铝合金压铸模具的制作
铝合金高压压铸工艺

铝合金高压压铸工艺铝合金高压压铸工艺是一种常用的铝合金制造工艺,广泛应用于汽车、航空航天、电子设备等领域。
本文将从铝合金的选择、工艺流程、工艺参数等方面介绍铝合金高压压铸工艺的相关内容。
一、铝合金的选择铝合金是一种轻质、高强度的金属材料,具有良好的导热性和导电性,因此在工业生产中得到广泛应用。
在高压压铸工艺中,常用的铝合金有ADC12、A380等。
选择合适的铝合金材料对于保证产品的质量和性能至关重要。
二、工艺流程铝合金高压压铸工艺的工艺流程主要包括模具设计、铝合金熔炼、注射成型、冷却固化、模具开启等步骤。
1. 模具设计:根据产品的形状和尺寸要求,设计合适的压铸模具。
模具应具有足够的强度和刚性,能够承受高压和高温的作用。
2. 铝合金熔炼:将选定的铝合金材料按照一定的配比放入熔炉中进行熔炼。
熔炼温度一般在650-750摄氏度之间,保持一定时间使铝合金均匀熔化。
3. 注射成型:将熔化的铝合金倒入注射机中,通过高压将铝合金注射到模具腔体中。
注射过程需要控制注射速度和压力,以确保铝合金充满整个模具腔体。
4. 冷却固化:注射完成后,将模具放置在冷却装置中进行冷却。
冷却过程中,铝合金逐渐凝固,形成所需的产品形状。
5. 模具开启:冷却完成后,打开模具,将成品取出。
在开模过程中需要注意避免产品变形或损坏。
三、工艺参数铝合金高压压铸工艺的成功与否与工艺参数的选择密切相关。
主要的工艺参数包括注射速度、注射压力、冷却时间等。
1. 注射速度:注射速度过快会导致铝合金在模具中产生气泡或冲刷模具表面,影响产品质量;注射速度过慢则会延长工艺周期。
因此,需要根据具体情况选择合适的注射速度。
2. 注射压力:注射压力过大会导致模具磨损加剧,甚至损坏;注射压力过小则无法充分充填模具腔体。
因此,需要根据模具结构和产品要求选择合适的注射压力。
3. 冷却时间:冷却时间过短会导致产品未完全凝固就开模,影响产品质量;冷却时间过长则会延长工艺周期。
(完整版)铝合金压铸工艺

压铸产品基本工艺流程压铸工艺是将压铸机、压铸模和合金三大要素有机地组合而加以综合运用的过程。
而压铸时金属按填充型腔的过程,是将压力、速度、温度以及时间等工艺因素得到统一的过程。
模具结构设计、热处理工艺、模具制造及模具装配对铝合金压铸模寿命的影响。
压铸工艺流程图示1。
11压铸工艺原理压铸工艺原理是利用高压将金属液高速压入一精密金属模具型腔内,金属液在压力作用下冷却凝固而形成铸件。
冷、热室压铸是压铸工艺的两种基本方式,其原理如图1—1所示。
冷室压铸中金属液由手工或自动浇注装置浇入压室内,然后压射冲头前进,将金属液压入型腔。
在热室压铸工艺中,压室垂直于坩埚内,金属液通过压室上的进料口自动流入压室。
压射冲头向下运动,推动金属液通过鹅颈管进入型腔。
金属液凝固后,压铸模具打开,取出铸件,完成一个压铸循环。
1.12压铸工艺的特点优点(1)可以制造形状复杂、轮廓清晰、薄壁深腔的金属零件。
压铸件的尺寸精度较高,表面粗糙度达Ra0。
8—3.2um,互换性好。
(2)材料利用率高。
