等离子体氧化技术
低温等离子体技术处理vocs
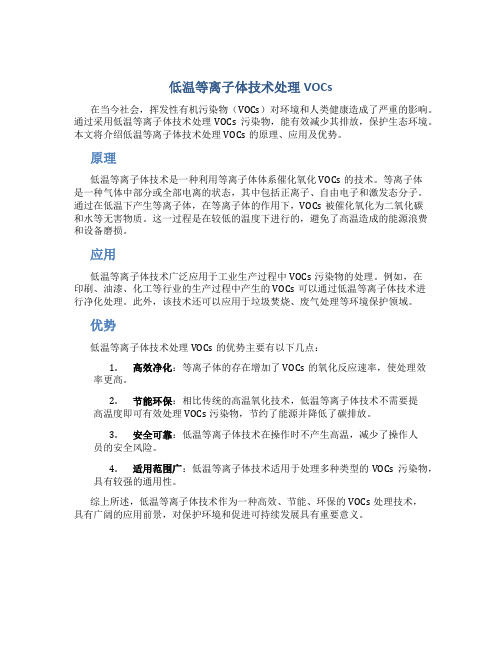
低温等离子体技术处理VOCs在当今社会,挥发性有机污染物(VOCs)对环境和人类健康造成了严重的影响。
通过采用低温等离子体技术处理VOCs污染物,能有效减少其排放,保护生态环境。
本文将介绍低温等离子体技术处理VOCs的原理、应用及优势。
原理低温等离子体技术是一种利用等离子体体系催化氧化VOCs的技术。
等离子体是一种气体中部分或全部电离的状态,其中包括正离子、自由电子和激发态分子。
通过在低温下产生等离子体,在等离子体的作用下,VOCs被催化氧化为二氧化碳和水等无害物质。
这一过程是在较低的温度下进行的,避免了高温造成的能源浪费和设备磨损。
应用低温等离子体技术广泛应用于工业生产过程中VOCs污染物的处理。
例如,在印刷、油漆、化工等行业的生产过程中产生的VOCs可以通过低温等离子体技术进行净化处理。
此外,该技术还可以应用于垃圾焚烧、废气处理等环境保护领域。
优势低温等离子体技术处理VOCs的优势主要有以下几点:1.高效净化:等离子体的存在增加了VOCs的氧化反应速率,使处理效率更高。
2.节能环保:相比传统的高温氧化技术,低温等离子体技术不需要提高温度即可有效处理VOCs污染物,节约了能源并降低了碳排放。
3.安全可靠:低温等离子体技术在操作时不产生高温,减少了操作人员的安全风险。
4.适用范围广:低温等离子体技术适用于处理多种类型的VOCs污染物,具有较强的通用性。
综上所述,低温等离子体技术作为一种高效、节能、环保的VOCs处理技术,具有广阔的应用前景,对保护环境和促进可持续发展具有重要意义。
微弧氧化,磨损率
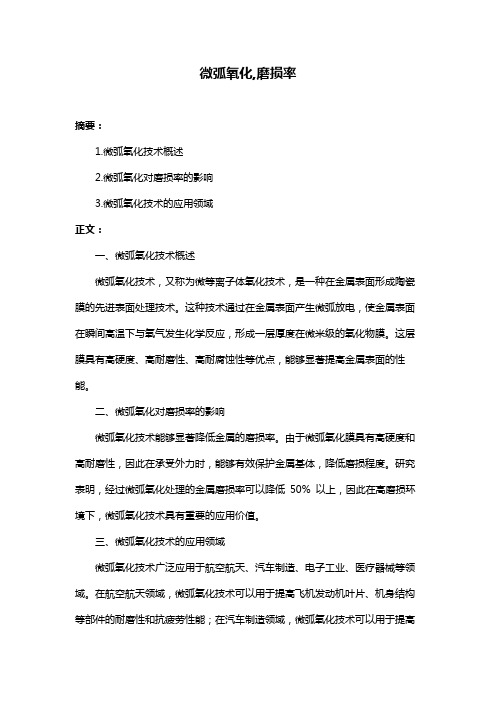
微弧氧化,磨损率
摘要:
1.微弧氧化技术概述
2.微弧氧化对磨损率的影响
3.微弧氧化技术的应用领域
正文:
一、微弧氧化技术概述
微弧氧化技术,又称为微等离子体氧化技术,是一种在金属表面形成陶瓷膜的先进表面处理技术。
这种技术通过在金属表面产生微弧放电,使金属表面在瞬间高温下与氧气发生化学反应,形成一层厚度在微米级的氧化物膜。
这层膜具有高硬度、高耐磨性、高耐腐蚀性等优点,能够显著提高金属表面的性能。
二、微弧氧化对磨损率的影响
微弧氧化技术能够显著降低金属的磨损率。
由于微弧氧化膜具有高硬度和高耐磨性,因此在承受外力时,能够有效保护金属基体,降低磨损程度。
研究表明,经过微弧氧化处理的金属磨损率可以降低50% 以上,因此在高磨损环境下,微弧氧化技术具有重要的应用价值。
三、微弧氧化技术的应用领域
微弧氧化技术广泛应用于航空航天、汽车制造、电子工业、医疗器械等领域。
在航空航天领域,微弧氧化技术可以用于提高飞机发动机叶片、机身结构等部件的耐磨性和抗疲劳性能;在汽车制造领域,微弧氧化技术可以用于提高
汽车发动机零件、齿轮等部件的耐磨性和抗磨损性能;在电子工业领域,微弧氧化技术可以用于提高电子元器件的耐磨性、抗腐蚀性和电绝缘性;在医疗器械领域,微弧氧化技术可以用于提高手术器械的耐磨性和抗腐蚀性,提高手术效果和安全性。
