广数圆度误差调试指导说明书
广州数控GSK25i使用手册 五轴联动系统(参数篇)

注 意 事 项
■ 运输与储存
● 产品包装箱堆叠不可超过六层 ● 不可在产品包装箱上攀爬、站立或放置重物 ● 不可使用与产品相连的电缆拖动或搬运产品 ● 严禁碰撞、划伤面板和显示屏 ● 产品包装箱应避免潮湿、暴晒以及雨淋
■ 开箱检查
● 打开包装后请确认是否是您所购买的产品 ● 检查产品在运输途中是否有损坏 ● 对照清单确认各部件是否齐全,有无损伤 ● 如存在产品型号不符、缺少附件或运输损坏等情况,请及时与本公司联 系
3
GSK25i 铣床加工中心数控系统 使用手册(第 3 分册: 参数篇)
安 全 责 任
制造者的安全责任
——制造者应对所提供的数控系统及随行供应的附件在设计和结构上已消除和/ 或控制 的危险负责。 ——制造者应对所提供的数控系统及随行供应的附件的安全负责。 ——制造者应对提供给使用者的使用信息和建议负责。
本使用手册的版权,归广州数控设备有限公司 所有,任何单位与个人进行出版或复印均属于非法行 为,广州数控设备有限公司将保留追究其法律责任的 权利。
1
GSK25i 铣床加工中心数控系统 使用手册(第 3 分册: 参数篇)
前
言
尊敬的客户:
对您惠顾选用广州数控设备有限公司的GSK 25i 铣床加工 中心数控系统,我们深感荣幸。 本手册为“使用手册第 3 分册:参数篇”部分。
设置参数的操作步骤如下所示: (1) 按 进入偏置设置界面,先进行相应的密码输入。
为了防止加工程序、CNC 参数等被恶意修改,GSK25i 系统提供了权限设置功能,密 码等级分为 5 级,由高到低分别为 1 级(系统厂商级) 、2 级(机床厂商级) 、3 级(高级用 户级) 、 4 级(普通用户级) 、开机上电系统默认最低级别(见图 2-1) 。
圆度仪操作规程
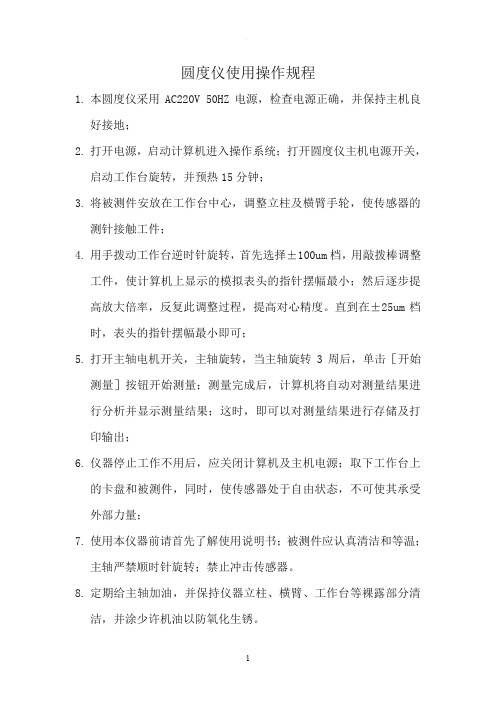
圆度仪使用操作规程1.本圆度仪采用AC220V 50HZ电源,检查电源正确,并保持主机良好接地;2.打开电源,启动计算机进入操作系统;打开圆度仪主机电源开关,启动工作台旋转,并预热15分钟;3.将被测件安放在工作台中心,调整立柱及横臂手轮,使传感器的测针接触工件;4.用手拨动工作台逆时针旋转,首先选择±100um档,用敲拨棒调整工件,使计算机上显示的模拟表头的指针摆幅最小;然后逐步提高放大倍率,反复此调整过程,提高对心精度。
直到在±25um档时,表头的指针摆幅最小即可;5.打开主轴电机开关,主轴旋转,当主轴旋转3周后,单击[开始测量]按钮开始测量;测量完成后,计算机将自动对测量结果进行分析并显示测量结果;这时,即可以对测量结果进行存储及打印输出;6.仪器停止工作不用后,应关闭计算机及主机电源;取下工作台上的卡盘和被测件,同时,使传感器处于自由状态,不可使其承受外部力量;7.使用本仪器前请首先了解使用说明书;被测件应认真清洁和等温;主轴严禁顺时针旋转;禁止冲击传感器。
8.定期给主轴加油,并保持仪器立柱、横臂、工作台等裸露部分清洁,并涂少许机油以防氧化生锈。
