表面缺陷定义
线缺陷和面缺陷
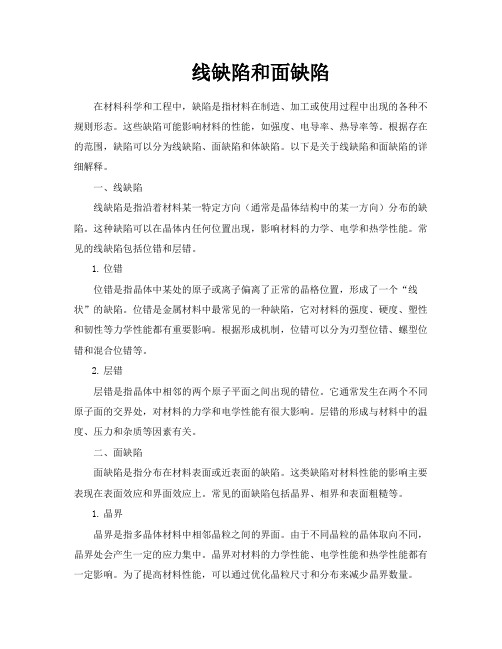
线缺陷和面缺陷在材料科学和工程中,缺陷是指材料在制造、加工或使用过程中出现的各种不规则形态。
这些缺陷可能影响材料的性能,如强度、电导率、热导率等。
根据存在的范围,缺陷可以分为线缺陷、面缺陷和体缺陷。
以下是关于线缺陷和面缺陷的详细解释。
一、线缺陷线缺陷是指沿着材料某一特定方向(通常是晶体结构中的某一方向)分布的缺陷。
这种缺陷可以在晶体内任何位置出现,影响材料的力学、电学和热学性能。
常见的线缺陷包括位错和层错。
1.位错位错是指晶体中某处的原子或离子偏离了正常的晶格位置,形成了一个“线状”的缺陷。
位错是金属材料中最常见的一种缺陷,它对材料的强度、硬度、塑性和韧性等力学性能都有重要影响。
根据形成机制,位错可以分为刃型位错、螺型位错和混合位错等。
2.层错层错是指晶体中相邻的两个原子平面之间出现的错位。
它通常发生在两个不同原子面的交界处,对材料的力学和电学性能有很大影响。
层错的形成与材料中的温度、压力和杂质等因素有关。
二、面缺陷面缺陷是指分布在材料表面或近表面的缺陷。
这类缺陷对材料性能的影响主要表现在表面效应和界面效应上。
常见的面缺陷包括晶界、相界和表面粗糙等。
1.晶界晶界是指多晶体材料中相邻晶粒之间的界面。
由于不同晶粒的晶体取向不同,晶界处会产生一定的应力集中。
晶界对材料的力学性能、电学性能和热学性能都有一定影响。
为了提高材料性能,可以通过优化晶粒尺寸和分布来减少晶界数量。
2.相界相界是指多相材料中不同相之间的界面。
相界处的原子结构和化学成分往往与主体材料不同,导致其性能具有各向异性。
相界对材料的力学性能、电学性能和热学性能都有重要影响。
优化相界结构可以提高材料的综合性能。
3.表面粗糙表面粗糙是指材料表面或近表面的微观不平整性。
它可能是由于加工过程中冷却速度不均匀、材料氧化等原因导致的。
表面粗糙会影响材料的表面能、润湿性、涂层附着力和摩擦学性能等。
通过表面处理技术(如抛光、喷砂等)可以改善表面粗糙度,提高材料的性能。
晶圆缺陷分类
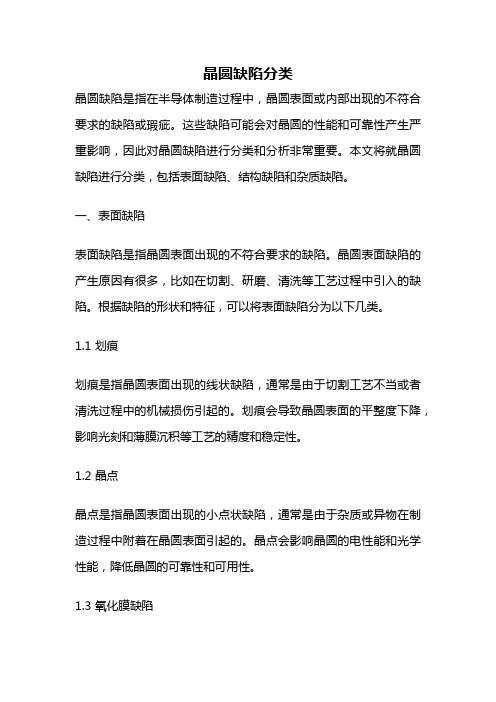
晶圆缺陷分类晶圆缺陷是指在半导体制造过程中,晶圆表面或内部出现的不符合要求的缺陷或瑕疵。
这些缺陷可能会对晶圆的性能和可靠性产生严重影响,因此对晶圆缺陷进行分类和分析非常重要。
本文将就晶圆缺陷进行分类,包括表面缺陷、结构缺陷和杂质缺陷。
一、表面缺陷表面缺陷是指晶圆表面出现的不符合要求的缺陷。
晶圆表面缺陷的产生原因有很多,比如在切割、研磨、清洗等工艺过程中引入的缺陷。
根据缺陷的形状和特征,可以将表面缺陷分为以下几类。
1.1 划痕划痕是指晶圆表面出现的线状缺陷,通常是由于切割工艺不当或者清洗过程中的机械损伤引起的。
划痕会导致晶圆表面的平整度下降,影响光刻和薄膜沉积等工艺的精度和稳定性。
1.2 晶点晶点是指晶圆表面出现的小点状缺陷,通常是由于杂质或异物在制造过程中附着在晶圆表面引起的。
