金刚石数值砂轮
金刚石砂轮成型模具设计
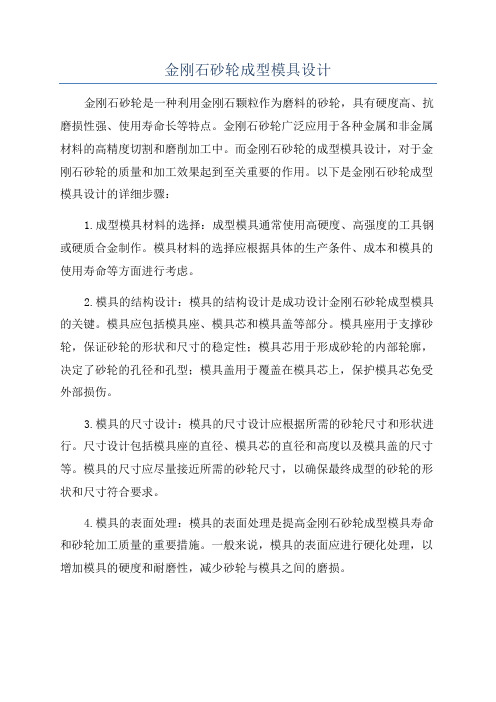
金刚石砂轮成型模具设计金刚石砂轮是一种利用金刚石颗粒作为磨料的砂轮,具有硬度高、抗磨损性强、使用寿命长等特点。
金刚石砂轮广泛应用于各种金属和非金属材料的高精度切割和磨削加工中。
而金刚石砂轮的成型模具设计,对于金刚石砂轮的质量和加工效果起到至关重要的作用。
以下是金刚石砂轮成型模具设计的详细步骤:1.成型模具材料的选择:成型模具通常使用高硬度、高强度的工具钢或硬质合金制作。
模具材料的选择应根据具体的生产条件、成本和模具的使用寿命等方面进行考虑。
2.模具的结构设计:模具的结构设计是成功设计金刚石砂轮成型模具的关键。
模具应包括模具座、模具芯和模具盖等部分。
模具座用于支撑砂轮,保证砂轮的形状和尺寸的稳定性;模具芯用于形成砂轮的内部轮廓,决定了砂轮的孔径和孔型;模具盖用于覆盖在模具芯上,保护模具芯免受外部损伤。
3.模具的尺寸设计:模具的尺寸设计应根据所需的砂轮尺寸和形状进行。
尺寸设计包括模具座的直径、模具芯的直径和高度以及模具盖的尺寸等。
模具的尺寸应尽量接近所需的砂轮尺寸,以确保最终成型的砂轮的形状和尺寸符合要求。
4.模具的表面处理:模具的表面处理是提高金刚石砂轮成型模具寿命和砂轮加工质量的重要措施。
一般来说,模具的表面应进行硬化处理,以增加模具的硬度和耐磨性,减少砂轮与模具之间的磨损。
5.模具的加工工艺:模具加工工艺主要包括切割、钻孔、螺纹加工、磨削和打磨等步骤。
模具的加工过程应严格按照设计要求进行,以确保最终成型的模具能够满足砂轮生产的需要。
6.模具的安装和调试:模具的安装和调试是金刚石砂轮成型模具设计的最后一步。
在安装时,应注意将模具芯正确地安装到模具座上,并调整模具盖的位置和紧固度。
然后,通过试制砂轮,检验成型效果和砂轮的质量。
总之,金刚石砂轮成型模具设计是一项复杂的任务,需要综合考虑材料性能、结构设计、尺寸设计、表面处理、加工工艺等多个因素。
只有合理设计和制造出适用的成型模具,才能保证金刚石砂轮的质量和加工效果。
金刚石树脂砂轮的制造配方【详解】
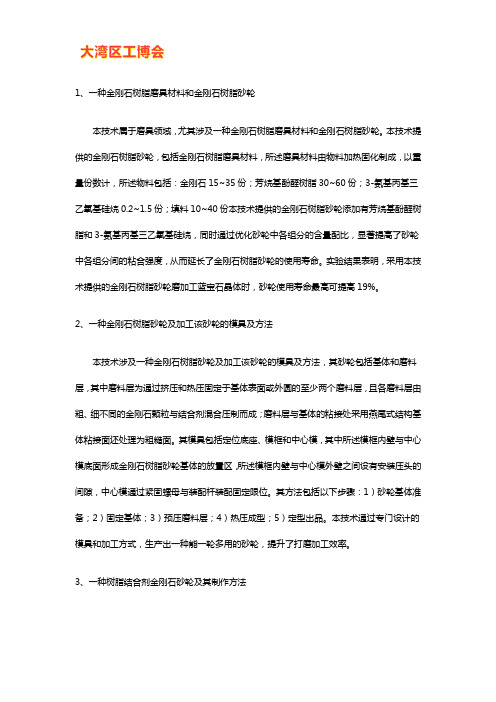
1、一种金刚石树脂磨具材料和金刚石树脂砂轮本技术属于磨具领域,尤其涉及一种金刚石树脂磨具材料和金刚石树脂砂轮。
本技术提供的金刚石树脂砂轮,包括金刚石树脂磨具材料,所述磨具材料由物料加热固化制成,以重量份数计,所述物料包括:金刚石15~35份;芳烷基酚醛树脂30~60份;3-氨基丙基三乙氧基硅烷0.2~1.5份;填料10~40份本技术提供的金刚石树脂砂轮添加有芳烷基酚醛树脂和3-氨基丙基三乙氧基硅烷,同时通过优化砂轮中各组分的含量配比,显著提高了砂轮中各组分间的粘合强度,从而延长了金刚石树脂砂轮的使用寿命。
