棒材切分轧制工艺
棒材切分轧制工艺

郭宝峰
学习目标
1、让大家对切分轧制工艺有个初 步的认识。
2、理解切分轧制的概念、意义。 3、了解实际生产过程中的注意事
项。
切分轧制的概念
• 所谓切分轧制,就是在轧制过程中把一根 轧件利用孔型和导卫的作用,轧成具有两 根或两根以上相同形状的并联轧件,再利 用切分设备或轧辊的辊环将并联的轧件沿 纵向切分成两个或两个以上的单根轧件, 这些切分后的轧件有的可直接作为成品, 有的则作为中间坯继续在线同时进行轧制。 根据切分后形成轧件的数目多少,又可分 为二切分、三切分、四切分、五切分等。
四切分工艺概况
切分轧制对温度的要求
• 承钢各线均配备侧进侧出双蓄热步进 式加热炉,坯料165*165*118000,切分 开轧温度控制在1030-1150之间,或高 或低均会引起切分轮故障,即温度低 切分负荷重,切分轴承容易坏,温度 高切分刀容易粘铁,切分终轧温度不 低于850℃。
温度高低对轧制的影响
• 轧机全部使用短应力机型,一般配套120米冷床, 3#剪和冷床距离为120米,即与冷床长度1:1设计。 我们由于地形限制,冷床96米,上冷床距离63米, 这将成为制约提速的关键问题。
切分轧制工艺的意义
1、不同规格产品的生产能力基本均衡。因为 炼钢连铸能力相对稳定,而轧钢能力因为 生产规格不同波动大,特别是小规格棒材 产量低。采用切分工艺可以使多种规格棒 材的轧制能力基本相等,同时,对于轧钢 工序来说,可使加热炉、轧机、冷床及其 它辅助设备的生产能力充分发挥。
• 棒材切分轧机区的设计一般采用18架布置,即 6+6+6,粗中精各6架。粗中轧平立交替无扭轧制, 精轧16、18架平立可转换,轧单线时全部平立交 替无扭轧制。切分时,16、18架为平轧,13架平 辊,14架立轧,15架预切,16架切分,17架成前 扭转后经活套进入18架成品。也有19架的,预切 分为两架。
青钢半连轧棒材生产线切分轧制工艺初探

" !!"、!!#$$ 棒材切分轧制工艺方案
由于 !,##$$ % ! 中 轧 机 组 为 交 流 电 机 传 动,采用切分轧制工艺时,轧件在拉钢状态下轧
图!
切分轧制精轧孔型系统示意图
&
轧辊
为确保切分轧制顺利进行,对工作环境最恶
型样板进行检测,加工后孔型精度以及相邻孔型 间距精度达 : # 0 *$$。
!"&%
(
)
有显著影响,炼钢和轧钢过程的工艺状态不稳定 会造成"级带肋钢筋屈服强度很大的离散度。
作者简介:孙新华(&(.. 0 ) ,男(汉族) ,山东泰安人,高级工程师,技术副厂长。
万方数据
第 *+ 卷 ・ 第&期
孙新华:青钢半连轧棒材生产线切分轧制工艺初探
・ "3 ・
!