YD200圆度仪的调整和检查一、主轴精度的检查本仪器的主轴精度要求:≤0.10μm将随仪器附带的玻璃半球作为试件,分几个方位测定,然后看各方向的测量结果是否相似,如果相似则测量一次即可判明主轴的圆度。
必须小心保护玻璃半球,可用软布或棉球沿圆面试拂,而不许用力静擦某点。
在试拂前也可将甲醇中加几滴油的溶液涂在球面上,以便在表面上留下一层油脂,可以清除浮渣。
如用手拿住的时间较长(如清理时),则在检查前必须将其放在工作台上使其等温,然后才能测量。
二、放大倍数的调整打开圆度仪,选择±25um档对随仪器附带的定标块进行测量,在2~50档,对定标快的圆度值进行评定,比较其测量值与定标块的标定值,如果二者不一致。
则打开计算机主机箱,可以看到如下图所示的前置板卡,调整图中所示的电位器(标记为4号)。
圆度仪校准规范【详解】
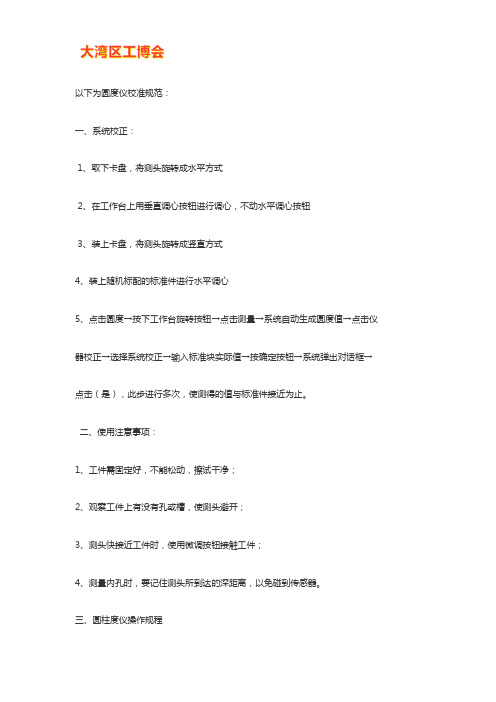
以下为圆度仪校准规范:一、系统校正:1、取下卡盘,将测头旋转成水平方式2、在工作台上用垂直调心按钮进行调心,不动水平调心按钮3、装上卡盘,将测头旋转成竖直方式4、装上随机标配的标准件进行水平调心5、点击圆度→按下工作台旋转按钮→点击测量→系统自动生成圆度值→点击仪器校正→选择系统校正→输入标准块实际值→按确定按钮→系统弹出对话框→点击(是),此步进行多次,使测得的值与标准件接近为止。
二、使用注意事项:1、工件需固定好,不能松动,擦试干净;2、观察工件上有没有孔或槽,使测头避开;3、测头快接近工件时,使用微调按钮接触工件;4、测量内孔时,要记住测头所到达的深距离,以免碰到传感器。
三、圆柱度仪操作规程打开气源→启动仪器→打开电脑→仪器归零→工件调整→各项测量1、工件调整:调整对心功能是测量准确性的前提准备首先:根据实际测量要求选取内外圆方式,系统默认为外圆。
其次:根据工件选择适量档位,共有5个档位,±5um,±10um,±30um,±100um,±300um. 第三步:将待测工件洗干净,采用精密卡盘装夹紧工件,侧头缓慢接触到工件表面,大概传感器读数为零左右。
第四步:顺时针旋转工作台180°,记下此刻读数,不要动调偏心装置在该位置,调整旋钮把偏心读数为(读数一+读数二)/2;如读数一为负,加其值。
如超量程,按上方法把传感器调到量程内。
按此办法调整另一旋钮,调整完毕后即可把偏心跳到1um左右。
2、工件调整好后可进行圆度、圆柱度、同心度、同轴度的测量。
圆度的测量:点击圆度→按下工作台旋转按钮→点击调整→系统自动显示图形与所测数据。
圆柱度的测量:点击圆柱度→按下工作台旋转按钮→点击调整→选择手动→点击测量→依照提示依次选择三个圆柱面→系统自动显示图形与所测数据同心度的测量:点击同心度→按下工作台旋转按钮→点击调整→点击测量→依照提示依次选择二个面→系统自动显示图形与所测数据同轴度的测量:点击同轴度→按下工作台旋转按钮→点击调整→点击测量→依照提示依次选择三个面→系统自动显示图形与所测数据。
数控机床的加工精度误差分析与校正方法