由于压铸件的精度较高,只需经过少量机械加工即可装配使用,有的压铸件可直接装配使用。
生产效率高。
由于高速充型,充型时间短,金属业凝固迅速,压铸作业循环速度快。
方便使用镶嵌件。
(3)缺点(1)由于高速填充,快速冷却,型腔中气体来不及排出,致使压铸件常有气孔及氧化夹杂物存在,从而降低了压铸件质量。
不能进行热处理。
(2)压铸机和压铸模费用昂贵,不适合小批量生产。
(3)压铸件尺寸受到限制。
压铸合金种类受到限制.主要用来压铸锌合金、铝合金、镁合金及铜合金。
1.13压铸工艺的应用范围压铸生产效率高,能压铸形状复杂、尺寸精确、轮廓清晰、表面质量及强度、硬度都较高的压铸件,故应用较广,发展较快.目前,铝合金压铸件产量较多,其次为锌合金压铸件。
第二章压铸合金2。
1 压铸合金压铸合金是压铸生产的要素之一,要生产优良的压铸件,除了要有合理的零件构造、设计完善的压铸模和工艺性能优越的压铸机外,还需要有性能良好的合金。
铝合金压铸工艺

铝合金压铸工艺简介铝合金压铸是一种常见的金属成形工艺,通常用于制造各种铝合金零件。
其原理是将熔融的铝合金注入到模具中,并在一定的压力下冷却和凝固,最终得到所需的铝合金零件。
本文将介绍铝合金压铸的工艺流程以及相关的工艺参数。
工艺流程铝合金压铸的工艺流程主要包括模具准备、铝合金液态处理、注液和凝固、零件脱模和表面处理等几个主要步骤。
下面将详细介绍每个步骤的内容。
1. 模具准备在铝合金压铸工艺中,模具是非常重要的一部分。
首先需要根据所需零件的形状和尺寸设计制作模具。
模具通常由两部分构成,一部分是固定模,另一部分是活动模。
固定模固定在压铸机上,而活动模则与固定模相连,在注液和凝固过程中参与零件的成形。
模具内部还需要加工一些通道和排气口,以便铝合金的顺利注入和冷却。
在使用模具之前,还需要对其进行表面处理,以确保零件的顺利脱模。
2. 铝合金液态处理铝合金压铸需要使用熔融的铝合金作为原料。
在铝合金的制备过程中,需要控制好温度和成分的配比。
通常采用电炉或燃气炉加热铝合金,直到其达到液态状态。
同时,在熔炼过程中还需要添加一些合适的轻质合金元素,以提高铝合金的流动性和强度。
3. 注液和凝固当铝合金达到液态后,可以开始注入模具中进行成型。
首先将模具合拢,并在一定的压力下将铝合金注入到模具的腔室中。
在注液的过程中,铝合金要通过模具内部的通道和排气口,以确保零件填充完全且没有气泡。
注液的时间和压力应根据零件的大小和形状进行调整。
当铝合金填充完毕后,需要保持一定的压力,直到零件完全凝固。
4. 零件脱模在铝合金凝固后,需要将零件从模具中取出,这个过程称为脱模。
脱模的方法有很多种,可以通过机械力或气动力来推动零件从模具中顺利脱离。
在脱模之前,需要注意保护零件的表面,以免在脱模过程中造成刮擦或其他损坏。
5. 表面处理铝合金压铸零件脱模后,通常还需要进行一些表面处理工艺,以提高零件的外观和性能。
常见的表面处理方法包括机械抛光、电镀、喷涂、阳极氧化等。
压铸铝合金工艺流程

压铸铝合金工艺流程
《压铸铝合金工艺流程》
压铸铝合金是一种常见的金属铸造材料,具有优良的机械性能和耐腐蚀性能。