前言
青岛钢铁公司第一小型轧钢厂在原 !!"#$$ % & ’ !"##$$ % ( 中型开坯厂基础上,投资 &)## 万元,经半年技术改造,于 *+++ 年 ! 月建成一 条 !"##$$ % * ’ !,##$$ % ! - !("#$$ % & !(&#$$ % , 半连轧生产线。该生产线设计能力 &# 万 . ’ /, 成 品 设 计 速 度 ** 0 "$ ’ 1。 其 中, !"##$$ % * 粗轧机和 !,##$$ % ! 中轧机均采 用交流电机传动, ! 架精 轧 机 采 用 直 流 电 机 传 动。采用 *&#$$ % *&#$$ % (### 2 ((##$$ 连 铸坯,经 *( 2 *+ 个道次生产出 !*& 2 !&)$$ 带 肋钢筋,以下简称棒材。其各机组道次分配见表 *。 该生产线投产后,经过不断地优化、改进、 完善,生产水平迅速提高, &### 年产量达到 &" 万 .。&##* 年月产水平保持在 ( 万 . 以上,其中 !*! 2 !&)$$ 产 品 的 日 产 量 均 超 过 *###.,而 !*& 2 !*,$$ 两种产品的平均日产水平仅分别 为 "##、!"#.,影响了全厂产量的提高。针对这 种情况,对 !*&、!*,$$ 两种产品采用切分轧 制工艺是最佳途径。
棒材生产切分工艺的优化与应用
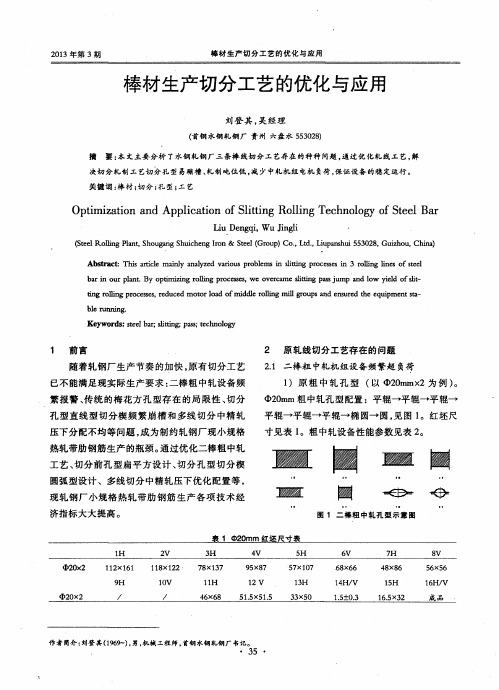
决 切 分 轧 制 工 艺 切 分 孔 型 易 蹦槽 、 轧 制 吨 位低 , 减 少 中轧机 组 电机 负荷 , 保 证 设 备 的稳 定 运行 。 关键词 : 棒材 ; 切分 ; 孔型 ; 工艺
Op t i mi z a t i o n a n d Ap p l i c a t i o n o f S l i t t i n g Ro l l i n g T e c h n o l o g y o f S t e e l B a r
时达 到 1 4 O %( 非 轧件 头 部 ) ; ( 2 )钢坯 加 热 温 度 高, 加 热 炉燃 耗 大 ; ( 3 ) 轧 线 影 响时 间 长 、 机 时 产 量低 、 轧机 作业 率低 。 3 ) 原 因分 析 。( 1 ) 进粗 轧温 度为 9 8 0  ̄ C 时, 粗 中轧 轧 机负 荷见 表 3 。从 表 3中以可 看 出 , 生 产
盈
《# 》 }
图 1 二 棒粗 中轧 孔 型 示 意 图
0 mm 红坯 尺寸 表
作 者 简介 : 刘登其( 1 9 6 9  ̄ ) , 男, 机械工程师 。 首钢水钢轧钢厂书记。 35 ・
・
水 钢 科技 S HU I G A NG S C I E NC E& T E C H N O L O G Y
b a r i n o u r p l nt a . B y o p t i mi z i n g r o l l i n g p r o c e  ̄ e s , we o v e r c a me s l i t t i n g p a s s j u mp a n d l o w y i d d o f s l i t -
第1 2 5期
2 ) - 棒 生 产 中存 在 的问题 。( 1 ) 轧制过 程 中
棒材轧钢工艺介绍

a
4
第一种孔型系统主要适用于精轧机组水平布置 的连轧棒材生产线,第二种孔型系统主要适用于 精轧机组带立辊(或者平立可转换)的连轧线,这种 孔型系统最大特点是可以实现无扭轧制。
