金刚石砂轮成型模具设计
金刚石砂轮成型模具设计
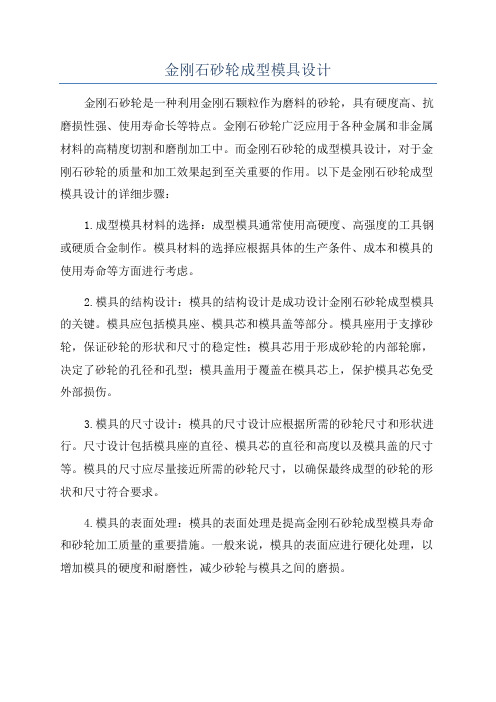
金刚石砂轮成型模具设计金刚石砂轮是一种利用金刚石颗粒作为磨料的砂轮,具有硬度高、抗磨损性强、使用寿命长等特点。
金刚石砂轮广泛应用于各种金属和非金属材料的高精度切割和磨削加工中。
而金刚石砂轮的成型模具设计,对于金刚石砂轮的质量和加工效果起到至关重要的作用。
以下是金刚石砂轮成型模具设计的详细步骤:1.成型模具材料的选择:成型模具通常使用高硬度、高强度的工具钢或硬质合金制作。
模具材料的选择应根据具体的生产条件、成本和模具的使用寿命等方面进行考虑。
2.模具的结构设计:模具的结构设计是成功设计金刚石砂轮成型模具的关键。
模具应包括模具座、模具芯和模具盖等部分。
模具座用于支撑砂轮,保证砂轮的形状和尺寸的稳定性;模具芯用于形成砂轮的内部轮廓,决定了砂轮的孔径和孔型;模具盖用于覆盖在模具芯上,保护模具芯免受外部损伤。
3.模具的尺寸设计:模具的尺寸设计应根据所需的砂轮尺寸和形状进行。
尺寸设计包括模具座的直径、模具芯的直径和高度以及模具盖的尺寸等。
模具的尺寸应尽量接近所需的砂轮尺寸,以确保最终成型的砂轮的形状和尺寸符合要求。
4.模具的表面处理:模具的表面处理是提高金刚石砂轮成型模具寿命和砂轮加工质量的重要措施。
一般来说,模具的表面应进行硬化处理,以增加模具的硬度和耐磨性,减少砂轮与模具之间的磨损。
5.模具的加工工艺:模具加工工艺主要包括切割、钻孔、螺纹加工、磨削和打磨等步骤。
模具的加工过程应严格按照设计要求进行,以确保最终成型的模具能够满足砂轮生产的需要。
6.模具的安装和调试:模具的安装和调试是金刚石砂轮成型模具设计的最后一步。
在安装时,应注意将模具芯正确地安装到模具座上,并调整模具盖的位置和紧固度。
然后,通过试制砂轮,检验成型效果和砂轮的质量。
总之,金刚石砂轮成型模具设计是一项复杂的任务,需要综合考虑材料性能、结构设计、尺寸设计、表面处理、加工工艺等多个因素。
只有合理设计和制造出适用的成型模具,才能保证金刚石砂轮的质量和加工效果。
聚酰亚胺树脂结合剂金刚石砂轮的制造与应用简介

聚酰亚胺树脂结合剂金刚石砂轮的制造与应
用简介
聚酰亚胺树脂结合剂金刚石砂轮是一种新型的超硬材料切削工具,具有高硬度、高耐磨性、高热稳定性和低热膨胀系数等优点,被广泛应用于加工高硬度、高强度、高耐磨材料的工业中。
该砂轮的制备方法包括选择合适的金刚石颗粒和聚酰亚胺树脂作为原料,采用特定比例的混合工艺制备金刚石砂轮药坯,再经过热压成型、回火处理、切割和精加工等工艺步骤,最终形成符合要求的聚酰亚胺树脂结合剂金刚石砂轮。
在应用方面,该砂轮适用于高硬度陶瓷、晶体材料、钢化玻璃、陶瓷基材料、合金材料等的深孔加工、平板加工、槽加工、内外圆加工等领域。
并且,该砂轮具有损耗小、耐用性高、加工效率高、加工质量好等特点,能够满足工业生产中对于高精密度、高质量的加工要求。
聚酰亚胺树脂金刚石砂轮的制造和应用
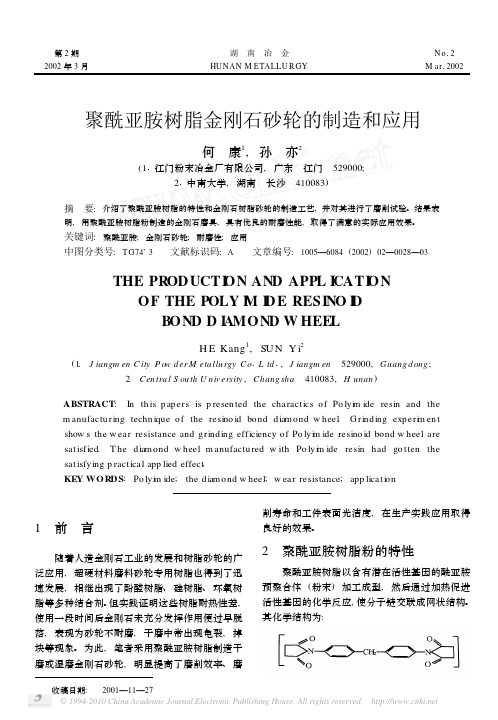
