瓶盖模具设计
啤酒瓶盖起子模具设计说明书
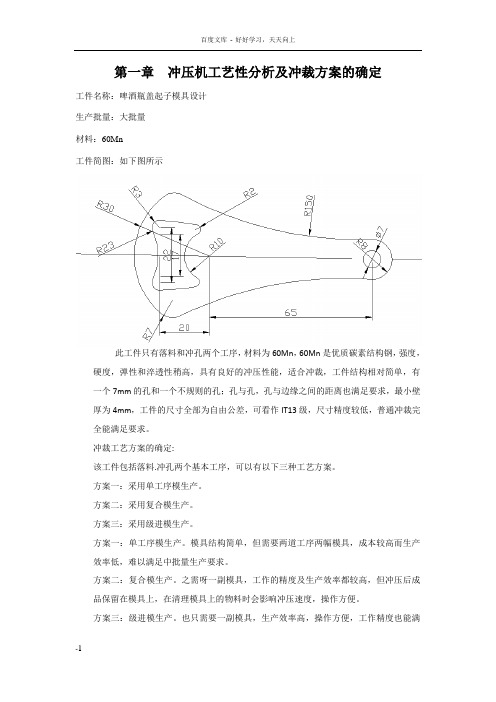
第一章冲压机工艺性分析及冲裁方案的确定工件名称:啤酒瓶盖起子模具设计生产批量:大批量材料:60Mn工件简图:如下图所示此工件只有落料和冲孔两个工序,材料为60Mn,60Mn是优质碳素结构钢,强度,硬度,弹性和淬透性稍高,具有良好的冲压性能,适合冲裁,工件结构相对简单,有一个7mm的孔和一个不规则的孔;孔与孔,孔与边缘之间的距离也满足要求,最小壁厚为4mm,工件的尺寸全部为自由公差,可看作IT13级,尺寸精度较低,普通冲裁完全能满足要求。
冲裁工艺方案的确定:该工件包括落料.冲孔两个基本工序,可以有以下三种工艺方案。
方案一:采用单工序模生产。
方案二:采用复合模生产。
方案三:采用级进模生产。
方案一:单工序模生产。
模具结构简单,但需要两道工序两幅模具,成本较高而生产效率低,难以满足中批量生产要求。
方案二:复合模生产。
之需呀一副模具,工作的精度及生产效率都较高,但冲压后成品保留在模具上,在清理模具上的物料时会影响冲压速度,操作方便。
方案三:级进模生产。
也只需要一副模具,生产效率高,操作方便,工作精度也能满足要求。
通过上述三种方案的分析比较,该件的冲压生产采用方案三为佳。
第二章主要设计计算排样方案的确定及计算设计级进模,首先要设计条料的排样图,啤酒瓶盖起子的形状具有一头大一头小的特点,直排样时材料利用率低,对于批量生产的零件,特别是零件材料较贵,为了节省材料,提高材料的利用率,应采用直对排样。
如图2-1所示的排样方法,设计成隔位冲压,可显著地减少废料,隔位冲压就是将第一遍冲压以后的条料水平方向旋转180,再冲第二遍,在第一次冲裁的间隙中冲裁出第二部分工件。
搭边值取2mm和,条料宽度为125mm和44mm,一个步距的材料利用率为52%。
查表2-1得最小搭边值:a=,a1=2mm条料宽度B:B=(D+2a1+nb1)第三章模具总体设计模具类型的选择模具类型分为三种分别是:单工序模,复合模和级进模。
单工序模又称简单冲裁模,是指在压力机一次行程内只完成一种冲裁工序的模具,如落料模,冲孔模,切断模切口模等。
瓶盖注塑模具设计.ppt

瓶盖注塑模具设计1. 引言注塑模具是一种用于制造塑料制品的工具,常用于生产各种类型的瓶盖。
瓶盖注塑模具设计的目标是实现高效、精确和可靠的生产过程,以满足市场的需求。
本文档将介绍瓶盖注塑模具设计的关键要素,包括模具的结构、选材、制造工艺和检验方法等。
2. 模具设计要素在进行瓶盖注塑模具设计之前,需要考虑以下几个要素:2.1 瓶盖形状和尺寸瓶盖的形状和尺寸将直接影响到模具的设计。
设计师需要根据瓶盖的要求确定模具的尺寸和形状,包括瓶盖的直径、高度、壁厚等。
2.2 模具结构模具的结构决定了瓶盖的成型过程和质量。
常见的模具结构包括单腔模具、多腔模具和家模具等。
不同的模具结构会影响到注塑工艺和成本。
2.3 材料选用模具的选材是瓶盖注塑模具设计的重要环节。
常用的模具材料包括优质钢材和合金钢等。
合理选择材料能够提高模具的硬度、耐磨性和使用寿命。
2.4 模具制造工艺模具制造工艺决定了模具的精度和寿命。
常见的模具制造工艺包括加工中心加工、电火花加工和线切割等。
合理选择工艺可以提高模具的制造效率和质量。
2.5 模具调试和调整模具调试和调整是确保瓶盖注塑模具正常运行的关键环节。
设计师需要根据生产工艺和成型效果进行模具调试和调整,以提高模具的稳定性和生产效率。
3. 模具制造过程瓶盖注塑模具的制造过程主要包括以下几个步骤:3.1 模具设计在模具设计阶段,设计师需要根据瓶盖的要求和生产工艺,绘制出模具的结构设计图,确定模具的尺寸、形状和材料。
3.2 模具加工模具加工是将设计好的模具结构图转化为实际模具的过程。
