TPS在广汽丰田零部件厂内物流系统中的应用
【物流规划】-广汽丰田物流模式探究

【物流规划】-广汽丰田物流模式探究广汽丰田汽车的物流充分运用了丰田生产方式(TPS)的准时化(JIT)和働自动化理念,以实现最佳物流品质、最低物流成本为目标,践行准时化物流和TPS的持续改善,致力于追求世界第一的物流模式,特别是借助于股东方日本丰田的经验优势,这些理念和目标已深深融入到汽车物流运作的每一个环节,形成明显的特色。
丰田目前基本上专注于对汽车的研发、设计、制造、销售及售后服务等领域,而物流业务都是采取外包的方式,委托物流供应商来实现。
“丰田为了控制成本,实现平准化生产,在供应链管理中实行‘零库存’方式。
所谓的‘零库存’当然不是完全没有库存,而是指没有多余的不必要的库存,设定的库存是可以维持生产需要的最少量的库存。
丰田通过有效地降低物流过程的库存,很好地控制了各环节的成本。
”这种JIT物流方式和现在广州本田和东风日产等汽车厂家的模式有所不同。
在零部件物流方面,广汽丰田为满足顾客需求,实现市场动向、工厂生产和零部件采购的同期化管理,全面采用了同步物流和循环取货的零部件物流模式。
“同步物流,是生产和供应之间的最短连接,快速高效,库存最小,体现了精益物流的精髓——消除一切浪费。
广汽丰田在项目规划时,就将50%以上货量的零部件布局在工厂周边,建立同步物流体系。
同步物流的信息,由生产线控制系统直接传送,就是说,我们将周边供应商完全纳入厂内工程系统。
可以说,运用最新的理念,进行前瞻性的规划布局,是广汽丰田物流成功的起点。
”“循环取货的特点是高效、准确、灵活,是供应链物流最有效的运输模式,也是中国汽车零部件物流发展的方向。
广汽丰田是中国汽车物流业‘循环取货’的先行者,也是其理论和方法的集大成者。
早在2006年,广汽丰田第一款车‘凯美瑞’投产时,就以丰田全球样板工厂的定位,导入了‘循环取货’的物流模式。
而丰田式的‘循环取货’最大的特色,是每个环节融入丰田生产方式的JIT理念,作‘平准化’的物流供应。
比如物流中转仓(Cross Dock),除了进度吸收,更重要的功能是进行与生产同步的平准化作业,这是一个操作过程,而非单纯的仓储功能。
丰田公司TPS管理模式

丰田公司的TPS 管理模式丰田的生产和管理系统长期以来一直是丰田公司的核心竞争力和高效率的源泉,同时也成为国际上企业经营管理效仿的榜样,例如,作为丰田生产管理一大特点的看板管理已被世界各地的企业所采用。
如今,世界很多大型企业都在学习丰田管理模式的基础上,建立了各自的管理系统,以试图实现标杆超越,像通用电气公司、福特公司、克莱斯勒公司等世界著名企业都加入了这一行列。
但是,令人惊异的是,尽管丰田管理模式已为全球所认同和接受,真正成功的企业却并不多,如今位于日本的丰田公司每天都要接受数以万计的企业高级管理者参观,这些参观者将他们看到的管理方式带到本国后,并没有得到意想的效果,为此,很多人认为丰田管理模式的成功根源于其独特的文化因素。
但事实并非如此,例如同是日本公司的尼桑和本田却并没有达到丰田的标准,而丰田本身却将其独特的管理模式带到了全世界,这其中的代表就是位于美国肯塔基州的丰田乔治城汽车生产厂,该厂自1988 年7 月开始在1300 英亩的厂址上进行批量生产,年生产能力为200000 辆Camry 轿车,相当于以往美国从日本进口同类型轿车的总量,1991 年秋天丰田美国公司引入了全新的Camry 轿车,1992 年该类型车的供应量为40000 辆,销售额将增加20%。
新的Camry 轿车属于中等家庭车系列,占有美国所有轿车市场l/3 的市场份额,价格平均为$18500 ,税前平均利润为17%,显然,其经营绩效是十分瞩目的。
