-精益生产项目报告模板-华制-20100613
精益生产项目改善报告模板

时间
% 完成
备注
Note: • 请包括改善项目在研讨会结束后需要跟踪的行动措施. • 工厂精益领导对此表的行动措施担负追踪推动责任. • 精益领导从此表中选择需要在其他工厂/生产线推广的措施,并推动实施。
25% Complete 50% Complete
75% Complete 100% Complete
责任人
目标完成日期
时间 计划
结束
% 完成百分比
备注
25% Complete 50% Complete
75% Complete 100% Complete
改善活动中学到的经验教训和知识工具
序号 1 2 3 4 5 6
知识工具/经验教训
描述
改善日志 – 持续推广的提案
持续推广提案I
责任人
目标完成日 期
运营单元 / 工位
问题
措施
指标/(单位) 改善前
结果
改善后
% 提高
客户
节约
持续保持的 方法
硬节约(金 额/每月)
软节约(金 额/每月)
照片-改善前
照片-改善后
标题:
子标题3:XXXX (该改善项目包含的独立子改善项目)
运营单元 / 工位
问题
措施
指标/(单位) 改善前
结果
改善后
% 提高
客户
节约
持续保持的 方法
标准化作业表 – 改善前:
标准化作业表 – 改善后
标准化作业表 – 改善后:
作业员平衡图 – 改善前
作业员平衡图 – 改善前:
作业员平衡图 – 改善后
作业员平衡图 – 改善后:
设备平衡图 – 改善前
设备平衡图 – 改善前:
工厂精益生产工作总结报告

工厂精益生产工作总结报告
近年来,我工厂在精益生产方面取得了显著的成绩。
通过全体员工的共同努力,我们成功地实施了一系列精益生产措施,取得了生产效率的显著提升,产品质量的大幅提高和成本的有效控制。
以下是我们工厂精益生产工作的总结报告。
首先,我们对生产流程进行了全面的优化。
通过价值流映射和价值流分析,我
们发现了生产过程中的瓶颈和浪费,通过精益生产工具,我们对生产流程进行了重新设计和优化,大大缩短了生产周期,提高了生产效率。
其次,我们注重员工的培训和激励。
我们通过培训,使员工了解精益生产的理
念和方法,并激励员工参与到精益生产改进中来。
通过员工的参与和创意,我们发现了许多潜在的改进点,并得到了很好的实施效果。
另外,我们还加强了对供应链的管理。
我们与供应商建立了紧密的合作关系,
共同优化了供应链,实现了原材料的及时供应和库存的有效控制,为生产提供了有力的保障。
最后,我们注重了对质量的管理。
通过精益生产工具,我们发现了许多潜在的
质量问题,并采取了有效的改进措施,大幅提高了产品的质量,降低了产品的次品率。
总的来说,我们工厂在精益生产方面取得了显著的成绩,但也面临着一些挑战。
未来,我们将继续努力,进一步优化生产流程,提高员工的技能和素质,加强与供应商的合作,提高产品质量,实现工厂的可持续发展。
相信在全体员工的共同努力下,我们的工厂一定能够取得更加辉煌的成绩。
精益项目报告模板
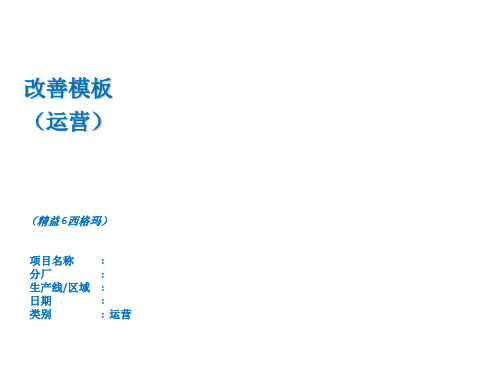
