连杆零件的工艺规程设计说明书
连杆零件的工艺规程设计说明书.(DOC)
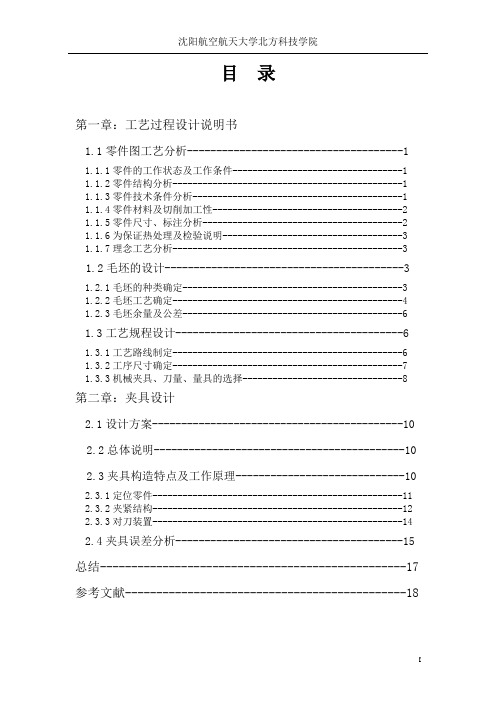
目录第一章:工艺过程设计说明书1.1零件图工艺分析-------------------------------------11.1.1零件的工作状态及工作条件----------------------------------11.1.2零件结构分析----------------------------------------------11.1.3零件技术条件分析------------------------------------------11.1.4零件材料及切削加工性--------------------------------------21.1.5零件尺寸、标注分析----------------------------------------21.1.6为保证热处理及检验说明------------------------------------31.1.7理念工艺分析----------------------------------------------3 1.2毛坯的设计-----------------------------------------31.2.1毛坯的种类确定--------------------------------------------31.2.2毛坯工艺确定----------------------------------------------41.2.3毛坯余量及公差--------------------------------------------6 1.3工艺规程设计---------------------------------------61.3.1工艺路线制定----------------------------------------------61.3.2工序尺寸确定----------------------------------------------71.3.3机械夹具、刀量、量具的选择--------------------------------8 第二章:夹具设计2.1设计方案-------------------------------------------10 2.2总体说明-------------------------------------------10 2.3夹具构造特点及工作原理-----------------------------102.3.1定位零件--------------------------------------------------11 2.3.2夹紧结构--------------------------------------------------12 2.3.3对刀装置--------------------------------------------------142.4夹具误差分析---------------------------------------15 总结-------------------------------------------------17 参考文献---------------------------------------------18摘要这次课程设计的题目是《连杆零件的工艺规程设计》,在这次课设中本说明书对连杆工艺规程及夹具规程进行说明。
连杆设计说明书机械毕业设计
