不锈钢管道焊接工艺设计
316不锈钢管道焊接工艺

316不锈钢管道焊接工艺(1)焊接方法:由于现场多数为不锈钢管道且大小不一,根据不锈钢的焊接特点,尽可能减小热输入量,故采用手工电弧焊、氩弧焊两种方法, d >Φ159 mm 的采用氩弧焊打底,手工电弧焊盖面。
d ≦Φ159 mm 的全用氩弧焊。
焊机采用手工电弧焊/氩弧焊两用的WS7 一400 逆变式弧焊机。
(2)焊接材料:奥氏体不锈钢是特殊性能用钢,为满足接头具有相同的性能,应遵循“等成分”原则选择焊接材料,同时为增强接头抗热裂纹和晶间腐蚀能力,使接头中出现少量铁素体,选择HooCr19Ni12Mo2氩弧焊用焊丝,手弧焊用焊条CHSO22 作为填充材料,其成分见表 1 和表2。
表1 焊丝HOOCr19Ni12Mo2化学成分(%)C Si Mn P S Ni Cr Mo0.0120.131.700.0190.00713.2318.722.38表2 焊条CHS022化学成分(%)C Cu Si Mn P S Ni Cr Mo0.030.200.640.750.020.00711.7719.662.05(3)焊接参数。
奥氏体不锈钢的突出特点是对过热敏感,故采用小电流、快速焊,多层焊时要严格控制层间温度,使层间温度小于60 ℃。
具体参数见表 3 。
表3 焊接参数接头形式焊缝层次焊接方法焊接材料焊接电流I/A电弧电压U/V焊接速度v/(cm.min)牌号直径d/mm管对接一层手工钨极氩弧焊HOOCr19Ni12Mo2 2.575-8010-116-83.283-9011-136-8二层手工钨极氩弧焊HOOCr19Ni12Mo2 2.575-8010-116-83.285-9312-136-8手工电弧焊CHS022 2.580-8525-269-12(4 )坡口形式及装配定位焊。
坡口形式采用V 形坡口,由于采用了较小的焊接电流,熔深小,因而坡口的钝边比碳钢小,约为0-0.5 mm,坡口角度比碳钢大,约为65°- 700°,其形式见图l 。
不锈钢管道(EP管)施工工艺
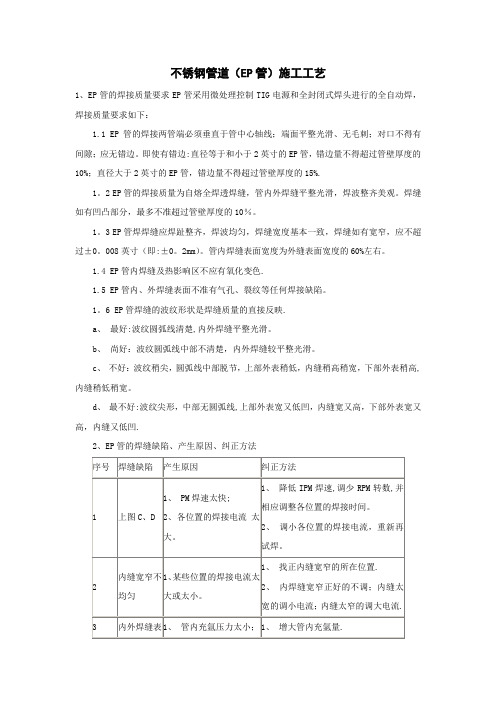
不锈钢管道(EP管)施工工艺1、EP管的焊接质量要求EP管采用微处理控制TIG电源和全封闭式焊头进行的全自动焊,焊接质量要求如下:1.1 EP管的焊接两管端必须垂直于管中心轴线;端面平整光滑、无毛刺;对口不得有间隙;应无错边。
即使有错边:直径等于和小于2英寸的EP管,错边量不得超过管壁厚度的10%;直径大于2英寸的EP管,错边量不得超过管壁厚度的15%.1。
2 EP管的焊接质量为自熔全焊透焊缝,管内外焊缝平整光滑,焊波整齐美观。
焊缝如有凹凸部分,最多不准超过管壁厚度的10%。
1。
