金刚石砂轮介绍
金刚石砂轮成型模具设计
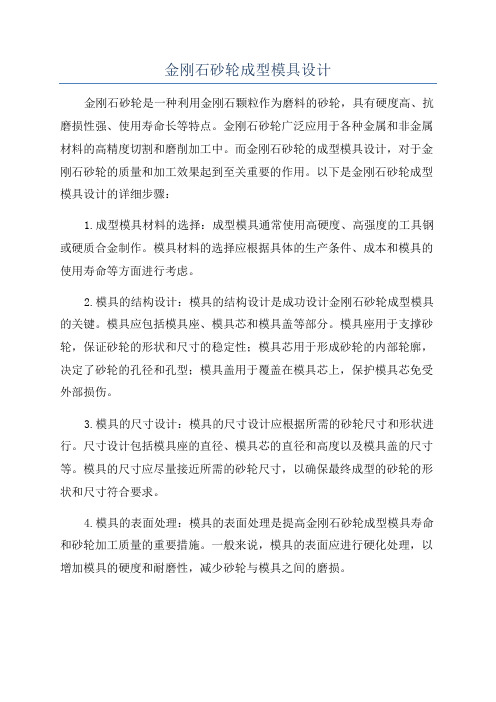
金刚石砂轮成型模具设计金刚石砂轮是一种利用金刚石颗粒作为磨料的砂轮,具有硬度高、抗磨损性强、使用寿命长等特点。
金刚石砂轮广泛应用于各种金属和非金属材料的高精度切割和磨削加工中。
而金刚石砂轮的成型模具设计,对于金刚石砂轮的质量和加工效果起到至关重要的作用。
以下是金刚石砂轮成型模具设计的详细步骤:1.成型模具材料的选择:成型模具通常使用高硬度、高强度的工具钢或硬质合金制作。
模具材料的选择应根据具体的生产条件、成本和模具的使用寿命等方面进行考虑。
2.模具的结构设计:模具的结构设计是成功设计金刚石砂轮成型模具的关键。
模具应包括模具座、模具芯和模具盖等部分。
模具座用于支撑砂轮,保证砂轮的形状和尺寸的稳定性;模具芯用于形成砂轮的内部轮廓,决定了砂轮的孔径和孔型;模具盖用于覆盖在模具芯上,保护模具芯免受外部损伤。
3.模具的尺寸设计:模具的尺寸设计应根据所需的砂轮尺寸和形状进行。
尺寸设计包括模具座的直径、模具芯的直径和高度以及模具盖的尺寸等。
模具的尺寸应尽量接近所需的砂轮尺寸,以确保最终成型的砂轮的形状和尺寸符合要求。
4.模具的表面处理:模具的表面处理是提高金刚石砂轮成型模具寿命和砂轮加工质量的重要措施。
一般来说,模具的表面应进行硬化处理,以增加模具的硬度和耐磨性,减少砂轮与模具之间的磨损。
5.模具的加工工艺:模具加工工艺主要包括切割、钻孔、螺纹加工、磨削和打磨等步骤。
模具的加工过程应严格按照设计要求进行,以确保最终成型的模具能够满足砂轮生产的需要。
6.模具的安装和调试:模具的安装和调试是金刚石砂轮成型模具设计的最后一步。
在安装时,应注意将模具芯正确地安装到模具座上,并调整模具盖的位置和紧固度。
然后,通过试制砂轮,检验成型效果和砂轮的质量。
总之,金刚石砂轮成型模具设计是一项复杂的任务,需要综合考虑材料性能、结构设计、尺寸设计、表面处理、加工工艺等多个因素。
只有合理设计和制造出适用的成型模具,才能保证金刚石砂轮的质量和加工效果。
金刚石砂轮规格型号标准
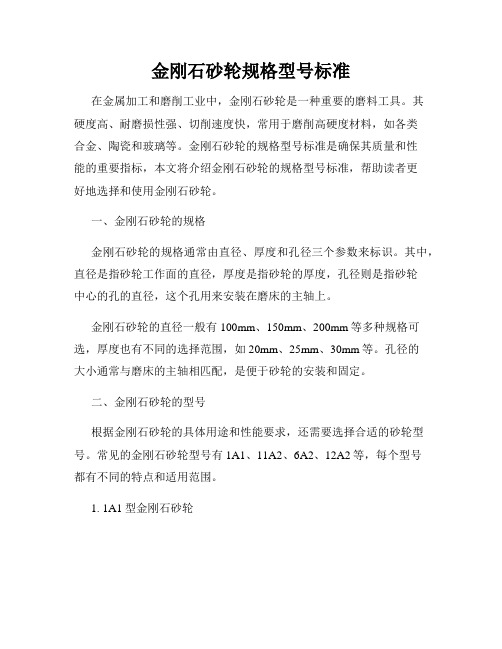
金刚石砂轮规格型号标准在金属加工和磨削工业中,金刚石砂轮是一种重要的磨料工具。
其硬度高、耐磨损性强、切削速度快,常用于磨削高硬度材料,如各类合金、陶瓷和玻璃等。
金刚石砂轮的规格型号标准是确保其质量和性能的重要指标,本文将介绍金刚石砂轮的规格型号标准,帮助读者更好地选择和使用金刚石砂轮。
