浅析机械可靠性设计
机械设计中的可靠性分析
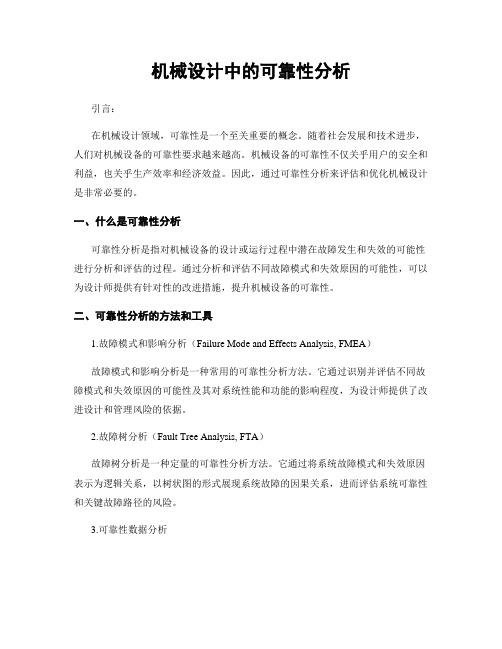
机械设计中的可靠性分析引言:在机械设计领域,可靠性是一个至关重要的概念。
随着社会发展和技术进步,人们对机械设备的可靠性要求越来越高。
机械设备的可靠性不仅关乎用户的安全和利益,也关乎生产效率和经济效益。
因此,通过可靠性分析来评估和优化机械设计是非常必要的。
一、什么是可靠性分析可靠性分析是指对机械设备的设计或运行过程中潜在故障发生和失效的可能性进行分析和评估的过程。
通过分析和评估不同故障模式和失效原因的可能性,可以为设计师提供有针对性的改进措施,提升机械设备的可靠性。
二、可靠性分析的方法和工具1.故障模式和影响分析(Failure Mode and Effects Analysis, FMEA)故障模式和影响分析是一种常用的可靠性分析方法。
它通过识别并评估不同故障模式和失效原因的可能性及其对系统性能和功能的影响程度,为设计师提供了改进设计和管理风险的依据。
2.故障树分析(Fault Tree Analysis, FTA)故障树分析是一种定量的可靠性分析方法。
它通过将系统故障模式和失效原因表示为逻辑关系,以树状图的形式展现系统故障的因果关系,进而评估系统可靠性和关键故障路径的风险。
3.可靠性数据分析可靠性数据分析是通过统计和分析已有的可靠性数据,获得系统或组件的可靠性参数,从而评估设备的可靠性。
常用的可靠性数据分析方法包括可靠性预测、可靠性增长法、可靠性试验和可靠性回顾等。
三、可靠性设计的原则和策略1.设计可靠性需考虑失效机理和失效模式在机械设计过程中,应根据机械设备的工作原理和工作环境,对可能的失效机理和失效模式进行全面的分析和评估。
只有深入了解失效机理和失效模式,才能有针对性地采取措施来提高设备的可靠性。
2.纠正性设计和防御性设计相结合纠正性设计是指通过设计改进和工艺改进,来消除潜在的缺陷和故障点,提高设备的可靠性。
防御性设计是指通过采用冗余设计、选用高可靠度的元件等手段,来提高设备对外界环境和故障的抵抗能力。
机械设计中的机械结构可靠性分析

机械设计中的机械结构可靠性分析机械结构的可靠性是指在一定的使用条件下,机械结构能够保持正常运行的程度。
机械设计中的可靠性分析是为了评估机械结构的可靠性,并通过分析得出相应结论和建议。
本文将从可靠性的定义、分析方法、计算指标及应用等方面进行探讨。
一、可靠性的定义在机械设计中,可靠性是指机械结构在一定使用条件下能够正常运行的概率。
可靠性分析的目的是通过对机械结构的设计、制造、使用等环节进行分析和评估,以提高机械结构的可靠性,并避免或减少故障和损坏的发生。
二、可靠性分析方法1.故障模式分析(FMEA)故障模式分析是一种通过分析和识别机械结构可能发生的故障模式和潜在故障原因的方法。
该方法通过对机械结构进行系统化的分解和分析,识别潜在的风险和故障点,并制定相应的改进措施以提高可靠性。
2.可靠性预测可靠性预测是一种基于统计和仿真分析的方法,通过模拟机械结构在使用过程中的故障和损坏情况,来预测机械结构在给定使用条件下的可靠性水平。
该方法可以通过引入故障率、平均寿命、失效模型等指标,来评估机械结构的可靠性。