常见的模具加工方法包括数控机床加工、车床加工和磨床加工等。
通过精密加工,可以保证模具的精度和质量。
3.3 模具装调模具装调是将制造好的模具安装到注塑机上,并进行调试和校准的过程。
在这个过程中,操作人员需要调整模具的位置、温度和注塑参数,以确保模具的正常运行和瓶盖的质量。
3.4 模具测试模具测试是对制造好的模具进行性能测试的过程。
瓶盖塑料模具设计(模具制造工技师论)知识分享

瓶盖塑料模具设计(模具制造工技师论)饮料瓶盖的塑料模具设计与制造摘要:本文以瓶盖塑料件为研究对象,在分析塑件结构特点基础上,对材料的选择和模具类型的选择做了详细的说明,提出了完善的模具设计方案,阐述了模具结构设计,介绍了模具工作过程,并以图示的方式模拟了模具的脱模过程。
关键词:瓶盖、注射模、浇注系统引言:在设计注塑模具过程中,模具结构尤其脱模结构是否合理,将直接影响模具的使用寿命、塑件的质量和生产效率。
如何在保证塑件质量的前提下,使模具结构简单、紧凑,加工制造方便,成为注射模设计中要解决的重要问题。
图1为一饮料瓶盖的塑料制品,该塑件属于大批量生产。
在塑料材料、制品设计及加工工艺确定后,塑料模设计对制品质量与产量就具有决定性的影响。
首先,模腔形状、尺寸、表面粗糙度、分型面、浇口与排气的选择以及脱模方式的确定等,均对制品尺寸精度和形状精度以及塑件的物理性能、内应力大小、表面质量与内在质量等起到十分重要的影响。
其次,在塑件加工过程中塑料模结构的合理性对操作的难易程度具有重要的影响。
再次,塑料模对塑件的成本也有相当大的影响,一般制模费用是十分昂贵的,尤其是大型塑料模具更是如此。
我国塑料模的发展极其迅速。
30年已走过国外90年的历程,现已具有相当规模。
塑料模的设计技术、制造技术、CAD技术、CAM技术、CAE技术、CAPP技术,已有相应的开发应用。
我国在塑料模设计技术和制造技术上与发达国家也有相当的差距,专用模具钢品种少,规格不全,质量不稳定,且供应渠道不畅,是约制我国模具行业快速发展障碍。
当前我国作为一个经济快速发展的国家,模具技术发展已是刻不容缓。
1.瓶盖塑件结构及工艺分析1.1 瓶盖成型结构分析。
图1所示塑件为某饮料瓶瓶盖,材料为PE( 聚乙烯)—高压聚乙烯LDPE 。
除螺纹处较厚外,瓶盖为壁厚为2mm的塑料制件,其余部位厚度则均匀一致。
瓶盖外形结构为圆形,中间有抽芯结构。
瓶盖内侧有凸起1mm半圆形的螺纹,内侧用圆弧过度,可以起到减少零件应力集中的效果。
小瓶盖塑料注塑模具设计说明书
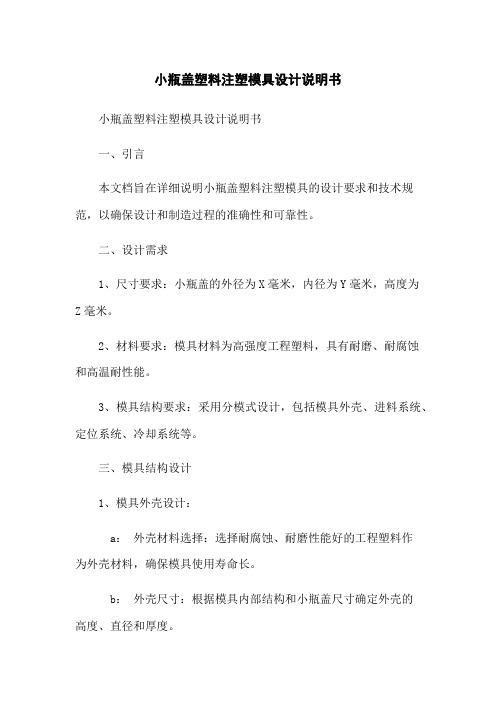
小瓶盖塑料注塑模具设计说明书小瓶盖塑料注塑模具设计说明书一、引言本文档旨在详细说明小瓶盖塑料注塑模具的设计要求和技术规范,以确保设计和制造过程的准确性和可靠性。
二、设计需求1、尺寸要求:小瓶盖的外径为X毫米,内径为Y毫米,高度为Z毫米。
2、材料要求:模具材料为高强度工程塑料,具有耐磨、耐腐蚀和高温耐性能。
3、模具结构要求:采用分模式设计,包括模具外壳、进料系统、定位系统、冷却系统等。
三、模具结构设计1、模具外壳设计:a:外壳材料选择:选择耐腐蚀、耐磨性能好的工程塑料作为外壳材料,确保模具使用寿命长。
b:外壳尺寸:根据模具内部结构和小瓶盖尺寸确定外壳的高度、直径和厚度。
c:模具外壳装配:确保外壳的装配牢固,能够承受注塑过程中的压力和冲击。
2、进料系统设计:a:进料口位置:进料口位于模具外壳上方,方便塑料材料的注入和冷却。
b:进料系统结构:进料系统包括进料管道、进料阀门和喷嘴等组成,确保塑料均匀流动。
3、定位系统设计:a:定位杆:在模具内部设置定位杆,以确保小瓶盖注塑时的位置准确性。
b:定位孔:在小瓶盖上开设定位孔,使得小瓶盖能够准确地套在定位杆上。
4、冷却系统设计:a:冷却通道:在模具内部设置冷却通道,以降低注塑过程中的温度,提高生产效率和产品质量。