第2期2002年3月湖 南 冶 金HUNAN M ETALLU R GYN o 12M ar 12002收稿日期: 2001—11—27聚酰亚胺树脂金刚石砂轮的制造和应用何 康1,孙 亦2(11江门粉末冶金厂有限公司,广东 江门 529000;21中南大学,湖南 长沙 410083)摘 要:介绍了聚酰亚胺树脂的特性和金刚石树脂砂轮的制造工艺,并对其进行了磨削试验。
结果表明,用聚酰亚胺树脂粉制造的金刚石磨具,具有优良的耐磨性能,取得了满意的实际应用效果。
关键词:聚酰亚胺;金刚石砂轮;耐磨性;应用中图分类号:T G 74+3 文献标识码:A 文章编号:1005—6084(2002)02—0028—03THE PROD UCTI ON AND APPL I CATI ONOF THE POLY I M I D E RESINO I DB OND D I AMOND W HEELH E Kang 1,SU N Y i2(1.J iangm en C ity P o w d er M eta llu rgy Co 1L td 1,J iangm en 529000,Guang d ong ;2.Cen tra l S ou th U n iversity ,Chang sha 410083,H unan )ABSTRACT :In th is papers is p resen ted the charactics of Po lyi m ide resin and them anufactu ring techn ique of the resino id bond diam ond w heel .Grinding experi m en tshow s the w ear resistance and grinding efficiency of Po lyi m ide resino id bond w heel aresatisfied .T he diam ond w heel m anufactu red w ith Po lyi m ide resin had go tten thesatisfying p ractical app lied effect .KEY WOR D S :Po lyi m ide ;the diam ond w heel ;w ear resistance ;app licati on1 前 言随着人造金刚石工业的发展和树脂砂轮的广泛应用,超硬材料磨料砂轮专用树脂也得到了迅速发展,相继出现了酚醛树脂、硅树脂、环氧树脂等多种结合剂。
金刚石树脂砂轮的制造配方【详解】
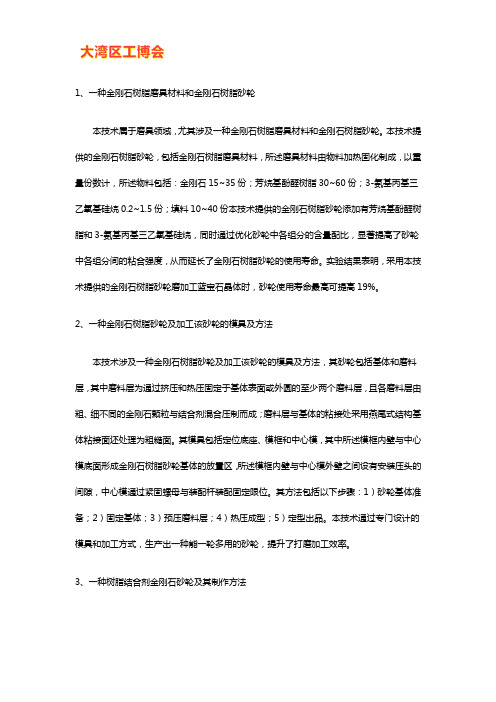
1、一种金刚石树脂磨具材料和金刚石树脂砂轮本技术属于磨具领域,尤其涉及一种金刚石树脂磨具材料和金刚石树脂砂轮。
本技术提供的金刚石树脂砂轮,包括金刚石树脂磨具材料,所述磨具材料由物料加热固化制成,以重量份数计,所述物料包括:金刚石15~35份;芳烷基酚醛树脂30~60份;3-氨基丙基三乙氧基硅烷0.2~1.5份;填料10~40份本技术提供的金刚石树脂砂轮添加有芳烷基酚醛树脂和3-氨基丙基三乙氧基硅烷,同时通过优化砂轮中各组分的含量配比,显著提高了砂轮中各组分间的粘合强度,从而延长了金刚石树脂砂轮的使用寿命。
实验结果表明,采用本技术提供的金刚石树脂砂轮磨加工蓝宝石晶体时,砂轮使用寿命最高可提高19%。
