻模、热挤压模、压铸模等、高速锻模。
回火
• 回火的目的就是使模具达到一定的硬度和韧性,并消除淬火应力。为 保证在使用中的组织稳定性和内应力尽可能小,挥回火时间必须充分, 一般回火时间可按3min/mm。但最少不低于2h。 对于二次硬化热作模具钢,淬火后组织中存在一定量的残余奥氏体, 第一次回火后,在冷却过程中,这些残余奥氏体基本上转变为相应的 等温产物,这些产物较脆,往往会成为开裂的根源,故必须进行第二 次回火,有时为了使用上的要求也可进行第三次回火。 一般来说,第 一次回火温度根据回火温度与硬度关系曲线的硬度要求而定,第二次 回火温度比第一次低20℃,但是有些情况下第一次回火温度也可采用 较低的温度,然后根据第一次回火后的硬度来选择第二次的回火温度, 以期达到所需硬度。 对于该模具钢采取的是高温回火,第一次回火温度600℃,第二次可 略低,取580℃。由于钢中含有一定量的Cr、Mn、Ni,或者Ni少量时 Cr、Mn共存的条件下,高温回火(尤其是在500~600℃之间进行时) 极易出现比较严重的第二类回火脆性,应在回火后采用快速冷却的方 式(油冷或水冷)以避免之。如果钢中的Mo的含量适当提高,钢的 回火脆性敏感性大大减小,高温回火后可以缓冷(空冷)。 经两次高温回火后获得的组织是回火屈氏体,并且 残余奥氏体的含量 极少可以忽略不 计,钢回火后的性能大大提高,强度、硬度有所下降,塑性韧性较淬 火后明显提高。回火后硬度可达47~49HRC。
压铸模流分析讲义ppt课件

2.這是一張模擬充填時間的結果圖
3.這是模擬充填過程的結果
4.這是模擬澆口充填速度的結果圖
5.這是模擬凝固時間的結果圖
6.這是模擬凝固過程的結果
7.這是模擬熱結點的結果圖
考試
用壓鑄模流分析的操作流程
壓鑄成型方案
開始模具CAE之前,我們必須先用Pro/e做 出壓鑄成型方案.以下是一壓鑄成型方案方案 核心案例:
產品
進澆口 流道 溢流槽 排氣槽
用該產品方案為例,演示壓鑄模流分 析的前處理與結果判讀.
先把cad model 轉為stl model ,做magma 前處理.轉為magma承認的圖形格式.
壓鑄具有生產性高,尺寸精度優良、后加工量少,鑄件表 面平滑,機械強度高,可鑄薄壁鑄件等優良特點.但由于熔湯高 速射入模穴,易卷入空氣,故使鑄件內常含有氣孔及充填不良 等,所以壓鑄模成型方案至關重要,在壓鑄模具的開發階段,人 們一直在致力于預先驗證模具設計方案的可行性,以確保製造
出高品質的壓鑄模具,壓鑄模流分析軟件(MAGMA)的應用,
為我們提供了捷徑.