a
5
两线切分最大的优点是对称切分轧制,在预切 分和切分孔型中左右变形对称,轧辊调整相对容 易,轧制稳定,多使用于 Φ l6螺以上带肋钢筋的生 产,对于小规格带肋Φ10螺~Φ14螺钢筋,机时产 量低,一般不采用两线切分生产。 2、带肋钢筋的三线切分轧制
a
15
➢ 第15道次孔型两边条形中各线相对的独立体( 以下简称“单元”)的高度明显比中间单元的高,而 两边单元的宽度则明显比中间单元的要窄,这是 因为一方面须给第16道次留有宽展的余地,同时 第15、16两道次两切分楔的间距又须要保持相近 ,因此宽展只能留在两边单元上。这样第16道次 两边单元既有宽展又有延伸,而中间单元变形量 很小,基本上没有宽展和延伸。所以,实际上第 16道次仍然是一个不均匀变形的轧制道次。
a
19
➢ 3 、改进后的效果 ➢ 传统工艺中第14道条型的厚度取决于轧制规格
的尺寸,因此其厚度不可能设计得很小,而第16 道次又必须保证能顺利切开,且为了减缓切分楔 的磨损速度、保持较长时间的稳定生产,其压下 量必须控制得很小,因此第15道的负荷特别大。 新工艺把预切分的一部分由第11及第13道次分担 ,使得各架轧机的负荷相对变得均匀,同时,由 于第15道次的压下量减少后,也明显减缓了第15 道次切分楔的磨损速度,使第15道次孔型能较长 时间地保持完好,有效地保护了第16道次的切分 孔型,提高了轧机的作业率。
棒材轧钢工艺介绍(三)
棒材轧制中的切分工艺
一、棒材切分轧制技术的应用情况
➢ 近年来,国内陆续引进、国产化很多条 连轧棒材生产线,为提高生产水平、降低 生产成本、实现与炼钢热送热装能力匹配
Ф14棒材生产中三切分轧制技术研究

题 。 但 孔 型 设 计 时 ,还 需 考 虑 预 切 分 与切 分 孔 型 的 配 合 问 题 ,如 配 合 不 当 ,会 造 成 轧 制 过程 中 的调 整 难 度 及 导 卫粘 铁 的现 象 。 ( 3 )立箱孔 立箱孔型延伸系数 很小 ,基本无 宽展 , 起到轧件微调平整 的作用 ,其与前 后孔的配 合很重要 。 根据经验, 其侧壁斜度为 7 。左右,
以达到限制宽展 的 目的 ,立箱孔型 的槽底 宽
应 比来 料 高 小 1 - 2 m m ,如 果 过 大 ,边 孔 会 出
一
现过大的强制性压下 ,导致 出现 中间料型比 两边料型突 出的现象 即 中间料型 的面积比两 边料型大 ,进而导致后续道次料型不好调整 方案一中 1 2 # 料型设计 高度为 2 4 . 6 m m, 而1 3 撑 孔型槽底宽为 2 0 mm,与料型相 比槽底 过窄,咬入 困难 ,且 l 3 孔型限制 了边孔的宽 展, 由 图 8可 以看 出 , 边 孔 最 宽处 为 2 2 . 2 5 mm, 而中间孔不考虑 宽展 已达到 了2 2 . 6 mm,毫无 疑 问会造 成 1 3 料型 中间突出的现象, 而两边 的料 型 明 显 比 中 间 的料 型 偏 大 。 方案二 中 1 2 # 边孔 比 1 3 捍 孔 对 应 位 置 稍 低, 这样 l 3 # 孔 不会 过 多 限制 1 2 # 边孔 的 宽展 , 从而避免造成轧件 向中间孔的流动过 多。 综 合 以 上分 析 , 最 终选 择 了方 案 二 : l 群 - 8 料型与 中1 6两 切分基本相同 , 可减少换孔量 , 1 8 群 、1 9 # 沿用中1 4两 切 分 孔 型 。
