粉末冶金原理(第二版) 第1部分 粉末成形
粉末冶金原理概述
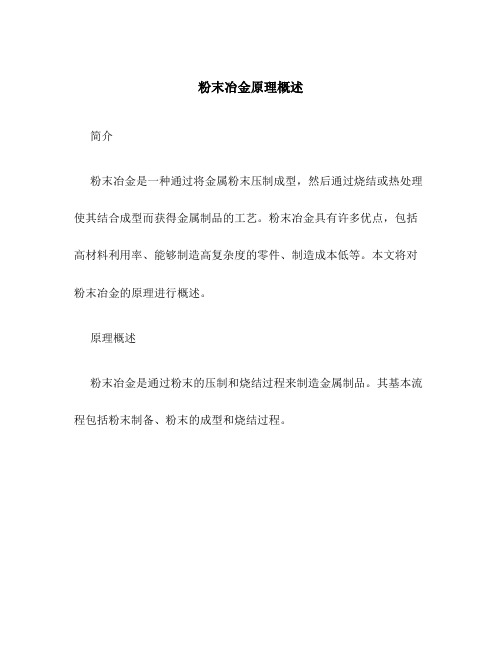
粉末冶金原理概述简介粉末冶金是一种通过将金属粉末压制成型,然后通过烧结或热处理使其结合成型而获得金属制品的工艺。
粉末冶金具有许多优点,包括高材料利用率、能够制造高复杂度的零件、制造成本低等。
本文将对粉末冶金的原理进行概述。
原理概述粉末冶金是通过粉末的压制和烧结过程来制造金属制品。
其基本流程包括粉末制备、粉末的成型和烧结过程。
粉末制备粉末制备是粉末冶金的第一步。
金属粉末可以通过多种方法来制备,包括机械研磨、凝固法、气相法等。
选择合适的粉末制备方法可以控制粉末的粒度、形状和组成,以适应所需的材料特性和制品要求。
粉末成型粉末成型是将金属粉末转化为所需形状的过程。
常见的成型方法包括压制、注塑、挤压等。
其中,压制是最常用的成型方法之一。
通过将金属粉末放入模具中,然后施加高压使其成型。
成型过程中,通过给予粉末适当的压力和温度,使粉末颗粒之间发生塑性变形和结合。
烧结过程烧结是粉末冶金的关键步骤之一。
在烧结过程中,经过成型后的粉末通过加热使其进行结合。
在加热的同时,粉末颗粒之间发生扩散,并形成跨粒界结合。
烧结温度和时间的选择对最终材料的性能和结构有重要影响。
后续热处理在烧结后,通常还需要对金属制品进行后续的热处理。
热处理可以有选择地改变材料的性能和结构,如提高强度、改善耐腐蚀性等。
常见的热处理方法包括固溶处理、时效处理、淬火等。
粉末冶金的优点粉末冶金具有以下优点:1.高材料利用率:由于粉末冶金可以直接利用金属粉末进行成型,因此避免了传统加工中的材料浪费,相比传统冶金方法,粉末冶金材料利用率更高。
2.制造高复杂度零件:粉末冶金可以制造复杂度高的零件,如多孔件、中空件等。
这是传统加工方法无法实现的。
3.制造成本低:粉末冶金不需要进行复杂的加工步骤,相比传统加工方法,制造成本更低。
4.可以利用废料:粉末冶金可以利用废料或回收材料进行制造,提高了资源的利用率。
应用领域粉末冶金广泛应用于各个领域,包括汽车制造、航空航天、船舶制造、化工、电子等。
粉末冶金原理简介课件
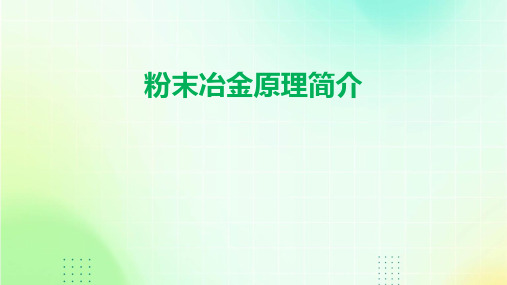
化学共沉淀法
总结词
通过化学反应使金属离子共沉淀形成均匀的金属氧化物或硫化物粉末。
详细描述
化学共沉淀法是一种制备金属粉末的方法,通过化学反应使金属离子共沉淀形成 均匀的金属氧化物或硫化物粉末。在沉淀过程中,控制溶液的pH值和浓度等条 件,使不同金属离子同时沉淀,形成成分均匀的混合物粉末。
喷雾干燥法
定义
粉末烧结是一种通过加热使粉末颗粒 间发生粘结,从而将它们转化为致由烧结和压制烧结。
烧结原理与过程
原理
烧结过程中,粉末颗粒通过表面扩散、粘性流动和塑性变形等机制相互粘结, 形成连续的固体结构。
过程
烧结过程通常包括加热、保温和冷却三个阶段,其中保温阶段是粉末颗粒粘结 的主要阶段。
能源领域
粉末冶金多孔材料可用于制造 燃料电池电极、核反应堆控制 棒等能源相关领域。
医疗器械
粉末冶金材料具有生物相容性 和耐腐蚀性,适用于医疗器械 制造,如人工关节、牙科植入
物等。
粉末冶金的发展历程
01
02
03
早期发展
粉末冶金起源于古代金属 加工技术,如青铜器时代 的铜合金制造。
20世纪发展
随着科技的发展,粉末冶 金在20世纪得到了广泛研 究和应用,涉及领域不断 扩大。