3.可靠性试验可靠性试验是一种通过对机械结构进行实际测试和观测,来评估机械结构可靠性的方法。
通过在实际使用条件下对机械结构进行试验,可以直接获得机械结构的可靠性数据,并根据试验结果来评估和改进机械结构的可靠性。
三、可靠性的计算指标1.失效率(Failure Rate)失效率是指单位时间内机械结构发生故障的概率。
失效率可以通过可靠性试验或可靠性预测来计算,是评估机械结构可靠性的重要指标。
2.平均寿命(Mean Time Between Failures,MTBF)平均寿命是指机械结构连续正常运行的平均时间。
它可以通过对机械结构的使用状态和维修记录进行统计和计算得出。
3.可用性(Availability)可用性是指机械结构在给定时间段内是可靠的,且进行维修和维护的时间较短的概率。
可用性可以通过计算机械结构的失效率和维修时间来评估。
机械工程的可靠性优化设计分析
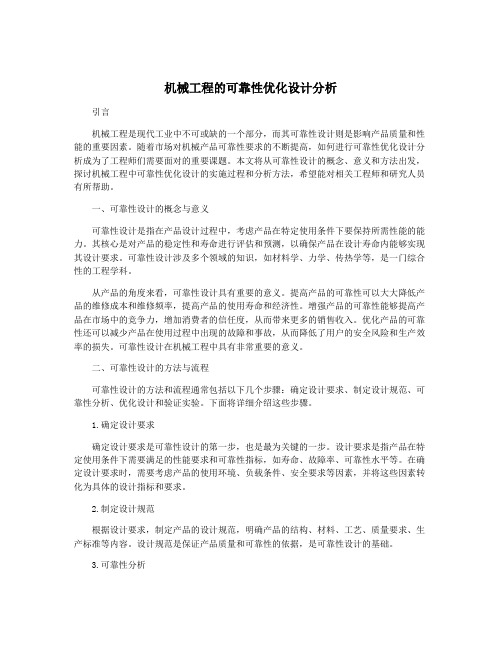
机械工程的可靠性优化设计分析引言机械工程是现代工业中不可或缺的一个部分,而其可靠性设计则是影响产品质量和性能的重要因素。
随着市场对机械产品可靠性要求的不断提高,如何进行可靠性优化设计分析成为了工程师们需要面对的重要课题。
本文将从可靠性设计的概念、意义和方法出发,探讨机械工程中可靠性优化设计的实施过程和分析方法,希望能对相关工程师和研究人员有所帮助。
一、可靠性设计的概念与意义可靠性设计是指在产品设计过程中,考虑产品在特定使用条件下要保持所需性能的能力。
其核心是对产品的稳定性和寿命进行评估和预测,以确保产品在设计寿命内能够实现其设计要求。
可靠性设计涉及多个领域的知识,如材料学、力学、传热学等,是一门综合性的工程学科。
从产品的角度来看,可靠性设计具有重要的意义。
提高产品的可靠性可以大大降低产品的维修成本和维修频率,提高产品的使用寿命和经济性。
增强产品的可靠性能够提高产品在市场中的竞争力,增加消费者的信任度,从而带来更多的销售收入。
优化产品的可靠性还可以减少产品在使用过程中出现的故障和事故,从而降低了用户的安全风险和生产效率的损失。
可靠性设计在机械工程中具有非常重要的意义。
二、可靠性设计的方法与流程可靠性设计的方法和流程通常包括以下几个步骤:确定设计要求、制定设计规范、可靠性分析、优化设计和验证实验。
下面将详细介绍这些步骤。
1.确定设计要求确定设计要求是可靠性设计的第一步,也是最为关键的一步。
设计要求是指产品在特定使用条件下需要满足的性能要求和可靠性指标,如寿命、故障率、可靠性水平等。
在确定设计要求时,需要考虑产品的使用环境、负载条件、安全要求等因素,并将这些因素转化为具体的设计指标和要求。
2.制定设计规范根据设计要求,制定产品的设计规范,明确产品的结构、材料、工艺、质量要求、生产标准等内容。
设计规范是保证产品质量和可靠性的依据,是可靠性设计的基础。
3.可靠性分析可靠性分析是评估产品可靠性的重要手段,其目的是确定产品的可靠性水平、故障模式和故障原因,并对故障发生的概率和后果进行分析。
机械设计中的可靠性与安全性分析与研究

机械设计中的可靠性与安全性分析与研究在现代工业生产中,机械设计扮演着至关重要的角色。