壓鑄模流分析應用原理
壓鑄模流分析就是利用數值模擬 ( numerical simulation ), 建構整個鑄造系統 模型 , 從熔融金屬液紊流進入模穴,從凝固到 補縮 , 都是架構在清楚的物理 模型上 , 透過 電腦螢幕 , 使用者按步就班調整幾 何模型 ( 澆道、進澆口、溢流槽等 )、 鑄造條件 ( 壓鑄溫度 , 壓鑄速度等 )來改善鑄造過程。
壓鑄模流分析
上課內容
一 . 壓 鑄 (Die casting)成形簡介; 二 . 壓 鑄 模 流 分 析 應 用 原 理 ; 三 . 壓 鑄 模 流 分 析 功 能 介 紹 ; 四 . CAE 應用軟體操作流程 ; 五. CAE 結果介紹 ; 六. 考試 ;
压铸工艺培训讲义
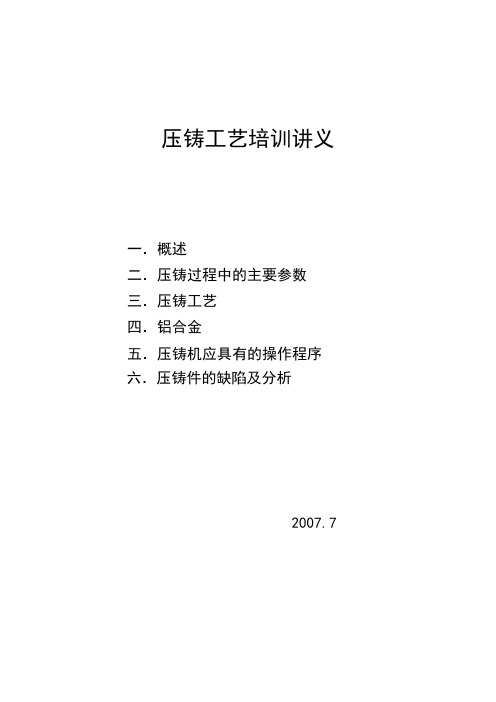
压铸工艺培训讲义一.概述二.压铸过程中的主要参数三.压铸工艺四.铝合金五.压铸机应具有的操作程序六.压铸件的缺陷及分析2007.7一. 概述压力铸造是近代金属加工工艺中发展较快的一种少无切削的特种铸造方法。
它是将熔融金属在高压高速下充填铸型,并在高压下结晶凝固形成铸件的过程。
高压高速是压力铸造的主要特征。
常用的压力为数十兆帕,填充速度(内浇口速度)约为16~80米/秒,金属液填充模具型腔的时间极短,约为0.01~0.2秒。
由于用这种方法生产产品具有生产效率高,工序简单,铸件公差等级较高,表面粗糙度好,机械强度大,可以省去大量的机械加工工序和设备,节约原材料等优点,所以现已成为我国铸造业中的一个重要组成部分。
二. 压铸过程中的主要参数在压力铸造的整个过程中,压力起到了主导作用。
熔融金属不仅在压力作用下充满压室进入浇注系统,而填充又在压力作用下凝固成型。
在压射过程中各个阶段,随着冲头位置的移动,压力也出现不同的变化,这个变化规律都会对铸件质量产生重大影响。
因此我们应对压铸过程中压力的作用与变化要有一个感性认识,这也是压铸技术的理论基础。
现以常用的卧式冷室压铸机为例,来逐步描绘出压射过程中,随着冲头位置的移动和压力之间的变化规律。
首先要说明的是在以下各阶段图形中,左图表示压射的过程,右上图表示每一个位移阶段相应的压力变化值,右下图为相应的压射冲头位移曲线。
现将图中各阶段的具体内容说明如下:图(a),起始阶段,金属液开始浇入压室,准备压射。
图(b),第Ⅰ阶段,压射冲头慢速移动越过浇料口,金属液受到冲头的推动,由于速度较慢,压室中不产生浪涌,故金属液不致从浇口中溅出,这种状况也是在起始压射阶段所要求的。
这时推动金属液的压力为P0。
其作用有二,即克服压射油缸中活塞在移动时的摩擦力和冲头与压室之间的摩擦力。
冲头越过浇料口的这段距离为S1,称为慢速封口阶段。
图(c),第Ⅱ阶段,压射冲头以高于第Ⅰ阶段的速度向前运动,此时金属液充满整个压室前端,聚集到内浇口前沿之处,与这一阶段速度响应的压力上升值达到P1,冲头在这一阶段所运动的距离为S2,称为金属液堆积阶段。
压铸铝合金模具材料

压铸铝合金模具材料介绍压铸铝合金模具是一种用于生产铝合金零件的重要工具。
在压铸过程中,熔融的铝合金经过高压注入到模具中,形成所需的零件。
模具材料的选择对于压铸工艺的成功和生产效率至关重要。