晶点会影响晶圆的电性能和光学性能,降低晶圆的可靠性和可用性。
1.3 氧化膜缺陷氧化膜缺陷是指晶圆表面氧化膜上出现的不符合要求的缺陷,通常是由于氧化过程中控制不当或杂质引入导致的。
氧化膜缺陷会影响晶圆的绝缘性能和介电常数,从而影响器件的电性能和可靠性。
二、结构缺陷结构缺陷是指晶圆内部出现的不符合要求的缺陷。
结构缺陷的产生原因有很多,比如晶圆生长过程中的晶格缺陷、掺杂过程中的离子损伤等。
根据缺陷的形态和分布特点,可以将结构缺陷分为以下几类。
2.1 晶格缺陷晶格缺陷是指晶圆内部出现的晶格结构不完整或不规则的缺陷,通常是由于晶圆生长过程中的温度变化、应力差异或杂质引入等原因引起的。
晶格缺陷会影响晶圆的结构稳定性和电性能,降低晶圆的可靠性和可用性。
2.2 晶界缺陷晶界缺陷是指晶圆内部晶界处出现的不符合要求的缺陷,通常是由于晶粒生长过程中的晶粒交错、晶粒边界不整齐等原因引起的。
晶界缺陷会影响晶圆的晶格结构和电性能,降低晶圆的可靠性和可用性。
2.3 晶体缺陷晶体缺陷是指晶圆内部出现的晶体结构不完整或有缺陷的区域,通常是由于晶圆生长过程中的温度梯度、晶体生长速率不均匀等原因引起的。
阳极氧化产品表面缺陷的定义

產品缺陷的定義
16. 色差:
定義:整体或局部偏离规定的颜色; 可能的原因:陰极氧化,蝕刻或PVD參數設置不當而生產的一种缺陷; 17.光泽不一: 定義:整体或局部与给定的光亮度或光泽度值有偏差
可能的原因:拋光,電拋,陰极氧化,蝕刻或PVD因參數設置不當或操作不當而 產生的一种缺陷; 18.表面粗糙不一:
產品缺陷的定義
10. 砂孔: 定義:產品表面的小孔; 可能的原因:材料內部本身有雜質或氣泡,拋光后呈現出的單個或聚集在一起的小
孔; 11. 變形:
定義:產品因受力產生的形變,如扭曲,凹陷等; 可能的原因:操作不當而產生的一种缺陷:如擺放,受外力,包裝,運輸不當等 12. 波浪紋: 定義:在產品表面類似”洗衣版狀”的波浪線,垂直於原材料料紋色呈現黃色;
可能產生的原因:
1). 產品在蝕刻中,由于蚀刻后的产品未及时去墨且在未去墨前未放入清 水中,使蚀刻面被残留在产品表面的药水所腐蚀形成的一種缺陷;
2). 或產品在電拋過程中,因參數設置不當而使產品表面呈現黃色;
3). 或產品在PVD過程中,因參數設置不當而使產品表面呈現黃色或PVD夾
6.披鋒: 定義: 在衝切或修剪的過程中,產品的沖切邊有多餘的物料,呈針狀或鋸齒狀; 可能的原因: 和異物接觸或不正當的操作碰撞到產品表面;
產品缺陷的定義
7. 形狀錯誤:
定義: 產品的形狀與指定的要求不一致; 可能的原因: 模具設計不正確或模具破損或漏工序; • 漏工序: 定義: 產品在生產時,因漏掉工序而生產的一种缺陷; 可能的原因:因操作不當而導致的產品少做某個工序或幾個工序; 9. 破损: 定義:產品爆裂,破损或裂开 可能的原因: 少油或錯誤的沖壓條件或物料使用不正確或模具設計不當;
五金件缺陷定义
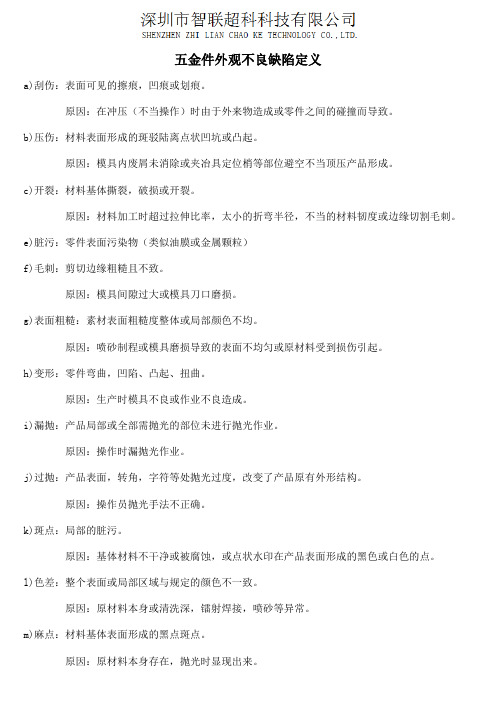
五金件外观不良缺陷定义
