数控车床工作台二维运动伺服进给系统设计
数控车床工作台二维运动伺服进给系统设计

数控车床工作台二维运动伺服进给系统设计摘要:数控车床在制造业中起着至关重要的作用。
为了提高生产效率和产品质量,设计一个稳定可靠、精确灵活的二维运动伺服进给系统尤为重要。
本文将针对数控车床工作台的二维运动伺服进给系统进行设计,包括运动控制算法、驱动器选型、传感器选择等方面。
1.引言数控车床是一种以电子技术、计算机技术和车床技术为基础的现代化机床。
它通过运动控制系统实现工作台的运动,可以实现复杂的加工工艺。
二维运动伺服进给系统是数控车床的核心部件之一2.运动控制算法运动控制算法是二维运动伺服进给系统的核心技术之一、常用的运动控制算法包括PID控制算法、自适应控制算法等。
PID控制算法是一种经典的,应用广泛的控制算法,它根据测量值与期望值的差异计算出控制量,并对系统进行修正。
自适应控制算法则是根据系统的参数变化自动地调整控制参数。
在设计二维运动伺服进给系统时需要根据实际情况选择合适的控制算法。
3.驱动器选型驱动器是实现工作台运动的关键部件,它将控制信号转换为电力信号,驱动电机工作。
在选择驱动器时需要考虑工作台的负载情况、速度要求和精度要求等因素。
常用的驱动器有直流伺服驱动器、交流伺服驱动器和步进驱动器等。
在设计二维运动伺服进给系统时需要根据实际情况选择合适的驱动器。
4.传感器选择传感器可以实现对工作台位置、速度和负载等参数的测量,是二维运动伺服进给系统的重要组成部分。
根据需要可以选择位置传感器、速度传感器和负载传感器等。
常用的位置传感器有编码器、激光干涉仪等,速度传感器有霍尔传感器、光电传感器等,负载传感器有压力传感器、力传感器等。
在设计二维运动伺服进给系统时需要根据实际需求选择合适的传感器。
5.结论设计一个稳定可靠、精确灵活的二维运动伺服进给系统对于提高数控车床的加工精度、提高生产效率具有重要意义。
本文针对数控车床工作台的二维运动伺服进给系统进行了详细的设计,包括运动控制算法、驱动器选型、传感器选择等方面。
数控车床伺服进给系统设计
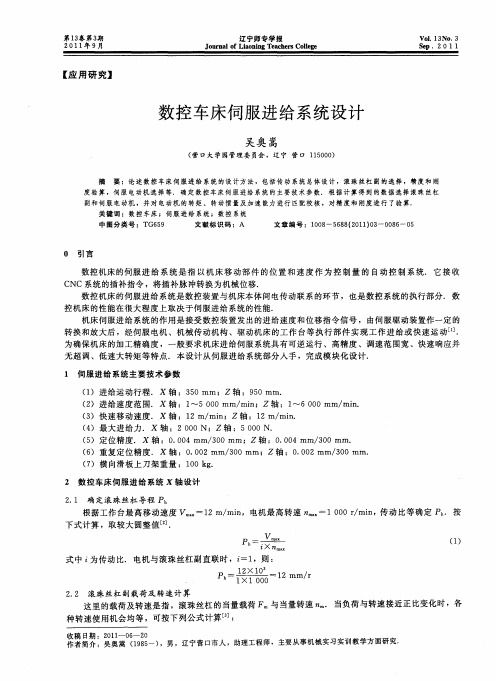
2 2 滚珠丝 杠副载 荷及转 速计 算 . 这里 的载荷及转 速是 指 ,滚珠丝 杠 的当量载荷 F 与 当量转 速 . 当负 荷与转 速接 近正 比变 化时 ,各 种转 速使 用机会均 等 ,可按下 列公 式计算 :
作 fr0嵩-5 , ,. 口人 助 工师 主 从机 实 实 教 方 研 誓 期 昊-60) 宁 市 ,理 程 ,要 事 械 习训 学 面 究 jC 2 9- 男 f 营 ,1 8 f :奥。 2 t  ̄ 11 日 吴 ( 矶买.毅力饼 头 罕 圆咒
F一 = F进 拾+ F i
() 4
则 Fr o ==20 0 . —2o 4 8N.故 F - 0 +4 8 o .  ̄
'’ :
一13 8N 3
2 2Ph
堡 二 堡 ! 一 坚± 二
”
() 5
则 n 一
- 2 8r mi. 0 / n
吴奥 嵩
数 控 车 床 伺 服 进 给 系统设 计
8 7
F:
m
±
3
() 2
假设 刀架 重量 1 0k ,溜板 重量 2 g 0 g Ok ,电机 重量 1 0k 0 g
F = g i
・
() 3
式 中 ,为滚动 摩擦 系数 ,取 , . 0 ,则 F i . 0 ×( 0 +2 ) 0 . . =0 0 4 =O 0 4 i 0 0 ×1 =4 8N