b:冷却介质:选择高效的冷却介质,如冷水或冷气等,快速降低模具温度。
四、模具制造要求1、加工工艺:采用先进的数控加工设备和工艺,确保模具的加工精度和表面光洁度。
2、查漏测试:在模具制造过程中进行查漏测试,确保模具没有任何渗漏。
五、附录本文档涉及以下附件:1、小瓶盖的详细尺寸图纸。
2、模具的3D设计图纸。
六、法律名词及注释1、注塑模具:指用于塑料注塑成型的模具,可分为热流道模具和冷流道模具。
2、工程塑料:指具有高强度、耐磨、耐腐蚀和高温耐性能的塑料材料。
3、渗漏:指模具在注塑过程中出现塑料渗漏的现象,对产品质量产生负面影响。
毕业设计(论文)-矿泉水瓶盖注塑模具的设计[管理资料]
![毕业设计(论文)-矿泉水瓶盖注塑模具的设计[管理资料]](https://img.taocdn.com/s3/m/9e7249520029bd64793e2c95.png)
第1章绪论随着中国当前的经济形势的日趋好转,在“实现中华民族的伟大复兴”口号的倡引下,中国的制造业也日趋蓬勃发展;而模具技术已成为衡量一个国家制造业水平的重要标志之一,模具工业能促进工业产品生产的发展和质量提高,并能获得极大的经济效益,因而引起了各国的高度重视和赞赏。
在日本,模具被誉为“进入富裕的原动力”,德国则冠之为“金属加工业的帝王”,在罗马尼亚则更为直接:“模具就是黄金”。
可见模具工业在国民经济中重要地位。
我国对模具工业的发展也十分重视,早在1989年3月颁布的《关于当前国家产业政策要点的决定》中,就把模具技术的发展作为机械行业的首要任务。
近年来,塑料模具的产量和水平发展十分迅速,高效率、自动化、大型、长寿命、精密模具在模具产量中所战比例越来越大。
注塑成型模具就是将塑料先加在注塑机的加热料筒内,塑料受热熔化后,在注塑机的螺杆或活塞的推动下,经过喷嘴和模具的浇注系统进入模具型腔内,塑料在其中固化成型。
本次毕业设计的主要任务是矿泉水瓶盖注塑模具的设计。
之所以选择这个设计题目的主要有两方面意义:1、瓶盖是带内螺纹的塑件要求设计时要充分考虑到脱模的方式方法,多分型面结构以及点浇口方式的模具结构设计方法;2、瓶盖属中小型件在我们的日常生活中有一定的普遍性和代表性,为今后的实用性模具设计奠定了基础以更好的服务模具制造业服务社会。
本次毕业设计的主要目的:了解模具设计的方法与内容;掌握各类型模具的基本结构以及各零部件与非标准件的设计;熟悉模具材料的性能与应用以及加工方法与加工手段;熟练应用各种模具设计软件,包括CAD、CAXA、Pro/E、UG等;了解模具的发展状况与发展方向。
希望通过本次设计为今后的工作奠定一个良好的基础。
第2章成型工艺规程编制产品技术要求和工艺分析产品技术要求产品设计图见图2-1、图2-2、图2-3。
图2-1产品3D图俯视图图2-2 产品3D图仰视图2-3 产品2D图此塑件上有三个尺寸有精度要求:零件上有多个尺寸有26±;12±;壁厚2mm,均为MT6级塑料精度,属于中等精度等级,在模具设计和精度要求,分别是:30±;制造过程中要严格保证这些尺寸的精度要求。
饮料瓶瓶盖注射模具设计
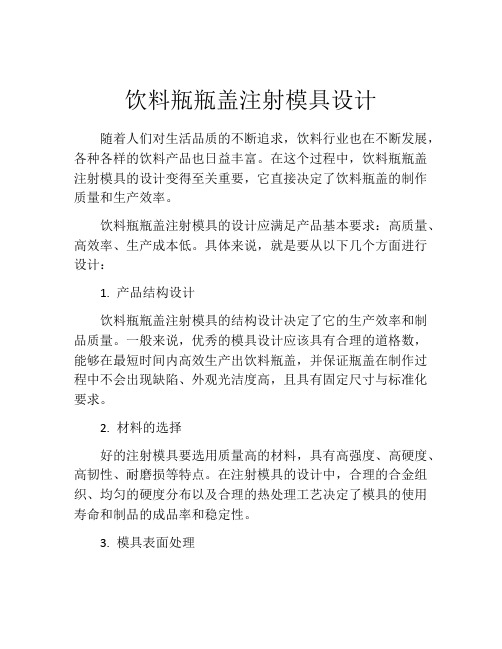
饮料瓶瓶盖注射模具设计随着人们对生活品质的不断追求,饮料行业也在不断发展,各种各样的饮料产品也日益丰富。
在这个过程中,饮料瓶瓶盖注射模具的设计变得至关重要,它直接决定了饮料瓶盖的制作质量和生产效率。
饮料瓶瓶盖注射模具的设计应满足产品基本要求:高质量、高效率、生产成本低。
具体来说,就是要从以下几个方面进行设计:1. 产品结构设计饮料瓶瓶盖注射模具的结构设计决定了它的生产效率和制品质量。
一般来说,优秀的模具设计应该具有合理的道格数,能够在最短时间内高效生产出饮料瓶盖,并保证瓶盖在制作过程中不会出现缺陷、外观光洁度高,且具有固定尺寸与标准化要求。