a)刮伤:表面可见的擦痕,凹痕或划痕。
原因:在冲压(不当操作)时由于外来物造成或零件之间的碰撞而导致。
b)压伤:材料表面形成的斑驳陆离点状凹坑或凸起。
原因:模具内废屑未消除或夹冶具定位梢等部位避空不当顶压产品形成。
c)开裂:材料基体撕裂,破损或开裂。
原因:材料加工时超过拉伸比率,太小的折弯半径,不当的材料韧度或边缘切割毛刺。
e)脏污:零件表面污染物(类似油膜或金属颗粒)
f)毛刺:剪切边缘粗糙且不致。
原因:模具间隙过大或模具刀口磨损。
g)表面粗糙:素材表面粗糙度整体或局部颜色不均。
原因:喷砂制程或模具磨损导致的表面不均匀或原材料受到损伤引起。
h)变形:零件弯曲,凹陷、凸起、扭曲。
原因:生产时模具不良或作业不良造成。
i)漏抛:产品局部或全部需抛光的部位未进行抛光作业。
原因:操作时漏抛光作业。
j)过抛:产品表面,转角,字符等处抛光过度,改变了产品原有外形结构。
原因:操作员抛光手法不正确。
k)斑点:局部的脏污。
原因:基体材料不干净或被腐蚀,或点状水印在产品表面形成的黑色或白色的点。
l)色差:整个表面或局部区域与规定的颜色不一致。
原因:原材料本身或清洗深,镭射焊接,喷砂等异常。
m)麻点:材料基体表面形成的黑点斑点。
原因:原材料本身存在,抛光时显现出来。
表面质量标准

晶体表面质量标准1.表面缺陷定义:有效通光面积内表面缺陷的最大允许尺寸和数量的定量(数值)的描述,数值表示“道子-斑点”,“S/D”例如:60-40表示道子的最大数值为60微米,斑点数最大数值为40丝依此类推: “40-20”表示道子的最大数值为40微米,斑点数的最大数值为20丝。
但“道子-斑点”的意义并不止于以上,在以下篇幅中,加以详细的描述2.道子道子指窄而长的缺陷道子数:道子的宽度。
单位:微米(0.001毫米),即60#的道子代表宽度为0.060毫米的道子。
最大的道子:宽度等于表面质量要求中道子数的道子,当元件中最大道子超过,表面质量要求中的最大道子时,元件不合格例如:元件质量要求为60-40,代表最大道子宽度0.060毫米,如果元件有70#道子,元件不合格(1)当元件最大道子小于表面质量要求中所代表的最大道子时,元件的道子数按以上步骤求和:a.求各尺寸道子的长度和(L)b.各长度之和除以元件平均直径(D)c.所得的数乘以相应的道子数.(N)d.最后求和:(2)无最大道子时,和不超过最大标称道子例元件为φ10.表面质量指标60-40,有1条50#道子2mm,1条40#道子3mm,另1条40#道子2mm,10#道子长度合计10mmC=N(L/D)C=50×(2/10)+40×(3/10)+40×(2/10)+10×(10/10)=40<60元件合格(3)当有最大道子存在时,所有最大道子的长度之和应不超过元件平均直径的1/4,即1/4D 例:如有一φ20mm的元件,对元件的要求为60-40,当只有1条60#道子长为4mm时,求元件是否合格根据要求:允许的最大道子的长度为:1/4D=1/4×20=5mm4mm<5mm此元件合格(4) 当有最大道子但又无1/4D#时,所有的道子的宽度之和是否大于指标中道子的1/2例:表面质量指标为60-40,φ20mm元件上有2条1mm的60#道子,1条4mm的40#道子N(L/D)=60×(2×1/20)+40×(4/20)=141/2S=1/2×60=30 14<30注:( S为S/D中道子数的代号) 元件合格3.