一、金刚石砂轮的规格金刚石砂轮的规格通常由直径、厚度和孔径三个参数来标识。
其中,直径是指砂轮工作面的直径,厚度是指砂轮的厚度,孔径则是指砂轮中心的孔的直径,这个孔用来安装在磨床的主轴上。
金刚石砂轮的直径一般有100mm、150mm、200mm等多种规格可选,厚度也有不同的选择范围,如20mm、25mm、30mm等。
孔径的大小通常与磨床的主轴相匹配,是便于砂轮的安装和固定。
二、金刚石砂轮的型号根据金刚石砂轮的具体用途和性能要求,还需要选择合适的砂轮型号。
常见的金刚石砂轮型号有1A1、11A2、6A2、12A2等,每个型号都有不同的特点和适用范围。
1. 1A1型金刚石砂轮1A1型金刚石砂轮是一种平面砂轮,其主要用于对各种材料的平面磨削。
该型号的砂轮结构紧密,磨削效率高,表面加工质量好。
适用于磨削硬度高的合金材料、陶瓷和石材等。
2. 11A2型金刚石砂轮11A2型金刚石砂轮是一种碟形砂轮,其特点是具有较大的孔径,用来进行内圆磨削。
该型号的砂轮适用于对轴承外圈、油封等零件进行磨削。
3. 6A2型金刚石砂轮6A2型金刚石砂轮是一种碟形砂轮,适用于刃磨刀具和切削工具。
该型号的砂轮具有较大的厚度,磨削时稳定性好,适用于对较大尺寸的工具进行磨削。
4. 12A2型金刚石砂轮12A2型金刚石砂轮是一种碟形砂轮,适用于刃磨锥形刀具和大尺寸的平刀。
该型号的砂轮具有大孔径,适用于磨削直径较大的工具。
除了以上几种常见的型号外,金刚石砂轮还有其他的型号,如1V1、12V9、14A1等。
不同的型号适用于不同的磨削任务和材料。
三、金刚石砂轮的标准1. GB/T 6409.1-2002《磨料砂轮特种砂轮》是中国国家标准中关于金刚石砂轮的规格型号标准。
金刚石砂轮

金刚石砂轮什么是金刚石砂轮?金刚石砂轮的组成、特性和用途有时什么?以下将做详细介绍。
以金刚石磨料为原料,分别用金属粉、树脂粉、陶瓷和电镀金属作结合剂,制成各种形状的制品,用于磨削、抛光、研磨的工具叫金刚石磨具,包括砂轮、油石(珩磨油石)、钻具、据具、粉状修正工具、修正滚轮、手工工具(锉刀类)、牙钻、雕刻工具、油石、内外圆切割锯片、砂轮刀、玻璃刀、车刀、木工圆盘锯片等。
其中以金刚石砂轮,金刚石锯片应用最广泛。
金刚石砂轮一般由工作层、基体、过渡层三部分组成。
工作层,又称金刚石层,由磨料、结合剂和填料组成,是砂轮的工作部分;过渡层,又称非金刚石层,由结合剂、金属粉和填料组成,是将金刚石层牢固地连接在基体上的部分;基体,用于承接磨料层,并在使用时用法兰盘牢固地把砂轮夹持在磨床主轴上,基体本身应该是在不影响其刚性和强度的条件下愈轻愈好,一般金属结合剂制品选用钢材,合金钢粉作基体,树脂结合剂制品选用铝合金,电木作基体。