运营单元 / 工位
问题
措施
指标/(单位) 改善前
结果
改善后
% 提高
客户
节约
持续保持的 方法
硬节约(金 额/每月)
软节约(金 额/每月)
照片-改善前
照片-改善后
标题:
子标题4:XXXX (该改善项目包含的独立子改善项目)
运营单元 / 工位
问题
措施
指标/(单位) 改善前
结果
改善后
% 提高
客户
节约
持续保持的 方法
设备平衡图 – 改善后
设备平衡图 – 改善前:
布局图 – 改善后
布局图 – 改善后:
标题:
子标题1:XXXX (该改善项目包含的独立子改善项目)
运营单元 / 工位
问题
措施
指标/(单位) 改善前
结果
改善后
% 提高
客户
节约
持续保持的 方法
硬节约(金 额/每月)
目标列表
项目标题: 线︱区域︱模块:
关键品质特 测量单位 性/目标
开始
目标
日期: 日期: (1天) (2天) (3天) (4天) (5天) % 提高百 状态
(1周) (2周)
分比
0-70% 71%-90% 91%-100% Above 100%
过程与信息流
跨职能部门业务流程图:
价值流图 – 现状
备注 :团队成员签名
改善项目总结 : XXXX
财务绩效指标
结果
主要目标
关键品质 开始 特性
目标
总财务收益
最近的绩效表 硬节约(金
现
额/月)
软节约 (金 额/月)
总计节约(金 额/月)
精益项目报告

精益项目报告项目概况:本项目旨在将公司生产流程转化为精益生产方式,减少浪费并提高工作效率。
该项目启动于2020年2月,预计在同年5月完成。
项目目标:通过引入精益生产方式,实现以下目标:1.减少生产过程中的浪费;2.提高生产效率;3.降低生产成本;4.提高客户满意度。
项目计划:1.项目启动(2月):确定团队成员,搭建项目管理平台,制定项目详细计划。
2.梳理生产流程(2月):对现有生产流程进行梳理,分析存在的问题,并确定改善措施。
3.制定改善方案(3月):根据前期分析结果,制定相应的改善方案,并进行实际操作,调整和优化。
4.生产流程优化(3月-4月):基于改善方案,对生产流程进行优化,逐步实现精益生产。
5.项目总结(5月):总结项目成果,撰写精益生产实施方法手册,确保后续生产保持精益。
项目进展:截至目前,项目团队已经完成了文档的准备,制定了详细的工作计划和时间表。
梳理了生产流程,并制定了可行的改善方案。
现正处于生产流程优化阶段,已经取得了显著的效果。
项目目前处于进度符合预期的状态。
项目成果:1.将现有生产流程转化为精益生产方式;2.减少生产流程中的浪费,提高工作效率,降低了生产成本;3.提高了客户满意度,并让公司在竞争中处于优势。
总结:本项目是公司实施精益生产的一次大胆尝试。
在项目的执行过程中,我们经历了诸多困难与挑战。
但团队始终坚守目标,并通过沟通、协作,不断调整和优化,最终实现了预期目标。
精益生产是一种全新的生产方式,带来了前所未有的效果和改变。
我们相信,这种方式将会带领公司走向更加美好的未来。
精益生产改善项目阶段报告