疵点数,允许点子的实际直径尺寸,用0.01mm表示,不规则疵点用最大长度和宽度的平均值即60#=0.60mm 40#=0.40mm最大疵点:即质量指标要求的最大标准值例如:质量指示要求为60-40元件,最大疵点为40#=0.40mm,当在任何φ20mm 范围内所有疵点直径之和不超过最大尺寸疵点的2倍。
表面缺陷与表面粗糙度的区分及计算
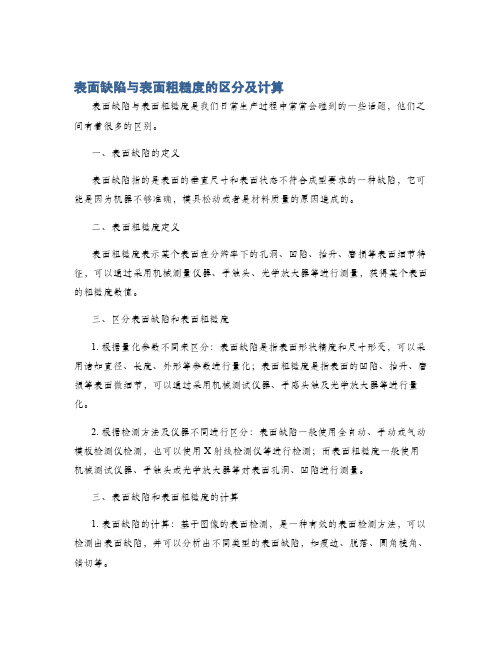
表面缺陷与表面粗糙度的区分及计算表面缺陷与表面粗糙度是我们日常生产过程中常常会碰到的一些话题,他们之间有着很多的区别。
一、表面缺陷的定义表面缺陷指的是表面的垂直尺寸和表面状态不符合成型要求的一种缺陷,它可能是因为机器不够准确,模具松动或者是材料质量的原因造成的。
二、表面粗糙度定义表面粗糙度表示某个表面在分辨率下的孔洞、凹陷、抬升、磨损等表面细节特征,可以通过采用机械测量仪器、手触头、光学放大器等进行测量,获得某个表面的粗糙度数值。
三、区分表面缺陷和表面粗糙度1. 根据量化参数不同来区分:表面缺陷是指表面形状精度和尺寸形变,可以采用诸如直径、长度、外形等参数进行量化;表面粗糙度是指表面的凹陷、抬升、磨损等表面微细节,可以通过采用机械测试仪器、手感头触及光学放大器等进行量化。
2. 根据检测方法及仪器不同进行区分:表面缺陷一般使用全自动、手动或气动模板检测仪检测,也可以使用X射线检测仪等进行检测;而表面粗糙度一般使用机械测试仪器、手触头或光学放大器等对表面孔洞、凹陷进行测量。
三、表面缺陷和表面粗糙度的计算1. 表面缺陷的计算:基于图像的表面检测,是一种有效的表面检测方法,可以检测出表面缺陷,并可以分析出不同类型的表面缺陷,如瘦边、脱落、圆角棱角、错切等。
2. 表面粗糙度的计算:表面粗糙度指标可以根据Rz、Rmr、Ra等参数,通过采用机械测量仪器对表面进行检测,进而获取其粗糙度数值。
其计算过程一般是采用移动平均法或者方差法等方式,来实现表面粗糙度的量化。
四、表面缺陷和表面粗糙度的影响1. 表面缺陷会影响颜色、硬度和耐磨性等技术特性,使得产品的外观变差,从而影响产品的销量和口碑。
2. 表面过于粗糙会降低表面光泽,粉刺明显,色泽发生变化,影响表面白度,这样就会增加污染物和微生物吸附,影响产品的抗菌性和耐候性能。
钣金中的部分表面缺陷定义汇总

