不锈钢管道焊接工艺规程
不锈钢管道焊接工艺(完整版)

不锈钢管道焊接工艺1.焊接准备1.1焊接方法:根据不锈钢的焊接特点,应尽可能减小热输入量,一般采用手工电弧焊、钨极氩弧焊两种方法,Φ>100 mm的采用氩弧焊打底加电弧焊填充盖面。
Φ≦100 mm且壁厚小于5mm的管道采用全用氩弧焊,壁厚大于等于5mm的管道采用氩弧打底,电弧焊填充盖面。
1.2电焊机:由于不锈钢焊接易产生引弧夹钨和收缩气孔需要配备高频引弧和电流衰减特性的专用氩弧焊机。
1.3焊材:焊丝采用Φ2.5/PP-TIG316L,焊条采用:Φ2.5-3.2/A022,使用前焊丝表面去除氧化层和油污使用丙酮或酒精揩干净;焊条应200-250 ℃烘干1h,存放保温筒内随取随用。
1.4焊接电流:不锈钢导热效率低,约为碳钢的1/3,电阻率约为碳钢的5倍,线膨胀系数比碳钢约大50%,密度大于碳钢,因此焊接电流应小于碳钢焊接电流。
手工电弧焊时焊机采用直流反接,氩弧焊时采用直流正接。
在焊接打底层应尽量采用小直径焊材,小电流,降低焊接线能量,提高熔敷金属的流动性。
因不锈钢导热性能差,故此应选用小电流避免焊条焊接过程中焊芯发红,药皮中气体保护成分过热挥发,造成焊条熔渣保护效果下降。
组对间隙较大的焊缝采用单侧连续送丝焊枪连续摆动,靠液态金属的流动性与另一侧母材熔化结合,防止单侧咬边。
手工电弧焊推荐电流(仅做参考)管对接一层氩弧焊TIG316L φ2.5 75-80 10-11 6-8二层氩弧焊TIG316L φ2.5 75-80 10-11 6-8φ2.5 80-85 25-26 9-12手工电弧焊A022φ3.2 90-105 25-26 10-151.5氩气:氩气瓶上应贴有出厂合格标签,使用纯氩≥99.99%或高纯氩≥99.999%,氩弧焊焊接不锈钢时,背面必须充氩气保护,保证背面成形圆滑,防止焊缝根部氧化降低焊缝耐腐蚀性。
气瓶中的氩气不能用尽,瓶内余压不得低于0.5MPa。
大管道采用在管道内局部充氩的方法,跟随焊接进度保护,流量为5-14L/min,正面氩气流量为12-13L/min。
1.2mm的不锈钢管子的焊接工艺

1.2mm的不锈钢管子的焊接工艺
焊接不锈钢管子需要特别的工艺和注意事项,以确保焊接质量
和管道的持久性。
首先,选择合适的焊接方法对于不锈钢管子至关
重要。
常用的方法包括TIG(氩弧焊)、MIG(气体保护焊)、电阻
焊等。
在选择焊接方法时,需要考虑管道的材质、厚度和管道用途
等因素。
其次,焊接不锈钢管子时,需要特别注意保护性气体的选择和
流量控制。
对于TIG焊接,使用惰性气体(通常是氩气)进行保护,以防止氧气和其他杂质进入焊接区域,从而避免产生氧化和腐蚀。
对于MIG焊接,同样需要保护性气体来保护焊接区域。
另外,焊接电流和电压的选择也是关键。
对于不锈钢管子,通
常需要较低的电流和电压,以避免产生过多的热量导致变形或者焊
接区域的氧化。
