机械可靠性设计8
机械可靠性设计课程设计
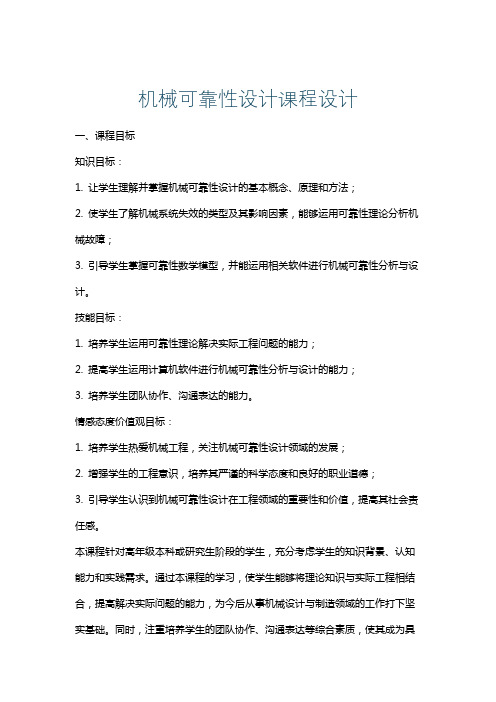
机械可靠性设计课程设计一、课程目标知识目标:1. 让学生理解并掌握机械可靠性设计的基本概念、原理和方法;2. 使学生了解机械系统失效的类型及其影响因素,能够运用可靠性理论分析机械故障;3. 引导学生掌握可靠性数学模型,并能运用相关软件进行机械可靠性分析与设计。
技能目标:1. 培养学生运用可靠性理论解决实际工程问题的能力;2. 提高学生运用计算机软件进行机械可靠性分析与设计的能力;3. 培养学生团队协作、沟通表达的能力。
情感态度价值观目标:1. 培养学生热爱机械工程,关注机械可靠性设计领域的发展;2. 增强学生的工程意识,培养其严谨的科学态度和良好的职业道德;3. 引导学生认识到机械可靠性设计在工程领域的重要性和价值,提高其社会责任感。
本课程针对高年级本科或研究生阶段的学生,充分考虑学生的知识背景、认知能力和实践需求。
通过本课程的学习,使学生能够将理论知识与实际工程相结合,提高解决实际问题的能力,为今后从事机械设计与制造领域的工作打下坚实基础。
同时,注重培养学生的团队协作、沟通表达等综合素质,使其成为具有创新精神和实践能力的高素质工程技术人才。
二、教学内容本章节教学内容主要包括以下几部分:1. 机械可靠性设计基本概念:介绍可靠性、失效、故障等基本概念,分析可靠性指标及其计算方法。
2. 机械系统失效类型及影响因素:阐述机械系统失效的类型,探讨应力、应变、温度、湿度等影响因素。
3. 可靠性数学模型:讲解可靠性数学模型的基本原理,包括概率论、数理统计、随机过程等。
4. 可靠性分析与设计方法:介绍常见的可靠性分析方法,如故障树分析、事件树分析、蒙特卡洛模拟等,以及可靠性设计方法。
5. 计算机软件应用:教授常用可靠性分析与设计软件的操作方法,如MATLAB、ANSYS等。
6. 实践案例:分析典型机械可靠性设计案例,使学生了解实际工程中的应用。
教学内容依据以下教材章节组织:1. 《机械可靠性设计》第一章:基本概念与方法;2. 《机械可靠性设计》第二章:失效类型及影响因素;3. 《机械可靠性设计》第三章:可靠性数学模型;4. 《机械可靠性设计》第四章:可靠性分析与设计方法;5. 《机械可靠性设计》第五章:计算机软件应用;6. 《机械可靠性设计》附录:实践案例。
机械设计中的机械结构可靠性分析

机械设计中的机械结构可靠性分析机械结构的可靠性是指在一定的使用条件下,机械结构能够保持正常运行的程度。
机械设计中的可靠性分析是为了评估机械结构的可靠性,并通过分析得出相应结论和建议。
本文将从可靠性的定义、分析方法、计算指标及应用等方面进行探讨。
一、可靠性的定义在机械设计中,可靠性是指机械结构在一定使用条件下能够正常运行的概率。
可靠性分析的目的是通过对机械结构的设计、制造、使用等环节进行分析和评估,以提高机械结构的可靠性,并避免或减少故障和损坏的发生。
二、可靠性分析方法1.故障模式分析(FMEA)故障模式分析是一种通过分析和识别机械结构可能发生的故障模式和潜在故障原因的方法。
该方法通过对机械结构进行系统化的分解和分析,识别潜在的风险和故障点,并制定相应的改进措施以提高可靠性。
2.可靠性预测可靠性预测是一种基于统计和仿真分析的方法,通过模拟机械结构在使用过程中的故障和损坏情况,来预测机械结构在给定使用条件下的可靠性水平。