05
粉末冶金材料性能
力学性能
高强度和硬度
粉末冶金材料通过细晶强 化等手段,表现出较高的 硬度和强度,能够满足各 种复杂工况的需求。
良好的耐磨性
由于粉末冶金材料的晶粒 细小且均匀,其耐磨性优 于传统铸造和锻造材料。
抗疲劳性能
由于材料的内部结构均匀 ,可以有效抵抗疲劳裂纹 的扩展,提高零件的寿命 。
特点
粉末冶金具有能够制备传统熔炼 方法难以制备的合金、材料纯度 高、材料性能可调范围广、节能 环保等优点。
高等粉末冶金原理课件:粉末模压成形原理(合肥工业大学研究生课件)

本讲内容§3.1 粉末模压成形原理§3.2 成形技术-1§3.3 成形技术-2程继贵材料科学与工程学院本讲内容-成形技术部分一、成形前的粉末冶金二、模压成形技术三、等静压成形四、粉末连续成形五、浆料成形专题-粉末注射成形四、粉末连续成形定义:粉末在压力作用下由松散状态经过连续变化而成 为具有一定密度、强度以及所需尺寸形状压坯或 制品的过程。
主要包括:粉末轧制、挤压、喷射成形、楔形压制等基本特征:● 是模压成形方法的重要补充,可以生产 普通模压成形无法生产的多孔或致密的 板、带、棒、及管材等;● 比钢模压制需要较少的设备、容器。
(一)金属粉末轧制(Powder rolling)概述1.1. 概述粉末轧制的概念:粉末在一对轧棍之间在轧辊力的作用下压实成具有一定强度的连续带坯的过程。
粉末轧制的特点:● 与熔铸轧制相比:11)基本原理相同,要实现轧制:μ+ξ>α2)可轧制出熔铸轧制无法生产或难以生产的板、带材等(尤多层复合板、带)33)工艺流程短、节能、成本较低44)压坯或产品成分精确可控、轧制产品各向同性55)成材率较高● 与模压成形相比:1)轧制能耗比压制低22)可以生产模压成形无法生产的板、带材3)压坯密度更均匀,压坯长度原则上不限44)板带材宽度、厚度有限:δ=(1/100 ~1/300)D,一般≤10mm 粉末轧制适用于生产宽度几百mm,厚度10mm 以下,长度原则不限的板带材,或D/D/δδ很大的衬套等粉末轧制的分类:● 粉末直接轧制(direct powder rolling )应用较广泛:对塑性好的粉末 ● 粉末粘结轧制 (bonded powder rolling)加入粘结剂改善粉末体的成形性● 包套粉末热轧(canned powder hot rolling ) 对活性粉末以及要求高致密度的材料粉末冷轧粉末热轧按进料方式分为:水平、垂直和倾斜轧制轧制过程的定量关系(轧制带坯厚度、密度与粉末特性及轧辊尺寸之间的定量关系)基本概念及符号: 咬入层、咬入角α(α1) H α— 咬入宽度δR — 轧制带坯厚度D 、r r —— 轧辊直径、半径 ρ松、ρ压—粉末松装密度及轧坯密度V 进、V 轧— 粉末进料速度和轧制速度粉末料柱宽度 B ≈轧坯宽度 b H α图4-26 粉末轧制时的咬入区和变形区H αδ几何关系:质量关系:1cos 1cos 11−−=⎥⎦⎤⎢⎣⎡−+=z D D R R ηαδδαηρρ)()(松压进轧v v /=η松压ρρ/=z ——延伸系数————压紧系数 定量关系式:影响轧制过程的因素1)粉末性能● 松装密度: ρ松↑,ρ压↑,δ↑(保证轧制条件下)● 流动性: 流动性↑,V进↑,η↓, ρ压↑,δ↑(保证轧制条件下)● 粉末硬度:低的粉末硬度便于变形和形成高的机械啮 合,↑成形性,↑压坯强度2)轧辊直径↑D, ρ(δR固定);δR ↑(ρ一定)3)给料方式水平与垂直:垂直 V V进↑,ρ↑、δR↑4)轧制速度↑ω,ρ、δR↓(m不变)5)辊缝t↑t,轧制压力降低,ρ↓,δR↑粉末轧制工艺:粉末准备→ 喂料(水平、垂直方式)→轧制(冷轧、热轧) → 轧坯→烧结(直接烧结、成卷烧结)粉末冷轧工艺● 室温下轧制● 轧制速度较低:0.6-30m/s● 轧坯可卷成卷后烧结,也可烧结后卷成卷,还可烧结后再热轧冷轧冷轧+ 热轧粉末热轧工艺● 可以对粉末、预成形坯等进行轧制● 防氧化—包套(真空)轧制或气氛保护粉末轧制的应用�多孔板材,如过滤板、催化剂板材�层状复合材料带、板材�多层钢背支撑轴承�纤维增强复合材料粉末、粉末压坯或粉末烧结坯在外力作用下,通过挤压筒的挤压嘴挤成坯料或制品的成形方法(二)粉末挤压1. 概述●粉末挤压的定义Powder Extrusion挤● 挤压的分类�粉末直接挤压(冷挤压):适应于塑性好的金属粉末�粉末增塑挤压:粉末加入一定量的成形剂或粘结剂后挤压,适应于硬质粉末如硬质合金粉末�粉末包套热挤:适应于弥散强化合金等�烧结坯或粉末压坯的热挤压:适应于塑性较好的有色金属材料。
粉末技术-成形

22
4.2摩擦力 4.2.1摩擦力与压制压力的关系
摩擦力又叫摩擦压力损失。可用下式来表达: 4.2.2摩擦压力损失与压坯尺寸的关系
侧压力=压制压强X侧压系数X侧面积 摩擦力=侧压力X摩擦系数 压坯的侧压面积影响摩擦压力损失 ,即影响有效压制压力
曲面压坯的压制方法
33
6.3成形剂的用量及效果 成形剂的加入量与粉末种类、颗粒大小、压制压力以及
摩擦表面有关,并与成形剂本身的性质有关。一般说来,细 颗粒粉末所需的成形剂加入量比粗粒度粉末的量要多一些。 成形剂的加入随压坯形状因素的不同而不同。由图可知,成 形剂的加入量与形状因素成正比。
形状因素对成形剂加入量的影响
19
(2)川北公夫压制理论 日本的川北公夫研究了多种粉末(大部分是金属氧化物)在压制
过程中的行为。采用钢压模,粉末装入压模后在压机上逐步加压,然 后测定粉末体的体积变化,作出各种粉末的压力-体积曲线,并得出 有关经验公式:
(3)黄培云压制理论方程 黄培云对粉末压制成形提出一种新的压制理论公式: 比较上述各压制方程可以看出:在多数情况下,黄培云的双对数
电 解 铜 粉压坯的抗 弯强度与 成形压力的 关系
还 原 铁 粉 压坯的抗 弯强度与成 形压力的关系
18
2
3.1金属粉末压制时压坯密度的变化规律 粉末体在压模中受压后发生位移和
变形,随着压力的增加,压坯的相对 密度出现有规律的变化,通常将这种 变化规律假设为如图所示的三个阶段。
压坯密度与成形压力的关系
4.1侧压力 粉末体在压模内受压时,压坯会向周围膨胀,模壁就会
粉末冶金知识讲义
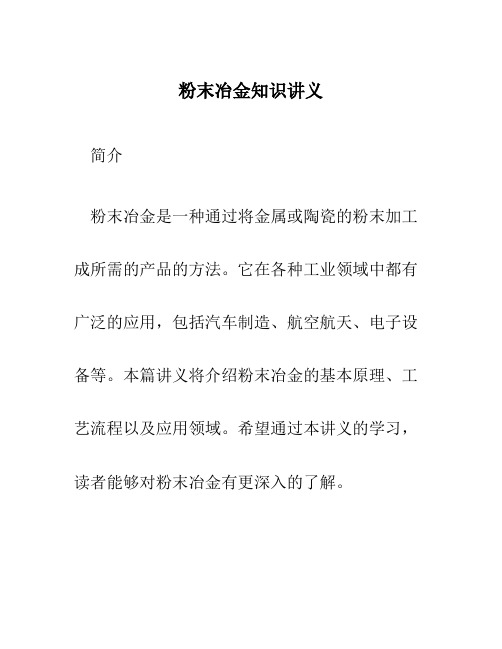
粉末冶金知识讲义简介粉末冶金是一种通过将金属或陶瓷的粉末加工成所需的产品的方法。
它在各种工业领域中都有广泛的应用,包括汽车制造、航空航天、电子设备等。
本篇讲义将介绍粉末冶金的基本原理、工艺流程以及应用领域。
希望通过本讲义的学习,读者能够对粉末冶金有更深入的了解。
粉末冶金的基本原理粉末冶金是利用金属或陶瓷的粉末制备材料的一种冶金方法。
它的基本原理是通过将粉末状的金属或陶瓷原料压制成形,在高温下进行烧结或热处理,使其形成致密的材料。
粉末冶金的主要原理包括:1.粉末制备:金属或陶瓷原料首先需要经过研磨和筛分等工艺步骤,制备成具有一定粒径和形状的粉末。