制品成型质量的好坏和使用精度的高低都与基体有很大关系。
因此,基体应该有几何形状和尺寸精度以及表面粗糙度要求。
金刚石砂轮的特性包括金刚石磨料泊种类、粒度、浓度、结合剂和形状尺寸。
金刚石砂轮的用途:由于金刚石磨料所独具的特性(硬度高、抗压强度高、耐磨性好),使金刚石砂轮在磨削加工中成为磨削硬脆材料及硬质合金的理想工具,不但效率高、精度高、而且粗糙度好、砂轮消耗少,使用寿命长,同时还可改善劳动条件。
因此广泛用于普通砂轮难以加工的低铁含量的金属和非金属硬脆材料,如硬质合金、高铝瓷、光学玻璃、玛瑙宝石、半导体材料、石材等。
各种型号金刚石砂轮的特点及用途金刚石砂轮是磨削硬质合金、陶瓷、玻璃等材料的理想工具,采用优质金刚石,结合先进工艺配方,产品质量稳定可靠,磨削效率高,磨削成本低,是非常理想的磨削工具。
金刚石砂轮金属结合剂(代号J):常见的是青铜结合剂(代号Q),主要用于制作金刚石砂轮。
青铜结合剂金刚石砂轮的特点是型面的成型性好,强度高,有一定韧性。
金刚石砂轮的形状和型号代码
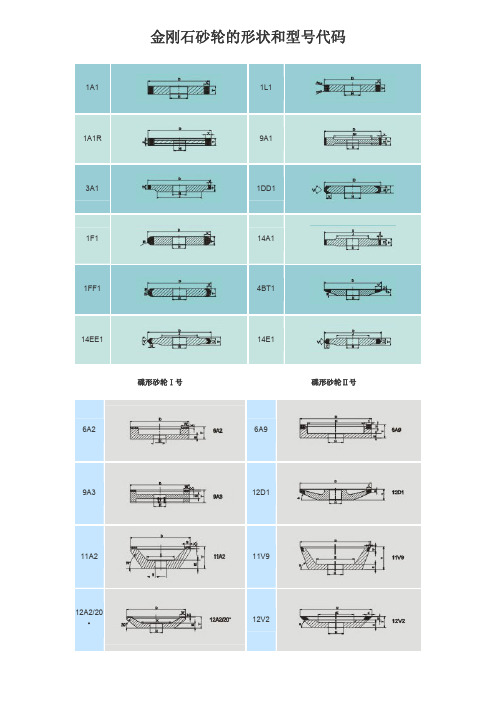
金刚石砂轮的形状和型号代码1a11l11a1r9a13a11dd11f114a11ff14bt114ee114e1碟形砂轮号碟形砂轮号6a26a99a312d111a211v912a22012v212a24512v9陶瓷结合剂金刚石砂轮陶瓷结合剂金刚石砂轮使用寿命长切削锋利效率高磨削不易发热和堵塞易控制加工精度及修整
金刚石砂轮的形状和型号代码
1A1
1L1
1A1R
9A1
3A1
1DD1
1F1
14A1
1FF1
4BT1
14EE1
14E1
碟形砂轮Ⅰ号
碟形砂轮Ⅱ号
6A2
6A9
9A3
12D1
11A2
11V9
12A2/20 °
12V2
12A2/45 °
12V9
陶瓷结合剂金刚石砂轮 陶瓷结合剂金刚石砂轮使用寿命长,切削锋利,效率高,磨削不易发热和堵塞,易控制加工精度 及修整。 主要用于 PCD、CVD、PCBN、硬质合金、陶瓷刀具以及其它刃具的快速高效低损伤磨削。河 南胜创超硬材料有限公司能够为您提供直径范围:ф80-600mm,砂轮厚度:3~200mm,磨料 粒度:W3.5~80/100 的陶瓷结合剂砂轮。 信息来源:/ch/All-Diamond-Wheels-Typle.html
