铝合金压铸件外观质量标准(2012.5)
压铸件外观通用检验标准(带图实例)
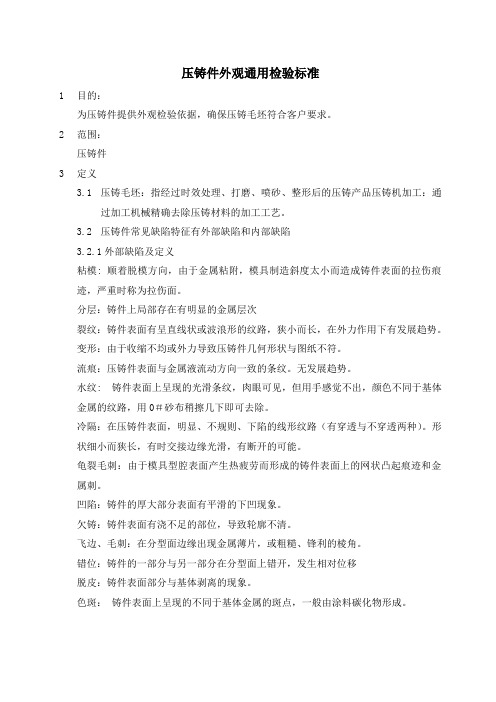
压铸件外观通用检验标准
1目的:
为压铸件提供外观检验依据,确保压铸毛坯符合客户要求。
2范围:
压铸件
3定义
3.1压铸毛坯:指经过时效处理、打磨、喷砂、整形后的压铸产品压铸机加工:通
过加工机械精确去除压铸材料的加工工艺。
3.2压铸件常见缺陷特征有外部缺陷和内部缺陷
3.2.1外部缺陷及定义
粘模: 顺着脱模方向,由于金属粘附,模具制造斜度太小而造成铸件表面的拉伤痕迹,严重时称为拉伤面。
分层:铸件上局部存在有明显的金属层次
裂纹:铸件表面有呈直线状或波浪形的纹路,狭小而长,在外力作用下有发展趋势。
变形:由于收缩不均或外力导致压铸件几何形状与图纸不符。
流痕:压铸件表面与金属液流动方向一致的条纹。
无发展趋势。
水纹: 铸件表面上呈现的光滑条纹,肉眼可见,但用手感觉不出,颜色不同于基体金属的纹路,用0#砂布稍擦几下即可去除。
冷隔:在压铸件表面,明显、不规则、下陷的线形纹路(有穿透与不穿透两种)。
形状细小而狭长,有时交接边缘光滑,有断开的可能。
龟裂毛刺:由于模具型腔表面产生热疲劳而形成的铸件表面上的网状凸起痕迹和金属刺。
凹陷:铸件的厚大部分表面有平滑的下凹现象。
欠铸:铸件表面有浇不足的部位,导致轮廓不清。
飞边、毛刺:在分型面边缘出现金属薄片,或粗糙、锋利的棱角。
错位:铸件的一部分与另一部分在分型面上错开,发生相对位移
脱皮:铸件表面部分与基体剥离的现象。
色斑:铸件表面上呈现的不同于基体金属的斑点,一般由涂料碳化物形成。
铝合金压铸件外观标准

铝合金压铸件外观标准
铝合金压铸件是一种常见的金属零件,广泛应用于汽车、航空航天、电子通讯
等领域。
其外观质量直接影响产品的整体美观度和性能表现,因此对铝合金压铸件的外观标准要求非常严格。
首先,铝合金压铸件的外观应该整体平整,没有凹凸不平或者明显的表面缺陷。
表面不应该有气泡、砂眼、裂纹等缺陷,否则会影响产品的强度和密封性能。
此外,外观应该干净整洁,不应该有油污、杂质等污染物,以保证产品的使用寿命和安全性。
其次,铝合金压铸件的尺寸和形状应该符合设计要求,没有明显的偏差。
尺寸
的偏差会直接影响产品的装配和使用效果,因此在生产过程中需要严格控制尺寸的精度,确保产品的稳定性和可靠性。
另外,铝合金压铸件的表面光洁度也是一个重要的外观标准。
产品的表面应该
光滑、无划痕、无氧化层,色泽均匀一致。
如果产品表面有划痕或者氧化层,会直接影响产品的美观度和耐腐蚀性能,降低产品的使用寿命。
最后,铝合金压铸件的外观标准还包括产品的标识和包装。
产品的标识应该清
晰可见,包括产品型号、生产日期、质量标志等信息,以便于用户使用和管理。
产品的包装应该牢固可靠,能够有效保护产品不受损坏,在运输和储存过程中保持产品的外观完好。
综上所述,铝合金压铸件的外观标准是一个综合性的要求,涉及产品的外观质量、尺寸精度、表面光洁度、标识和包装等方面。