2. 材料的选择好的注射模具要选用质量高的材料,具有高强度、高硬度、高韧性、耐磨损等特点。
在注射模具的设计中,合理的合金组织、均匀的硬度分布以及合理的热处理工艺决定了模具的使用寿命和制品的成品率和稳定性。
3. 模具表面处理对模具表面进行光面处理能够提高注射模具的质量,表面处理的方法有电解镀铬、电子氧化等。
通过优化模具表面,能够减轻瓶盖模具的摩擦力,避免产品破损、变形等质量问题。
4. 注塑工艺设计饮料瓶瓶盖的生产过程中,温度、压力、流速等因素的控制是非常重要的。
优秀的注塑工艺设计应该包含精细的注塑参数设置、优化的熔体流动状态,并且要有良好的产品验收、测试程序与机器的调整性能。
总之,饮料瓶瓶盖注射模具设计对于饮料生产企业的产品质量和效率起着至关重要的作用。
优秀的注射模具应该满足生产企业的实际需求,采用高质量的材料、优化的结构设计等方式进行设计,同时还应该结合注塑工艺的合理配置,使生产过程达到高效、低成本并且质量优异的效果。
只有注射模具设计的高效性和高质量性得到保证,才能使饮料行业的生产得以更好地发展。
PE塑料瓶盖模具设计
1前言1.1制品原材料的选择及对材料的介绍1.1.1制品为塑料瓶盖, 选择LDPE材料低密度聚乙烯(LDPE)是高压下乙烯自由基聚合而获得的热塑性塑料。
LDPE是树脂中的聚乙烯家族中最老的成员, 二十世纪四十年代初期就作为电线包皮第一次商业生产。
LDPE综合了一些良好的性能: 透明、化学惰性、密封能力好, 易于成型加工。
这决定了LDPE是当今高分子工业中最广泛使用的材料之一。
LDPE级别可以满足大部分热塑性成型加工技术的规定。
涉及: 薄膜吹制、薄膜铸制、挤压贴胶、电线电缆贴胶、注射成型、吹塑成型。
模塑。
在聚乙烯树脂家族的竞争中, 吹塑成型与注射成型使用常规LDPE已经相对稳定。
LDPE 树脂由于它的抗曲挠性和加工特性而被用于模塑成型。
树脂熔融指数范围为0.5—2.0克/10分钟, 密度变化范围0.918—0.922克/立方厘米。
LDPE模塑应用于制作规定挤压性能的医用和日用消费瓶以及封密件。
根据以上材料的性能特点及塑料瓶盖的一般使用寿命及性能规定, 我们完全可以选用LDPE作为模塑材料。
常用注射工艺参数: LDPE、柱塞式、直角式喷嘴模具温度: 30-45℃注射压力: 60-100MPa保压时间: 15-60S注射时间: 0-5S冷却时间: 15-60S成型时间: 40-140S1.1.2材料性能介绍(1)聚乙烯是结晶材料, 吸湿性小。
(2)流动性能极好, 溢边值为0.02mm左右, 流动性能对压力变化敏感。
(3)容易发生熔融破裂, 当与有机溶剂接触时可发生开裂。
(4)加热时间过长则发生分解烧伤。
(5)冷却速度较慢, 因此必须充足冷却, 宜设冷料穴, 在模具设计的时候应当设计冷却系统。
(6)聚乙烯材料的收缩率范围较大, 收缩值也大, 方向性明显, 易变形, 翘曲。
结晶度及模具冷却条件对收缩率影响大, 应控制模温, 保持冷却均匀, 稳定。
(7)宜用高压注射, 料温均匀, 填充速度应快, 保压应当充足。
瓶盖注塑模具设计
技术要求;1、材料:PP2、产量:10万件3、未注公差尺寸按GB/T14486-1993中MT6。
4、要求塑件表面不得有气孔、熔接痕、飞边等缺陷,不得有明显的浇口痕迹。
图1图21.对塑件的工艺性分析1.1塑料品种:PP颜色:绿色、红色基本特性:聚丙烯无色、无味、无毒。
外观似聚乙烯,但比聚乙烯更透明、更轻。
密度仅为0.90~0.91g/cm3。
它不吸水,光泽好,易着色。
聚丙烯具有聚乙烯所有的优良性能,如卓越的介电性能、耐水性、化学稳定性,宜于成形加工等;还具有聚乙烯所没有的许多性能,如屈服强度、抗拉强度和硬度及弹性比聚乙烯好。