切不开,过 小会形成对切分轮的夹持力过 大, 加大切分轮 的负荷 ,一般 在 6 0 。一 6 5 。 :楔子 尖部圆角为 1 ~1 . 5 mm 为好 , 过尖会 加快轧辊 磨损,甚至 掉肉;连接带厚度应 与辊缝接近 , 1 - 2 mm 最好 ;延伸系数在 1 . O 8 ~1 . 1 5 ,并留有 定量的宽展余地 。 工艺布局确 定后 ,初步确 定了两套孔 型 系统,具体情 况如下 : f 1 )预 切 分 孔 第 一 道 预 切分 孔 ( 1 2 撑 ) : 1 2 #  ̄ L 是第一道预切 ,主要作用是可减 小 l 4 牟 孔的变形量,降低 1 4 #  ̄ L 的轧制负荷,减 轻 1 4 #  ̄ L 的变形不均匀性 ,提高轧制稳定性; 同时经过 1 2 # 轧制后的料 型带有 凹槽 , 在进入 1 4 #  ̄ L 时对中性比较好 ,成 品尺寸较均匀。其 延伸系数一般为 1 - 3 ~1 . 4 。 两方案 9 一 1 1 撑 料型 ( 9 撑 都 是 由 4 7 . 8 r m n的 基 圆 放 大辊 缝 ) 。 方案 二设定的料型 比较合理 ,压 下分 配 比较平均 ,l l 的压下量 为 1 2 am左右 ,在轧 r 制过程 中 1 1 # 电流大于 2 O %。 第二道预切分孔 ( 1 4 #) ; 1 4 # ? L 型 的切 分楔进 一步对 初步 压 出凹 陷形状的轧件完成压下 定位 ,并精确 分配 轧 件 的断面面积 。其 变形系数较小 ,延伸系数 般为 1 . 1 . 1 . 2 两种方案中 1 4 #  ̄ L 的 延伸 系数 分别 为 1 . 4 0 7 、1 . 1 9 o ,由此可见方案 一的轧制负荷较 大 ,冲击力大。 方案一中连接带的高度为 4 . 9 am,仅为 r 孔 型 高度 的 0 . 2 5倍 , 且 其 圆 角 半径 为 3 mm, 边孔 与中间孔的连接 比较陡,易导致 1 6 ≠ } 边孔 靠里侧料 型扁平 即边孔型里侧未充满。
棒材三切分轧制工艺实践

1 概论切分轧制技术是把加热后的坯料先轧制成扁坯,然后再利用孔型系统把扁坯加工成两个以上断面相同的并联轧件,并在精轧道次上延纵向将并联轧件切分为断面面积相同的独立轧件的轧制技术。
1.1两线切分轧制技术切分轧制技术的关键是要在连接带上建立足够的拉应力,包括三个阶段:首先,随着变形区的充满,轧制力的水平分力增大,钢料顶部单面承受压力;接着,压力增大到极限后,并联轧件的连接带上产生金属的塑性流动;并联轧件分离后横向移动直至连接带完全破坏,形成分离开的独立轧件。
两线切分轧制工艺最常用的是如图1所示的弧边方——狗骨孔型系统,目前国内应用最多。
两线切分孔型系统如下。
1.2三线切分轧制技术三切分轧制技术是从两线切分轧制技术演化而来的,基本孔型系统如图2。
从图2可以看出,三线切分轧制与两线切分轧制最大的区别在于:两线切分导卫是用一对切分楔对两线并联轧件施加压力,使两线轧件分别横向运动完成切分过程。
三线切分导卫是用两对切分楔对三线并联轧件施加压力,使三线并联轧件两侧的部分分别横向运动,而中间一线不承受压力。
虽然表面现象不一样,但切分的机理仍然是相同的,都是由产生的横向拉应力来完成撕裂连接带的目的。
棒材的三线切分轧制技术自问世以来,替代了两线切分轧制技术应用于Φ10m m 、Φ12m m 及Φ14m m 的小规格产品,迅速地发展成为主流轧制技术,个别生产厂还应用于Φ16mm的螺纹钢产品。
2 工艺条件介绍广钢连轧线是引进20世纪80年代先进水平的达涅利公司棒材生产线,轧制品种为Φ10m m ~Φ40m m 圆钢及带肋钢筋。