只有严格按照外观标准要求进行生产和检验,才能保证铝合金压铸件的质量稳定,满足用户的需求和期望。
压铸铝合金产品外观检验标准

压铸铝合金产品外观检验标准1.外观缺陷检查:(1)表面缺陷:包括表面气泡、缩孔、气孔、夹渣、皱纹、划痕、氧化皮、裂纹等。
(2)几何尺寸检查:包括产品尺寸、形状、平整度、垂直度、圆度等。
(3)光泽度检查:包括产品的亮度、反光度和颜色。
2.外观检验方法:(1)目视检查法:通过直接观察产品表面,发现表面缺陷。
(2)放大镜法:使用放大镜对产品表面进行检查,以发现微小缺陷。
(3)试验片法:将产品与已知合格的试验片进行对比,检查产品表面是否存在缺陷。
(4)光源法:使用光源对产品表面进行照射,以发现表面缺陷。
3.外观检验标准:(1)根据产品的不同用途,制定不同的外观检验标准。
一般可参照相关国家或地区的标准,如ISO、ASTM、JIS等。
(2)可根据产品的外观质量要求确定检验标准,如表面缺陷的数量、大小、位置等指标。
(3)外观检验标准应确保产品的外观质量满足客户的需求,并在一定范围内允许存在一定的缺陷。
4.外观检验流程:(1)根据产品的设计要求和相关标准确定外观检验的项目和标准。
(2)对产品进行外观检查,记录表面缺陷的种类、数量和位置。
(3)对外观缺陷进行分类和判定,判断是否符合产品的质量要求。
(4)将产品分为合格品和不合格品,合格品可以销售,不合格品需要进行修复或淘汰。
5.外观检验的重要性:(1)外观是产品的第一印象,直接影响消费者对产品的购买决策。
外观缺陷会降低产品的美观性和使用寿命。
(2)外观缺陷可能会导致产品的性能下降,如气孔可能导致产品的强度降低。
(3)外观检验是对压铸工艺的控制和过程优化的一个重要手段,能够发现生产过程中的问题并进行调整,提高产品的质量和生产效率。
综上所述,压铸铝合金产品的外观检验是确保产品质量和生产过程控制的重要环节。
制定合适的外观检验标准,并进行有效的检验方法,能够及时发现和解决外观缺陷问题,提高产品的质量和市场竞争力。
铝合金压铸件及表面处理零件外观检验标准

压铸件外观检验标准1.目的:规范和统一公司压铸件及表面处理零件外观标准。
2.范围:适用于公司所生产的所有压铸件、表面处理零件产品,客户特别规定的除外。
3.权责:本标准由品质部编制,运用于判定压铸件外观缺陷及接收标准。
4.定义4.1压铸件、表面处理等级一级:产品外露表面即装饰表面,表面处理为抛光或电镀零件。
二级:安装前可见的表面,壳体内表面等。
三级:结构件,非外露表面或零件。
4.2压铸件表面缺陷描述流痕:在表面出现波浪或条纹,原因为流入模具内的熔汤熔融状态不充分。
充填不良:由于模具充填不充分而导致零件部分缺省。
裂缝:由于外力产生微小的裂纹。
原因为铸件凝固收缩,或脱模时包紧力过大。
缩限:材料有像火山口一样的凹陷。
原因为铸件在肉厚处的收缩。
起泡:铸件表面的气孔,有像水泡或肿块凸起,为铸件开模或热处理时表面气体膨胀。
积炭:熔汤熔着模具表面,使得铸件表面产生缺肉或粗糙的现象。
模裂纹:模具表面有热裂纹的伤痕时使得铸件表面产生同样形状的伤痕。