定向拉伸后聚丙烯可制作铰链,有特别高的抗弯曲疲劳强度。
熔点为164℃~170℃,耐热性好,能在100℃以上的温度下进行消毒灭菌。
其低温使用温度达-15℃,低于-35℃时会脆裂。
聚丙烯的高温绝缘性能好,而且由于其不吸水,绝缘性能不受湿度的影响,但在氧、热、光的作用下极易解聚、老化,所以必须加入防老化剂。
成形特点:1)成形加工性好,可以用注射、挤出、吹塑及真空成形等方法加工;2)吸湿性小,可能发生熔体破裂,长期与热金属接触容易分解;3)比聚乙烯流动性好,溢边值0.03mm,压力对熔体粘度比温度影响显著,应在较高压力下成形;4)冷却速度快,浇注系统及冷却系统应缓慢散热,适当延长冷却时间,以稳定尺寸;5)收缩率大且波动范围大,方向性明显,易发生缩孔、凹陷及变形;6)应注意控制成形温度,料温低时方向性明显,尤其低温高压时更显著,模温低于50℃时,塑件表面不光泽,易产生熔接不良和流痕,模温高于90℃时易发生翘曲和变形;7)塑件壁厚应均匀,避免缺口和尖角,防止应力集中,塑件内不能有铜质嵌件,聚丙烯与铜接触后会变脆;8)取向显著,不宜采用直接浇口,否则浇口附近残余应力大,易使塑件翘曲变形。
1.2塑件尺寸精度:塑件有7尺寸标注,按标准GB/T14486-1993中属于一般精度,按MT6级精度。
瓶盖注塑模具设计
瓶盖注塑模具设计瓶盖注塑模具设计是一项关键的制造技艺,该技术被广泛应用于瓶盖生产行业。
该技术的成功需要经验丰富的设计团队和设备的精湛制造,遵循一定的规范和标准,以确保生产出高质量的瓶盖产品。
注塑模具的设计制造可以分为以下步骤:1.进行模具项目的调查研究。
在瓶盖注塑模具设计中,需要了解瓶盖的类型、尺寸、形状和样式。
2.确定模具成本和设计时间。
该步骤涉及到生产成本、制造周期、所需用材和生产的数量等参数。
3.设计模具的三维图。
先完成模具的原理图和技术方案图,再通过CAD软件进行三维建模。
4.模拟模具制造的过程。
该步骤的作用是检测该模具的设计是否符合生产规范,以珍撤销昂贵修补的必要和预测出未来可能出现的问题。
5.计算模具结构参数。
该步骤根据模具的结构计算出所需的尺寸和其他参数,以保证产出瓶盖产品的质量和精度。
6.完成模具制造并进行测试。
将设计好的模具进行生产并进行制造质量测试,以确保模具质量符合生产标准。
7.按照客户要求进行调整。
在完成模具生产后,对其进行修改和调整以满足客户的要求。
瓶盖注塑模具设计的需要考虑各种因素。
例如模架、模具部件、模具材料、尺寸和胶管尺寸等。
在设计模具时,必须保证有适当的空间以便于后期修复和调整。
模具的结构和制造质量是直接影响到瓶盖生产工艺和产品精度的因素之一。
使用高质量的钢材和其他金属材料使得模具的抗压、抗腐蚀和氧化能力更强。
在制造模具时还需要保证其精度和质量在高温和高压条件下仍然能够稳定性工作,保证生产稳定和高效率。
总之,瓶盖注塑模具设计是一项非常重要的制造工艺,需要高度专业的技术知识和经验。
通过合理设计和细致制造,可以生产出高精度、高质量的瓶盖产品。
瓶盖注塑模具设计(有全套图纸)
本科毕业设计(论文)通过答辩
目录 摘要 1 塑料的成型基础·····························································································································1
关键词:CAD;ProE 等软件;浇注系统;冷却系统
本科毕业设计(论文)通过答辩
The injecting model design of coverof the bottle bit of shampoo