金刚石压制砂轮的原理
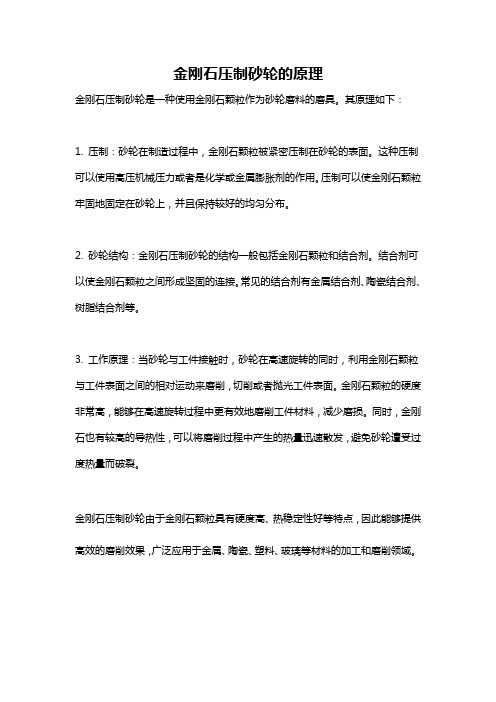
金刚石压制砂轮的原理
金刚石压制砂轮是一种使用金刚石颗粒作为砂轮磨料的磨具。
其原理如下:
1. 压制:砂轮在制造过程中,金刚石颗粒被紧密压制在砂轮的表面。
这种压制可以使用高压机械压力或者是化学或金属膨胀剂的作用。
压制可以使金刚石颗粒牢固地固定在砂轮上,并且保持较好的均匀分布。
2. 砂轮结构:金刚石压制砂轮的结构一般包括金刚石颗粒和结合剂。
结合剂可以使金刚石颗粒之间形成坚固的连接。
常见的结合剂有金属结合剂、陶瓷结合剂、树脂结合剂等。
3. 工作原理:当砂轮与工件接触时,砂轮在高速旋转的同时,利用金刚石颗粒与工件表面之间的相对运动来磨削,切削或者抛光工件表面。
金刚石颗粒的硬度非常高,能够在高速旋转过程中更有效地磨削工件材料,减少磨损。
同时,金刚石也有较高的导热性,可以将磨削过程中产生的热量迅速散发,避免砂轮遭受过度热量而破裂。
金刚石压制砂轮由于金刚石颗粒具有硬度高、热稳定性好等特点,因此能够提供高效的磨削效果,广泛应用于金属、陶瓷、塑料、玻璃等材料的加工和磨削领域。
金刚石砂轮生产工艺
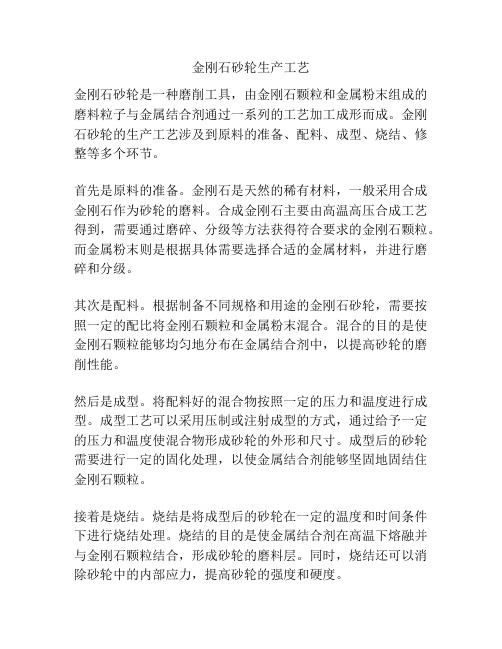
金刚石砂轮生产工艺金刚石砂轮是一种磨削工具,由金刚石颗粒和金属粉末组成的磨料粒子与金属结合剂通过一系列的工艺加工成形而成。
金刚石砂轮的生产工艺涉及到原料的准备、配料、成型、烧结、修整等多个环节。
首先是原料的准备。
金刚石是天然的稀有材料,一般采用合成金刚石作为砂轮的磨料。
合成金刚石主要由高温高压合成工艺得到,需要通过磨碎、分级等方法获得符合要求的金刚石颗粒。
而金属粉末则是根据具体需要选择合适的金属材料,并进行磨碎和分级。
其次是配料。
根据制备不同规格和用途的金刚石砂轮,需要按照一定的配比将金刚石颗粒和金属粉末混合。
混合的目的是使金刚石颗粒能够均匀地分布在金属结合剂中,以提高砂轮的磨削性能。
然后是成型。
将配料好的混合物按照一定的压力和温度进行成型。
成型工艺可以采用压制或注射成型的方式,通过给予一定的压力和温度使混合物形成砂轮的外形和尺寸。
成型后的砂轮需要进行一定的固化处理,以使金属结合剂能够坚固地固结住金刚石颗粒。
接着是烧结。
烧结是将成型后的砂轮在一定的温度和时间条件下进行烧结处理。
烧结的目的是使金属结合剂在高温下熔融并与金刚石颗粒结合,形成砂轮的磨料层。
同时,烧结还可以消除砂轮中的内部应力,提高砂轮的强度和硬度。