钣金中的部分表面缺陷定义发布日期:2008-7-6 [ 收藏评论没有找到想要的知识 ]1.焊接1.1咬边:咬边是焊缝边缘局部低于母材面的凹陷缺陷.它是由于焊接电流过大,焊接速度太快,电弧过长或运条操作不当形成.1.2 焊瘤:焊瘤是熔化金属溢流到焊缝之外未熔化母材上形成的金属瘤,常出现在立焊、仰焊、横焊和单面焊双面成形的背面缝上.1.3弧坑:弧坑是收弧不正确成形的,它影响外观质量并易引到裂纹,应清理后进行补修复.1.4气孔:气孔是焊接熔池中的气泡在凝固时未能及时逸出,而残留在焊缝中形成的孔穴,产生的原因有焊条受潮,焊件不洁,电流过大或过小,电弧过气对溶池保护不良,焊接速度太快等.1.5缩孔:缩孔是熔化金属在凝固过程中因收缩产生并残留在焊疑中的孔穴.1.6夹杂和夹渣:由冶金反应产生的非金属夹杂物,氧化物和熔渣在焊接过程中来不及浮出,残留在焊缝中形成夹杂物和夹渣,形成夹渣的原因有:多层焊时清渣不干净,运条操作不当,焊接电流太小,工件坡口角度太小等.1.7未焊合与未焊透:未焊合是由于焊接电流过小,电弧偏吹,待焊表面污染等原因,使熔化金属与母材或金属焊道之间没有完全熔化结合造成的.1.8裂纹:焊接裂纹主要有冷裂纹和热裂纹,热裂纹是焊缝和热影响区金属冷却到故相浅温度附近产生的.产生的裂纹称结晶裂纹,常出现在焊缝中心和弧坑中,热裂纹出现在表面时有氧化白色,这是判断热裂纹的主要标志,冷裂纹是焊接接头冷却到较低温度时产生的裂纹.它是焊后几小时几天甚至更长时间出现的裂纹.防止裂纹的槽施有预热、后热.采用低氢焊条,焊条烘干清除坡口附近油锈,减小焊接应力等.2.表面喷涂部分2.1 涂层光泽度:对喷涂表面用光泽仪将光线呈60°斜角方向射向涂层表面后在其表面反射光的程度,一般平光漆的光泽度在30%以下.2.2 结瘤:因油漆质量不良喷涂后而在涂层表面上形成的一块一块的疙瘩.2.3 缩孔:俗称麻点,涂层干燥后滞留的若干大小不等分布各异的圆形小坑.2.4 起泡:因喷涂时,涂层覆盖部分气体,在烘烤时而产生的表面凸起现象.2.5 针孔:从喷涂表面贯穿到喷涂底部或基体金属的微小孔道.2.6 开裂:在涂层表面形成一道道裂纹.2.7 剥落:一道或多道涂层脱落.2.8 粉化:涂层表面由于一种或几种漆基的降低颜料的分解而呈现出附着疏松细粉的现象.2.9 颗粒:因材料杂质或外来物(如焊渣等)的影响而在表面形成的,颜色与正常表面一致的凸起现象.2.10 流挂:喷涂时由于涂层的流动而产生的堆积现象.2.11 露底:局部无涂层或覆盖不平.2.12 夹杂物:由于前处理时未完全消除表面的杂物及喷涂环境不良而附着在涂层里的杂物.3.电镀、铬酸盐处理件3.1 镀前划痕:电镀或氧化之前因操作不当或对明显缺陷进行粗糙打磨等人为造成的基体材料上的划伤或局部磨擦痕迹,一般呈线型.3.2 镀前凹坑:由于基体材料缺陷或在加工过程中外来金属屑的影响而在材料表面留下的小浅坑状痕迹.3.3 抛光区:对基材上的腐蚀、划伤、焊接区、铆接区等部位进行机械抛光后表现出的局部高光泽、光亮区域、无裂痕.3.4 烧伤:拉丝处理时因操作不当,造成零件表面过热而留下的烧蚀痕迹.3.5 水印:电镀或氧化后因清洗水未及时干燥或干燥不彻底所形成的斑纹、印迹.3.6 露白:镀锌彩色钝化膜因摩擦而被去除露出锌层,呈现为区别于周围彩色的白色.3.7 基材花斑:电镀或氧化前因基体材料腐蚀或者材料中的杂质,或者材料微孔等原因所造成的与周围材质表面不同光泽或粗糙度的斑块状花纹外观.3.8 