由此看来,丰田管理模式并不是因为其独特的日本文化而难以为其他国家的企业所学习,之所以存在管理方法难以移植的情况,主要原因在于参观者所看到的丰田管理模式只是其外在的东西,诸如它的活动、连接和生产流等都是较为固定、甚至死板的东西,但是,在这些看似简单的活动和流程后面,却蕴含着丰田公司巨大的柔性和适应性,正是这些看似简单、却颇具柔性的管理特点,造就了丰田公司举世瞩目的经营业绩,也使得他的柔性化生产管理方式--TPS (Toyota Production System )成为管理中的精髓,并使大规模定制模式下的敏捷产品开发和生产成为现实。
广汽丰田物流运输详解

一、GTMC物流概述1、GTMC物流的背景(TPS)丰田生产方式(Toyota Production System,简称“TPS”)是TOYOTA 在长期的实践中逐步建立和完善的一套理论体系。
它以企业获得最大利润、服务社会、创造美好生活、培养优秀员工为根本目的,以彻底杜绝浪费为基本思想,在持续改善的基础上追求制造产品合理性品质至上的一种生产方式。
准时生产制:(Just in Time,简称“JIT”)和自働化是丰田生产方式的两大支柱。
1).JIT(准时生产制)JIT(准时生产制)要求在所需要的时间按所需要的数量生产所需要的品种,尽可能消除一切浪费;为了实现准时生产,丰田在整个物流过程中(从供应商到生产线)努力实现持续的小批量高频率平稳的部品运送。
而平准化和看板的运用则是实现准时生产的重要途径。
平准化平准化是实现JIT 的大前提,其含义是将生产或供给的物品的种类和数量进行平均化。
在生产和供应的过程中如果没有实现平准化,将会造成自工序完成品不足或为防止缺品而准备库存,也会造成人员、器材必须以浮动的最大值准备,造成不必要的浪费。
在物流工程中,平准化具有重要的意义,右图就是在物流中未实施平准化的例子,可以明显的看出没有实施平准化所造成工时和物流器材的增加。
2 )看板JIT 是一种拉动式的管理方法,它需要从最后一道工序通过信息流向上一道工序传递信息,这种传递信息的载体就是看板。
没有看板,JIT 是无法进行的。
看板分为引取看板和生产看板两种,记载着生产和运送的数量、时间、目的地、放置场所、搬运工具等信息,从装配工序逐次向前工序追溯。
在装配线将所使用的部品上所带的看板取下,以此再去前一道工序领取。
前工序则只生产被这些看板所领走的量,“后工序领取”及“适时适量生产”就是通过这些看板来实现的。
看板具有以下作用和规则:①引取情报(前工程按后工程看板后补充生产);②生产指示情报(前工程按看板数生产);③防止生产过程搬运过多(无看板,不生产、不搬运);④问题明显化,可调节库存。
丰田汽车的TPS生产管理系统

丰田汽车的TPS生产管理系统第一,丰田的BOM系统。
和其它制造业一样,汽车制造业实现管理信息化,也必须构建自己的基本数据库(BOM),但是由于汽车相比其它制造业而言,涉及的范围更为广泛,构成的因素也大得多,光是零部件就有成千上万个,而这些由于设计的变更又会经常的改动,这就要求BOM系统相比起来要更加的灵活,更能应用于汽车制造业本身,同时需要关联的数据库也会更加的复杂,上层需要考虑到与开发相结合,下层需要考虑到与计划、零部件展开供应链等相结合,当然基本数据库并不能完全体现丰田管理方式与其它管理模式的区别。
第二,丰田的生产计划执行系统。
丰田的生产计划,大致可以分为三个阶段,第一个就是最初的年计,当然年计也分为长期计划和一年期计划,具体的一年期计划也就是按照各方面的因素,结合工厂和供应商的产能以及市场销售预测制定,当然这个各个厂家是大同小异,主要是满足零部件采购周期长的需要。
其次就是月度计划,月度计划是按照系统来进行执行的,理想的模式是从销售终端汇总来的订单数据,根据该数据确定下一月或者当月的生产计划,当然通常情况是将真实需求与市场消费预测相结合,以此来决定具体的生产计划,包括车型,颜色,等级等等的生产比例,决定月度生产计划之后,我们利用BOM系统得出各零部件的当月必要数。