冲蚀:熔汤高温高速冲蚀模具,使得铸件产生与模具相同的伤痕。
脱皮:铸件表面部分剥离的现象,最易发生在表面光滑的铸件上。
针孔:氢气导致针状细小的砂孔,因除气不彻底产生的内部缺陷。
擦伤:由于磨损使表面不理想,有比较长的痕迹。
缩孔:因熔汤凝固收缩而产生的内部砂孔。
气孔:因卷入气体或空气导致铸件内部存在的砂孔。
玷污:其它材料或其它材料的加入使表面变色,如机器润滑油,离型剂等。
隔层:铸件层剥皮。
变形:产品收缩应力或顶出变形。
凹陷:由于不同的材料的结合度和收缩率不同,引起表面凹陷。
拉伤:铸件表面的磨损或磨擦使得表面不理想。
腐蚀:在材质表面有不连续的痕迹,由氧化引起。
凹痕:由于挤压或撞击而产生的凹坑。
毛刺:在孔或边有粗糙和锋利的棱角(相对于材料的厚度和凸起的高度)。
冷隔:在两处或更多的材料融合点有线条(并且终止了结合或流动)分模线:在模具的两块或镶块之间有一条明显的线,例如:如果模具安装不当,在模具的主要部分能明显的看到明显的看到微小的凸起的线条。
铝合金压铸件检验标准
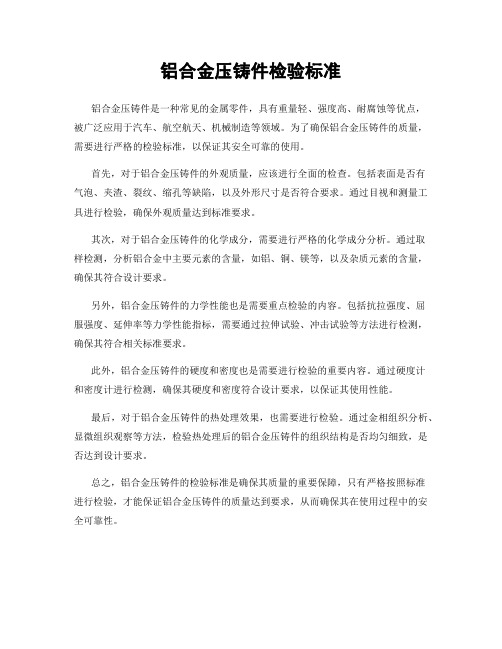
铝合金压铸件检验标准
铝合金压铸件是一种常见的金属零件,具有重量轻、强度高、耐腐蚀等优点,
被广泛应用于汽车、航空航天、机械制造等领域。
为了确保铝合金压铸件的质量,需要进行严格的检验标准,以保证其安全可靠的使用。
首先,对于铝合金压铸件的外观质量,应该进行全面的检查。
包括表面是否有
气泡、夹渣、裂纹、缩孔等缺陷,以及外形尺寸是否符合要求。
通过目视和测量工具进行检验,确保外观质量达到标准要求。
其次,对于铝合金压铸件的化学成分,需要进行严格的化学成分分析。
通过取
样检测,分析铝合金中主要元素的含量,如铝、铜、镁等,以及杂质元素的含量,确保其符合设计要求。
另外,铝合金压铸件的力学性能也是需要重点检验的内容。
包括抗拉强度、屈
服强度、延伸率等力学性能指标,需要通过拉伸试验、冲击试验等方法进行检测,确保其符合相关标准要求。
此外,铝合金压铸件的硬度和密度也是需要进行检验的重要内容。
通过硬度计
和密度计进行检测,确保其硬度和密度符合设计要求,以保证其使用性能。
最后,对于铝合金压铸件的热处理效果,也需要进行检验。
通过金相组织分析、显微组织观察等方法,检验热处理后的铝合金压铸件的组织结构是否均匀细致,是否达到设计要求。
总之,铝合金压铸件的检验标准是确保其质量的重要保障,只有严格按照标准
进行检验,才能保证铝合金压铸件的质量达到要求,从而确保其在使用过程中的安全可靠性。
铝合金压铸件检验标准
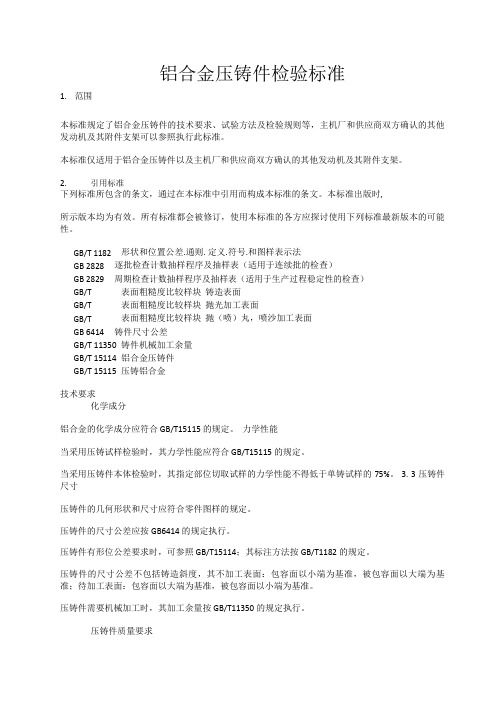
铝合金压铸件检验标准1.范围本标准规定了铝合金压铸件的技术要求、试验方法及检验规则等,主机厂和供应商双方确认的其他发动机及其附件支架可以参照执行此标准。
本标准仅适用于铝合金压铸件以及主机厂和供应商双方确认的其他发动机及其附件支架。
2.引用标准下列标准所包含的条文,通过在本标准中引用而构成本标准的条文。
