棒材切分轧制导卫系统的应用与改进
南钢棒材生产线切分轧制的运用

南钢 棒 材 生产 线 切分 轧 制 的运 用
项 幼 阳 Leabharlann ( 南昌钢铁有限责任公司 , 江西 南 昌 30 1 ) 30 2
摘
要 : 介绍了南钢棒材厂生产 ql In中In @1 mn J2l , 4 l l l m, 6 l螺纹钢材二线切分轧制工艺, 切分孔型
及导卫装嚣的运 用 , 以及切分轧制提高 产量 , 降低成本的效果。
关
键
词 : 棒 材 ; 分 轧制 ; 切 运用 文献标 识码 : B
中图分 类号 : T 3 5 1 G 3 .9
Ap iat fSp itng Ro ln t t r Ro ln n n Na t e pl c i o lti li g a he Ba l g Li e i nse l on i
设 计年 产量 :0万 t 4 。 最 大成 品速 度 :8m s J / 。
2 2 工艺流 程 .
整体年设计能力4 万 t 0 , 全部采用国产化设备 ,0 1 20 年2 1 1 月 83 投产。现主要生产 J m, l m 2m 4 m,
J 6 mm, 2 0 mm , 2 2 mm, 2 5 mm, 2 8 mm , 3 2
・ 5・ 3
3 切分轧制工艺分析 与开发应用
3 1 切 分轧制 .
带连接成一体的两根 轧件 。泼轧件在离开倒数第
三机 架进入 切分 轮导 卫 装 置 后 , 即被 其 中 的两 个 切 分轮 “ 撕开 ” 为两个 单独 的 圆轧 件 也 就是 说 , 切 在
切分轧制是在热轧过程中, 用特殊 的轧辊孔型 和导卫装置或其它切分设备将轧件沿纵 向剖分成 2 条或多条轧件, 从而将延伸系数减小到原来的I2 /, l3 变单条轧制为多条轧制的生产工艺。实现小 / 等, 轧机吃大坯料, 减少轧制道次和轧制时间 , 显著提高 轧机产量 , 降低能耗和成本 。目前螺纹钢切分轧制 主要用 的是特 殊 的轧 辊孑 型加 切分 轮装 黄 。孔型 主 L
棒材切分导卫原理
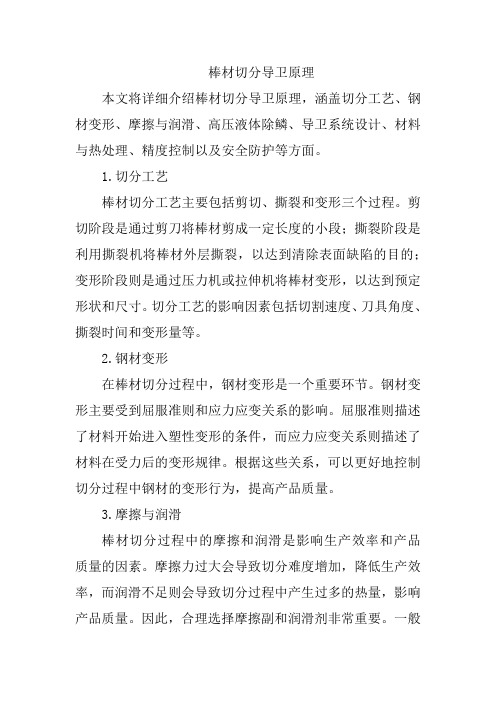
棒材切分导卫原理本文将详细介绍棒材切分导卫原理,涵盖切分工艺、钢材变形、摩擦与润滑、高压液体除鳞、导卫系统设计、材料与热处理、精度控制以及安全防护等方面。
1.切分工艺棒材切分工艺主要包括剪切、撕裂和变形三个过程。
剪切阶段是通过剪刀将棒材剪成一定长度的小段;撕裂阶段是利用撕裂机将棒材外层撕裂,以达到清除表面缺陷的目的;变形阶段则是通过压力机或拉伸机将棒材变形,以达到预定形状和尺寸。
切分工艺的影响因素包括切割速度、刀具角度、撕裂时间和变形量等。
2.钢材变形在棒材切分过程中,钢材变形是一个重要环节。
钢材变形主要受到屈服准则和应力应变关系的影响。
屈服准则描述了材料开始进入塑性变形的条件,而应力应变关系则描述了材料在受力后的变形规律。
根据这些关系,可以更好地控制切分过程中钢材的变形行为,提高产品质量。
3.摩擦与润滑棒材切分过程中的摩擦和润滑是影响生产效率和产品质量的因素。
摩擦力过大会导致切分难度增加,降低生产效率,而润滑不足则会导致切分过程中产生过多的热量,影响产品质量。
因此,合理选择摩擦副和润滑剂非常重要。
