原版 剪板、折弯工件检验标准.wps
折弯通用检验规范
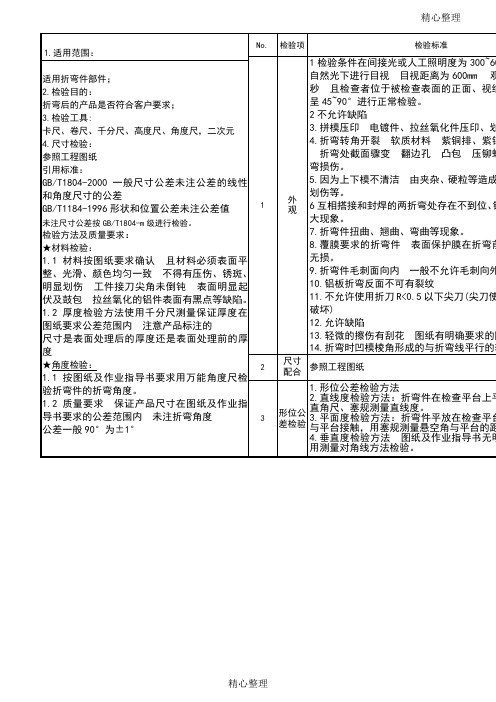
精心整理精心整理1.适用范围:适用折弯件部件; 2.检验目的:折弯后的产品是否符合客户要求; 3.检验工具:卡尺、卷尺、千分尺、高度尺、角度尺,二次元 4.尺寸检验: 参照工程图纸 引用标准:GB/T1804-2000一般尺寸公差未注公差的线性和角度尺寸的公差GB/T1184-1996形状和位置公差未注公差值 未注尺寸公差按GB/T1804-m 级进行检验。
检验方法及质量要求:★材料检验:1.1材料按图纸要求确认且材料必须表面平整、光滑、颜色均匀一致不得有压伤、锈斑、明显划伤工件接刀尖角未倒钝表面明显起伏及鼓包拉丝氧化的铝件表面有黑点等缺陷。
1.2厚度检验方法使用千分尺测量保证厚度在图纸要求公差范围内注意产品标注的尺寸是表面处理后的厚度还是表面处理前的厚度★角度检验:1.1按图纸及作业指导书要求用万能角度尺检验折弯件的折弯角度。
1.2质量要求保证产品尺寸在图纸及作业指导书要求的公差范围内未注折弯角度 公差一般90°为±1°1检验条件在间接光或人工照明度为300~60自然光下进行目视目视距离为600mm 观秒且检查者位于被检查表面的正面、视线呈45~90°进行正常检验。
2不允许缺陷3.拼模压印电镀件、拉丝氧化件压印、划4.折弯转角开裂软质材料紫铜排、紫铜折弯处截面骤变翻边孔凸包压铆螺弯损伤。
5.因为上下模不清洁由夹杂、硬粒等造成划伤等。
6互相搭接和封焊的两折弯处存在不到位、错大现象。
7.折弯件扭曲、翘曲、弯曲等现象。
8.覆膜要求的折弯件表面保护膜在折弯前无损。
9.折弯件毛刺面向内一般不允许毛刺向外10.铝板折弯反面不可有裂纹11.不允许使用折刀R<0.5以下尖刀(尖刀使破坏)12.允许缺陷13.轻微的擦伤有刮花图纸有明确要求的除14.折弯时凹模棱角形成的与折弯线平行的轻1.形位公差检验方法2.直线度检验方法:折弯件在检查平台上平直角尺、塞规测量直线度。
折弯通用检验规范

1.适用范围:适用折弯件部件;2.检验目的:折弯后的产品是否符合客户要求;3.检验工具:卡尺、卷尺、千分尺、高度尺、角度尺,二次元4.尺寸检验:参照工程图纸引用标准:GB/T 1804-2000 一般尺寸公差未注公差的线性和角度尺寸的公差GB/T 1184-1996 形状和位置公差未注公差值未注尺寸公差按GB/T 1804 -m级进行检验。
检验方法及质量要求:★材料检验:1.1材料按图纸要求确认且材料必须表面平整、光滑、颜色均匀一致不得有压伤、锈斑、明显划伤工件接刀尖角未倒钝表面明显起伏及鼓包拉丝氧化的铝件表面有黑点等缺陷。
1.2厚度检验方法使用千分尺测量保证厚度在图纸要求公差范围内注意产品标注的尺寸是表面处理后的厚度还是表面处理前的厚度★角度检验:1.1按图纸及作业指导书要求用万能角度尺检验折弯件的折弯角度。
1.2质量要求保证产品尺寸在图纸及作业指导书要求的公差范围内未注折弯角度公差一般90°为±1°1检验条件在间接光或人工照明度为300~600LUX的近似自然光下进行目视目视距离为600mm观测时间为10秒且检查者位于被检查表面的正面、视线与被检表面呈45~90°进行正常检验。
2不允许缺陷3.拼模压印电镀件、拉丝氧化件压印、划伤。
4.折弯转角开裂软质材料紫铜排、紫铜板、铝板等折弯处截面骤变翻边孔凸包压铆螺母钉折弯损伤。
5.因为上下模不清洁由夹杂、硬粒等造成的表面压伤、划伤等。
6互相搭接和封焊的两折弯处存在不到位、错位及缝隙过大现象。
7.折弯件扭曲、翘曲、弯曲等现象。
8.覆膜要求的折弯件表面保护膜在折弯前后必须完好无损。
9.折弯件毛刺面向内一般不允许毛刺向外。
10.铝板折弯反面不可有裂纹11.不允许使用折刀R<0.5以下尖刀(尖刀使SECC板锌层破坏)12.允许缺陷13.轻微的擦伤有刮花图纸有明确要求的除外。
14.折弯时凹模棱角形成的与折弯线平行的轻微模印。
024剪板折弯件检验标准
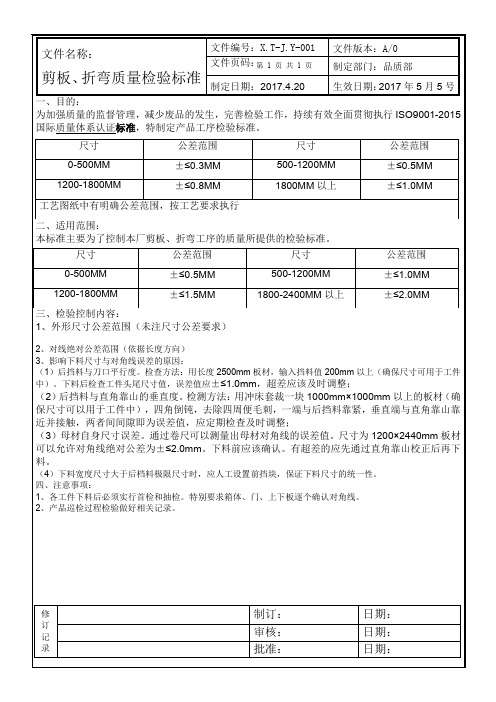