1 伺 服进给 系统主 要技术 参数
( )进 给运动行 程. X 轴 :3 0mm;Z轴 :9 0mm. 1 5 5 ( )进 给速度 范围. X 轴 :1 0 2 ~50 0mm/ n mi;Z轴 :1 0 ~60 0 mm/ n mi. ( )快 速移动 速度. X 轴 :1 mi ;Z轴 :1 mi. 3 2m/ n 2m/ n () 最大进 给力.X 轴 :20 0N;Z轴 :50 0N. 4 0 0 ()定 位精度 .X 轴 :0 0 4 rm/ 0 5 .0 a 3 0mm;Z轴 :0 0 4rm/ 0 . 0 a 3 0mm. () 重复定位 精度 .X 轴 :0 0 2mm/ 0 6 . 0 3 0mm;z轴 :0 0 2mm/ 0 .0 3 0mm. ( )横 向滑板 上刀 架重 量 :1 0k . 7 0 g 2 数控 车床伺服 进给 系统 x 轴 设计 2 1 确定 滚珠丝杠 导程 P . h
数控车床进给系统设计

数控车床进给系统设计一、进给系统的结构设计1.可靠性高:进给系统的关键零部件应采用优质的材料和加工工艺,以保证系统的稳定性和长寿命。
2.刚性好:进给系统的结构应具备足够的刚度,以保证在高速切削和大负载的工况下,机床能够保持稳定运行。
3.灵活性强:设计时应考虑到不同工件的加工要求,进给系统应能够快速调整和变换,以满足不同工件的加工需求。
二、进给系统的控制方法设计1.PTP控制方式:即点对点控制方式,根据工件形状和切削要求设计程序,实现工件形状的控制和切削路径的规划。
2.直线插补控制方式:通过数学模型进行直线切削路径的插补计算,实现工件形状的控制和切削路径的规划。
3.圆弧插补控制方式:通过数学模型进行圆弧切削路径的插补计算,实现工件形状的控制和切削路径的规划。
三、进给系统的传动方式设计传统数控车床进给系统的传动方式有液压传动和蜗杆传动两种,在设计进给系统时需要选择合适的传动方式,以满足不同加工工况的需求。
1.液压传动:液压传动以其可适应性强、能源利用率高等优点,在高负载和高速切削的工况下表现出较好的性能。
2.蜗杆传动:蜗杆传动以其结构简单、体积小、传动精度高等优点,在精密加工和高速加工的场合得到广泛应用。
四、进给系统的反馈装置设计进给系统的反馈装置是保证机床加工精度的重要组成部分,主要分为位置反馈和力反馈两种。
设计反馈装置时需要考虑以下几个因素:1.精度要求:根据机床加工的精度要求选择合适的反馈装置,以保证加工精度的稳定性。
2.反馈方式:根据加工工况选择合适的反馈方式,如光电编码器、脉冲等。
3.反馈信号的处理:对反馈信号进行合理的滤波和放大处理,以保证控制系统的稳定性和精度。
总之,数控车床进给系统的设计直接影响机床的加工精度和工作效率。
在设计进给系统时应考虑到结构、控制方法、传动方式和反馈装置等方面的因素,以满足不同加工要求。
同时,还需要对系统进行可靠性和稳定性分析,以确保数控车床的长期稳定运行。
数控车床工作台二维运动伺服进给系统设计
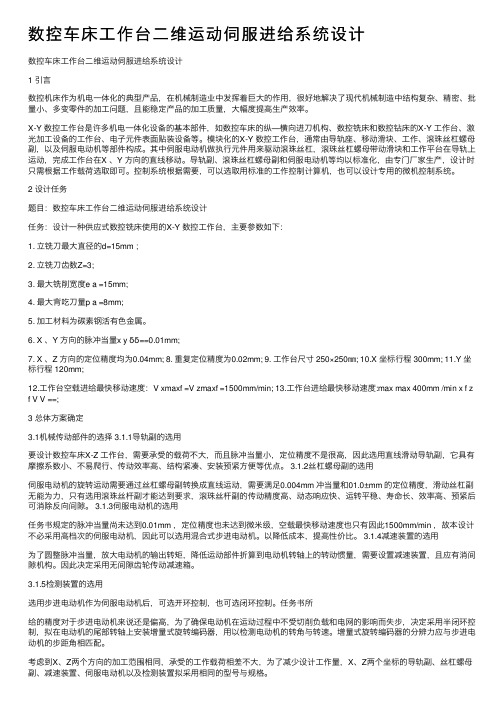
数控车床⼯作台⼆维运动伺服进给系统设计数控车床⼯作台⼆维运动伺服进给系统设计1 引⾔数控机床作为机电⼀体化的典型产品,在机械制造业中发挥着巨⼤的作⽤,很好地解决了现代机械制造中结构复杂、精密、批量⼩、多变零件的加⼯问题,且能稳定产品的加⼯质量,⼤幅度提⾼⽣产效率。