实验结果表明,采用本技术提供的金刚石树脂砂轮磨加工蓝宝石晶体时,砂轮使用寿命最高可提高19%。
2、一种金刚石树脂砂轮及加工该砂轮的模具及方法本技术涉及一种金刚石树脂砂轮及加工该砂轮的模具及方法,其砂轮包括基体和磨料层,其中磨料层为通过挤压和热压固定于基体表面或外圆的至少两个磨料层,且各磨料层由粗、细不同的金刚石颗粒与结合剂混合压制而成;磨料层与基体的粘接处采用燕尾式结构基体粘接面还处理为粗糙面。
其模具包括定位底座、模框和中心模,其中所述模框内壁与中心模底面形成金刚石树脂砂轮基体的放置区,所述模框内壁与中心模外壁之间设有安装压头的间隙,中心模通过紧固螺母与装配杆装配固定限位。
其方法包括以下步骤:1)砂轮基体准备;2)固定基体;3)预压磨料层;4)热压成型;5)定型出品。
本技术通过专门设计的模具和加工方式,生产出一种能一轮多用的砂轮,提升了打磨加工效率。
3、一种树脂结合剂金刚石砂轮及其制作方法一种树脂结合剂金刚石砂轮及其制作方法,树脂结合剂金刚石砂轮包括设置在基体上的磨料层,磨料层的组份包括金刚石磨料和树脂结合剂,磨料层的组份中还包括填充增强料:铜包铁粉。
磨料层的组份还包括辅助磨料,辅助磨料为碳化硅、碳化硼、白刚玉、单晶刚玉和锆刚玉中的一种或一种以上的组合。
一种树脂结合剂金刚石砂轮,金刚石磨料为5~15%,辅助磨料为10~25%,热固性聚酰亚胺树脂为25~50%,铜包铁粉为3~10%,碳化硅微粉为15~40%,金属氧化物的填料为0~8%,以上分别为磨料层中各物料所占有的体积百分比。
金刚石砂轮生产工艺
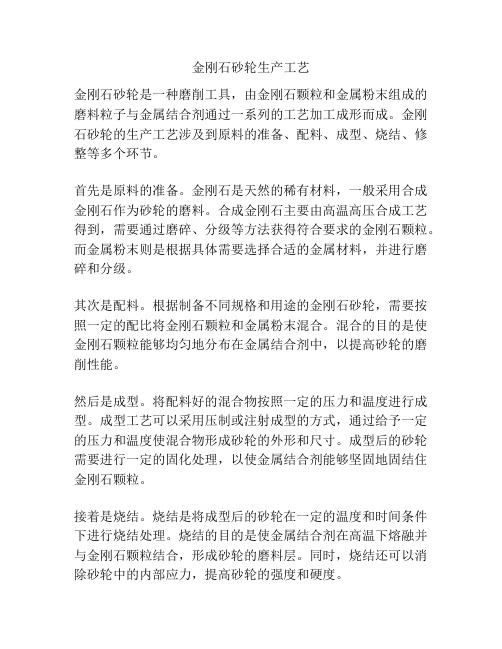
金刚石砂轮生产工艺金刚石砂轮是一种磨削工具,由金刚石颗粒和金属粉末组成的磨料粒子与金属结合剂通过一系列的工艺加工成形而成。
金刚石砂轮的生产工艺涉及到原料的准备、配料、成型、烧结、修整等多个环节。
首先是原料的准备。
金刚石是天然的稀有材料,一般采用合成金刚石作为砂轮的磨料。
合成金刚石主要由高温高压合成工艺得到,需要通过磨碎、分级等方法获得符合要求的金刚石颗粒。
而金属粉末则是根据具体需要选择合适的金属材料,并进行磨碎和分级。
其次是配料。
根据制备不同规格和用途的金刚石砂轮,需要按照一定的配比将金刚石颗粒和金属粉末混合。
混合的目的是使金刚石颗粒能够均匀地分布在金属结合剂中,以提高砂轮的磨削性能。
然后是成型。
将配料好的混合物按照一定的压力和温度进行成型。
成型工艺可以采用压制或注射成型的方式,通过给予一定的压力和温度使混合物形成砂轮的外形和尺寸。