本标准出版时,所示版本均为有效。
所有标准都会被修订,使用本标准的各方应探讨使用下列标准最新版本的可能性。
GB/T 1182形状和位置公差.通则. 定义.符号.和图样表示法GB 2828逐批检查计数抽样程序及抽样表(适用于连续批的检查)GB 2829周期检查计数抽样程序及抽样表(适用于生产过程稳定性的检查)GB/T 表面粗糙度比较样块铸造表面GB/T 表面粗糙度比较样块抛光加工表面GB/T 表面粗糙度比较样块抛(喷)丸,喷沙加工表面GB 6414铸件尺寸公差GB/T 11350铸件机械加工余量GB/T 15114铝合金压铸件GB/T 15115压铸铝合金技术要求化学成分铝合金的化学成分应符合 GB/T15115 的规定。
力学性能当采用压铸试样检验时,其力学性能应符合 GB/T15115 的规定。
当采用压铸件本体检验时,其指定部位切取试样的力学性能不得低于单铸试样的 75%。
3. 3 压铸件尺寸压铸件的几何形状和尺寸应符合零件图样的规定。
压铸件的尺寸公差应按 GB6414 的规定执行。
压铸件有形位公差要求时,可参照 GB/T15114;其标注方法按 GB/T1182 的规定。
压铸件的尺寸公差不包括铸造斜度,其不加工表面:包容面以小端为基准,被包容面以大端为基准;待加工表面:包容面以大端为基准,被包容面以小端为基准。
压铸件需要机械加工时,其加工余量按 GB/T11350 的规定执行。
压铸件质量要求压铸件应符合零件图样的规定。
表面质量压铸件表面粗糙度应符合 GB/ 的规定。
压铸件表面不允许有裂纹、欠铸、疏松、气泡和任何穿透性缺陷。
压铸件外观通用检验标准(带图实例)
压铸件外观通用检验标准1目的:为压铸件提供外观检验依据,确保压铸毛坯符合客户要求。
2范围:压铸件3定义3.1压铸毛坯:指经过时效处理、打磨、喷砂、整形后的压铸产品压铸机加工:通过加工机械精确去除压铸材料的加工工艺。
3.2压铸件常见缺陷特征有外部缺陷和内部缺陷3.2.1外部缺陷及定义粘模: 顺着脱模方向,由于金属粘附,模具制造斜度太小而造成铸件表面的拉伤痕迹,严重时称为拉伤面。
分层:铸件上局部存在有明显的金属层次裂纹:铸件表面有呈直线状或波浪形的纹路,狭小而长,在外力作用下有发展趋势。
变形:由于收缩不均或外力导致压铸件几何形状与图纸不符。
流痕:压铸件表面与金属液流动方向一致的条纹。
无发展趋势。
水纹: 铸件表面上呈现的光滑条纹,肉眼可见,但用手感觉不出,颜色不同于基体金属的纹路,用0#砂布稍擦几下即可去除。
冷隔:在压铸件表面,明显、不规则、下陷的线形纹路(有穿透与不穿透两种)。
形状细小而狭长,有时交接边缘光滑,有断开的可能。
龟裂毛刺:由于模具型腔表面产生热疲劳而形成的铸件表面上的网状凸起痕迹和金属刺。
凹陷:铸件的厚大部分表面有平滑的下凹现象。
欠铸:铸件表面有浇不足的部位,导致轮廓不清。
飞边、毛刺:在分型面边缘出现金属薄片,或粗糙、锋利的棱角。
错位:铸件的一部分与另一部分在分型面上错开,发生相对位移脱皮:铸件表面部分与基体剥离的现象。