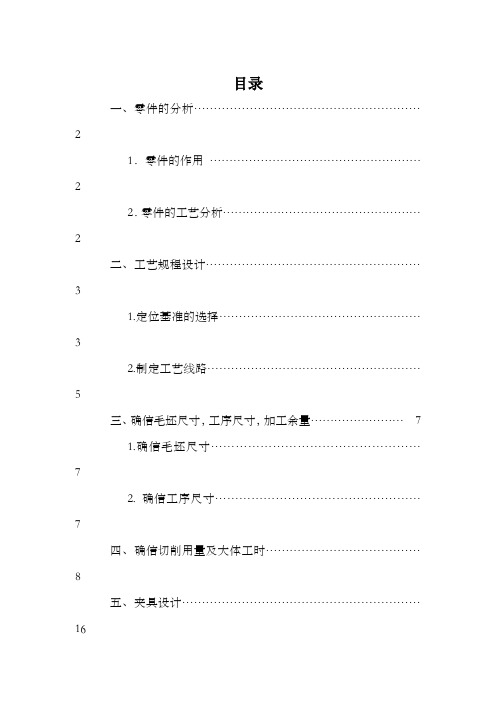
目录一、零件的分析 (2)1.零件的作用 (2)2.零件的工艺分析 (2)二、工艺规程设计 (3)1.定位基准的选择 (3)2.制定工艺线路 (5)三、确信毛坯尺寸,工序尺寸,加工余量 (7)1.确信毛坯尺寸 (7)2. 确信工序尺寸 (7)四、确信切削用量及大体工时 (8)五、夹具设计 (16)六.参考文献 (20)一、零件的分析1.零件的的作用连杆是要紧传力部件之一,其小头经活塞销与活塞连接,大头与曲轴连杆轴颈连接。
燃烧室内受紧缩的油气混合气体经点火燃烧后急剧膨胀,以专门大的压力压向活塞顶面,连杆那么将活塞所受的力传给曲轴,推动曲轴旋转。
在工作进程中,连杆要经受膨胀气体交变压力的作用和惯性力的作用,连杆除应具有足够的强度和刚度外,还应尽可能减少惯性力的作用。
连杆杆身一样都采纳从大头到小头慢慢变小的工字型截面形状。
连杆大、小头两头面对称散布在连杆中截面的双侧。
考虑到装夹、安放、搬运、要求,连杆大、小头的厚度相等(大体尺寸相同)。
2.连杆的工艺分析连杆上需进行机械加工的主要表面为:大、小头孔及其两头面等。
连杆总成的技术要求如下:1.为了使连杆大、小头运动副之间配合良好,大头孔的尺寸公差的品级取为IT6,表面粗糙度Ra不大于μm ;小头孔的尺寸公差品级约取为IT5(加工后再按0.0025mm距离分组),表面粗糙度Ra应不大于μm ;对它们的圆柱度也规定了严格的要求。
2.大、小头孔的中心距的尺寸公差品级应该不低于IT9。
大、小头孔中心线所在的公共平面为连杆平面,一样规定两孔轴线在连杆轴线平面内的平行度公差品级应不低于7级,在垂直于连杆轴线平面内的平行度公差品级应不低于8级。
3.连杆大头孔两头面对大头孔中心线的垂直度误差过大,将加重连杆大头两端面与曲轴连杆轴颈两头面之间的磨损,乃至引发烧伤,一样规定其垂直度公差品级应不低于9级。
4.连杆大、小头两头面间距离的大体尺寸相同,但其技术要求是不同的。
大头两头面间的尺寸公差品级为IT9 ,表面粗糙度Ra不大于μm ;小头两头面间的尺寸公差品级为IT12 ,表面粗糙度Ra不大于μm 。
连杆工艺工装设计说明书

连杆工艺工装设计说明书1. 引言本文档旨在介绍连杆工艺工装的设计及其使用说明。
连杆是一种用于连接和传递力量的机械零件,常用于发动机、压缩机、车辆等设备中。
连杆工艺工装的设计旨在提高生产效率、降低人工操作风险,并确保产品质量。
2. 工艺工装设计要求连杆工艺工装的设计应满足以下要求:•安全性:工装设计应保证操作人员的安全,避免意外发生。
•可靠性:工装设计应具备稳定、可靠的性能,确保连杆的加工质量。
•精确性:工装设计应符合产品的尺寸精度要求,确保产品的工装性能。
•可维护性:工装设计应方便维修和更换零部件,提高整体的可用性。
•生产效率:工装设计应优化生产流程,提高生产效率,降低成本。
•环保性:工装设计应考虑环保因素,减少对环境的影响。
3. 工装设计流程3.1 产品需求分析在工装设计之前,需要对连杆产品的要求进行分析,包括尺寸、材料、加工工艺等方面的要求。
3.2 工装设计概念确定根据产品需求分析的结果,确定工装设计的概念,包括工装的结构、功能和使用方式等。
3.3 工装设计详细设计在工装设计概念确定之后,进行详细设计。
包括确定工装的具体尺寸、材料、加工工艺和装配方式等。
3.4 工装制造与调试按照详细设计的要求,制造工装,并进行调试,确保工装的性能和质量符合要求。
3.5 工装使用与维护将工装投入使用,并进行维护。
包括定期检查、保养和更换零部件等。