它广泛应用于汽车、航空航天、机械制造等领域。
压铸铝合金的工艺流程通常包括以下几个步骤。
首先是原材料的准备,包括铝合金锭、添加剂和熔炼炉。
铝合金锭是压铸铝合金的主要原料,它们通常是由工厂提供,具有一定的成分和机械性能要求。
添加剂用于调整合金的成分,以满足不同的性能要求。
熔炼炉是用来将原材料融化并混合的设备。
接下来是压铸模具的制备。
压铸模具是用来制造铝合金零件的关键工具,它的质量直接影响到最终产品的质量。
制备过程包括模具设计、模具制造和模具调试。
然后是熔炼和浇注。
在熔炼过程中,将原材料放入熔炼炉中加热直至融化。
然后将融化的铝合金通过浇注系统注入到压铸模具中,待冷却后即可取出成品。
最后是进行加工和表面处理。
成品经过去闪耳、去毛刺、修整等加工工序后,还需要进行表面处理,以提高其耐腐蚀性能和外观质量。
以上就是压铸铝合金工艺流程的主要步骤。
在实际操作中,各
个步骤都需要严格控制,以确保最终产品的质量。
同时,不断创新和改进工艺流程也是提高生产效率和产品质量的关键。
铝合金壳体压铸模具设计
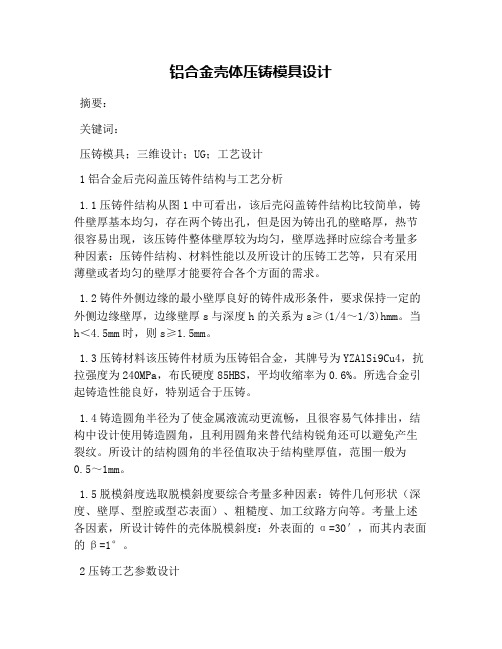
铝合金壳体压铸模具设计摘要:关键词:压铸模具;三维设计;UG;工艺设计1铝合金后壳闷盖压铸件结构与工艺分析1.1压铸件结构从图1中可看出,该后壳闷盖铸件结构比较简单,铸件壁厚基本均匀,存在两个铸出孔,但是因为铸出孔的壁略厚,热节很容易出现,该压铸件整体壁厚较为均匀,壁厚选择时应综合考量多种因素:压铸件结构、材料性能以及所设计的压铸工艺等,只有采用薄壁或者均匀的壁厚才能要符合各个方面的需求。
1.2铸件外侧边缘的最小壁厚良好的铸件成形条件,要求保持一定的外侧边缘壁厚,边缘壁厚s与深度h的关系为s≥(1/4~1/3)hmm。
当h<4.5mm时,则s≥1.5mm。
1.3压铸材料该压铸件材质为压铸铝合金,其牌号为YZAlSi9Cu4,抗拉强度为240MPa,布氏硬度85HBS,平均收缩率为0.6%。
所选合金引起铸造性能良好,特别适合于压铸。
1.4铸造圆角半径为了使金属液流动更流畅,且很容易气体排出,结构中设计使用铸造圆角,且利用圆角来替代结构锐角还可以避免产生裂纹。
所设计的结构圆角的半径值取决于结构壁厚值,范围一般为0.5~1mm。
1.5脱模斜度选取脱模斜度要综合考量多种因素:铸件几何形状(深度、壁厚、型腔或型芯表面)、粗糙度、加工纹路方向等。
考量上述各因素,所设计铸件的壳体脱模斜度:外表面的α=30′,而其内表面的β=1°。
2压铸工艺参数设计2.1压铸机选择选择压铸机必须先确定锁模力。
锁模力作用有二:一个是用来平衡反压力,以达到锁紧分型面的目的;一个是用来阻止飞溅的金属液,以达到获得目标尺寸精度的目的。
设计的铸件不存在分胀型力,因为此模具是没有侧抽芯的(压铸件无侧孔与侧凹)。
因此F 锁≥KF主=1.25×1288.352=1610.44kN根据上述计算得到锁模力的值还有铸件重量,根据这两个主要因素进行压铸机选择,最后选用机型为:卧式冷室压铸机(2500kN)———J1125型,主要参数:①最大金属浇注量———3.2Kg,②模具厚度———250~650mm,③动模座板行程———400mm,④压射力———143~280kN。