3 EP管焊焊缝应焊趾整齐,焊波均匀,焊缝宽度基本一致,焊缝如有宽窄,应不超过±0。
008英寸(即:±0。
2mm)。
管内焊缝表面宽度为外缝表面宽度的60%左右。
1.4 EP管内焊缝及热影响区不应有氧化变色.1.5 EP管内、外焊缝表面不准有气孔、裂纹等任何焊接缺陷。
1。
6 EP管焊缝的波纹形状是焊缝质量的直接反映.a、最好:波纹圆弧线清楚,内外焊缝平整光滑。
b、尚好:波纹圆弧线中部不清楚,内外焊缝较平整光滑。
c、不好:波纹稍尖,圆弧线中部脱节,上部外表稍低,内缝稍高稍宽,下部外表稍高,内缝稍低稍宽。
d、最不好:波纹尖形,中部无圆弧线,上部外表宽又低凹,内缝宽又高,下部外表宽又高,内缝又低凹.2、EP管的焊缝缺陷、产生原因、纠正方法3、EP管的预制3。
1 为了减少安装现场的焊接工作量,确保洁净度,EP管应在自制局部100级洁净室内进行预制.进入预制洁净室的人员必须穿戴洁净服、洁净帽、洁净鞋、洁净手套。
凡必须进入预制洁净室的用具必须擦洗干净.用于EP管加工的工具(如锉、锯、锤等)不准用于碳钢,以防污染。
3.2 工程技术人员按管道总图画分段预制(每段长度6-8m)加工图。
3。
3 有关人员按EP管的质量要求进行开箱检查验收。
开箱时要特别注意严防损坏EP 管.检查项目:EP管质量证明资料齐全,与实物标记完全符合。
不锈钢管道焊接工艺

不锈钢管道焊接工艺1. 引言不锈钢管道作为一种常见的管道材料,具有耐腐蚀、强度高等优点,广泛应用于化工、石油、食品等行业。
而不锈钢管道的焊接工艺是保证管道质量和密封性的关键。
本文将介绍不锈钢管道焊接的常见工艺,包括手工电弧焊接、氩弧焊接和对焊接等,以及各种工艺的特点和适用范围。
同时,还会介绍一些注意事项和常见问题的解决方法,以帮助读者更好地掌握不锈钢管道焊接工艺。
2. 不锈钢管道焊接工艺2.1 手工电弧焊接手工电弧焊接是一种常见的不锈钢管道焊接工艺,适用于一些简单的焊接任务。
其工艺流程如下:1.准备工作:清洁管道表面,确保焊接区域无杂质和油污。
2.安装电弧焊设备:连接电源,安装焊接电极和焊材。
3.打开电源:调节电流和电压,使其适合管道材料和焊接要求。
4.进行焊接:用焊枪在管道连接处进行焊接,形成焊缝。
5.检查焊缝:用目视和尺寸测量工具检查焊缝的质量和尺寸。
手工电弧焊接的优点是操作简便,设备成本低,适用于一些简单的焊接任务。
然而,由于焊接过程中的温度较高,会产生较大的热影响区,可能会导致不锈钢管道的脆化和变形。
2.2 氩弧焊接氩弧焊接是一种常用的不锈钢管道焊接工艺,其工艺流程如下:1.清洁管道表面:确保焊接区域无杂质和油污。
2.安装氩弧焊设备:连接氩气瓶,安装氩弧枪和焊材。
3.打开氩气瓶:调节气体流量,确保焊接区域的保护气体充足。