1800-2400MM以上
±≤2.0MM
3、影响下料尺寸与对角线误差的原因:
(1)后挡料与刀口平行度。检查方法:用长度2500mm板材,输入挡料值200mm以上(确保尺寸可用于工件中)。下料后检查工件头尾尺寸值,误差值应±≤1.0mm,超差应该及时调整;
(2)后挡料与直角靠山的垂直度。检测方法:用冲床套裁一块1000mm×1000mm以上的板材(确保尺寸可以用于工件中),四角倒钝,去除四周便毛刺,一端与后挡料靠紧,垂直端与直角靠山靠近并接触,两者间间隙即为误差值,应定期检查及时调整;
一、目的:
为加强质量的监督管理,减少废品的发生,完善检验工作,持续有效全面贯彻执行ISO9001-2015国际质量体系认证标准,特制定产品工序检验标准。
二、适用范围:
本标准主要为了控制本厂剪板、折弯工序的质量所提供的检验标准。
三、检验控制内容:
1、外形尺寸公差范围(未注尺寸公差要求)
尺寸
公差范围
尺寸
2、产品巡检过程检验做好相记录。
公差范围
0-500MM
±≤0.3MM
500-1200MM
±≤0.5MM
1200-1800MM
±≤0.8MM
1800MM以上
±≤1.0MM
工艺图纸中有明确公差范围,按工艺要求执行
2、对线绝对公差范围(依据长度方向)
尺寸
公差范围
尺寸
公差范围
0-500MM
±≤0.5MM
500-1200MM
±≤1.0MM
1200-1800MM
(3)母材自身尺寸误差。通过卷尺可以测量出母材对角线的误差值。尺寸为1200×2440mm板材可以允许对角线绝对公差为±≤2.0mm。下料前应该确认。有超差的应先通过直角靠山校正后再下料。
各工种检验标准

各工种检验标准一、放样、下料和切割1、放样和样板允许偏差2、下料允许偏差1)剪切下料之零件边缘不得有裂纹及超过1。
0之缺棱。
2)气割下料边缘斜度允许偏差:3)钢管下料端面斜度允许偏差4) 板材下料长度或宽度L 允许偏差5)圆钢、钢管及各类型钢,下料长度允许偏差3、切割的允许偏差二、制孔1、 螺栓口的边缘不应有裂纹、飞刺和大于1.5mm 的缺棱。
2、 制孔的允许偏差三、几何尺寸1、单元塔节及单根构件长度L允许偏差见表2、单元塔节整体弯曲矢高f不得大于全长L的1/1000;主柱及横杆局部弯曲不得大于被测长度的1/750;斜腹杆局部弯曲不得大于被测长度的1/350;有焊接节点的平台梁局部弯曲不得大于被测长度的1/500。
四、焊接1、对于重要部位或设计要求的焊缝按50205-95的规定进行二级检验;对于其它部位或设计无要求的焊缝按50205-95的规定进行三级检验。
2、焊缝质量在外观上应符合下列要求:(1)具有平滑的细鳞形表面、无折皱、间断和未焊满的陷槽,并与基本金属平滑连接。
(2)焊缝金属应细密无裂纹、夹渣等缺陷。
(3)焊缝咬边深度不得超过0.5mm,累计总长度不得超过焊缝长度的20%。
(4)对于施焊困难的地方或焊缝高度大于10mm时,焊缝咬边深度不得超过1.0mm,累计总长度不得超过焊缝长度的25%。
五、组装1、组装前,零件、部件应经检查合格;连接接触面和沿焊缝边缘每边30~50mm范围内的铁锈、毛刺、污垢、冰雪等应除干净。
2、板材、型材的拼接,应在组装前进行;构件的组装应在部件组装、焊接、校正后进行。
3、组装顺序应根据结构形式、焊接方法和焊接顺序等因素确定。
4、构件的隐蔽部位应焊接、涂装,并经检查合格后方可封闭;完全封闭的构件内表面可不得涂装。
5、当采用夹具组装时,拆除夹具时不得损伤母材;对残留的焊疤应修磨平整。
6、顶紧接触应有75%以上的面积紧贴,用0.3mm塞尺检查,其塞尺面积应小于25%,边缘间隙不应大于0.8mm。
剪板、开槽、折弯时定额标准(发布版-剪板、开槽、折、铆弯)第1版

剪板、开槽、折弯时定额标准(发布版-剪板、开槽、折、铆弯)第1版LtD剪板、折弯、铆弯工时定额标准前言:为了力求工时定额的公平、公正、合理、平衡,保证时间核定标准的统一性,同时便于快速计算焊接时间,并增强焊接工时核算依据的透明度,工艺部根据国家相关工时定额标准,结合楚天原有的工时定额标准和现行实际情况,特制订此方案与标准。