本文将探讨几种常用的压铸铝合金模具材料,包括铝合金模具钢、热应力较小的冷作模具钢、高耐磨的工具钢和耐高温的耐烧蚀合金。
铝合金模具钢铝合金模具钢是一种特殊钢材,具有良好的切削性能和热导率,能够有效地耐受高温和高压力环境。
它通常包括以下几种成分: - 高碳含量:高碳含量能提高模具钢的硬度和耐磨性,使其能够承受高压下的剪切和冲击力; - 高钼含量:高钼含量可提高模具钢的耐蚀性和耐磨性,延长模具的使用寿命; - 高硅含量:高硅含量可提高模具钢的热导率和耐氧化性能,使其能够有效散热并防止氧化。
铝合金模具钢通常经过热处理,如淬火和回火,以提高其硬度和韧性。
它具有较高的强度和硬度,适用于生产高质量的铝合金零件。
冷作模具钢冷作模具钢是一种具有良好冷热疲劳性能和高韧性的模具材料。
它的主要特点是热应力较小,能够在高温下保持稳定的尺寸和形状。
常用的冷作模具钢包括:CR12CR12是一种高碳钢,具有极高的硬度和耐磨性。
它适用于生产大型厚壁铝合金零件,能够承受高压力和剪切力。
CR12MOVCR12MOV是CR12钢的改进型材料,添加了少量的硅和钼元素。
它具有更好的耐腐蚀性和耐磨性,适用于生产高精度的铝合金零件。
9CrWMn是一种高碳高合金工具钢,具有优异的硬度和耐磨性。
它适用于生产复杂形状的铝合金零件,能够承受高温和高压下的应力和冲击。
4Cr5MoSiV14Cr5MoSiV1是一种热加工模具钢,具有较高的韧性和耐热性。
它适用于生产大型高温铝合金零件,能够承受高温和高压力下的变形和拉伸。
高耐磨工具钢高耐磨工具钢是一种能够在高压力和高摩擦环境下保持良好硬度和耐磨性的模具材料。
常用的高耐磨工具钢包括:SKD11SKD11是一种专用冷作模具钢,具有良好的切削性能和硬度。
压铸模讲义专题培训

壓鑄模設計
2024/10/10
Macherchen
22
三.壓鑄模零部件設計
4)模具結構及壓鑄工藝旳影響 尺寸計算:
LM+ δZ/2=(LZ -△/2 )+ (LZ - △/2)K’ -δC/2
a 型腔徑向尺寸:
LM=[(1+K’) LZ-X△] =(1+K’) LZ-1/2(△ +δZ+δC )
K’------預定收縮率旳平均值
一. 分型面旳類型 二. (一)分型面型腔旳相對位置分類
動模
定模
動模
定模
動模
定模
壓鑄模設計
2024/10/10
Macherchen
8
三.壓鑄模零部件設計
(二)按分型面旳形狀分類 1 平直分型 2. 傾斜分型
3. 階梯分型
4 曲面分型
壓鑄模設計
2024/10/10
Macherchen
9
三.壓鑄模零部件設計
Macherchen
5
二. 壓鑄模旳結構組成
二).壓鑄模結構根據作用分類
壓鑄模設計
2024/10/10
Macherchen
6
二. 壓鑄模旳結構組成
二).壓鑄模結構根據作用分類
壓鑄模設計
2024/10/10
Macherchen
7
三.壓鑄模零部件設計
定義:1. 成型零部件:構成模腔旳全部零部件旳統稱. 2.結構零部件:保証模具有足夠旳剛度,強度及正確安裝和模具 正常工作.
第二講完
壓鑄模設計
2024/10/10
Macherchen
28
(1) 凸模是成型壓件整體內形旳零部件,所以也稱為主型芯. 主型芯旳結構形式有:整體式,通孔台肩式,通孔無台肩 (螺絲固定)式及非通孔.