2.粉末成形:粉末通过压制工艺成形,常见的成形方法包括压制成型、注射成型和挤压成型等。
3.烧结或热处理:压制成形的粉末被置于高温下,经过烧结或热处理,使其形成致密的材料。
4.后续加工:经过烧结或热处理后的材料需要进行后续加工,例如机加工、表面处理等,以满足产品的具体要求。
粉末冶金的工艺流程粉末冶金的工艺流程包括粉末制备、成形、烧结或热处理以及后续加工等步骤。
具体工艺流程如下:粉末制备粉末制备是粉末冶金的第一步,它决定了最终材料的粒度和形状。
常见的粉末制备方法包括:•研磨:将金属块或陶瓷块通过研磨设备研磨成粉末状。
•气相沉积:通过将金属或陶瓷元素在高温下蒸发,然后在室温下与气体反应产生粉末。
•溶液法:通过将金属或陶瓷溶解在溶剂中,然后通过蒸发溶剂得到粉末。
成形成形是粉末冶金的第二步,它将粉末状的原料转化为所需的形状。
常见的成形方法包括:•压制成型:将粉末状原料放入模具中,通过压力将其固化成形。
•注射成型:将粉末与粘结剂混合后注射到模具中,通过固化将其成形。
•挤压成型:在高温下将粉末状原料通过挤压工艺转化为所需的形状。
烧结或热处理烧结或热处理是粉末冶金的关键步骤,它将成形后的粉末进行高温处理,使其结合成致密的材料。
常见的烧结或热处理方法包括:•烧结:将成形后的粉末置于高温下,使其颗粒之间发生结合,形成致密的材料。
粉末冶金的工艺流程-粉末成形

简介 粉末冶金生产中的基本工序之一,目的是将松散的粉末制成具有预定几何形
状、尺寸、密度和强度的半成品或成品。模压(钢模)成形是粉末冶金生产中采 用最广的成形方法。18世纪下半叶和19世纪上半叶,西班牙、俄国和英国为制造 铂制品,都曾采用了相似的粉末冶金工艺。当时俄国索博列夫斯基 (П.Г.Соболевсκий)使用 的是 钢模 和螺 旋压 机。 英 国的 沃拉 斯顿 (W.H.Wol laston )使 用 压 力 更 大 的 拉 杆 式 压 机 和 纯 度 更 高 的 铂 粉 ,制 得 了 几 乎 没 有 残余孔隙的致密铂材。后来,模压成形方法逐渐完善,并用来制造各种形状的铜 基 含 油 轴 承 等 产 品 。 20世 纪 30年 代 以 来 , 在 粉 末 冶 金 零 件 的 工 业 化 生 产 过 程 中 , 压 机 设 备 、模 具 设 计 等 方 面 不 断 改 进 , 模 压 成 形 方 法 得 到 了 更 大 的 发 展 ,机 械 化 和 自动化已达到较高的程度。为了扩大制品的尺寸和形状范围,特别是为了提高制 品密度和改善密度的均匀性相继出现和发展了多种成形方法。早期出现的有粉末 轧制、冷等静压制、挤压、热压等;50年代以来又出现了热等静压制、热挤压、 热锻等热成形方法。这些方法推动了全致密、高性能粉末金属材料的生产。 主要功能
料 为 金 属( 低 碳 钢 、不 锈 钢 、钛 ),还 可 用 玻 璃 和 陶 瓷 。由 于 温 度 和 等 静 压 力 的 同 时作用,可使许多种难以成形的材料达到或接近理论密度,并且晶粒细小,结构 均匀,各向同性和具有优异的性能。热等静压法最适宜于生产硬质合金、粉末高 温合金、粉末高速钢和金属铍等材料和制品;也可对熔铸制品进行二次处理,消 除气孔和微裂纹;还可用来制造不同材质紧密粘接的多层或复合材料与制品。 粉末锻造
粉末冶金原理(I)知识整理