雾状:指镀层表面存在程度不同的云雾状覆盖物,多数产生于光亮镀层表面.3.9 局部无铬层:指镀铬表面因电镀工艺的局限而在凹槽内、深孔内、折弯内角等低电位区出现铬层未电镀上的现象.3.10 凹痕:因基材受撞击而呈现的凹陷现象.3.11 修补:因膜层损伤而用涂料所作的局部遮盖.3.12 异物:由材料、模具、环境或机器设备中的灰尘、夹杂物、污物等影响而形成的与表面不同色的斑点.3.13 浅划痕:膜层表面划伤、但未伤及底层表面;对其它表面则为:目测不明显、手指甲触摸无凹凸感,未伤及材料本体的伤痕.3.14 深划痕:表面膜层划伤、且伤及底层面;对无膜层表面则为:目测明显、手指甲触摸有凹凸感,伤及材料本体的伤痕.3.15 挂具印:指电镀、氧化或喷涂等表面处理生产过程中,因装挂用辅助工具的遮挡而使其与零件相抵触的部位局部无膜层的现象.3.16 针孔:从镀层表面贯穿到镀层底部或基体金属的微小孔道.3.17 麻点:在电镀过程中由于种种原因而在电镀表面形成的小坑.3.18 起皮:镀层呈片状脱落基体的现象.3.19 起泡:在电镀中由于镀层与底金属之间失去结合力而引起一种凸起状缺陷.3.20 削落:由于某些原因(例如不均匀的热膨状或收缩)引起的镀层表面的破裂与脱落.3.21 阴阳面:指镀层表面局部亮度不均或色泽不均匀的缺陷.3.22 斑点:指镀层表面的一类色斑,暗斑等缺陷,它是由于电镀过程中沉淀不良、异物粘附或钝化液清洗不干净造成.3.23 烧焦镀层:在过高电流的情况下形成的黑暗色,粗糙松散、质量差的沉积物,其中含有氧化物或其它杂质.3.24 树枝状结晶:电镀时在阴极上(特别是边缘和其它高电流密度)形成粗糙、松散的树枝或不规则突起的沉积物.3.25 海绵状镀层:与基体材料结合不牢固的疏松多孔的沉积物.3.26 黑点:因材料表面有未去除的锈迹、锈斑、电镀后在镀层表面形成的黑暗的缺陷.4.塑胶件、压铸件4.1 水纹:塑胶或压铸件成形时,熔体流动产生的可见条纹.4.2 缩水:因材料、工艺等原因使塑胶或压铸件表面出现凹陷的收缩现象.4.3 气泡:指塑胶体因工艺原因内部出现的可见空气泡.4.4 砂眼:塑胶或压铸件表面的疏松针孔.4.5 披锋:压铸或塑胶件上浇口残留物取掉后的毛刺.钣金常见表面缺陷的预防与补救措施发布日期:2008-7-6 [ 收藏评论没有找到想要的知识 ]常见表面缺陷的预防与补救措施涂覆膜层分三个类别:一.电镀膜层二.转化膜层(氧化、钝化、磷化)三.有机膜层(喷油、喷粉)一.电镀膜层一.电镀膜层6).脆性:镀层能受基体变形的能力,主要决定于材料应力.7).麻点:电镀层表面形成的小凹坑.8).海绵状:镀层与基体结合不牢固的疏松多孔的沉积物.9).斑点:镀层表面出现后斑点或污点.1 10).树枝状结晶:电镀时在阳极上(特别是边缘和其它高电流密度区)形成的粗糙/松散的树枝状或不规则突起的沉积物.二.转化膜层1). 1).烧损:在阳极氧化过程中,氧化膜层受到严重电击穿,铝局部损坏,或局部过热表面呈松软的粉状现象.2).封孔灰:表面封孔产生一层松软浮灰层.二.