4. 工装设计方案4.1 工装结构设计连杆工装的结构设计需要考虑以下因素: - 夹持方式:选择合适的夹持方式,确保连杆在加工过程中的稳定性。
- 支撑方式:选择合适的支撑方式,确保连杆在加工过程中的位置固定。
- 导向方式:选择合适的导向方式,确保加工刀具与连杆之间的对齐精度。
- 传递力量方式:选择合适的传递力量方式,确保加工过程中的力量传递效果。
4.2 工装加工工艺设计连杆工装的加工工艺设计需要考虑以下因素: - 加工工序:确定工装的加工工序,包括加工顺序和加工方法。
连杆零件的机械加工工艺规程和专用夹具设计
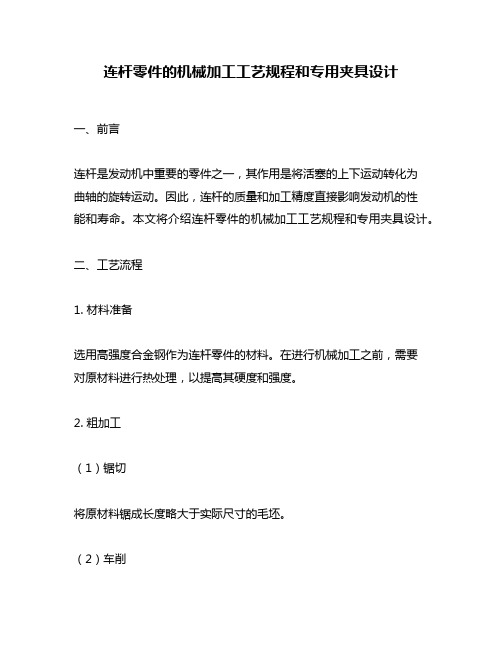
连杆零件的机械加工工艺规程和专用夹具设计一、前言连杆是发动机中重要的零件之一,其作用是将活塞的上下运动转化为曲轴的旋转运动。
因此,连杆的质量和加工精度直接影响发动机的性能和寿命。
本文将介绍连杆零件的机械加工工艺规程和专用夹具设计。
二、工艺流程1. 材料准备选用高强度合金钢作为连杆零件的材料。
在进行机械加工之前,需要对原材料进行热处理,以提高其硬度和强度。
2. 粗加工(1)锯切将原材料锯成长度略大于实际尺寸的毛坯。
(2)车削采用车床进行粗加工,先将毛坯两端面加工成平行面,然后进行外圆柱面、内孔等基本形状的车削。
(3)铣削采用立式铣床进行粗加工,主要是对连杆头部进行铣削,并开出油孔等结构。
3. 精密加工(1)磨削采用平面磨床和圆柱磨床对外圆柱面、内孔和连杆头等进行精密加工。
(2)钻孔采用钻床对油孔等细小结构进行加工。
(3)拉削采用拉床对轴向槽、键槽等进行加工。
4. 热处理将加工好的连杆零件进行热处理,以提高其硬度和强度。
通常采用淬火和回火的方式进行处理。
5. 组装将经过热处理的连杆零件组装到曲轴上,并进行调整,以确保其与其他零件的配合精度和运动平稳性。
三、专用夹具设计为了保证连杆零件在机械加工过程中的精度和稳定性,需要设计专用夹具。
下面介绍一种常见的夹具设计方案:1. 夹具整体结构该夹具主要由夹紧块、支撑块、定位块、压板等组成。
其中,夹紧块负责固定毛坯,支撑块负责支撑毛坯,在车削时起到了很好的辅助作用;定位块则是为了确保毛坯在夹具中的位置准确;压板则是为了防止毛坯在车削时发生移动。
2. 夹具夹紧方式该夹具采用机械夹紧的方式,通过螺旋压板来实现对毛坯的夹紧。
在进行车削等加工时,需要根据不同工序进行调整,以确保毛坯的稳定性和精度。
3. 夹具使用注意事项在使用该夹具时,需要注意以下几点:(1)夹具的各个部位需要经常清洗和润滑,以保证其正常运作。
(2)在进行车削等加工时,需要根据不同工序进行调整,并且要保证毛坯与夹具之间的接触面积充分。
零件加工工艺说明书
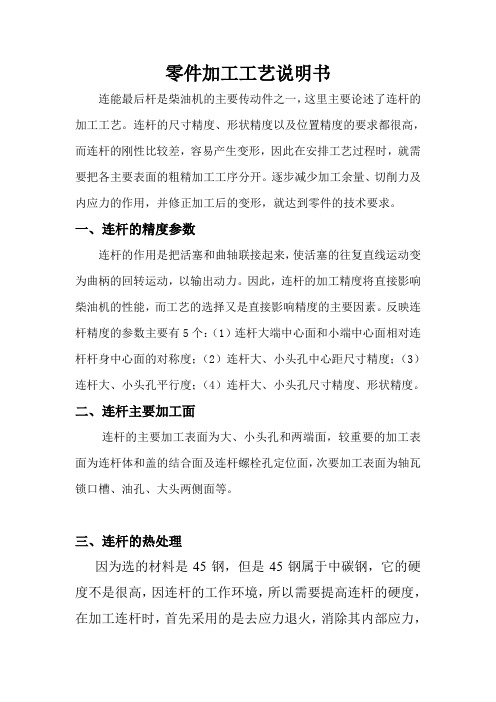
零件加工工艺说明书连能最后杆是柴油机的主要传动件之一,这里主要论述了连杆的加工工艺。
连杆的尺寸精度、形状精度以及位置精度的要求都很高,而连杆的刚性比较差,容易产生变形,因此在安排工艺过程时,就需要把各主要表面的粗精加工工序分开。
逐步减少加工余量、切削力及内应力的作用,并修正加工后的变形,就达到零件的技术要求。
一、连杆的精度参数连杆的作用是把活塞和曲轴联接起来,使活塞的往复直线运动变为曲柄的回转运动,以输出动力。
因此,连杆的加工精度将直接影响柴油机的性能,而工艺的选择又是直接影响精度的主要因素。
反映连杆精度的参数主要有5个:(1)连杆大端中心面和小端中心面相对连杆杆身中心面的对称度;(2)连杆大、小头孔中心距尺寸精度;(3)连杆大、小头孔平行度;(4)连杆大、小头孔尺寸精度、形状精度。