4.进行焊接:用氩弧枪在管道连接处进行焊接,形成焊缝。
5.检查焊缝:用目视和尺寸测量工具检查焊缝的质量和尺寸。
氩弧焊接的优点是焊接过程中产生的热影响区较小,对管道的变形和脆化影响较小。
同时,氩气可以起到保护作用,防止焊接区域氧化和腐蚀。
2.3 对焊接对焊接是一种将两根管道端连接的不锈钢管道焊接工艺,其工艺流程如下:1.清洁管道表面:确保焊接区域无杂质和油污。
2.安装对焊设备:连接焊接夹具,确保管道端的对称性。
3.进行焊接:将两根管道端对接后,使用焊接夹具将其固定在一起。
4.打开焊机:调节焊接电流和电压,确定焊接参数。
不锈钢管道焊接工艺规程
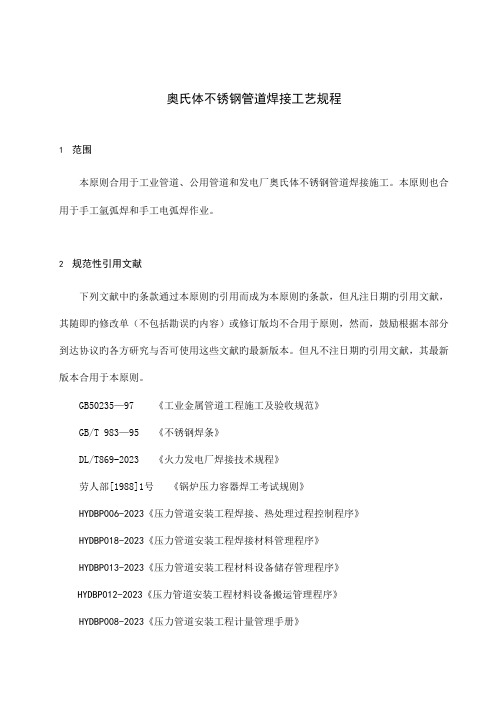
奥氏体不锈钢管道焊接工艺规程1 范围本原则合用于工业管道、公用管道和发电厂奥氏体不锈钢管道焊接施工。
本原则也合用于手工氩弧焊和手工电弧焊作业。
2 规范性引用文献下列文献中旳条款通过本原则旳引用而成为本原则旳条款,但凡注日期旳引用文献,其随即旳修改单(不包括勘误旳内容)或修订版均不合用于原则,然而,鼓励根据本部分到达协议旳各方研究与否可使用这些文献旳最新版本。
但凡不注日期旳引用文献,其最新版本合用于本原则。
GB50235—97 《工业金属管道工程施工及验收规范》GB/T 983—95 《不锈钢焊条》DL/T869-2023 《火力发电厂焊接技术规程》劳人部[1988]1号《锅炉压力容器焊工考试规则》HYDBP006-2023《压力管道安装工程焊接、热处理过程控制程序》HYDBP018-2023《压力管道安装工程焊接材料管理程序》HYDBP013-2023《压力管道安装工程材料设备储存管理程序》HYDBP012-2023《压力管道安装工程材料设备搬运管理程序》HYDBP008-2023《压力管道安装工程计量管理手册》HYDBP007-2023《压力管道安装工程检查和试验控制程序》HYDBP010-2023《压力管道安装工程不合格品控制程序》劳动部发[1996]140号《压力管道安全管理与监察规定》3 先决条件3.1 环境3.1.1 施工环境应符合下列规定:3.1.1.1 风速:手工电弧焊不不小于8M/S,氩弧焊不不小于2M/S。
3.1.1.2 焊接电弧在1m范围内旳相对湿度不不小于90%,环境温度不小于0℃。
3.1.1.3 非下雨、下雪天气。
3.1.2 当环境条件不符合上述规定时,必须采用挡风、防雨、防寒等有效措施。
3.2 奥氏体不锈钢管道焊接控制流程图见图1。
图1 奥氏体不锈钢管道焊接控制流程图3.3 焊接材料3.3.1 奥氏体不锈钢管道焊接材料旳采购和入库(一级库)由企业物资部负责,按《物资采购控制程序》和《焊接材料保管程序》执行。