X-Y 数控⼯作台是许多机电⼀体化设备的基本部件,如数控车床的纵—横向进⼑机构、数控铣床和数控钻床的X-Y ⼯作台、激光加⼯设备的⼯作台、电⼦元件表⾯贴装设备等。
模块化的X-Y 数控⼯作台,通常由导轨座、移动滑块、⼯作、滚珠丝杠螺母副,以及伺服电动机等部件构成。
其中伺服电动机做执⾏元件⽤来驱动滚珠丝杠,滚珠丝杠螺母带动滑块和⼯作平台在导轨上运动,完成⼯作台在X 、Y ⽅向的直线移动。
导轨副、滚珠丝杠螺母副和伺服电动机等均以标准化,由专门⼚家⽣产,设计时只需根据⼯作载荷选取即可。
控制系统根据需要,可以选取⽤标准的⼯作控制计算机,也可以设计专⽤的微机控制系统。
2 设计任务题⽬:数控车床⼯作台⼆维运动伺服进给系统设计任务:设计⼀种供应式数控铣床使⽤的X-Y 数控⼯作台,主要参数如下:1. ⽴铣⼑最⼤直径的d=15mm ;2. ⽴铣⼑齿数Z=3;3. 最⼤铣削宽度e a =15mm;4. 最⼤背吃⼑量p a =8mm;5. 加⼯材料为碳素钢活有⾊⾦属。
6. X 、Y ⽅向的脉冲当量x y δδ==0.01mm;7. X 、Z ⽅向的定位精度均为0.04mm; 8. 重复定位精度为0.02mm; 9. ⼯作台尺⼨ 250×250㎜; 10.X 坐标⾏程 300mm; 11.Y 坐标⾏程 120mm;12.⼯作台空载进给最快移动速度:V xmaxf =V zmaxf =1500mm/min; 13.⼯作台进给最快移动速度:max max 400mm /min x f zf V V ==;3 总体⽅案确定3.1机械传动部件的选择 3.1.1导轨副的选⽤要设计数控车床X-Z ⼯作台,需要承受的载荷不⼤,⽽且脉冲当量⼩,定位精度不是很⾼,因此选⽤直线滑动导轨副,它具有摩擦系数⼩、不易爬⾏、传动效率⾼、结构紧凑、安装预紧⽅便等优点。
加工中心的工作台和伺服进给系统的设计

加工中心的工作台和伺服进给系统的设计加工中心是一种高精度、高效率的数控机床,它能够进行多种复杂形状的零件加工。
在加工中心的设计中,工作台和伺服进给系统起着至关重要的作用。
下面将详细介绍加工中心工作台和伺服进给系统的设计。
一、工作台的设计工作台是加工中心加工零件的基础,并且工作台的设计直接影响加工中心的加工精度和稳定性。
在工作台的设计中,需要考虑以下几个关键方面:1.材料选择:工作台需要具备足够的强度和刚性,以承受加工过程中的各种力。
常见的工作台材料有铸铁、钢等。
根据具体的加工要求,可以选择合适的材料。
2.结构设计:工作台的结构设计要求稳定可靠,并具备足够的刚性。
同时,还需要考虑工作台的刚性回馈和振动阻尼措施,以提高加工精度。
3.加工面设计:工作台需要具备足够的平面度和光洁度,以保证加工精度。
在加工面的设计中,需要考虑加工范围、加工力矩和刚性等因素,以满足具体的加工要求。
4.夹具设计:工作台上通常需要使用夹具来固定工件。
夹具设计需要考虑工件的形状、大小、加工工艺等因素,以保证夹具与工件的稳定性和刚性。
伺服进给系统是加工中心实现各轴运动的关键部分,它的设计直接影响加工中心的工作精度和生产效率。
在伺服进给系统的设计中,需要考虑以下几个关键方面:1.传动方式选择:伺服进给系统的传动方式有直线传动和旋转传动两种。
根据具体的加工要求和工作场合,选择合适的传动方式。
常见的传动方式有丝杠传动、齿轮传动等。
2.驱动器选择:伺服进给系统的驱动器负责控制电机的运转。
驱动器的选择需要考虑驱动功率、精度和响应速度等因素,以满足加工要求。
3.反馈系统设计:伺服进给系统的反馈系统用于检测电机的位置和速度。