等离子体技术在科学研究中的应用与前景

等离子体技术在科学研究中的应用与前景等离子体是一种高温、高能量的物态。
它的能量密度非常高,能够产生强烈的光、电、磁等效应,因此在科学研究中有着广泛的应用前景。
下面,我们就来探究一下等离子体技术在科学研究中的应用与前景。
一、等离子体技术在材料科学中的应用1.等离子体表面处理技术等离子体表面处理技术被广泛应用于材料表面的改性和增强。
等离子体处理可以通过改变表面的化学和物理性质,使材料的表面具有更好的柔性、防腐蚀性、耐磨性、热稳定性等特性。
目前,等离子体表面处理技术已经应用于航空航天、汽车制造、电子、医疗器械等行业。
2.等离子体辅助材料合成技术等离子体辅助材料合成技术可以通过等离子体的化学反应和沉积过程,在材料表面或内部形成纳米颗粒、薄膜、涂层等新型材料。
这些材料具有独特的光、电、磁性能,对于新型电子器件和催化剂等方面有着很大的应用前景。
3.等离子体放电合成技术等离子体放电合成技术是在等离子体的作用下,在气体中合成具有特殊功能的纳米材料。
例如,利用等离子体放电技术可以制备出一系列的纳米颗粒,如氧化铁、氧化钼、氮化硅等,这些粒子主要用于高分子复合材料、显示器件、感应器、化学传感器等领域。
二、等离子体技术在能源领域中的应用1.等离子体温度计等离子体温度计是在等离子体的辐射发射光谱法基础上发展的。
它能够测量高温、高能量等离子体的温度。
这种技术可以应用于热核聚变等领域。
2.等离子体离子源等离子体离子源可以作为高能量离子束的加速器,应用于核物理、材料学等领域。
它可以生产出高能量的粒子束,用于材料表面的改性,或用于核物理实验。
这种技术在核聚变反应堆中也有着广阔的应用前景。
三、等离子体技术在生物医学中的应用1.等离子体治疗技术等离子体治疗技术是一种新型的医学治疗方法。
它利用等离子体的化学反应、放电等特性,对生物组织进行疗效处理。
这种技术可以应用于各种肿瘤、细胞排异等治疗中。
2.等离子体消毒技术等离子体消毒技术可以在不使用化学药品的情况下,快速有效地消毒。
等离子体氧化技术

缺点
• 1)膜层为蜂窝状的多孔结构,故膜层的耐 腐蚀性能比较低;
• 2)膜层中含有大量基体金属的氧化物和氢 氧化物,容易与酸性介质反应;
• 3)膜层厚度较小,虽然材料耐磨性好,但 总体来说其耐磨寿命较短;
• 4)高耗能,在高电压,大电流下进行,单 个工作的加工面积很难提高,降低了生产 效率。
应用
等离子体氧化实验装置
影 响 因 素
分类
优点
• 1)反应在溶液进行,只要是溶液可及地 方都能形成膜层;
• 2)电解液及反应过程都没有害物质; • 3)硬度高,耐磨性好; • 4)能够经受高低温的变化; • 5)绝缘性能优良; • 6)膜层光洁度好且易于着色,适用于装饰
涂层; • 7)成本低,操作简单,便于大规模生产。
• 腐蚀防护膜层:化学设备、建筑、泵部件 • 耐磨膜层:纺织机械、发动机部件、管道 • 电防护膜层:电子、化工设备、能源工业 • 装饰膜层:仪器仪表、土木工程 • 光学膜层:精密仪器 • 功能性膜层:催化、医疗设备、医用材料