成型后的砂轮需要进行一定的固化处理,以使金属结合剂能够坚固地固结住金刚石颗粒。
接着是烧结。
烧结是将成型后的砂轮在一定的温度和时间条件下进行烧结处理。
烧结的目的是使金属结合剂在高温下熔融并与金刚石颗粒结合,形成砂轮的磨料层。
同时,烧结还可以消除砂轮中的内部应力,提高砂轮的强度和硬度。
最后是修整。
修整是对砂轮进行加工和修整以获得符合要求的产品。
修整包括砂轮的修整和尺寸的修整。
砂轮的修整是根据具体的形状要求,通过切割、磨削等方法将砂轮修整成相应的形状。
尺寸的修整是根据砂轮的精度要求,通过切割和磨削的方法将砂轮修整到合适的尺寸。
综上所述,金刚石砂轮的生产工艺主要包括原料的准备、配料、成型、烧结、修整等环节。
这些环节的精细操作和严格控制可以使金刚石砂轮具有良好的磨削性能和使用寿命。
金刚石砂轮树脂结合剂含量
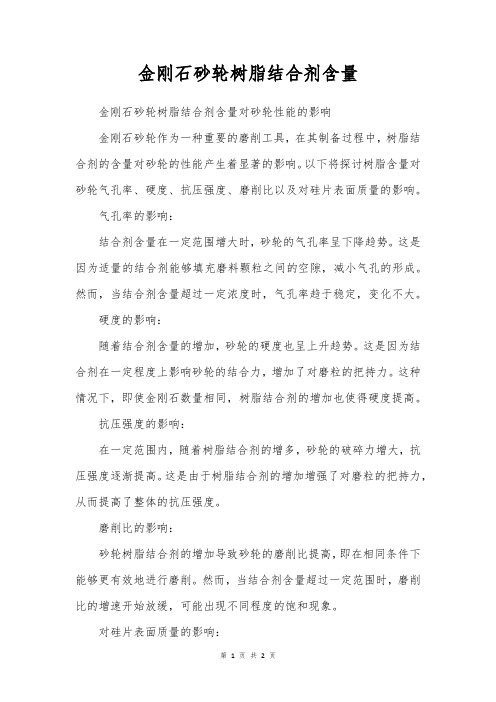
金刚石砂轮树脂结合剂含量金刚石砂轮树脂结合剂含量对砂轮性能的影响金刚石砂轮作为一种重要的磨削工具,在其制备过程中,树脂结合剂的含量对砂轮的性能产生着显著的影响。
以下将探讨树脂含量对砂轮气孔率、硬度、抗压强度、磨削比以及对硅片表面质量的影响。
气孔率的影响:结合剂含量在一定范围增大时,砂轮的气孔率呈下降趋势。
这是因为适量的结合剂能够填充磨料颗粒之间的空隙,减小气孔的形成。
然而,当结合剂含量超过一定浓度时,气孔率趋于稳定,变化不大。
硬度的影响:随着结合剂含量的增加,砂轮的硬度也呈上升趋势。
这是因为结合剂在一定程度上影响砂轮的结合力,增加了对磨粒的把持力。
这种情况下,即使金刚石数量相同,树脂结合剂的增加也使得硬度提高。
抗压强度的影响:在一定范围内,随着树脂结合剂的增多,砂轮的破碎力增大,抗压强度逐渐提高。
这是由于树脂结合剂的增加增强了对磨粒的把持力,从而提高了整体的抗压强度。
磨削比的影响:砂轮树脂结合剂的增加导致砂轮的磨削比提高,即在相同条件下能够更有效地进行磨削。
然而,当结合剂含量超过一定范围时,磨削比的增速开始放缓,可能出现不同程度的饱和现象。
对硅片表面质量的影响:树脂结合剂的含量对硅片表面质量同样产生重要影响。
适量的结合剂有助于提高砂轮的磨削效率,从而改善硅片的表面质量。
然而,过量的结合剂可能导致砂轮性能的饱和,对硅片表面质量的提升效果不再显著。
总体而言,树脂结合剂在金刚石砂轮中的含量调节对砂轮性能具有重要意义。
合理的结合剂含量可以优化砂轮的气孔率、硬度、抗压强度等性能,提高磨削效率,为工业生产和加工提供更加可靠的磨削工具。
在实际应用中,需要根据具体的工艺和要求精确调控结合剂含量,以达到最佳的砂轮性能。
磨具的磨粒率CBN砂轮的浓度计算