无论是大型的工业设备,还是日常生活中的小型机械产品,其可靠性与安全性都直接关系到使用者的生命财产安全以及生产效率和经济效益。
因此,深入分析和研究机械设计中的可靠性与安全性问题具有极其重要的现实意义。
机械设计的可靠性,简单来说,就是指机械产品在规定的条件下和规定的时间内,完成规定功能的能力。
这不仅包括产品在正常使用条件下的稳定运行,还涵盖了在一些极端环境或意外情况下的适应性和容错能力。
而安全性则侧重于防止机械产品对人员造成伤害、对环境产生破坏等不良影响。
要实现机械设计的可靠性,首先需要对产品的使用需求和工作环境有清晰的认识。
例如,一台用于矿山开采的大型机械设备,其工作环境恶劣,粉尘多、湿度大、振动强烈,那么在设计时就需要选用能够适应这些条件的材料和零部件,并对结构进行优化,以确保其在长期的高强度作业中依然能够稳定运行。
同时,充分的可靠性试验也是必不可少的环节。
通过模拟实际工作条件,对产品进行各种性能测试,可以提前发现潜在的问题并加以改进,从而提高产品的可靠性。
在机械设计中,影响可靠性的因素众多。
设计方案的合理性是首要因素。
如果设计方案存在缺陷,例如结构不合理、受力不均等,那么即使选用了高质量的材料和先进的制造工艺,也难以保证产品的可靠性。
材料和零部件的质量同样关键。
低质量的材料和零部件容易出现磨损、疲劳、腐蚀等问题,从而影响整个机械系统的运行。
制造工艺的水平也会对可靠性产生影响。
粗糙的加工工艺可能导致尺寸偏差、表面粗糙度不符合要求等问题,进而影响产品的装配精度和性能。
安全性是机械设计中另一个不容忽视的方面。
机械产品在运行过程中可能会产生各种危险因素,如运动部件的碰撞、高温高压的介质泄漏、电气故障引发的火灾等。
为了确保安全性,在设计阶段就需要采取一系列的防护措施。
例如,对于高速旋转的部件,应设置防护装置,防止人员接触;对于可能产生高温高压的部位,应安装安全阀、压力表等监测和保护装置;对于电气系统,应采用绝缘材料、接地保护等措施,防止触电事故的发生。
机械结构可靠性设计与分析

机械结构可靠性设计与分析导言机械结构可靠性是指机械产品在设计、制造和使用过程中保持其预定性能的能力。
机械结构可靠性设计与分析是现代工程领域中的重要课题,对于确保产品的安全性、可用性和寿命至关重要。
本文将从可靠性设计的概念、方法和实践等方面进行讨论,以帮助读者更好地理解和应用机械结构可靠性设计与分析。
一、可靠性设计的概念可靠性设计是指在产品设计阶段就要考虑产品的可靠性问题,通过合理的设计来降低产品出现故障的可能性和减少故障对产品性能的影响。
可靠性设计的目标是确保产品在整个使用寿命内满足用户的要求,并保持良好的稳定性和可用性。
为了进行可靠性设计,需要对产品的使用环境、工作原理和故障模式等进行全面的分析和评估。
通过采用可靠性工程的方法和技术,可以对产品的各个部件和系统进行设计、优化和验证,从而提高产品的可靠性和性能。
二、可靠性设计的方法1. 可靠性分析可靠性分析是可靠性设计过程中必不可少的环节,通过对产品的各个部件和系统进行分析,可以确定故障发生的概率、故障模式和故障对产品性能的影响。
常用的可靠性分析方法包括故障模式与影响分析(FMEA)、故障树分析(FTA)和可靠性块图等。