常见的反馈系统有编码器、光栅尺等,根据具体的加工要求选择合适的反馈系统。
4.控制系统设计:伺服进给系统的控制系统用于控制电机的运转。
控制系统可以采用开放环控制或闭环控制,根据具体的加工要求选择合适的控制系统。
总结:加工中心的工作台和伺服进给系统的设计是影响加工中心加工精度和生产效率的关键因素。
数控车床进给系统设计
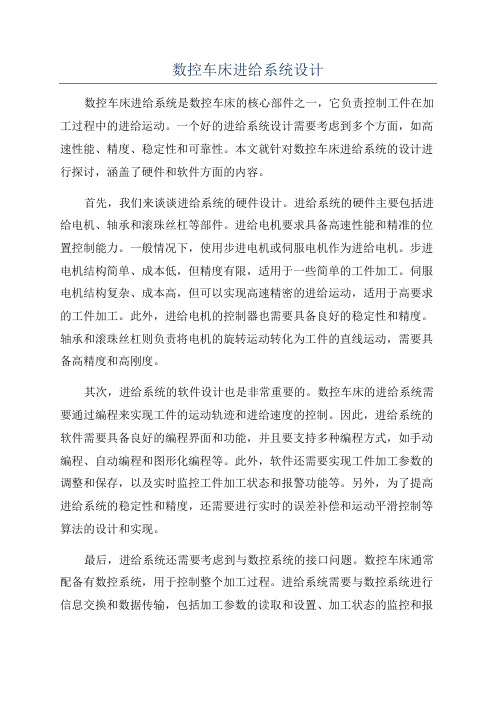
数控车床进给系统设计数控车床进给系统是数控车床的核心部件之一,它负责控制工件在加工过程中的进给运动。
一个好的进给系统设计需要考虑到多个方面,如高速性能、精度、稳定性和可靠性。
本文就针对数控车床进给系统的设计进行探讨,涵盖了硬件和软件方面的内容。
首先,我们来谈谈进给系统的硬件设计。
进给系统的硬件主要包括进给电机、轴承和滚珠丝杠等部件。
进给电机要求具备高速性能和精准的位置控制能力。
一般情况下,使用步进电机或伺服电机作为进给电机。
步进电机结构简单、成本低,但精度有限,适用于一些简单的工件加工。
伺服电机结构复杂、成本高,但可以实现高速精密的进给运动,适用于高要求的工件加工。
此外,进给电机的控制器也需要具备良好的稳定性和精度。
轴承和滚珠丝杠则负责将电机的旋转运动转化为工件的直线运动,需要具备高精度和高刚度。
其次,进给系统的软件设计也是非常重要的。
数控车床的进给系统需要通过编程来实现工件的运动轨迹和进给速度的控制。
因此,进给系统的软件需要具备良好的编程界面和功能,并且要支持多种编程方式,如手动编程、自动编程和图形化编程等。
此外,软件还需要实现工件加工参数的调整和保存,以及实时监控工件加工状态和报警功能等。
另外,为了提高进给系统的稳定性和精度,还需要进行实时的误差补偿和运动平滑控制等算法的设计和实现。
最后,进给系统还需要考虑到与数控系统的接口问题。
数控车床通常配备有数控系统,用于控制整个加工过程。
进给系统需要与数控系统进行信息交换和数据传输,包括加工参数的读取和设置、加工状态的监控和报警等。
因此,进给系统的硬件设计中需要考虑到与数控系统的连接接口和通信协议等问题。
综上所述,一个好的数控车床进给系统设计需要综合考虑硬件和软件等多个因素。
在硬件设计方面,需要选择适合的进给电机、轴承和滚珠丝杠等部件,并确保它们具备高速性能、精度和稳定性。
在软件设计方面,需要具备良好的编程界面和功能,并实现误差补偿和运动平滑控制等算法。
CK数控车床主传动系统及进给伺服系统设计

CK数控车床主传动系统及进给伺服系统设计CK数控车床是一种智能化的机床设备,具有高效、精度高、自动化程度高等特点,被广泛应用于机械制造、航空航天、军工等领域。
CK数控车床的主传动系统是其核心部件之一,关系到车床的工作效率和加工精度。
进给伺服系统则是保证车床加工过程稳定性的重要组成部分。
本文主要从CK数控车床主传动系统和进给伺服系统的设计角度进行分析和讨论。
一、CK数控车床主传动系统的设计1. 主轴驱动方式主轴驱动方式通常可以由电机、齿轮传动或皮带传动等方式实现。
在CK数控车床中,常用的主轴驱动方式为交流伺服电机直接驱动主轴,具有驱动力矩大、响应速度快、控制精度高等特点。
2. 齿轮系统设计齿轮系统是实现主轴传动的关键组成部分,其设计应考虑到精度、牢固性、噪声等因素。
通常使用调质淬火的合金钢齿轮,采用齿轮精度等级要求高于齿轮传动的精度等级,以保证齿轮传动的精确性和稳定性。
同时,为了减少噪声和振动,应该选择齿轮结构简单、转速变化范围小和运转平衡的齿轮组合。