2、一种金刚石树脂砂轮及加工该砂轮的模具及方法本技术涉及一种金刚石树脂砂轮及加工该砂轮的模具及方法,其砂轮包括基体和磨料层,其中磨料层为通过挤压和热压固定于基体表面或外圆的至少两个磨料层,且各磨料层由粗、细不同的金刚石颗粒与结合剂混合压制而成;磨料层与基体的粘接处采用燕尾式结构基体粘接面还处理为粗糙面。
其模具包括定位底座、模框和中心模,其中所述模框内壁与中心模底面形成金刚石树脂砂轮基体的放置区,所述模框内壁与中心模外壁之间设有安装压头的间隙,中心模通过紧固螺母与装配杆装配固定限位。
其方法包括以下步骤:1)砂轮基体准备;2)固定基体;3)预压磨料层;4)热压成型;5)定型出品。
本技术通过专门设计的模具和加工方式,生产出一种能一轮多用的砂轮,提升了打磨加工效率。
3、一种树脂结合剂金刚石砂轮及其制作方法一种树脂结合剂金刚石砂轮及其制作方法,树脂结合剂金刚石砂轮包括设置在基体上的磨料层,磨料层的组份包括金刚石磨料和树脂结合剂,磨料层的组份中还包括填充增强料:铜包铁粉。
磨料层的组份还包括辅助磨料,辅助磨料为碳化硅、碳化硼、白刚玉、单晶刚玉和锆刚玉中的一种或一种以上的组合。
一种树脂结合剂金刚石砂轮,金刚石磨料为5~15%,辅助磨料为10~25%,热固性聚酰亚胺树脂为25~50%,铜包铁粉为3~10%,碳化硅微粉为15~40%,金属氧化物的填料为0~8%,以上分别为磨料层中各物料所占有的体积百分比。
金刚石砂轮生产工艺
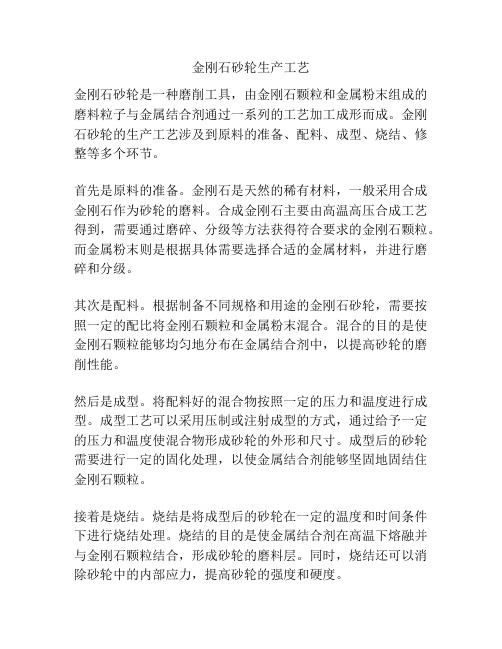
金刚石砂轮生产工艺金刚石砂轮是一种磨削工具,由金刚石颗粒和金属粉末组成的磨料粒子与金属结合剂通过一系列的工艺加工成形而成。
金刚石砂轮的生产工艺涉及到原料的准备、配料、成型、烧结、修整等多个环节。
首先是原料的准备。
金刚石是天然的稀有材料,一般采用合成金刚石作为砂轮的磨料。
合成金刚石主要由高温高压合成工艺得到,需要通过磨碎、分级等方法获得符合要求的金刚石颗粒。
而金属粉末则是根据具体需要选择合适的金属材料,并进行磨碎和分级。
其次是配料。
根据制备不同规格和用途的金刚石砂轮,需要按照一定的配比将金刚石颗粒和金属粉末混合。
混合的目的是使金刚石颗粒能够均匀地分布在金属结合剂中,以提高砂轮的磨削性能。
然后是成型。
将配料好的混合物按照一定的压力和温度进行成型。
成型工艺可以采用压制或注射成型的方式,通过给予一定的压力和温度使混合物形成砂轮的外形和尺寸。
成型后的砂轮需要进行一定的固化处理,以使金属结合剂能够坚固地固结住金刚石颗粒。
接着是烧结。
烧结是将成型后的砂轮在一定的温度和时间条件下进行烧结处理。
烧结的目的是使金属结合剂在高温下熔融并与金刚石颗粒结合,形成砂轮的磨料层。
同时,烧结还可以消除砂轮中的内部应力,提高砂轮的强度和硬度。
最后是修整。
修整是对砂轮进行加工和修整以获得符合要求的产品。
修整包括砂轮的修整和尺寸的修整。
砂轮的修整是根据具体的形状要求,通过切割、磨削等方法将砂轮修整成相应的形状。
尺寸的修整是根据砂轮的精度要求,通过切割和磨削的方法将砂轮修整到合适的尺寸。
综上所述,金刚石砂轮的生产工艺主要包括原料的准备、配料、成型、烧结、修整等环节。
这些环节的精细操作和严格控制可以使金刚石砂轮具有良好的磨削性能和使用寿命。
数控成型磨床砂轮修整器的设计

