机械结构可靠性设计.
机械结构不确定性分析与可靠性设计研究

机械结构不确定性分析与可靠性设计研究过去几十年来,机械结构的不确定性分析与可靠性设计已经成为机械工程领域中一个重要的研究方向。
在涉及到工程结构的设计和可靠性评估时,我们不能忽视机械结构内部存在的不确定性因素。
这些因素可能包括材料性能的波动、制造误差、加载条件的随机性等。
不确定性分析是指通过数学和统计方法,对机械结构内部的不确定因素进行处理和评估的过程。
它为工程师提供了一种分析结构在不确定条件下的安全性和可靠性的途径。
在不确定性分析中,常用的方法包括概率论、统计学、模拟和演化算法等。
这些方法通过建立合理的数学模型,对不确定因素进行模拟和预测,从而评估结构的可靠性。
在机械结构的可靠性设计中,不仅仅要考虑结构在正常工作条件下的可靠性,还要考虑在不正常工作条件下结构的可靠性。
例如,在假设结构工作温度较高的情况下,结构的性能是否会受到影响?这是一个需要考虑的不确定因素。
然而,不确定性分析和可靠性设计并不是简单地将不确定因素考虑进去,还需要根据具体的工程要求和约束进行灵活的处理。
机械结构不确定性分析与可靠性设计在工程实践中发挥了重要作用。
首先,它可以帮助工程师评估结构在设计和制造过程中存在的随机性和不确定性的影响。
例如,在设计一个机械零件时,不确定性分析可以帮助工程师确定材料的强度和刚度参数的范围,从而保证设计的合理性和可靠性。
此外,不确定性分析和可靠性设计还可以帮助工程师提升结构的性能和可靠性。
例如,在风电场设计中,风能的变化是一个不可控因素。
通过针对不确定性的分析和设计,可以优化风机结构的叶片和轴的尺寸和材料,使其在不同气候和风速条件下的性能更加稳定和可靠。
近年来,随着计算机技术和数值计算方法的发展,机械结构的不确定性分析和可靠性设计也取得了显著的进展。
计算机模拟和仿真技术的应用大大提高了分析和设计的效率和准确性。
同时,通过大量的仿真计算和实验验证,可靠性设计的理论和方法也得到了不断的完善和改进。
总的来说,机械结构不确定性分析与可靠性设计是一个复杂而重要的研究方向。
机械设计中的机械结构可靠性分析

机械设计中的机械结构可靠性分析机械结构的可靠性是指在一定的使用条件下,机械结构能够保持正常运行的程度。
机械设计中的可靠性分析是为了评估机械结构的可靠性,并通过分析得出相应结论和建议。
本文将从可靠性的定义、分析方法、计算指标及应用等方面进行探讨。
一、可靠性的定义在机械设计中,可靠性是指机械结构在一定使用条件下能够正常运行的概率。
可靠性分析的目的是通过对机械结构的设计、制造、使用等环节进行分析和评估,以提高机械结构的可靠性,并避免或减少故障和损坏的发生。
二、可靠性分析方法1.故障模式分析(FMEA)故障模式分析是一种通过分析和识别机械结构可能发生的故障模式和潜在故障原因的方法。
该方法通过对机械结构进行系统化的分解和分析,识别潜在的风险和故障点,并制定相应的改进措施以提高可靠性。
2.可靠性预测可靠性预测是一种基于统计和仿真分析的方法,通过模拟机械结构在使用过程中的故障和损坏情况,来预测机械结构在给定使用条件下的可靠性水平。
该方法可以通过引入故障率、平均寿命、失效模型等指标,来评估机械结构的可靠性。
3.可靠性试验可靠性试验是一种通过对机械结构进行实际测试和观测,来评估机械结构可靠性的方法。
通过在实际使用条件下对机械结构进行试验,可以直接获得机械结构的可靠性数据,并根据试验结果来评估和改进机械结构的可靠性。