一般情况下,选择具有高摩擦系数和良好润滑性能的摩擦副和润滑剂是最佳选择。
4.高压液体除鳞在棒材切分过程中,高压液体除鳞是一种有效的表面处理方法。
通过使用高压水、乳化液或其他液体对棒材表面进行冲洗,可以清除表面的鳞片、氧化皮和其他污染物。
高压液体除鳞不仅可以提高产品的表面质量,还有助于提高刀具的寿命。
在选择清洗剂时,需要考虑到清洗剂的化学性质和压力范围,以确保其能够有效地清除污染物,同时不会对棒材和设备造成损害。
此外,为了确保除鳞效果和生产效率,需要选择合适的密封材料,以保证清洗剂和棒材表面之间的密封性。
5.导卫系统设计棒材切分导卫系统是保证切分过程顺利进行的关键。
导卫系统设计需要考虑的因素包括导卫形式、材料和热处理工艺。
导卫形式主要有滑动式、滚动式和浮动式。
选择合适的导卫形式需要考虑棒材的直径、长度、表面质量以及切分过程中的摩擦和变形等因素。
棒材生产切分工艺的优化与应用
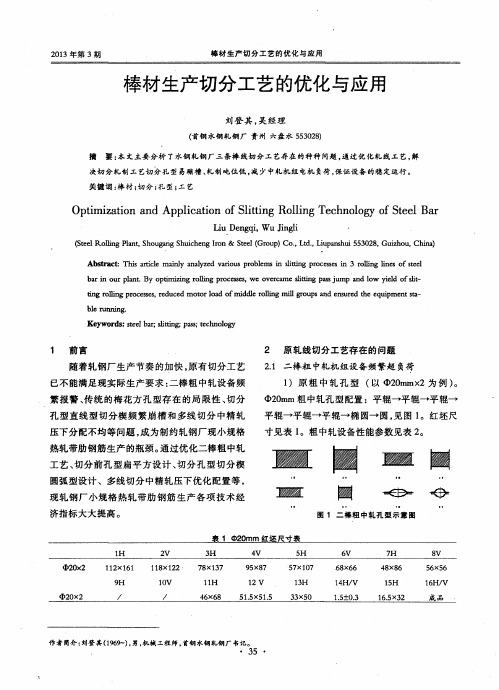
决 切 分 轧 制 工 艺 切 分 孔 型 易 蹦槽 、 轧 制 吨 位低 , 减 少 中轧机 组 电机 负荷 , 保 证 设 备 的稳 定 运行 。 关键词 : 棒材 ; 切分 ; 孔型 ; 工艺
Op t i mi z a t i o n a n d Ap p l i c a t i o n o f S l i t t i n g Ro l l i n g T e c h n o l o g y o f S t e e l B a r
时达 到 1 4 O %( 非 轧件 头 部 ) ; ( 2 )钢坯 加 热 温 度 高, 加 热 炉燃 耗 大 ; ( 3 ) 轧 线 影 响时 间 长 、 机 时 产 量低 、 轧机 作业 率低 。 3 ) 原 因分 析 。( 1 ) 进粗 轧温 度为 9 8 0  ̄ C 时, 粗 中轧 轧 机负 荷见 表 3 。从 表 3中以可 看 出 , 生 产
盈
《# 》 }
图 1 二 棒粗 中轧 孔 型 示 意 图
0 mm 红坯 尺寸 表
作 者 简介 : 刘登其( 1 9 6 9  ̄ ) , 男, 机械工程师 。 首钢水钢轧钢厂书记。 35 ・
・
水 钢 科技 S HU I G A NG S C I E NC E& T E C H N O L O G Y
b a r i n o u r p l nt a . B y o p t i mi z i n g r o l l i n g p r o c e  ̄ e s , we o v e r c a me s l i t t i n g p a s s j u mp a n d l o w y i d d o f s l i t -
第1 2 5期
2 ) - 棒 生 产 中存 在 的问题 。( 1 ) 轧制过 程 中
棒材车间自动分钢优化与改进

棒材车间自动分钢优化与改进摘要:自动数支器作为轧钢棒材线生产过程质量控制关键装备,其数支精度直接影响到轧区料型调整和成品尺寸控制,数支错误将给生产过程控制造成干扰,同时精整对多支少支的处理造成作业量增加。
新疆天山钢铁巴州有限公司轧钢厂通过自动分钢系统优化,提升了工作效率,改善了数支准确率和成品包外观质量。