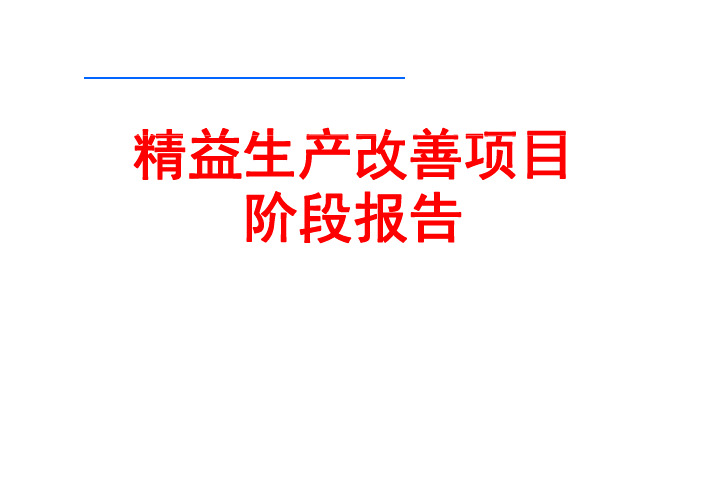
改善内容:
从控制柜引出一启动按钮至生产工位, 使职工不用走动就可以随时停止和启动 传输线。
3、改善实施-上料管路自动控制的改善
2、前后生产线需要周转、库存 折波和PU工序都是典型的孤岛作业,存在大量的在制品;
3、半成品离生产线远: 滤纸需要从滤纸库转运到生产工位,骨架从空一网子工段转运到工位;
4、手工校型,费时 手工操作,不能保证一致性,需要两头内外校型,时间长;
5、工位安排不合理 拍波生产线远离PU生产线;
3、改善实施-生产布局的原始状态分析
3、改善实施-修边半自动化的改善
改善前
改善后
改善前问题点描述:
改善后内容:
KLQ466滤芯,上边有一个长方形孔,职工 用剪刀修边,修一件内孔大概需要20s,每班 生产700件,手工修边劳动强度大,手工修 边过程中,容易扎伤手指,存在安全隐患;
根据PU胶的硬度,多次调整冲裁间隙,制作 冲裁模,将滤芯孔放入冲裁模中,将边沿一 次冲裁,需要时间5s,班产量增加为800余 件。
,现在为19s缩短了15s; 2、修边效率提升为30%;
; 2.效率提升收益:46000元
高班产量15%。
3、人员减少1人;
;
总计年收益:76000元;
1、可动率由76.19%提升到
1.北线“一个流”布局,可动 86.9%,效率提升14.10%; 1、人员减少效益:30000
2
率由原来的76.19%提升到 85%,效率提升11.56%;
1、现状把握-人员分析
需要5人同时工作,工序繁琐还需要一条折波线 的折波供应。
1、现状把握-产量分析
KLQ-466装配生产线
日期 作业人数 班产量 人均班产量
2014.5
精益制造工作总结报告格式
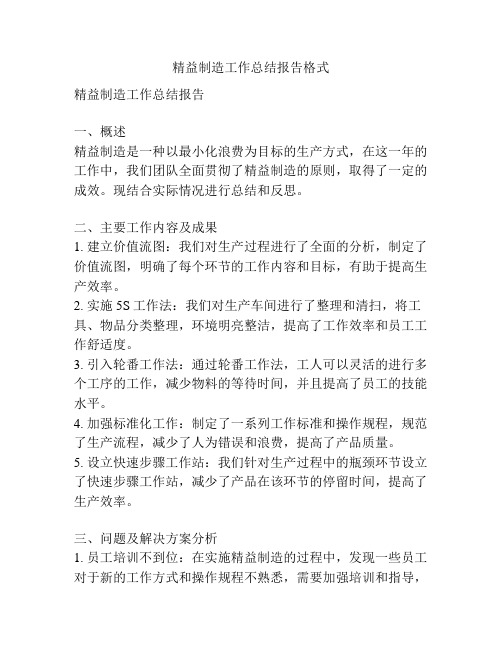
精益制造工作总结报告格式精益制造工作总结报告一、概述精益制造是一种以最小化浪费为目标的生产方式,在这一年的工作中,我们团队全面贯彻了精益制造的原则,取得了一定的成效。
现结合实际情况进行总结和反思。
二、主要工作内容及成果1. 建立价值流图:我们对生产过程进行了全面的分析,制定了价值流图,明确了每个环节的工作内容和目标,有助于提高生产效率。
2. 实施5S工作法:我们对生产车间进行了整理和清扫,将工具、物品分类整理,环境明亮整洁,提高了工作效率和员工工作舒适度。
3. 引入轮番工作法:通过轮番工作法,工人可以灵活的进行多个工序的工作,减少物料的等待时间,并且提高了员工的技能水平。
4. 加强标准化工作:制定了一系列工作标准和操作规程,规范了生产流程,减少了人为错误和浪费,提高了产品质量。
5. 设立快速步骤工作站:我们针对生产过程中的瓶颈环节设立了快速步骤工作站,减少了产品在该环节的停留时间,提高了生产效率。
三、问题及解决方案分析1. 员工培训不到位:在实施精益制造的过程中,发现一些员工对于新的工作方式和操作规程不熟悉,需要加强培训和指导,提高员工素质和技能。
解决方案:加强对员工的培训,定期组织技能培训班和经验分享会,提高员工对精益制造的理解和掌握程度。