三、可靠性的计算指标1.失效率(Failure Rate)失效率是指单位时间内机械结构发生故障的概率。
失效率可以通过可靠性试验或可靠性预测来计算,是评估机械结构可靠性的重要指标。
2.平均寿命(Mean Time Between Failures,MTBF)平均寿命是指机械结构连续正常运行的平均时间。
它可以通过对机械结构的使用状态和维修记录进行统计和计算得出。
3.可用性(Availability)可用性是指机械结构在给定时间段内是可靠的,且进行维修和维护的时间较短的概率。
可用性可以通过计算机械结构的失效率和维修时间来评估。
机械工程中的可靠性优化设计

机械工程中的可靠性优化设计引言:机械工程是一个广泛应用于各行各业的领域,而在机械工程中,可靠性优化设计是一个至关重要的方面。
可靠性优化设计旨在提高机械系统的可靠性,延长设备的使用寿命,减轻后续的维修成本,提高工业生产效率。
本文将探讨机械工程中的可靠性优化设计的原理和方法,并介绍一些实际应用案例。
一、可靠性的基本概念在机械工程中,可靠性是一个关键的指标,它表示一个系统在给定的时间内正常工作的能力。
可靠性可以通过计算系统的故障率、失效率、平均寿命等指标来评估。
在可靠性优化设计中,目标是降低系统的故障率,提高系统的可靠性。
二、可靠性优化设计的原则1. 考虑系统的可靠性要素可靠性优化设计要考虑系统设计的各个方面,包括材料的选择、结构的设计、工艺的控制等。
系统的可靠性是由多个因素共同作用决定的,因此必须综合考虑各个方面的因素。
2. 运用可靠性工具在可靠性优化设计中,有许多工具和方法可供选择,如故障模式与影响分析(FMEA)、故障树分析(FTA)、可靠性块图(RBD)等。
这些工具能够帮助工程师深入分析系统的故障模式和风险,从而指导设计的改进和优化。
3. 进行系统辨识和优化在可靠性优化设计中,系统辨识是一个重要的步骤。
通过系统辨识,可以找出系统中的关键部件和环节,以及它们之间的相互作用关系。
然后,可以针对这些关键部件和环节进行优化设计,提高系统的可靠性。
三、可靠性优化设计的方法1. 材料的选择材料是机械系统中一个重要的方面,对系统的可靠性起着至关重要的作用。
在选择材料时,需要考虑其物理性质、化学性质、热学性质等因素,并根据系统的工作环境和使用条件选择合适的材料。
2. 结构的设计在机械工程中,结构的设计对系统的可靠性有着重要的影响。
良好的结构设计应该考虑到力学强度、刚度、防振动、冲击和疲劳等因素。
通过优化结构设计,可以提高机械系统的可靠性。
3. 工艺的控制机械系统的制造过程对其可靠性也有重要的影响。
控制好工艺流程、提高工艺的精度和稳定性,可以降低系统的故障率。
机械可靠性设计系统可靠性设计
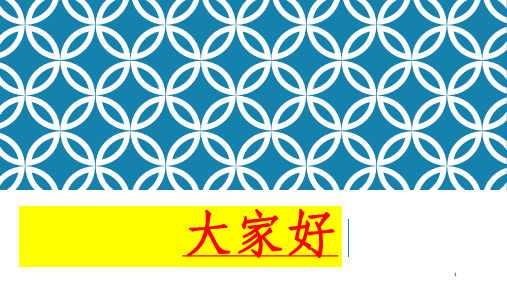
• 1 表决系统(工作储备系统)
55
1)2/3表决系统
56
57
58
例4-4
有一架装有3台发动机的飞机,它至少需要 2台发动机正常才能飞行,设飞机发动机的平 均无故障工作时间MTBF=2000h,试估计工作 时间为10h和100h的飞机可靠度。 解:n=3,k=2
RS (t) 3R 2 2R 3 3e 2t 2e 3t
73
1)冷储备系统 (1)两个单元(一个单元备用)的系统
74
75
(2)n个单元(n-1个单元备用)的系统
76
77
(3)多个单元工作的系统
Ri e t
RS(t )
e
Lt
1
Lt
(Lt )2 2!
(Lt )3 3!
(Lt )n n!