这些方法可以帮助工程师在设计阶段识别和评估潜在的故障源,并采取相应的措施进行改进和优化。
2. 可靠性试验可靠性试验是验证设计的可靠性的常用方法之一,通过模拟产品的使用环境和负载条件进行试验,可以评估产品在实际使用中的可靠性和寿命。
常见的可靠性试验方法包括加速寿命试验、可靠性增长试验和可靠性示威试验等。
通过试验数据的分析和处理,可以得到产品的可靠性指标,为后续的设计改进提供依据。
三、可靠性设计的实践在实际的工程项目中,可靠性设计需要结合工程经验和专业知识进行综合考虑和分析。
下面将以一个机械结构设计的实例来介绍可靠性设计的实践过程。
假设我们需要设计一台机械臂,用于抓取和搬运重物。
首先,我们需要对机械臂的工作环境和使用要求进行分析,确定其受力和负载情况。
机械产品的可靠性设计与分析

机械产品的可靠性设计与分析在当今高度工业化的社会中,机械产品在各个领域都发挥着至关重要的作用。
从日常生活中的家用电器到工业生产线上的大型设备,从交通运输工具到航空航天领域的精密仪器,机械产品的可靠性直接影响着人们的生活质量、生产效率以及生命财产安全。
因此,机械产品的可靠性设计与分析成为了机械工程领域中一个极其重要的研究课题。
可靠性设计是指在产品设计阶段,通过采用各种技术和方法,确保产品在规定的条件下和规定的时间内,能够完成规定的功能,并且具有较低的故障率和较长的使用寿命。
可靠性分析则是对产品的可靠性进行评估和预测,找出可能存在的薄弱环节,为改进设计提供依据。
在机械产品的可靠性设计中,首先要进行的是需求分析。
这就需要充分了解产品的使用环境、工作条件、用户要求以及相关的标准和规范。
例如,对于一台用于户外作业的工程机械,需要考虑到恶劣的天气条件、复杂的地形地貌以及高强度的工作负荷等因素;而对于一台家用洗衣机,需要重点关注其洗涤效果、噪声水平和使用寿命等方面的要求。
只有明确了这些需求,才能为后续的设计工作提供正确的方向。
材料的选择是影响机械产品可靠性的重要因素之一。
不同的材料具有不同的物理、化学和机械性能,因此需要根据产品的工作要求和使用环境,选择合适的材料。
例如,在高温、高压和腐蚀环境下工作的零件,需要选用耐高温、耐高压和耐腐蚀的材料;对于承受重载和冲击载荷的零件,则需要选用高强度和高韧性的材料。
同时,还要考虑材料的成本和可加工性等因素,以确保产品在满足可靠性要求的前提下,具有良好的经济性。
结构设计也是可靠性设计的关键环节。
合理的结构设计可以有效地减少应力集中、提高零件的承载能力和抗疲劳性能。
例如,采用圆角过渡可以避免尖锐的棱角引起的应力集中;采用对称结构可以使载荷分布更加均匀;采用加强筋和肋板可以提高结构的刚度和强度。
此外,还需要考虑结构的装配和维修便利性,以便在产品出现故障时能够快速进行维修和更换零件。
机械系统的可靠性分析与设计
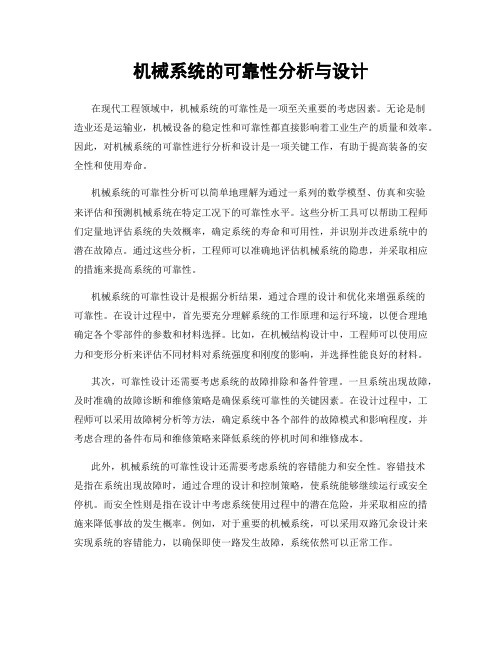
机械系统的可靠性分析与设计在现代工程领域中,机械系统的可靠性是一项至关重要的考虑因素。
无论是制造业还是运输业,机械设备的稳定性和可靠性都直接影响着工业生产的质量和效率。
因此,对机械系统的可靠性进行分析和设计是一项关键工作,有助于提高装备的安全性和使用寿命。
机械系统的可靠性分析可以简单地理解为通过一系列的数学模型、仿真和实验来评估和预测机械系统在特定工况下的可靠性水平。