色斑:铸件表面上呈现的不同于基体金属的斑点,一般由涂料碳化物形成。
32.2内部缺陷及定义砂孔:在压铸件中,由于压铸的特殊性,铝合金是在高温、高速、高压的状态下成型的,所以压铸件内部是不可避免的存在孔洞,我们统称这些孔洞为砂孔。
缩孔:铸件凝固过程中,金属补偿不足所形成的呈现暗色、形状不规则的孔洞,即为缩孔气孔:因卷入气体而导致的压铸件内部的孔状缺陷,解剖后外观检查或探伤检查,气孔具有光滑的表面、形状为圆形。
脆性:铸件基体金属晶粒过于粗大或极小,使铸件易断裂或破碎渗漏:压铸件经耐压试验,产生漏气、渗水硬点:机械加工过程或加工后外观检查或金相检查:铸件上有硬度高于金属基体的细小质点或块状物使刀具磨损严重,加工后常常显示出不同的亮度。
压铸铝合金产品外观检验标准
2、变形:图面上有具体要求,以图面要求为准。未注形位公差以国标为准。
3、裂纹:除用清理方法可去除且不影响产品外观、功能的裂纹外,产品上不允许。
的与金属基体颜色不一致无
方向性的纹路,无发展趋势。
压铸件表面有明显的、不规则
的、下陷线性纹路(有穿透与
6
冷隔
不穿透2种)形状细小而狭长,
有时交接边缘光滑,在外力作
用下有发展的可能。
7
网状毛刺、龟裂纹
压铸件表面上有网状发丝一样凸起或凹陷的痕迹,随压铸次数增加而不断扩大和延伸。
8
凹陷
铸件平滑表面上出现凹陷部位。
表4可接受表面缺陷总数限定
表面大小
可接受缺陷总数
1级面
2级面
3级面
小面
2
4
5
中面
4
8
10
大面
5
12
15
超大面
7
15
20
7.2
7.2.1压铸件表面外观缺陷定义
表5压铸件表面外观缺陷定义
序号
缺陷名称
缺陷定义
图例
序号
缺陷名称
缺陷定义
图例
1
拉伤
沿开模方向铸件表面呈现条状的拉伤痕迹,有一定深度,严重时为一面状伤痕;另一种是金属液与模具产生焊合、粘附而拉伤,以致铸件表面多肉或缺肉。
0.80
0.30
>250~400
1.10
0.40
>400~630
1.50
压铸铝合金产品外观检验标准
被检表面按其面积或最大外形尺寸划分为不同大小类别,当有两个条件满足时、以大的一类
为准。表面大小划分标准如表2。(注:一般情况下,被检表面上的缺陷个数超过2个时,缺陷之间的距离必须大于10 mm,否则视为同一缺陷,尺寸以其总和计。)
表3表面大小类别划分
表面大小
划分标准
按面积(mm2)
按最大外形尺寸(mm)
的与金属基体颜色不一致无
方向性的纹路,无发展趋势。
压铸件表面有明显的、不规则
的、下陷线性纹路(有穿透与
6
冷隔
不穿透2种)形状细小而狭长,
有时交接边缘光滑,在外力作
用下有发展的可能。
7
网状毛刺、龟裂纹
压铸件表面上有网状发丝一样凸起或凹陷的痕迹,随压铸次数增加而不断扩大和延伸。
8
凹陷
铸件平滑表面上出现凹陷部位。
序号
缺陷名称
缺陷定义
图例
9
欠铸、轮廓不清
铸件表面有浇不足部位,轮廓不清。
10
毛刺、飞边
压铸件在分型面边缘上出现金属薄片。
11
分层、隔皮
铸件上局部存在有明显的金属层次。
12
变色斑点
铸件表面上呈现不同于基体金属颜色的斑点。