精密制造与自动化2011年第3期设计与开发数控成型磨床砂轮修整器的设计蔡国英(上海理工大学机械工程学院上海200093)摘 要分析评价了目前使用的修整渐开线、三角形、直齿花键等形状的两轴联动数控修整器,介绍了研制开发的一种新的数控成型砂轮修整器。
详细介绍了采用尖端具有过渡圆弧的金刚石修整器的结构及特点优势。
总结出简化成形砂轮修整的编程过程,避免了复杂的数字控制和软件计算分析,同时可以降低修整器的制造成本,可为数控成型磨床砂轮修整方案设计提供参考。
关键词成型磨削新型砂轮修整器数控修整目前普遍使用的数控花键轴修整器(以MKA8612/H的修整器为例)是两轴联动的数控修整器,它可以通过数控编程来修整砂轮呈渐开线形、三角形、直齿花键等各种形状。
但这种修整器是采用金刚石滚轮来进行修整的,滚轮对砂轮进行修整那部分的工作半径不能太小,因此对砂轮的修整形状也有所限制,如把砂轮修整成内凹或比较尖锐的形状就不能实现。
为了要弥补上述修整器修整功能的不足,最近研制开发了一种新的数控成型砂轮修整器。
1 数控砂轮修整器的结构设计一般来讲,当数控磨床的两个数控移动轴在进行两轴联动时,可以使用单点金刚石修整很简单的成形砂轮轮廓,但对于成形砂轮截面轮廓多变并且斜率变化非常大时,因为修整工具具有一定的厚度,还是可能出现单点金刚石砂轮修整器与砂轮轮廓的干涉。
因此应限制金刚石笔的轴线与成形砂轮轮廓之间的夹角保持在一定的角度范围内可以摆动,这样就可以消除金刚石笔与砂轮轮廓可能发生的干涉现象。
金刚石笔摆动的圆心位置决定数控修整程序中的曲线插补过程,因为随着金刚笔的摆动需要两个移动轴进行补偿运动才能保证修整点按照设定曲线轨迹运动,当金刚笔需要转过一定角度时,必须同时移动两根轴才能保证砂轮修整点位置的不发生变化。
这时可以简单地将金刚笔的摆动圆心设在过渡圆弧的圆心上,这时金刚笔的摆动角度就不会对金刚笔与砂轮修整点的位置产生影响。
修整时金刚笔的摆动中心将沿着砂轮轮廓作等距线的运动,这样就可以简化金刚石砂轮修整器修整轨迹的数控程序设计。
树脂金刚石砂轮的工艺
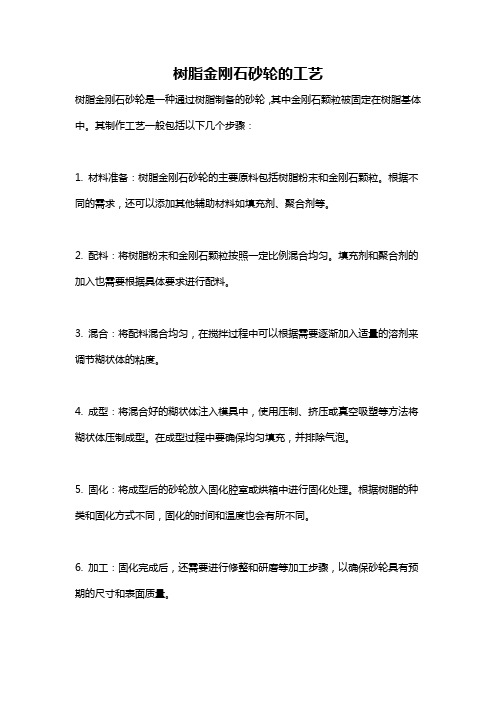
树脂金刚石砂轮的工艺
树脂金刚石砂轮是一种通过树脂制备的砂轮,其中金刚石颗粒被固定在树脂基体中。
其制作工艺一般包括以下几个步骤:
1. 材料准备:树脂金刚石砂轮的主要原料包括树脂粉末和金刚石颗粒。
根据不同的需求,还可以添加其他辅助材料如填充剂、聚合剂等。
2. 配料:将树脂粉末和金刚石颗粒按照一定比例混合均匀。
填充剂和聚合剂的加入也需要根据具体要求进行配料。
3. 混合:将配料混合均匀,在搅拌过程中可以根据需要逐渐加入适量的溶剂来调节糊状体的粘度。
4. 成型:将混合好的糊状体注入模具中,使用压制、挤压或真空吸塑等方法将糊状体压制成型。
在成型过程中要确保均匀填充,并排除气泡。
5. 固化:将成型后的砂轮放入固化腔室或烘箱中进行固化处理。
根据树脂的种类和固化方式不同,固化的时间和温度也会有所不同。
6. 加工:固化完成后,还需要进行修整和研磨等加工步骤,以确保砂轮具有预期的尺寸和表面质量。
7. 质检:对成品砂轮进行严格的质量检测,包括外观检查、尺寸测量、硬度测试、金刚石颗粒的粒度分析等。
8. 包装:经过质检合格的砂轮进行包装和标识,以便存储和运输。