普通磨具的配方一般有三种表示方法,一种是以磨料为100% ,其他材料都以占磨料的百分数表示,如表1:表1A F46陶瓷结合剂配方表(%)这种表示方法的优点是:调整配方中任何一项数据时不直接影响其他数据的数值。
例如表1中,硬度H的结合剂量由9%变为10%时,糊精、润湿剂和成型密度仍然可以是2%、2.5%2.15g/cm3。
我国70年代以前的配方大多都不标组织号,但确定组织号的磨粒率可以由配方数据计算出来,如表1中硬度H的配方点磨粒率为:u=γ/d×ΣWu—毛坯磨粒率γ—成型密度d—磨料颗粒密度ΣW—配方百分重量总合u=2.15/3.92×(100+9+2+2.5)%=0.4832≌48%毛坯组织号按磨粒率48%换算:N=(62-48)/2=7即硬度为H的配方点毛坯组织号,N=7陶瓷结合剂磨具配方的另一种表示方法为:磨料百分数与结合剂百分数之和为100%,配方如表2:表2A F60陶瓷结合剂磨具配方表配方表毛坯磨粒率的计算与前例略有不同,如表2中硬度H 配方点的毛坯磨粒率为:u=γ×91.5% /3.92×(91.5+8.5+3+2.8)%=0.4765≌48%由毛坯磨粒率换算成毛坯组织号,N=7此外还有一种配方表是:将不同材质不同粒度的磨具的结合剂量、成型密度、润湿剂等分别列表,结合起来使用。
磨具的成品磨粒率计算比较复杂,参见《陶瓷结合剂砂轮配方》1991。
超硬磨具(金刚石和CBN 磨具)与普通磨具不同的是磨粒率被称为浓度,其含义为在超硬磨具的体积中超硬磨料的体积占25%时,浓度为100% ;超硬磨料的质量以“克拉”为单位,每0.2克为1克拉。
其浓度与质量的关系,见表3:表3 超硬磨料的浓度超硬磨料比较贵重,所以超硬磨具制品的浓度高低对成本和磨削加工都有着明显的影响,一般说浓度高,磨料密度大,耐用度高,磨削效率低;浓度低磨削效率高,耐用度低;但过低的浓度磨料稀疏,磨粒易脱落,效率反而下降,甚至不能正常使用。
穆德魁 钎焊微粉金刚石砂轮制备工艺

穆德魁钎焊微粉金刚石砂轮制备工艺穆德魁钎焊微粉金刚石砂轮制备工艺金刚石砂轮是一种重要的磨削工具,广泛应用于机械加工、磨削和抛光等领域。
为了提高金刚石砂轮的性能,钎焊微粉金刚石砂轮制备工艺应运而生。
本文将介绍穆德魁钎焊微粉金刚石砂轮的制备工艺。
我们需要准备以下材料和设备:微粉金刚石、金刚石基体、钎焊料、砂轮模具、钎焊炉和砂轮机床等。
制备穆德魁钎焊微粉金刚石砂轮的第一步是制备金刚石基体。
金刚石基体是砂轮的主要组成部分,它起到支撑和固定微粉金刚石的作用。
制备金刚石基体的常用方法有热压法、热成型法和电化学法等。
这些方法都可以使金刚石颗粒紧密结合,形成坚固的金刚石基体。
接下来,我们需要将微粉金刚石与钎焊料混合均匀。