二、连杆主要加工面连杆的主要加工表面为大、小头孔和两端面,较重要的加工表面为连杆体和盖的结合面及连杆螺栓孔定位面,次要加工表面为轴瓦锁口槽、油孔、大头两侧面等。
三、连杆的热处理因为选的材料是45钢,但是45钢属于中碳钢,它的硬度不是很高,因连杆的工作环境,所以需要提高连杆的硬度,在加工连杆时,首先采用的是去应力退火,消除其内部应力,在精加工之前,采用调质处理,提高其硬度达到220—330HBW。
四、连杆精度的处理连杆的小头与活塞销连接,属于小间隙配合,配合精度不是很高,采用的是IT7级,所以小头孔的圆柱度精度为0.0025,内孔面的粗糙度为0.4;连杆大头与曲轴连接,属于小间隙配合,但是大孔在与曲轴一起转动时,所承受的力量比较大,所以大头孔的精度等级比较高,这里设定为IT7,孔的圆柱度精度为0.0012,空面的粗糙度为0.4;由于大小孔工作环境的受限制,大小受限,所以大小孔相对于中心线的对称度为0.02。
五、连杆的胀断处理由于连杆大头与曲轴的工作,连杆大头需要分开,为了使连杆大头断开后能够从新啮合上,保证其工作环境依然很好,这里采用的胀断。
连杆的机械加工工艺规程

下面以CA6102发动机为例,对其连杆和曲轴的加工工艺及发动机总成进行分析。
1.1 连杆加工工艺1.1.1 连杆的功用、结构特点及工作条件连杆是汽车发动机主要的传动构件之一,它是把作用于活塞顶部的膨胀气体压力传给曲轴,使活塞的往复直线运动变为曲轴的回转运动,以输出功率。
CA6102发动机连杆采用直剖式结构,它由从大头到小头逐步变小的工字形截面的连杆体及连杆盖、螺栓、螺母等组成。
由以上部分合在一起形成连杆的大、小头及杆身。
连杆大头孔套在曲轴的连杆轴颈上,与曲轴相连,内装有轴瓦。
为了便于安装,大头设计成两半,然后用连杆螺栓连接。
连杆小头与活塞销相连,小头压人耐磨的铜衬套,孔内设有油槽。
小头顶部有油孔,以便使曲轴转动时飞溅的润滑油能流到活塞销的表面上,起到润滑作用。
为了减少惯性力,连杆杆身部位的金属重量应当减少并且要有一定的刚度,所以杆身采用工字形断面。
连杆杆身部位是不加工的。
在毛坯制造时,杆身的一侧作出定位标记,作为加工及装配基准。
连杆在工作中主要承受着以下三种动载荷:①气缸内的燃烧压力(连杆受压);②活塞连杆组的往复运动惯性力(连杆受拉);③连杆高速摆动时产生的横向惯性力(连杆受弯曲应力);为了保证工作时连杆的一些危险点(螺栓、杆身或大端盖等)不发生断裂,将其设计成如图1.1.1所示的结构。
该结构不仅重量轻、刚度大,而且具有足够的疲劳强度和冲击韧性。
1.1.2 连杆材料及毛坯制造方法由于连杆在工作中承受多种急剧变化的动载荷,所以不仅要求其材料具有足够的疲劳强度及结构刚度,而且还要使其纵剖面的金属宏观组织纤维方向应沿着连杆中心线并与连杆外形相符,不得有扭曲、断裂、裂纹、疏松、气泡、分层、气孔和夹杂等缺陷。
连杆成品的金相显微组织应为均匀的细晶结构,不允许有片状铁素体。
CA6102发动机连杆材料采用 55#或 35MnVs ,经调质处理后,硬度为 226-271 HBS 。
采用整体模锻的加工方式,具有劳动生产率高、锻件质量好、材料利用率高、成本低等优点。
三孔连杆工艺课程设计说明书(模板)

