浅谈铝合金压铸模
铝合金压铸模具失效分析及寿命提高措施

铝合金压铸模具失效分析及寿命提高措施摘要:各类工业技术的高速发展带动着压铸技术得到了相对广泛的应用,其中最具有代表性的便是铝合金压铸模具。
而从具体工作展开与推进上来看,铝合金压铸模具会受到材料、压铸方式以及外界因素的综合影响,出现压铸失效的情况造成材料的过度浪费。
由此,要对铝合金压铸模具失效的情况进行分析,寻找提高使用寿命的各类方式。
关键词:铝合金;压铸技术;模具;使用寿命引言压铸技术自诞生以来,常常被用在高强度、公差小且精准度高的各类合金生产当中,其中又以铝合金压铸最具代表性,在汽车制造行业有着较广的应用范围。
在近几年间,社会对铝合金压铸模具的整体需求量呈现出逐步上涨的趋势,对铝合金压铸成效的要求也相对较高,需要相关工作者明确生产当中可能会出现模具失效各类情况,延长模具本身的使用寿命,带动国内铝合金压铸技术的全面发展。
一、铝合金压铸模具的常见失效形式(一)热裂在对金属类材料展开现代化的加工时,往往需要对金属材料采取高温加工的方式,提高金属材料可塑性的同时,优化后期压铸成效。
在高温加工当中,热裂属于一类相对常见的问题,也是压铸模具技术在应用当中出现概率最高的失效情况。
从各项数据上来看,超过八成的压铸模具失效,都是受到模具钢在应用当中出现热疲劳抗力下降以及高温环境下稳定能力较弱而诱发的。
金属类材料基本都存在有疲劳度极限,而模具钢在应用过程中会长时间处在高温环境下,进而在热疲劳上会出现逐步下降的情况,持续高温软化与冷却工作,会是的金属材料在这一过程中慢慢丧失优质的变形抗力,此时金属材料的应变力会持续上升到金属疲劳度的峰值。
铝合金压铸模具在生产当中所受到的热应力会呈现出周期性的变化,而材料表面此时也会因外力作用而出现塑性压应变以及弹性拉应变,随着变形次数的增加,材料表面的氧化膜会出现破损问题,以此来释放剩余的应力。
如果所释放的剩余应力已经超过材料本身的承受能力,则会在模具材料上出现热裂问题。
需要注意的是,热裂纹在形成方面,往往会集中在模具的型腔位置以及热应力相对集中的位置,在出现热裂现象后,模具所受到的应力会表现出二次分布的情况,使得热裂范围逐步增加。
铝压铸模具简介

鋁壓鑄模具簡介一.壓鑄模概述:(1).鋁壓鑄是采用機械設備將液態鋁合金快速注入永久性鋼模中,經冷卻成型后出模,反復高效地生產.(2).壓鑄成型的特點是效率高,精度高,表面質量好,后續加工簡易.二.壓鑄模的基本要求:(1).在冷熱交替的生產中不可過早地出現龜裂老化現象.(2).不可被鋁水沖刷而侵蝕模具,造成精度,外觀等不良.(3).出模容易,可連續地大量生產,后續加工方便.(4).制品表面無縮水凹陷,針孔,花紋等,干燒400℃,10分鐘不起泡鼓脹.三. 壓鑄模的設計制造:1. 由于模具需在200℃左右的模溫和高壓狀態下工作,受熱膨脹等影響,避免設計“斜頂”結構.若產品結構需要,要設計抽芯成型,則可考慮設計中子(油缸動作)抽芯或滑塊(角梢動作)抽芯來完成.2. 避免燒焊,保証模具壽命.3. 正確地設計分型面,為開設澆道,澆口.冷料井和排气道及后續加工作準備.a. 澆道:澆道也即橫澆道,可分為三大類:(1)錐形.例K40.H56;(2)扇形.例雙片三明治模具;(3)螃蟹形.例K98-1.主澆道一般都開成梯形截面,此特點是冷料少,加工容易.寬深比為3:1,最大深度在15mm以下,出模斜度為單邊10度,底部R5.澆道開公模還是開母模,取決于進澆口角度的需要,以進澆順暢為原則,可減少紊(亂)流,減少气體的卷入.