第三阶段就是与生产实际相结合的日次生产计划,这个是相互调整的,有很多的灵活性,具体思路就是根据前一天的生产实绩作出往后的日次虚拟生产线,以此为根据采购近郊周期相对较短的零部件。
这样的计划模式可取之处就在于可以灵活应对变化多样的市场,及时调整生产满足销售的需求。
第三,丰田的控制系统丰田追求的是小批量生产模式,这就要求从生产设备到装配线上的零部件供给都必须满足既定的要求,实现单台生产的可能。
在布置日生产计划同时,按照平准化的顺序事先安排好生产,利用控制系统的各层次功能进行生产控制和生产指示的发出,这其中主要难点就在于由于事先是不知道生产什么样什么类型的车,只有到了一定的阶段后工序才会知道接下来需要生产车辆的类型,从而决定需要什么样的零部件,或者说机器人该执行什么样的工作指令等等,这就是说在设计控制系统的时候需要将车辆生产过程划分为若干个部分,需要综合规划控制系统的功能,同时又需要将它与计划系统,物流系统相结合起来。
TPS在广汽丰田物流系统的应用及借鉴意义_下

笔 者认
销 (销
门日 ) ( 门白
售
当的
生产
物流 ) 体系
才是恰
下 工序 ) 的思想 , 使
包括 经销 商
供应 商
工厂
运
输商在 内所有 的工序 紧密结成一
T p S 在 物流 系 统应 用 的重 点 难点及其借 鉴意 义
企业 ( 组织 ) 如 同有生命 的 生物 , 有其本 身应有 生存环 境和 运行规 律 , 符 合规律 就会健 康发 展 , 违 背规律 就会付 出健康 甚至 生命 的代价 不 同国界 的人 , 尽 管生存 环境 等不尽相 同但其 生物 本质 相 同 ( 需 要 衣食 住 行等 )
反而会成为累赘
在 市场爆 发式 增长期 或不可预测
时 , 有观点认 为 只有 大量 改造厂 房 设 备达 到 G M C 的水平 且 T 投人 巨资 打造计算机 系统才 能推 行 TPs , 笔者 以为 , 只有 思想 先 行 才是 正道 , 丰 田当年推 行 TP S 并没 有一 次性 大量改 造设 备 , 甚 至很 多设 备长期处 于同行落 后水
断解决 问题 和意识 革命 , 丰 田以
非 常强 , 根本不需要换装 例 如 , 油 漆线如果 连续更换 颜色会 造成
点带 面坚定信 念不 断解决 问题 ,
在 解 决 问 题 中培 养 人 才 并 推 进 TPS , 缺失 了 JIT 就不是 TPS 还有 观点认 为 TP 就是 看板 S
在 各环 节削减 库存 和资金 占用 的 同时 , 也 面临订 单交 付响应时 间
但滞 销会带来 实质 的损失 二者
翻译 成
精益 , 远 没 有表 达 出 笔者认 为 , 为 了真实 表
的 原 意 , 可 把 L a 翻译 e n (音 : 动心 ) , 即感 动
TPS及其在企业中的应用分析
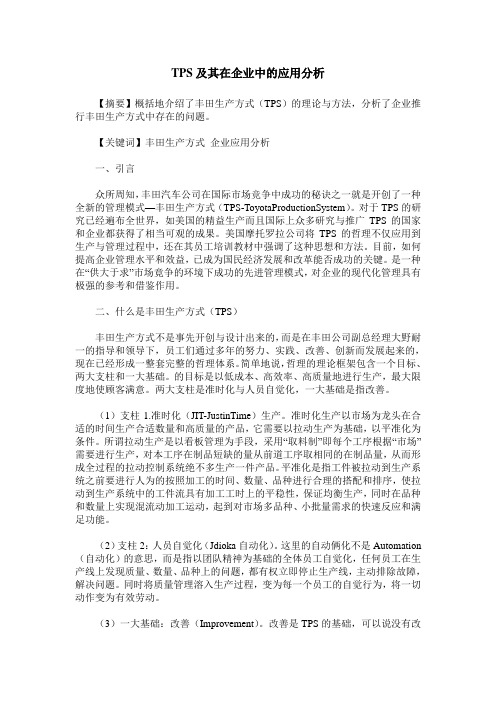
TPS及其在企业中的应用分析【摘要】概括地介绍了丰田生产方式(TPS)的理论与方法,分析了企业推行丰田生产方式中存在的问题。
【关键词】丰田生产方式企业应用分析一、引言众所周知,丰田汽车公司在国际市场竞争中成功的秘诀之一就是开创了一种全新的管理模式—丰田生产方式(TPS-ToyotaProductionSystem)。
对于TPS的研究已经遍布全世界,如美国的精益生产而且国际上众多研究与推广TPS的国家和企业都获得了相当可观的成果。
美国摩托罗拉公司将TPS的哲理不仅应用到生产与管理过程中,还在其员工培训教材中强调了这种思想和方法。
目前,如何提高企业管理水平和效益,已成为国民经济发展和改革能否成功的关键。