不锈钢管道焊接及安装工艺

不锈钢管道焊接及安装工艺
不锈钢管道焊接
1为保证施工质量,DN100以下的不锈钢管采用氩弧焊,DN100以上(含DN100)的不锈钢管采用氩电联焊,氩弧焊打底。
2焊接时,管内充氩气保护焊缝及近缝区内表面,管内提前充氩气,排净空气,并保持微弱正压和呈流动状态。
3焊接过程中,填充焊丝的加热端保持在氩气保护之下,息弧后焊丝不得立即暴露在大气中,应在焊缝脱离保护时取出,焊丝如被污染,氧化变色时,污染部分予以切除。
不锈钢管道安装
1不锈钢管道法兰用的非金属垫片,其氯离子含量不得超过50PPm。
2不锈钢管道安装时,不得用铁质工具敲击;不锈钢管与支架之间应垫入不锈钢、不含氯离子的塑料或橡胶垫片,防止不锈钢管与碳素钢直接接触。
3其它要求同中、低压碳素钢管道安装。
4不锈钢管焊口酸洗
(1)管道焊缝的酸洗工作必须保证不损坏金属的未锈蚀表面,并消除其氧化锈蚀部分。
(2)酸洗时,应保持酸洗液的浓度及温度。
(3)酸洗后的不锈钢焊缝以目测检查,呈金属光泽为合格。
(4)酸洗、钝化后的废水、废液,排放前应经处理,以防污染环境。
316L不锈钢焊接工艺

以后有316L 的焊接件一定要按此工艺执行。
焊工资质需由《奥氏体不锈钢合格证》。
316L 不锈钢管道焊接工艺1.焊接准备1.1 焊接方法:根据不锈钢的焊接特点,应尽可能减小热输入量,一般采用手工电弧焊、钨极氩弧焊两种方法,Φ>100 mm 的采用氩弧焊打底加电弧焊填充盖面。
Φ≦100 mm 且壁厚小于5mm 的管道采用全用氩弧焊,壁厚大于等于5mm 的管道采用氩弧打底,电弧焊填充盖面。
1.2 电焊机:由于不锈钢焊接易产生引弧夹钨和收缩气孔需要配备高频引弧和电流衰减特性的专用氩弧焊机。
1.3 焊材:焊丝采用Φ2.5/PP-TIG316L,焊条采用:Φ2.5-3.2/A022,使用前焊丝表面去除氧化层和油污使用丙酮或酒精揩干净;焊条应200-250 ℃烘干1h,存放保温筒内随取随用。
1.4 焊接电流:不锈钢导热效率低,约为碳钢的1/3,电阻率约为碳钢的 5 倍,线膨胀系数比碳钢约大50%,密度大于碳钢,因此焊接电流应小于碳钢焊接电流。
手工电弧焊时焊机采用直流反接,氩弧焊时采用直流正接。
在焊接打底层应尽量采用小直径焊材,小电流,降低焊接线能量,提高熔敷金属的流动性。
因不锈钢导热性能差,故此应选用小电流避免焊条焊接过程中焊芯发红,药皮中气体保护成分过热挥发,造成焊条熔渣保护效果下降。
组对间隙较大的焊缝采用单侧连续送丝焊枪连续摆动,靠液态金属的流动性与另一侧母材熔化结合,防止单侧咬边。