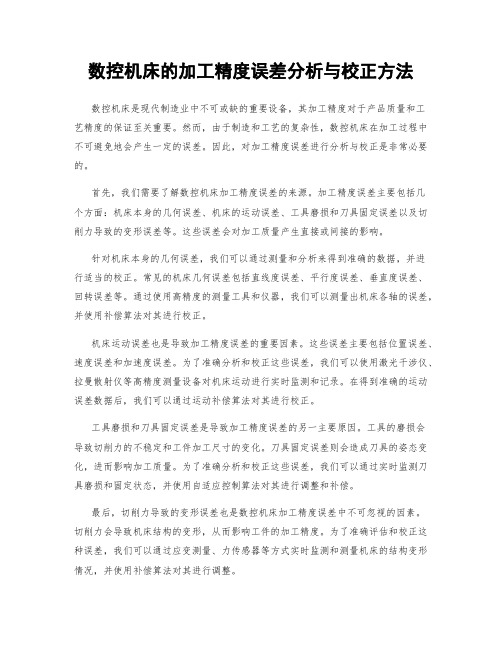
数控机床的加工精度误差分析与校正方法数控机床是现代制造业中不可或缺的重要设备,其加工精度对于产品质量和工艺精度的保证至关重要。
然而,由于制造和工艺的复杂性,数控机床在加工过程中不可避免地会产生一定的误差。
因此,对加工精度误差进行分析与校正是非常必要的。
首先,我们需要了解数控机床加工精度误差的来源。
加工精度误差主要包括几个方面:机床本身的几何误差、机床的运动误差、工具磨损和刀具固定误差以及切削力导致的变形误差等。
这些误差会对加工质量产生直接或间接的影响。
针对机床本身的几何误差,我们可以通过测量和分析来得到准确的数据,并进行适当的校正。
常见的机床几何误差包括直线度误差、平行度误差、垂直度误差、回转误差等。
通过使用高精度的测量工具和仪器,我们可以测量出机床各轴的误差,并使用补偿算法对其进行校正。
机床运动误差也是导致加工精度误差的重要因素。
这些误差主要包括位置误差、速度误差和加速度误差。
为了准确分析和校正这些误差,我们可以使用激光干涉仪、拉曼散射仪等高精度测量设备对机床运动进行实时监测和记录。
在得到准确的运动误差数据后,我们可以通过运动补偿算法对其进行校正。
工具磨损和刀具固定误差是导致加工精度误差的另一主要原因。
工具的磨损会导致切削力的不稳定和工件加工尺寸的变化。
刀具固定误差则会造成刀具的姿态变化,进而影响加工质量。
为了准确分析和校正这些误差,我们可以通过实时监测刀具磨损和固定状态,并使用自适应控制算法对其进行调整和补偿。
最后,切削力导致的变形误差也是数控机床加工精度误差中不可忽视的因素。
切削力会导致机床结构的变形,从而影响工件的加工精度。
为了准确评估和校正这种误差,我们可以通过应变测量、力传感器等方式实时监测和测量机床的结构变形情况,并使用补偿算法对其进行调整。
总结来说,数控机床的加工精度误差分析与校正是确保产品质量和工艺精度的关键步骤。
在这个过程中,我们需要准确地识别和分析加工精度误差的来源,并采取相应的校正措施。
数控滑枕铣床加工圆形工件的精度调整
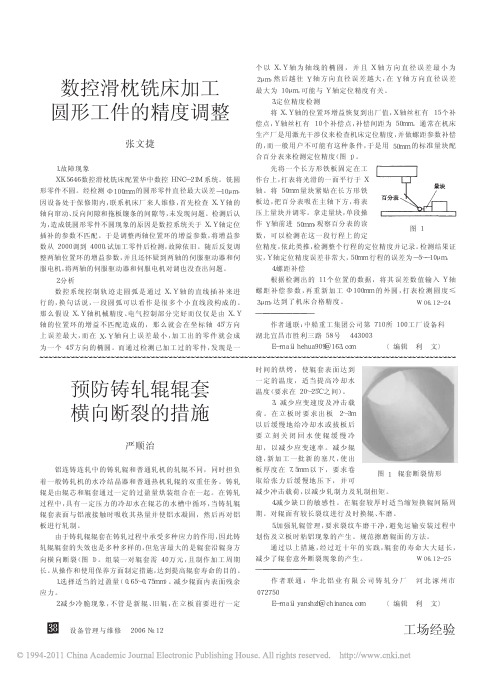
E- mail: yanshzh@chinanca.com 〔 编辑 利 文〕
!" 设备管理与维修 2006 №12
工场经验
由于铸轧辊辊套在铸轧过程中承受多种应力的作用, 因此铸 划伤及立板时粘铝现象的产生。规范擦磨辊面的方法。
轧辊辊套的失效也是多种多样的, 但危害最大的是辊套沿辊身方
通过以上措施, 经过近十年的实践, 辊套的寿命大大延长,
向横向断裂( 图 1) 。组装一对辊套需 40 万元, 且制作加 工 周 期 减少了辊套意外断裂现象的产生。
铝连铸连轧中的铸轧辊和普通轧机的轧辊不同, 同时担负 着一般铸轧机的水冷结晶器和普通热机轧辊的双重任务。铸轧
板 厚 度 在 7.5mm 以 下 , 要 求 卷 取给张力后缓慢地压下, 并可
图 1 辊套断裂情形