需要注意的是,树脂金刚石砂轮的工艺步骤可能因制造厂家和产品要求的不同而有所差异,上述步骤仅为一般制作过程的参考。
金刚石砂轮精密修整工艺研究
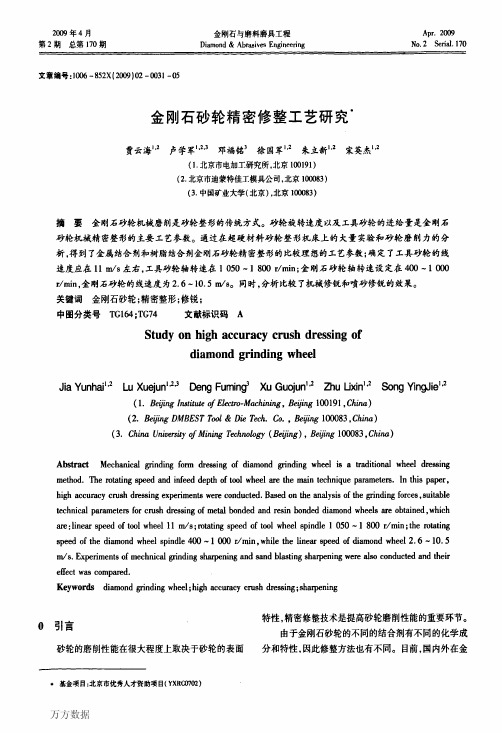
万方数据万方数据万方数据金刚石与磨料磨具丁程总第170期进给量为O.06mm时出现最大值;粒度为180。
的金属结合剂砂轮材料去除率在工具砂轮进给量为0.05mm时出现最大值;粒度为400。
的金属结合剂砂轮材料去除率在-丁具砂轮进给量为0.04mm时出现最大值。
从图4b可以知道粒度为80’的树脂结合剂砂轮材料去除率在工具砂轮进给量为0.05mm时出现最大值;粒度为180。
的树脂结合剂砂轮材料去除率在工具砂轮进给量为0.04mm时出现最大值;粒度为400。
的树脂结合剂砂轮材料去除率在工具砂轮进给量为0.03mm时出现最大值。
比较图4a与图4b可以知道,相同直径、宽度、粒度的金刚石砂轮,金属结合剂金刚石砂轮材料去除率最优值对应的工具砂轮进给量要大于树脂结合剂金刚石砂轮。
图5是实验得到的砂轮磨削能与金刚石材料去除率的关系曲线,从图5可以知道,磨削能与金刚石砂轮材料去除率的关系与工具砂轮进给量与材料去除率的关系是相似的,即工具砂轮最小、最大进给量或最大、最小磨削能时,金刚石砂轮材料去除率均不是最优值,此时的磨削效率均不高。
O1020∞加∞∞70瘩削健/O/-一)图5砂轮磨削能与材料去除率的关系曲线4金刚石砂轮的修锐工艺罔6a是粒度为180。
的金刚石砂轮整形后的局部放大图,图7a是粒度为400。
的金刚石砂轮整形后的局部放大图,可以看到整形后的金刚石砂轮的金刚石颗粒只有少数露出微刃,因此需通过修锐修出金刚石颗粒的微刃。
机械修锐是比较常用的方法,根据前面的分析,在砂轮整形机床上通过改变工具砂轮和金刚石砂轮的线速度比,可以完成金刚石砂轮的修锐。
在超硬材料砂轮整形机床上修整时,将金刚石砂轮的主轴转速提高到1800r/min,这时其线速度达到18.8∥s;将T具砂轮的转速调整到600r/min,这时其线速度达到6.2m/s,调整工具砂轮进给量大约为0.005mm,连续进给三次后,金刚石砂轮修锐后的局部放大图如图6b所示。
- 1、下载文档前请自行甄别文档内容的完整性,平台不提供额外的编辑、内容补充、找答案等附加服务。
- 2、"仅部分预览"的文档,不可在线预览部分如存在完整性等问题,可反馈申请退款(可完整预览的文档不适用该条件!)。
- 3、如文档侵犯您的权益,请联系客服反馈,我们会尽快为您处理(人工客服工作时间:9:00-18:30)。
燕山大学课程设计说明书题目:金刚石砂轮成型模具的设计学院(系):材料科学与工程学院年级专业:10级超硬学号:学生姓名:指导教师:教师职称:教授设计日期:2013.10.28-11.10燕山大学课程设计(论文)任务书院(系):材料科学与工程学院基层教学单位:10级超硬学号学生姓名专业(班级)10级超硬设计题目金刚石砂轮成型模具的设计(杯型砂轮)设计技术参数 1.金刚石砂轮成型模具选用合金工具钢作为模套、定位套、下压环以及上压环的材料。
许用应力[σ]= 5000Kg/ cm ²,波桑系数=0.3。
2.设计杯型砂轮的尺寸为:150×25×10×30。
工作层的厚度为6mm,基体的直径为150mm,工作高度为25mm,凹面高度10mm。