展望
• 1)探索新的基材微弧氧化前处理工艺,以 提高膜层的结合力为目标;
• 2)探索新的电解液添加剂,以增强膜的自 身能力为目标;
• 3)研制体积更小,更加智能化的电源设备, 降低能耗;
• 4)探索新的膜层后处理工艺,使得微弧氧 化膜层能与其他防护方法相结合为性能更 加优良的复合膜层。
• 阳极氧化:表面生成一层很薄的绝缘氧化膜;
• 火花放电:当电压达到临界击穿电压时,氧化膜 被击穿,式样表面出现无数的白色火花;
• 微弧阶段:随着外加电压和膜厚的增加,表面出 现异动的较大红色弧电,同时存在大量细小的白 色火花;
• 熄弧阶段:红色弧电开始稀疏,在固定位置连续 放电,也称为弧放电阶段。
镁合金微弧氧化
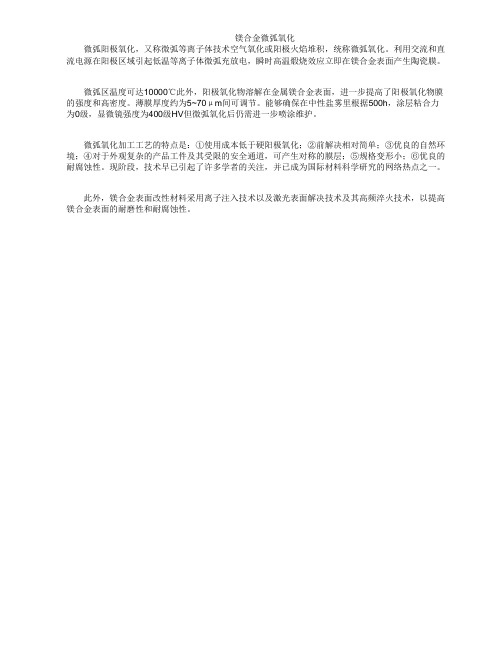
镁合金微弧氧化
微弧阳极氧化,又称微弧等离子体技术空气氧化或阳极火焰堆积,统称微弧氧化。
利用交流和直流电源在阳极区域引起低温等离子体微弧充放电,瞬时高温煅烧效应立即在镁合金表面产生陶瓷膜。
微弧区温度可达10000℃此外,阳极氧化物溶解在金属镁合金表面,进一步提高了阳极氧化物膜的强度和高密度。
薄膜厚度约为5~70μm间可调节。
能够确保在中性盐雾里根据500h,涂层粘合力为0级,显微镜强度为400级HV但微弧氧化后仍需进一步喷涂维护。
微弧氧化加工工艺的特点是:①使用成本低于硬阳极氧化;②前解决相对简单;③优良的自然环境;④对于外观复杂的产品工件及其受限的安全通道,可产生对称的膜层;⑤规格变形小;⑥优良的耐腐蚀性。
现阶段,技术早已引起了许多学者的关注,并已成为国际材料科学研究的网络热点之一。
此外,镁合金表面改性材料采用离子注入技术以及激光表面解决技术及其高频淬火技术,以提高镁合金表面的耐磨性和耐腐蚀性。
等离子灭菌原理
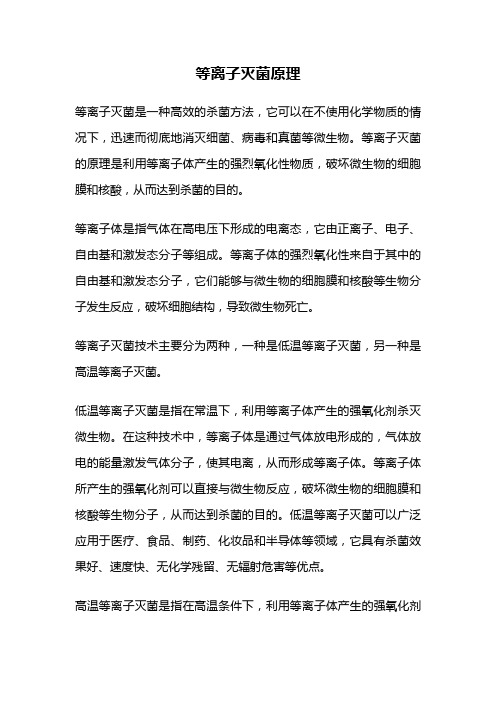
等离子灭菌原理等离子灭菌是一种高效的杀菌方法,它可以在不使用化学物质的情况下,迅速而彻底地消灭细菌、病毒和真菌等微生物。
等离子灭菌的原理是利用等离子体产生的强烈氧化性物质,破坏微生物的细胞膜和核酸,从而达到杀菌的目的。
等离子体是指气体在高电压下形成的电离态,它由正离子、电子、自由基和激发态分子等组成。
等离子体的强烈氧化性来自于其中的自由基和激发态分子,它们能够与微生物的细胞膜和核酸等生物分子发生反应,破坏细胞结构,导致微生物死亡。
等离子灭菌技术主要分为两种,一种是低温等离子灭菌,另一种是高温等离子灭菌。
低温等离子灭菌是指在常温下,利用等离子体产生的强氧化剂杀灭微生物。
在这种技术中,等离子体是通过气体放电形成的,气体放电的能量激发气体分子,使其电离,从而形成等离子体。
等离子体所产生的强氧化剂可以直接与微生物反应,破坏微生物的细胞膜和核酸等生物分子,从而达到杀菌的目的。
低温等离子灭菌可以广泛应用于医疗、食品、制药、化妆品和半导体等领域,它具有杀菌效果好、速度快、无化学残留、无辐射危害等优点。
高温等离子灭菌是指在高温条件下,利用等离子体产生的强氧化剂杀灭微生物。