2. 形式主义和程序化:一些员工对标准化工作和流程过于依赖,缺乏创新意识,对标准化工作只是形式化执行,没有真正理解其背后的目的。
解决方案:加强对员工的培训,强调标准化工作的目的和意义,鼓励员工主动思考和参与流程改进,培养员工的创新精神。
3. 浪费和不良品率未能显著下降:尽管我们采取了一系列的措施来减少浪费和不良品率,但仍未能取得预期的效果。
解决方案:进一步深入分析生产过程中存在的问题,针对性地采取措施,加强质量管理,提高工艺技术水平,优化生产流程,减少浪费和不良品率。
四、工作体会和启示在精益制造的工作过程中,我们深刻认识到精益制造是一个系统工程,需要全员参与,不仅仅是工人,还包括管理层和技术人员。
年度精益生产总结报告范文

一、前言随着我国经济社会的快速发展,企业对提高生产效率和降低成本的要求日益迫切。
本年度,我公司在总公司的指导下,全面推进精益生产,通过优化生产流程、提高员工素质、强化设备管理等方面,取得了显著成效。
现将本年度精益生产工作总结如下:一、精益生产工作回顾1. 组织架构优化为推动精益生产工作的深入开展,我公司成立了精益生产领导小组,明确了各部门职责,确保精益生产工作的顺利推进。
同时,成立了精益生产办公室,负责统筹协调、监督考核等工作。
2. 生产流程优化通过对生产流程的梳理和分析,我们发现存在以下问题:生产节拍不均衡、生产现场物料堆放混乱、生产设备故障率高、员工操作不规范等。
针对这些问题,我们采取了以下措施:(1)优化生产节拍,确保生产均衡;(2)规范生产现场物料堆放,提高空间利用率;(3)加强设备维护保养,降低设备故障率;(4)开展员工培训,提高员工操作技能。
3. 质量管理提升为提高产品质量,我公司从以下几个方面入手:(1)加强质量意识教育,提高员工质量意识;(2)完善质量管理体系,严格执行质量标准;(3)开展质量攻关活动,解决生产过程中存在的质量问题。
4. 成本控制在成本控制方面,我公司采取了以下措施:(1)优化生产计划,降低生产成本;(2)加强物料采购管理,降低采购成本;(3)加强能源管理,降低能源消耗。
二、精益生产工作成效1. 生产效率提升通过精益生产工作的推进,我公司生产效率得到显著提高。
本年度,生产任务完成率达到了95%,较去年同期提高了5个百分点。
2. 产品质量稳定本年度,我公司产品质量合格率达到98%,较去年同期提高了3个百分点。
3. 成本降低通过精益生产工作的开展,我公司生产成本较去年同期降低了5%。
4. 员工素质提高通过培训和学习,员工操作技能和综合素质得到明显提升。
三、存在问题及改进措施1. 问题:部分员工对精益生产理念认识不足,执行力不强。
改进措施:加强精益生产理念的宣传和培训,提高员工对精益生产的认识。
某电子厂精益生产项目总结报告
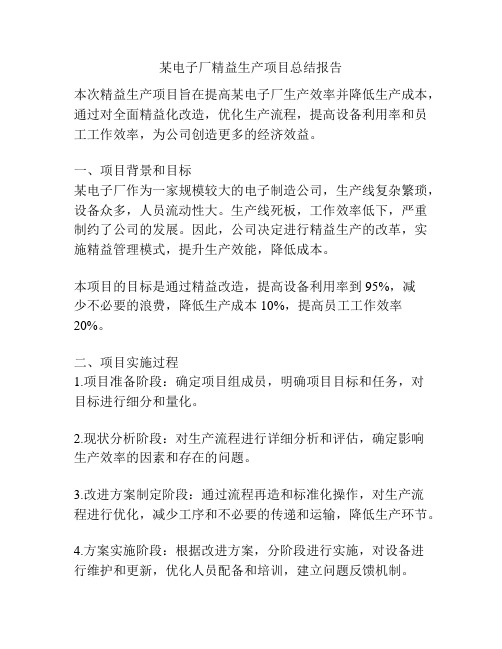
某电子厂精益生产项目总结报告本次精益生产项目旨在提高某电子厂生产效率并降低生产成本,通过对全面精益化改造,优化生产流程,提高设备利用率和员工工作效率,为公司创造更多的经济效益。