是一种在“供大于求”市场竟争的环境下成功的先进管理模式,对企业的现代化管理具有极强的参考和借鉴作用。
二、什么是丰田生产方式(TPS)丰田生产方式不是事先开创与设计出来的,而是在丰田公司副总经理大野耐一的指导和领导下,员工们通过多年的努力、实践、改善、创新而发展起来的,现在已经形成一整套完整的哲理体系。
简单地说,哲理的理论框架包含一个目标、两大支柱和一大基础。
的目标是以低成本、高效率、高质量地进行生产,最大限度地使顾客满意。
两大支柱是准时化与人员自觉化,一大基础是指改善。
(1)支柱1.准时化(JIT-JustinTime)生产。
准时化生产以市场为龙头在合适的时间生产合适数量和高质量的产品,它需要以拉动生产为基础,以平准化为条件。
所谓拉动生产是以看板管理为手段,采用“取料制”即每个工序根据“市场”需要进行生产,对本工序在制品短缺的量从前道工序取相同的在制品量,从而形成全过程的拉动控制系统绝不多生产一件产品。
平准化是指工件被拉动到生产系统之前要进行人为的按照加工的时间、数量、品种进行合理的搭配和排序,使拉动到生产系统中的工件流具有加工工时上的平稳性,保证均衡生产,同时在品种和数量上实现混流动加工运动,起到对市场多品种、小批量需求的快速反应和满足功能。
TPS在广汽丰田物流系统的应用及借鉴意义
TPS在广汽丰田物流系统的应用及借鉴意义摘要:丰田汽车公司源于物流平准化的持续改善凝结成TPS,TPS在丰田汽车公司的全面应用使其得到快速发展,全球掀起学习TPS的浪潮。
TPS在广汽丰田物流系统的成功运用,使生产得到有效保障,现场运行有条不紊,做到了安全、质量、环境保护、5S和成本等各方面的精益,有着非常值得学习的地方。
希望本文能为学习TPS的企业和个人有所给力。
1. 引言长期以来,丰田一直将物流管理、营销管理及财务管理等同视之为核心管理技术。
丰田物流企划部的员工自豪地说:“TPS(Toyota Production System,丰田生产体系)的发展史就是一部物流发展的历史。
”日本物流协会前会长、丰田前总经理、现董事长张富士夫(TPS的创始人大野耐一的弟子之一,曾参与创建TPS)曾担任丰田生产管理部物流管理室的第一任室长,由有物流管理从业背景的人出任企业最高管理者在世界汽车界也是绝无仅有的,足见丰田汽车公司对物流的重视和物流在TPS中的重要性。
本文描述的物流系统是指按照采购订单有组织地将零部件从供应商以多种物流服务方式输送至汽车生产工厂指定位置暂时停放及卸货,并有序、准确地向生产车间进行零部件上线,以及完成汽车生产后商品车运输管理的整个物流过程。
广汽丰田汽车有限公司(以下简称GTMC)的物流模式,是基于TPS思想构筑的物流管理体系,用计算机系统辅以人的智慧制定切实可行、精益的物流计划,用最简单和容易理解的方式在最恰当的时间把恰到好处的作业指令在最恰当的场所传递给每一个合格作业人员(即JIT的作业指令,或称恰到好处的作业指令),其形式上可以是指示牌、作业指示书等作业指令和附着在物品或器具上的看板或其他形式的管理道具,很多看板可以及时暴露问题。
当工作条件恰当,工作内容简单、易于执行可以及时发现不良,整个系统的每个人都知道什么时间干什么,工作时间被安排得有条不紊、忙而不乱时,全面彻底的包含各管理要素的标准作业(安全、质量、环境保护、5S和成本等)就能使各方面都做到最精益。
浅谈丰田管理方式在物流中的应用
浅谈丰田管理方式在物流中的应用(作者:___________单位: ___________邮码: ___________)论文关键词:物流丰田汽车TPS论文摘要:丰田汽车作为物流业的先驱将自己优秀的生产和管理系统融入到了物流配送体系中,大大降低了物流成本同时又提高了公司整体运作的效率。
其以TPS为管理精髓的模式中与物流相关的JIT及时生产方式,标准化作业,5S,可视化管理都非常值得我们研究与借鉴。