三孔连杆的机械加工工艺及机床夹具设计说明书题目:三孔连杆(中批生产)工艺课程设计专业班级:农机(一)班学生姓名:张传东学号: 10129008指导教师:杨义2013年5月目录摘要1序言41零件的分析 5(标准零件图纸一张,AUTOCAD)1.1 零件的作用 5 1.2 零件的工艺分析52工艺规程设计7(毛坯合图一张,AUTOCAD或手绘图纸都可以)2.1 确定毛坯的制造形式 7 2.2 基面的选择7 2.3 制定工艺路线8 2.4 机械加工余量、工序尺寸及毛坯尺寸确定 9 2.5 确定切削余量及基本工时 10 (若干张零件工艺卡)结论19致谢20参考文献21机械制造工艺学课程设计任务书设计内容:1、产品零件图1张2、产品毛坯图1张3、机械产加工工艺过程卡片1份4、机械加工工序卡1张5、课程设计说明书1份序言机械制造工艺学课程设计是在我们学完了大学的全部基础课、技术基础及大部分专业课之后进行的。
这是我们在进行毕业设计之前对所学课程的一次深入的综合性的链接,也是一次理论联系实际的训练。
因此,它在我们的大学学习生活有十分重要的地位。
就我个人而言,我希望能通过这次课程设计对自己未来将从事的工作进行一次适应性训练,从中锻炼自己分析问题、解决问题的能力,为今后参加祖国的现代化建设打下一个良好的基础。
将设计图样转化成产品,离不开机械制造工艺与夹具,因而它是机械制造业的基础,是生产高科技产品的保障。
离开了它,就不能开发制造出先进的产品和保证产品质量,不能提高生产率、降低成本和缩短生产周期。
机械制造工艺技术是在人类生产实践中产生并不断发展的。
机械制造工艺的内容极其广泛,它包括零件的毛坯制造、机械加工及热处理和产品的装配等机械制造工艺课程设计是我们学完了大学的全部基础课、技术基础课以及大部分专业课之后进行的.这是我们在进行毕业设计之前对所学各课程的一次深入的综合性的总复习,也是一次理论联系实际的训练,因此,它在我们三年的大学生活中占有重要的地位。
连杆铸造工艺设计说明书

球墨铸铁连杆一、生产条件及技术要求1、生产性质大批量流水生产。
2、材质材质为QT400—15。
3、零件图4、主要技术要求力学性能:σb>400MPa;δ≥15%;130-180HBW。
金属组织:球化等级≤4级;石墨大小5.8级;φ(P)≤20%;ω(Fe3C)≤3%.二、造型、制芯1、造型采用气冲高压造型机,比压为0.7-0.9MPa;砂箱尺寸920mm*610mm*250mm,每型4件。
2、制芯设备采用单工位热芯盒制芯机。
三、熔炼工艺1、铁液的化学成分ω(C)=3.6%-3.9%;ω(Si) ≤3.0%;ω(Mn)<0.5%;ω(P) ≤0.07%;ω(S)<0.03%;ω(Mg)残=0.03%-0.05%;ω(Re)残=0.01%-0.03%。
2、球化剂稀土镁硅铁合金,加入量为铁液质量分数的1.5%-1.7%。
3、出炉温度 1420-1440℃。
4、浇注温度 1320-1350℃。
5、孕育剂 75Si-Fe合金孕育,加入量为包内铁液质量分数的0.3%-0.7%。
6、熔炼设备 10t无芯工频感应电炉熔炼原铁液;在1t铁液包中进行球化处理;转150Kg浇包进行浇注。
四、主要工艺参数1、加工余量 2.5mm。
2、收缩率 1%。
3、拔模斜度 1°。
4、砂型硬度砂型硬度大于40(C型硬度计)。
5、吃砂量吃砂量为30-60mm。
6、型砂性能湿压强度为0.12-0.14MPa,透气性≥100cm2/(Pa*s),紧实率为40%-48%(夏季),41%-47%(冬季)。
7、铸造圆角铸造圆角为R2。
五、铸造工艺方案1、浇注位置及分型面的选择根据便于起模的原则,分型面的选取如下图所示:2、铸件图的确定根据之铸件的分型面选择以及铸件加工余量和拔模斜度的确定,作出连杆铸件图如下所示:3、型芯设计根据铸件孔的基本尺寸及其加工余量,确定型芯的相关尺寸,相关数据参数如下图所示:4、工艺分析图的确定根据铸件分型面、加工余量、拔模斜度以及型芯的相关设计,作出铸件的工艺分析图如下所示:5、冒口设计根据球墨铸铁凝固特点,此件采用控制压力冒口进行补缩。