3. 主轴轴承设计主轴轴承是支撑主轴的关键组成部分,其设计应考虑到承载能力、耐磨性、轴向刚度以及寿命等因素。
常用的主轴轴承采用滚道式或杯状式结构,具有承载能力大、耐磨性好等优点。
同时,应合理选择轴承的接触角度和精度等级,减小径向力矩、抗疲劳性好,以提高轴向刚度和使用寿命。
4. 润滑系统设计润滑系统是保障主轴正常运转的关键组成部分,其设计应考虑到润滑方式、油品种类和加油方式等因素。
常用的润滑方式包括油脂润滑和油膜润滑,油品种类应选择合适的润滑油,加油方式应考虑到主轴的运转状态,一般采用快速注油式或定期注油式。
二、CK数控车床进给伺服系统的设计1. 进给驱动方式进给驱动方式通常可以由电机、齿轮传动或滑块传动等方式实现。
在CK数控车床中,常用的进给驱动方式为伺服电机驱动滚珠丝杠,具有进给精度高、稳定性好、响应速度快等特点。
2. 滚珠丝杠设计滚珠丝杠是实现进给传动的关键组成部分,其设计应考虑到精度、耐磨性、轴向刚度以及寿命等因素。
数控机床伺服进给装置的设计
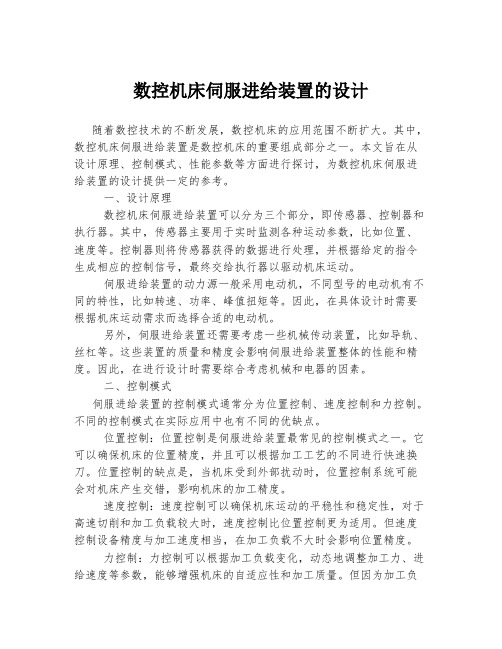
数控机床伺服进给装置的设计随着数控技术的不断发展,数控机床的应用范围不断扩大。
其中,数控机床伺服进给装置是数控机床的重要组成部分之一。
本文旨在从设计原理、控制模式、性能参数等方面进行探讨,为数控机床伺服进给装置的设计提供一定的参考。
一、设计原理数控机床伺服进给装置可以分为三个部分,即传感器、控制器和执行器。
其中,传感器主要用于实时监测各种运动参数,比如位置、速度等。
控制器则将传感器获得的数据进行处理,并根据给定的指令生成相应的控制信号,最终交给执行器以驱动机床运动。
伺服进给装置的动力源一般采用电动机,不同型号的电动机有不同的特性,比如转速、功率、峰值扭矩等。
因此,在具体设计时需要根据机床运动需求而选择合适的电动机。
另外,伺服进给装置还需要考虑一些机械传动装置,比如导轨、丝杠等。
这些装置的质量和精度会影响伺服进给装置整体的性能和精度。
因此,在进行设计时需要综合考虑机械和电器的因素。
二、控制模式伺服进给装置的控制模式通常分为位置控制、速度控制和力控制。
不同的控制模式在实际应用中也有不同的优缺点。
位置控制:位置控制是伺服进给装置最常见的控制模式之一。
它可以确保机床的位置精度,并且可以根据加工工艺的不同进行快速换刀。
位置控制的缺点是,当机床受到外部扰动时,位置控制系统可能会对机床产生交错,影响机床的加工精度。
速度控制:速度控制可以确保机床运动的平稳性和稳定性,对于高速切削和加工负载较大时,速度控制比位置控制更为适用。
但速度控制设备精度与加工速度相当,在加工负载不大时会影响位置精度。
力控制:力控制可以根据加工负载变化,动态地调整加工力、进给速度等参数,能够增强机床的自适应性和加工质量。
但因为加工负载难以实时查询,速度接近慢速或轻负载条件下的削减力控制将导致大幅度速度的波动和加工质量的下降。
因此,力控制需要在合适的运动参数下才能获得理想的加工质量。
三、性能参数伺服进给装置的性能参数直接影响到加工质量和加工效率。
- 1、下载文档前请自行甄别文档内容的完整性,平台不提供额外的编辑、内容补充、找答案等附加服务。
- 2、"仅部分预览"的文档,不可在线预览部分如存在完整性等问题,可反馈申请退款(可完整预览的文档不适用该条件!)。
- 3、如文档侵犯您的权益,请联系客服反馈,我们会尽快为您处理(人工客服工作时间:9:00-18:30)。