同時也減少模仁的沖蝕和粘模的出現.b. 澆口:即進澆口,分二種類形:(1).澆道開至距產品1mm處,由另一模仁開進澆口.(2).由澆道延伸直至進澆型腔.澆口開設需注意二個問題:a.產品在澆口附近有鑲針時要加擋點分流,以免沖斷鑲針,b.澆口厚度一般在1.0-1.5之間,任何情況下澆口厚度必須小于平均肉厚.澆口截面的計算:Ag=V/Vg*t其中: Ag為澆口截面.單位:平方毫米v為通過澆口的鑄件體積,包括冷料和成品,單位立方厘米Vg為進澆速度,平均肉厚1.8-2.0時取30-40m/s’T為鑄造時間,取0.02-0.04 S’c 分型面:一般設計在平均肉厚的高度上,分型面的設計與澆道.澆口的設計是互相關聯的,同時分型面的設計也是冷料井和排氣道制造的前提,分型面不設計過多的枕位,以減少挂模,飛料,枕位壓爛的異常.d.冷料井,排气道:顧名思義.冷料井就是排除冷料,同時與排气道作用排出型腔氣體.冷料井還可作為產品出模時頂出用,尤其是在產品上不宜設置頂針時,例H40烤盤.排气道分二類:一是以厚0.1-0.15,寬10-20轉折1-2次后修出模框;二是以R4-R5開半圓形槽,連接多個冷料井后開至排氣塊,由排氣塊排氣也有采用抽真空排氣的設計.e. 加工量:蘭圖尺寸是我們的產品尺寸,鋁合金的縮水率為0.5%,同時車邊,磨邊等加工量都是模具制造時必須考慮到的.4.模具與機台: 模具設計時,可按下列方案評估配用機台.T=1.3*A*P/1000其中: T為鎖模力,單位:吨1.3為糸數,可放寬至1.5.A為成品投影面積,單位:平方厘米P為鑄造壓力,單位:Kg/平方厘米1000(Kg)=1(吨)在確定好所對應機台后,灌口尺寸參照下列數值選擇:150T:ψ50. ψ60.250T: ψ50 . ψ60 . ψ70.420T: ψ60 . ψ60 . ψ80.500T: ψ70 . ψ80.800T: ψ80 . ψ100 . ψ120.在同一機台,灌口尺寸選大則能提供的最大鑄造壓力將減小.5.模具與鋼材: 現廣泛使用的模仁材質為ASSAB 8407,SKD61;模框材質為FCD-50;頂針鑲針為加硬的SKD61.(1). 模仁一般是粗加工后作淬火加硬,然后再精加工,最后作回火消除應力處理,回火至硬度HRC44-48.(2)目前公司產品大多采用ψ3,ψ3.5糸列螺絲.要鋁制品上,ψ2.7. ψ3.2的螺孔一般用ψ4.0頂針磨成鑲針,生產部門把ψ4.0頂針作為常用備件,這為維修提供方便.生產部門曾多次發文,要求用鑲針成型螺孔,而不是用人工鑽孔加工螺孔.6.冷卻水路:分三大類型 a.直通水路:b.沿產品較厚部位開設回型水路;c.公母模仁凸出較高常采用點水路,即采用分水片或內外套管循環水路,水路型腔距離以20平方厘米為宜.7.出模斜度:一般設計為3度,特殊要求需圖面標示清楚.8.拋光與表面處理:為減少制品表面的水紋,模具不會作亮面拋光,一般拋至#320-#400油石即可.沒有對壓鑄模作電鍍的做法,但氮化,電火花披復,ABP(噴丸 )等處理的效果仍需大家評論.在制造時只進行到淬火,回火,其它熱處理要求必須載明于合約書上.四.壓鑄模的試模:(1).已完成制造的模具,要根據設計的機台頓位上模.(2)正確連接所有水路路並開1/2水量,對模面涂布重(機油)或壓鑄專用脫模劑.(3)開機用慢射做15-30模次,使模溫提升至150℃以上.(4).切換為快射,同時配合調整各個壓力.時間.距離等參數以達到制品表面效果較好.若模溫升至200℃或更高,須將水路全開.(5). 鋁湯溫度以650-670℃為宜.。