- 1、下载文档前请自行甄别文档内容的完整性,平台不提供额外的编辑、内容补充、找答案等附加服务。
- 2、"仅部分预览"的文档,不可在线预览部分如存在完整性等问题,可反馈申请退款(可完整预览的文档不适用该条件!)。
- 3、如文档侵犯您的权益,请联系客服反馈,我们会尽快为您处理(人工客服工作时间:9:00-18:30)。
目录第一章:工艺过程设计说明书1.1零件图工艺分析-------------------------------------11.1.1零件的工作状态及工作条件----------------------------------11.1.2零件结构分析----------------------------------------------11.1.3零件技术条件分析------------------------------------------11.1.4零件材料及切削加工性--------------------------------------21.1.5零件尺寸、标注分析----------------------------------------21.1.6为保证热处理及检验说明------------------------------------31.1.7理念工艺分析----------------------------------------------31.2毛坯的设计-----------------------------------------31.2.1毛坯的种类确定--------------------------------------------31.2.2毛坯工艺确定----------------------------------------------41.2.3毛坯余量及公差--------------------------------------------61.3工艺规程设计---------------------------------------61.3.1工艺路线制定----------------------------------------------61.3.2工序尺寸确定----------------------------------------------71.3.3机械夹具、刀量、量具的选择--------------------------------8第二章:夹具设计2.1设计方案-------------------------------------------102.2总体说明-------------------------------------------102.3夹具构造特点及工作原理-----------------------------102.3.1定位零件--------------------------------------------------112.3.2夹紧结构--------------------------------------------------122.3.3对刀装置--------------------------------------------------142.4夹具误差分析---------------------------------------15总结-------------------------------------------------17参考文献---------------------------------------------18摘要这次课程设计的题目是《连杆零件的工艺规程设计》,在这次课设中本说明书对连杆工艺规程及夹具规程进行说明。