最后是修整。
修整是对砂轮进行加工和修整以获得符合要求的产品。
修整包括砂轮的修整和尺寸的修整。
砂轮的修整是根据具体的形状要求,通过切割、磨削等方法将砂轮修整成相应的形状。
尺寸的修整是根据砂轮的精度要求,通过切割和磨削的方法将砂轮修整到合适的尺寸。
综上所述,金刚石砂轮的生产工艺主要包括原料的准备、配料、成型、烧结、修整等环节。
这些环节的精细操作和严格控制可以使金刚石砂轮具有良好的磨削性能和使用寿命。
砂轮片成分

砂轮片成分1. 简介砂轮片是一种常用的磨具,广泛应用于金属加工、石材加工、玻璃加工等行业。
它由磨料和结合剂组成,具有高硬度、高强度和耐磨损的特性。
本文将对砂轮片的成分进行详细介绍。
2. 磨料2.1 金刚石磨料金刚石是一种最硬的天然物质,其硬度仅次于自然界中的金刚石。
金刚石具有优异的耐高温性能和耐腐蚀性能,因此被广泛应用于制造高品质的砂轮片。
金刚石磨料通常采用人造合成的金刚石颗粒,这些颗粒经过特殊处理后形成均匀分布在结合剂中。
2.2 刚玉磨料刚玉是一种主要由氧化铝(Al2O3)组成的无机化合物,具有较高的硬度和抗压强度。
刚玉可通过天然原料或人工合成方式制备得到,其颗粒形状多为多面体。
刚玉磨料常用于制造低成本的砂轮片,广泛应用于金属加工和石材加工等领域。
2.3 碳化硅磨料碳化硅是一种由碳和硅元素组成的化合物,具有高硬度、高熔点和优异的耐腐蚀性能。
碳化硅磨料通常采用人造合成的碳化硅颗粒,其颗粒形状多为角砾状或针状。
碳化硅磨料在高温环境下仍能保持较高的硬度,因此适用于高速切削和精密加工。
2.4 氧化铝磨料氧化铝是一种由氧化铝(Al2O3)组成的无机化合物,具有良好的耐高温性能和抗压强度。
氧化铝颗粒形态多样,可以是圆形、角形或棱柱形。
氧化铝磨料在制备过程中通常采用特殊处理技术,以提高其耐冲击性和耐压强度。
3. 结合剂结合剂是将不同磨料颗粒固定在一起的材料,起到连接和支撑磨料的作用。
常见的结合剂包括陶瓷结合剂、金属结合剂和树脂结合剂。
3.1 陶瓷结合剂陶瓷结合剂通常由氧化铝(Al2O3)和硅酸盐等物质组成,具有较高的耐高温性能和抗冲击性能。
陶瓷结合剂能够在高温下保持较好的稳定性,因此适用于高速切削和重切工艺。
3.2 金属结合剂金属结合剂通常由铜、铝等金属粉末与其他添加剂混合而成。
金属结合剂具有良好的导热性和韧性,可以提供较好的切削效果和切削稳定性。
金属结合剂适用于高速切削和重切工艺。
3.3 树脂结合剂树脂结合剂通常由环氧树脂、酚醛树脂等有机物质制成。
树脂砂轮和金刚石砂轮的区别在哪里?