铝压铸工艺流程

铝压铸工艺流程铝压铸工艺流程是指将铝合金熔化后,通过压力将熔融的铝合金注入到模具中,并经过冷却固化,最终得到铝合金零件的一种制造流程。
下面将详细介绍铝压铸工艺的主要步骤。
首先是设备准备,包括压铸机、模具、炉子等。
压铸机是将熔融的铝合金注入模具的主要设备,模具则是用来制造所需铝合金零件形状的工具。
炉子用于将铝合金加热至熔化温度。
第二步是材料准备。
选择合适的铝合金材料,根据零件的要求,确保材料的成分合适。
将铝合金材料放入炉子中,加热至熔化温度。
第三步是模具准备。
将模具放入压铸机中,调整好模具的位置和保护装置,确保安全操作。
同时,在模具中涂抹一层润滑剂,以防止铝合金在注射过程中粘附在模具上。
第四步是熔融铝合金注射。
当铝合金熔化至适当温度后,将炉子倾斜,使熔融的铝合金流入铸料室。
然后,通过压铸机的活塞,施加压力将熔融的铝合金注入到模具中。
注射过程中需要控制注入速度和压力,确保铝合金充满模具所有的腔体。
第五步是冷却固化。
当铝合金注射到模具中后,需要等待一段时间进行冷却。
冷却时间的长短取决于铝合金的厚度和形状。
在冷却过程中,铝合金逐渐固化,并且与模具表面接触。
最后一步是铝合金零件的取出。
当铝合金完全冷却固化后,打开压铸机,取出模具中的铝合金零件。
然后对铝合金零件进行修整,去除可能存在的毛刺或其他不完美的地方。
通过以上几个步骤,我们就可以完成铝压铸工艺流程,得到满足要求的铝合金零件。
铝压铸工艺具有成本低、生产效率高、加工精度高等特点,广泛应用于汽车、航空航天、电子电气等领域。
同时,铝压铸技术也在不断发展,为铝合金零件的制造提供更多可能性。
铝合金真空压铸技术

铝合金真空压铸技术铝合金真空压铸技术是一种高效、精密的铝合金铸造工艺,通过在真空环境中进行压铸,可以有效避免铸件表面氧化、气孔等缺陷,提高铸件的质量和性能。
以下是关于铝合金真空压铸技术的详细介绍,包括其工艺流程、优势、应用领域等方面。
一、铝合金真空压铸技术概述铝合金真空压铸技术是一种在真空环境下进行的高压铸造工艺。
其主要步骤包括:模具封闭,抽真空,充填铝液,施加高压,保压定型,冷却固化,开模取件。
整个过程在真空条件下进行,以确保铸件表面无气孔、氧化等缺陷,同时通过高压实现铝液的充分充填,提高铸件的密度和机械性能。
二、铝合金真空压铸技术的工艺流程模具设计和制造:根据产品的形状和尺寸,设计并制造合适的压铸模具,确保模具具有足够的强度和耐磨性。
模具封闭:将设计好的模具封闭,形成一个密封的腔室,以准备进行真空铸造。
真空抽气:在模腔封闭后,通过真空泵将模腔内的空气抽出,创造真空环境。
真空状态有助于减少铝液中气体的溶解,防止气孔的生成。
铝液充填:在真空状态下,将预热至一定温度的铝液注入模腔,确保铝液在模腔中均匀充填。
施加高压:在铝液充填后,施加高压,使铝液充分充填模腔,提高铸件的密度和机械性能。
保压定型:在高压作用下,保持一段时间,使铝液定型成型。