压铸模知识点讲解
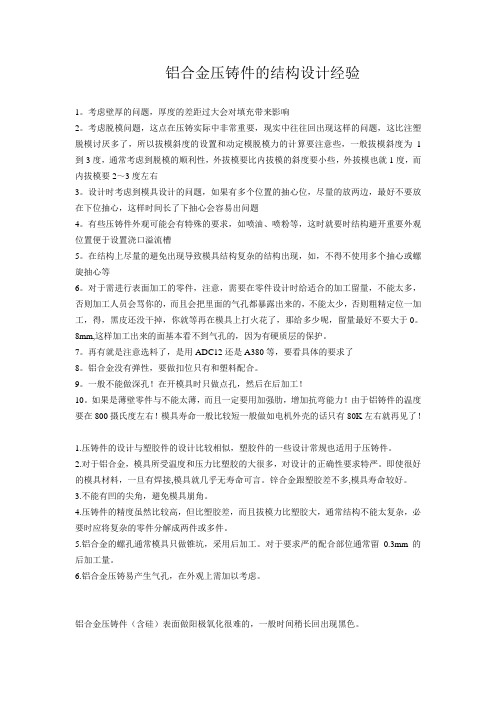
铝合金压铸件的结构设计经验1。
考虑壁厚的问题,厚度的差距过大会对填充带来影响2。
考虑脱模问题,这点在压铸实际中非常重要,现实中往往回出现这样的问题,这比注塑脱模讨厌多了,所以拔模斜度的设置和动定模脱模力的计算要注意些,一般拔模斜度为1到3度,通常考虑到脱模的顺利性,外拔模要比内拔模的斜度要小些,外拔模也就1度,而内拔模要2~3度左右3。
设计时考虑到模具设计的问题,如果有多个位置的抽心位,尽量的放两边,最好不要放在下位抽心,这样时间长了下抽心会容易出问题4。
有些压铸件外观可能会有特殊的要求,如喷油、喷粉等,这时就要时结构避开重要外观位置便于设置浇口溢流槽5。
在结构上尽量的避免出现导致模具结构复杂的结构出现,如,不得不使用多个抽心或螺旋抽心等6。
对于需进行表面加工的零件,注意,需要在零件设计时给适合的加工留量,不能太多,否则加工人员会骂你的,而且会把里面的气孔都暴露出来的,不能太少,否则粗精定位一加工,得,黑皮还没干掉,你就等再在模具上打火花了,那给多少呢,留量最好不要大于0。
8mm,这样加工出来的面基本看不到气孔的,因为有硬质层的保护。
7。
再有就是注意选料了,是用ADC12还是A380等,要看具体的要求了8。
铝合金没有弹性,要做扣位只有和塑料配合。
9。
一般不能做深孔!在开模具时只做点孔,然后在后加工!10。
如果是薄壁零件与不能太薄,而且一定要用加强肋,增加抗弯能力!由于铝铸件的温度要在800摄氏度左右!模具寿命一般比较短一般做如电机外壳的话只有80K左右就再见了!1.压铸件的设计与塑胶件的设计比较相似,塑胶件的一些设计常规也适用于压铸件。
2.对于铝合金,模具所受温度和压力比塑胶的大很多,对设计的正确性要求特严。
即使很好的模具材料,一旦有焊接,模具就几乎无寿命可言。
锌合金跟塑胶差不多,模具寿命较好。
3.不能有凹的尖角,避免模具崩角。
4.压铸件的精度虽然比较高,但比塑胶差,而且拔模力比塑胶大,通常结构不能太复杂,必要时应将复杂的零件分解成两件或多件。
铝合金压铸模具结构
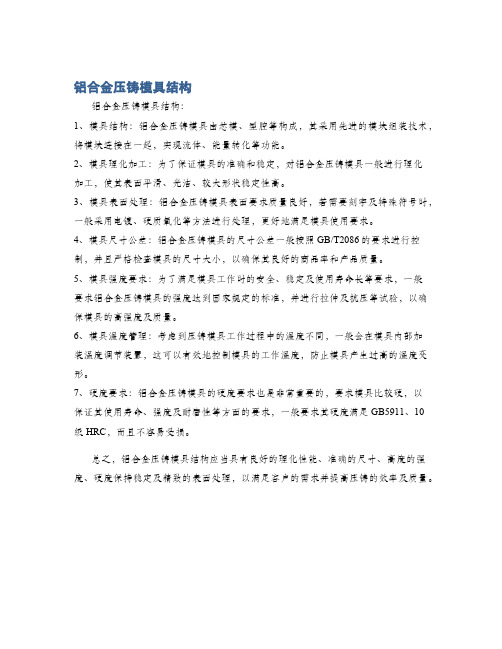
铝合金压铸模具结构
铝合金压铸模具结构:
1、模具结构:铝合金压铸模具由芯模、型腔等构成,其采用先进的模块组装技术,将模块连接在一起,实现流体、能量转化等功能。
2、模具理化加工:为了保证模具的准确和稳定,对铝合金压铸模具一般进行理化
加工,使其表面平滑、光洁、较大形状稳定性高。
3、模具表面处理:铝合金压铸模具表面要求质量良好,若需要刻字及特殊符号时,一般采用电镀、硬质氧化等方法进行处理,更好地满足模具使用要求。
4、模具尺寸公差:铝合金压铸模具的尺寸公差一般按照GB/T2086的要求进行控制,并且严格检查模具的尺寸大小,以确保其良好的商品率和产品质量。