辊是由辊芯和辊套通过一定的过盈量烘装组合在一起。在铸轧 减少冲击载荷, 以减少轧制力及轧制扭矩。
时间的烘烤, 使辊套表面达到
预防铸轧辊辊套
一定的温度, 适当提高冷却水 温度( 要求在 20~25℃之间) 。
横向断裂的措施
3. 减少应变速度 及 冲 击 载 荷 。 在 立 板 时 要 求 出 板 2~3m 以后缓慢地给冷却水或拔板后
严顺治
要立刻关闭回水使辊缓慢冷 却, 以减少应变速率。减少辊
缝, 新加工一批新的塞尺, 使出
行的, 换句话说, 一 段 圆 弧 可 以 看 作 是 很 多 个 小 直 线 段 构 成 的 。 3μm, 达到了机床合格精度。
W06.12- 24
那么假设 X、Y 轴机械精度、电气控制部分完好而仅仅是由 X、Y — —— —— —— —— —— —— ——
轴的位置环的增益不匹配造成的, 那么 就 会 在 坐 标 轴 45°方 向 上 误 差 最 大 , 而 在 X、Y 轴 向 上 误 差 最 小 , 加 工 出 的 零 件 就 会 成
广州数控数控车床操作编程说明书
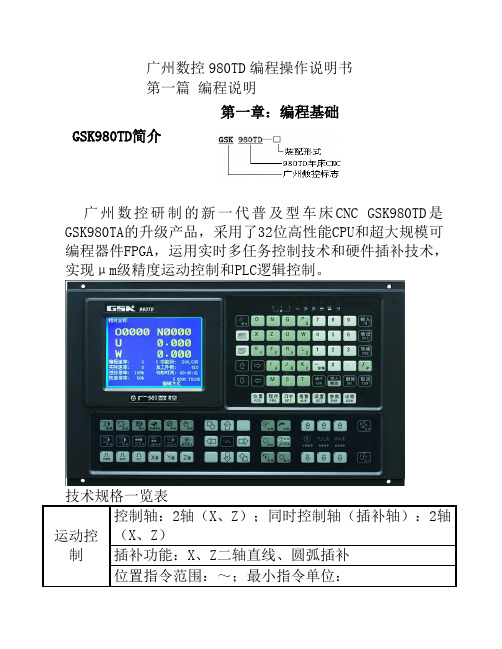
广州数控980TD 编程操作说明书第一篇 编程说明第一章:编程基础GSK980TD 简介广州数控研制的新一代普及型车床CNC GSK980TD 是GSK980TA 的升级产品,采用了32位高性能CPU 和超大规模可编程器件FPGA ,运用实时多任务控制技术和硬件插补技术,实现μm 级精度运动控制和PLC 逻辑控制。
技术规格一览表运动控制 控制轴:2轴(X 、Z );同时控制轴(插补轴):2轴(X 、Z )插补功能:X 、Z 二轴直线、圆弧插补位置指令范围:~;最小指令单位:机床数控系统和数控机床数控机床是由机床数控系统(Numerical Control Systems of machine tools)、机械、电气控制、液压、气动、润滑、冷却等子系统(部件)构成的机电一体化产品,机床数控系统是数控机床的控制核心。
机控系统由控制装置(Computer Numerical Controler简称CNC)、伺服(或步进)电机驱动单元、伺服(或步进)电机等构成。
数控机床的工作原理:根据加工工艺要求编写加工程序(以下简称程序)并输入CNC,CNC加工程序向伺服(或步进)电机驱动单元发出运动控制指令,伺服(或步进)电机通过机械传动构完成机床的进给运程序中的主轴起停、刀具选择、冷却、润滑等逻辑控制指令由CNC传送给机床电气控制系统,由机床电气控制系统完成按钮、开关、指示灯、继电器、接触器等输入输出器件的控制。
目前,机床电气控制通常采用可编程逻辑控制器(Programable Logic Controler 简称PLC),PLC具有体积小、应用方便、可靠性高等优点。
由此可见,运动控制和逻辑控制是数控机床的主要控制任务。
GSK980TD车床CNC同时具备运动控制和逻辑控制功能,可完成数控车床的二轴运动控制,还具有内置式PLC功能。