1.工艺规程设计包括划分工艺路线和具体工序设计(1)划分工艺路线从零件进行工艺分析开始选择和设计毛坯,分析,加工精度,包括加工方法的选择,加工路线选择,定位基准选择,热处理辅助工序等。
(2)具体工序设计每一步都包含了夹具和基准的选择,各种常用机床设备和加工方法及其经济精度,提高表面质量的加工方法,工艺,与实际形结合,注意工艺过程的技术经济性。
2.家居规程设计中,需要了解各类机床夹具的特征及专用夹具色设计方法,分析夹具的定位方案,夹紧的方法,构造特点及工作原理。
在设计过程中保证加工精度并使加工精度稳定,缩短辅助时间。
提高劳动生产率,分析加工误差的组成。
通过此记录课程设计,了解理论和实际相结合的重要性,与此同时,使我们专业素养得到很大提高。
关键词:连杆,工艺规程,夹具设计第一章 工艺规程设计说明书1.1零件图工艺分析1.1.1零件的工作状态及工作条件在这次课程设计中我们所设计的零件为摩托车气缸内连杆,此零件作用于传递内燃机所产生动力.工作状态为连续的往复运动,工作状态是内燃机内部封闭状态工作。
1.1.2零件结构分析零件的结构可看作是两端圆柱形,中间为工字梁做连接,总形状可以看出零件的配合处是两个圆柱端,因此要求此件与配合件之间存在一定的配合要求。
1.1.3零件的技术分析 (1)零件表面精度从零件图的要求可知,此零件的工作表面的精度要求较高,上下表面间的尺寸为11.08±0.05两孔的直径分别为012.0005.22+Φ和007.0005.014+-Φ。
上下表面的粗糙度为R a0.8两孔的内侧粗糙度为Ra0.1。
(2)表面间的位置精度从零件图可知,此件的位置精度较高,上下表面的平行度0.03,大孔轴线对上下表面的垂直度为0.01。
两孔轴线平行度0.008。
大孔内侧对轴线的圆柱度0.003。
小孔内侧对轴线的圆柱度0.0025,大孔圆柱度为0.003,小孔圆柱度为0.0025。
(3)零件的其他技术要求零件表面要进行渗碳,渗碳层深度为0.095~1.071。
同时要求渗碳深度表面淬火,要求硬度≥HRC60。
毛坯的要求应满足以下几点:a.模锻件采用锤上模锻;b.未注明拔模角︒5;c.未注明圆角半径R2;d.沿分模面允许错移量0.5mm;e.磁力探伤检验;f.非渗碳面允许保留防护层;g.连杆重量为51±2g;h.表面缺陷层深度不超过加工层的一半;i.同边允许参与残余毛边0.8mm;j.本锻件进行ⅡC类检验;检验要求:毛坯内部无砂眼,无残余应力,无塑性变形。
1.1.4零件的材料及切削加工性此零件的材料为20CrMnTi,此材料的硬度较低所以加工性较低,所以加工性较好,可用一般的刀具加工,同时此材料的刚性较好。
1.1.5零件尺寸标注分析有零件图的分析可知,此零件的主要表面为两孔内侧表面及两轴线的尺寸。
同时上下表面也要求较高,所以在进行给定工序时,必须首先考虑重要工作表面的尺寸精度,位置精度与形状精度。
所以我们在加工时,工件的较高精度首先保证,其他可以接一般的要求进行。
1.1.6为保证热处理的检验说明此零件要求进行检验,在工件加工之后,发货之前进行ⅡC 类检验以保证加工要求,在加工过程中要进行中间检验,以保证后面工序的加工要求。
在工作加工后进行磁力探伤。
以保证加工零件的工作安全。
1.1.7零件的工艺分析从加工精度的角度来看,此零件的加工精度要求特别高,这就要求我们加工的设备,加工刀具以及工人的技术水平等都要有一定的高度。
从零件的设计要求来看,主要的要求为工件的上下表面的平行度。