近年来,物流业迅速崛起已经成为中国最有前景、最有潜力的新兴行业之一。
作为物流业的先驱者丰田汽车,将自己优秀的生产和管理系统融人到了物流配送体系中,大大降低了物流成本同时又提高了公司整体运作的效率。
一、丰田汽车的生产管理方式丰田汽车的生产管理方式主要是以TPS为管理精髓的一系列的管理模式,JIT的生产方式、看板的管理方法等等。
TPS丰田生产系统又称为TOYOTAWAY,目的是消除运营中所有的过载、不均衡、浪费,通过PDCA—计划、执行、检查、纠正的方法解决问题,改善质量、成本、交货期,突现零故障,零事故、零人力资源浪费等等。
从TPS中衍生出很多细化的管理概念,在这里我们挑一些与物流紧密相关的来介绍一下。
1.JIT及时制生产JIT生产方式的基本思想是:在需要的时候、提供需要的产品、提供需要的量,这种生产方式的目标就是追求零库存,或者说库存达到最小的生产系统。
2.标准化作业标准化作业就是将作业流程首先进行整体规划,确定作业目标、内容、重点以及安全问题,再将整个流程细化成为各个小的部分,有时会细化到每一个动作。
统一标准不仅可以方便管理.更重要的是可以很容易的发现作业中的错误。
3.5S5S即整理、整顿、清洁、清扫和素养。
在丰田管理体系中,5S是对作业场所最基本的管理。
4.可视化管理可视化管理也是丰田管理的一大特色。
所谓可视化管理就是将标准化作业书等一系列作业管理资料都贴在工作场所的管理板上。
这样做可以使每一个人对各个工位的作业情况一目了然,同时也便于管理者及时发现问题。
丰田公司的TPS管理模式
邁向Just-In-Time管理的道路--豐田公司的TPS管理模式豐田的生產和管理系統長期以來一直是豐田公司的核心競爭力和高效率的源泉,同時也成為國際上企業經營管理效仿的榜樣,例如,作為豐田生產管理一大特點的看板管理已被世界各地的企業所採用。
如今,世界很多大型企業都在學習豐田管理模式的基礎上,建立了各自的管理系統,以試圖實現標杆超越,像通用電氣公司、福特公司、克萊斯勒公司等世界著名企業都加入了這一行列。
但是,令人驚異的是,儘管豐田管理模式已為全球所認同和接受,真正成功的企業卻並不多,如今位於日本的豐田公司每天都要接受數以萬計的企業高級管理者參觀,這些參觀者將他們看到的管理方式帶到本國後,並沒有得到意想的效果,為此,很多人認為豐田管理模式的成功根源於其獨特的文化因素。
但事實並非如此,例如同是日本公司的尼桑和本田卻並沒有達到豐田的標準,而豐田本身卻將其獨特的管理模式帶到了全世界,這其中的代表就是位於美國肯塔基州的豐田喬治城汽車生產廠,該廠自1988年7月開始在1300英畝的廠址上進行批量生產,年生產能力為200000輛Camry轎車,相當於以往美國從日本進口同類型轎車的總量,1991年秋天豐田美國公司引入了全新的Camry轎車,1992年該類型車的供應量為40000輛,銷售額將增加20%。
新的Camry轎車屬於中等家庭車系列,佔有美國所有轎車市場l/3的市場份額,價格平均為$18500,稅前平均利潤為17%,顯然,其經營績效是十分矚目的。
由此看來,豐田管理模式並不是因為其獨特的日本文化而難以為其他國家的企業所學習,之所以存在管理方法難以移植的情況,主要原因在於參觀者所看到的豐田管理模式只是其外在的東西,諸如它的活動、連接和生產流等都是較為固定、甚至死板的東西,但是,在這些看似簡單的活動和流程後面,卻蘊含著豐田公司巨大的柔性和適應性,正是這些看似簡單、卻頗具柔性的管理特點,造就了豐田公司舉世矚目的經營業績,也使得他的柔性化生產管理方式--TPS(Toyota Production System)成為管理中的精髓,並使大規模定制模式下的敏捷產品開發和生產成為現實。
丰田公司TPS管理模式