树脂砂轮和⾦刚⽯砂轮的区别在哪⾥?
树脂砂轮是⽤树脂做成的砂轮,这种砂轮在强度上⾮常⾼,制作简单,具有⼀定的弹性,⼯艺周期短,耐热性低。
⾦刚⽯砂轮是以⾦刚⽯磨料为原料,分别⽤⾦属粉、树脂粉、陶瓷和电镀⾦属作结合剂制成的,它是超级强硬的,⼀点弹性也没有,其耐热性⾮常的好,但制作复杂,同时⼯艺周期长等。
总体⽽⾔,这两种砂轮的区别在于,⾦刚⽯砂轮较为⼴泛的运⽤是在于混凝⼟切割作业上,在⽽树脂砂轮则偏向于⼀些⾦属制品的磨削。
⾦刚⽯树脂砂轮
另外还有⼀种叫⾦刚⽯树脂砂轮的,其实是上⾯两者的结合体。
它的⼯作层是由⾦刚⽯和树脂结合剂组成,树脂结合剂主要成分是树脂及辅料,与⾦刚⽯粉粒混合,经加压加热固化与基体牢固结合⽽成的砂轮。
这样混合切割可在切割的时候增加它的强度,以及在有些材料的切割及打磨中,能够有效的控制切割效果等,更加适合于⼀些⾦属制品的打磨与切割。
- 1、下载文档前请自行甄别文档内容的完整性,平台不提供额外的编辑、内容补充、找答案等附加服务。
- 2、"仅部分预览"的文档,不可在线预览部分如存在完整性等问题,可反馈申请退款(可完整预览的文档不适用该条件!)。
- 3、如文档侵犯您的权益,请联系客服反馈,我们会尽快为您处理(人工客服工作时间:9:00-18:30)。
金刚石砂轮介绍
简介:
以金刚石磨料为原料,分别用金属粉、树脂粉、陶瓷和电镀金属作结合剂,制成各种形状的制品,用于磨削、抛光、研磨的工具叫金刚石磨具
结构
金刚石磨具结构一般由工作层、基体、过渡层三部分组成。
工作层又称金刚石层,由磨料、结合剂和填料组成,是磨具的工作部分。
过渡层又称非金刚石层,由结合剂、金属粉和填料组成,是将金刚石层牢固地连接在基体上的部分。
基体是由铝、钢或电木加工而成,起支承工作层和装卡磨具的作用。
用途
由于金刚石磨料所具有的特性(硬度高、抗压强度高、耐磨性好),是金刚石磨具在磨削加工中成为磨削硬脆材料及硬质合金的理想工具,不但效率高、精度高,而且粗糙度好、磨具消耗少、使用寿命长,同时还可改善劳动条件。
因此广泛用于普通磨具难于加工的低铁含量的金属及非金属硬脆材料,如硬质合金、高铝瓷、光学玻璃、玛瑙宝石、半导体材料、石材等。
[编辑本段]
分类:
金刚石砂轮按结合剂可分为:树脂结合剂金刚石砂轮;陶瓷结合剂金刚石砂轮;金属结合剂金刚石砂轮(青铜结合剂金刚石砂轮)
金刚石砂轮按生产工艺可分为:烧结式金刚石砂轮(树脂结合剂金刚石砂轮;陶瓷结合剂金刚石砂轮;金属结合剂金刚石砂轮);电镀金刚石砂轮;钎焊金刚石砂轮。
金刚石砂轮按磨削方式可分为:磨钻石用金刚石砂轮;磨硬质合金用金刚石砂轮(金刚石刀磨砂轮);磨金刚石复合片用金刚石砂轮;无芯磨床用无心磨金刚石砂轮;
磨陶瓷制品用金刚石砂轮;切割用金刚石砂轮(也被称为金刚石切割片);金刚石锯片。
金刚石砂轮按外观或形状可分为:平行砂轮;筒形砂轮;杯形砂轮;碗形砂轮;碟形砂轮;磨边砂轮;磨盘等。
