铝合金壳体压铸模具设计
铝合金盖体挤压铸造工艺与模具设计

田福祥
["] 保压时间
在保证制件成形密致和完全结晶凝固条件下, 保压 时间愈短愈好。一般挤压铸造的保压时间大约是金属 模重力浇注的 ’ 7 %。保压时间与铸件的断面最大厚度 有关, 一般为 & " + , ’ 8 7 66。例如制件最大壁厚为 !& 最大保压时间不超过 !& 8, 最小保压时间不低于 ’! 66, 此件需保压 %1 , 91 8。 8。按图 ’ 铸件的最大壁厚计算, !"% 浇注温度 通常根据金属的液相线温度和凝固范围确定合适 的浇注温度。在挤压铸造铝镁合金 #$%&’ 时, 浇注温度 选择在 +1& , :&& ; 较合适。 !"&
3.期刊论文 郭国文.陈维平.李元元.罗宗强 新型高强韧铝铜系合金的挤压铸造 -特种铸造及有色合金2003,""(z1)
为实现某种重载车辆负重轮的"以铸代锻",进行了负重轮简约化缩小模型挤压铸造的试验研究.采用自行研制的一种新型铝铜合金,结合挤压铸造工艺,制得了负 重轮模型铸件.挤压铸造工艺参数为:比压50 MPa,浇注温度720~730 ℃,摸具温度250~350 ℃,开始加压时间7~10 s,保压时间8~15 s.热处理后铸件的组织、性 能和断口形貌的检测结果表明,挤压铸件的晶粒更为细小,组织更加致密,T5和T6热处理的力学性能分别为抗拉强度428、440 MPa,屈服强度360、395 MPa,伸长率 13.1%、11.3%.与重力金属型铸造相比,挤压铸造使铸件的力学性能得到明显提高.
规定的温度。为了稳定工艺参数, 保证产品质量, 组合 凹模设有冷却水道, 通过调节水流大小把模具温度控制 在一定的范围内。 冲头由型芯、 顶杆和模套组合而成, 以形成铸件的 复杂内腔。 对图 # 所示模具, 模套、 顶杆和凹模采用 ’FG#H-I 钢, 热处理硬度 JKF$$ L $-; 型芯采用 H(-FG$I。为了 提高模具的使用寿命, 模具的工作表面进行氮化处理。 氮化 层 厚 度 一 般 为 + & ’) 11、 氮化后硬度 + & $+ 11, JKF). L .+。 模具工作过程: 调整好模具, 模具工作表面充分润 滑后, 将熔化的合金液用浇勺浇入凹模, 下降上模进行 模压, 机床压力升至缺陷临界值压力时进行保压。保压 完成后, 上模抬起, 组合冲头带着铸件升至一定高度以 后, 扳动副油缸控制管路上的操纵阀, 使高压油进入油 缸上部, 通过活塞杆、 顶板、 顶杆和模套, 将铸件推离组 合模芯。将上下模工作部分润滑后, 扳回控制阀手把,
铝压铸件的设计

铝合金压铸件的结构设计经验1。
考虑壁厚的问题,厚度的差距过大会对填充带来影响2。
考虑脱模问题,这点在压铸实际中非常重要,现实中往往回出现这样的问题,这比注塑脱模讨厌多了,所以拔模斜度的设置和动定模脱模力的计算要注意些,一般拔模斜度为1到3度,通常考虑到脱模的顺利性,外拔模要比内拔模的斜度要小些,外拔模也就1度,而内拔模要2~3度左右3。
设计时考虑到模具设计的问题,如果有多个位置的抽心位,尽量的放两边,最好不要放在下位抽心,这样时间长了下抽心会容易出问题4。
有些压铸件外观可能会有特殊的要求,如喷油、喷粉等,这时就要时结构避开重要外观位置便于设置浇口溢流槽5。
在结构上尽量的避免出现导致模具结构复杂的结构出现,如,不得不使用多个抽心或螺旋抽心等6。