焊接速度也需要适当控制,以确保焊缝的质量和外观。
此外,还需要注意焊接工艺中的预热和后热处理。
对于较大直
径或者壁厚的不锈钢管子,通常需要进行预热以减少焊接应力和避
免裂纹的产生。
焊接完成后,还需要进行适当的后热处理,以消除
残余应力并提高焊接接头的性能。
最后,焊接不锈钢管子时,还需要严格控制焊接工艺参数,包括焊接速度、焊接角度、焊接层间间隙等。
同时,还需要进行焊后的检测和评价,以确保焊接质量符合相关标准和要求。
总之,焊接不锈钢管子需要综合考虑材料特性、焊接方法、工艺参数等多个因素,以确保焊接质量和管道的使用性能。
希望以上信息能够帮助你更好地理解不锈钢管子的焊接工艺。
不锈钢管焊接工艺规程
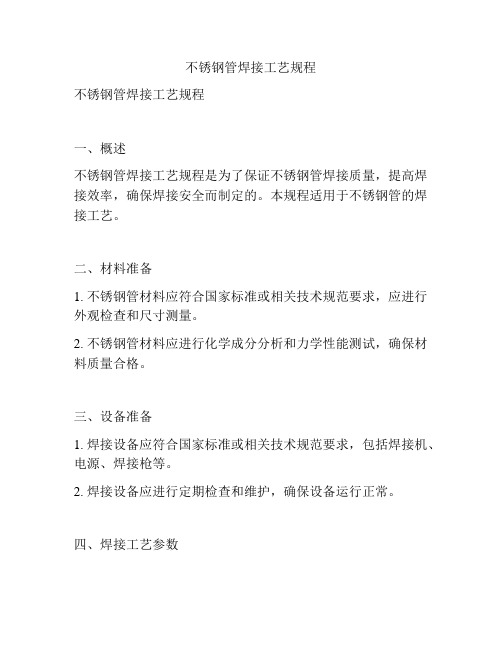
不锈钢管焊接工艺规程不锈钢管焊接工艺规程一、概述不锈钢管焊接工艺规程是为了保证不锈钢管焊接质量,提高焊接效率,确保焊接安全而制定的。
本规程适用于不锈钢管的焊接工艺。
二、材料准备1. 不锈钢管材料应符合国家标准或相关技术规范要求,应进行外观检查和尺寸测量。
2. 不锈钢管材料应进行化学成分分析和力学性能测试,确保材料质量合格。
三、设备准备1. 焊接设备应符合国家标准或相关技术规范要求,包括焊接机、电源、焊接枪等。
2. 焊接设备应进行定期检查和维护,确保设备运行正常。
四、焊接工艺参数1. 焊接电流和电压应根据不锈钢管的材料和壁厚确定,确保焊接质量。
2. 焊接速度应根据不锈钢管的材料和壁厚确定,确保焊缝的均匀性。
3. 焊接温度应控制在合适的范围内,避免过高或过低导致焊接缺陷。
五、焊接操作1. 焊工应熟悉不锈钢管的焊接工艺要求和操作规程,严格按照规程进行操作。
2. 焊工应佩戴防护设备,包括焊接面罩、手套等,确保个人安全。
3. 焊工应注意焊接过程中的熔渣和气孔等缺陷,及时进行修补或更换焊条。
六、焊后处理1. 焊接完成后,应对焊缝进行外观检查和尺寸测量,确保焊缝质量合格。
2. 焊缝表面应进行清理和抛光处理,使其达到要求的光洁度。
3. 焊缝应进行无损检测,确保焊接质量合格。
七、质量控制1. 焊接过程中应进行质量控制,包括焊缝外观、尺寸、化学成分等方面的检查。
2. 焊接过程中出现问题时,应及时进行调整和修正,确保焊接质量。
3. 焊接完成后应进行质量评定,确保焊接质量符合要求。
八、安全措施1. 在焊接过程中应注意防止火花飞溅和烟尘产生,保持工作环境清洁。
2. 焊接过程中应注意防止电击和火灾等事故的发生,确保人身安全。
3. 在操作不锈钢管时应注意防止划伤和损坏管材,确保材料完好。
九、总结不锈钢管焊接工艺规程是确保不锈钢管焊接质量的重要文件,通过严格执行规程要求,可以提高焊接效率,降低焊接风险,保证焊接安全。
各相关单位和人员应严格按照本规程要求进行操作,共同维护不锈钢管焊接质量。
不锈钢管道焊接工艺规程