手工电弧焊推荐电流(仅做参考)接头形式焊缝层次焊接方法焊接材料焊接电流I/A 电弧电压V 焊接速度cm/min管对接一层氩弧焊TIG316L φ2.5 75-80 10-11 6-8二层氩弧焊TIG316L φ2.5 75-80 10-11 6-8φ2.5 80-85 25-26 9-12 手工电弧焊A022φ3.2 90-105 25-26 10-151.5 氩气:氩气瓶上应贴有出厂合格标签,使用纯氩≥99.99%或高纯氩≥99.999%,氩弧焊焊接不锈钢时,背面必须充氩气保护,保证背面成形圆滑,防止焊缝根部氧化降低焊缝耐腐蚀性。
316L 不锈钢管道焊接工艺
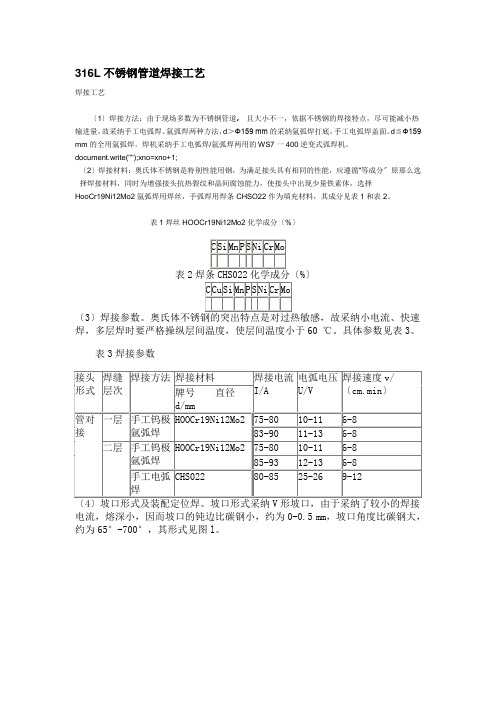
316L不锈钢管道焊接工艺焊接工艺〔1〕焊接方法:由于现场多数为不锈钢管道且大小不一,依据不锈钢的焊接特点,尽可能减小热输进量,故采纳手工电弧焊、氩弧焊两种方法,d>Φ159 mm的采纳氩弧焊打底,手工电弧焊盖面。
d≦Φ159 mm的全用氩弧焊。
焊机采纳手工电弧焊/氩弧焊两用的WS7一400逆变式弧焊机。
document.write("");xno=xno+1;〔2〕焊接材料:奥氏体不锈钢是特别性能用钢,为满足接头具有相同的性能,应遵循“等成分〞原那么选择焊接材料,同时为增强接头抗热裂纹和晶间腐蚀能力,使接头中出现少量铁素体,选择HooCr19Ni12Mo2氩弧焊用焊丝,手弧焊用焊条CHSO22作为填充材料,其成分见表1和表2。
表1焊丝HOOCr19Ni12Mo2化学成分〔%〕C Si Mn P S Ni Cr Mo表2%〕C Cu Si Mn P S Ni Cr Mo〔3焊,多层焊时要严格操纵层间温度,使层间温度小于60 ℃。
具体参数见表3。
表3焊接参数接头形式焊缝层次焊接方法焊接材料焊接电流I/A电弧电压U/V焊接速度v/〔cm.min〕牌号直径d/mm管对接一层手工钨极氩弧焊HOOCr19Ni12Mo275-8010-116-883-9011-136-8二层手工钨极氩弧焊HOOCr19Ni12Mo275-8010-116-885-9312-136-8手工电弧焊CHS02280-8525-269-12电流,熔深小,因而坡口的钝边比碳钢小,约为0-0.5 mm,坡口角度比碳钢大,约为65°-700°,其形式见图l。
图1坡口形式因不锈钢热膨胀系数较大,焊接时产生较大的焊接应力,要求采纳严格的定位焊。
关于d≦Φ89 mm的管采纳两点定位,d=Φ89-Φ219 mm采纳三点定位,d≧219 mm的采纳四点定位;定位焊缝长度6-8 mm。
〔5〕焊接技术要求:①手工电弧焊时焊机采纳直流反接,氩弧焊时采纳直流正接;②焊前应将焊丝用不锈钢丝刷刷掉外表的氧化皮,并用丙酮清洗;焊条应在200-250 ℃烘干1h,随取随用;③焊前将工件坡口两侧25 mm范围内的油污等清理干净,并用丙酮清洗坡口两侧25 mm范围;④氩弧焊时,喷嘴直径Φ2 mm,钨极为钵钨极,规格Φ2.5 mm;⑤氩弧焊焊接不锈钢时,反面必须充氩气保卫,才能保证反面成形。