该方法可以通过引入故障率、平均寿命、失效模型等指标,来评估机械结构的可靠性。
3.可靠性试验可靠性试验是一种通过对机械结构进行实际测试和观测,来评估机械结构可靠性的方法。
通过在实际使用条件下对机械结构进行试验,可以直接获得机械结构的可靠性数据,并根据试验结果来评估和改进机械结构的可靠性。
三、可靠性的计算指标1.失效率(Failure Rate)失效率是指单位时间内机械结构发生故障的概率。
失效率可以通过可靠性试验或可靠性预测来计算,是评估机械结构可靠性的重要指标。
2.平均寿命(Mean Time Between Failures,MTBF)平均寿命是指机械结构连续正常运行的平均时间。
它可以通过对机械结构的使用状态和维修记录进行统计和计算得出。
3.可用性(Availability)可用性是指机械结构在给定时间段内是可靠的,且进行维修和维护的时间较短的概率。
可用性可以通过计算机械结构的失效率和维修时间来评估。
机械零件的可靠性设计

3
加强维护
定期维护和保养机械零件,延长其寿命并提高可靠性。
可靠性测试和验证
测试方法
使用可靠性测试方法来验证零件的寿命和性能。
验证过程
验证设计的可靠性,确保其在实际使用中能够达到 预期要求。
案例研究和实践经验
1
汽车发动机设计
通过可靠性改进措施和测试验证,成功提高了发动机的可靠性和性能。
2
航空航天器零件
可靠性评估方法
故障模式与影响分析 (FMEA)
通过识别故障模式和评估其影响,确定潜在故障并采取措施预防。
可靠性指标计算
计算关键零件的故障率、平均寿命等指标,用于评估系统的可靠性水平。
可靠性改进措施
1
优化设计
通过改善设计来减少潜在的故障点,提高分析、可靠性预测等工具来预防和诊断故障。
在航空航天工程中,可靠性设计是确保安全和可靠运行的核心要素。
3
电力设备
在电力行业,可靠性设计是保障稳定供电和电网安全的关键。
机械零件的可靠性设计
在机械工程中,可靠性设计至关重要。本演示将介绍可靠性设计的基本原则, 影响因素和评估方法,以及可靠性改进和测试验证的案例研究和实践经验。
机械零件的可靠性设计的意义
1 保证性能
可靠性设计确保机械零件在使用期间保持良好性能,降低故障率,以满足用户需求。
2 成本节约
通过提前识别和解决潜在问题,可靠性设计可以减少维修和更换零件的成本。
可靠性设计的基本原则
设计简化
简化设计可以减少故障点,提 高系统的可靠性。
材料选择
选择适当的材料可以提高零件 的耐用性和抗腐蚀性。
质量控制
严格控制零件生产过程中的质 量,可以降低缺陷率。
机械可靠性设计技术

在可靠性技术迅速发展的今天,从指标试验评价发展到从指标论证、设计、原材料选择到工艺控制及售后服务的全过程的综合管理和评价,许多产品打出“零失效”的王牌。
产品的可靠性在很大程度上取决于设计的正确性。
机械可靠性设计是近期发展起来并得到推广应用的一门现代设计理论和方法,以提高产品可靠性为目的、以概率论与数理统计理论为基础,综合运用数学、物理、工程力学、机械工程学、人/机工程学、系统工程学、运筹学等多方面的知识来研究机械工程的最佳设计问题。
为了提高广大企业从业人员机械可靠性设计水平,中国电子标准协会应会员单位要求,决定组织召开“机械可靠性设计技术高级研修班”。
现将相关事宜通知如下:课程特点:本课程针对机械动力学系统的设计,涵盖了材料的选择、力学的计算、表面处理和热处理工艺的选择、失效的分析、振动噪声的消除与预防、动力学测试与分析等方面内容。