根据机床的输入、输出控制要求编写PLC程序(梯形图)并下载到GSK980TD,就能实现所需的机床电气控制要求,方便了机床电气设计,也降低了数控机床成本。
圆度仪使用说明书Microsoft Word 文档

Y90系列高速圆度仪使用说明书1一.用途和特点1.用途:本仪器主要用于轴承行业测量各种轴承套圈内外径及内外滚道之圆度、波纹度,还可测量短圆柱滚子、钢球的圆度、波纹度,并可对被测轮廓表面状态做谐波分析和斜率分析。
适于在车间或计量室使用。
可用于机床故障分析调整机床,零件工艺分析试验,零件或成品检验等。
2.特点:结构简单,操作方便,适于车间使用,图形和数字显示工件圆度的形状及数值,数据准确可靠,屏幕提示清晰,菜单选择,速度快、操作简单、稳定性好,测量结果可通过打印机打印出来。
二.主要技术指标1. 测量范围:最小内径 f 17mm最大外径 f 130mm (可根据用户要求,到f 250mm)最大高度100mm最大重量10Kg2. 主轴精度:采用标准玻璃球鉴定仪器整个系统的综合误差。
主轴的旋转精度优于0.08m m3. 主轴转速:115转/分4. 放大倍率及分辨率:4.1 放大倍率(测量范围)4.2 分辩率:0.01m m(适用于所有量程)5.滤波范围:分六个波段:2~152~502~1502~50015~50016.气源压力:4×105Pa~5×105Pa(主轴工作压力)7.环境要求:温度:10℃——30℃相对湿度:低于85% (未压缩)8.电源:单相AC220V±10%50Hz9.消耗功率:约300W10.测量效率:50~100件/小时。
三.仪器工作原理本仪器采用的是半径法测量圆度,工件旋转式.如图一所示:将工件19放在工作台18的大致中心位置上,启动电机31,通过调心装置17对工件进行调心,使工件被调整到与空气主轴27同心,通过传感器21可将工件的轮廓形状变化转换为电信号,通过插入计算机内的前置电路进行转换、滤波、放大,再经A/D转换为数字信号,在主机内进行处理计算,在显示器上显示出整个测量过程及最终结果,包括圆度值和被测截面的轮廓形状以及最小二乘法圆度值。
除此之外,还可进行最小区域法、最大内接圆、最小外切圆圆度值计算,斜率分析、谐波分析等,并可根据需要在打印机上打印图形及数据。
广_州_数_控_GSK928TE_数控系统用户手册范本
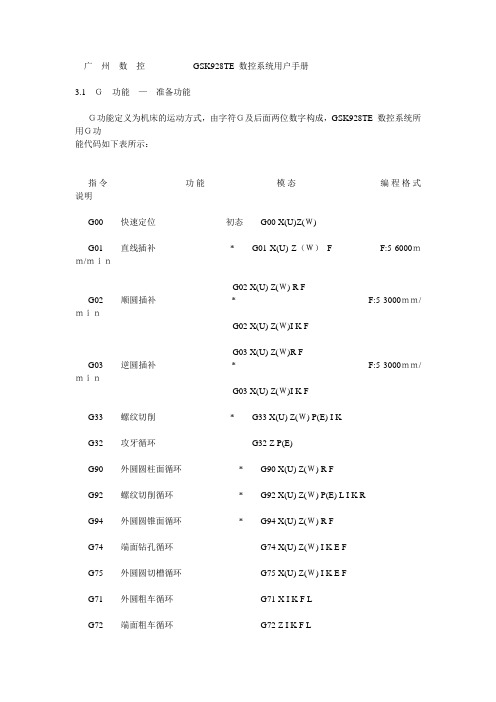
广州数控GSK928TE 数控系统用户手册3.1 G功能—准备功能G功能定义为机床的运动方式,由字符G及后面两位数字构成,GSK928TE 数控系统所用G功能代码如下表所示:指令功能模态编程格式说明G00 快速定位初态G00 X(U)Z(W)G01 直线插补* G01 X(U) Z(W)F F:5-6000mm/minG02 X(U) Z(W) R FG02 顺圆插补* F:5-3000mm/minG02 X(U) Z(W)I K FG03 X(U) Z(W)R FG03 逆圆插补* F:5-3000mm/minG03 X(U) Z(W)I K FG33 螺纹切削* G33 