78
(4)考虑检测器和开关可靠性的系统
Rs(t ) e 1t
84
85
86
87
88
89
2 全概率公式法(分解法)
90
91
92
3 检出支路法(路径枚举法)
93
94
95
4.3 系统可靠性预计
1 可靠性预计的目的
可靠性预计是指产品的设计与研制阶段,根据产品的功能 结构、工作环境以及组成产品单元的相互关系和可靠性数据, 推测产品可能达到的可靠性指标。可靠性预计是一个由局部 到整体、由小到大、由下到上的过程,是一个综合的过程。
52
• Rs1=R1R2R3 Rs2=R4R5 Rs3=1-(1-Rs1)(1Rs2) Rs4=1-(1-R6)(1R7) Rs=Rs3Rs4R8
53
• 储备模型 当采用串联模型的设计不能满足设计指标要求时,
机械结构的优化设计与可靠性分析
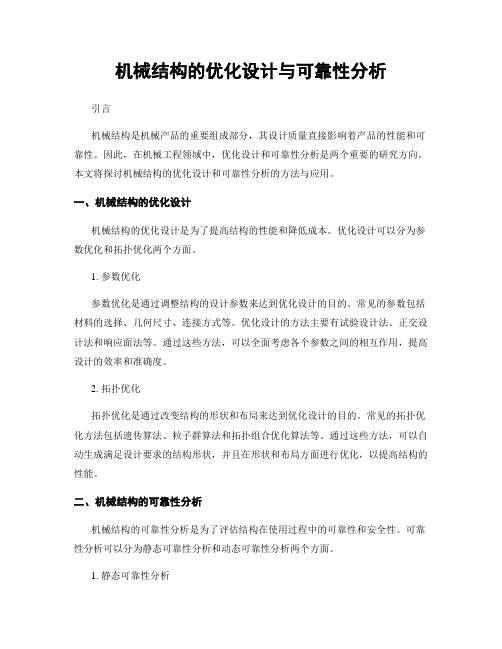
机械结构的优化设计与可靠性分析引言机械结构是机械产品的重要组成部分,其设计质量直接影响着产品的性能和可靠性。
因此,在机械工程领域中,优化设计和可靠性分析是两个重要的研究方向。
本文将探讨机械结构的优化设计和可靠性分析的方法与应用。
一、机械结构的优化设计机械结构的优化设计是为了提高结构的性能和降低成本。
优化设计可以分为参数优化和拓扑优化两个方面。
1. 参数优化参数优化是通过调整结构的设计参数来达到优化设计的目的。
常见的参数包括材料的选择、几何尺寸、连接方式等。
优化设计的方法主要有试验设计法、正交设计法和响应面法等。
通过这些方法,可以全面考虑各个参数之间的相互作用,提高设计的效率和准确度。
2. 拓扑优化拓扑优化是通过改变结构的形状和布局来达到优化设计的目的。
常见的拓扑优化方法包括遗传算法、粒子群算法和拓扑组合优化算法等。
通过这些方法,可以自动生成满足设计要求的结构形状,并且在形状和布局方面进行优化,以提高结构的性能。
二、机械结构的可靠性分析机械结构的可靠性分析是为了评估结构在使用过程中的可靠性和安全性。
可靠性分析可以分为静态可靠性分析和动态可靠性分析两个方面。
1. 静态可靠性分析静态可靠性分析是在给定荷载条件下,评估结构在一定寿命内不发生失效的概率。
静态可靠性分析可以通过概率统计方法、有限元法和可靠性索引方法等进行。
通过这些方法,可以评估结构在设计寿命内的可靠性,并且提供对结构进行改进的建议。
2. 动态可靠性分析动态可靠性分析是在结构受到外界荷载变化时,评估结构在一定时间内不发生失效的概率。
动态可靠性分析可以通过随机振动分析和动力有限元分析等进行。
通过这些方法,可以考虑结构在振动和冲击等动态荷载下的可靠性,并且提供对结构进行抗震和抗冲击改进的建议。
结论机械结构的优化设计和可靠性分析是机械工程领域中的重要研究方向。
通过优化设计,可以提高结构的性能和降低成本;通过可靠性分析,可以评估结构的可靠性和安全性。
机械产品的可靠性设计与分析

机械产品的可靠性设计与分析在当今高度工业化的社会中,机械产品在各个领域都发挥着至关重要的作用。
从日常生活中的家用电器到工业生产线上的大型设备,从交通运输工具到航空航天领域的精密仪器,机械产品的可靠性直接影响着人们的生活质量、生产效率以及生命财产安全。
因此,机械产品的可靠性设计与分析成为了机械工程领域中一个极其重要的研究课题。
可靠性设计是指在产品设计阶段,通过采用各种技术和方法,确保产品在规定的条件下和规定的时间内,能够完成规定的功能,并且具有较低的故障率和较长的使用寿命。
可靠性分析则是对产品的可靠性进行评估和预测,找出可能存在的薄弱环节,为改进设计提供依据。
在机械产品的可靠性设计中,首先要进行的是需求分析。
这就需要充分了解产品的使用环境、工作条件、用户要求以及相关的标准和规范。