1 、一般类零件的结构剪板、折弯时间 1.1一般类零件的结构定义一般类结构零件:是指常规产品的〔外表件有电器箱体、门、台板罩〕等结构件零件1.2剪板工时定额计算方法剪板单件工时定额: a —每块工时系数、见表b —剪角次数L0~100100~300 300~600 600~900 900~1200 1200~1500 1500~1800 1800~2100 2100~24002400以上a 0.5 0.6 0.7 0.8 0.9 11.1 1.2 1.3 1.5剪板、毛刺、校正:T 校=k*T 材料系数: K=1.5 重量系数为:B 重量 0~5kg 5~10kg 10~20kg 20~30kg 30~40kg 40~50kg 50~60kg 60~70kg B 1 1.1 1.2 1.3 1.4 1.5 1.6 1.8 重量 70~80kg 80~90kg 90~120kg 120~150kg150~300kg 以上B22.533.54.5举例案例:剪板单件工时厚度:t1, 长度 500 (a0.7+b4×0.23)×k1.5=2.43×B1.1×1.1=2.84 设为3分钟剪板单件工时厚度:t1, 长度 4000 (a1.5+b4×0.5)×k1.5=5.525×b3×1.1=14剪板单件工时厚度:t6, 长度4000 (a1.5+b4×0.5)×k1.5=5.525×B4.5×1.1=25T= k* 〔 a + b a〕31.3不锈钢碳钢材料剪板工时标准(见表1)表1 不锈钢碳钢材料剪板固定工时标准板厚 t长+宽↓ 1 1.2 1.5 2 2.5 3 4 5 60 200 2 2 2 2 2 2 2 2 2201 500 3 3 3 3 3 3 3 3 3501 800 4 4 4 4 4 4 4 4 4801 1000 4 4 4 4 4 4 4 4 41001 1500 5 5 5 5 5 5 5 6 61501 2000 6 6 6 6 6 7 7 9 92001 2500 8 8 8 9 9 9 11 12 132501 3000 11 11 11 11 11 13 13 14 153001 3500 13 13 13 15 15 15 17 17 183501 4000 14 14 14 19 19 19 21 22 251、表内为总工时,长宽各1刀,就高不就低2、单件小批量保底3分钟〔按最终的结果〕,大批量的可以不保底;1.4折弯工时定额计算方法折弯系数表×材料系数表×准备工时系数表=1刀的工时L 0~100 101~200 201~400 401~600 601~800 801~1000 1001~1200 1201~1500 1501~1800 1801~2000 a 0.6 0.7 0.8 0.9 1.1 1.2 1.3 1.4 L 2001~22002201~25002501~30003001~35003501~4000a 1.5 1.6 1.7 1.8 1.9t 1 1.2 1.5 2 3 4 5 6 8 10 12b 1.3 1.5 1.6 1.8 1.9t 1 1.2 1.5 2 3 4 5 6 8 10 12c 1.2 1.41.5 1.82.5举例案例: 折弯单件工时厚度:t1, 长度200 a0.7×b1.2×c1.2 =1分钟/刀折弯单件工时厚度:t1, 长度4000 a1.9×b1.2×c1.2=3分钟/刀折弯单件工时厚度:t5, 长度4000 a1.9×b1.9×c2.5 =10分钟/刀1.4不锈钢碳钢材料折弯工时标准(表表2 不锈钢碳钢材料折弯固定工时标准板厚 t折弯长度↓ 1 1.2 1.5 2 3 4 5 6 8 10 121 100 1 1 1 1 12 2 2 2 2 2101 200 1 1 1 2 2 2 2 2 2 2 2 201 400 1 2 2 2 2 2 2 3 3 3 3 401 600 2 2 2 2 2 2 2 3 3 4 4 601 800 2 2 2 2 2 2 2 3 3 4 4 801 1000 2 2 