浅谈汽车齿轮箱铝合金压铸模选材与强化

碳 化物 不均 匀等 将 急剧 降低 热 疲 劳 寿命 , 中夹 钢
杂物是 热疲 劳龟裂 源 。机械 冲蚀 主要是 磨蚀 和气
先 进水平 。
二 、 效 分 析 与 压 铸 模 性 能 指 标 失 ( ) 疲 劳 龟 裂 一 热
经模 具解 剖和热 稳定 曲线 与热 疲劳 试样 剖面
上硬 度变 化 , 得模具 型 面温度 : 口处 8 0 测 浇 0 ℃~ 80 、 腔 70 ~ 70 2℃ 型 0℃ 5 ℃。高 温 急热 使 模 具 产
N O 4Vo . .院学 报 NE ANGZ YE I HUXUEY UI HI S UANX UEB AO
・ 6 ・ 5
浅 谈 汽 车 齿 轮 箱 铝 合 金 压 铸 模 选 材 与 强 化
李 聪 , 周 常 春
6 1O ) 4 l O
采用 壁厚 不均 匀 的薄壁 结构 , 圆角 过渡 , 避免 尖角 锐边 , 出模 斜 度宜 大 不 宜小 , 增强 抗 热疲 劳 性 能 , 减少模 具 热载 荷 , 止产 生 热 裂 纹 和 引起 崩 块 和 防
断裂 失效 。
( ) 腔 塑 性 变 形 三 型
倍, 且具 有低 粗糙 度值 的光 洁表 面 , 到 同类 产 品 达
钢 。试 验 表 明 : 选用 4 rMo Ni c 3 2 VNb B精 炼 压 铸 模钢, 采用 复合强 化处 理新 工艺 , 使用 寿命 比原用
3 rw8 电炉 钢 制 该 模 常 规 热 处 理 提 高 3 4 C2 V ~
过 烧 和 晶粒 粗 大 , 导致 晶界 结合 力 降低 , 脆性 大 , 屈服 强度 急剧 降低 等上 述 因素均 会造成 压铸 模服 役 时发 生早 中期 崩块 断 裂 失 效 。因 此 , 铸件 宜 压
铝合金压铸模具失效原因与寿命关系分析

模具型腔或其它部位在使用中产生变形,使得工件表面质量下降或影响压铸正常进行的现象称为变形失效。变形失效又可分为损伤性变形失效和非损伤性变形失效。最常见的损伤性变形失效是模具工作时因粘有工件留下的毛刺、微粒等,在模具表面造成压痕、塌陷,或者由于设计不当,型腔局部温度过高而软化等。非损伤性变形多发生在长效模具上,且尤以发生于模架者为多。可见,模架的组织稳定处理、中间去应力回火等均应受到充分重视。
[2]铝合金压铸模具龟裂失效分析[J].赵建伟.??中国金属通报.?2020(01)
[3]浅谈压铸模结构对铸件质量及模具寿命的影响[J].吴燕华,王宏霞,朱芬芳.??模具制造.?2015(07)
[4]我国中高档压铸模的发展成为产业突破重点[J]. ??模具工业.?2012(10)
[5]浅谈如何提高低压铸模寿命[J].安琳,张响.??铸造技术.?2007(10)
(3)冷却水道与镶件型腔有足够的距离目前大多数模具采用水冷却,目的是保持模具有良好的热平衡性,避免局部受热不均。
3.2模具材料与模具制造
模具材料与模具制造是保证模具有较长的寿命关键之一。模具型腔承受巨大的交变应力作用,要求镶件材料在高温下有好的热韧性,才能经受得冷热交替作用。
(1)模具材料
模具套板多采用45钢且调质处理。镶件的材料要求较高,产品产量小于3万套,镶件可选用一般国产H13或是3Cr2W8V即可,比较经济;产量在3万~7万套,可选用日本牌号SKD61,DH31-S,价格中等;对于产量高于7万套,最好选用品质较高的热模钢,如瑞典一胜百8407,DIEVAR和德国葛利兹2344supper等。当然上面谈到压铸模数也不是绝对的,在同等的模具和压铸工艺条件下,如大型、结构复杂的模具寿命自然会低很多,小型结构简单的模具寿命自然会高很多。