一、项目背景和目标某电子厂作为一家规模较大的电子制造公司,生产线复杂繁琐,设备众多,人员流动性大。
生产线死板,工作效率低下,严重制约了公司的发展。
因此,公司决定进行精益生产的改革,实施精益管理模式,提升生产效能,降低成本。
本项目的目标是通过精益改造,提高设备利用率到95%,减少不必要的浪费,降低生产成本10%,提高员工工作效率20%。
二、项目实施过程1.项目准备阶段:确定项目组成员,明确项目目标和任务,对目标进行细分和量化。
2.现状分析阶段:对生产流程进行详细分析和评估,确定影响生产效率的因素和存在的问题。
3.改进方案制定阶段:通过流程再造和标准化操作,对生产流程进行优化,减少工序和不必要的传递和运输,降低生产环节。
4.方案实施阶段:根据改进方案,分阶段进行实施,对设备进行维护和更新,优化人员配备和培训,建立问题反馈机制。
5.效果评估阶段:通过数据分析和实际观察,对改进方案效果进行评估,查找问题和进一步改进的空间。
三、项目成果和效益经过数月的改造和实施,本项目取得了以下成果和效益:1.设备利用率提高:通过设备的优化和维护,设备利用率提高到95%,减少了设备闲置时间和故障率。
2.减少浪费:通过流程再造和标准化操作,减少了不必要的工序和材料传递,降低了废品率和二次加工率。
3.降低生产成本:精细管理和减少浪费带来的效益,降低了生产成本10%。
4.提高员工工作效率:对员工进行培训和调整,合理规划工作流程,提高了员工工作效率20%。
通过以上措施,本项目取得了预期的效果,为公司提供了更多的经济效益。
同时,项目也暴露了一些问题,例如人员培训和设备更新需要持续跟进。
因此,建议公司在项目结束后,建立长期的监控机制,不断优化改进,为公司的发展提供更好的支持。
- 1、下载文档前请自行甄别文档内容的完整性,平台不提供额外的编辑、内容补充、找答案等附加服务。
- 2、"仅部分预览"的文档,不可在线预览部分如存在完整性等问题,可反馈申请退款(可完整预览的文档不适用该条件!)。
- 3、如文档侵犯您的权益,请联系客服反馈,我们会尽快为您处理(人工客服工作时间:9:00-18:30)。
二、铸二车间设备问题 ◆ 5#线电炉冷却水问题 线电炉冷却水问题 由于水质太差, ★由于水质太差,导致炉体外循环内铜管外皮水垢太 阻碍炉体内循环冷却,使水温过高超标: 多,阻碍炉体内循环冷却,使水温过高超标 (1)形成安全隐患,大修安全隐患小,小修安全隐患大 形成安全隐患, 形成安全隐患 大修安全隐患小, 由于炉体水温太高,有时会导致水管破裂, ,由于炉体水温太高,有时会导致水管破裂,对维修工 人施工时造成很大的伤害,增加工伤费用; 人施工时造成很大的伤害,增加工伤费用; (2)影响生产效率,现在平均每周小修 次,一次大 影响生产效率, 影响生产效率 现在平均每周小修3-4次 约需要一个半小时,大约影响产量70-90件左右,一个月 件左右, 约需要一个半小时,大约影响产量 件左右 大约1120-1440件;使维修费用过高,平均 个月维修一次 大约 件 使维修费用过高,平均2个月维修一次 