关键词:自动;分钢;优化;效率;质量引言轧钢产线生产能力其根本决定于设备能力。
棒材产线生产,倍尺材在经冷床收集冷却后由定尺剪剪切为定尺材,通过输送辊道和移钢小车输送至收集平台,实现数支分钢和收集。
新疆天山钢铁巴州有限公司轧钢厂棒材产线,精整区域工艺设计配置120米冷床,1.2米输送辊道,850吨冷剪,1号、2号两个收集平台,收集平台设置4段链传输棒把,自动数支分钢系统完成数支和分把。
该产线设计产能60万吨/年,现因工艺优化改进产能达100万吨/年,在工艺优化的同时精整区域匹配了1.5米输送辊道和1200吨定尺剪以承载效率提升后的产能负荷,收集平台区域设备保留原装备能力。
1生产过程现状产能提升后定尺剪剪切的棒把增大,定尺材经输送辊道和移钢小车输送至收集平台后易形成交叉和堆叠,平台链条输送过程定尺材不能拉开间距,钢材重叠缠绕情况不能改善,自动数支分钢系统易出现错误,数支准确率偏低,尤其是在12-16小规格生产过程数支错误率达到10%,每班班需人工数支整改异常支数成品包,造成职工低效劳动工作量增加。
分钢后棒把呈倾斜转态运输至落料收集装置,下落过程两端不同步,收集后的成品包外观呈缠绕扭曲状态,流入市场后严重影响品牌形象。
钢材的扎制一般分为两种:一种是普通扎制,在扎制后按照每捆的实际重量出厂计价;另一种为负公差扎制,在扎制后按照理论计算重量出厂计价。
在两种扎制制度中,由于负公差扎制的理论重量比实际重量大,如φ12 螺纹钢的理论重量比实际重量高出5%以上[1]。
2问题原因分析2.1 收集品台效率低导致前端高效生产的定尺材不能及时数支分把收集打包,前段倍尺材过度冗余,造成冷剪剪切棒把增大,棒把越大收集和数支分钢效果越差,造成恶性循环。
棒材轧制扭转辊的技术改造及运用效果

棒材轧制扭转辊的技术改造及运用效果赵永生杨家勇徐国玉摘要:本文对信钢棒材线粗、中轧的扭转导卫进行了技术改造,从当初的滑动导卫到滚动导卫直到现在的翻钢辊的投入使用进行了综合分析论证,在实际运行中通过轧制实践证明显示出良好的运行效果。
关键词:扭转导卫、翻钢辊、翻钢角度、生产实践一、前言信钢棒材线自02年投产以来,随着生产节奏的加快及操作员水平的提高,粗、中轧扭转导卫已越来越不适应快速连续的生产节奏,由于扭转导卫工艺事故多,调整困难且停机更换时间长,严重地制约着产能的提高,轧钢厂针对现有状况,先后对K16、K14、K12的出口扭转辊进行技术改造,新上线的翻钢辊克服了原扭转导卫的缺陷,不仅扭转到位、过钢量大为提高,而且事故次数大为减少,从而使轧机的日历作业率也得以大幅度的提升。
二、工艺技术分析1、棒材线粗、中轧工艺流程钢坯从加热炉出来后,经过粗轧K17~K13这5座轧机的连轧出了K13后进入粗轧机后辊道,通过中轧机前辊道进入中轧K12,经过中轧四架轧机后进精轧直至出成品上冷床。
由以上轧制工艺流程及各机架的料形尺寸要求可以得出:为了保证轧件在轧制过程中内部结构的均匀性以及为获得各机架的规定料形,在对于平辊轧制过程中必须在偶数辊道上设置相应的扭转机构。