X(U) Z(W) P(E) I KG32 攻牙循环G32 Z P(E)G90 外圆圆柱面循环* G90 X(U) Z(W) R FG92 螺纹切削循环* G92 X(U) Z(W) P(E) L I K RG94 外圆圆锥面循环* G94 X(U) Z(W) R FG74 端面钻孔循环G74 X(U) Z(W) I K E FG75 外圆圆切槽循环G75 X(U) Z(W) I K E FG71 外圆粗车循环G71 X I K F LG72 端面粗车循环G72 Z I K F LG22 局部循环开始G22 LG80 局部循环结束G80G50 设置工件绝对坐标系G50 X ZG26 X、Z 轴回参考点G26 按G00 方式快速移动G27 X 轴回参考点G27 按G00 方式快速移动G29 Z 轴回参考点G29 按G00 方式快速移动G04 定时延时G04 DG93 系统偏置G93 X(U)Z(W)G98 每分进给* G98 F 1~6000mm/minG99 每转进给G99 F 0.01~99.99mm/r注1:表中带*指令为模态指令,即在没有指定其它G 指令的情况下一直有效。
注2:表中指令在每个程序段只能有一个G04 之外的G 代码,仅G04 指令可和其它G 代码在同一程序段中出现。
- 1、下载文档前请自行甄别文档内容的完整性,平台不提供额外的编辑、内容补充、找答案等附加服务。
- 2、"仅部分预览"的文档,不可在线预览部分如存在完整性等问题,可反馈申请退款(可完整预览的文档不适用该条件!)。
- 3、如文档侵犯您的权益,请联系客服反馈,我们会尽快为您处理(人工客服工作时间:9:00-18:30)。
圆度误差调试指导
原理说明: 18XP系列世纪星硬件设计具有可以采集脉冲数据的特性,因而可以来对走圆过程中的X轴与Y轴的脉冲进行采集与分析,带有采集功能的18XP设
计了通过图形界面的方式来显示两轴的同步误差,对两个进给轴插补铣圆的轨
迹进行同步描绘并显示出误差精度,以便分析后进行相关参数调整,将铣削圆
度误差控制在较小的范围内。
接线说明: 1.0.3m 电缆和2m 电缆共同的DB15头孔接到21(或18)世纪星的轴口
2.0.3m 电缆的DB15头针接到21(或18)世纪星的轴口指令线上
3.2m 电缆的另一DB15头孔接到18XP的轴口上
[注意]:以上接线中,21(或18)系统的X轴与18XP的X轴连接;21(或
18)系统的Y轴与18XP的Y轴连接
18XP调试18系列世纪星的接线见<刚性攻丝调试指导说明书>附图1
18XP调试21系列世纪星的接线见<刚性攻丝调试指导说明书>附图2
参数设置: 在21的轴参数中设置以下几个参数:
1、外部脉冲当量分子:18XP跟21设置成一致;
2、外部脉冲当量分母:18XP设置成21的值乘以4;例如,21若为2,
则18XP需设置成8;
3、电机每转脉冲数:18XP设置成21的值乘以4;例如,21若为2500,
则18XP设置成10000;
4、是否带反馈:18XP和21都需设置成45(带反馈);