砂轮内径为30mm。
3.结合剂选用金属基结合剂(铁基结合剂),相对密度θ为0.8~0.87,选取θ=0.8,侧压系数=0.38。
4.金属基结合剂单位面积需要压力为4000Kg/cm2,经过计算,压机需要提供的压力大概为176t.正式压制时,压力可以适当取大一些。
设计要求学生必须在规定的期限内完成下述任务:1)规划设计:熟悉设计步骤,确定结构方案。
2) 设计计算:选择所用材料及确定材料的力学性能,根据材料性能及设备功能的要求设计结构尺寸,确定金刚石砂轮模具的生产效率。
3) 绘图:计算机上利用inventer软件4) 编写设计说明书本说明书主要在于设计一套砂轮模具用以大批量生产,结构为杯型砂轮,采用金属基结合剂,模具主要将工作层压制成型,然后经过后处理将工作层焊接于基体上。
工作量技术熟练型员工平均日产500件。
一套模具至少可以正常生产十万件而不出现较大的尺寸误差。
工作计划任务时间安排设计内容规划设计1.5天1.1、布置设计任务书;2、熟悉设计步骤;3、确定结构方案;设计计算2.5天1.选择设备材料;2.确定所需设计设备的基本结构,计算结构尺寸;3.设备能力校验计算;4.使用操作方法说明。
绘图3天1.绘制草图;2.绘制总图;3.绘制零件图。
写说明书2天说明书应使用统一格式的16开纸书写(或B5纸打印),并附有封皮,装订成册。
考核1天面试考核参考资料1.万隆,陈石林,刘小磐主编《超硬材料与工具》北京化学工业出版社出版2.吕智,郑超,莫时雄,章兼植合编《超硬材料工具设计与制造》冶金工业出版社出版3.韩晓娟编《机械设计课程设计指导手册》中国标准出版社4.刘鸿文编《简明材料力学》高等教育出版社出版指导教师签字基层教学单位主任签字说明:此表一式四份,学生、指导教师、基层教学单位、系部各一份。
2013年 11月 5 日目录一、原始数据及资料二、对设计课题的分析三、设计设备的简图四、设计计算五、设计小结六、参考文献设计说明书《超硬材料设备》课程设计是无机非金属材料与工程专业超硬材料专业方向的一门专业方向必修课。
是学生在完成基础课、技术基础课和大部分专业课学习后的一个教学环节,是培养学生应用已学到的理论知识来解决实际工程问题的一次训练,并为毕业设计奠定基础。
在设计过程中,了解和掌握超硬材料设备的设计思想、设计原则和设计方法,即能掌握设计要领,又具有一定的设计能力。
通过设计使学生们对超硬材料设备以及所学过的相关课程进行必要的复习,并在实践中检验学生综合掌握,灵活运用的程度和效果。
通过设计使培养学生熟练运用手册和参考资料的能力,过程中需要涉及电脑中软件的使用,更能培养同学思考以及动手的能力。
一、原始数据及资料选用合金工具钢作为模套、定位套、下压板、上压板以及支撑块和脱模所需的压环的材料。
许用应力[σ]cm,波桑系数=0.3。
=5000Kg/2设计杯型砂轮的尺寸为:150×10×25×6(mm),基体为一个杯型,外径为150mm,工作高度为25mm,凹面厚度为10mm,砂轮内径为30mm。
压制成型后的金刚石层通过焊接的方法焊到基体上,结合剂选用金属基结合剂(铁基结合剂),相对密度θ为0.8~0.85,选取θ=0.8,侧压系数=0.38。
二、设计分析1、零件作用:模具主要由模套,阴模,上下压环,定位块,以及脱模时所需要的支撑块和定位套组成。