4、出口扭转导卫的结构及工作原理以K14流动导卫为例,其结构简图如下:其工作原理是:轧件从K14出来后(其料形为77×135,横截面为椭圆),经过K14出口导卫时受到上、下扭转辊的支撑作用,且产生了一个力偶,使其发生相向旋转,由此而产生了扭转,到下一架轧机K13咬入之时,轧件头部正好扭转了90℃5、扭转辊的完善过程投产之初,粗、中轧的扭转导卫采用的是夹板式滑动扭转,在实际运行过程中,暴露出磨损严重,扭转不到位(或过多)及产品表面质量缺陷严重等缺陷,于是从2003年开始先后将粗、中轧扭转导卫换装了导辊能随着轧件转动的滚动导卫,该种导卫减少了滑动导卫易易造成的各类缺陷,产品质量也相应地得到了保证,但同时又产生了导辊因受钢温变化、轧件冲击、冷却水等因素的影响而易破碎的问题,除了易诱发工艺事故,增加了换导卫的次数、加大了轧钢工的劳动强度,更因为频繁更换更换造成停机时间长。
导卫说明
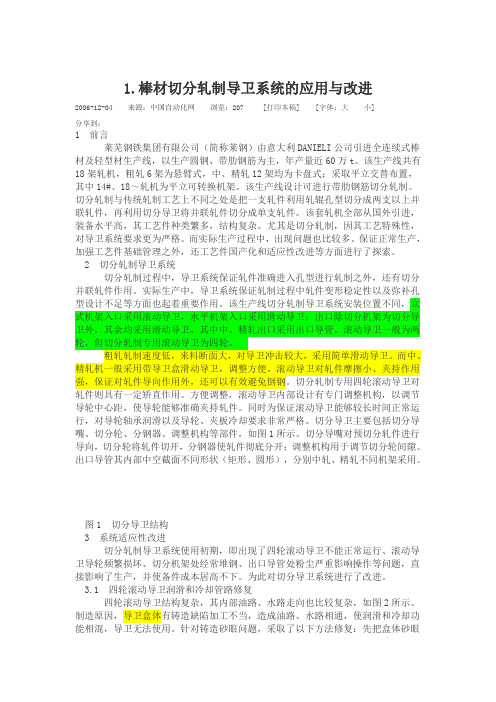
1.棒材切分轧制导卫系统的应用与改进2006-12-04 来源:中国自动化网浏览:207 [打印本稿] [字体:大小]分享到:1 前言莱芜钢铁集团有限公司(简称莱钢)由意大利DANIELI公司引进全连续式棒材及轻型材生产线,以生产圆钢、带肋钢筋为主,年产量近60万t。
该生产线共有18架轧机,粗轧6架为悬臂式,中、精轧12架均为卡盘式;采取平立交替布置,其中14#、18~轧机为平立可转换机架。
该生产线设计可进行带肋钢筋切分轧制。
切分轧制与传统轧制工艺上不同之处是把一支轧件利用轧辊孔型切分成两支以上并联轧件,再利用切分导卫将并联轧件切分成单支轧件。
该套轧机全部从国外引进,装备水平高,其工艺件种类繁多,结构复杂。
尤其是切分轧制,因其工艺特殊性,对导卫系统要求更为严格。
而实际生产过程中,出现问题也比较多。
保证正常生产,加强工艺件基础管理之外,还工艺件国产化和适应性改进等方面进行了探索。
2 切分轧制导卫系统切分轧制过程中,导卫系统保证轧件准确进入孔型进行轧制之外,还有切分并联轧件作用。
实际生产中,导卫系统保证轧制过程中轧件变形稳定性以及弥补孔型设计不足等方面也起着重要作用。
该生产线切分轧制导卫系统安装位置不同,立式机架入口采用滚动导卫,水平机架入口采用滑动导卫;出口除切分机架为切分导卫外,其余均采用滑动导卫,其中中、精轧出口采用出口导管。
滚动导卫一般为两轮,但切分轧制专用滚动导卫为四轮。
粗轧轧制速度低,来料断面大,对导卫冲击较大,采用简单滑动导卫。
而中、精轧机一般采用带导卫盒滑动导卫,调整方便。
滚动导卫对轧件摩擦小、夹持作用强,保证对轧件导向作用外,还可以有效避免倒钢。
切分轧制专用四轮滚动导卫对轧件则具有一定矫直作用。
方便调整,滚动导卫内部设计有专门调整机构,以调节导轮中心距,使导轮能够准确夹持轧件。
同时为保证滚动导卫能够较长时间正常运行,对导轮轴承润滑以及导轮、夹板冷却要求非常严格。
切分导卫主要包括切分导嘴、切分轮、分钢器、调整机构等部件,如图1所示。
棒材2号飞剪切头轧废的分析与改进

棒材2号飞剪切头轧废的分析与改进摘要:本文主要针对棒材2号飞剪在切头后,钢头不能正常掉落到下方废料收集装置的原因进行分析。
对剪前热检光栅HMD信号异常、飞剪剪刃导致轧件切头切不开的问题进行改进,着重对剪后导板装置进行了改造,有效的解决了飞剪在切头过程中将钢头带入下游轧机或导槽,阻碍轧件的正常运行,使得下支轧件无法正常轧制造成轧废的问题。