例如,对于一台用于户外作业的工程机械,需要考虑到恶劣的天气条件、复杂的地形地貌以及高强度的工作负荷等因素;而对于一台家用洗衣机,需要重点关注其洗涤效果、噪声水平和使用寿命等方面的要求。
只有明确了这些需求,才能为后续的设计工作提供正确的方向。
材料的选择是影响机械产品可靠性的重要因素之一。
不同的材料具有不同的物理、化学和机械性能,因此需要根据产品的工作要求和使用环境,选择合适的材料。
例如,在高温、高压和腐蚀环境下工作的零件,需要选用耐高温、耐高压和耐腐蚀的材料;对于承受重载和冲击载荷的零件,则需要选用高强度和高韧性的材料。
同时,还要考虑材料的成本和可加工性等因素,以确保产品在满足可靠性要求的前提下,具有良好的经济性。
结构设计也是可靠性设计的关键环节。
合理的结构设计可以有效地减少应力集中、提高零件的承载能力和抗疲劳性能。
例如,采用圆角过渡可以避免尖锐的棱角引起的应力集中;采用对称结构可以使载荷分布更加均匀;采用加强筋和肋板可以提高结构的刚度和强度。
此外,还需要考虑结构的装配和维修便利性,以便在产品出现故障时能够快速进行维修和更换零件。
机械结构可靠性分析与优化设计
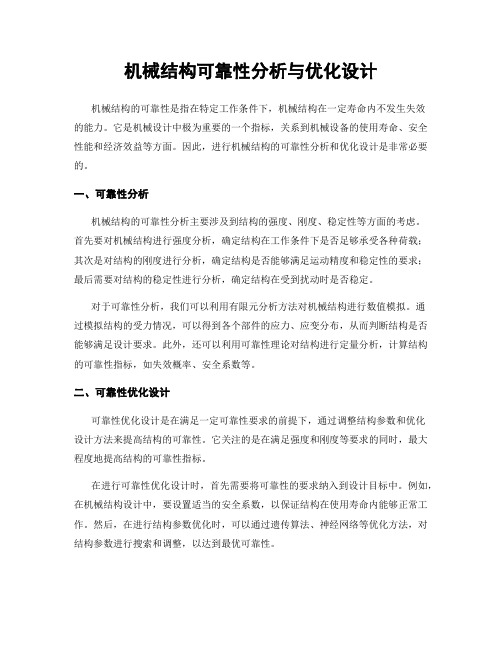
机械结构可靠性分析与优化设计机械结构的可靠性是指在特定工作条件下,机械结构在一定寿命内不发生失效的能力。
它是机械设计中极为重要的一个指标,关系到机械设备的使用寿命、安全性能和经济效益等方面。
因此,进行机械结构的可靠性分析和优化设计是非常必要的。
一、可靠性分析机械结构的可靠性分析主要涉及到结构的强度、刚度、稳定性等方面的考虑。
首先要对机械结构进行强度分析,确定结构在工作条件下是否足够承受各种荷载;其次是对结构的刚度进行分析,确定结构是否能够满足运动精度和稳定性的要求;最后需要对结构的稳定性进行分析,确定结构在受到扰动时是否稳定。
对于可靠性分析,我们可以利用有限元分析方法对机械结构进行数值模拟。
通过模拟结构的受力情况,可以得到各个部件的应力、应变分布,从而判断结构是否能够满足设计要求。
此外,还可以利用可靠性理论对结构进行定量分析,计算结构的可靠性指标,如失效概率、安全系数等。
二、可靠性优化设计可靠性优化设计是在满足一定可靠性要求的前提下,通过调整结构参数和优化设计方法来提高结构的可靠性。
它关注的是在满足强度和刚度等要求的同时,最大程度地提高结构的可靠性指标。
在进行可靠性优化设计时,首先需要将可靠性的要求纳入到设计目标中。
例如,在机械结构设计中,要设置适当的安全系数,以保证结构在使用寿命内能够正常工作。
然后,在进行结构参数优化时,可以通过遗传算法、神经网络等优化方法,对结构参数进行搜索和调整,以达到最优可靠性。
此外,还可以应用可靠性设计理论进行概率设计。
概率设计是通过考虑不确定性因素,确定合理的设计参数范围,使得结构在任何设计参数取值下都能够满足一定的可靠性要求。
例如,通过概率设计可以确定零部件的公差范围,确保结构在制造过程中的变化仍能满足可靠性要求。
结构的可靠性分析和优化设计是机械工程领域的重要内容,它直接关系到机械设备的使用寿命和安全性能。
通过可靠性分析,可以了解结构的强度、刚度、稳定性等方面的情况,并根据这些情况进行相应的改进。
可靠性分析在机械结构设计中的应用研究

可靠性分析在机械结构设计中的应用研究引言:在现代工程设计中,机械结构的可靠性是一个至关重要的指标。
可靠性分析作为一种评估和优化机械结构设计的方法,已经被广泛应用于许多领域。
本文将探讨可靠性分析在机械结构设计中的应用研究,并重点介绍一些常用的可靠性分析方法和工具。
一、可靠性分析方法可靠性分析方法是评估机械系统中部件和系统的可靠性的数学和统计学方法。
其中,最常用的方法包括故障模式与效果分析(FMEA)、故障树分析(FTA)和可靠性增益图(RBD)等。