对于需进行表面加工的零件,注意,需要在零件设计时给适合的加工留量,不能太多,否则加工人员会骂你的,而且会把里面的气孔都暴露出来的,不能太少,否则粗精定位一加工,得,黑皮还没干掉,你就等再在模具上打火花了,那给多少呢,留量最好不要大于0。
8mm,这样加工出来的面基本看不到气孔的,因为有硬质层的保护。
7。
再有就是注意选料了,是用ADC12还是A380等,要看具体的要求了8。
铝合金没有弹性,要做扣位只有和塑料配合。
9。
一般不能做深孔!在开模具时只做点孔,然后在后加工!10。
如果是薄壁零件与不能太薄,而且一定要用加强肋,增加抗弯能力!由于铝铸件的温度要在800摄氏度左右!模具寿命一般比较短一般做如电机外壳的话只有80K左右就再见了!1.压铸件的设计与塑胶件的设计比较相似,塑胶件的一些设计常规也适用于压铸件。
浅谈铝合金压铸件质量与模具设计的关系

2 . 2 型 腔数 的确 定
设备的能加 , 模具加工 的情 况、 生产数量 及铸件精 度要求等 都会影 响型腔 数的确 定。尤其是多型腔模具, 由于较大的模具加工难度 、 尺 寸精 度误差大、 不易均衡流道配 置, 使各型腔铸件性能不一致 。一般情况对压 铸 件的精度要 求很高 , 对于形状复杂 的压铸件 最好能做到一模一腔 。对 于小型铸 件则根据 具体情况进行确定 。
2 . 4 排 气 系统 设 计
模具要设置排气通道及 溢流槽并具有足够 的溢流 范围, 这是使产品 质量得到保证的关键 。人们常常对金属液过早堵死溢流通道 的情况视而 不见 , 采用 图 1 结构 , 可 以使 金属液 向溢流槽较深 的部位流入 , 使排气孔 直是通 流槽中的金
收稿 日期: 2 0 1 3 — 6 — 2 4
图 1溢流槽和排气
2 . 5 模 具 温 度
作为影响铸件质量 的一个 重要 因素的压铸模温度 , 如果其不合 理既 对铸件的 内外质量产生影 响还会 降低铸件尺寸精度甚至使铸件变形 , 龟
裂 的情况 出现在压铸模 时 , 使铸件表 面形成 网状 毛刺, 对压铸 件 的外观 质量产生影响。 例如铝合金温度达到 6 7 0 ~ 7 1 0 ℃浇入铸型, 总结相关生产
止模 具变形 。
2 I 3 浇 注 系统 的设 计
浇注 系统 既是液体金属充填压铸型 的通道 , 还可 以调节熔化液流动 速度 、 排气 条件及 传递压力等 。因此 , 进行浇注 系统的设计时 , 要对铸件 的结构特 点、 技术 要求、 合金种类及压铸机 的类 型等进 行认真分析 , 这样 才 可以设计 出合理 的浇注系统 。 目前没 有统 一 的计算 浇道 系统 的方法 ,一 般是 根据 经 验进 行设 计, 试模 调整 。 对于 浇道尺寸 根据 内浇 口截面积 进行确 定; 内浇 口截面 积 与浇道截 面积之 比是 1 : 3 1 : 4 ; 内浇 口厚 度与浇道 厚度之 比是 1 : 5 ~
铝合金压铸工艺中的模具设计
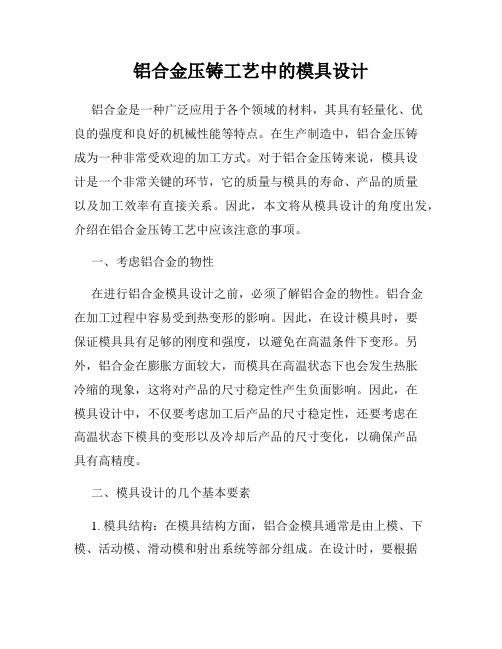
铝合金压铸工艺中的模具设计铝合金是一种广泛应用于各个领域的材料,其具有轻量化、优良的强度和良好的机械性能等特点。
在生产制造中,铝合金压铸成为一种非常受欢迎的加工方式。
对于铝合金压铸来说,模具设计是一个非常关键的环节,它的质量与模具的寿命、产品的质量以及加工效率有直接关系。
因此,本文将从模具设计的角度出发,介绍在铝合金压铸工艺中应该注意的事项。
一、考虑铝合金的物性在进行铝合金模具设计之前,必须了解铝合金的物性。