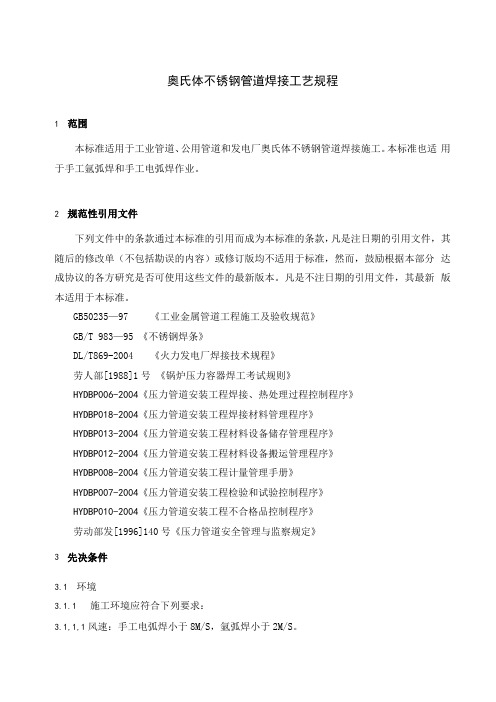
奥氏体不锈钢管道焊接工艺规程1范围本标准适用于工业管道、公用管道和发电厂奥氏体不锈钢管道焊接施工。
本标准也适用于手工氩弧焊和手工电弧焊作业。
2规范性引用文件下列文件中的条款通过本标准的引用而成为本标准的条款,凡是注日期的引用文件,其随后的修改单(不包括勘误的内容)或修订版均不适用于标准,然而,鼓励根据本部分达成协议的各方研究是否可使用这些文件的最新版本。
凡是不注日期的引用文件,其最新版本适用于本标准。
GB50235—97 《工业金属管道工程施工及验收规范》GB/T 983—95 《不锈钢焊条》DL/T869-2004 《火力发电厂焊接技术规程》劳人部[1988]1号《锅炉压力容器焊工考试规则》HYDBP006-2004《压力管道安装工程焊接、热处理过程控制程序》HYDBP018-2004《压力管道安装工程焊接材料管理程序》HYDBP013-2004《压力管道安装工程材料设备储存管理程序》HYDBP012-2004《压力管道安装工程材料设备搬运管理程序》HYDBP008-2004《压力管道安装工程计量管理手册》HYDBP007-2004《压力管道安装工程检验和试验控制程序》HYDBP010-2004《压力管道安装工程不合格品控制程序》劳动部发[1996]140号《压力管道安全管理与监察规定》3先决条件3.1环境3.1.1施工环境应符合下列要求:3.1,1,1风速:手工电弧焊小于8M/S,氩弧焊小于2M/S。
3.1.1.2焊接电弧在1m范围内的相对湿度小于90%,环境温度大于0℃。
3.1.1.3非下雨、下雪天气。
3.1.2当环境条件不符合上述要求时,必须采取挡风、防雨、防寒等有效措施。
3.2奥氏体不锈钢管道焊接控制流程图见图1。
图1 奥氏体不锈钢管道焊接控制流程图3.3焊接材料3.3.1奥氏体不锈钢管道焊接材料的采购和入库(一级库)由公司物资部负责,按《物资采购控制程序》和《焊接材料保管程序》执行。
不锈钢管道焊接程序

目的为了不锈钢管道焊接工艺进程的有效操纵和顺利实施,以确保工程焊接质量。
1.适用范围本工艺适用于铬镍奥氏体不锈钢管道、铁镍合金、镍合金管道及工业炉管的焊接施工和预制。
2.相关文件工业金属管道工程施工及验收标准GB50235 — 97现场设备、工业管道焊接工程施工及验收标准GB50236 — 98石油化工剧毒、可燃介质管道工程施工及验收标准SHJ3501 — 20023.先决条件3.1焊接材料不锈钢管道焊接所用的焊接材料应有出厂质量证明书,其查验项目和技术指标应符合以下要求:3.1.1不锈钢焊条应符合《不锈钢焊条》GB/T 983-95的规定。
3.1.2不锈钢焊丝应符合《焊接用不锈钢丝》GB/T 5092-96的规定或《惰性气体爱惜焊接用不锈钢棒及钢丝》GB/T 5091-93中的规定。
3.1.3高温合金焊丝应符合《焊接用高温合金冷拔丝》GB184-84中的规定。