浅谈铝合金压铸件质量与模具设计的关系

2 . 2 型 腔数 的确 定
设备的能加 , 模具加工 的情 况、 生产数量 及铸件精 度要求等 都会影 响型腔 数的确 定。尤其是多型腔模具, 由于较大的模具加工难度 、 尺 寸精 度误差大、 不易均衡流道配 置, 使各型腔铸件性能不一致 。一般情况对压 铸 件的精度要 求很高 , 对于形状复杂 的压铸件 最好能做到一模一腔 。对 于小型铸 件则根据 具体情况进行确定 。
2 . 4 排 气 系统 设 计
模具要设置排气通道及 溢流槽并具有足够 的溢流 范围, 这是使产品 质量得到保证的关键 。人们常常对金属液过早堵死溢流通道 的情况视而 不见 , 采用 图 1 结构 , 可 以使 金属液 向溢流槽较深 的部位流入 , 使排气孔 直是通 流槽中的金
收稿 日期: 2 0 1 3 — 6 — 2 4
图 1溢流槽和排气
2 . 5 模 具 温 度
作为影响铸件质量 的一个 重要 因素的压铸模温度 , 如果其不合 理既 对铸件的 内外质量产生影 响还会 降低铸件尺寸精度甚至使铸件变形 , 龟
裂 的情况 出现在压铸模 时 , 使铸件表 面形成 网状 毛刺, 对压铸 件 的外观 质量产生影响。 例如铝合金温度达到 6 7 0 ~ 7 1 0 ℃浇入铸型, 总结相关生产
止模 具变形 。
2 I 3 浇 注 系统 的设 计
浇注 系统 既是液体金属充填压铸型 的通道 , 还可 以调节熔化液流动 速度 、 排气 条件及 传递压力等 。因此 , 进行浇注 系统的设计时 , 要对铸件 的结构特 点、 技术 要求、 合金种类及压铸机 的类 型等进 行认真分析 , 这样 才 可以设计 出合理 的浇注系统 。 目前没 有统 一 的计算 浇道 系统 的方法 ,一 般是 根据 经 验进 行设 计, 试模 调整 。 对于 浇道尺寸 根据 内浇 口截面积 进行确 定; 内浇 口截面 积 与浇道截 面积之 比是 1 : 3 1 : 4 ; 内浇 口厚 度与浇道 厚度之 比是 1 : 5 ~
铝合金压铸特点
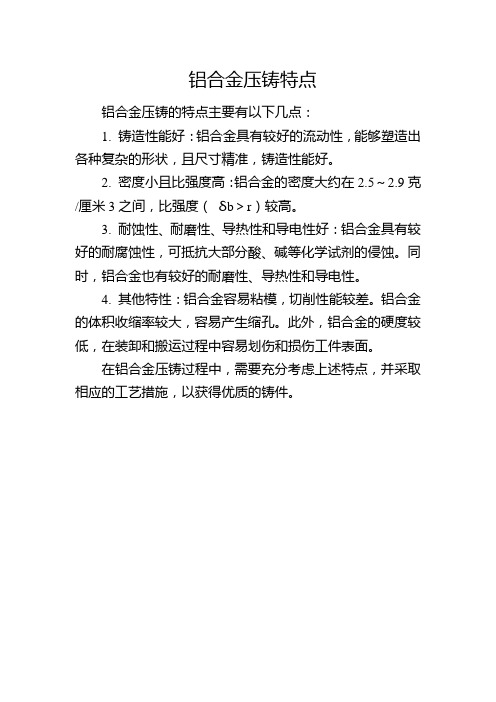
铝合金压铸特点
铝合金压铸的特点主要有以下几点:
1. 铸造性能好:铝合金具有较好的流动性,能够塑造出各种复杂的形状,且尺寸精准,铸造性能好。
2. 密度小且比强度高:铝合金的密度大约在2.5~2.9克/厘米3之间,比强度(δb>r)较高。
3. 耐蚀性、耐磨性、导热性和导电性好:铝合金具有较好的耐腐蚀性,可抵抗大部分酸、碱等化学试剂的侵蚀。
同时,铝合金也有较好的耐磨性、导热性和导电性。
4. 其他特性:铝合金容易粘模,切削性能较差。
铝合金的体积收缩率较大,容易产生缩孔。
此外,铝合金的硬度较低,在装卸和搬运过程中容易划伤和损伤工件表面。
在铝合金压铸过程中,需要充分考虑上述特点,并采取相应的工艺措施,以获得优质的铸件。
铝合金压铸工艺中的模具设计
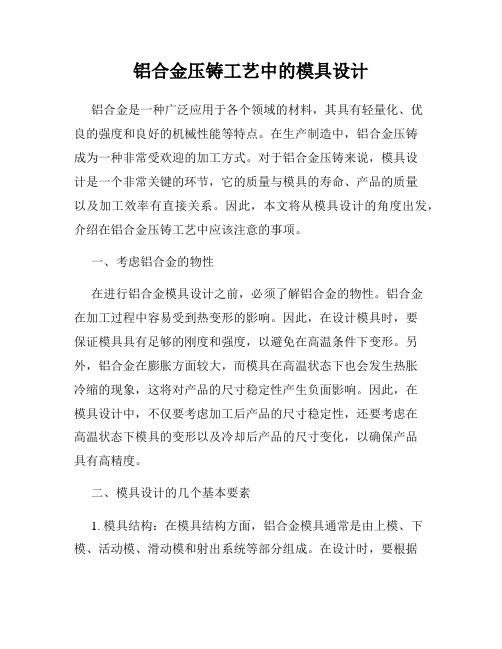
铝合金压铸工艺中的模具设计铝合金是一种广泛应用于各个领域的材料,其具有轻量化、优良的强度和良好的机械性能等特点。
在生产制造中,铝合金压铸成为一种非常受欢迎的加工方式。