实践证明,采用改造后的剪后导槽生产运行稳定,2号飞剪切头稳定掉落入下方的废料收集装置,降低了轧废,提高了作业率,有效降低了生产成本。
关键词:飞剪、切头1前言二棒生产线为仿一棒Danieli棒材生产线建造,设备全国产化,由18机架平立布置的短应力线轧机组成,分为粗、中、精轧机组,以6+6+6的数量化分,全线轧机成平立交替式布置,其中,精轧机组的16、18架轧机为平立可转换轧机。
轧件在1~10架轧机之间采用微张力轧制技术,10~18架轧机之间采用活套无张力轧制。
装机总容量为31224KW。
一直以165×165mm方坯作为主要原料,设计规格为螺纹钢Φ10-Φ50mm。
目前生产线主要采用切分轧制的生产工艺,主要轧制规格为Ф10-Ф22mm螺纹钢筋。
2生产中存在的问题及原因分析2.1 2号飞剪结构及功能2号飞剪安装在中轧、精轧之间,为回转式飞剪。
其剪切系统由剪前导槽、剪体、剪后导槽、气缸带动的翻板、溜槽等组成。
最大剪切面积2901mm2,剪切速度2.0~9.6米/秒之间。
设计的主要功能为进行棒材的切头、切尾以及出现轧废等事故的碎断。
2.2 2号飞剪切头2号剪切头功能主要是对轧件头部降温较快产生的黑头以及不均匀变形造成的缺陷进行切除,避免切分不均匀造成的轧废。
在切头功能时,热检HMD检测到轧件时,即刻启动计数器记录轧机编码器的脉冲,按照轧辊直径,计算轧件运行过的距离及速度,同时根据剪刃位置及热检到剪切点的距离L,确定启动飞剪的时刻,如果轧件头部到达预定位置,PLC即通过驱动电机运行,启动飞剪按一定的速度曲线完成剪切,剪切完成后,开始制动,并使飞剪复位到一固定位置,准备下一次的剪切[1]。
Φ14棒材生产中三切分轧制技术研究

Φ14棒材生产中三切分轧制技术研究摘要:本文叙述了棒材生产中φ14螺纹钢三切分的工艺选择、调试时出现的问题、改进方案及效果。
关键词:螺纹钢三切分工艺方案1、前言切分轧制是在轧机上利用特殊的轧辊孔型和导卫或者其他切分装置,将原来的一根坯料纵向切成两根以上的轧件,进而轧制多根成品或中间坯的轧制工艺。
采用切分轧制技术可缩短轧制节奏,提高机时产量,显著提高生产效率,降低能耗和成本。
目前切分轧制技术已发展到五切分轧制,且两线切分轧制技术和三线切分轧制技术作为成熟技术已经普遍应用在小规格螺纹钢的生产中。
本文所述棒材厂从2005年开始逐步应用切分轧制技术,现已成功开发了φ14、φ16、φ18螺纹钢二切分、φ12螺纹钢三切分轧制技术。
2010年,为了实现147万吨的年产量目标,棒材厂决定充分发挥切分技术的产能优势,在ф12螺纹钢三切分的基础上实施ф14螺纹钢的三切分轧制。
2、设备配置情况车间的工艺布置为粗轧7架平轧闭口轧机、中轧为平立交替的6架两辊闭口轧机、精轧为平立交替6架预应力轧机。
、3、工艺方案的选择3.1 工艺布局的确定在φ12螺纹三切工艺和φ14螺纹两切分工艺的经验基础上,对一道预切与两道预切的方案进行了比较:如采用一道预切,则预切分孔(k4)的压下和延伸比较大,轧制负荷大、轧制不稳定,且其切分楔处的压下系数远大于槽底的压下系数,造成切分楔处磨损严重;来料进预切分孔时的对中性差,进而导致预切料型进切分孔时不均匀,这样3支成品之间的尺寸不均匀,负差也不易控制。