粉末冶金原理(Ⅰ)第一章导论1粉末冶金技术的发展史History of powder metallurgy粉末冶金是采用金属粉末(或非金属粉末混合物)为原料,经成形和烧结操作制造金属材料、复合材料及其零部件的加工方法。
粉末冶金既是一项新型材料加工技术,又是一项古老的技术。
.早在五千年前就出现了粉末冶金技术雏形,古埃及人用此法制造铁器件;.1700年前,印度人采用类似方法制造了重达6.5T的“DELI柱”(含硅Fe合金,耐蚀性好)。
.19世纪初,由于化学实验用铂(如坩埚)的需要,俄罗斯人、英国人采用粉末压制、烧结和热锻的方法制造致密铂,成为现代粉末冶金技术的基础。
.20世纪初,现代粉末冶金的发展起因于爱迪生的长寿命白炽灯丝的需要。
钨灯丝的生产标志着粉末冶金技术的迅速发展。
.1923年硬质合金的出现导致机加工的革命。
.20世纪30年代铜基含油轴承的制造成功,并在汽车、纺织、航空、食品等工业部门的广泛应用。
随后,铁基粉末冶金零部件的生产,发挥了粉末冶金以低的制造成本生产高性能零部件的技术优点。
.20世纪40年代,二战期间,促使人们开发研制高级的新材料(高温材料),如金属陶瓷、弥散强化合金作为飞机发动机的关键零部件。
.战后,迫使人们开发研制更高性能的新材料,如粉末高速钢、粉末超合金、高强度铁基粉末冶金零部件(热锻)。
大大扩大了粉末冶金零部件及其材料的应用领域。
.粉末冶金在新材料的研制开发过程中发挥其独特的技术优势。
2粉末冶金工艺粉末冶金技术的大致工艺过程如下:原料粉末+添加剂(合金元素粉末、润滑剂、成形剂)↓成形(模压、CIP、粉浆浇注、轧制、挤压、温压、注射成形等)↓烧结(加压烧结、热压、HIP等)↓粉末冶金材料或粉末冶金零部件—后续处理Fig.1-1 Typical Processing flowchart for Powder Metallurgy Technique 3粉末冶金技术的特点.低的生产成本:能耗小,生产率高,材料利用率高,设备投资少。
粉末冶金原理(二) 教学大纲
粉末冶金原理(二)一、课程说明课程编号:070110Z20课程名称:粉末冶金原理(二)/Powder Metallurgy Principle(二)课程类别:专业教育课程学时/学分:40/2.5先修课程:物理化学,材料科学基础,金属热处理适用专业:粉体材料科学与工程教材、教学参考书:1黄培云主编.粉末冶金原理(第二版).北京:冶金工业出版社.2008年2 R M German. Powder Metallurgy Science (second edition).19983阮建明、黄培云主编. 粉末冶金原理.北京:机械工业出版社.2012年二、课程设置的目的意义《粉末冶金原理(二)》是为粉体材料科学与工程专业设置的最重要的专业核心课程。
通过本课程的学习,使学生掌握粉末冶金技术的过程原理与粉末冶金材料的制备方法。
通过粉末冶金原理课程的学习,使学生运用所学的有关基础理论、基本知识,培养分析与解决粉末冶金材料制备过程中的实际问题的能力。
为从事粉末冶金技术研究与粉末冶金新材料的制备与新材料研制、以及相关教学、制造的能力培养打下较深厚的专业基础。
三、课程的基本要求知识:掌握各种粉末成形方式的特点、粉末压制致密化机理粉末烧结概念及烧结种类的内涵及特征,烧结热力学及动力学与烧结图概念,液相烧结种类及其特征,液相烧结过程及致密化机理及显微结构演变规律,活化烧结与强化烧结概念。