提纲:课程大纲以根据学员要求,上课时会有所调整,具体以报到时的讲义为准。
第一章机械可靠性设计基本依据1.1干涉模型 1.2大数定律与中心极限定理 1.3基本载荷形式1.4综合作用类型 1.5主要失效模式 1.6系统功能关系第二章基于载荷环境的材料工艺准则2.1广义载荷 2.2环境类形 2.3材料类型2.4毛坯工艺 2.5加工准则第三章结构可靠性技术准则3.1优化设计 3.2余度设计 3.3防错设计3.4环境适应性设计 3.5维修性设计第四章机械可靠性设计数学模型4.1应力强度干涉模型 4.2静载荷作用的可靠性设计 4.3交变载荷作用的疲劳可靠性设计4.4压力容器的可靠性设计 4.5交变温度作用的热负荷可靠性 4.6腐蚀与磨损条件下构件可靠性第五章机械可靠性设计准则5.1基于材力三大假设的静载设计 5.2基于交变载荷或谱载荷作用的抗疲劳设计5.3基于当量初始缺陷分布的概率断裂控制 5.4基于压力容器快速断裂控制的损伤容限5.5基于交变温度作用的热疲劳特性 5.6构件防腐蚀和耐磨损设计第六章机械可靠性应用6.1冲击载荷与霍普金圣效应 6.2 各态遍历的随机振动 6.3随机振动试验准则6.4冲击载荷作用的设计准则 6.5结构柔性与变形协调设计 6.6压力容器与动载作用设计6.7振动环境作用的可靠性准则 6.8复合载荷环境材料匹配 6.9载荷环境毛坯匹配准则6.10减振器与结构阻尼准则 6.11润滑与降噪准则 6.12表面技术与润滑匹配6.13 箱座、支架类零部件材料阻尼准则 6.14铸件减震设计准则6.15锻件、焊接件抗冲击设计准则第七章受热结构影响因素7.1总体热惯性与最高温度 7.2比热容与高温持续时间 7.3表面辐射系数7.4热阻与热循环特性 7.5隔热设计准则 7.6耐热限制 7.7主动冷却技术第八章机械可靠性工程实施8.1可靠性预计和分配 8.2可靠性设计 8.3可靠性试验- 8.4可靠性管理第九章典型结构可靠性分析与设计9.1弹簧疲劳与老化机理 9.2弹簧抗疲劳设计 9.3橡胶耐磨性分析9.4小子样产品可靠性评价 9.5名义应力-应变与局部应力-应变 9.6结构变形与失稳分析9.7产品安全系数与可靠性参数 9.8机械结构典型寿命分布 9.9旋转件动平衡问题分析9.10 齿轮耐磨性影响分析 9.11受力构件零件的应力松弛分析师资介绍:申博士:机械可靠性技术专家,研究员,专业研究方向为机械装备可靠性与失效控制,长期从事机械可靠性与环境工程研究,曾任国防军工单位高级技术职务,在疲劳、断裂、残骸分析、失效物理和动力学测试技术方面有深厚的功底,提出了变形疲劳、气动激励载荷与振动环境精确预示方法、复杂部件可靠性设计技术、紧固件环境适应性设计、高速运动件动态参数测试技术等新技术,并有光弹、电测、扫描电镜分析和模态的丰富试验经验机械可靠性设计技术培训【时间地点】 2012年12月21-22日深圳【参加对象】从事动力学机构设计的机械工程师、系统工程师、测试工程师、可靠性工程师、技术经理、总工等【费用】 3200元/人(包括资料费、午餐及上下午茶点等)【课程热线】4OO-O33-4O33(森涛培训,提前报名可享受更多优惠)【内训服务】本课程可根据客户需求提供内训服务,欢迎来电咨询。
机械设备可靠性设计

机械设备可靠性设计
一机械设备可靠性设计要点
答:1.确定零件合理的安全系数;
2.储备设计(冗余设计);
3.耐环境设计;
4.简单化和标准化设计;
5.提高结合部的可靠性;
6.结构安全设计;
7.设置齐全的安全装置;