铝合金在加工过程中容易受到热变形的影响。
因此,在设计模具时,要保证模具具有足够的刚度和强度,以避免在高温条件下变形。
另外,铝合金在膨胀方面较大,而模具在高温状态下也会发生热胀冷缩的现象,这将对产品的尺寸稳定性产生负面影响。
因此,在模具设计中,不仅要考虑加工后产品的尺寸稳定性,还要考虑在高温状态下模具的变形以及冷却后产品的尺寸变化,以确保产品具有高精度。
二、模具设计的几个基本要素1. 模具结构:在模具结构方面,铝合金模具通常是由上模、下模、活动模、滑动模和射出系统等部分组成。
在设计时,要根据铝合金的物性和加工要求来确定模具结构和形状,以达到高效生产的目的。
2. 模具材料:在模具材料的选择方面,应根据铝合金的物性进行选择。
通常,适合用于铝合金模具的材料应具有高强度、高耐磨性和高温耐受性等特点。
目前,常用的模具材料有SKD61、H13和CRM等。
3. 考虑注塑工艺:在进行模具设计时,必须考虑到注塑工艺。
这意味着必须根据注塑工艺的参数来设计模具。
例如,应根据化学成分和温度参数来确定注塑机的射出系统和出口形状,以确保正常的注塑过程。
三、注塑机的选择在进行铝合金压铸加工时,注塑机的选择是非常关键的环节。
不同的注塑机具有不同的投影面积和射程,这会对产品的尺寸稳定性、成型速度和加工效率产生直接影响。
因此,在选择注塑机时,不仅要考虑加工数量和生产周期,还要考虑产品的几何形状、尺寸和质量要求。
四、模具维护模具在长期使用过程中,需要进行定期维护和保养。
铝合金压铸件的结构设计经验
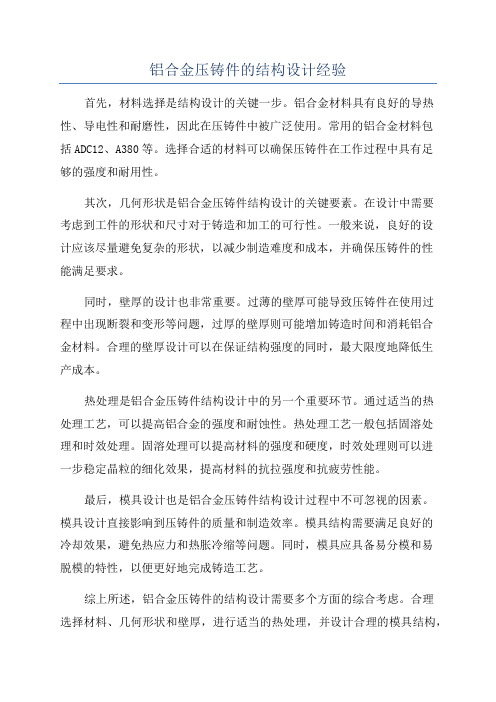
铝合金压铸件的结构设计经验首先,材料选择是结构设计的关键一步。
铝合金材料具有良好的导热性、导电性和耐磨性,因此在压铸件中被广泛使用。
常用的铝合金材料包括ADC12、A380等。
选择合适的材料可以确保压铸件在工作过程中具有足够的强度和耐用性。
其次,几何形状是铝合金压铸件结构设计的关键要素。
在设计中需要考虑到工件的形状和尺寸对于铸造和加工的可行性。
一般来说,良好的设计应该尽量避免复杂的形状,以减少制造难度和成本,并确保压铸件的性能满足要求。
同时,壁厚的设计也非常重要。
过薄的壁厚可能导致压铸件在使用过程中出现断裂和变形等问题,过厚的壁厚则可能增加铸造时间和消耗铝合金材料。
合理的壁厚设计可以在保证结构强度的同时,最大限度地降低生产成本。
热处理是铝合金压铸件结构设计中的另一个重要环节。
通过适当的热处理工艺,可以提高铝合金的强度和耐蚀性。
热处理工艺一般包括固溶处理和时效处理。
固溶处理可以提高材料的强度和硬度,时效处理则可以进一步稳定晶粒的细化效果,提高材料的抗拉强度和抗疲劳性能。
最后,模具设计也是铝合金压铸件结构设计过程中不可忽视的因素。
模具设计直接影响到压铸件的质量和制造效率。
模具结构需要满足良好的冷却效果,避免热应力和热胀冷缩等问题。
同时,模具应具备易分模和易脱模的特性,以便更好地完成铸造工艺。
综上所述,铝合金压铸件的结构设计需要多个方面的综合考虑。
合理选择材料、几何形状和壁厚,进行适当的热处理,并设计合理的模具结构,可以确保铝合金压铸件具有优良的性能和稳定的质量,满足不同工程领域的需求。
五金、铝合金压铸件的结构设计、生产工艺和相关模具

五金、铝合金压铸件的结构设计、生产工艺和相关模具一、铝合金压铸件的结构设计作为五金制品的一种,铝合金压铸件在工业生产中具有很重要的作用,它广泛应用于汽车零部件、摩托车零部件、自行车零部件、电工设备、航空航天领域等。