学会从粉末冶金材料性能出发选择具体的粉末成形工艺与烧结方法,建立粉末冶金材料设计的基本思维方式,形成粉末冶金材料的微观结构与性能受控于粉末(材料类型与粉末性能)和粉末加工工艺(成形+烧结)基本知识结构。
能力:通过阐述粉末冶金过程原理和粉末冶金材料的制备方法,将这些过程原理与制备方法应用于解决粉末冶金材料制备的工程问题。
运用粉末压制致密化规律及烧结过程中粉末坯件显微结构的演化规律实现对粉末冶金材料的显微结构控制,形成研制粉末冶金新材料的创新能力。
粉末冶金原理中文(1)
的高性能硬质合金。 ➢ 3、用增强致密化过程来制造一般含有混合相组成的特殊
合金。 ➢ 4、制造非均匀材料、非晶态、微晶或者亚稳合金。 ➢ 5、加工独特的和非一般形态或成分的复合零部件。
粉末冶金原理中文(1)
一、粉末制备技术
球磨机中的研磨过程取决于众多因素: 筒内装料量、装球量、球磨筒尺寸、球磨机 转速、研磨时间、球体与被研磨物料的比例 (球料比)、研磨介质以及球体直径等。
粉末冶金原理中文(1)
一、粉末制备技术
例如:球磨筒转速n=0.7-0.75n临界时,球体发生抛 落; n=0.6n临界时,球体发生滚动; n<0.6n临界时,
粉末冶金原理中文(1)
依据物料粉碎的最终程度,又可以分为粗碎和 细碎两类。以压碎为主要作用的有碾压、锟轧以及 颚式破碎等;以击碎为主的有锤磨;属于击碎和磨 削等多方面作用的机械粉碎有球磨、棒磨等。
实践表明,机械研磨比较适用于脆性材料。利
用塑性金属或合金来制取粉末多采用涡旋研磨、冷
气流粉碎等方法。
粉末冶金原理中文(1)
2、将粉末压制成型为所需形状的坯块。成型的目的是制 得一定形状和尺寸的压坯,并使其具有一定的密度和强度。 成型的方法基本上分为加压成型和无压成型。加压成型中 应用最多的是模压成型,还有挤压成型、爆炸成型等。
粉末冶金原理中文(1)
绪论
3、坯块的烧结。烧结是粉末冶金工艺中的关键性工序。 成型后的压坯通过烧结使其得到所要求的最终物理力学性 能。烧结又分为单元系烧结和多元系烧结。对于单元系和 多元系的烧结,若烧结温度比所用的金属及合金的熔点低, 则称之为固相烧结;若烧结温度一般比其中难熔成分的熔 点低,而高于易熔成分的熔点,则称为液相烧结。除普通 烧结外,还有松装烧结、熔浸法、热压法烧结等特殊的烧 结工艺。
粉末冶金原理P2第一二章
粉末冶金原理P2第一二章
n 烧结颈部与附近区域(线度为ρ)空位浓度的空位 浓度梯度
n ▽Cv= CvoγΩ/(kTρ2) n 可以发现 n ↑γ(活化) n ↓ρ(细粉) n 均有利于提高浓度梯度
粉末冶金原理P2第一二章
3 蒸发-凝聚气相迁移动力—蒸汽压差 driving force for mass transportation by
n 细粉末与粒度组成与较高的压制压力
n 3)提高γ(活化)
粉末冶金原理P2第一二章
2 烧结扩散驱动力(driving force for atom
diffusion)空位浓度梯度
n 处于平衡状态时,平衡空位浓度 Cvo=exp(Sf/k).exp(-Efo/kT) n exp(Sf/k)—振动熵项,Sf为生成一个空位造成系
n 在烧结过程中存在液相的烧结过程 n 有液相出现的多元系烧结过程
粉末冶金原理P2第一二章
n 烧结操作的重要性
n 1 粉末冶金工艺两个基本加工步骤之一
n 磁粉芯,粘结磁性材料,W/Cu粉末药型罩例外
n 2 决定了P/M制品的性能 工艺决定结构 结构决定性能 n 3 烧结废品很难补救