转化膜层3).起粉:膜层,疏松,附着不牢固.4).着色不均:颜色不均匀,发花.5).剥落:碎裂和附着力下降的现象.6).应力破裂:机械加工受热影响产生的内应变,膜层裂开.三.有机涂层缺陷1).起泡:涂层局部粘附不良引起涂膜浮起.2).针孔:涂层表面上以看见类似针刺成的微小孔.3).开裂:涂层出现不连续的外观开裂变化,通常由于涂层老化而引起的.4).剥落:一道或多道涂层脱离下涂层,或涂层完全脱离基材的现象7).厚边:靠基体的边缘或折弯角处的涂料堆积现象.三.有机涂层缺陷6).粉化:涂层表面由于一种或多种漆基的降解及颜料的分解而呈现出疏松附着细粉的现象.5).流挂:喷涂时涂层流动产生的堆积8).收缩:涂层干燥后仍滞留的若干大小不等,分布各异的圆形小坑现象.9).露底(漏涂区):局部无涂层或涂料覆盖不严等现象(常见于内折弯角处,孔的连缘截面,基材切口边缘截面等部位)二.常见缺陷产生原因.预防措施和补救措施起泡原因:1.电镀工艺配方有缺陷2.电镀溶液有污梁3.电镀前除油不彻底(前处理不干净)4.工序不完整.起泡预防:1.选择证明良好的配方2.严格管理维护镀液3.加强控制前处理4.完善工序.其中基材原因:选用不合适的材料,氢气量增加,氢脆造成.补救措施:无法补救,必须重镀 .二. 基材花斑原因:电镀前基材料产生严重锈蚀而出现,电镀后形成花斑.预防:对基材采取良好有效的工序间进行防腐蚀性措施.补救措施:基材粗糙而易镀层中产生微小缺陷.镀后无法补救,镀前可用机械方法消除(拉丝,打磨)三. 挂印原因:表面处理生产的必然的印迹现象.预防:补救是必然进行的,在挂印位置在工件内表面和B面必曾时增加工艺孔. 补救措施:1.手工涂漆2.镀彩锌采用金色漆修补3.相同颜色漆作修补(其它金属)四. 黑点原因:有多种,各环节都有可能导致.1.基材中有不允许的杂质,有裂纹或小针孔.2. 钝化膜质量不良.3. 表面处理后因素:1).环境恶劣. 2).污染(汗液,胶水,气体腐蚀).4.搬运过程中划碰伤.四. 黑点预防:1. 选用合格的基体材料2. 机械加工过程中有保护措施.3. 处理后避免污染,选择良好的环境.4.加强电镀工艺,使钝化良好.五.基材晶粒粗大原因:金属材料(铝板)在轧制过程中出现问题 .预防:加强材料来料质量控制 .补救措施:无法补救,由于材料轧制时的工艺参数控制不良而产生的此种现象,导致性能发生变化 .六.裂纹原因:多是因为材料本身的性能较差所决定或者折弯前材料表面有微小裂纹.预防:1.严格按照设计要求,采用性能延伸良好材料.2.避免微小深划痕迹(拉丝) .3.尽量避免拉丝、拉丝纹路与拆弯直线方向一致.补救措施:无法补救,表面处理前进行补救,封严或扩大开口.七.露白原因:1.溶液截留而滞后腐蚀导致,如缝隙,微孔,裂纹,压铆缝隙,盲孔.2.因磨擦磨损导致.预防:1.控制焊缝质量及夹缝大/小。
表面缺陷与表面粗糙度的区分及其评定

表面缺陷与表面粗糙度的区分及其评定
表面缺陷与表面粗糙度是表面质量的两个关键指标,它们在产品质量控制和工程设计中具有重要的意义。