数控车床工作台二维运动伺服进给系统设计1 引言数控机床作为机电一体化的典型产品,在机械制造业中发挥着巨大的作用,很好地解决了现代机械制造中结构复杂、精密、批量小、多变零件的加工问题,且能稳定产品的加工质量,大幅度提高生产效率。
X-Y 数控工作台是许多机电一体化设备的基本部件,如数控车床的纵—横向进刀机构、数控铣床和数控钻床的X-Y 工作台、激光加工设备的工作台、电子元件表面贴装设备等。
模块化的X-Y 数控工作台,通常由导轨座、移动滑块、工作、滚珠丝杠螺母副,以及伺服电动机等部件构成。
其中伺服电动机做执行元件用来驱动滚珠丝杠,滚珠丝杠螺母带动滑块和工作平台在导轨上运动,完成工作台在X 、Y 方向的直线移动。
导轨副、滚珠丝杠螺母副和伺服电动机等均以标准化,由专门厂家生产,设计时只需根据工作载荷选取即可。
控制系统根据需要,可以选取用标准的工作控制计算机,也可以设计专用的微机控制系统。
2 设计任务题目:数控车床工作台二维运动伺服进给系统设计任务:设计一种供应式数控铣床使用的X-Y 数控工作台,主要参数如下:1. 立铣刀最大直径的d=15mm ;2. 立铣刀齿数Z=3;3. 最大铣削宽度e a =15mm;4. 最大背吃刀量p a =8mm;5. 加工材料为碳素钢活有色金属。
6. X 、Y 方向的脉冲当量x y δδ==0.01mm;7. X 、Z 方向的定位精度均为0.04mm; 8. 重复定位精度为0.02mm; 9. 工作台尺寸 250×250㎜; 10.X 坐标行程 300mm; 11.Y 坐标行程 120mm;12.工作台空载进给最快移动速度:V xmaxf =V zmaxf =1500mm/min; 13.工作台进给最快移动速度:max max 400mm /min x f z f V V ==;3 总体方案确定3.1机械传动部件的选择 3.1.1导轨副的选用要设计数控车床X-Z 工作台,需要承受的载荷不大,而且脉冲当量小,定位精度不是很高,因此选用直线滑动导轨副,它具有摩擦系数小、不易爬行、传动效率高、结构紧凑、安装预紧方便等优点。
3.1.2丝杠螺母副的选用伺服电动机的旋转运动需要通过丝杠螺母副转换成直线运动,需要满足0.004mm 冲当量和01.0±mm 的定位精度,滑动丝杠副无能为力,只有选用滚珠丝杆副才能达到要求,滚珠丝杆副的传动精度高、动态响应快、运转平稳、寿命长、效率高、预紧后可消除反向间隙。
3.1.3伺服电动机的选用任务书规定的脉冲当量尚未达到0.01mm ,定位精度也未达到微米级,空载最快移动速度也只有因此1500mm/min ,故本设计不必采用高档次的伺服电动机,因此可以选用混合式步进电动机。
以降低成本,提高性价比。
3.1.4减速装置的选用为了圆整脉冲当量,放大电动机的输出转矩,降低运动部件折算到电动机转轴上的转动惯量,需要设置减速装置,且应有消间隙机构。
因此决定采用无间隙齿轮传动减速箱。
3.1.5检测装置的选用选用步进电动机作为伺服电动机后,可选开环控制,也可选闭环控制。
任务书所给的精度对于步进电动机来说还是偏高,为了确保电动机在运动过程中不受切削负载和电网的影响而失步,决定采用半闭环控制,拟在电动机的尾部转轴上安装增量式旋转编码器,用以检测电动机的转角与转速。
增量式旋转编码器的分辨力应与步进电动机的步距角相匹配。
考虑到X、Z两个方向的加工范围相同,承受的工作载荷相差不大,为了减少设计工作量,X、Z两个坐标的导轨副、丝杠螺母副、减速装置、伺服电动机以及检测装置拟采用相同的型号与规格。