对于铝合金压铸来说,模具设计是一个非常关键的环节,它的质量与模具的寿命、产品的质量以及加工效率有直接关系。
因此,本文将从模具设计的角度出发,介绍在铝合金压铸工艺中应该注意的事项。
一、考虑铝合金的物性在进行铝合金模具设计之前,必须了解铝合金的物性。
铝合金在加工过程中容易受到热变形的影响。
因此,在设计模具时,要保证模具具有足够的刚度和强度,以避免在高温条件下变形。
另外,铝合金在膨胀方面较大,而模具在高温状态下也会发生热胀冷缩的现象,这将对产品的尺寸稳定性产生负面影响。
因此,在模具设计中,不仅要考虑加工后产品的尺寸稳定性,还要考虑在高温状态下模具的变形以及冷却后产品的尺寸变化,以确保产品具有高精度。
二、模具设计的几个基本要素1. 模具结构:在模具结构方面,铝合金模具通常是由上模、下模、活动模、滑动模和射出系统等部分组成。
在设计时,要根据铝合金的物性和加工要求来确定模具结构和形状,以达到高效生产的目的。
2. 模具材料:在模具材料的选择方面,应根据铝合金的物性进行选择。
通常,适合用于铝合金模具的材料应具有高强度、高耐磨性和高温耐受性等特点。
目前,常用的模具材料有SKD61、H13和CRM等。
3. 考虑注塑工艺:在进行模具设计时,必须考虑到注塑工艺。
这意味着必须根据注塑工艺的参数来设计模具。
例如,应根据化学成分和温度参数来确定注塑机的射出系统和出口形状,以确保正常的注塑过程。
三、注塑机的选择在进行铝合金压铸加工时,注塑机的选择是非常关键的环节。
不同的注塑机具有不同的投影面积和射程,这会对产品的尺寸稳定性、成型速度和加工效率产生直接影响。
因此,在选择注塑机时,不仅要考虑加工数量和生产周期,还要考虑产品的几何形状、尺寸和质量要求。
四、模具维护模具在长期使用过程中,需要进行定期维护和保养。
铝压铸模具材料
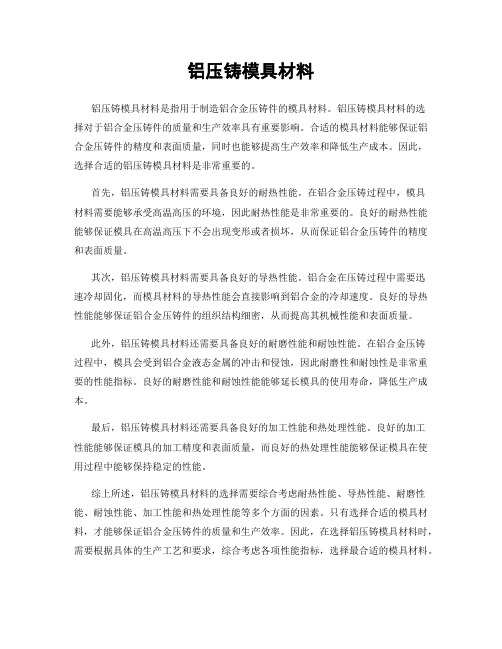
铝压铸模具材料铝压铸模具材料是指用于制造铝合金压铸件的模具材料。
铝压铸模具材料的选择对于铝合金压铸件的质量和生产效率具有重要影响。
合适的模具材料能够保证铝合金压铸件的精度和表面质量,同时也能够提高生产效率和降低生产成本。
因此,选择合适的铝压铸模具材料是非常重要的。
首先,铝压铸模具材料需要具备良好的耐热性能。
在铝合金压铸过程中,模具材料需要能够承受高温高压的环境,因此耐热性能是非常重要的。
良好的耐热性能能够保证模具在高温高压下不会出现变形或者损坏,从而保证铝合金压铸件的精度和表面质量。
其次,铝压铸模具材料需要具备良好的导热性能。
铝合金在压铸过程中需要迅速冷却固化,而模具材料的导热性能会直接影响到铝合金的冷却速度。
良好的导热性能能够保证铝合金压铸件的组织结构细密,从而提高其机械性能和表面质量。
此外,铝压铸模具材料还需要具备良好的耐磨性能和耐蚀性能。
在铝合金压铸过程中,模具会受到铝合金液态金属的冲击和侵蚀,因此耐磨性和耐蚀性是非常重要的性能指标。
良好的耐磨性能和耐蚀性能能够延长模具的使用寿命,降低生产成本。
最后,铝压铸模具材料还需要具备良好的加工性能和热处理性能。
良好的加工性能能够保证模具的加工精度和表面质量,而良好的热处理性能能够保证模具在使用过程中能够保持稳定的性能。
综上所述,铝压铸模具材料的选择需要综合考虑耐热性能、导热性能、耐磨性能、耐蚀性能、加工性能和热处理性能等多个方面的因素。
只有选择合适的模具材料,才能够保证铝合金压铸件的质量和生产效率。
因此,在选择铝压铸模具材料时,需要根据具体的生产工艺和要求,综合考虑各项性能指标,选择最合适的模具材料。