这些分析工具可以帮助工程师们定量地评估系统的失效概率,确定系统的寿命和可用性,并识别并改进系统中的潜在故障点。
通过这些分析,工程师可以准确地评估机械系统的隐患,并采取相应的措施来提高系统的可靠性。
机械系统的可靠性设计是根据分析结果,通过合理的设计和优化来增强系统的可靠性。
在设计过程中,首先要充分理解系统的工作原理和运行环境,以便合理地确定各个零部件的参数和材料选择。
比如,在机械结构设计中,工程师可以使用应力和变形分析来评估不同材料对系统强度和刚度的影响,并选择性能良好的材料。
其次,可靠性设计还需要考虑系统的故障排除和备件管理。
一旦系统出现故障,及时准确的故障诊断和维修策略是确保系统可靠性的关键因素。
在设计过程中,工程师可以采用故障树分析等方法,确定系统中各个部件的故障模式和影响程度,并考虑合理的备件布局和维修策略来降低系统的停机时间和维修成本。
此外,机械系统的可靠性设计还需要考虑系统的容错能力和安全性。
容错技术是指在系统出现故障时,通过合理的设计和控制策略,使系统能够继续运行或安全停机。
而安全性则是指在设计中考虑系统使用过程中的潜在危险,并采取相应的措施来降低事故的发生概率。
例如,对于重要的机械系统,可以采用双路冗余设计来实现系统的容错能力,以确保即使一路发生故障,系统依然可以正常工作。
总之,机械系统的可靠性分析与设计是确保机械设备安全可靠运行的重要手段。
通过对系统进行综合的可靠性分析,工程师们可以识别系统中的潜在故障点,并采取相应的设计和控制措施来提高系统的可靠性。
浅谈机械可靠性设计

浅谈机械可靠性设计摘要:文章对机械可靠设计进行了概述,介绍了机械可靠性设计的原则和方法,并对其发展趋势进行了分析。
关键词:机械可靠性设计;发展趋势;原则方法可靠性是机械零件设计时必须考虑的重要指标。
只有那些可靠性好的产品,才能长期发挥其使用性能而受到客户的欢迎。
不仅如此,有些产品如汽车、轮船和飞机,如果其关键零部件不可靠,不仅会给客户带来不便,而且耽误时间、推迟日程,造成经济损失,甚至还可能直接危及使用者的生命安全。
1.机械可靠性概述1.1 定义GJB451-90 给出可靠性的定义:产品在规定时间内,在规定的使用条件下,完成规定功能的能力或性质。
可靠性的概率度量称为可靠度。
1.2 发展可靠性技术的研究开始于20 世纪20 年代,40 年代在结构工程设计中开始应用。
可靠性技术最早应用在二战末期德国V- Ⅱ火箭的诱导装置上。
自从1946 年Freuenthal 在国际上发表“结构的安全度”一文以来,可靠性问题开始引起学术界和工程界的普遍关注与重视。
当前,张义民等应用随机有限元法和一阶可靠性技术对随机结构可靠性问题进行了研究,开辟了以一次二阶矩法、摄动技术、有限元理论和实用概率统计学为基础的现代结构可靠性分析与设计理论的新途径。
1.3 我国机械可靠性设计发展及现状在我国可靠性研究开始于上世纪60年代,对于机械产品的可靠性研究则起步更晚,20世纪80年代才得到较快的发展,机械行业相继成立了可靠性研究的相关协会,各有关院所和高校也开展了机械产品的可靠性研究,制定了一批可靠性标准,取得了较大的成果。