丰田公司的TPS管理模式丰田的生产和管理系统长期以来一直是丰田公司的核心竞争力和高效率的源泉,同时也成为国际上企业经营管理效仿的榜样,例如,作为丰田生产管理一大特点的看板管理已被世界各地的企业所采用。
如今,世界很多大型企业都在学习丰田管理模式的基础上,建立了各自的管理系统,以试图实现标杆超越,像通用电气公司、福特公司、克莱斯勒公司等世界著名企业都加入了这一行列。
但是,令人惊异的是,尽管丰田管理模式已为全球所认同和接受,真正成功的企业却并不多,如今位于日本的丰田公司每天都要接受数以万计的企业高级管理者参观,这些参观者将他们看到的管理方式带到本国后,并没有得到意想的效果,为此,很多人认为丰田管理模式的成功根源于其独特的文化因素。
但事实并非如此,例如同是日本公司的尼桑和本田却并没有达到丰田的标准,而丰田本身却将其独特的管理模式带到了全世界,这其中的代表就是位于美国肯塔基州的丰田乔治城汽车生产厂,该厂自1988年7月开始在1300英亩的厂址上进行批量生产,年生产能力为200000辆Camry轿车,相当于以往美国从日本进口同类型轿车的总量,1991年秋天丰田美国公司引入了全新的Camry轿车,1992年该类型车的供应量为40000辆,销售额将增加20%。
新的Camry轿车属于中等家庭车系列,占有美国所有轿车市场l/3的市场份额,价格平均为$18500,税前平均利润为17%,显然,其经营绩效是十分瞩目的。
由此看来,丰田管理模式并不是因为其独特的日本文化而难以为其他国家的企业所学习,之所以存在管理方法难以移植的情况,主要原因在于参观者所看到的丰田管理模式只是其外在的东西,诸如它的活动、连接和生产流等都是较为固定、甚至死板的东西,但是,在这些看似简单的活动和流程后面,却蕴含着丰田公司巨大的柔性和适应性,正是这些看似简单、却颇具柔性的管理特点,造就了丰田公司举世瞩目的经营业绩,也使得他的柔性化生产管理方式--TPS(Toyota Production System)成为管理中的精髓,并使大规模定制模式下的敏捷产品开发和生产成为现实。
- 1、下载文档前请自行甄别文档内容的完整性,平台不提供额外的编辑、内容补充、找答案等附加服务。
- 2、"仅部分预览"的文档,不可在线预览部分如存在完整性等问题,可反馈申请退款(可完整预览的文档不适用该条件!)。
- 3、如文档侵犯您的权益,请联系客服反馈,我们会尽快为您处理(人工客服工作时间:9:00-18:30)。
使 用状态
分割 进度 数进一 步细
化 就 是平 准 化 水 平 的 进 一 步 提
子
再 到 SP 区 ( 或 生 产线 ) S
广州地 区以外 因为运输周 期较长
( 如无 对策则 对应 生产计 划变更 的 响应 周期 长 ), 零 部件 出厂时 对应 的生产顺 序 尚未确定 , 这些 课 题都需 要在 厂 内物 流环节逐 一
产 线 出现 异 常, G M C 停 止 向供 T 应 商下达取 货指令使包 括空 器具 返 回的物流 停止 , 后续 恢复生产
四 连 互 生 CT E 载渔旦 LE U尺 二 S
在不同 的 P 链
表1 不同线路供应商取货便数及对应p 链数
. . 睡藏 差. . . . . 跪泣自. 口且四 到 . . 目画回 参曰
部件 几乎完全相同
生 产指示 在供 应商完 成排序 ( 分
类 ) 再 进 行 JI 引取 配送 T 对于 物 流距 离较远 (卫星工厂之外的 ,
使用, 则分割进度数> P 链数,
2加9 年再 次分 割进 度 数 二 ( 日 6 3 取货便数可为 l 2 3 4 6 9
12 13 18 36 ), P 链 数 二 , 29
参考
TPS
在广汽 丰 田物 流系统 的应 用及借 鉴 意义 (上 ) 中装车顺序图 ( 图