人造金刚石又称"工业钻石",它和天然金刚石一样,是当今人们已知自然界中最硬的物质。
由于它具有极高的硬度,抗压强度和耐磨性,抗酸碱性以及良好的导热性和半导体性能,因而它被制成的各种工具制品能广泛应用于冶金、机械、地质、石油、电子、光学、建筑、石材等各个领域。
人造金刚石砂轮是以人造金刚石为主要原材料配以其他金属粉料经过高温、高压形成的一种人造金刚石制品,能广泛应用于硬质合金、有色金属和非金属的磨削加工。
粒度选用
人造金刚石粒度的粗细以粒度号表示。
粒度的粗细直接影响工件表面粗糙度、磨削效率和磨具损耗。
选择粒度原则上是在满足加工工件要求的条件下选用尽可能粗的粒度,这样可以提高磨削效率和降低磨具的损耗。
(见右表)
金刚石粒度一般分
磨削工序选用粒度
粗磨30#-120#
中磨120#-240#
精磨240#-W40
研磨、抛光W40-W1
结合剂选用
人造金刚石砂轮根据结合剂的不同一般分为树脂砂轮、金属砂轮、陶瓷砂轮和电镀砂轮。
不同的结合剂有着不同的性能,要根据不同的加工对象、要求来选用合适的结合剂。
结合剂代号主要用途
树脂结合剂B 用于硬质合金、玻璃、陶瓷、石材和宝石的切割、磨削。
金属结合剂M 用于硬质合金、玻璃、陶瓷、石材、宝石等重负荷切割、磨削耐磨性好。
陶瓷结合剂V 用于各种钢材和铸铁等的干磨和湿磨,更适合磨削长轴和丝轩。
电镀结合剂D 用于各种材料特殊型面、小孔的磨削及贵重材料的切割下料。
浓度选用
浓度是指人造金刚石在磨具磨料层中的含量。
①树脂结合剂砂轮一般采用50%-100%的浓度;其中大部分用75%,要求光洁度较高时可低于75%,成型磨削和要求使用寿命较长的砂轮,可用100%或以上。
②金属结合剂制品中一般采用25%-150%的浓度;其中粗粒度的切割锯片、浓度一般较底,即25-50%,细粒度的较高;而其他金属结合剂砂轮一般要求浓度要50%-100%的浓度。
总体而言,粗磨用较高浓度,半精磨用中等浓度,而精磨、抛光等用较高的浓度。
浓度磨料含量体积% 克拉/cm3
25% 6.25 1.1
50% 12.5 2.2
75% 18.75 3.3
100% 25 4.4
125% 31.25 5.5
150% 37.5 6.6
立方氮化硼磨具性能
立方氮化硼是由六方氮化硼和触媒在高温高压下合成的,是继人造金刚石问世后出现的又一种新型高新技术产品。
它具有很高的硬度、热稳定性和化学惰性,以及良好的透红外形和较宽的禁带宽度等优异性能,它的硬度仅次于金钢石,但热稳定性远高于金钢石,对铁系金属元素有较大的化学稳定性。
立方氮化硼磨具的磨削性能十分优异,不仅能胜任难磨材料的加工,提高生产率,还能有效地提高工件的磨削质量。
立方氮化硼的使用是对金属加工的一大贡献,导致磨削发生革命性变化,是磨削技术的第二次飞跃。
立方氮化硼与金刚石性能比较
项目立方氮化硼金刚石
热稳定性(空气中)/C° 1200-1400 600-850
热膨胀系数/Kˉ1 3.5×10ˉ6 0.9 ×10ˉ6