微粉金刚石是一种颗粒细小的金刚石粉末,具有较高的磨削性能。
钎焊料是一种能够在高温下熔化并与金刚石基体结合的材料。
混合微粉金刚石和钎焊料的比例需要根据具体要求进行调整,以保证钎焊后微粉金刚石能够均匀分布在金刚石基体上。
然后,我们将混合好的微粉金刚石和钎焊料填充到砂轮模具中。
砂轮模具是用来塑造砂轮形状的工具,它可以根据需要制作不同形状和尺寸的砂轮。
填充时需要注意将混合料填充均匀,并用适当的力量压实,以确保微粉金刚石与金刚石基体紧密结合。
接下来,我们将填充好的砂轮模具送入钎焊炉进行钎焊。
钎焊炉是一种能够提供高温环境的设备,它能够使钎焊料熔化并与金刚石基体和微粉金刚石进行结合。
在钎焊过程中,需要控制好温度和时间,确保钎焊料完全熔化并与金刚石基体形成牢固的连接。
我们将钎焊好的砂轮进行修整和抛光。
修整是为了使砂轮的外形尺寸和形状达到要求,抛光则是为了提高砂轮的表面光洁度和精度。
修整和抛光可以使用砂轮机床进行,通过调整砂轮机床的参数,可以达到理想的修整和抛光效果。
穆德魁钎焊微粉金刚石砂轮制备工艺包括制备金刚石基体、混合微粉金刚石和钎焊料、填充砂轮模具、钎焊、修整和抛光等步骤。
这一工艺能够使微粉金刚石与金刚石基体紧密结合,提高砂轮的性能和使用寿命。
树脂金刚石砂轮的工艺
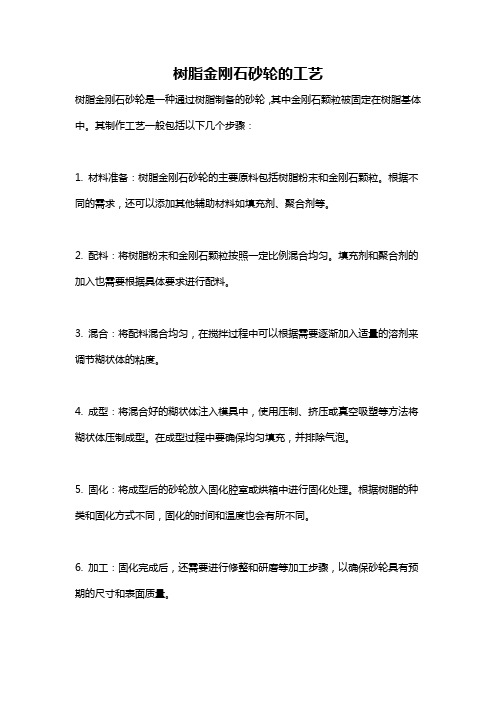
树脂金刚石砂轮的工艺
树脂金刚石砂轮是一种通过树脂制备的砂轮,其中金刚石颗粒被固定在树脂基体中。
其制作工艺一般包括以下几个步骤:
1. 材料准备:树脂金刚石砂轮的主要原料包括树脂粉末和金刚石颗粒。
根据不同的需求,还可以添加其他辅助材料如填充剂、聚合剂等。
2. 配料:将树脂粉末和金刚石颗粒按照一定比例混合均匀。
填充剂和聚合剂的加入也需要根据具体要求进行配料。
3. 混合:将配料混合均匀,在搅拌过程中可以根据需要逐渐加入适量的溶剂来调节糊状体的粘度。
4. 成型:将混合好的糊状体注入模具中,使用压制、挤压或真空吸塑等方法将糊状体压制成型。
在成型过程中要确保均匀填充,并排除气泡。
5. 固化:将成型后的砂轮放入固化腔室或烘箱中进行固化处理。
根据树脂的种类和固化方式不同,固化的时间和温度也会有所不同。
6. 加工:固化完成后,还需要进行修整和研磨等加工步骤,以确保砂轮具有预期的尺寸和表面质量。
7. 质检:对成品砂轮进行严格的质量检测,包括外观检查、尺寸测量、硬度测试、金刚石颗粒的粒度分析等。
8. 包装:经过质检合格的砂轮进行包装和标识,以便存储和运输。
需要注意的是,树脂金刚石砂轮的工艺步骤可能因制造厂家和产品要求的不同而有所差异,上述步骤仅为一般制作过程的参考。