- 1、下载文档前请自行甄别文档内容的完整性,平台不提供额外的编辑、内容补充、找答案等附加服务。
- 2、"仅部分预览"的文档,不可在线预览部分如存在完整性等问题,可反馈申请退款(可完整预览的文档不适用该条件!)。
- 3、如文档侵犯您的权益,请联系客服反馈,我们会尽快为您处理(人工客服工作时间:9:00-18:30)。
一·前言铝合金以其低密度高强度越来越多得到广泛应用,经过对铝合金化学成分的组成与优化,铝合金的铸造成型工艺、热挤压加工工艺和人工时效等工艺,使铝合金的性能得到发挥,铝合金压铸类产品主要用于电子、汽车、电机、家电和一些通讯行业,一些高性能、高精度、高韧性的优质铝合金产品也被应用到大型飞机、船舶等技术要求比较高的行业中,但是其主要应用还是在一些机械零件中。
铝合金压铸工艺较其他铝合金成型工艺有其自身的优势:压铸范围广;逐渐尺寸精度高、稳定性好;表面粗糙度低;生产率高;金属利用率高;铸件强度和表面硬度高等等。
二·服役条件铝合金压铸模属于热作模具。
热作模具在工作时承受巨大的冲击力、压应力、张应力、弯曲应力,模具型腔与高温(有时可达1150~1200℃)金属接触后,本身温度可达300~400℃,局部高达500~600℃。
还经常受空气、油、水等的反复冷却,在时热时冷的苛刻条件下工作的模具,其型腔表面极易产生疲劳裂纹(即龟裂)。
此外,炽热的金属在模具型腔中变形所产生的强烈摩擦,容易因摩擦而使精度降低,因而要求热作模具钢具有足够的热强行、热疲劳性、韧性、硬度和耐磨性、良好的导热性和耐蚀性,还要求具有较高的淬透性,以保证整个截面具有一致的力学性能。
三·材料的选择根据被加工金属的种类、负荷大小、使用温度和成形速度等条件,提出不同的要求来选用不同的热作模具钢种。
热作模具钢的ω(c)一般在0.3~0.6%,含碳量过高时,钢的韧性和塑性下降,导热性较差;含碳量过低时,硬度和耐磨性达不到要求。
热作模具钢中一般加入Cr、Mn、Ni、Si等元素以强化铁素体基体,提高钢的淬透性强度和韧性,Ni还能改善热疲劳抗力,为了细化晶粒提高强度和硬度、回火稳定性,防止回火脆性,还加入Ni、Mo、V等元素。
此外,Ni、Mo、V等元素在回火时以碳化物的形式析出产生二次硬化,使热作模具钢在较高温度下仍能保持较高的强度。
一般把热作模具钢分为三类:(1)高韧性热作模具钢 5CrMnMo、5CrNiMo、4Cr5MoVSi(H11)等,适宜制作一般的锻造模具;(2)高热强钢 3Cr2W8V、Y4、Y10、以及基体钢5Cr4Mo2W2SiV等,宜用作热挤压模、压铸模等;(3)强韧兼备的热作模具钢 4Cr5MoV1Si(H13)、HM3、4Cr5W2SiV等,宜用作热锻模、热挤压模、压铸模等、高速锻模。
目前一般用作压铸模的钢种有H13钢、3Cr2W8V钢,传统用钢是3Cr2W8V钢。
这类钢属于中耐热韧性模具钢,这类钢与低耐热高韧性热作模具钢相比主要特点是含有较多的Cr、Mo、V、W等碳化物形成元素以及含碳量较低,ω(c)一般为0.32~0.45。
由于钢中含较多的Cr元素,因而具有很好的淬透性,直径100mm的棒材在空气淬火的条件下可完全淬透,故被称为空冷硬化热作模具钢。
在截面尺寸<150mm时具有与5CrNiMo钢相近的韧性,而在工作温度500~600℃却具有更高的硬度、热强性和耐磨性。