2 2 3 3 3 3 41001 1200 2 2 2 2 3 3 3 3 41201 1500 2 2 2 3 3 3 3 3 41501 1800 2 2 2 3 3 3 3 4 41801 2000 2 3 3 3 3 3 4 4 52001 2200 2 3 3 3 3 3 4 4 52201 2500 2 3 3 3 4 5 4 5 52501 3000 3 3 3 4 4 4 5 5 73001 3500 3 3 3 4 4 4 5 5 73501 4000 4 5 5 5 6 6 7 7 7注释1、以上数据均为刨槽折弯数据2、对于不刨槽折弯, 1-5mm的板料,按照折弯刀数,增加每刀划线0.25min时间3、对于不刨槽折弯, 5mm以上的板料 ,增加每刀划线0.5min时间.4、折弯系数表(包括折弯操作与折弯后的工件校正的基数)×材料厚度系数表(包括调换上下模具的基数)×准备工时系数表(包括看图计算、手工编程序、上下行程调整的基数)=折弯1刀的工时5、当1-3mm板料相应以下宽度系数计算≥长 1000 宽800 宽度对应折弯长度,按理论计算折弯刀数工时×1.2折弯系数≥长 1500 宽1200 宽度对应折弯长度,按理论计算折弯刀数工时×1.3折弯系数≥长 2500 宽1500 宽度对应折弯长度,按理论计算折弯刀数工时×1.5折弯系数6、当4-8mm板料相应以下宽度系数计算≥长 1000 宽800 宽度对应折弯长度,按理论计算折弯刀数工时×1.8折弯系数≥长 1500 宽1200 宽度对应折弯长度,按理论计算折弯刀数工时×1.9折弯系数≥长 2500 宽1500 宽度对应折弯长度,按理论计算折弯刀数工时×2.5折弯系数图1:举例案例: 折弯单件工时厚度:t2 长度×宽≥长 1000×800 2分钟/刀×4刀=8分钟按理论计算折弯刀数工时×1.2折弯系数=共计10分钟图2:举例案例: 折弯单件工时厚度:t2 长度×宽≥长1000×800 2分钟/刀×8刀=16分钟按理论计算折弯刀数工时×1.2折弯系数=共计19分钟1.6不锈钢碳钢材料刨槽工时标准(见表3)表3 不锈钢碳钢材料刨槽固定工时标准板厚t1.2 1.5 22.5 3槽深及走刀次数0.5(2刀) 0.75(3刀) 1(5刀) 1.25(8刀) 1.5(8刀)刨槽长度↓ 1.2 1.5 2 2.5 30 200 2 2 2 3 3201 500 2 2 2 3 3501 800 2 2 2 3 3801 1000 3 3 3 4 41001 1500 4 4 5 6 61501 2000 5 5 6 8 82001 2500 6 6 8 10 102501 3000 8 8 10 12 123001 3500 ———14 143501 4000 ———16 161、表中工时按每条槽计算;2、一般向内折弯可考虑刨槽,向外折弯不需要;3、接瓶盘之类可能藏污纳垢的零件不刨槽;4、单件小批量保底3分钟,大批量的可以不保底;1.7铆弯工时定额计算方法铆弯系数表*材料厚度系数*准备工时系数表=1个弯边的工时L 0~20 21~40 41~60 61~80 81~100 101~120 121~140 141~160 161~301 301~400 a 1.2 1.4 1.8 2 2.5 3 3.5t 3 4 5 6 8 10 12 16 18 20b 1.8 1.9 2 2.5 3 3.5 4.5 5.5t 3 4 5 6 8 10 12 16 18 20c 1.8 2.5 3.51.8不锈钢碳钢材料铆弯工时标准(表4)表4 不锈钢碳钢板料铆弯固定工时标准t板厚铆弯长宽度3 4 5 6 8 10 12 16 18 20↓0 20 4 4 4 5 6 11 11 14 14 2321 40 5 5 5 6 8 12 12 16 16 2741 60 5 5 5 6 8 12 12 16 16 2761 80 6 6 6 8 10 16 16 20 20 3581 100 6 6 6 8 10 16 16 20 20 35101 120 6 7 7 9 11 