冷却固化:在定型后,通过冷却系统将模腔内的铝液迅速冷却,固化成为铝合金铸件。
开模取件:冷却固化后,打开模具,取出成型的铝合金铸件,进行后续的处理和加工。
三、铝合金真空压铸技术的优势减少氧化和气孔:在真空环境下进行铸造可以有效减少铸件表面的氧化,同时通过真空抽气减少气体的溶解,避免气孔的生成,提高铸件的表面质量。
提高密度和机械性能:高压充填和保压定型能够使铝液充分充填模腔,提高铝合金铸件的密度和机械性能。
精密铸造:铝合金真空压铸技术可以实现更精密的铸造,适用于复杂形状、高精度要求的铝合金零件生产。
高生产效率:由于真空压铸工艺的高压和高速度,可以实现较短的充填时间和较快的冷却速度,提高生产效率。
浅谈铝合金压铸生产中模具的设计制造

浅谈铝合金压铸生产中模具的设计制造摘要:铝合金压铸模具是进行压铸生产的重要工艺装备,同时,也是铝合金压铸生产中三大必备因素之一。
文章首先分析了铝合金压铸模具设计制造技术,其次,就铝合金压铸模具设计制造中需要注意的几个技术问题进行了深入的探讨,具有一定的参考价值。
关键词:铝合金;压铸模具;制造技术铝合金压铸模具是进行压铸生产的重要工艺装备,同时,也是铝合金压铸生产中三大必备因素之一。
生产过程能否顺利进行,铸件质量是否有保证,在很大程度上取决于模具结构的合理性和技术上的先进性。
铝合金压铸模设计制造的优劣,直接影响压铸件的形状、尺寸、强度、表面质量等方面。
而压铸件的质量和稳定性,反映出整个压铸生产过程和压铸模制造过程的技术水平和经济效益。
1铝合金压铸模具设计在铝合金压铸模具设计过程中必须全面分析压铸件结构,熟悉压铸机操作过程,了解压铸机及工艺参数得以调整的可能性及范围,掌握在不同压铸条件下的金属液填充特性和流动特性,并考虑到经济因素,才能设计出切合实际并满足生产要求的压铸模。
铝合金压铸模设计前,设计人员应对所提供的设计依据,包括压铸产品图和生产纲领进行工艺分析,并进行如下必要准备:①根据产品图,对所选用的压铸合金、压铸件的形状、结构、精度和技术要求进行工艺性分析,确定机械加工部位、加工余量和机械加工时所要采取的工艺措施以及定位基准等。
②根据产品图和生产纲领,确定压射比压,计算锁模力:估算压铸件所需的开模力和推出力,以及压铸机的开模距离;选定压铸机的型号和规格。
③根据产品和压铸机的型号和规格,对模具结构进行初步分析,选择分型面和确定型腔数量;选择内浇口进口位置,确定浇注系统和溢流槽、排气槽朗总体布置方案;对带嵌件的压铸件,要考虑嵌件的装夹和固定方式;确定功模和定模镶块,动模和定模套板外形尺寸,以及导核、导套的位置和尺寸;确定冷却和加热管道的位置和尺寸,控制压铸过程的热平衡等。
④绘制压铸件毛坯图。
包括分型面位置、浇注系统、溢流槽和排气槽,推出元件的位置和尺寸以及机械加工余量、加工基准等数值。
- 1、下载文档前请自行甄别文档内容的完整性,平台不提供额外的编辑、内容补充、找答案等附加服务。
- 2、"仅部分预览"的文档,不可在线预览部分如存在完整性等问题,可反馈申请退款(可完整预览的文档不适用该条件!)。