与4Cr5MoSiV相比,H13(4Cr5MoSiV1)的热强性和硬度更高,在中温条件下具有较高的热强度,热疲劳性能、高的韧性和一定的耐磨性;在较低的奥氏体化温度条件下进行空气淬火,热变形处理变形小,空冷淬火时产生氧化皮的倾向小,而且可以抵抗熔融铝的冲蚀作用。
4Cr5MoSiV1钢,即美国钢号AISI-H13,也是日本钢号JIS-SKD61,是国际上广泛应用的一种空冷硬化热作模具钢,进口设备上都配用H13钢制造的模具。
H13钢有较高的韧性和耐冷热疲劳性能,不容易产生热疲劳裂纹,即使出现了热疲劳裂纹也细而且短,不容易扩展,因此用其制作的模具生产的压铸件外观质量有很大的提高。
模具在使用前无须预热,而且可以采用自来水喷冷,以抑制模具的升温,减轻了操作工人的劳动强度。
该钢材同时具备较高的热强性,是一种强韧兼备的优质廉价钢种,既可用作热锻模材料,也可在模腔升温低于600℃的工况下用作压铸模材料。
H13钢的化学成分(质量分数)如下:C:0.32%~0.45%;Si:0.80%~1.20%;Mn:0.20%~0.50%;Cr:4.75%~5.50%; Mo:1.10%~1.7-5%;Ni≤0.25%;V:0.80%~1.20%;P≤0.03%;S≤0.03%。
H13钢的物理性能、力学性能如下:线膨胀系数αl:11.5×10-6/℃,(22~500℃);12.2×10-6/℃,(22~800℃);热导率λ:28.4W/(m·K) (800℃);密度ρ:7.8g/cm3 ,(20℃);7.7g/cm3 ,(400℃);临界点:Ac1 860℃;Ac3 915℃;Ar1 775℃;Ar3 815℃;Ms 340℃。
四·模具的热处理工艺该铝合金压铸模的生产工艺流程图如下:下料锻造球化退火粗加工稳定处理精加工淬火两次回火钳修打磨渗碳或渗氮本文仅对模具的热处理工艺做详细研究,机加工工艺不做评述。
1 锻造经下料后须锻造成毛坯件,而不是将原料直接进行机加工成毛坯件,一方面减少材料的损耗,节约材料:另一方面,经锻造后,钢发生塑性变形,晶胞拉伸,成形变胞,沿流线方向的抗拉强度大,有利于提高毛坯件的强度。
首先对型材进行加热,加热温度1100~1160℃,始锻温度1060~1150℃,以保证锻造过程中钢处于奥氏体状态,可塑性强,终锻温度≥800℃。
2 球化退火加热保温时间和等温时间由模具材料、尺寸及加热设备类型而定,模具退火一般采用箱式炉,加热保温时间按照模具有效厚度计算,加热系数1~2min\mm。
原始组织的好坏对模具钢的韧性和冷热疲劳性能有很大的影响,为改善热作模具钢的强韧性配合,对于性能要求比较高的模具,可采用预调质处理或者采用淬火加高温回火或退火相结合的方法,以获得细小的珠光体和细小弥散分布的碳化物组织,为最终热处理提供很均匀的组织,从而使得最终热处理后能达到优良的强韧性配合。
在等温球化退火工艺的制定过程中,奥氏体化温度及等温转变温度十分重要。
奥氏体化温度较高时,未溶碳化物数量较少,奥氏体晶粒较大,而且其中的碳含量的分布也比较均匀,因而有利于球化过程的进行。
等温转变温度较低时,碳(及合金元素)在奥氏体中扩散较困难,也不利于球化过程的进行。
只有当奥氏体温度较低,等温转变温度较高的处理规程下,才能得到球化组织。
等温球化退火规范:首先毛坯入炉,随炉升温缓慢加热,加热至Ac1+(20~30℃),保温3~4h,经查表,H13钢的Ac1为860℃,故升温加热至880℃~890℃并保温3~4h;然后随炉缓冷至Ar1-(20~30℃)保温4~5h,经查表H13钢的Ar1为775℃,故升温加热至745℃~755℃并保温4~5h;然后再随炉缓冷至550℃,空冷至室温。