铝合金压铸件的结构设计是非常重要的,它直接影响到产品的质量和使用性能。
1.结构设计原则(1)设计合理性:要求产品设计合理,能够满足产品的使用要求和生产工艺要求。
(2)易于加工:要求产品的结构设计能够方便加工和生产,减少生产成本。
(3)适应性强:要求产品的结构设计能够适应不同的工艺要求和使用环境。
2.结构设计要点(1)壁厚:对于铝合金压铸件来说,壁厚的设计是非常重要的,壁厚太厚容易造成收缩不均匀、气泡、裂纹等问题,壁厚太薄则会影响产品的强度和稳定性。
(2)加工余量:在设计铝合金压铸件时需要考虑到加工余量,保证产品在结束后进行加工时不会出现问题。
(3)结构形式:产品的结构形式要具有设计的合理性和美学性,能够顺应现代的审美观念。
(4)浇口设计:浇口的设计直接影响到产品的成型质量,需要设计合理的浇口位置和形式。
3.结构设计方法(1)CAD设计:利用CAD软件进行产品的三维设计和分析,可以有效地减少设计过程中的错误和成本。
(2)模具设计:根据产品的结构设计进行模具的设计,保证产品的生产质量和效率。
二、铝合金压铸件的生产工艺铝合金压铸件的生产工艺是一个复杂的过程,需要结合材料特性和模具设计才能完成。
生产工艺的质量直接关系到产品的质量和性能。
1.型腔填充铝合金压铸件的成型过程是通过将铝合金在一定的温度下充入模具中,并施加一定的压力来完成的。
型腔填充是成型过程中的关键一步,需要确保模具内的铝合金能够充分填满型腔,避免气泡和缩松等问题的产生。
2.固化冷却在型腔充填完成后,需要将模具进行固化冷却,使铝合金在模具中凝固成型。
固化冷却过程中需要控制温度和时间,保证产品的成型质量。
3.反压和除渣在成型后的铝合金压铸件表面可能会出现一些氧化物和杂质,需要进行反压和除渣处理,保证产品的表面质量。
浅谈铝合金压铸生产中模具的设计制造

浅谈铝合金压铸生产中模具的设计制造摘要:铝合金压铸模具是进行压铸生产的重要工艺装备,同时,也是铝合金压铸生产中三大必备因素之一。
文章首先分析了铝合金压铸模具设计制造技术,其次,就铝合金压铸模具设计制造中需要注意的几个技术问题进行了深入的探讨,具有一定的参考价值。
关键词:铝合金;压铸模具;制造技术铝合金压铸模具是进行压铸生产的重要工艺装备,同时,也是铝合金压铸生产中三大必备因素之一。
生产过程能否顺利进行,铸件质量是否有保证,在很大程度上取决于模具结构的合理性和技术上的先进性。
铝合金压铸模设计制造的优劣,直接影响压铸件的形状、尺寸、强度、表面质量等方面。
而压铸件的质量和稳定性,反映出整个压铸生产过程和压铸模制造过程的技术水平和经济效益。
1铝合金压铸模具设计在铝合金压铸模具设计过程中必须全面分析压铸件结构,熟悉压铸机操作过程,了解压铸机及工艺参数得以调整的可能性及范围,掌握在不同压铸条件下的金属液填充特性和流动特性,并考虑到经济因素,才能设计出切合实际并满足生产要求的压铸模。
铝合金压铸模设计前,设计人员应对所提供的设计依据,包括压铸产品图和生产纲领进行工艺分析,并进行如下必要准备:①根据产品图,对所选用的压铸合金、压铸件的形状、结构、精度和技术要求进行工艺性分析,确定机械加工部位、加工余量和机械加工时所要采取的工艺措施以及定位基准等。
②根据产品图和生产纲领,确定压射比压,计算锁模力:估算压铸件所需的开模力和推出力,以及压铸机的开模距离;选定压铸机的型号和规格。