18 18 一一一121 140 8 9 9 11 14 22 22 一一一141 160 8 9 9 11 14 一一一一一161 180 8 9 9 11 14 一一一一一181 200 11 12 13 16 19 一一一一一201 220 11 12 13 16 19 一一一一一221 250 11 13 13 16 19 一一一一一251 300 11 12 13 16 19 一一一一一301 350 11 12 13 16 19 一一一一一351 400 11 12 13 16 19 一一一一一注释1、以上数据均为刨槽后铆弯数据,对于不刨槽铆弯,按照铆弯边数量增加1分钟划线/边次2、铆弯系数×材料厚度系数×准备工时系数=铆弯1/边次的工时3、单件小批量与批量的需要做工装的现场工艺员核定另外给予实际的工装制作工时4、≥宽140 宽度对应铆弯,按理论计算铆弯边次数工时×1.5系数1.9铆弯圆料工时定额计算方法铆弯系数*管料系数*准备工时系数=总工时L 0~20 21~40 41~60 61~80 81~100 101~120 121~140 141~160 161~301 301~400 a 1.2 1.4 1.8 2 2.5 3 3.5t 3 4 5 6 8 10 12 16 18 20b 1.8 1.9 2 2.5 3 3.5 4.5 5.5t 3 4 5 6 8 10 12 16 18 20c 1.8 2.5 3.5 2不锈钢碳钢材料铆弯工时标准(表4)表4 不锈钢碳钢圆钢与圆管铆弯固定工时标准管D直径铆弯长度↓ 3 4 5 6 8 10 12 16 18 20 0 20 4 4 4 5 6 11 11 14 14 23 21 40 5 5 5 6 6 12 12 16 16 27 41 60 5 5 5 6 8 12 12 16 16 27 61 80 6 6 6 8 10 16 16 20 20 35 81 100 6 6 6 8 10 16 16 20 20 35 101 120 6 7 7 9 11 18 18 一一一121 140 8 9 9 11 14 22 22 一一一141 160 8 9 9 11 14 一一一一一161 180 8 9 9 11 14 一一一一一181 200 11 12 13 16 19 一一一一一201 220 11 12 13 16 19 一一一一一221 250 11 13 13 16 19 一一一一一251 300 11 12 13 16 19 一一一一一301 350 11 12 13 16 19 一一一一一351 400 11 12 13 16 19 一一一一一注释1、以上数据均为刨槽后铆弯数据,对于不刨槽折弯,按照铆弯边数量增加1分钟划线/边次2、铆弯系数×管材系数×准备工时系数=铆弯1次的工时3、单件小批量与批量的需要做工装的现场工艺员核定另外给予实际的工装制作工时4、≥宽140 宽度对应铆弯,按理论计算铆弯边次数工时×1.5系数注: 根据各工种结构的情况按上表所表列相应的数据,计算工时间定额时, 特殊情况的结构需要根据现场观察核实调整工艺设计部2021年10月31日编制: 会审: 批准:。
折弯工序检验指导书

折弯工序检验指导书一、引言折弯工序是金属加工中常用的一种工艺,用于将金属板材折弯成所需形状。
为了确保折弯过程的准确性和质量,及时发现和纠正可能存在的问题,制定一份折弯工序检验指导书具有重要意义。
本文将介绍折弯工序的基本要求和检验步骤,并提供相应的操作指导,以保证折弯工序的可靠性和稳定性。
二、折弯工序的基本要求1. 产品图纸:在进行折弯加工之前,需要准备好相应的产品图纸。
图纸应清晰明了,包含折弯尺寸、角度和工序要求等信息。
2. 设备准备:确保折弯机及相关设备的正常运转,保证设备的准确性和稳定性。
3. 材料选择:根据产品要求选择合适的金属板材,并确保材料的质量达到要求。
三、折弯工序的检验步骤1. 准备工作:a. 检查折弯机的工作台面是否干净平整,确保无杂质和凹凸不平的情况。
b. 检查折弯模具的安装是否稳固,模具表面是否光滑,确保无划痕和损伤。