费用7000多; 费用 多 (3)如果继续使用此水,再坚持 个月可能会导致整个 如果继续使用此水, 如果继续使用此水 再坚持2-3个月可能会导致整个 电炉系统瘫痪,整个炉体外循环内部铜管报废, 电炉系统瘫痪,整个炉体外循环内部铜管报废,其费用 铜管)大约18万左右,(两个炉体感应圈 大约32万 万左右,(两个炉体感应圈) (铜管)大约 万左右,(两个炉体感应圈)大约 万 左右,(磁鄂)大约4500/个,两个炉体 个,总共 万, ,(磁鄂 左右,(磁鄂)大约 个 两个炉体20个 总共9万 其费用累计59万左右 万左右。 其费用累计 万左右。 水质如果解决每年大约节省维修费用15万左右 ★水质如果解决每年大约节省维修费用 万左右
二、பைடு நூலகம்二车间设备问题解决措施
◆解决水质问题 已联系工业软化水厂家, 已联系工业软化水厂家,现订购一台每小时软化水 500L的处理设备试点。费用大约 的处理设备试点。 的处理设备试点 费用大约2000多。 多
二、铸二车间品质改善项目
项目实施记录(设备(工装)改善、 项目实施记录(设备(工装)改善、作业 标准及培训指导书) 标准及培训指导书)
三、铸二车间设备改善项目
铸二车间设备精益项目改善方案及进度一 览表
三、铸二车间设备改善项目
铸二车间项目改善对比
5月份检修改善图片 月份检修改善图片
7月份检修改善图片 月份检修改善图片
一、加工一车间改善后突显问题解决措施
◆固定品种,防止短时间内就换线,造成时间浪费 固定品种,防止短时间内就换线, ◆增加一台(群钻)钻床 增加一台(群钻) ◆增加风扇,解决天气热的问题 增加风扇,
◆修善厂房顶棚,解决漏雨问题 修善厂房顶棚,
二、铸二车间品质改善项目
铸二车间品质精益项目改善方案及进度一 览表
一、加工一车间改善后突显问题原因分析
◆产品换线品种多 钻的群钻, ◆其中两个品种法兰盘加工需18钻的群钻,群钻受限, 其中两个品种法兰盘加工需 钻的群钻 群钻受限, 其钻孔需用摇臂钻来加工,加工时间太长,效率低, 其钻孔需用摇臂钻来加工,加工时间太长,效率低, 在制品积压 ◆天气太热 ◆顶棚漏雨,尤其南区漏雨严重,导致下雨天停产影响效率 顶棚漏雨,尤其南区漏雨严重, ◆产品工艺的缺陷,使法兰盘区域毛刺太大,使加工负担过 产品工艺的缺陷,使法兰盘区域毛刺太大, 大,影响效率
浩信机械有限公司二分厂精益生产
项目报告
浩信精益办 201 27日 2010年7月27日
2002-1-18
浩信二厂精益生产 总体推进计划
一、机加一车间项目改善方案
机加一车间项目改善方案及进度一览表
一、机加一车间
机加一车间布局改善前后一览表
一、加工一车间改善后突显问题
★生产效率没达到预期的目标值 目标值: 改善后现状( 天):6.587 目标值:7.722 改善后现状(16天): 1-6月份现状:6.616 月份现状: 月份现状 ★产品流线距离的缩短,在制品增多,导致员工 产品流线距离的缩短,在制品增多, 工作区域缩小,影响员工的工作积极性; 工作区域缩小,影响员工的工作积极性;使不 安全系数加大。