经硬度检测,硬度可达229HBW,共晶碳化物等级≤3级。
如果钢中的原始组织网状碳化物较严重,则需要加热到略高于Acm的温度,使碳化物网溶入奥氏体,然后再较快地冷却到Ar1一下温度进行等温球化退火。
经过球化退火,可使可切削性能大大提高;在淬火时,溶入奥氏体的碳化物较均匀;淬火开裂和淬火变形减轻;而韧性有所增加等等多方面有所改善。
3 淬火热挤压模具钢的淬火工艺过程包括预热、解热、保温、冷却和均热。
由于这类钢合金元素含量较高,钢的导热性较差,所以在对钢进行加热时必须严格控制加热速度。
1)预热在空气介质加热炉中加热时可以控制加热速度,使其以很缓慢的速度进行升温,在盐浴炉中想控制其加热速度是很困难的,因此必须采取预热的方法。
预热次数的多少取决于钢的成分和模具变形的要求:对于般要求变形不严格的模具,在不开裂的情况下预热次数可适当少些,但对于变形要求严格的模具必须多次预热。
在较低的温度预热一般是在空气介质加热炉中进行的,两段预热的加热速度必须缓慢进行,一般≤30~60℃/min。
因为钢在这个温度范围处于弹性状态,内外温差所产生的热应力一旦超过弹性极限就会开裂。
当钢的温度高于650℃开始转入塑性状态,当热应力达到一定数值时,钢将产生塑性变形,从而使内应力下降,因此此时加热速度可适当快些(≤80~100℃/min),当然对于变形要求严格的模具来书,这一段时间的加热速度仍然不必过快。
综合以上因素考虑,对于该模具使用的H13钢选择550℃、850℃两个温度进行预热。
2)淬火加热温度淬火加热温度取决于钢的成分和使用要求,对于同一种钢来说,当要求有较高的韧性时,往往采用较低的温度淬火;当要求较好的高温强度时,则采用较高的淬火温度。
对于该模具选择淬火加热温度1020~1050℃,属于完全淬火,该加热温度使钢完全奥氏体化。
淬火加热为了保证模具表面不脱碳,需采用脱氧保护良好的氯化钡盐浴炉中进行加热。
3)淬火保温时间淬火保温时间应保证使钢的原始组织能够全部形成奥氏体,同时还必须保证碳化物能够充分溶解,设溶解后含碳量和合金元素能够充分地扩散,从而达到奥氏体均匀化。
这样,保证热作模具刚具有较好的高温性能,这一点非常重要。
所以,一般热作模具钢的淬火保温时间较长,在盐浴炉中加热淬火保温时间系数一般是0.5~1min/mm,模具尺寸小,系数取上限。
4)冷却冷却以大于钢临界冷速的冷却速度冷却到室温。
中耐热韧性模具钢由于淬透性很高,一般可采用油冷或空冷,对于变形较小的模具也可采用在500~600℃等温后空冷,冷却介质的选择必须考虑到对性能的要求,同时为使冷却时热应力尽量下,故尽可能地选择冷却能力较低的介质。
对于该模具可选择油作为淬火介质。
5)均热中耐热韧性模具钢的热应力较大,为防止开裂和变形,绝对不允许冷却到室温,一般冷到150~180℃,均热后应立即回火,均热时间可按照0.6min/mm计算。
淬火后,钢获得马氏体组织,强度、硬度均有所提高,冷却后硬度为57~60HRC。
4 回火回火的目的就是使模具达到一定的硬度和韧性,并消除淬火应力。
为保证在使用中的组织稳定性和内应力尽可能小,挥回火时间必须充分,一般回火时间可按3min/mm。
但最少不低于2h。
对于二次硬化热作模具钢,淬火后组织中存在一定量的残余奥氏体,第一次回火后,在冷却过程中,这些残余奥氏体基本上转变为相应的等温产物,这些产物较脆,往往会成为开裂的根源,故必须进行第二次回火,有时为了使用上的要求也可进行第三次回火。