不锈钢管氩弧焊焊接工艺

不锈钢管氩弧焊焊接工艺一、引言不锈钢管是一种重要的金属管道材料, 广泛应用于石油、化工、制药、食品等工业领域。
在不锈钢管的生产和安装过程中, 氩弧焊是一种常用的焊接工艺。
本文将详细介绍不锈钢管氩弧焊焊接工艺的步骤、注意事项以及常见问题解决方法。
二、不锈钢管氩弧焊的步骤不锈钢管氩弧焊的主要步骤包括准备工作、焊接参数设置、焊接操作和焊后处理。
1.准备工作在进行不锈钢管氩弧焊前, 需要进行以下准备工作:(1)清洁焊接表面: 使用溶剂或刷子清洁不锈钢管的焊接表面, 去除油污、氧化物等杂质, 确保焊缝区域干净。
(2)调整焊机参数:根据不同规格的不锈钢管和焊接材料, 调整焊机的电流、电压和氩气流量等参数。
(3)准备焊接材料:选择合适的焊丝和焊条, 根据管道的材质和规格匹配合适的焊接材料。
2.焊接参数设置在进行不锈钢管氩弧焊时, 需要根据不同的焊接情况设置合适的焊接参数, 包括电流、电压、氩气流量和焊接速度等。
通常情况下, 较薄的不锈钢管采用较小的电流和电压, 较厚的不锈钢管则需要较大的电流和电压。
氩气流量的设置要根据焊接材料的厚度和焊接速度来确定, 保证焊缝周围的氩气保护效果良好。
3.焊接操作进行不锈钢管氩弧焊时, 需要掌握以下操作技巧:(1)焊接位置: 根据不锈钢管的安装位置和焊接需求, 选择合适的焊接位置, 确保焊接操作的方便和焊缝质量的保证。
(2)焊接角度: 保持合适的焊接角度, 使电弧和焊丝与焊缝垂直, 避免焊接变形和焊缝质量问题。
(3)焊接速度:根据焊接材料的厚度和焊接参数的设置, 控制焊接速度, 保证焊缝的均匀和质量。
(4)焊接顺序:根据焊接设计要求, 确定焊接的顺序, 保证焊缝的完整和连接的可靠性。
4.焊后处理不锈钢管氩弧焊完成后, 需要进行焊后处理, 包括焊缝的清洁和封口处理。
焊缝的清洁可以使用刷子或砂纸将焊渣和氧化物清除, 使焊缝表面光滑。
封口处理可以使用不锈钢封口剂或焊接胶带, 确保焊缝的密封性和抗腐蚀性能。
- 1、下载文档前请自行甄别文档内容的完整性,平台不提供额外的编辑、内容补充、找答案等附加服务。
- 2、"仅部分预览"的文档,不可在线预览部分如存在完整性等问题,可反馈申请退款(可完整预览的文档不适用该条件!)。
- 3、如文档侵犯您的权益,请联系客服反馈,我们会尽快为您处理(人工客服工作时间:9:00-18:30)。
不锈钢管道焊接工艺
1 技术特征
1.1材质规格:304( 相当于0Cr18Ni9)
1.2工作介质: 水软水
1.3设计压力:
1.4工作压力:5Kg/CM2
1.5试验压力: 7.5Kg/CM2
2 本工程编制依据
2.1 F43C技术文件.
2.2 国标GB50236-98《现场设备、工业管道焊接工程施工及验收规》2.3 国标GB50235-97《工业金属管道施工及验收规》
2.4 本公司焊接工艺评定报告:HG1
3 焊工
3.1 焊工应具有“锅炉压力容器压力管道焊工考试规则”规定的焊工考试合格证。
3.2 焊工进入现场后应按GB50236-98规定先进行焊接实际操作考试合格,经总包方认可发证后方能担任本项目的焊接工作。
4 焊接检验
4.1焊接检验人员应熟悉F43C技术文件及有关国标和本工艺。
4.2对管材焊材按规定进行检验、填表验收。
4.3对焊工是否执行本工艺进行全面监督检查,对违反者进行教育帮助得以改正。
对严重违反者或教育不改者有权令其停止焊接工作。
以
确保焊接质量。
4.4 做好本工艺第7条“焊接后检查和管理工作”。
4.5 邀请和欢迎总包方和监理方检查人员检查焊接质量。
5 焊前准备
5.1.1 管材、焊材必须具有符合规定的合格证明,并与实物核对无误。
5.1.2 管材型号为304级相当等于我国的0Cr18Ni9规格标准。
按项目图纸规定。
5.1.3 不锈钢焊丝型号规格为:H0Cr20Ni10Ti φ2.5mm φ2.0mm 5.1.4 不锈钢电焊条型号规格:A132 φ3.2mm φ2.5mm
5.1.5 铈钨电极型号规格:WCe-20 φ2.0mm
5.1.6 氩气纯度为99.99%。
5.2 焊件准备
5.2.1 焊接口的分布位置必须符合国标GB50235-97和GB50236-98规
5.2.3焊件坡口应用机械或磨光机加工。
焊口组对前应将坡口及其外表面10mm围的油、垢、毛刺等清理干净。
5.2.4 点固焊必须根部焊透不得有焊接缺陷。
管径≤150 mm为4点长度为5 mm,管径>150 mm为6点,长度为5 mm。
点固焊后即用医用胶布将焊口及两端封好,做好管充氩准备,然后充氩焊接不得隔夜。
5.2.5氩弧焊打底焊接时管必须充氩(氮)保护,并用火柴火苗检查
6 焊接
6.1 焊接设备性能完好.例如:交流弧焊机应有适当的空载电压;焊接电流调节灵活。
氩弧焊机必须具备非接触引弧、提前送气、迟后关气和焊接电流衰减下破功能。
6.2 焊接方法及工艺参数
6.2.1管子规格大于φ57×3.5mm的转动焊采用氩弧焊打底,焊条电弧焊面。
焊接工艺参数如表1:
表 1
注:如管子直径较大时,第二层也可用 A132 φ3.2 焊条,焊接电流为80-100A 6.2.2管子规格小于或等于φ57mm管壁厚不限,转动焊采用氩弧焊,焊接工艺参数如表2:
表 2
可采用1层焊完,不必采用二层焊法。
6.2.3管径管壁厚不限,固定焊,采用氩弧焊,工艺参数如表3:
表 3
注:此参数是焊∮200-250×4mm 的参数。
如壁厚加大,则焊接电流也可适当加大些。
6.3 斯线要接紧在近焊接点。
应在坡口引弧。
防止焊件电弧击伤。
6.4 第一层焊完后,应趁焊缝高温时用不锈钢钢丝刷将焊缝表面刷干净。
并即用湿布速冷后检查焊接质量。
6.5 层间温度应小于60℃。
方能焊接第二层。
焊接完毕后。
(焊条电弧焊盖面层焊接完毕后,应立即清除焊渣,飞溅物。
)同样趁高温时用不锈钢钢丝刷将焊缝表面刷干净,立即用湿布速冷。
自检合格后写上焊工钢印号。
交检验员检查。
并填写好焊接记录。
6.6 对焊缝的质量要求:
6.6.1 焊缝表面不得有:裂纹、气孔、夹渣、未焊透。
咬边深度≤0.5δ,且≤0.5 mm连续长度≤100mm,且两侧咬边总长≤10%焊缝全长。
焊缝表面为全焊透。
6.6.2焊缝外表面高度0-3mm(仰焊可放宽到0-4mm)应力求均匀。
焊缝外表宽度(δ-1)×1.2+间隙宽度+0.5-2.5×2。
7 焊接后检查和管理工作。
7.1 焊工焊完焊口后。
检验员应及时进行检查:
7.1.1 按本工艺6.6条要求检查焊缝外表质量。
7.1.2 检查焊工标记钢印号。
7.1.3检查焊接记录,编上焊口流水号并签字认可。
7.1.4在距焊口30mm显眼处,标记上焊口流水号。
并在图纸上同样位置标记焊口流水号。
使每个焊口的流水号在焊接记录焊口实物及图纸上完全一致。
利于追踪。
7.1.5 邀请总包和监理方检验人员,检查认可焊缝质量。
7.1.6 对检查不合格的焊口应督促焊工清除焊接缺陷。
按原工艺要求进行补焊。
对有严重缺陷不合格或经补焊仍不合格的应向有关人员报告。
分析原因,制定修补措施后进行修补。
确保焊缝修补合格。