) 3 和本 文图 2 , 厂内运输链最多 可 容纳 16 个托 盘 , G M C 提 前 0 T 60 分钟 向供应商下 达进度需求 , 供 应 商 厂 内排 序 需要 1 分 钟 , 0 座椅 运 输 车 辆 在 供 应 商 装 车 一
内物流 , 图 2 是座椅 配送 的工 程
图
在库
供应商 没有空托 盘时 也会
至此容易 理解 有效
停止 生产
T G M C 卸 车需要 r 分钟 , 则运输 o
链 上 最 多 有 4 分钟 的缓 存 , 凯 0 美瑞 雅力 士 均 为 1 托 盘 / 台,
控制 器具发行数 量可 以有效控 制
库存,,
此案 例 的所 有观点 同样适用
l吕
l 9
,八
荐垂 稀泳 些 些
图3 P 链示意图
2t
刀
2王
24
一 __ _ 一 ~ _ 亡
有产 品 , 再把 顺序排 列方式转 变
物流技术与应用
L O G }S T } S & C
2013年第5期
M A T E R }A L H A N D L } G N
四
高 P 链 的 作用 和 目的主 要有 3 类 , 其一是 按生 产进度 供给 , 防
口连 载l韭 丛 里 LCURE S
T p S 在广汽丰田零部件厂 内物流系统中的应用
金形 乐德林2 冯鸿 金尸
正 如连 载
TP 在 广 汽丰 田 S
中
厂 内物流系统 统
物流 系统 的应 用及 借鉴意 义
的描述 , 零部 件厂 内物流 系统是
零 部 件 物 流 系统 的 重 要 组 成 部
{ 华浴 告 浴
止 厂内零部 件 的溢 出和 欠品 ; 其
二是 分割功 能 . 根 据分割链 实施
小批 量 的供 给 ; 其 三是 吸收厂外
和厂 内物 流的进 度差 (类似于 他 子 ), 确保下工序 可以及时引取 零部 件并减 少机材 数 集装箱 到
图4
P链
物流运送& 拆箱作业 区 pC棚
尸 棚 示意图 C
货 的 K D 进 口零 部件 物流 的运 作
.. ........ . 盯 的作业 南令
分 , 下 文将对 拉动 引取 的零 部件 厂 内物流 系统展 开详 细介绍
本 文描述 的厂 内物流 系统是 零部 件从 工厂受人 口运送 到生产 线 的物流 统称 , 图 l 为 厂内物 流
睑 收信箱 箱
S P S
A尺 ,丫 O .
现 受叮 调 ... 品 崛 入 口
链 并 没 有 追 求 绝 对 数 量 的最 少 由于 G M C 的厂 内物流 业务 T 化 , 而是 保 留了必要 的数量 , 其
最大 的好 处是运 输链本身 成 了吸
流程复 杂 , 与生产 线联动最 为紧 密, 整体企 划及 现场作业管 理工
作均 由 G M C 自行 管理 T
纳不平准 的 池子
于 没 有 实 际运 输 链 的平 场 地 物 流一 具有缓 冲功能 的流动机 能 ; 分类 的重要性 ; 空器具返 回的重
汉 兰 达 2 托 盘 /台 , 生产 节拍 为
1 6 秒 / 台时 , 则 运输链 上最 多托 盘数 =40 x 60巧1 x 6 5=47 托盘 / 运 输节拍 慢于生 产节拍 甚至
使用 的零部 件按一 定包装方 式一
想状态 的 P 链不是 货满 为安 , 正 常情况下 , 进 度链 及其后 若干 链 的零 部件 是齐全 的 , 多数 链都 处 于逐 渐到 货状 态 随着 GT M C 已
并取 回 , 所 以每车都 是一个 或几 个供应 商 的产 品, 不 同供应 商生
产 的产 品 品种 体 积各不 相 同, 取 货频 次也不相 同 前述 座椅 的顺 引物流 , 根 据
位置 T G M C 在建 厂 之初 单班 生产
45 台 / 天 , 1 小 时 /天 , 分 割 0 6 成 2 个 进度 并配 置 2 条 P 链 , 4 4
生产稳定 性和员工能 力提高, 将 P 链和进度数 提高为 3 2
引取 的批链 为空时如 果及 时安排