ABSTRACT Mold CAD, ProE, software technology is 80-90 years before the emergence of a new design technology, These software technologies greatly enhance the wider use of the product and mold design quality products and the best performance. The software's main task is to help designers of the injection process, interpretation of the data and
- 1、下载文档前请自行甄别文档内容的完整性,平台不提供额外的编辑、内容补充、找答案等附加服务。
- 2、"仅部分预览"的文档,不可在线预览部分如存在完整性等问题,可反馈申请退款(可完整预览的文档不适用该条件!)。
- 3、如文档侵犯您的权益,请联系客服反馈,我们会尽快为您处理(人工客服工作时间:9:00-18:30)。
瓶盖塑料模具设计摘要1 瓶盖塑料模具设计1.1拟定模具的结构形式1.1.1 塑件成型工艺性分析该塑件是一塑料瓶盖,如图1所示 ,塑件壁厚属薄壁塑件,生产批量大,材料为聚乙烯(PE,在高密度聚乙烯中掺入了部分低密度聚乙烯,改善塑件的柔韧性),成型工艺性很好,可以注射成型。
1.1.2 分型面位置的确定根据塑件结构形式,分型面选在瓶盖的底平面,如图2所示。
1.1.3 确定型腔数量和排列方式(1)型腔数量的确定该塑件精度要求不高,又是大批大量生产,可以采用一模多腔的形式。
考虑到模具制造费用,设备运转费低一些,初定为一模八腔的模具形式。
(2) 型腔排列形式的确定该塑件有两圈内螺纹,要使螺纹型芯从塑件上脱出,必须设计一套自动螺纹的齿轮传动结构,并且型腔的分布圆直径和齿轮分布圆直径相吻合,若采用一模八腔,型腔分布圆直径就相当大了,这样模具结构尺寸就比较大,加上齿轮传动系统,模具结构复杂,制造费用也很高。
但该塑件螺纹的牙型不高,且呈圆弧形牙,内侧突起与直径的比例约为5.26%(6.266.2628-⨯100% =5.26%)。
因为所用材料为聚乙烯,材料弹性模量比较小,材质硬度不高,课采取强制脱模的方式,这也是注塑厂成型这种类型瓶盖的常用方法。
因此本设计采用推件板推出的强制推脱方法,型腔的排列方式采用双列直排,如图2所示。
1.1.4 模具结构形式的确定从上面分析中可知,本模具拟采用一模八腔,双列直排,推件板推出,流道采用平衡式,浇口采用潜伏式浇口或侧浇口,定模不需要设置分型面,动模部分需要一块型芯固定板和支撑板,因此基本上可确定模具结构形式为A型带推件板的单分型面注射模。
1.1.5 注射机型号的选定(1) 注射量的计算通过计算或Pro/E建模分析,塑件质量m1为2.8g,塑件体积V1=ρ1m=91.08.2= 3.077cm3,流道凝料的质量m2还是个未知数,课按塑件质量的0.6倍来估算。
从上述分析中确定为一模八腔,所注射量为M = 1.6nm1= 1.6 ⨯8⨯2.8 = 35.84g 。
(2)塑件和流道凝料在分型面上的投影面积及所需锁模力的计算流道凝料(包括浇口)在分型面上的投影面积A2,在模具设计前是个未知值,根据多型腔模的统计分析,A 2是每个塑件在分型面上的投影面积A1的0.2倍~0.5倍,因此可用0.35nA1来进行估算,所以A = nA1+ A2= nA1+ 0.35nA1= 1.35nA1= 8412.336mm2式中A1=4πd2= 0.785 ⨯ 31.52 = 778.92mm2。
Fm=Ap型= 8412.336 ⨯ 30 = 252370N = 252.37KN式中型腔压力p型取30MPa(因是薄壁塑件,浇口又是潜伏式浇口,压力损失大,取大一些)。
(3) 选择注射机根据每一生产周期的注射量和锁模力的计算值,可选用SZ-60/450卧式注射机(上海第一塑料机械厂),见表1。