③根据产品和压铸机的型号和规格,对模具结构进行初步分析,选择分型面和确定型腔数量;选择内浇口进口位置,确定浇注系统和溢流槽、排气槽朗总体布置方案;对带嵌件的压铸件,要考虑嵌件的装夹和固定方式;确定功模和定模镶块,动模和定模套板外形尺寸,以及导核、导套的位置和尺寸;确定冷却和加热管道的位置和尺寸,控制压铸过程的热平衡等。
④绘制压铸件毛坯图。
包括分型面位置、浇注系统、溢流槽和排气槽,推出元件的位置和尺寸以及机械加工余量、加工基准等数值。
铝合金箱体压铸模具设计说明书

毕业设计(论文)任务书 2015 届机械工程及自动化专业题目:铝合金箱体压铸模具的设计子题:学生姓名:班级学号:指导教师:职称:所在系(教研室):机电与信息工程系下达日期:2014年7月4日完成日期:2015年5月8日摘要压铸模具是铸造液态模锻的一种方法,一种在专用的压铸模锻机上完成的工艺。
它的基本工艺过程是:金属液先低速或高速铸造充型进模具的型腔内,模具有活动的型腔面,它随着金属液的冷却过程加压锻造,既消除毛坯的缩孔缩松缺陷,也使毛坯的内部组织达到锻态的破碎晶粒。
毛坯的综合机械性能得到显著的提高。
本文运用大学所学的知识,了解压铸模具的工作原理,在此基础上,设计一款铝合金箱体压铸模具。
通过查找相关资料,了解铝合金箱体压铸模具的内部结构和工作原理,构建了铝合金箱体压铸模具组成结构的总的指导思想,从而得出了该铝合金箱体压铸模具的优点是高效,经济,并且运行效果好,运行平稳的结论。
关键词:铝合金箱体压铸模具;型腔;效率;模具AbstractThe environment of global economic development, China industries affected by other countries advanced technology at the same time, foreign enterprises and brand spread to more and more Chinese has become an opportunity. Cap pressing machine in industry through a variety of ways have been working with the relevant technology, and constantly improve their own strength and core competitiveness, and narrow the gap with developed countries.In the new market demand, update the sleeve pressing machine is a pressing matter of the moment. The production of pipe pressing machine equipment manufacturing enterprises to fully tap the potential of the market, vigorously develop the sleeves of large low cost pressing special machinery and equipment, plays a positive role in the evolution of automatic assembly, the assembly