- 3、如文档侵犯您的权益,请联系客服反馈,我们会尽快为您处理(人工客服工作时间:9:00-18:30)。
铝合金压铸模具的制作
铝合金压铸模具的制作(刘氏模具)铝合金压铸模具的制作一般可以分为这几个步骤:审图—备料—加工—模架加工—模芯加工—电极加工—模具零件加工—检验—装配—飞模—试模—生产。
A:模架加工:1打编号,2 A/B板加工,3面板加工,4顶针固定板加工,5底板加工。
模架加工细节:
1,打编号要统一,模芯也要打上编号,应与模架上编号一致并且方向一致,装配时对准即可不易出错。
2,A/B板加工(即动定模框加工),a:A/B板加工应保证模框的平行度和垂直度为0.02mm,b :铣床加工:螺丝孔,运水孔,顶针孔,机咀孔,倒角c:钳工加工:攻牙,修毛边。
3,面板加工:铣床加工镗机咀孔或加工料嘴孔。
4,顶针固定板加工:铣床加工:顶针板与B板用回针连结,B板面向上,由上而下钻顶针孔,顶针沉头需把顶针板反过来底部向上,校正,先用钻头粗加工,再用铣刀精加工到位,倒角。
5,底板加工:铣床加工:划线,校正,镗孔,倒角。
(注:有些模具需强拉强顶的要加做强拉强顶机构,如在顶针板上加钻螺丝孔)
B:模芯加工:1飞边,2粗磨,3铣床加工,4钳工加工,5CNC粗加工,6热处理,7精磨,8CNC精加工,9电火花加工,10省模
模芯加工细节:
1)粗加工飞六边:在铣床上加工,保证垂直度和平行度,留磨余量1.2mm 2)粗磨:大水磨加工,先磨大面,用批司夹紧磨小面,保证垂直度和平行度在0.05mm,留余量双边0.6-0.8mm
3)铣床加工:先将铣床机头校正,保证在0.02mm之内,校正压紧工件,先加工螺丝孔,顶针孔,穿丝孔,镶针沉头开粗,机咀或料咀孔,分流锥孔倒角再做运水孔,铣R角。
4)钳工加工:攻牙,打字码
5)CNC粗加工
6)发外热处理HRC48-52
7)精磨;大水磨加工至比模框负0.04mm,保证平行度和垂直度在0.02mm 之内
8)CNC精加工
9)电火花加工
10)省模,保证光洁度,控制好型腔尺寸。
11)加工进浇口,排气,锌合金一般情况下浇口开0.3-0.5mm,排气开0.06-0.1mm,铝合金浇口开0.5-1.2mm排气开0.1-0.2,塑胶排气开0.01-0.02,尽量宽一点,薄一点。
C:模具零件加工:1滑块加工,2压紧块加工,3分流锥浇口套加工,4镶件加工
铝合金压铸模具的制作注意事项
压铸件加工是一种利用高压强制将金属溶液压入形状复杂的金属模具内的一种精密铸造法,为了更好的保证压铸件的特点,对于铝合金压铸加工中的一些事项还是需要引起注意的:
要知道,日常所用的合金金属的散热较好,很难形成瞬间难却的时候局部先后冷却的现象,而且合金的收缩率也相对较小,很难导致塑料产品缩水的现象,所以在压铸件加工设计的时候,不需要严格的厚度,但是要保证相对均匀。
另外,对于压铸设备的选择根据合金的不同选用的设备也不尽相同,基本上可以分为两类,一类是冷室机,另一类是热室机。
冷室机适合铜、镁、铝等高温合金,而锌、、锡、铅等一般使用热室机。
(注:文档可能无法思考全面,请浏览后下载,供参考。
可复制、编制,期待你的好评与关注)。