采用两道预切,可减小k4孔(第二道预切)的变形量,降低k4孔的轧制负荷,减轻其变形不均匀性,提高轧制稳定性;同时带有凹陷部位的来料进k4孔时,容易对中,对轧辊切分楔的冲击较小,成品尺寸较均匀;由于k4变形系数小,故改变k4的压下量对轧件的断面面积影响较小,降低了成品尺寸随k4料型变化而变化的敏感性,提高了轧制的稳定性及料型调整的方便性和精确性。
3.2 孔型设计切分工艺的孔型设计中预切分和切分孔的设计尤为重要,其次是立箱孔型,这几道次的孔型设计,关系到切分轧制是否能成功。
- 1、下载文档前请自行甄别文档内容的完整性,平台不提供额外的编辑、内容补充、找答案等附加服务。
- 2、"仅部分预览"的文档,不可在线预览部分如存在完整性等问题,可反馈申请退款(可完整预览的文档不适用该条件!)。
- 3、如文档侵犯您的权益,请联系客服反馈,我们会尽快为您处理(人工客服工作时间:9:00-18:30)。
棒材切分轧制导卫系统的应用与改进
2006-7-12 11:39:18未知来源供稿
1 前言
莱芜钢铁集团有限公司(简称莱钢)由意大利DANIELI公司引进的全连续式棒材及轻型材生产线,以生产圆钢、带肋钢筋为主,年产量近60万t。
该生产线共有18架轧机,粗轧6架为悬臂式,中、精轧12架均为卡盘式;采取平立交替布置,其中14#、18~轧机为平立可转换机架。
该生产线设计可进行带肋钢筋切分轧制。
切分轧制与传统轧制在工艺上的不同之处是把一支轧件利用轧辊孔型切分成两支以上的并联轧件,再利用切分导卫将并联轧件切分成单支轧件。
该套轧机全部从国外引进,装备水平高,其工艺件种类繁多,结构复杂。
尤其是切分轧制,因其工艺的特殊性,对导卫系统的要求更为严格。
而在实际生产过程中,出现的问题也比较多。
为了保证正常生产,除了加强工艺件的基础管理之外,还在工艺件国产化和适应性改进等方面进行了探索。
2 切分轧制导卫系统
在切分轧制过程中,导卫系统除了保证轧件准确地进入孔型进行轧制之外,还有切分并联轧件的作用。
在实际生产中,导卫系统在保证轧制过程中轧件变形的稳定性以及弥补孔型设计的不足等方面也起着重要作用。
该生产线切分轧制的导卫系统根据安装位置不同,立式机架入口采用滚动导卫,水平机架入口采用滑动导卫;出口除切分机架为切分导卫外,其余均采用滑动导卫,其中中、精轧出口采用出口导管。
滚动导卫一般为两轮,但切分轧制的专用滚动导卫为四轮。
粗轧轧制速度低,来料断面大,对导卫的冲击较大,采用简单的滑动导卫。
而中、精轧机一般采用带导卫盒的滑动导卫,调整方便。
滚动导卫对轧件摩擦小、夹持作用强,除了保证对轧件的导向作用外,还可以有效地避免倒钢。
切分轧制专用的四轮滚动导卫对轧件则具有一定的矫直作用。
为了方便调整,滚动导卫内部设计有专门的调整机构,以调节导轮的中心距,使导轮能够准确地夹持轧件。
同时为保证滚动导卫能够较长时间正常运行,对导轮轴承的润滑以及导轮、夹板的冷却要求非常严格。
切分导卫主要包括切分导嘴、切分轮、分
钢器、调整机构等部件,如图1所示。
切分导嘴对预切分轧件进行导向,切分轮将轧件切开,分钢器使轧件彻底分开;调整机构用于调节切分轮间隙。
出口导管根据其内部中空截面的不同形状(矩形、圆形),分别在中轧、精轧的不同机架采用。