各个零件的结构形状和数量则根据砂轮的类型和压制方法确定,各个零件的作用如下:(1)模套:是模具的外套,是关键零件,直接影响砂轮的压制质量。
其厚度受材料自身强度的限制,根据不同材料的许用应力,通过强度计算或经验推算确定。
壁太厚浪费材料,又不便搬运。
模套高度根据砂轮高度和粉末松装密度等因素确定。
材料选用耐热合金钢或球墨铸铁,本模具采用的是合金工具钢。
(2)上压环:是本次杯型砂轮设计中的压制零件,直接承受和传递压力,要求有高的抗压强度、硬度,和适当的韧性传递压力至压腔,提供结合剂压制成型所需的高压强。
(3)下压环:下压环与阴模、定位块构成容纳粉末的压制腔体,,要求有高的耐磨性。
下压环底部支撑模具,起到限位的作用,使压制时在这个位置停下来。
(4)定位套:起固定基体,确定砂轮工作层的厚度。
但是本模具中因为没有基体,所以上下定位套整合成一个,主要目的就是起固定工作层的作用。
(5)支撑块以及定位环:脱模时起支撑作用,是压环及定位套全部脱出,可以直接将制品脱出。
2、模具结构的设计模具结构要根据砂轮的用途和形状以及不同的基体和生产工艺方法来进行设计,其区别于普通磨料磨具的是:(a)所得产品为金刚石砂轮,系超硬工具;(b)结合剂采用的是金属基,即铁粉,不同于普通的陶瓷基砂轮。
因此模具结构和压制操作过程相对复杂。
而且烧结温度比较高,一般达到750-850摄氏度,由于压力以及温度比较高,所以需要基体和金刚石层分开烧结,对材料的耐热和耐磨性都有严格的要求,下面说一下模具零件的设计:A、模套设计:模套从材料力学考虑,实际上它是一个厚壁圆筒,也就是其壁厚至少大于平均直径的十分之一。
因此,按壁厚圆筒的应力计算方法,根据所选材料的许用应力、泊桑比和弹性模量以及砂轮的外径,即可求得模框的外径尺寸。
a 模套外径尺寸的确定:模具在压制过程中,对粉末胚体施加垂直压力,粉末压缩沿着圆周向外膨胀,把压力传递给模框内壁,这叫“侧压力”。
由于受到粉末之间的摩擦力和与内壁之间摩擦力的影响,侧压力总是小于施加的垂直压力。
而侧压力对模框形成径向应力和切向应力,径向应力是压应力,越接近壁厚内径压应力越大;切向应力是拉应力,越接近壁厚内径表面,其值越大。
具体计算过程见下。
b 模套高度的确定:模套高度H由装粉高度h0,上下模冲定位高度h1,h2两部分组成。
装粉高度h0与粉末的松装密度有关,松装密度越小,装粉高度越高。
提高粉末的松装密度可以降低模框的高度,不但节省材料,还可以减少密度梯度,有利操作。
h0一般取胎体厚度的2.5到3.5倍,本设计用3倍。
本模具所压砂轮工作层厚度为6mm,所以h0=18mm,根据需求h1,h2都取8mm,所以H=h0+h1=18+8*2=34mm.c 模套材质的选择:本设计采用合金工具钢。
合金工具钢,是在碳素工具钢基础上加入铬、钼、钨、钒等合金元素以提高淬透性、韧性、耐磨性和耐热性的一类钢种。
它主要用于制造量具、刃具、耐冲击工具和冷、热模具及一些特殊用途的工具。
合金工具钢的淬硬性、淬透性、耐磨性和韧性均比碳素工具钢高,按用途大致可分为刃具、模具和量具用钢3类。
其中碳含量高的钢(碳质量分数大于0.080%)多用于制造刃具、量具和冷作模具,这类钢淬火后的硬度在HRC60以上,且具有足够的耐磨性;碳含量中等的钢(碳质量分数0.35%~0.70%)多用于制造热作模具,这类钢淬火后的硬度稍低,为HRC50~55,但韧性良好。