3.2 控制系统的设计1)设计的X-Z工作台准备用在数控车床上,其控制系统应该具有单坐标定位,两坐标直线插补与圆弧插补的基本功能,所以控制系统设计成连续控制型。
2)对于步进电动机的半闭环控制,选用MCS-51系列的8位单片机AT89S52作为控制系统的CPU,能够满足任务书给定的相关指标。
3)要设计一台完整的控制系统,在选择CPU之后,还要扩展程序存储器,键盘与显示电路,I/O接口电路,D/A转换电路,串行接口电路等。
4)选择合适的驱动电源,与步进电动机配套使用。
3.3 绘制总体方案图总体方案图如图所示:系统结构原理框图4 机械传动部件的计算与选型4.1 导轨上移动部件的重量估算按照下导轨上面移动部件的重量来进行估算。
包括工件、夹具、工作台、上层电动机、减速箱、滚珠丝杠副、导轨座等,估计重量约为500N4.2 铣削力的计算设零件的加工方式为立式铣削,采用硬质合金立铣刀,工件的材料为碳钢。
则由表3-7查得立铣时的铣削力计算公式为:0.850.750.73 1.00.13c e z p 118a fd a n Z F -= (6-11)今选择铣刀的直径为d=15mm ,齿数Z=3,为了计算最大铣削力,在不对称铣削情况下,取最大铣削宽度为e a 15mm =,背吃刀量p a =8mm ,每齿进给量z f 0.1mm =,铣刀转速n 300r/min =。
则由式(6-11)求的最大铣削力:F C =118 x150.85x 0.10.75x 15-0.73x 81.0x 3000.13x 3N=1463N采用立铣刀进行圆柱铣削时,各铣削力之间的比值可由表查得,考虑逆铣时的情况,可估算三个方向的铣削力分别为:1607N F 1.1F C f ≈=,556N F 38.0F C e ≈=,N 663F 25.0F C fn ≈=。
图3-4a 为卧铣情况,现考虑立铣,则工作台受到垂直方向的铣削力N 556F F e z ≈=,受到水平方向的铣削力分别为f F 和fn F 。
今将水平方向较大的铣削力分配给工作台的纵向,则纵向铣削力N 1607F F f x ≈=,径向铣削力为N 366F F fn y ≈=。
4.3 导轨的计算由于使用的是双矩形滑动导轨,故不要求进行相应的计算。
4.4 滚珠丝杠螺母副的计算与选型 4.4.1 最大工作载荷Fm 的计算如前所述,在立铣时,工作台受到进给方向的载荷(与丝杠轴线平行)Fx=1607N,受到横向载荷(与丝杠轴线垂直)Fy=366N ,受到垂直方向的载荷(与工作台面垂直)Fz=556N.已知移动部件总重量G=500N ,按矩形导轨进行计算,取颠覆力矩影响系数K=1.1,滚动导轨上的摩擦系数μ=0.04。
求得滚珠丝杠副的最大工作载荷:Fm=KFx+μ(Fz+Fy+G)=[1.1⨯1408+0.04⨯(556+366+500)]N ≈1827N 4.4.2 最大动工作载荷FQ 的计算设工作台在承受最大铣削力时的最快进给速度v=400mm/min ,初选丝杠导程Ph=5mm,则此时丝杠转速n=v/Ph=80r/min 。
取滚珠丝杠的使用寿命T=15000h,代入L0=60Nt/106,得丝杠寿命系数L0=72(单位为:106r )。