8.人机界面设计。
二如何取得人机系统的最佳效果
答:为了取得人机系统的最佳效果,对人和机分别提出“人适应于机”、“机适宜于人”的不同要求,即“人是机”与“机宜人”。
“人是机”是指人要适应机器的要求就需要对人的因素予以限制,对人进行教育、训练,并且尽量发挥人的积极因素。
所谓“机宜人”是指机器作为人从事生产和生活活动的工具,要求设计、制造出来的机器应尽量满足使用者的要求。
三人机系统常见事故。
答:物体打击;机械伤害;触电;灼烫;其他伤害。
四交通限速规定
答:依据《中华人民共和国道路交通安全法》规定,在没有限速标志的路段,应当保持安全车速。
夜间行驶或者在容易发生危险的路段行驶,以及遇有沙尘、冰雹、雨、雪、雾、结冰等气象条件时,应降低行驶速度。
第八章可靠性试验案例

n f (t ) ns (t ) n
其它参数可按如下相应公式计算 可靠度
ns (t ) R (t ) n
《机械可靠性设计》
20
第八章 累积失效概率(不可靠度)
可靠性试验
F (t )
失效概率密度
n f (t ) n
n f (t ) n t
f (t )
其中
失效率
n f (t ) n f (t t ) n f (t )
无替换定时截尾试验,记作[n,无,t0];
有替换定时截尾试验,记作[n,有,t0]; 无替换定数截尾试验,记作[n,无,r];
有替换定数截尾试验,记作[n,有,r];
《机械可靠性设计》
11
第八章
可靠性试验
三、寿命试验设计
可靠性寿命试验应根据被试验产品的性质和试验目的 来设计试验方案。但无论试验是否加速,有无替换,定数 还是定时截尾,一般均应包括下列基本内容: 1)明确试验对象 2)确定试验条件 3)拟定失效标准 4)选定测试周期 当产品寿命为指数分布时,累计失效分布函数为:
r 10 n 35.27, 取n 36 F (t ) 0.2835
从上面的计算结果可以看出,要在规定的时间t内观察
到较多的失效数r,则应增加投试样品数n。若要求观测到的 失效数r不变,如能增加投试样品数n,则可以缩短时间。
16
《机械可靠性设计》
第八章
可靠性试验
6)确定试验截止时间
n t0 ln nr
《机械可靠性设计》
第八章
可靠性试验
§8-3
寿命试验结果的统计分析及参数估计
一、一般分布完全寿命试验的数据处理
对n个随机抽取的样品进行寿命试验,直到全部样品 失效为止,这样的试验称为完全寿命试验。 n个随机样品的寿命是n个独立同分布的随机变量。一 次完整试验可以测得n个样品的失效时间。将全部样品失 效时间从小到大顺序排列,其顺序统计量为
机械零件的可靠性设计
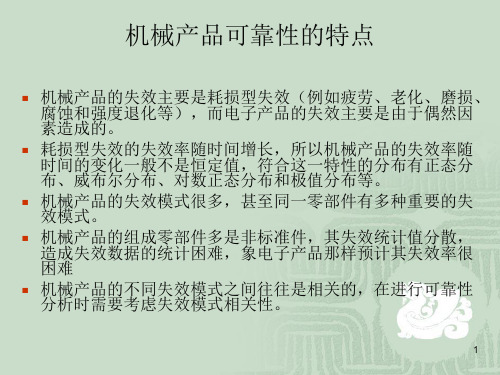
R2 1
X XS
2
2 S
1
350 310 302 102
1 (1.26) 1 0.1038 0.8962
28
(3)“R3σ”可靠性含义下的安全系数:
50000 30000
1.67
R1 1(ZR ) 1
S
2+
2 S
1
50000 30000 10002 30002
1.000
R2 1
S
2+
2 S
1
50000 30000 120002 30002
0.947
27
例2 某汽车零件,其强度和应力均服从正态分布,强度的均
17
例题1
当强度的标准差增大到120MPa时,
z s 850 380 470 3.6968
2
2 S
422 1202 127.1377
查标准正态分布值,得R=0.999 89.