金刚石砂轮精密修整工艺研究
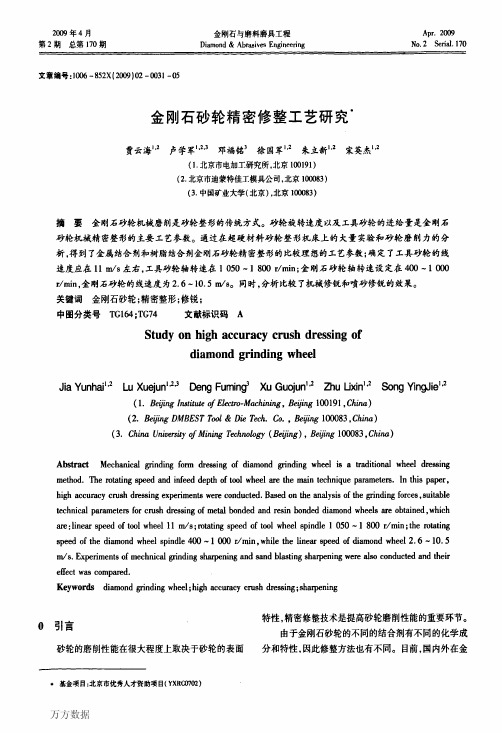
万方数据万方数据万方数据金刚石与磨料磨具丁程总第170期进给量为O.06mm时出现最大值;粒度为180。
的金属结合剂砂轮材料去除率在工具砂轮进给量为0.05mm时出现最大值;粒度为400。
的金属结合剂砂轮材料去除率在-丁具砂轮进给量为0.04mm时出现最大值。
从图4b可以知道粒度为80’的树脂结合剂砂轮材料去除率在工具砂轮进给量为0.05mm时出现最大值;粒度为180。
的树脂结合剂砂轮材料去除率在工具砂轮进给量为0.04mm时出现最大值;粒度为400。
的树脂结合剂砂轮材料去除率在工具砂轮进给量为0.03mm时出现最大值。
比较图4a与图4b可以知道,相同直径、宽度、粒度的金刚石砂轮,金属结合剂金刚石砂轮材料去除率最优值对应的工具砂轮进给量要大于树脂结合剂金刚石砂轮。
图5是实验得到的砂轮磨削能与金刚石材料去除率的关系曲线,从图5可以知道,磨削能与金刚石砂轮材料去除率的关系与工具砂轮进给量与材料去除率的关系是相似的,即工具砂轮最小、最大进给量或最大、最小磨削能时,金刚石砂轮材料去除率均不是最优值,此时的磨削效率均不高。
O1020∞加∞∞70瘩削健/O/-一)图5砂轮磨削能与材料去除率的关系曲线4金刚石砂轮的修锐工艺罔6a是粒度为180。
的金刚石砂轮整形后的局部放大图,图7a是粒度为400。
的金刚石砂轮整形后的局部放大图,可以看到整形后的金刚石砂轮的金刚石颗粒只有少数露出微刃,因此需通过修锐修出金刚石颗粒的微刃。
机械修锐是比较常用的方法,根据前面的分析,在砂轮整形机床上通过改变工具砂轮和金刚石砂轮的线速度比,可以完成金刚石砂轮的修锐。
在超硬材料砂轮整形机床上修整时,将金刚石砂轮的主轴转速提高到1800r/min,这时其线速度达到18.8∥s;将T具砂轮的转速调整到600r/min,这时其线速度达到6.2m/s,调整工具砂轮进给量大约为0.005mm,连续进给三次后,金刚石砂轮修锐后的局部放大图如图6b所示。
- 1、下载文档前请自行甄别文档内容的完整性,平台不提供额外的编辑、内容补充、找答案等附加服务。
- 2、"仅部分预览"的文档,不可在线预览部分如存在完整性等问题,可反馈申请退款(可完整预览的文档不适用该条件!)。
- 3、如文档侵犯您的权益,请联系客服反馈,我们会尽快为您处理(人工客服工作时间:9:00-18:30)。
2.1 总的工艺流程图 根据实际生产,设计总的工艺流程图如图所示。
图总的工艺流程图