c. 检查刀具的状况,如有损坏或磨损应及时更换,确保折弯刀具的锋利度。
2. 材料准备:a. 根据产品图纸的要求,选择合适的金属板材,并进行相应的切割和打磨。
b. 检查金属板材的材质和厚度是否符合要求,如有问题应及时更换。
3. 折弯操作:a. 将金属板材放置在折弯机的工作台面上,并调整好位置。
b. 根据产品图纸的要求,进行折弯角度和尺寸的调整。
c. 注意调整工作台面和夹具的位置,确保金属板材的定位准确。
d. 执行折弯操作,保持稳定的速度和力度,避免过快或过慢产生不良效果。
e. 检查折弯后的产品是否符合要求,包括尺寸、角度和形状等方面。
四、折弯工序的常见问题及纠正措施1. 折弯角度偏差:若折弯角度偏差较大,则需调整折弯机参数或更换合适的模具,以保证折弯角度的准确性。
2. 折弯尺寸不一致:若折弯产品的尺寸不一致,可能是工作台面和夹具的位置调整不准确或者金属板材的定位不稳定。
可通过重新调整位置或改进定位方法来解决问题。
3. 折弯过程中产生划痕:若折弯过程中金属板材表面出现划痕,可能是折弯模具存在问题,应重新检查模具的表面是否平滑,如有问题应更换合适的模具。
折弯工序检验指导书(2023最新版)

折弯工序检验指导书折弯工序检验指导书⒈引言⑴目的本文档旨在提供折弯工序的检验指导,确保产品质量达到要求。
⒉术语和定义⑴折弯工序折弯工序是将金属板材通过机械设备进行弯曲的加工工序。
⑵弯曲角度弯曲角度指在折弯工序中,被弯曲金属板材的所形成的角度。
⒊检验准备⑴检验设备⒊⑴弯曲机用于对金属板材进行弯曲的机械设备。
⒊⑵游标卡尺用于测量金属板材的尺寸。
⒊⑶角度测量仪用于测量金属板材的弯曲角度。
⑵检验环境⒊⑴温度控制检验环境应保持在适宜的温度范围内,避免温度对金属板材弯曲造成影响。
⒊⑵光线条件检验环境应具备良好的光线条件,便于观察和测量。
⒋检验方法⑴样品选择应从批量生产中随机选取若干样品进行检验,样品的数量应符合相关标准的要求。
⑵检验步骤⒋⑴对金属板材进行弯曲在弯曲机上依据工艺要求对金属板材进行弯曲。
⒋⑵测量金属板材的尺寸使用游标卡尺测量弯曲后金属板材的尺寸,与设计要求进行对比。
⒋⑶测量金属板材的弯曲角度使用角度测量仪测量弯曲后金属板材的弯曲角度,与设计要求进行对比。
⒌检验结果⑴合格判定当金属板材的尺寸和弯曲角度与设计要求相符合时,判定为合格。
⑵不合格判定当金属板材的尺寸和弯曲角度与设计要求不符合时,判定为不合格。
⒍附件本文档涉及以下附件:- 样品选择表- 游标卡尺测量数据记录表- 角度测量数据记录表⒎法律名词及注释⑴合格:符合设计要求的标准,符合相关标准的要求。
⑵不合格:不符合设计要求的标准,不符合相关标准的要求。
折弯工序检验指导书

折弯工序检验指导书折弯工序检验指导书1-检验目的1-1 确保折弯工序输出的产品符合要求。
1-2 验证折弯工艺过程是否正确执行。
2-检验范围2-1 所有经过折弯工序的产品均需进行检验。
2-2 检验包括尺寸、外观和质量等方面。
3-检验器材3-1 游标卡尺。
3-2 高度规。
3-3 量规。
3-4 检验板。
3-5 斜尺。
3-6 电子显微镜。
4-检验步骤4-1 检验尺寸4-1-1 使用游标卡尺、高度规和量规对折弯后的产品进行尺寸测量。
4-1-2 比对测量结果与产品要求规定的尺寸范围,记录测量差异。
4-1-3 若测量结果超出规定范围,将产品视为不合格。
4-2 检验外观4-2-1 使用检验板和斜尺检查折弯后产品的外观质量。
4-2-2 检查产品表面是否有划痕、凹陷、变形等表面缺陷。
4-2-3 若发现产品有外观缺陷,将产品视为不合格。
4-3 检验质量4-3-1 使用电子显微镜对折弯后的产品进行质量检查。
4-3-2 检查产品的半成品材料质量、成形质量等方面。
4-3-3 若发现产品有质量缺陷,将产品视为不合格。
5-检验记录5-1 依据检验结果,记录产品的尺寸、外观和质量等方面的数据。
5-2 将检验记录归档并妥善保存。
6-附件本文档涉及附件,请参考附件部分内容。