虽然它们都与表面特征相关,但是它们之间有着明显的区别。
表面缺陷是指在产品表面上出现的不符合设计要求或规格的瑕疵或
不良现象。
它们可能是由于制造过程中的误差、材料缺陷或外力作用等原因引起的。
常见的表面缺陷包括划痕、裂纹、气孔、凹坑等。
表面缺陷对产品的外观质量和功能性能都有着直接影响,因此需要通过适当的评定方法进行检测和评估。
表面粗糙度是指表面上的微小不平整度或纹理特征。
它是由于材料的粒子或切削工具的运动引起的。
表面粗糙度主要是通过测量表面的垂直高度差来描述的,常用的参数有Ra、Rz等。
表面粗糙度的大小对
产品的摩擦、密封性、润滑性和光学性能等方面都有着重要的影响。
因此,在设计和制造过程中,需要合理控制和评定表面粗糙度。
为了评定表面缺陷和表面粗糙度,常用的方法有目视检查、光学显微镜观察、扫描电子显微镜观察、触觉检测、表面轮廓仪测量等。
这些方法可以对表面进行定性和定量的评定,从而判断产品是否符合要求。
此外,为了更精确地评定表面缺陷和表面粗糙度,还可以使用表面缺
陷评定标准和表面粗糙度参数进行定量分析。
例如,ISO 4287标准可以用于评定表面粗糙度,而ISO 8785标准则可以用于评定表面缺陷。
总之,表面缺陷和表面粗糙度是表面质量的两个重要指标,它们的评定可以通过多种方法进行,从而保证产品的质量和性能。
在工程设计和生产制造中,合理控制和评定表面缺陷和表面粗糙度对于提高产品的竞争力和市场价值具有重要的意义。
- 1、下载文档前请自行甄别文档内容的完整性,平台不提供额外的编辑、内容补充、找答案等附加服务。
- 2、"仅部分预览"的文档,不可在线预览部分如存在完整性等问题,可反馈申请退款(可完整预览的文档不适用该条件!)。
- 3、如文档侵犯您的权益,请联系客服反馈,我们会尽快为您处理(人工客服工作时间:9:00-18:30)。
表面缺陷定义
【原创版】
目录
1.表面缺陷的定义
2.表面缺陷的分类
3.表面缺陷的影响
4.如何检测和修复表面缺陷
正文
【表面缺陷的定义】
表面缺陷是指在物体表面的不均匀、不规则或损坏的现象。
这些缺陷可能会影响物体的外观、功能和性能。
表面缺陷通常包括诸如裂纹、凹痕、气泡、脱落、腐蚀和其他形式的损伤。
【表面缺陷的分类】
表面缺陷通常根据其形状、大小和位置进行分类。
例如,裂纹可能是长而细的,而气泡则可能是圆形或椭圆形的。
缺陷也可能在物体的表面、边缘或角落中出现。
【表面缺陷的影响】
表面缺陷可能会对物体的性能和外观产生负面影响。
例如,裂纹可能会导致物体的结构强度降低,而气泡可能会降低物体的防水性能。
此外,表面缺陷可能会影响物体的美观度,降低其价值和使用寿命。
【如何检测和修复表面缺陷】
表面缺陷通常可以通过视觉检查、测量和无损检测技术进行检测。
一旦发现了表面缺陷,就可以采取一些方法进行修复。
例如,可以使用填充物或粘合剂来修复裂纹或凹痕,或者使用砂纸或喷砂来去除表面缺陷。
在
某些情况下,可能需要进行更彻底的修复,例如焊接或更换整个部件。
表面缺陷是指在物体表面的不均匀、不规则或损坏的现象,可能会影响物体的外观、功能和性能。