王光远和谭东耀建立了基于随机模糊性的结构优化设计的概念和方法;陈立周等提出了一种基于概率密度函数矩不等式的契贝雪夫点法。
赵国藩等建立了广义随机空间内考虑随机变量相关性的结构可靠度实用分析方法,扩大了现有可靠度计算方法的适用范围。
李云贵和赵国藩提出了计算可靠度的4次高阶矩法,提高了可靠度的计算精度。
胡云昌等在分析现有可靠性计算方法的基础上,给出了较全面的评价结构系统可靠性的标准。
- 1、下载文档前请自行甄别文档内容的完整性,平台不提供额外的编辑、内容补充、找答案等附加服务。
- 2、"仅部分预览"的文档,不可在线预览部分如存在完整性等问题,可反馈申请退款(可完整预览的文档不适用该条件!)。
- 3、如文档侵犯您的权益,请联系客服反馈,我们会尽快为您处理(人工客服工作时间:9:00-18:30)。
17
可靠性设计步骤(13~15步 )
❖ 13)计算各个零件的可靠度
对于系统中所有的关键零部件重复上述步骤,求出各自的可靠度。
❖ 14)计算系统的可靠度(具有迭代性)
在已知每个零部件可靠度的基础上,计算子系统的以及整个系统的 可靠度。
14
可靠性设计步骤(11步 )
❖ 11)确定同时考虑到所有致命失效模式情况下零件的可靠度
确定每一失效模式的可靠度之后,下一步是确定考虑所有失效模式 的零件的整个可靠度
一种方法是,假设所有的失效模式都是可能的,每个失效模式可能 是独立地或相关的产生,当至少一种失效模式出现时,零件即失效。
n
R0 R1R2R3 K K Rn Ri i 1
机械可靠性设计分析
(第五部分)
张建国
北京航空航天大学 工程系统工程系
1
第四章 设计方法与静强度可靠性设计
❖ 4.1 机械零件设计应考虑的问题 ❖ 4.2 可靠性设计方法与步骤 ❖ 4.3 静强度可靠性设计 ❖ 4.4 小结 ❖ 4.5作业
2
4.1 机械零件设计应考虑的问题
❖ 研制费用问题
应用可靠性设计方法,比应用传统的设计方法要花费较 多的时间和费用。
❖ 10)对于每一种致命的失效模式,确定其与应力分 布和强度分布相关的可靠度。
对于零件的每一种致命的失效模式,都应计算其可靠度。 这些失效模式可能是:屈服、断裂、疲劳、过度变形、 压杆室温、振幅过大、蠕变、磨损、腐蚀、噪声过大等。
有的零件可能只有一种致命的失效模式,这时只需要根 据这一种失效模式的判据来计算可靠度。但是,在别的 情况下,很可能还有其它的致命失效模式。这时,当然 也需要计算与这些失效模式相应的可靠度。
11
可靠性设计步骤(6 ~ 7步 )
❖ 6)确定应力公式
对于每一种失效模式,必须确定载荷、尺寸、温度、时 间、物理性质、使用和工作环境等设计变量和参数之间 的函数关系,从而得到应力公式。
❖ 7)确定每个失效模式下的应力分布
对于每一种失效模式,必须确定载荷、尺寸、温度、时 间、物理性质、使用和工作环境等设计变量和参数之间 的函数关系,从而得到应力公式。
另一种方法是,假定零件将在最可能发生的一种失效模式下失效
R0 Rimin
15
可靠性设计步骤(11步 )
比较两种方法,零件的实际可靠度是在上两式所给出的值之间。如 果的确是由于单一的失效模式引起零件失效,则实际的可靠度将接
近于或等于 Rim。in 如果是n由于多种原因引起零件失效,则零件的实际