在这种技术中,等离子体是通过高温气体放电形成的,高温气体放电的能量激发气体分子,使其电离,从而形成等离子体。
高温等离子灭菌可以杀灭大多数微生物,包括芽孢、病毒和真菌等,具有杀菌效果好、速度快、对微生物的抵抗性低等优点。
高温等离子灭菌主要应用于医疗、实验室、制药和食品加工等领域,是一种重要的杀菌技术。
等离子灭菌是一种高效、无污染、无化学残留的杀菌方法,它通过利用等离子体产生的强氧化剂杀灭微生物,具有杀菌效果好、速度快、对微生物的抵抗性低等优点,是一种重要的杀菌技术。
等离子电解氧化
等离子电解氧化等离子电解氧化是一种常见的表面处理技术,它可以改善金属材料的表面性能,提高其耐腐蚀性、耐磨性和耐热性等。
本文将介绍等离子电解氧化的原理、应用以及优缺点。
一、原理等离子电解氧化是利用电解液中的电解质与金属表面产生化学反应,形成一层氧化膜。
这个过程中,通过施加电压使金属表面产生氧化还原反应,金属阳极溶解,氧化膜形成。
等离子电解氧化的核心是利用等离子体产生的高能离子束,对金属表面进行处理,使得氧化膜的结构致密、均匀,提高其耐腐蚀性和机械性能。
二、应用1. 耐腐蚀性提升:等离子电解氧化可以形成一层致密的氧化膜,提高材料的耐腐蚀性。
这对于一些需要长期暴露在恶劣环境中的金属制品特别重要,如航空航天设备、汽车零部件等。
2. 表面硬化:等离子电解氧化可以显著提高金属材料的硬度,增加磨擦和磨损的抵抗力。
这对于一些需要经受强烈摩擦的零部件特别重要,如发动机活塞环、齿轮等。
3. 表面改良:等离子电解氧化可以改善金属表面的润滑性和耐磨性,减少摩擦损失。
这对于一些需要高速旋转或高频振动的设备特别重要,如风力发电机组件、轴承等。
4. 美观性提升:等离子电解氧化可以使金属表面呈现出丰富的颜色,提高其美观性。
这对于一些需要外观吸引力的产品特别重要,如珠宝、手表等。
三、优缺点1. 优点:(1)高效性:等离子电解氧化是一种快速的表面处理技术,可以在短时间内完成对金属材料的处理。
(2)环保性:等离子电解氧化的过程中不需要使用有毒有害的化学物质,对环境没有污染。
(3)适用性广泛:等离子电解氧化适用于多种金属材料,如铝、镁、钛等。
(4)成本低廉:与其他表面处理技术相比,等离子电解氧化的成本较低。
2. 缺点:(1)不适用于所有金属:等离子电解氧化只适用于具有一定导电性的金属材料,对于非金属材料无效。
(2)氧化膜易受损:氧化膜在使用过程中容易受到外界因素的影响,如机械磨损、腐蚀等,导致其耐腐蚀性能下降。
(3)工艺复杂:等离子电解氧化的工艺相对复杂,需要控制电解液的成分、温度、电解时间等参数,以获得理想的处理效果。
等离子体微弧氧化技术及其应用
Ab ta t P a m a m ir a c o ia in i a n w e h i u , ih c n i. iu f r t e sr c : ls co r xd to S e t c nq e wh c a n st o m h
c r m i c a i g n t u f c so o o ・ e r u e as Th e eo i g h s o ya d e a c o t s o kes r a e fs me n n f r o sm t l . e d v l p n i t r n n