2.2 对关键工艺环节的简要说明 2.2.1 配料 配料计算是树脂金刚石砂轮制造中最重要的一个环节,要求准确无误。首先根据砂轮的 规格、形状算出金刚石层体积,然后根据制造数量,按有关公式计算各种原材料的用量。采 用刚玉涂覆的金刚石制造树脂基砂轮的计算方法与采用原始金刚石的计算方法是类似的,不 同之处在于,计算时需考虑金刚石经刚玉涂覆处理后,其表观密度已发生了变化,其对应关 系可见表。图 MBD6 40/50 金刚石在不同小球作用下的破碎情况
4 结论
1)磨削效率:刚玉涂覆的金刚石树脂砂轮比未涂覆刚玉的金刚石树脂砂轮,其磨削效率 提高了 35%。
2)砂轮寿命:刚玉涂覆的金刚石树脂结合剂砂轮比未涂覆的金刚石树脂结合剂制造成本:在不降低加工效率和使用寿命的基础上,可降低制造成本。
参考文献 1 余家国等.三种树脂金刚石砂轮的耐磨性对比试验研究.超硬材料与工程,1995(4):14~16 2 余家国等.超细增韧聚酰亚胺树脂粉在金刚石砂轮中的应用.磨料磨具与磨削,1995(6):19~ 22 3 赵玉成等.刚玉涂覆的超硬材料.金刚石与磨料磨具工程,1999(5):4~6
例 2 采用涂覆金刚石,降低其用量 20%的(树脂结合剂)砂轮:(对比试验) 1)被磨削工件材料:金刚石复合片(聚晶金刚石+YG20~15); 2)机床:M6025 万能工具磨床; 3)磨削参数:砂轮线速度(m/s)20;轴向进给速度 Vf(m/min)0.4;工件速度(m/min)12; 磨削深度:0.008(mm)。
刚玉涂覆的金刚石树脂砂轮的制造及其
应用
066004 燕山大学材料科学与工程学院 赵玉成 臧建兵 王明智
摘要 本文探讨了采用刚玉涂覆的金刚石制造树脂基砂轮的方法,并对比研究了采用不同表面状态的
金刚石所制造的树脂砂轮用于磨削金刚石复合片的实验。结果表明,采用刚玉涂覆的金刚石制造的树脂砂 轮,其工作效率比未采用刚玉涂覆处理的金刚石制造的树脂基砂轮提高了 35%,使用寿命延长 35%以上; 采用涂覆刚玉的金刚石,减少金刚石的实际投放量 20%,其使用性能仍不低于采用原始金刚石制造的树脂 基砂轮。
4)磨削液:硼砂+三乙醇胺+水; 5)砂轮寿命:310~330 件/每片砂轮。
例 3 未涂覆金刚石(树脂结合剂)砂轮:(对比试验) 1)被磨削工件材料:金刚石复合片(聚晶金刚石+YG20~15); 2)机床:M6025 万能工具磨床; 3)磨削参数:砂轮速度(m/s)20;轴向进给速度 Vf(m/min)0.4;工件速度(m/min)12;磨 削深度:0.008(mm)。 4)磨削液:硼砂+三乙醇胺+水; 5)砂轮寿命:290~300 件/每片砂轮。
3 刚玉涂覆的金刚石树脂砂轮的应用实例