据粗略统计,需要增加的时间大约为1/4~2倍,而需要增 加的费用约为1/5~1/2。
但是在取得了设计经验和积累了设计数据之后,情况便 会大有改善。而且,多花费的时间和费用在以后能够得 到补偿。因为可靠性设计能够消除保守的、不合理的设 计,同时,在零件和设备的整个寿命期内,失效次数会 减少,而维修费用也会降低。
28
静强度可靠性设计举例
29
静强度可靠性设计举例
30
静强度可靠性设计举例
31
静强度可靠性设计举例
32
静强度可靠性设计举例
33
静强度可靠性设计举例
34
静强度可靠性设计举例
35
静强度可靠性设计举例
36
静强度可靠性设计举例
37
静强度可靠性设计举例
38
静强度可靠性设计举例
39
静强度可靠性设计举例
10
可靠性设计步骤(5步 )
❖ 5)确定涉及到的每种失效模式的判据
比较常用的判据有: (1)最大正应力; (2)最大剪应力; (3)最大变形能; (4)最大应变能; (5)最大应变; (6)最大变形; (7)疲劳情况下的变形能; (8)疲劳情况下的最大总应变; (9)最大许用腐蚀量; (10)最大许用磨损量; (11)最大许用振幅; (12)最大许用蠕变,等等。
❖ 静强度概率设计方法
强度应力干涉理论(第三部分)
强度与应力都是正态分布时,可靠度的计算公式
R f Z dZ
0
其中: Z S s
Z
2 S
2 s
(3-1)
为可靠性指标,(3-1)式将强度、应力和可靠度三者
联系起来了,称为“联结方程”
其他常用概率分布的可靠度计算公式参见表3-1。
19
9
可靠性设计步骤(4步 )
❖ 4)确定零件的失效模式是独立的还是相关的
如果所有的失效模式是互相独立的,也就是说一种失效 模式不影响任何其它失效模式的性质,则在进行一种失 效模式下的应力及强度计算时,不需考虑所有其它失效 模式的影响。
如果一种失效模式的性质受到另一个可能同时发生的失 效模式的影响,则受到影响的应力和强度应当加以修正。 这样计算出的每种失效模式的可靠度,将是互相独立的。
3
机械零件设计应考虑的问题
❖ 解决主要问题与主要矛盾
进行可靠性设计时,应当注意,并不是所有的零部件都 要求很高的可靠度,也不是所有的零部件都要求同样的 可靠性指标。
例如一架有30000多个零(元)件的飞机,经常发生故障 的零件只有600多个,即只占2%左右。根据帕累托定理 (Pareto Law),这600多个零件称为主要少数,其余 30000多个称为次要多数。
例如,当提到“某零件在置信度为90%时的可靠度为95%”时,意 思是说:
(1)在100个零件中,经过一定时间t之后,有5个可能会失效,表 示为R(t)=0.95;
(2)在对10个样本(容量为n=100)进行试验时,其中9个样本中 将有5个或少于5个的零件失效;有一个样本会有5个以上的零件失效, 表示为C.L.=0.90。
静强度可靠性设计
❖ 静强度概率设计的主要步骤为
给定结构零部件的设计可靠性指标 确定主要失效模式 确定每种失效模式应力分布 确定每种失效模式的强度分布 应用连接方程确定零部件的设计参数
20
静强度可靠性设计举例
查标准正态分布表得可靠性系数: 3.1
21
静强度可靠性设计举例
22
静强度可靠性设计举例
8
可靠性设计步骤(3步 )