7-法律名词及注释7-1 折弯工序:将板材按照需要的角度进行折弯,用于形成各种构件的加工过程。
7-2 游标卡尺:一种用于测量长度和间距的测量工具。
7-3 高度规:一种用于测量高度差的测量工具。
7-4 量规:一种用于测量直径、孔径等尺寸的测量工具。
7-5 检验板:用于检查产品外观平整度的辅助工具。
7-6 斜尺:用于检查产品角度和曲线的辅助工具。
7-7 电子显微镜:用于放大、观察并记录微小物件的设备。
- 1、下载文档前请自行甄别文档内容的完整性,平台不提供额外的编辑、内容补充、找答案等附加服务。
- 2、"仅部分预览"的文档,不可在线预览部分如存在完整性等问题,可反馈申请退款(可完整预览的文档不适用该条件!)。
- 3、如文档侵犯您的权益,请联系客服反馈,我们会尽快为您处理(人工客服工作时间:9:00-18:30)。
侧板插接槽
料厚度、下料尺寸
折型尺寸、角度
δ8/Q345
长度(300±2)*
10%
重叠件注意折弯尺寸
长度300为800以上假帮用;长度350为600~700假帮用
10
侧板插接槽
料厚度、下料尺寸
折型尺寸、角度
δ8/Q345
长度:(1280±2)*
10%
重叠件注意折弯尺寸
长度1280为800以上假帮用;长度650为600~750假帮用
首件必检
3
纵梁
料厚度、下料尺寸、折型尺寸、角度
δ8/Q345
长度 ×展开宽度
卡尺
盒尺
30%
“100”范围至“1000 -2”
首件必检
4
平衡支座底板
料厚度、下料尺寸
δ10/Q345
620 *350 =1,对角线差不大于1mm
卡尺
盒尺
10%
5
后尾梁
料厚度、下料尺寸、折型尺寸、角度
δ6/Q345
δ12/Q345
10%
7
上防
护侧
板
料厚度、下料尺寸
δ4
板转立车TY(SFH-670)
卡尺
盒尺
10%
8
上防
护板
料厚度、下料尺寸
δ3
长度 ×宽度,为1.5米板幅宽度的一半
卡尺
盒尺
10%
9
加强
梁
料厚度、下料尺寸
折型尺寸、角度
δ3
650*(178+208)=2,
卡尺
盒尺
10%
注:每日过程检验按以上抽检比例进行,但要确保所投每种车型必须要检查到位。
长度 ×展开宽度 (240/220/210)
卡尺
盒尺
30%
成形板来料尺寸+5、-10mm
首件必检
2
封板
料厚度、下料尺寸、折型尺寸、角度
S6/Q345
长度 ×展开宽度
卡尺
盒尺
30%
3
中横
梁2
料厚度、下料尺寸、折型尺寸、角度
S6/Q345
腿高一致注意区分折形长度 ×展开宽度
卡尺
盒尺
10%
4
中、后横梁
料厚度、下料尺寸、折型尺寸、角度
前板件
序号
工件
名称
检验项目
料厚/材质
检验标准
检验方法
及工具
抽样
方案
备注
1
前板
料厚度、下料尺寸
随订单
宽度 ×高度 ,对角线差小于等于3mm
卡尺
盒尺
10%
成形板来料尺寸+2mm
2
竖梁
料厚度、下料尺寸、折弯尺寸、
δ6
/Q345B
长度 ×展开宽度 ,
卡尺
盒尺
10%
“180 ”范围至“180±1”
3
工作
板
料厚度、下料尺寸
TY(YGJ-780-865)-8600100
首件必检
2
料厚度、下料尺寸
δ6/Q345
500*10=2④加强筋
卡尺盒尺
10%
3
油箱支架总成件
料厚度、下料尺寸、折型尺寸、角度
Δ6
955*130=2, 小槽梁1下料尺寸
238*130=2②小槽梁2下料尺寸
腿高一致(折型尺寸)
卡尺
盒尺
角度尺
20%
TY(YXJ-148)-8600200
卡尺
盒尺
角度尺
10%
注:每日过程检验按以上抽检比例进行,但要确保所投每种车型必须要检查到位。
侧板件
序号
工件
名称
检验项目
料厚/材质
检验标准
检验方法及工具
抽样
方案
备注
1侧板Biblioteka 料厚度、下料尺寸随订单
长度 ×高度 ,对角线差小于3mm
卡尺
盒尺
10%
成形板来料尺寸±5mm
2
前后
立柱
料厚度、下料尺寸
折型尺寸、角度
料厚度、下料尺寸、折型尺寸、角度
δ4
卡尺
盒尺
角度尺
10%
12
假帮侧框
料厚度、下料尺寸、折型尺寸、角度
δ4/Q235
δ6/T610
卡尺
盒尺
角度尺