两孔的轴线位置精度和孔轴线的要求,孔的圆柱度与圆度的要求,都是加工的难点。
我们必须采用相应的措施保证加工要求。
为了保证粗糙度的要求,必须选择适当的刀具与加工机床,为了保证位置精度,必须选择精度较高的夹具,以保证零件各处要求的位置关系,同时选择技术高的工人是保证加工精度的另一个重要因素。
1.2毛坯的设计1.2.1毛坯的种类确定从零件图可知,此零件毛坯要求为锤上模锻,此零件的毛坯外形简单。
只有凸台、凸肩,以及两孔,所以适用于模锻。
1.2.2毛坯的工艺要求(1)分模面确定为对称面,这要确定有利于毛坯的加工,同时以保证毛坯质量。
图1-1从本工件的加工工艺性与加工经济性来看,所选择的工艺路线为:a.加工方法的选择b.阶段的划分:根据加工的过程可以把加工分为四个阶段:①从毛坯的锻造到工件上下表面的加工。
②工件表面的孔的粗加工③工件表面的精加工④工件孔的精加工c. 工序基准的选择加工工序基准的选择如图所示,加工A面时用D面定位,加工D面时用A面定位。
加工孔时用A、B、C定位。
图1-2d. 热处理工序的安排根据零件的硬度要求,此工件的材料20CrMnTi,未能达到硬度要求HRC60,所以工件要进行热处理工序(即渗碳,淬火和回火)热处理应安排在精加工之前,从而使零件达到硬度要求。
e. 工艺路线总体分析从工艺路线的过程看,本工件上下表面是机械加工中的主要定位基准,应首先加工出两表面,可以采用铣削和磨削加工。
以保证加工表面能达到预定的加工要求,加工两表面之后进行孔加工,粗加工可采用扩孔和粗镗,半精加工可采用精镗,粗精加工可采用珩磨。
在中间检验之后要进行孔的渗碳处理以保证加工表面有一定的韧性和硬度,最后进行检验。
(2)圆角半径根据毛坯的加工要求,此毛坯的圆角度为R2,选择圆角是为了保证毛坯在加工时不易破坏 (3)拔模斜度此拔模的斜度按要求为︒5 (4)技术要求及说明毛坯的技术要求同1.1.3—(3) 1.2.3毛坯的余量和公差由此零件加工上下表面和两个孔,所以此毛坯的加工余量在上下表面有计算分析得加工余量:saia E E A如图所示:A=15-11.8=3.2Esa =1-(-0.05)=1.05 Eia =-1-0.05=-1.05sa ia E E A = 1.051.05-2.3+图1-31.3 工艺规程设计 1.3.1工艺规程的制定根据加工要求可以选择不同的加工方法。
下面可以达到设计精度要求几种工艺方案,用方框图,形式如图1-1所示。
1.3.2工序尺寸的确定如表1-1所示孔渗碳度计算:渗碳前工序尺寸14.0088.21+Φ 06.006.083.13+-Φ 渗碳层深度为0.6-0.9即3.006.0+Φ渗碳后工序尺寸012.005.22+Φ007.0005.014+-Φ 则渗碳层尺寸为sb ib E E BB=11.025+0.6-10.94=0.765 Es b=0.3+0.006=0.306 E ib=0+0-0.07=-0.07 则渗碳层深度为0.695-1.0711.3.3机床夹具、刀具、量具的选择粗精铣 设备 立式铣床 夹具 矩形电磁盘 量具 游标卡尺 刀具 圆柱铣刀刀具材料 硬质合金 YG8 p a =2.0mm精磨 设备 卧轴矩台平面磨床m7130k 夹具 矩形电磁盘 量具 外径千分尺 刀具 平行砂轮扩孔设备摇臂钻床23025夹具专用夹具量具内径千分尺刀具硬质合金扩孔钻镗孔设备坐标镗床 T4145夹具专用夹具量具内径千分尺刀具内孔镗刀细镗孔设备金刚石钻床M42513夹具专用夹具量具内径千分表刀具珩磨头第二章钻床夹具设计2.1设计方案由于该家具应用于孔的加工,所以要求该家具除可以保证孔本身的加工精度外,还要保证圆轴线间的中心距的位置精度。