[img]20067121137199832.gif[/img]
图1 切分导卫结构
3 系统的适应性改进
切分轧制导卫系统在使用初期,即出现了四轮滚动导卫不能正常运行、滚动导卫导轮频繁损坏、切分机架处经常堆钢、出口导管处粉尘严重影响操作等问题,直接影响了生产,并使备件成本居高不下。
为此对切分导卫系统进行了改进。
3.1 四轮滚动导卫润滑和冷却管路的修复
四轮滚动导卫结构复杂,其内部油路、水路的走向也比较复杂,如图2所示。
由于制造原因,导卫盒体有铸造缺陷并且加工不当,造成油路、水路相通,使润滑和冷却功能相混,导卫无法使用。
针对铸造砂眼问题,采取了以下方法修复:先把盒体砂眼处镗孔,然后镶套,将油路、水路隔开;同时,采取钻孔镶入销子的方法对其它水路与油路相通处进行修复。
[img]200671211372872025.gif[/img]
图2 四轮滚动导卫油、水路结构
3.2 轴承防尘盖的设计加工
原设计中,滚动导卫的轴承多数不带密封。
在轧制过程中,导轮直接夹持高温轧件进行高速旋转,一方面使润滑脂很快流失,另一方面氧化铁皮、冷却水等侵入轴承内部,使滚动体产生滑动摩擦,产热大而烧坏轴承,进而影响了导轮的使用寿命。
经详细分析导轮、轴承的工作状态并考虑轴承外圈的尺寸,设计出三种防尘盖用于滚动导卫。
防尘盖外径小于轴承外圈外径1mm,内径略大于导轮轴直径。
在导轮旋转过程中,防尘盖外沿压在轴承外圈上,随导轮一起旋转,既能封住轴承内部润滑脂不向外溢出,保证润滑效果;又能防止外部氧化铁皮等杂物落入轴承内部。
3.3 切分导卫的改进
针对切分轧制时切分导卫频繁粘钢进而造成堆钢的问题,进行了分析,认为是由于切分导嘴设计不合理造成的。
原设计两片切分导嘴之间留给红钢通过的空间偏小,切分导嘴分料棱与红钢接触过于紧密。
而红钢塑性好,表面摩擦系数大,冷却水又不充足,经过一段时间后,摩擦脱落物逐渐积累,发生粘钢,进而堆钢。
为此,重新设计了切分导嘴,将分料棱改为圆弧过渡,增大过钢空间。
在切分导嘴上开出冷却水路,强制冷却导嘴。
改造实施后,切分导嘴粘钢现象大大减少。
针对随后出现的切分轮严重粘钢的问题,通过改造切分轮压紧碟簧和加强维护,减少了过钢时切分轮的弹跳。
3.4 水封器的设计加工
轧制过程中,车间内弥漫着大量的粉尘,直接影响对红钢运行状态的观察,同时影响环境卫生、危害职工身体健康。
粉尘主要集中在轧制区,特别是轧机出口导管处。
分析认为是由于轧制力大和轧制温度高,大量粉末状氧化铁皮弥散形成的。
原设计未考虑除尘装置,各机架后也没有足够的安装空间。
为解决此问题,利用一定压力的轧机冷却水在出口导管处形成水帘,吸收粉尘,粉尘随水排入地沟进入沉淀池沉淀,即“水封除尘”。
如图3所示,针对圆导管,设计了一种分离式水封器。
对于出口半管,利用其壁厚空间,直接在侧壁上打通主水路和喷水孔,实现水封除尘。
[img]200671211375157320.gif[/img]
图3 水封器主体示意图
根据现场生产的实际情况,从熟悉导卫结构入手,进行针对性分析并迅速解决问题,取得了事半功倍的效果。
同时,通过对导卫系统的适应性改进,使工艺件的使用效果最大限度地处于受控范围内,大大降低了备件消耗,有效地保证了正常生产的需要。