n 如铁基部件的脱渗碳和严重的烧结变形,硬质合金烧结废品
曲面平直化趋势
烧结驱动力逐步减小
粉末冶金原理P2第一二章
n 2) 烧结中期
n 孔隙网络形成,烧结颈继续长大 n 有效烧结应力Ps为 n Ps =Pv-γ/ρ n Pv为烧结气氛的压力 n 若在真空中, Pv =0
粉末冶金原理P2第一二章
n 3) 烧结后期 n 孔隙网络坍塌,形成孤立孔隙 n 封闭的孔隙中的气氛压力随孔径收缩而增大 n 由气态方程Pv.Vp=nRT
- 1、下载文档前请自行甄别文档内容的完整性,平台不提供额外的编辑、内容补充、找答案等附加服务。
- 2、"仅部分预览"的文档,不可在线预览部分如存在完整性等问题,可反馈申请退款(可完整预览的文档不适用该条件!)。
- 3、如文档侵犯您的权益,请联系客服反馈,我们会尽快为您处理(人工客服工作时间:9:00-18:30)。
不锈钢注射成形件
• 2)便于制造难加工材料
• 陶瓷/金属复合材料---金属陶瓷cermet • 粉末超合金 powder superalloys • 粉末高速钢 powder high-speed steels • 金属基复合材料 metal matrix composites
• 弥散强化材料 dispersion-strengthened materials
• §1 压制前粉末料准备 • 1 还原退火 reducing and annealing • 作用 • 降低氧碳含量,提高纯度 • 消除加工硬化,改善粉末压制性能
• 粉末钝化 • 使细粉末适度变粗,或形成氧化薄膜,防止
粉末自燃 • 退火温度 • 高于回复-再结晶温度,(0.5-0.6)Tm • 退火气氛 • 还原性气氛(CO,H2),惰性气氛,真空
• 研究粉末冶金加工过程中的相关工程科学 (Engineering Science)问题
• 研究粉末成形与烧结过程中的工程科学问 题
3 粉末冶金技术的主要特点
粉末冶金既是冶金方法,也是零件制造技术
什么是粉末冶金? 利用金属粉末或化合物粉末为原料,经过 成形和烧结操作,制取金属材料及其复合 材料的加工方法
• 固体火箭发动机燃料 超细Al, Mg粉等
• 金刚石合成粉末触媒 Fe-Ni合金粉末
• 电子焊料(solder) 电子封装用Cu,Ag合金粉末
•
太阳能电池微细铝粉末
• 高性能电路保护器 PTC中超细金属Ni, Fe粉
• 焊料 细铁粉
• ……
• 绝大多数作为应用于工程结构中部件(结构件、 功能件或粉末(总铁大于71.5%,SiO2小于0.3%)→ 隧道窑高温还原(1050-1100℃ ) →破碎→ 磁选→精还原(750-800℃) →破碎 →磁选 →合批→铁粉→混合(添加合金元素) →压 制→烧结→(热处理)→P/M齿轮
• 传统工艺比粉末冶金工艺
• ①主要工序:前者15个以上,后者8个
• 1)机械零件
• 汽车(70%) • 工程机械 • 摩托车 • 家电 • 办公机械 • 电动工具等
• 2)机械加工 • 刀具 • 硬质合金,粉末高速钢,金属陶瓷等 • 加工电极 • W-Cu电火花加工电极 • 汽车薄板焊接用弥散强化铜电极
• 3)航天航空
• 火箭发动机喉衬及喷管 • 飞机发动机蜗轮叶片等 • 导弹鼻锥等 • 卫星导航陀螺等 • 制动材料
粉末冶金原理(第二版) 第1部分 粉 末成形
• 1 课程的任务和意义 • 粉末冶金材料加工的两个基本过程 • 金属粉末