(B p r me o a eil ce ea c n lg Qi a m tt t }Ch m ia c o o y 1e a t m fM t rasS inc ndTe h oo y. n ol qlue 0 e cl Te hn lg
Qi a h n o g-6 0 8 n 。S a d n 2 6 4 )
1 微弧 氧 化 技 术 概述
11 微弧氧化技术 . 等 离 子体 微 弧 氧化 简 称微 弧 氧化 ( MAO) 又
称 为 微 等 离 子 体 氧 化 ( O) 阳 极 火 花 沉 积 MP 、 ( D) AS 或火 花放 电 阳极氧 化 ( ANOF)还 有 人称 , 之 为 等离 子 俸 增 强 电化 学 表 面 陶 瓷化 (E C) PC , 它是 一种 直接在 有色 金属 表面原 位 生长陶 瓷层
t ers a c r g e so lr a co ia in,h a i p icpe a d p o u i gp o e so h e e r h p o r s f c o r xd t m o t eh sc rn i l n r d cn r c s f
等离子体微弧氧化常识及应用范围
等离子体微弧氧化常识及应用范围微等离子体氧化(Microplasma oxidation, MPO),又叫微弧氧化,是通过电解液与相应电参数的组合,在铝、镁、钛及其合金表面依靠弧光放电产生的瞬时高温高压作用,生长出以基体金属氧化物为主的陶瓷膜层。
在微弧氧化过程中,化学氧化、电化学氧化、等离子体氧化同时存在,因此陶瓷层的形成过程非常复杂,至今还没有一个合理的模型能全面描述陶瓷层的形成。
微弧氧化工艺将工作区域由普通阳极氧化的法拉第区域引入到高压放电区域,克服了硬质阳极氧化的缺陷,极大地提高了膜层的综合性能。
微弧氧化膜层与基体结合牢固,结构致密,韧性高,具有良好的耐磨、耐腐蚀、耐高温冲击和电绝缘等特性。
该技术具有操作简单和易于实现膜层功能调节的特点,而且工艺不复杂,不造成环境污染,是一项全新的绿色环保型材料表面处理技术,在航空航天、机械、电子、装饰等领域具有广阔的应用前景。
微弧氧化技术的原理及特点:微弧氧化或微等离子体表面陶瓷化技术,是指在普通阳极氧化的基础上,利用弧光放电增强并激活在阳极上发生的反应,从而在以铝、钛、镁金属及其合金为材料的工件表面形成优质的强化陶瓷膜的方法,是通过用专用的微弧氧化电源在工件上施加电压,使工件表面的金属与电解质溶液相互作用,在工件表面形成微弧放电,在高温、电场等因素的作用下,金属表面形成陶瓷膜,达到工件表面强化的目的。
微弧氧化技术的突出特点是:(1)大幅度地提高了材料的表面硬度,显微硬度在1000至2000HV,最高可达3000HV,可与硬质合金相媲美,大大超过热处理后的高碳钢、高合金钢和高速工具钢的硬度;(2)良好的耐磨损性能;(3)良好的耐热性及抗腐蚀性。
这从根本上克服了铝、镁、钛合金材料在应用中的缺点,因此该技术有广阔的应用前景;(4)有良好的绝缘性能,绝缘电阻可达100MΩ。