of mechanical equipment. There is a large pipe equipment on equipment safety index has strict requirements of production. In the production equipment of enterprises, give full consideration to the possible problems in the operation of the equipment, so as to reduce the noise pollution caused by vibration or improper operation of equipment phenomenon and manufacturing of domestic pipe pressing equipment with global appeal, economic, security and stability of the theme consistent. Increase and production pipe pressing equipment of new energy saving.Key word:pneumatic manipulator;cylinder;pneumatic loop;Fout degrees of freedom.目录摘要 (1)Abstract (2)第一章绪论 (3)1.1 模具介绍 (4)1.2 模具在加工工业中的地位................... 错误!未定义书签。
- 1、下载文档前请自行甄别文档内容的完整性,平台不提供额外的编辑、内容补充、找答案等附加服务。
- 2、"仅部分预览"的文档,不可在线预览部分如存在完整性等问题,可反馈申请退款(可完整预览的文档不适用该条件!)。
- 3、如文档侵犯您的权益,请联系客服反馈,我们会尽快为您处理(人工客服工作时间:9:00-18:30)。
铝合金壳体压铸模具设计
摘要:
关键词:
压铸模具;三维设计;UG;工艺设计
1铝合金后壳闷盖压铸件结构与工艺分析
1.1压铸件结构从图1中可看出,该后壳闷盖铸件结构比较简单,铸件壁厚基本均匀,存在两个铸出孔,但是因为铸出孔的壁略厚,热节很容易出现,该压铸件整体壁厚较为均匀,壁厚选择时应综合考量多种因素:压铸件结构、材料性能以及所设计的压铸工艺等,只有采用薄壁或者均匀的壁厚才能要符合各个方面的需求。
1.2铸件外侧边缘的最小壁厚良好的铸件成形条件,要求保持一定的外侧边缘壁厚,边缘壁厚s与深度h的关系为s≥(1/4~1/3)hmm。
当h<4.5mm时,则s≥1.5mm。
1.3压铸材料该压铸件材质为压铸铝合金,其牌号为YZAlSi9Cu4,抗拉强度为240MPa,布氏硬度85HBS,平均收缩率为0.6%。
所选合金引起铸造性能良好,特别适合于压铸。
1.4铸造圆角半径为了使金属液流动更流畅,且很容易气体排出,结构中设计使用铸造圆角,且利用圆角来替代结构锐角还可以避免产生裂纹。
所设计的结构圆角的半径值取决于结构壁厚值,范围一般为
0.5~1mm。
1.5脱模斜度选取脱模斜度要综合考量多种因素:铸件几何形状(深度、壁厚、型腔或型芯表面)、粗糙度、加工纹路方向等。
考量上述各因素,所设计铸件的壳体脱模斜度:外表面的α=30′,而其内表面的β=1°。
2压铸工艺参数设计