• 小部分直接应用:功能性
• 隐形涂料 Fe,Ni及其合金纳米粉末 • 食品医药 超细铁粉
• 涂料 汽车用Al粉, 变压器用超细铜粉
• 自发热材料(取暖和野外食品自热) 超细Fe粉
• 1)经济性:低成本
• 将材料冶金与零件制造有机地结合在一起, 直接制造零部件
• 加工流程少,能耗低,材料利用率高
• 生产效率高
• 制造过程高度自动化
• 齿轮
• 1)传统工艺:铸锭冶金+机加工
• 铁精矿→ 高炉炼铁→铁水 →炼钢 →铸锭 →开坯(多道次) →热挤压(多道次) →钢锭 (棒料) → 下料→机加工(车外圆 → 平端 面→铣轴向孔 →滚齿) →(热处理)→齿轮
• 4)微电子
• 电子封装热沉材料
• 5) 军事工业 • 重合金,钼材料等 • 6) 通信技术 • 钨合金振子、钼铜封装材料 • 7 )运动器材 • 钨合金高尔夫球头
……..
第一部分 粉末成形
powder shaping or forming
• 具体部件具有一定的几何形状和尺寸 利用外力或粘结剂联结松散状态粉末体中的颗 粒,将粉末体转变成具有足够强度的几何体 的过程
• ②高温工序:前者8个以上,后者3个
Powder press • 全自动 • 液压机
Adaptor 模架
Sintering Furnace:网带烧结炉
轿车部件
电动工具与汽车部件
齿轮保持架(Ford)
汽车发动机用粉末烧结钢零件
汽车变速器系统用粉末烧结钢件
粉末锻造(Powder Forged)连杆
• 粉末颗粒间的结合力为机械啮合力或范德华 力
• 分类: • 刚性模(rigid die)压制 • 普通模压、温压与模压流动成形
非模压成形 冷、热等静压,注射成形,粉末挤压, 粉末轧制,粉浆浇注,无模成型,喷射成 形,爆炸成形等
第一章 粉末压制 Powder Pressing or Compaction
• 4)绿色环保 • 废弃物排放很低 • “洁净”冶金
• 粉末冶金技术的不足 • 1)加工的零件或材料尺寸有限 • 2)应用范围有限 • 固相烧结材料中的孔隙造成部件或材料的物理、
力学性能较低 低强度,低拉伸塑性 • 这些不足渐被粉末冶金新技术所克服 • 扩大粉末冶金部件或材料的应用范围
5 粉末冶金材料应用
• 微观结构可控材料
• 多孔材料,非晶态材料,超细结构材料等
钨合金 硬质合金 重合金 钨靶材 钨/钼基电工合金 纳米晶材料 nano-grained materials 梯度复合材料functionally gradient materials 等
• 3)尺寸一致性高 • 铁基P/M零件 • 钢模寿命:2万件左右 • 硬质合金模:5-6万件
• 粉末冶金制品
• 加工成块体材料或部件
• 需经过成形(shaping or forming)和烧结 (sintering)操作
• 成形和烧结控制着粉末冶金材料及其部件的微 观结构与性能
• 主宰着粉末冶金材料及其部件的应用
2 课程对象
• 材料设计的概念 • 工程应用(服役条件)→技术指标(性能
要求)→材料性能设计→微观结构设计 →材质类型、加工工艺设计(经济性) 研究粉末类型、加工工艺参数与材料微 观结构及部件几何性能间的关系
• 2 合批与混合 blending and mixing
• 混合 • 将不同成分的粉末混合均匀的过程 • 合批 • 同类粉末或粉末混合物的混合 • 消除因粉末在运输过程中产生的偏析或在 • 粉末生产过程中不同批号粉末之间的性能