13
粘附物痕迹
其它材料(如机器润滑油、离型剂等)的加入,使铸件表面呈现不同于基体金属颜色的斑点和痕迹。
表4可接受表面缺陷总数限定
表面大小
可接受缺陷总数
1级面
2级面
3级面
小面
2
4
5
中面
4
8
10
大面
5
12
15
超大面
7
15
20
铝合金压铸件检验标准
铝合金压铸件检验标准1.范围本标准规定了铝合金压铸件的技术要求、试验方法及检验规则等,主机厂和供应商双方确认的其他发动机及其附件支架可以参照执行此标准。
本标准仅适用于铝合金压铸件以及主机厂和供应商双方确认的其他发动机及其附件支架。
2.引用标准下列标准所包含的条文,通过在本标准中引用而构成本标准的条文。
本标准出版时,所示版本均为有效。
所有标准都会被修订,使用本标准的各方应探讨使用下列标准最新版本的可能性。
GB/T 1182 形状和位置公差.通则.定义.符号.和图样表示法GB 2828 逐批检查计数抽样程序及抽样表(适用于连续批的检查)GB 2829 周期检查计数抽样程序及抽样表(适用于生产过程稳定性的检查)GB/T 6060.1 表面粗糙度比较样块铸造表面GB/T 6060.4 表面粗糙度比较样块抛光加工表面GB/T 6060.5 表面粗糙度比较样块抛(喷)丸,喷沙加工表面GB 6414 铸件尺寸公差GB/T 11350 铸件机械加工余量GB/T 15114 铝合金压铸件GB/T 15115 压铸铝合金3.技术要求3.1化学成分铝合金的化学成分应符合GB/T15115的规定。
3.2 力学性能3.2.1当采用压铸试样检验时,其力学性能应符合GB/T15115的规定。
3.2.2当采用压铸件本体检验时,其指定部位切取试样的力学性能不得低于单铸试样的75%。
3. 3 压铸件尺寸3.3.1压铸件的几何形状和尺寸应符合零件图样的规定。
3.3.2压铸件的尺寸公差应按GB6414的规定执行。
3.3.3压铸件有形位公差要求时,可参照GB/T15114;其标注方法按GB/T1182的规定。
3.3.4压铸件的尺寸公差不包括铸造斜度,其不加工表面:包容面以小端为基准,被包容面以大端为基准;待加工表面:包容面以大端为基准,被包容面以小端为基准。
3.3.5压铸件需要机械加工时,其加工余量按GB/T11350的规定执行。
3.4压铸件质量要求3.4.1压铸件应符合零件图样的规定。
- 1、下载文档前请自行甄别文档内容的完整性,平台不提供额外的编辑、内容补充、找答案等附加服务。
- 2、"仅部分预览"的文档,不可在线预览部分如存在完整性等问题,可反馈申请退款(可完整预览的文档不适用该条件!)。
- 3、如文档侵犯您的权益,请联系客服反馈,我们会尽快为您处理(人工客服工作时间:9:00-18:30)。
编号: 克拉克过滤器(中
国)有限公司
铝合金铸件 外观质量标准(暂行) 共2 页 第1 页
1.适用范围: 本标准适用于为克拉克过滤器(中国)有限公司配套的铝合金铸件(以下简称铸件)的外观检验,包括低压、高压铸造毛坯、成品滤座(完成铸造后机械加工的滤座)。
2.质量要求:
2.1总体要求