表1 注射机主要技术参数(4)注射机有关参数的校核①由注射机料筒塑化速率校核模具的型腔数n 。
n≤123600 /m mkMt-=8.28.286.03600/3036006.58.0⨯⨯-⨯⨯⨯=43.2>>8,型腔数校核合格。
式中k──注射机最大注射量的利用系数,一般取0.8;M──注射机的额定塑化量(5.6g/s);t──成型周期,取30s 。
②注射压力的校核。
p e ≥k'p= 1.3⨯130 = 169MPa,而pe= 170MPa,注射压力校核合格。
式中k'──取1.3;p──取130MPa(属薄壁窄浇口类)。
③锁模力校核。
F≥KAp型= 1.2⨯252.37 = 302.84kN,而F = 450kN,锁模力校核合格。
其他安装尺寸的校核要待模架选定,结构尺寸确定以后才可进行。
1.2 浇注系统的设计1.2.1 主流道设计(1) 主流道尺寸根据所选注射机,则主流道小端尺寸为d = 注射机喷嘴尺寸+ (0.5~1)= 3.5+0.5= 4mm主流道球面半径为SR = 喷嘴球面半径+ (1~2)= 20+ 2 = 22mm(2)主流道衬套形式本设计虽然是小型模具,但为了便于加工和缩短主流道长度,衬套和定位圈还是设计成分体式,主流道长度取40mm,约等于定模板的厚度(见图3)。
衬套如图5所示,材料采用T10A钢,热处理淬火后表面硬度为53HRC~57HRC 。
(3)主流道凝料体积q 主=12hπ(D2 + Dd + d2) =1240π(6.12+ 6.1 ⨯ 4 + 42) = 812mm3≈0.8cm3(4) 主流道剪切速率校核由经验公式.γ=33.3nRqπγ= 1840.19= 1840s1-<5⨯ 103s1-式中qγ=q主+ q分+ q塑件=0.8 + 2.772 + 8⨯3.077 = 28.188cm3Rn =22/)1.64(+ =205.5 = 0.2525cm主流道剪切速率偏小主要是注射量小、喷嘴尺寸偏大,使主流道尺寸偏大所致。
1.2.2 分流道设计(1) 分流道布置形式分流道应能满足良好的压力传递和保持理想的填充状态,使塑料熔体尽快地经分流道均衡的分配到各个型腔,因此,采用平衡式分流道,如图4所示。
(2)分流道长度第一级分流道L1=50mm第二级分流道 L2= 10mm第三级分流道L3= 15.5mm(3) 分流道的形状、截面尺寸以及凝料体积①形状及截面尺寸。
为了便于机械加工及凝料脱模,本设计的分流道设置在分型面上定模一侧,截面形状采用加工工艺性比较好的梯形截面。
梯形截面对塑料熔体及流动阻力均不大,一般采用下面经验公式来确定截面尺寸,即B = 0.2654m·4L= 0.265448.2⨯⨯50= 1.996mm根据参考文献[1]取B = 4mm。
H =32B =32⨯4 = 2.67mm ,取H = 3mm 分流道L 1截面形状如图5所示。
从理论上L 2、L3分流道可比L 1截面小10%,但为了刀具的统一和加工方便,在分型面上的分流道采用一样的截面。
② 凝料体积。
分流道长度 L =(50 + 10 ⨯ 2 + 15.5 ⨯ 4)⨯2 = 264m m分流道截面积 A =234+⨯3 = 10.5mm 2 凝料体积 q分= 264 ⨯ 10.5 = 2772m m3 = 2.772cm 3 (4) 分流道剪切速率校核 采用经验公式⋅γ =33.3nR q π= 2.39 ⨯ 103S 1-在5⨯102~5⨯103之间,剪切速率校核合格。
式中q =tv = 141v ⨯ = 4 ⨯ 3.077 = 12.3cm 3Rn = 322cA π= 0.1755cm 式中 t ──注射时间,取1s; ﻩ A ──梯形面积(0.105cm2);ﻩ c ──梯形周长(1.3cm )。