查表,取载荷系数fw=1.2,滚道硬度为60HRC 时,取硬度系数fH=1.0,代入式(3-23),求得最大动载荷:N F f f F m H w Q 9116L 30≈=4.4.3 初选型号根据计算出的最大动载荷和初选的丝杠导程,选择济宁博特精密丝杠制造有限公司生产的G 系列2005-4型滚珠丝杠副,为内循环固定反向器单螺母式,其公称直径为20mm ,导程为5mm ,循环滚珠为3圈*1系列,精度等级取5级,额定动载荷为11082N ,大于F Q ,满足要求。
表3.1滚珠丝杠螺母副几何参数4.4.4 选择滚珠丝杠直径时,还应综合考虑下列问题丝杠工作长度L ,应满足控制中的行程要求。
L 应为丝杠工作长度:134l l H l l ≥+++式中,1l 为控制系统中需要的行程(mm ),H 为螺母的安装高度(mm ),3l 为满足行程以外的余量,一般10~5=l ,4l 为由丝杠防护结构确定的长度(mm ),于是:横向丝杠: 410mm 08251300l x=++⨯+=纵向丝杠: mm 30208251021l y =++⨯+= (1) 根据结构设计,螺杆的总长度l 总应为螺杆的工作长度L 加上结构长度。
横向: mm l 579178401=+=总纵向: mm l399178221=+=总(2) 丝杠的长度还应满足刚度的要求,根据刚度要求确定丝杠的直径d横向:40~3416.2325/579≤==dl总纵向:40~3496.1525/399≤==dl总即满足40~34≤dl总(3) 因此,滚珠丝杠直径可以都选为d=25mm4.4.5 传动效率η的计算将公称直径d 0=20mm,导程P h =5mm,代入λ=arctan[P h /(∏d 0)],得丝杠螺旋升角λ=4°33′。
将摩擦角ψ=10′,代入η=tan λ/tan(λ+ψ),得传动效率η=96.4%。
4.4.6 刚度的验算(1) X-Y 工作台上下两层滚珠丝杠副的支承均采用“单推-单推”的方式。
丝杠的两端各采用-对推力角接触球轴承,面对面组配,左、右支承的中心距约为a=500mm ;钢的弹性模量E=2.1х105Mpa;查表得滚珠直径D w =3.175mm ,丝杠底径d 2=16.2mm,丝杠截面积S=22d π/4=206.12m 2m 。
忽略式(3-25)中的第二项,算得丝杠在工作载荷Fm 作用下产生的拉/压变形量⨯⨯==1.2/(5001826[)/(1ES Fma δ105)]12.206⨯mm=0.0211mm.。
(2) 根据公式0(/)3W Z d D π=-,求得单圈滚珠数Z=20;该型号丝杠为单螺母,滚珠的圈数⨯列数为3⨯1,代入公式Z ∑=Z ⨯圈数⨯列数,得滚珠总数量Z ∑=60。
丝杠预紧时,取轴向预紧力YJ m F F =/3=609N 。
则由式(3-27),求得滚珠与螺纹滚道间的接触变形量20.0024δ≈mm 。
因为丝杠有预紧力,且为轴向负载的1/3,所以实际变形量可以减少一半,取2δ=0.0012mm 。
(3) 将以上算出的1δ和2δ代入12δδδ=+总,求得丝杠总变形量(对应跨度500mm )δ总=0.0212mm=21.2m μ本例中,丝杠的有效行程为330mm ,由表知,5级精度滚珠丝杠有效行程在315~400mm 时,行程偏差允许达到25m μ,可见丝杠刚度足够。
4.4.7 压杆稳定性校核根据公式(3-28)计算失稳时的临界载荷F K 。
取支承系数k f =1;由丝杠底径d 2=16.2mm 求得截面惯性矩42/64I d π=≈3380.884mm ;压杆稳定安全系数K 取3(丝杠卧式水平安装);滚动螺母至轴向固定处的距离a 取最大值500mm 。
代入式(3-28),得临界载荷F K =1557N ,故丝杠不会失稳。