则每链对应 2 台套的零部件 (进 0 度正 常时 对 应 4 分钟 , 异 常 时 0 则 4 分钟 的说法不妥 ), 因为平 0 准化 的生 产计划 , 每 链摆放 的零
链的概念 P 链是在零部件送到
工厂 的检收 场之后存放 零部件 的 一个 临时 区域 这个 区域将检 收 后 的零部件按 一定 的规则码放 ,
成为 厂内物 流和厂外物 流的 临界
进 度看 板 ) 的指示顺 序 引取 各 P 链零 件 , 该链 引取 之后 为空 理
作业 , 到供 应商集 货时是将 该供 应商生 产 的 G M C 在一定周 期 内 T
时生产排 序不变 , 此 时可 以把必
要 的时间理解为 必要 的批 次 运
通 用小 标准件 外 , 其他 中小零件
输链上必 要数量 的收容数对 控制
采用 SPS 方式分 拣配套后 配送上
线
库存和对 应异常 非常重要 , 不 同 于传 统意 义上 的库存 , 笔者 形象
地将 之称 为 动机 能 从 图 2 和前述 可 以看 出空器 具 的返 回是 物 流 的重 要 组 成 部 分 , 空器具 的有 序返 还不但 对物 具有缓 冲功能 的流
J
~2 目 叫 一 曰 冲 返 .曰
嗯
呻照 照 卿 恩
侧日比口 口
, 甲吸 彝
李士
.
工 程图 , 包 括 : 从 检收场 到货确
认 开 始 , 从 P 链 和 P C 棚 搬人 ,
经 过分类 场零件分 拣再 到 出发链
的按需 配 送 上架 , SP 和顺 引 上 S 线 , 以及 空容器 返 回
过程
参考
TP 在 广汽 丰 田厂外 S
物流系统的应用 中继地的表述 ,
容易理解供应商取货 的频次是 1, 经过 中继地 后被调整成 2 , 可见 4 中继地 的好处 根据 上述前 提条 件画 出 P 链 捆 区 PC 棚 以及 SP 区 S
从 厂 外 物 流 的 描 述 可 以看 出 , 集 货是 以挂车 为物流单 元 的 成 水平排 列方 式 , 就 不难 理解 P 示意 图 (见 图 3 ) : 按 进 度 指示 安灯 (电子
解决
4 掣 2 抢翌 鹭 日 度示安 n 指 灯 飞
谁 翻阳 阳
3 二 门
生产量 : 48 0 台/天 1 La ne : 4 8 0/24 二 0 台 2
日
十 - 书侣 侣
. 匕) )
, 门
卸车之 后 的第 一项 工作一 定
是 暂放 , 暂放 的方 法要 对最终 的
释粗
垃
l1
t4
.
间
下爵 线
. ;
产 LP 零 件 ( 天津
离供 应 商 ) 及 K D 零件 到货 后进
物流技术与应用
L O G {S T IC S &
20 13年
M A T E R IA L H A N
撇 口
驴
图2
座椅顺引物流工程图
( 厂 内排序 ) 方式配送上线 (4 ) 总 装 除顺 引 顺建
空 时下一个 托盘处 于等待状 态 , 可 以解 读为 上工序在 必要 的时 间生产必要数量的产 品 从 图 2 可 以看 出, 厂 内运输
供 应商
输链
座椅运输 车辆
运
下
座椅装 配工 分别是上
要性 ; 场地
非空
时 , 物流停
工 序 , 对座 椅装配 工而言 , 把 厂 内运 输链末 端视做 上工序 , 座 椅 装配 工领取 座椅可 以解读为 下
个 别座椅运 输车辆 出现异 常时 , 运 输链上 的产 品可 以确保生 产的
不 间断 , 利 用生产 线停止 时 ( 班
臼
零 部 件 上 线 使 用 有 帮助 才 有 意
义 , 不必要 的搬运 就 是浪费 如
l5 矛 6
}下线
l了 .
总{ 装 一
图 2 所 示 , 每 个托 盘 的座 椅都是 按照 需求 的顺 序排 序 , 如果 把一
个托 盘看作 一个 时间段需要 的所
2 便/天 , jZ个 订单/便 2 4个订 单/天
甚 至天津
上海 等地 ) 的非顺 引