在18的轴参数中设置以下几个参数:
5、外部脉冲当量分子:18XP跟18设置成一致;
6、外部脉冲当量分母:18XP跟18设置成一致;
7、电机每转脉冲数:18XP跟18设置成一致;
8、是否带反馈:18XP和21都需设置成45(带反馈);
另外18XP中要设置:
1、要查看18XP中:“诊断”-“伺服调试”-“轴设置”中是否为系统默
认设置,即(x y z c):(0 1 2 0),若不是,则改为如此。
2、要查看18XP中:“诊断”-“伺服调试”-“轮廓误差”-“参数设置”
中是否为系统默认设置,即radius =20 ,此值与18XP系统自带的G代码程序
O00F1中的铣圆半径值20一致;若要修改圆半径,则这两个值都要修改成一
致。
[注意]:18XP的X轴轴参数对应21(或18)的X轴轴参数;18XP的Y轴轴参数对应21(或18)的Y轴轴参数。
编程实例: %1234
G92 X0 Y0 Z0 ;设立工件坐标系
G02 X0 Y0 I40 J0 F500 ;以工件坐标系零点为起点和终点,画半径
40的圆(此编程半径值必须为“参数设置”
中半径值的2倍)
M30
测试步骤: 1、编辑好以上的测试程序(注意画圆的半径值),进入“伺服调试”中的“轮廓误差”,然后将18XP设置成检测“实际”脉冲的状态(“采样停止”后
用PgDn键选择)。
2、然后先按“记录开始”,再让21(或18)系统走铣圆程序,18XP界面
上就会显示圆弧行走轨迹。
注意:检测之前先将两个进给轴的反向间隙暂时设置为0,因为18XP系统检测的反馈信号是从电机读取,所以设置反向间隙后在检测电机轨迹过象限
时检测轨迹会有很明显的突跳,不利于观察。
调试示例:1)、分析下图可以得出,X轴驱动增益偏软,Y轴增益偏硬。
根据这个结论对进给轴驱动器的参数进行调整,直到检测得到的圆弧轨迹在视觉上看不出
明显偏差。
此外,还可以通过测量两个轴同步误差的方法来检测两个轴是否匹配,测量方法:用18XP“伺服调试”中的“同步误差”功能测量X、Y轴,螺距设
置为1,使X、Y轴插补行走45度的斜线,也可以得出两轴的同步误差,相
应的对伺服驱动器进行参数调整消除误差。
2)、下图的情况为:X轴驱动增益偏硬,Y轴增益偏软
3)、下图的情况为:系统设置了X轴反向间隙,没有设置Y轴反向间隙
4)、下图的情况为:系统设置了Y轴反向间隙,没有设置X轴反向间隙
5)、系统不设置X轴的螺距误差补偿,只设置Y轴的螺距误差补偿
6)、系统设置X、Y轴的螺距误差补偿
根据以上情况对相应的参数值进行调整后,可以得出较小误差的圆轨迹,说明数控系统发出的圆弧脉冲指令在理论上是理想的。
之后补上机床反向间隙可以进行实际加工测量。
将X、Y轴反向间隙设置正确,进行加工完成测量。
加工后进行4个象限的测量,如果4个象限上有误差应该是机械精度造成的;如果是其它地方上有误差则为反向间隙造成的。
如果出现的测量结果与图1)基本相似的话,应该为X向反向间隙设置偏小,Y向反向间隙设置过大造成的。
进行相关参数的调整,应该可以达到理想的效果。