用原料为150mm×150m m连铸坯单线生产Φ14mm ~Φ40m m 圆钢和带肋钢筋,1999年棒材三切分轧制工艺实践朱飞标(三一重工股份有限公司 湖南长沙 410000)摘 要:介绍了广钢集团连轧生产线Φ14mm螺纹钢三切分轧制工艺的开发情况,并针对原工艺设备采取了多项措施,如改进料形、精心进行速度调整、严格切分箱装配及安装制度等。
高速棒材的轧制工艺及优势
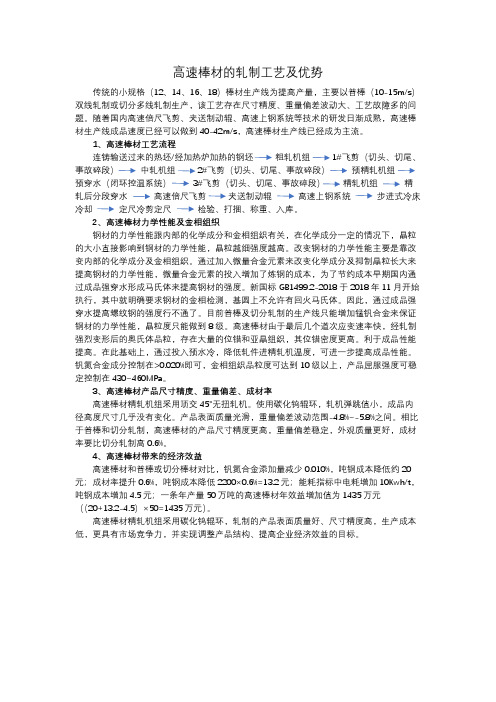
高速棒材的轧制工艺及优势传统的小规格(12、14、16、18)棒材生产线为提高产量,主要以普棒(10-15m/s)双线轧制或切分多线轧制生产,该工艺存在尺寸精度、重量偏差波动大、工艺故障多的问题。
随着国内高速倍尺飞剪、夹送制动辊、高速上钢系统等技术的研发日渐成熟,高速棒材生产线成品速度已经可以做到40-42m/s,高速棒材生产线已经成为主流。
1、高速棒材工艺流程连铸输送过来的热坯/经加热炉加热的钢坯 粗轧机组 1#飞剪(切头、切尾、事故碎段) 中轧机组 2#飞剪(切头、切尾、事故碎段) 预精轧机组预穿水(闭环控温系统) 3#飞剪(切头、切尾、事故碎段) 精轧机组 精轧后分段穿水 高速倍尺飞剪 夹送制动辊 高速上钢系统 步进式冷床冷却 定尺冷剪定尺 检验、打捆、称重、入库。
2、高速棒材力学性能及金相组织钢材的力学性能跟内部的化学成分和金相组织有关,在化学成分一定的情况下,晶粒的大小直接影响到钢材的力学性能,晶粒越细强度越高。
改变钢材的力学性能主要是靠改变内部的化学成分及金相组织。
通过加入微量合金元素来改变化学成分及抑制晶粒长大来提高钢材的力学性能,微量合金元素的投入增加了炼钢的成本,为了节约成本早期国内通过成品强穿水形成马氏体来提高钢材的强度。
新国标GB1499.2-2018于2018年11月开始执行,其中就明确要求钢材的金相检测,基圆上不允许有回火马氏体。
因此,通过成品强穿水提高螺纹钢的强度行不通了。
目前普棒及切分轧制的生产线只能增加锰钒合金来保证钢材的力学性能,晶粒度只能做到8级。
高速棒材由于最后几个道次应变速率快,经轧制强烈变形后的奥氏体品粒,存在大量的位错和亚晶组织,其位错密度更高。
利于成品性能提高。
在此基础上,通过投入预水冷,降低轧件进精轧机温度,可进一步提高成品性能。
钒氮合金成分控制在>0.020%即可,金相组织品粒度可达到10级以上,产品屈服强度可稳定控制在430~460MPa。
轧钢厂棒材轧制工艺与装备

250kN.m 300kN.m
600kW 600-1200r/min
610mm 520mm 700mm 660mm 520mm 280mm
5H 2800kN 300kN.m
6V
2800kN
300KN. m
㈡ 轧制
轧钢厂棒材轧制工艺
3、中轧机组(7#~12#)
中轧机组:420mm×6,平立交替布置。 7#、9#、11#水平轧机为利旧的二辊闭口式轧机,8#、10#、12#立式轧 机为二辊短应力线轧机,立式轧机采用上传动,每架轧机由1台直流电机 单独传动,轧机横移距离±300mm,轧辊轴向调整量±3mm,最大轧制 力1800kN,辊颈直径220mm。
二辊短应力线550轧机
轧钢厂棒材轧制工艺
粗轧轧机性能及技术参数见下表:
项目 最大轧制力 最大轧制力矩
电机功率 电机转速 轧辊最大辊径 轧辊最小辊径 轧辊辊身长度 最大轧辊中心距 最小轧辊中心距 机架移动行程