❖ 3)进行失效模式、影响及危害性分析(FMECA)
目的找出所设计系统的关键件与重要件,找出影响系统 功能和可靠性的主要失效模式。使设计人员在设计时抓 住主要矛盾。
因为进行可靠性设计时,应当注意,并不是所有的零部 件都要求很高的可靠度,也不是所有的零部件都要求同 样的可靠性指标。
然后对设计进行迭代,直到系统的可靠度等于或大于事先规定的系 统可靠度目标值为止。
❖ 15)系统优化综合
如果必要,对整个设计的下列内容进行优化,包括:(1)性能; (2)可靠性;(3)维修性;(4)安全;(5)费用;(6)重量; (7)体积;(8)操作性;(9)交货日程表,可靠度将接近于或等于 Ri。 i 1
实际上,零件的真实的可靠度只有在进行集中的可靠性试验或获得 并分析实际使用数据之后,才能计算出经过验证了的可靠度。图3-6 所示为求零件的整个可靠度的流程。
16
可靠性设计步骤(12步 )
❖ 12)确定零件可靠度的置信度
在求出零件的可靠度之后,便会产生一个问题:“这个预测的可靠 度在多大程度上是可以相信的?”这时,便需引入置信度的概念。
求为止。
53
作业
54
表9-1 荐用的可靠度值分类表
55
表9-2 一些机械产品的可靠性指标(七十年代)
56
图3-3 航天飞行器的任务轮廓
57
图3-4 航天飞行器的环境轮廓
58
图3-3 航天飞行器的任务轮廓
59
表3-3 航天飞行器功能系统的目标可靠度分配
60
图3-6 确定零件可靠度的流程
52
4.4 小结
❖ 可靠性设计的主要理论基础:干涉理论。 ❖ 强度可靠性设计的主要思路:
1)确定主要失效模式; 2)确定每种失效模式应力分布; 3)确定每种失效模式的强度分布; 4)应用连接方程计算零可靠度; 5)同设计要求的可靠度相比,满足设计要求,结束。 6)不满足要求,调整设计参数或从新选材,直到满足要
表9-2所列为国外七十年代的一些机械产品的可靠性指标, 可供参考和比较。
5
4.2 可靠性设计方法与步骤
❖ 六十年代初期由D.Kececioglu教授提出的方法:
这一方法认为,现代的复杂而昂贵的零件和系统要求高可靠性,所 以必须保证把规定的可靠性目标值设计到零件中去,从而设计到系 统中去。
在实际使用和工作环境下零件的应力的所有参数,实际零件的强度 的所有参数,都是随即变量或呈分布状态。
7
可靠性设计步骤(2步 )
❖ 2)确定有关的设计变量和参数
这些设计变量和参数应当是: (1)对设计任务是有意义的; (2)唯一的和不重复的; (3)在试验前后和进行期间都能度量的。
凡设计任务涉及的所有基本方程都能用这些设计变量和 参数来进行计算。
例如在设计同时受弯矩和扭矩作用的轴时,需要确定的 设计变量和参数有:轴的直径d,弯应力,剪应力,材料 的持久极限,以及应力集中系数、尺寸系数和表面质量 系数等。
40
静强度可靠性设计举例
41
静强度可靠性设计举例
42
静强度可靠性设计举例
43
静强度可靠性设计举例
44
静强度可靠性设计举例
45
静强度可靠性设计举例
46
静强度可靠性设计举例
47
静强度可靠性设计举例
48
静强度可靠性设计举例
49
静强度可靠性设计举例
50
静强度可靠性设计举例
51
静强度可靠性设计举例
所以:
s
(s , s
)