砂轮规格: 400×10×25,浓度为 80%的树脂结合剂砂轮 例 1 采用刚玉涂覆的金刚石(树脂结合剂)砂轮: 1)被磨削工件材料:金刚石复合片(聚晶金刚石+YG20~15); 2)机床:M6025 万能工具磨床; 3)磨削参数:砂轮线速度(m/s)20;轴向进给速度 Vf(m/min)0.5;工件速度(m/min)12; 磨削深度:0.01(mm)。 4)磨削液:硼砂+三乙醇胺+水; 5)砂轮寿命:390~420 件/每片砂轮。
主题词 刚玉涂覆 金刚石 树脂砂轮
1 引言
树脂结合剂金刚石砂轮是以金刚石为磨料,树脂粉为粘接剂,加入一些填充材料,通过 配料、混料、热压成型、加工等工艺过程而制成具有一定几何形状的,能适用不同磨削要求 的一种磨加工工具。由于这种砂轮具有弹性好,强度高,耐冲击,生产周期短,在磨削中自 锐性好,不易堵塞,磨削效率高,加工表面光洁度好,从而在工业生产中得到了广泛的应用。 在影响树脂结合剂金刚石砂轮使用性能的各种因素当中,最关键的因素是所采用金刚石的有 关特性。适合于树脂基砂轮的金刚石一般选用 RVD(JR 1)型金刚石,该晶型的金刚石价位 低,表面较粗糙,有利于树脂基体对其的有效把持。但在早期树脂砂轮的制造过程中普遍采 用酚醛树脂,该树脂热稳定性不好,易造成金刚石颗粒早期脱落,使金刚石不能充分发挥磨 削作用。后来普遍采用热稳定性较高的聚酰亚胺树脂,从而使树脂基金刚石砂轮的耐磨性得 到了提高。为进一步提高树脂基金刚石砂轮的性能,自 70 年代以来,国内外开始采用镀镍、 镀铜金刚石用于制造树脂基砂轮,由于金刚石经过镀镍、镀铜处理后,其表面状态发生了巨 大变化,使原始的金刚石表面变为更加粗糙的表面,增加了树脂基体对其的把持作用,从而 使树脂基金刚石砂轮的使用寿命有了一定程度的提高。采用镀镍的金刚石所制造的树脂砂 轮,虽然其使用寿命有了一定程度的提高,但由于经过镀镍处理后,金刚石表面厚厚的镍金 属衣使得原本为脆性材料的金刚石表现出很大的韧性,自锐性变差,从而使其加工效率大大 降低。为此我们研制开发了一种新型的涂覆技术,在金刚石的表面涂覆一层或多层刚玉,使 金刚石经过处理后,其表面形态变为凹凸不平,其表面粗糙程度更甚于镀镍的金刚石的表面 状态。不仅提高了树脂基体对金刚石颗粒的把持力,而且由于刚玉为脆性材料,处理后的金 刚石依然保留了良好的自锐特性,使刚玉涂覆的金刚石树脂砂轮的使用寿命和加工效率均有 很大幅度的提高。
第一作者简介:赵玉成,男,1967 年生,副教授,在读博士。
表刚玉涂覆的金刚石的表观密度与增重之间的关系
2.2.2 热压成型 树脂金刚石砂轮成型主要采用热压成型工艺。其工艺原理为在压制的过程中同时加热砂 轮,使结合剂快速熔化,并在保压时间内缩聚硬化或半硬化。 在热压过程中既要注意成型压力的大小、加压方式的选取、压制速度的确定,又要注意 热压温度和热压时间的选取与确定。