故障模式与效果分析(FMEA)是一种通过分析系统中各个部件的故障模式和故障对系统的影响程度来评估系统可靠性的方法。
通过FMEA,工程师们可以识别和评估系统中的潜在故障,并采取相应的措施来提高系统的可靠性。
故障树分析(FTA)是一种通过构建树状图来分析和评估系统故障概率的方法。
在FTA中,各个事件(包括故障事件和故障的原因)通过逻辑门(例如与门、或门和非门)相连接,形成树状结构。
通过分析系统中各个事件的故障概率,可以计算系统整体的故障概率,并提出相应的改进方案。
可靠性增益图(RBD)是一种通过图形的方式来表示系统结构和可靠性指标的方法。
在RBD中,每个系统组件由一个方框表示,方框之间通过线段连接。
通过分析RBD中各个组件的可靠性指标,可以评估整个系统的可靠性,并对系统进行优化设计。
二、可靠性分析工具为了支持可靠性分析的实施,工程师们使用了许多可靠性分析工具。
其中,最常用的工具包括故障模式与效果分析软件(如FMEA软件)、故障树分析软件(如FTA软件)和可靠性增益图软件(如RBD软件)等。
故障模式与效果分析软件是一种用于支持FMEA分析的工具。
通过这种软件,工程师们可以方便地识别、评估和管理系统中的潜在故障。
此外,这种软件还可以生成报表和图表,以便更好地分析和优化系统的可靠性。
故障树分析软件是一种用于支持FTA分析的工具。
通过这种软件,工程师们可以方便地构建和分析故障树,从而评估系统的故障概率。
- 1、下载文档前请自行甄别文档内容的完整性,平台不提供额外的编辑、内容补充、找答案等附加服务。
- 2、"仅部分预览"的文档,不可在线预览部分如存在完整性等问题,可反馈申请退款(可完整预览的文档不适用该条件!)。
- 3、如文档侵犯您的权益,请联系客服反馈,我们会尽快为您处理(人工客服工作时间:9:00-18:30)。
传统安全系数
可靠性安全系数
以“强度均值/应力均值”为定义的统 计安全系数的计算 设强度与应力服从正态分布,强度均值 为 ,标准差 ,应力均值为 ,标准 差为 ,强度变差系数 ,应力变 差系数
S f0 L
1 Z CVS 2 CVL 2 Z 2CVS 2CVL 2 1 Z CVS
机械结构可靠性设计
程真英 2011.9
机械可靠性设计的主要方法
传统安全系数
安全系数的定义
平均强度/平均载荷 最小强度/最大载荷
传统安全系数的特点
把各种参数都当作定值,没有分析参数的随机特性
没有与定量的可靠性相联系,安全系数不能代表可 靠性,没有分析参数的离散度对可靠性的影响
N(2500,30)N,材料强度极限也服从正态分 布,强度极限均值 S 80N/mm2,标准差 S 3.2N/mm2,要求具有可靠性R=0.999,试设 计该链杆的直径。(设直径的制造公差为 ±0.01d)
习题
附表1 正态分布函数表
(u )
u
1 u 2 / 2 e du 2
2 2
可靠性安全系数
以“最小强度/最大载荷”为定义的统 计安全系数的计算
例1
例1
例2
有一ห้องสมุดไป่ตู้棒拉杆的受力情况如图所示。已知作用于杆上的拉力P~ N(29400,441)N,拉杆的材料为低合金钢,回火温度为538℃, (查材料手册得:其强度极限均值µs=1054.48N/mm2,标准差 σs=41.36 N/mm2并服从正态分布),制造中半径r=r±0.015r 也服从正态分布,设加工后圆棒拉杆的可靠度为R=0.999,求 该圆棒拉杆的直径等于多少?
习题
有一机械零件,承受应力和材料强度都 服从正态分布,其中承受的应力均值为 20N/mm2、标准差为3N/mm2,该零件材 料强度均值为40N/mm2、标准差为4N/ mm2 ,求该零件的破坏概率。
习题
附表1 正态分布函数表
(u )
u
1 u 2 / 2 e du 2
习题
有一受拉链杆如图所示,已知拉力P∽