10%
600以上假帮使用δ6;
300至550使用δ4
注:每日过程检验按以上抽检比例进行,但要确保所投每种车型必须要检查到位。
钳工件:
序号
工件名称
检验项目
料厚/材质
卡尺
盒尺
角度尺
10%
首件必检
8
贯穿梁
料厚度、下料尺寸、折型尺寸、角度
S6/Q345
560*268
卡尺
盒尺
角度尺
100%
9
辅助支撑梁
料厚度、下料尺寸、折型尺寸、角度
S6/Q345
396 *360 保高
卡尺
盒尺
角度尺
10%
10
油缸架支撑梁
料厚度、下料尺寸、折型尺寸、角度
S6/Q345
长度 ×展开宽度 腿高一致注意区分折形
(陕西型轻量化)必保宽度130,长度 ×展开宽度
860 *150 =1
卡尺
盒尺
30%
“130 ”范围至“130 ”
首件必检
6
后翻转座梁
料厚度、下料尺寸、折型尺寸、角度
δ8/Q345
必保130边的尺寸,长度 ×展开宽度
卡尺
盒尺
100%
“130 ”范围至“130 ”
7
安全支
架顶板
料厚度、下料尺寸
δ6/Q345
检验标准
检验方法及工具
抽样
方案
备注
1
油缸支架总成件
料厚度、下料尺寸
折型尺寸、角度
δ8/Q345
1120*266=2①油缸架下料尺寸
368 *110=3,②加强板1加强板2(打孔)
368 *140=1, 368 *180=1③支撑板
必保腿高200 和角度为90±1度
(油缸架折弯尺寸)
卡尺
盒尺
角度尺
20%
TY(PHJ)-0000100
首件必检
12
料厚度、下料尺寸
后翻转连接板,泵架子,挡泥板,锁片、连接板、
后限位、安全支架等下料对角线小于2mm
卡尺盒尺
20%
首件必检
(注:每日过程检验按以上抽检比例进行,但要确保所投每种车型必须要检查到位。)
序号
工件
名称
检验项目
料厚/材质
检验标准
检验方法
及工具
抽样
方案
备注
首件必检
4
料厚度、下料尺寸、折型尺寸、角度
δ6
③槽梁380*190=2 腿高一致
卡尺盒尺
角度尺
20%
5
料厚度、下料尺寸
δ6
④端固定板318*180=1
卡尺盒尺
10%
δ6
⑤固定板318*140=1, 保腿高110
卡尺盒尺
10%
6
料厚度、下料尺寸
δ10
⑥三角撑
卡尺盒尺
10%
7
翻转座件
料厚度、下料尺寸、折型尺寸
500±2*
卡尺
盒尺
角度尺
10%
重叠件注意折形
9
矿用车上框加强角
尺料厚度、下料尺寸、折型尺寸、角度
δ10/Q345
尺寸±1
长度-2
卡尺
盒尺
角度尺
10%
10
假帮边框
料厚度、下料尺寸、折型尺寸、角度
δ6/Q345
δ4/Q345
卡尺
盒尺
角度尺
10%
600以上假帮使用δ6;
300至550使用δ4
11
假帮立柱
1
底板
料厚度、下料尺寸
随订单
长度 ×宽度 ,宽度方向拼接一条焊道时必须小于基准尺寸3mm;两条焊道时必须小于基准尺寸5mm且其中一条宽度小于110mm
卡尺
盒尺
10%
2
纵梁2
料厚度、下料尺寸、折型尺寸、角度
δ8/Q345
长度×宽度 ,长度=纵梁长度+30至+90之间,卧前板和特殊车除外
卡尺
盒尺
30%
“130”范围至“1300 -2”
δ10/Q235
84 *503=2 84 *160=2 84 *90=2
卡尺盒尺
10%
TY(FZZ-ZZ)-0000400
8
平衡架件
料厚度、下料尺寸
δ6/Q345
连接板
1400 ×560 ,板,对角线小于3mm
卡尺盒尺
10%
TY(PHJ)-0000100
9
料厚度、下料尺寸
δ6/Q345
②顶板加强板
1215 ×470 ,板,对角线小于3mm
(纵梁高度为260时使用)首件必检
13
T式支撑梁
料厚度、下料尺寸、折型尺寸、角度
δ8
1180*展开料 或 腿高一致
卡尺
盒尺
100%
14
T式后翻转座
料厚度、下料尺寸、折型尺寸、角度
δ8/Q345
长度580
30%
首件必检
15
T式纵梁
料厚度、下料尺寸、折型尺寸、角度
S8/B510L
长度 ×展开宽度
卡尺
盒尺
30%
特殊车型除外
首件必检
16
封板
料厚度、下料尺寸、折型尺寸、角度