2.1压铸机选择选择压铸机必须先确定锁模力。
锁模力作用有二:一
个是用来平衡反压力,以达到锁紧分型面的目的;一个是用来阻止飞
溅的金属液,以达到获得目标尺寸精度的目的。
设计的铸件不存在分
胀型力,因为此模具是没有侧抽芯的(压铸件无侧孔与侧凹)。
因此F 锁≥KF主=1.25×1288.352=1610.44kN根据上述计算得到锁模力的值
还有铸件重量,根据这两个主要因素进行压铸机选择,最后选用机型为:卧式冷室压铸机(2500kN)———J1125型,主要参数:①最大金属浇注量———3.2Kg,②模具厚度———250~650mm,③动模座板行程———400mm,④压射力———143~280kN。
2.2压铸压力压铸工艺中压铸压力是主要参数之一,因此掌握液态金
属在压铸过程中上的压力变化情况,对压铸过程中各阶段的压力进行
合理控制,具有重要意义:①获得合格铸件———致密的组织,清晰
的轮廓;②初算压射比压———根据所选压射力计算。
压射比压还与
模具型腔空间、铸件壁厚、金属液流程等因素相关,结合所设计模具
的具体参数,以及初算值,此压铸模的压射比压最终定为90MPa。
2.3压铸速度压铸速度的选择有以下两方面:压射速度选择和充型速
度选择。
两种速度的选择至关重要,其直接决定了铸件内在外在的质
量及轮廓清晰度等。
选择充型速度时考虑因素:①铸件的大小、②铸
件结构的复杂程度、③铸件所选合金的种类、④压射比压的高低。
具
体选择:①充型较容易的———壁厚简单或有较高的内部质量要求的
铸件,选择:低速、高比压、大浇口;②需要快速充型———复杂薄
壁或有较高的表面质量要求的铸件,选择:高速,高比压。
综合考量,根据本压铸件的具体特点———结构较简单,选择中速,范围为20~
90m/s。
2.4压铸时间确定压铸时间,其由三部分所需时间组成:充型时间、
持压时间及压铸件在压铸模具中停留的时间。
几种因素综合作用产生
了这种结果:压力、速度、温度、金属液特征,以及铸件结构(主要
是壁厚和体积)和模具结构(特别是浇注系统和排溢系统)等因素。
充型时间大多在0.01~0.2s之间。
其长短由铸件的大小以及结构的复
杂程度决定:结构简单体积大的铸件,需要相对长些的充型时间;结
构较复杂和壁厚较小的铸件,所需时间短。
经实践检验,充型时间定
为0.2s左右,对于本文设计的中小型铝合金压铸件是比较合理的。
持
压时间作用是:压射冲头有足够的时间对未凝固的金属施压,使得结
晶过程可以在压力下进行,增强补缩,成功获得致密组织。
影响时间
长短的因素:所选合金熔点、结晶温度范围和铸件壁厚等。
熔点高、
范围大、壁厚大的铸件所需时间较长,2~3s;当所确定时间过短,则
缩松现象会出现,但并不是持压时间延长就能起到显著的效果。
1~2s
为一般持压时间范围。
本设计中铸件的平均壁厚为3mm、考虑其结构以及合金性质,选择3s作为持压时间。
2.5压铸温度保证合格铸件的主要工艺参数———金属液的浇注温度
以及模具的工作温度,影响它的因素有许多:铸件的结构、壁厚、充
型的压力、速度以及合金种类等。
需要通过综合考量上述参数,保证
压铸温度稳定处于合理范围内,提供良好的充型条件。
浇注温度不在
合理的范围内会造成产品质量下降甚至不合格:①过高的浇注温度———冷却时会造成过大的收缩,产品易形成裂纹,产生较粗大的晶粒,较差的力学性能,甚至造成粘模,降低模具寿命;②过低的浇注温度———造成缺陷包括冷隔、表面花纹和浇注不足等。