(5)基体原位生长陶瓷膜,结合牢固,陶瓷膜致密均匀。
微弧氧化工艺流程:去油 ‐‐‐‐ 水洗 ‐‐‐‐ 微弧氧化 ‐‐‐‐ 纯水洗 ‐‐‐‐ 封闭微弧氧化工作影响因素1.工件材质及表面状态(1)微弧氧化对铝材要求不高,不管是含铜或是含硅的难以阳极氧化铝合金,只要阀金属比例占到40%以上,均可用于微弧氧化,且能得到理想膜层。
等离子电解氧化
等离子电解氧化等离子电解氧化是一种常用的表面处理技术,它通过在材料表面产生等离子体,并在电场作用下进行氧化反应,从而改善材料的表面性能。
该技术广泛应用于金属、合金、陶瓷等材料的表面处理和涂层制备等领域,具有很高的实用性和经济性。
等离子电解氧化技术的原理是利用外加电场将电解质溶液中的阳离子与阴离子分开,形成等离子体。
等离子体中含有高能电子和离子,它们具有较高的活性,能够与材料表面发生反应,形成氧化膜。
通过控制电场强度和处理时间,可以调节氧化膜的厚度和性质,从而实现对材料表面性能的调控。
等离子电解氧化技术具有许多优点。
首先,它可以在常温下进行,不需要高温和高压条件,避免了材料因过高温度而发生相变或变形的问题。
其次,该技术对材料的侵蚀性较小,能够保持材料的整体性能。
再次,等离子电解氧化可以在较短的时间内完成,提高了生产效率。
此外,该技术对环境的影响较小,不会产生有害气体或废液,符合可持续发展的要求。
在金属和合金材料的表面处理中,等离子电解氧化可以增加材料的耐腐蚀性、耐磨损性和耐热性。
氧化膜形成后,可以有效阻止金属与外界介质的接触,减少了材料的腐蚀速率。
同时,等离子电解氧化还可以使材料表面形成一层致密的氧化膜,提高了材料的硬度和耐磨损性。
此外,氧化膜还可以提高材料的耐高温性能,使其能够在高温环境下稳定工作。
在陶瓷材料的表面处理中,等离子电解氧化可以增加材料的粘附性和美观性。
氧化膜形成后,可以提高陶瓷与涂层之间的粘附力,增强涂层的附着力。
同时,等离子电解氧化还可以改变陶瓷材料的表面形貌和颜色,使其具有更好的装饰效果。
除了在金属和陶瓷材料的表面处理中应用较为广泛外,等离子电解氧化技术还可以用于制备功能性涂层。
通过调节电解质溶液的组成和处理条件,可以在材料表面形成具有特殊功能的氧化膜,如超疏水、超疏油、抗菌等功能。
这些功能性涂层可以广泛应用于建筑、汽车、航空航天等领域,具有很大的应用潜力。
总的来说,等离子电解氧化是一种重要的表面处理技术,它能够改善材料的表面性能,提高其耐腐蚀性、耐磨损性和耐高温性能。
- 1、下载文档前请自行甄别文档内容的完整性,平台不提供额外的编辑、内容补充、找答案等附加服务。
- 2、"仅部分预览"的文档,不可在线预览部分如存在完整性等问题,可反馈申请退款(可完整预览的文档不适用该条件!)。
- 3、如文档侵犯您的权益,请联系客服反馈,我们会尽快为您处理(人工客服工作时间:9:00-18:30)。
应用
• • • • • • 腐蚀防护膜层:化学设备、建筑、泵部件 耐磨膜层:纺织机械、发动机部件、管道 电防护膜层:电子、化工设备、能源工业 装饰膜层:仪器仪表、土木工程 光学膜层:精密仪器 功能性膜层:催化、医疗设备、医用材料