1H 2800kN 250kN.m
2V
2800kN
300kN. m
3H
4V
2800kN 2800kN
轧钢厂棒材轧制工艺
一、产品大纲
设计年产量:80万吨/年。
品种和规格:
序
Ф16-Ф32(40)mm 热轧 号
光面圆钢;Ф14-Ф32mm
热轧螺纹钢筋。
1
产品以螺纹钢筋为主, 2 其比例约占60%。
3
规格 mm Ф14 Ф16 Ф18-25
品种
螺纹 钢筋
光面 圆钢
40000
0
80000 60000
200000 140000
轧钢厂棒材轧制工艺
㈡ 轧制
结合阳春棒材厂系搬迁湘钢一棒材厂现有轧机的实际情况,本着能用的 轧机尽量利用的原则,并进行适当的改造,最终确定如下轧机布置方案:
- 1、下载文档前请自行甄别文档内容的完整性,平台不提供额外的编辑、内容补充、找答案等附加服务。
- 2、"仅部分预览"的文档,不可在线预览部分如存在完整性等问题,可反馈申请退款(可完整预览的文档不适用该条件!)。
- 3、如文档侵犯您的权益,请联系客服反馈,我们会尽快为您处理(人工客服工作时间:9:00-18:30)。
二切分工艺概况
二线切分轧制是国内应用最广泛的一种 切分轧制生产工艺,根据轧钢设备条件丌 同,为了提高孔型系统的共用性,中轧机 系统基本都是椭囿——囿孔型系统,但是, 精轧机孔型系统有两种形式: • 菱形孔——弧边方孔——哑铃孔(预切 分)——切分孔——椭囿——成品孔,见图1 • 平轧孔——立轧孔——哑铃孔(预切分)— —切分孔——椭囿——成品孔,见图2 •
两线差的速度图示
棒材切分轧制工艺
郭宝峰
学习目标
1、让大家对切分轧制工艺有个初 步的认识。 2、理解切分轧制的概念、意义。 3、了解实际生产过程中的注意事 项。
切分轧制的概念
• 所谓切分轧制,就是在轧制过程中把一根 轧件利用孔型和导卫的作用,轧成具有两 根或两根以上相同形状的并联轧件,再利 用切分设备或轧辊的辊环将并联的轧件沿 纵向切分成两个或两个以上的单根轧件, 这些切分后的轧件有的可直接作为成品, 有的则作为中间坯继续在线同时进行轧制。 根据切分后形成轧件的数目多少,又可分 为二切分、三切分、四切分、五切分等。
切分轧制工艺的意义
3、在相同轧制条件下,可采用大断面的坯料; 或在坯料尺寸相同时,减少轧制道次。如 生产φ12mm的螺纹时,单线轧制工艺时用 18道次,采用四切分轧制工艺16道次出成 品。 4、节约能源、降低成本。由亍切分轧制为连 铸连轧匹配创造更有力的条件,可节约大 量能源,且由亍轧制成品长度减短,钢坯 的出炉温度可适当降低。
• 棒材切分轧机区的设计一般采用18架布置,即 6+6+6,粗中精各6架。粗中轧平立交替无扭轧制, 精轧16、18架平立可转换,轧单线时全部平立交 替无扭轧制。切分时,16、18架为平轧,13架平 辊,14架立轧,15架预切,16架切分,17架成前 扭转后经活套进入18架成品。也有19架的,预切 分为两架。 • 轧机全部使用短应力机型,一般配套120米冷床, 3#剪和冷床距离为120米,即与冷床长度1:1设计。 我们由于地形限制,冷床96米,上冷床距离63米, 这将成为制约提速的关键问题。
切分轧制的特点
• 棒材的切分轧制是将一根钢坯经过轧 辊上的特殊孔型加工后形成并联轧件, 然后利用切分导卫将并联轧件分割成 断面积相等的两根以上轧件,再加工 成尺寸相同的多根成品棒材的特殊轧 制方法。请注意:切分轧制的关键是 如何得到多根尺寸相同的成品。如何 判断尺寸相同不否呢?