18
2、概率密度函数联合积分法(一般情况)
g()
f (s)
应力s0处于ds区间内的概率为
f (s0 )
f ( )
f (s)
1 2
y
0 exp[
(
y
y
2
2 y
)2
]dy
y S
y=-S
0
-10
0
10
20
y =-S
y0 y0
30
40
S
50
y=
2
2 S
不可靠度为: F P ( y 0)
1
2 y
0
exp[
(
y
y
机械可靠性设计

零件失效的概率或零件的故障概率Q(t)定义为:
常用故障频 数直方图来 反映某类零 件发生故障 的概率。
横坐标取为某类零件的寿命间隔; 纵坐标表示某类零件在各寿命间隔内发生故障的 个数(或频次)。
故障概率密度函数f(t)
二、三种失效率——失效模式
产品的失效(或故障)有其规律。 ※ 大量的研究表明,机电产品零件的典型失效率曲线,明显可 划分为三个区域:早期失效区域、正常工作区域和功能失效区域。 1)早期失效区域的失效率较 高,故障率由较高的值迅速下 降。一般属于试车的跑合期。 2)正常工作区域出现的失效 具有随机性,故障率变化不太 大,有的微微下降或上升。可 以称为使用寿命期或偶然故障 期。在此区域内,故障率较低。 3)功能失效区域的失效率迅速上升。一般情况下,零件表现为 耗损、疲劳或老化所致的失效。 失效率曲线的三个区域反映了零件的三种故 障模式,它们均具有一定的概率分布特性。
7)重要度(Importance)。 1)可靠度(Reliability);
6)有效度(Availability);
一、可靠度和失效率
可靠度: 零、部件在规定的寿命期限内,在规定的使用条 件下,无故障地进行工作的概率。 在规定的使用条件下,可靠度是时间的函数,用R(t)表示。 对总数为N个零件进行试验,经过t时间后,有NQ(t)件失效, NR(t)件仍正常工作,那么该类零件的可靠度R(t)定义为:
安全系数法对问题的提法是:零件的安全系数(等于零件的强
度除以零件的应力;即n=F/S)是多大?
在计算安全系数时,零件材料的强度F和零件所承受的应力
S都是取单值的。
机械可靠性设计方法认为:零件的应力、强度以及其他的设计
参数,如载荷、几何尺寸和物理量等都是多值的,即呈分布状态。
- 1、下载文档前请自行甄别文档内容的完整性,平台不提供额外的编辑、内容补充、找答案等附加服务。
- 2、"仅部分预览"的文档,不可在线预览部分如存在完整性等问题,可反馈申请退款(可完整预览的文档不适用该条件!)。
- 3、如文档侵犯您的权益,请联系客服反馈,我们会尽快为您处理(人工客服工作时间:9:00-18:30)。
则:
1t、2 t、n t
t
, ………… 1tdt
R1 t e 0
t
2 t dt R2 t e 0
t
n t dt Rn t e 0
RS R1tR2 tRn t
exp
t
0
1
t
2
t
n
t
dt
令:s t 1t 2 t n t
则:RS
exp
t
s
t
dt
ቤተ መጻሕፍቲ ባይዱ
0
串联系统的失效率等于各单元失效率之和。 当串联系统的各单元失效率为常数时,串 联系统的失效率为常数,这时,有:
可靠性预测包括单元可靠性预测和系统可 靠性预测。
§8.2.2 单元可靠性预测
单元可靠性预测是系统可靠性预测的基础, 预测单元的可靠度,首先要确定单元的失效率 , 可通过从手册、资料中查得。
常用零部件的失效率 G
G
当使用条件与工作条件不相同时,应加 以修正,即:
kFG
§8.2.3 系统可靠性预测
§8.1.2 系统可靠性的类型
系统可靠性设计的目的,就是要使系统在满 足规定的可靠性指标、完成额定功能的前提下 使系统的技术指标、重量指标、制造成本和使 用寿命等获得协调并达到最优化的结果。系统 可靠性设计方法可归纳为两种类型:
1.按照已知零件或单元的可靠性数据,计 算系统的可靠性指标,称为可靠性预测。
§8.3.1 等分配法
1.串联系统可靠度分配
n
Rs R1R2 Rn Ri Rn i 1 1
R RSn
2.并联系统可靠度分配
RS 1 1 R n
R
1
1
RS
1 n
3.串并联系统可靠度分配
利用等分配法对串并联系统进行可靠度分 配时,可将串并联系统简化为等效串联系统和 等效单元,再按串联系统的等可靠度分配方法 给各等效单元分配可靠度。若等效单元为并联 子系统,则按并联系统可靠度分配方法给并联 子系统各单元分配可靠度。例如:
机械可靠性设计
§8 系统可靠性
§8.1 系统可靠性的基本概念
§8.1.1系统的组成与类型
系统是由某些彼此相互协调工作的零件、 部件、子系统组成,为完成某一特定功能的综 合体。组成该系统并相对独立的机件,通称为 单元。系统与单元的含义是相对的概念,视研 究对象而定。系统可分为不可修复系统和可修 复系统。
当并联系统中只有一个单元工作,其它单 元不工作而作贮备,而当工作单元失效时,则 贮备单元中的一个单元立即顶替上,将失效单 元换下,使系统工作不至中断,这种系统称为 贮备系统。在给定时间内,只要累积的失效单 元不多余n-1个,则系统不会失效。设各单元 的失效率均为λ时,常用泊松分布计算系统可 靠度。
RS
t
RS
sdt
e 0
est
2)并联系统的可靠性预测
若并联系统由n个单元组成,系统发生失 效要求n个单元都同时失效。因此系统的不可 靠度和可靠度分别为:
FS 1 R1 1 R2 1 Rn
RS 1 FS 可见,并联系统随单元数和单元的可靠度增大, 系统可靠度增大。
3)贮备系统的可靠性预测
§8.3 可靠性分配
可靠性分配是指将工程规定的系统可靠度 指标合理地分配给组成该系统的各个单元,确 定各组成单元的可靠性度,从而使整个系统的 可靠性指标得到保证。
可靠性分配的本质是一个工程决策问题, 应按系统工程原则:“技术上合理,经济上效 益高,时间方面见效快”来进行。在进行可靠 性分配时,必须明确目标函数和约束条件,随 着目标函数和约束条件的不同,可靠性分配方 面也不同。
1.系统逻辑图
1)串联系统 定义:系统中各单元从逻辑关系上看,
好象由许多环链连接成的链条,一个单元失效 就会导致整个系统失效,这个系统叫做串联系 统。
2)并联系统 定义:如果组成系统的所有单元失效,整
个系统才会失效,这个系统叫做并联系统。 特点:单元数n和单元可靠度愈大,系统的可 靠度就愈高。
为了减少系统失效概率,可采用冗余法或 贮备法,使用两个或更多的相同功能单元来完 成同一任务,当其中一个单元失效时,其它单 元仍能完成这一功能而使系统不失效。
5)串并联系统的可靠性预测
,
⑴先求串联系统单元3,4,及5,6子系统 的可靠度
R34 R3 R4
R56 R5 R6
⑵ 求 R34 , R56 ,7,8的可靠度
R3456 1 1 R34 1 R56 R78 1 1 R7 1 R8
⑶ 求系统可靠度
R R1R2R3456R78
t
exp
t
1
t
1 t
2!
2
1 t
3!
3
n
11!t
n 1
4)表决系统的可靠度预测 由n个单元组成的并联系统,只要任意k个
单元不失效,则系统就不会失效,这种系统称 为 n 中取k 的表决系统k/n ,在机械系统中常 用的表决系统2/3。2/3的表决系统的可靠度为:
RS R1R2 R3 1 R1 R2 R3 R11 R2 R3 R1R2 1 R3
2.按照给定的系统可靠性指标,对组成系 统的单元进行可靠性分配,并在多种设计方案 中比较优选。
§8.2 可靠性预测
可靠性预测是在设计阶段定量地估计未来 产品的可靠性的方法。它是运用以往的工程经 验、故障数据以及当前的技术水平尤其是以元 器件、零件的失效率作为依据,预测产品实际 可能达到的可靠度。
§8.2.1可靠度预测的目的
注意:单元是否为串联或并联,是以功能 关系确定,不是结构关系。
2.数学模型
1)串联系统的可靠性预测 若串联系统由n个单元组成,系统正常工
作必需要求n个单元都能同时正常工作。因此 系统可靠度为:
RS R1tR2tRn t
由此可见,随单元数的增加和单元可靠度的减 小,串联系统的可靠度迅速降低。
设串联系统各单元的失效率为:
①求等效串联系统
②给等效串联系统各等效单元分配可靠度
1
R1 R2 R3 R4 Rs 4
③给等效单元 3 中各单元分配可靠度
R34
R56
1
1
1
R3 2
1
R3 R4 R34 2
1
1.检验本设计是否满足给定的可靠性目标, 预测产品的可靠度;
2.协调设计参数及性能指标,以提高产品的 可靠性;
3.比较不同设计方案的特点及可靠度,选择 最佳的设计方案;
4. 发 现 影 响 产 品 可 靠 性 的 主 要 因 素 , 找 出 薄弱环节,采取必要的措施,降低产品的失效 率,提高其可靠性。