展望
• 1)探索新的基材微弧氧化前处理工艺,以 提高膜层的结合力为目标; • 2)探索新的电解液添加剂,以增强膜的自 身能力为目标; • 3)研制体积更小,更加智能化的电源设备, 降低能耗; • 4)探索新的膜层后处理工艺,使得微弧氧 化膜层能与其他防护方法相结合为性能更 加优良的复合膜层。
缺点
• 1)膜层为蜂窝状的多孔结构,故膜层的耐 腐蚀性能比较低; • 2)膜层中含有大量基体金属的氧化物和氢 氧化物,容易与酸性介质反应; • 3)膜层厚度较小,虽然材料耐磨性好,但 总体来说其耐磨寿命较短; • 4)高耗能,在高电压,大电流下进行,单 个工作的加工面积很难提高,降低了生产 效率。
等离子体氧化实验装置
影 响 因 素
分类
优点
• 1)反应在溶液进行,只要是溶液可及的地 方都能形成膜层; • 2)电解液及反应过程都没有害物质; • 3)硬度高,耐磨性好; • 4)能够经受高低温的变化; • 5)绝缘性能优良; • 6)膜层光洁度好且易于着色,适用于装饰 涂层; • 7)成本低,操作简单,便于大规模生产。
基本工艺
• 将待处理的材料浸入特定的电解液中作电极, 另有一个金属电极作其对电极。在两极之间施 加电压,将作用区域由普通阳极氧化的法拉第 区域引入到高压放电区域,同时伴随有弧光产 生,此时电极在热化学、等离子体化学和电化 学过程的共同作用下生成陶瓷膜层。
• 阳极氧化:表面生成一层很薄的绝缘氧化膜; • 火花放电:当电压达到临界击穿电压时,氧化膜 被击穿,式样表面出现无数的白色火花; • 微弧阶段:随着外加电压和膜厚的增加,表面出 现异动的较大红色弧电,同时存在大量细小的白 色火花; • 熄弧阶段:红色弧电开始稀疏,在固定位置连续 放电,也称为弧放电阶段。
特点
• 可在轻金属(Al、Mg. Ti等)材料表面原位生 长出耐蚀、耐磨的氧化陶瓷膜。该技术处 理所得氧化膜与金属基体间的结合力强, 膜厚范围较宽且可控,形成的复合材料具 有高硬度、耐腐蚀、耐磨损、抗热震等优 异性能。
现状
• 目前,美、俄、日、德等国已将PEO应用 于尖端武器装备的制造中,解决了许多其 他方法无法解决的关键技术问题; PEO在国 内的纺织、航空等行业也有一些尝试性的 应用。因此,PEO已成为目前国际、国内 材料表面工程技术领域的研究热点之一。
等离子体氧化技术简介
林立 140620030
介绍
• 等离子体,是由部分电子被剥夺后的原子及原子 团被电离后产生的正负离子组成的离子化气体状 物质。
它广泛存在于宇宙中,常被 视为是除去固、液、气外, 物质存在的第四态。
等离子体氧化
• 等离子体电解氧化(Plasma Electrolytic Oxidation,PEO), 又称微弧放电氧化(Microarc Discharge Oxidation,MDO)、 微弧氧化(Microarc Oxidation,MAO) • 通过电解液与相应电参数的组合,在铝、 镁、钛及其合金表面依靠弧光放电产生的 瞬பைடு நூலகம்高温高压作用,生长出以基体金属氧 化物为主的陶瓷膜层。