B、压环设计:cm,压环采用合金工具钢,许用应力为[σ]=5000Kg/2因为压环的外直径就是成型砂轮的外径尺寸,压环的内径为砂轮基体的外径,为150mm,为130mm,上压环高度为14mm,下压环为14mm.C、定位套的设计:定位套主要起固定砂轮基体,限制工作层压缩高度的作用,但是因为不需要基体,所以上下定位套做成一个,其高度根据需求设计为34mm,直径为130mm。
D、脱模所需的支撑块以及定位套:脱模时,需要将上下压模以及阴模和模套分开,这就需要一个定位套放在阴模上方,一个支撑块放在下压膜下,使脱模时阴模脱掉就停止运动。
支撑块高34mm,定位套可以稍微高一点,防止脱模时压到制品,高35mm。
3、模具的使用过程:先将下模、阴模、以及定位套组合到一起,其中下模与其他两个应该有一定的接触长度,然后装料,放上上压模之后放入压机中,开始加压后注意上下压头与模具,当接触时停止加压。
卸模时,将专门的定位环放在阴模上,支撑块放在下模下,接下来继续加压当支撑块全部进入阴模中后停止加压,因为压制层在脱模后,会有一定的膨胀率,所以可以直接从中心定位棒上取下。
三、设计设备的简图四、设计计算:套筒的计算:一、径向计算砂轮直径为150 ㎜,砂轮凹面基体厚度为10 mm,孔为30㎜,套筒内径尺寸为150㎜.求侧向压力以及m值:(1)已知压件材料致密状态下的侧压系数为ε=0.38,相对密度为0.8~0.85,取θ=0.8,压机作用在金刚石层的压力为4000kg/cm²。
根据公式P侧=εθP,可以求得P侧=1216kg/cm²。
单层筒时所需要的m值:m≥﹛[σ]+P侧(1-μ)﹜½÷﹛[σ]-P侧﹙1+μ﹚½对于钢模,其波桑系数=0.3,代入可得m≥1.31,取m=1.4 (2)求K1:P187公式6-22 P58表2-36 P202表6-19P188公式6-28AP202表6-18将m=1.4代入K1=1—[2m²(m—1)]/[(3m+1)(m²+1)],K1=0.90(3)求m组以及模套半径、阴模半径:m组=m≥﹛[σ]+P侧(kⅠ-μ)﹜½÷﹛[σ]-P 侧﹙kⅠ+μ﹚½,可以求得m组=1.27,为了接下来满足强度以及应力要求,取m=1.6砂轮d=150,r=75模套半径R=mr=75*1.6=120mm阴模与模套配合半径r中=(√m)r=√1.6*75=95mm (4)求预紧力:P预=[m﹙m-1﹚÷﹙3m﹢1﹚﹙m+1﹚] P侧代入可得P预=77.5kg/cm²(5)求过盈量Δr中=2P预r中³/E[﹙m²-1﹚÷﹙﹙m²+1﹚r 中²-2R²]求得:Δr中=0.03mm直径过盈量为2Δr中=0.06mm(6)求热装所需温度α为模套材料的线膨胀系数,对于钢材,其值为12.5~13.5*10^(-6),取α=13*10^(-6),t=﹙Δr中+0.1﹚÷αr中=106℃P192公式6-48A P193公式6-49A P192公式6-47BP193公式6-50AP193公式6-51A五设计小结两周的课程设计已经结束,这两周可以说是收获颇丰,我从一开始的连题目都不懂,到最后的可以设计出一个砂轮模具,中间多亏了老师的耐心讲解以及各位好心同学的帮助,我克服了一个又一个困难。