(5) 分流道的表面粗糙度分流道的表面粗糙度Ra 并不要求很低,一般取0.8µm ~1.6µm 即可,在此取1.6µm,如图5所示。
1.2.3 浇口的设计根据外部特征,外观表面质量要求比较高,应看不到明显的浇口痕迹,圆周上布满了防滑直纹,因此采用潜伏式浇口,在开模时浇口自行剪断,几乎看不到浇口的痕迹。
对于这类小型薄壁塑件,几乎所有工厂都是这样做的(个别工厂在盖的顶部采用点浇口),若采用侧浇口,不太符合工程实践。
(1) 潜伏式浇口尺寸的确定 由经验公式得d = n k4A = 0.6 ⨯ 0.2724A = 1.1mm式中 A = dh π+ πr2= 2.69.456m m2(塑件的表面积);n ──塑料材料系数取0.6;k ──塑件壁厚的函数值取0.272 。
ﻩ浇口截面形状如图6所示,浇口先取φ0.8,在试模式根据填充情况再进行调整。
(2)浇口剪切速率的校核 由点浇口的经验公式得.γ =34Rq π = 3)04.0(14.3077.34⨯⨯= 61244.488s 1-= 6.1 ⨯ 104s1- .γ为104s 1-~105s 1-,剪切速率校核合格。
1.2.4 冷料穴的设计(1) 主流道冷料穴如图7所示,采用半球形,并采用球形头拉料杆,该拉料杆固定在动模固定板上,开模时利用凝料对球头的包紧力使主流道凝料从主流道衬套中脱出。
(2) 分流道冷料穴在分流道端部加长5m m(约1.5d 0)作分流道冷料穴。
1.3 成型零件的设计模具中确定塑件几何形状和尺寸精度的零件称为成型零件。
在本设计中成型零件就是成型盖外表面的凹模,成型内表面的螺纹型芯(凸模)。
1.3.1成型零件的结构设计(1) 凹模(型腔)瓶盖圆周上均匀分布着防滑直纹,若凹模制成整体式,则直纹用机械加工方法很困难(没有退刀位置),若制成一个电极来加工防滑直纹,成本也比较高。
整体模板都要用价格较贵重的模具钢,维修也不方便。
因此,瓶盖圆周部分若采用局部嵌入式凹模,上述存在的问题能够很方便地得到解决,如图8所示,嵌件外径尺寸按经验]2[,取44mm(壁厚7mm)。
(2) 型芯型芯是一个带有两圈螺纹的、且牙型不高的整体式型芯,如图9所示。
1.3.2 成型零件钢材的选用瓶盖是大批量生产,成型零件所选用钢材耐磨性和抗疲劳性能应该良好;机械加工性能和抛光性能也应良好。
因此构成型腔的嵌入式凹模钢材选用S M1 。
定模板构成瓶盖顶部花纹、文字部分,成型时有料流的冲刷,但没有脱模时塑件的摩擦,因此采用55钢调质(定模板材质可和模架厂协商)。
螺纹型芯因为是采用强制脱模,磨损比较厉害,采用硬度比较高的模具钢Gr12MoV,淬火后表面硬度为58HRC~62H RC 。
1.3.3 成型零件工作尺寸的计算(1)型腔径向尺寸L M= [(1 + s )L s -∆χ]zδ+0= 31.9860104.00+式中 s ──塑件平均收缩率s =2035.0015.0+=0.025;ﻩ L s ──塑件外径尺寸(取31.5);χ──修正系数(取0.58);ﻩ ∆──塑件公差值(查塑件公差表,取0.52); ﻩ z δ──制造公差,(取∆/5)。
(2)螺纹型芯径向尺寸① 螺纹型芯大径d 大M = [(1 + s)d 大s + ∆中]oz δ-= 28.85003.0-式中 d大s ──塑件内螺纹大径基本尺寸(取28); ∆中──塑件内螺纹中径公差(取制造公差z δ的5倍);z δ──中径制造公差,根据参考文献[1]中的表9.4-10(取0.03)。
② 螺纹型芯小径d 小M = [(1 + s)d小s + ∆中]oz δ-= 27.415003.0-式中d 小s ──塑件内螺纹小径基本尺寸(取26.6)。
③ 螺距工作尺寸T M = tS (1 + s ) ±2zδ = 4.61 ± 0.015式中t S ──塑件内螺纹螺距(取4.5)。