2.1.1整体外观:铸件外表面必须经过抛丸处理;颜色为白亮的银灰色,色泽均匀无色斑;各部位表面粗糙度的观感均衡。
2.1.2欠铸、气孔的封堵:铸件允许采用浸渗工艺封堵微孔,但不允许使用堵漏剂对大的孔穴进行人工封堵;特殊品种确需人工封堵时需要对堵漏剂的颜色、可靠性进行充分评价,并经我公司技术部、质量部书面批准。
2.1.3镶嵌件的锈蚀:铸件带有的任何嵌件不允许存在色斑、锈点等缺陷。
2.1.4隔皮、夹渣:铸件不允许存在隔皮、夹渣;
2.2非加工外表面
2.2.1表面修磨:对铸件外表面的任何修磨必须在抛丸前进行,修磨面与相邻表面应良好过渡;
2.2.2浇冒口:浇冒口应予以修磨,修磨后表面高出、凹陷不能超过0.5mm;
2.2.3顶杆痕迹:铸件顶杆痕迹高出、凹陷不能超过0.5mm,其表面形态(弧面或平面)应与所处位置一致;
2.2.4气孔或缩孔:气孔或缩孔的深度不能超过1mm,直径不能超过2mm,每50cm 2范围内存在的缺陷不能超过一处;
2.2.5飞边:铸件分型面飞边高度不能超过0.5mm;
2.2.6边角残缺:铸件因磕碰导致的边角残缺深度不超过0.5mm,宽度不超过2mm,任意100mm 长度范围内缺陷不得超过1处;
2.2.7线状凸起、凸瘤:铸件外表面因任何原因导致的线状凸起高度不允许超过0.3mm、长度不超过5mm;凸瘤高度、直径不能超过0.5mm,每个表面存在的缺陷数不得超过2处;
2.2.8 错型:除复杂零件另有规定外,铸件错型值不得超过0.5mm;
2.3加工面(适用于成品滤座)
2.3.1加工面孔穴:加工面存在的散布的目视可见的小针孔直径不允许超过1mm;直径0.5mm以上至1mm的针孔在整个所在平面上不允许超过1个;直径0.5mm以下的针孔在整个所在平面上不允许超过5个;
2.3.2擦痕:加工面上存在的引起表面色泽变化但不伤及基体的擦痕的影响面积不能超过所在平面的5%;
2.3.3 划伤:加工面线状划伤、起刺长度不得超过3mm,深度、高度不得超过0.2;每个表面不能超过3处;
2.3.4凹痕:加工面的压伤凹陷直径不能超过1mm,每个表面不能超过2处;
2.3.5毛刺:加工面周边毛刺应予以清除,不允许残留;
2.4螺纹((适用于成品滤座)
2.4.1磕碰:铸件上螺纹应牙形完整,不允许存在明显的磕碰伤;
2.4.2积屑:铸件上螺牙内不允许有通过超声清洗无法去除的积屑;
2.4.3气孔:铸件上内螺纹前2牙不能有可见缺陷,其余螺纹上不允许存在直径大于1mm的气孔;直径0.5mm以上至1mm的气孔不能超过5个;
2.5内腔
2.5.1多肉:因砂型脱皮等原因导致的多肉高度不应超过2mm,影响面积不能超过内腔面积的10%;
2.5.2气孔或缩孔:铸件内腔气孔或缩孔的深度不能超过2mm,直径不能超过3mm,存在的缺陷不能超过3处;
2.5.3飞边:铸件内腔因分型面等原因导致飞边高度不能超过0.5mm;
2.5.4毛刺、粘附:铸件内腔所有毛刺、加工导致的材料粘附应予以清除。
3.实施日期:
本标准2012年5月14日起实施。
编制 李现茂 批准 李建国。