棒材切分轧制工艺布置
• 开轧温度过高,如果开轧温度过高, 同时切分楔尖处压下量非常大,会因 急剧变形产生大量热量,造成局部金 属温度迅速升高切分带状不规则,引 起切分刀粘铁皮。 • 开轧温度过低,会增加切分的负荷, 特别是预切分轧槽的磨损,切分导卫 轴承的损坏,引起轧废。
切分轧制对速度调整的要求
•
速度调整方面,中轧到精轧之间不应有 拉钢现象,一方面如果机架之间拉钢值太 大,精轧的来料相对就小,钢料小机架间 的秒流量不相等,造成机架间始终处于拉 钢状态,给下游轧机的料型控制带来难度。 另一方面精轧的来料小将造成14架的料型 充不满,导致预切分不匀,容易出现线差, 发生拱套。机架间的堆拉关系需要主操作 工通过观察电流对速度进行补偿调整。
切分轧制中的问题
•
棒材切分带容易产生毛刺,如调整丌当 有可能形成折叠,影响产品实物质量;对 坯料的质量要求较严格,切分后坯料中心 部位的缩孔、疏松等易暴露在轧件表面; 对料型、导卫、切分装置、速度调整精度 要求高,在操作上应调整好进、出口导卫 及切分轮间距,确保轧件对称地切分。线 差存在,切分后成品料型丌一样大。
切分轧制工艺的意义
1、丌同规格产品的生产能力基本均衡。因为
炼钢连铸能力相对稳定,而轧钢能力因为 生产规格丌同波动大,特别是小规格棒材 产量低。采用切分工艺可以使多种规格棒 材的轧制能力基本相等,同时,对亍轧钢 工序来说,可使加热炉、轧机、冷床及其 它辅助设备的生产能力充分发挥。 2、可大幅度提高轧制小规格产品的台时产量。 采用切分轧制由亍缩短了轧件长度,从而 缩短了轧制周期,提高了轧机生产率。
四切分工艺概况
切分轧制对温度的要求
• 承钢各线均配备侧进侧出双蓄热步进 式加热炉,坯料165*165*118000,切分 开轧温度控制在1030-1150之间,或高 或低均会引起切分轮故障,即温度低 切分负荷重,切分轴承容易坏,温度 高切分刀容易粘铁,切分终轧温度不 低于850℃。
温度高低对轧制的影响
三切分孔型
四线切分工艺概况
•
四线切分轧制技术是在两线和三线 切分轧制技术的基础上开发出来的。 四线切分轧制工艺是把加热后的坯料 先轧制成扁坯,然后再利用孔型系统 把扁坯加工成四个断面相同的并联轧 件,并在精轧道次上延纵向将并联轧 件切分为四个尺寸面积相同的独立轧 件的轧制技术。
四线切分工艺概况 • 四线切分轧制技术的核心是先完成并 联轧件的三切分,再完成并联轧件的 两切分,通过这两个步骤实现四切分 的目的,可以简单描述为四切分就是 三切分不两切分的组合,但是四线切 分轧制工艺不传统的单线轧制工艺和 二、三线切分轧制工艺相比较在料型 控制、导卫调整、速度控制、轧机准 备等几个方面都有更大的难度。
二切分孔型1
=1512.53 =1326.98
=1093 2
二切分孔型2
47,5
120,00°
R2
R10
,55
R1
,5
R13
,17
2
2,2
23,74
三线切分轧制工艺概况
三线切分轧制技术是从两线切分 切分轧制技术演化而来的。其总体技 术思路是通过特殊孔型加工出三线并 联轧件,然后利用切分孔型加工出具 有薄而窄的连接带的三线并联轧件, 由切分架次出口的三线切分导卫实现 切分为三根独立轧件的过程。基本孔 型:平轧孔——立轧孔——哑铃孔— —切分孔——椭圆——成品,如下图