为了获得合格铸件,除了需要考虑浇注温度外,还应该同时考虑压力、压铸模具温度、充型速度以及铸件所选合金。
本压铸件选用铝硅合金,根据其流动性
及模具特性,选定620℃作为压铸温度。
3后壳闷盖压铸件模具结构设计
3.1分型面的确定该零件结构简单,按分型面选取原则,应选择最大
投影截面处,如图2所示分型面。
3.2浇注系统的设计浇注系统由四部分组成:①直浇道、②横浇道、
③内浇口、④冷料穴。
具体设计:①整体式压室———压室与浇口套
的连接方式;②横浇道的截面形状———扁梯形;③内浇口———环
型侧浇口;④侧浇口———布置在铸件的分型面上;⑤一模四腔,图3为具体结构形式。
3.3溢流槽与排气系统设计对溢流槽进行结构设计,综合考量各种因
素选择的截面形状为梯形(图4)。
合理的结构具有以下作用:①改善模具的热平衡状态———调节模具各处的温度,减少铸件出现流痕、
冷隔和浇不足的现象,转移缩孔、缩松、涡流裹气;②排出型腔中的
气体———配合排气槽迅速排气;③储存冷污金属液———涂料残渣
和气体的混合体。
3.4顶出系统的设计在压铸过程中,一个完整的成形周期结束后需要
开模取压铸件,会在凸模一侧发现被包裹着的压铸件,需要将其取下,此任务需要附加一种顶件机构来执行。
模具结构设计中顶出系统占有
重要地位,构成顶出系统主要有三部分:①顶出、②复位、③导向。
本套模具采用两种顶杆顶出机构,分别用于铸件顶出和浇道顶出,顶
杆直径分别为6mm和8mm。
在系统中设计限位装置:①限位块、②复位杆,用以提高机构的复位精度以及防止机构部件运动过程中行程超限。
3.5成型零件尺寸计算
3.5.1型腔与型芯尺寸:
3.5.2计算中心距离、位置尺寸:式中:L'-成型部分的中心距离、位置的平均尺寸(mm);L-压铸件中心距离、位置的平均尺寸(mm)。
3.6冷却系统的设计选择高效、易控制的模具冷却方法———水冷,
用以获得高质量铸件和长的模具使用寿命。
水冷的冷却效果取决于冷
却水道的布局,将其布置在型腔内:①温度最高、②热量比较集中、
③模具下面、④操作者的对面一侧。
为了提高输水胶管安装便利性,
要求统一水道的外径几何尺寸。
其结构布置见图5所示。
3.7压铸模总装图作出后壳闷盖压铸模具的总装配图(图6)。
压铸
模由两部分组成:定模、动模。
定模静止不动,位于定模板上,动模
随着随动板移动,位于随动模固定板上,通过动模相对于动模的运动
实现合模、开模。
①合模:二者闭合形成型腔,高压下使用浇注系统
用金属液对型腔进行充填;②开模:保压后二者分离,推出机构完成
从型腔中推出产品的任务。
4结束语
参考文献
1杨裕国.压铸工艺与模具设计M.北京:机械工业出版社.2009.
2姜银方,顾卫星.压铸模具工程师手册M.北京:机械工业出版
社.2009.
3姜彬.UG压铸模具设计入门及提高M.北京:电子工业出版社.2003.
4刘传胜.铝合金高压压铸模拟分析J.武汉科技大学学报.2005,28(1):28-31.
5毛平淮,互换性与测量技术基础M.北京:机械工业出版社.2010.
6朱先琦,胡群林.UG环境下端盖的三维建模及压铸模设计J.安徽工程科技学院学报,2005,20(2):45-47.
7间德海,王琳琳.连接盘压铸模设计J.模具工业,2014,40(6):62-64.
8董艺,范晓明,张荣华.基于Pro/E软件的阀盖压铸模设计J.热加工
工艺,2010,39(21):174-176.
铝合金壳体压铸模具设计。