压缩率/(m2×Nˉ1)2.4 ×10ˉ2 1.4 - 1.8 ×10ˉ2
对铁族化学元素的作用惰性易反应
电阻率(Ω×cm)20C° 1010-1012 1014 -1016
立方氮化硼磨具主要优点:
1、立方氮化硼砂轮硬度高,可以加工高硬度工件,特别是对硬度高、韧性大、高温强度高、热传导率低的材料,具有良好的磨削性能。
2、立方氮化硼砂轮耐用度很高,磨削比可达3500-5500,比普通刚玉砂轮高百倍,比金刚石砂轮高3-5倍。
3、立方氮化硼砂轮比普通刚玉砂轮加工磨削力小,磨削热也小,加工工件应力小,应力层薄,表面精度高,不产生烧伤、裂纹和退火变软现象,并且可以获得残余应力,显著提高工件的疲劳强度,被磨削工件的耐用度能提高30-50%;由于导热性能比刚玉大得多,因而能将磨削热迅速导出,减少工件热变形,磨削容易保持尺寸精度。
4、磨具形状保持性好,修整更换次数少,不但容易保持加工工件精度高,而且大大缩短总的加工时间。
有利于在自动线上加工。
5、同一砂轮通常可磨削不同材料、不同规格的工件,适宜在多品种、小批量生产的柔性数控(CNC)、柔性制造系统(FMS)、微机集成制造时(CIM)使用。
6、立方氮化硼虽然单个磨具价格较高,但由于磨具磨损小、寿命长、加工效率高,分摊到每个工件的成本反而比普通磨具低。
使用立方氮化硼磨具比普通刚玉磨具可降低成本40% 左右。
立方氮化硼磨具与普通刚玉磨具使用成本对比
刚玉磨具立方氮化硼磨具
磨具成本2% 14%
磨削成本53% 35%
处置成本45% 11%
总计100% 60%
立方氮化硼磨具使用范围
1、在自动机床上大批量生产的工件(微型轴承、空压机、曲轴、凸轮轴、高精度螺纹、仪表等)的精磨和终磨。
2、要求磨具具有良好的棱角保持性的复杂型面工件(插齿刀、拉刀、高精度齿轮、靠
模、冲头等)的磨削。
3、大型精密工件(机床导轨、高精度机床丝杠等)的精磨和终磨。
这些工件往往由于磨削温度高而引起较大变形。
4、对由耐热钢、不锈钢、高硬度(HRC55以上)的合金钢制成的精密零件的精磨和终磨。
这些零件用普通磨具时因磨具消耗或磨钝过快而不能获得很高的精度。
5、对特殊钢材如含钨、含钨钼高速钢,钒合金钢、钴合金钢、特种高速钢刀具刃磨,难加工耐热钢工件的超精加工,以及其他钢淬火工具的珩磨。
立方氮化硼磨具分类
根据使用结合剂不同分为陶瓷结合剂、树脂结合剂、电镀金属结合剂、超硬材料金属结合剂磨具。
根据用途可分为通用磨具和专用磨具,通用磨具按其形状分为平行系列、杯形系列、蝶形系列、筒形系列和磨石系列等。
专用磨具有光学精磨片、电解磨轮、光学磨边砂轮、双端面磨盘等。
立方氮化硼砂轮速度
砂轮速度
磨削形式干磨湿磨结合剂备注
平面磨削28-45 20-30 树脂、陶瓷通常用湿式
外圆磨削23-48 20-30 树脂、陶瓷通常用湿式内圆磨削17-28 15-25 树脂、陶瓷通常用湿式
工具磨削22-30 15-28 树脂、陶瓷通常用干式。