5、模具强度要求:为了满足模具工作时的安全、稳定及使用寿命长等要求,一般
要求铝合金压铸模具的强度达到国家规定的标准,并进行拉伸及抗压等试验,以确保模具的高强度及质量。
6、模具温度管理:考虑到压铸模具工作过程中的温度不同,一般会在模具内部加
装温度调节装置,这可以有效地控制模具的工作温度,防止模具产生过高的温度变形。
7、硬度要求:铝合金压铸模具的硬度要求也是非常重要的,要求模具比较硬,以
保证其使用寿命、强度及耐磨性等方面的要求,一般要求其硬度满足GB5911、10
级HRC,而且不容易受损。
总之,铝合金压铸模具结构应当具有良好的理化性能、准确的尺寸、高度的强度、硬度保持稳定及精致的表面处理,以满足客户的需求并提高压铸的效率及质量。
压铸模流分析讲义

压铸模流分析讲义一、引言压铸是一种常用的金属成形工艺,广泛应用于汽车、摩托车、航空航天等领域。
而在压铸过程中,模具的设计和模流分析是非常重要的环节,能够对压铸件的质量和成形效果起到关键的影响。
本讲义将介绍压铸模流分析的基本原理、流程和应用。
二、压铸模流分析的原理1.流动性分析原理:通过数值模拟方法,计算金属液在模穴中的流动速度、填充压力和温度分布等,并结合模具结构特点预测模具充填过程中的缺陷,如气孔、冷隔、夹杂等。
2.凝固性分析原理:根据金属液的凝固特性,分析模具结构对液态金属凝固过程的影响,预测可能出现的缺陷,如热裂纹、收缩缺陷等。
3.温度场分析原理:通过计算得到金属液在模具中的温度分布,进一步预测可能出现的缺陷。
4.应力变形分析原理:根据模具在铸造过程中的受力情况,分析金属液对模具的应力和变形,预测可能出现的变形和裂纹。
三、压铸模流分析的流程1.模型导入:将要分析的压铸模的三维CAD模型导入流体动力学(CFD)软件中。
2.网格划分:对导入的CAD模型进行网格划分,将模型划分为若干个网格单元,用于模拟流体的流动。
3.材料参数设置:设置金属液的物性参数,如密度、黏度、比热等,并将其导入CFD软件。
4.界面边界条件设置:设置金属液与模具壁之间的界面条件,如润滑和传热系数等。
5.操作条件设置:设置压铸过程中的操作参数,如压力、速度、温度等。
6.数值模拟:基于数值方法,对模具进行流动性、凝固性、温度场、应力变形等方面的模拟。
7.结果分析:根据模拟结果,对流动性、凝固性、温度场、应力变形等方面进行分析和评估。
8.优化设计:根据分析结果,对模具的结构和工艺参数进行优化设计,以改善铸件质量。
9.结果验证:通过样品试铸,验证优化后的模具设计和工艺参数是否能够达到预期效果。
四、压铸模流分析的应用1.优化模具结构设计:通过分析流动性、凝固性和应力变形等方面,可以找出模具设计中存在的问题,并提出相应的改进方案,以提高铸件的质量和生产效率。