3.1.4国内其它焊接材料及国外焊接材料应符合合同规定的技术标准。
3.1.5焊材的验收、贮存和保管,依照常规要求进行。
3.1.6非熔化极气体爱惜焊宜采铈钨极棒,并应符合《惰性气体爱惜电弧焊和等离子焊接、切割用钨铈电极》GB4194中的规定。
爱惜用氩气应具有合格证,并注明纯度。
3.2焊前预备3.2.1焊接工艺评定依照设计要求,安排焊接工艺评定。
3.2.2焊工要求参加不锈钢管道焊接的焊工,必需按评定合格的焊接工艺和不锈钢压力管道焊接规程的要求同意考试,持考试合格证者方能承担焊接施工任务。
3.2.3坡口加工及检查3.2.3.1不锈钢管子切割及坡口加工,应采纳机械方式或等离子切割,并清理加工表面。
3.2.3.2坡口加工后应进行外观检查,坡口表面不得有裂纹、分层等缺点。
3.2.3.3假设设计要求对坡口表面进行无损查验时,应按设计规定执行,发觉缺点应及时排除。
3.2.4焊件组对3.2.4.1管子组对前,应用手工或机械化方式清理其内外表面,在坡口边缘20mm范围内不得有油漆、毛刺、铸造垢皮及其它对焊接有害的物质。
不锈钢管对接工艺流程
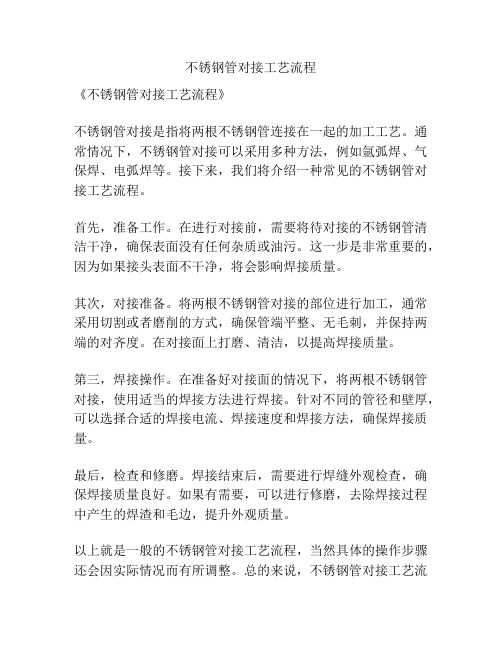
不锈钢管对接工艺流程
《不锈钢管对接工艺流程》
不锈钢管对接是指将两根不锈钢管连接在一起的加工工艺。
通常情况下,不锈钢管对接可以采用多种方法,例如氩弧焊、气保焊、电弧焊等。
接下来,我们将介绍一种常见的不锈钢管对接工艺流程。
首先,准备工作。
在进行对接前,需要将待对接的不锈钢管清洁干净,确保表面没有任何杂质或油污。
这一步是非常重要的,因为如果接头表面不干净,将会影响焊接质量。
其次,对接准备。
将两根不锈钢管对接的部位进行加工,通常采用切割或者磨削的方式,确保管端平整、无毛刺,并保持两端的对齐度。
在对接面上打磨、清洁,以提高焊接质量。
第三,焊接操作。
在准备好对接面的情况下,将两根不锈钢管对接,使用适当的焊接方法进行焊接。
针对不同的管径和壁厚,可以选择合适的焊接电流、焊接速度和焊接方法,确保焊接质量。
最后,检查和修磨。
焊接结束后,需要进行焊缝外观检查,确保焊接质量良好。
如果有需要,可以进行修磨,去除焊接过程中产生的焊渣和毛边,提升外观质量。
以上就是一般的不锈钢管对接工艺流程,当然具体的操作步骤还会因实际情况而有所调整。
总的来说,不锈钢管对接工艺流
程需要在准备工作和焊接操作上严格把关,确保最终的焊接质量。
不锈钢管道焊接工艺标准规范标准
|不锈钢管道焊接工艺1技术特征1.1材质规格:304(相当于0Cr18Ni9)1.2工作介质:空气去离子水1.3 设计压力:0.2MPa,0.4MPa1.4 工作压力:2Kg/CMf 4Kg/cM1.5 试验压力:4.6Kg/CM 22本工程编制依据2.1 F43C技术文件.2.2国标GB50236-98《现场设备、工业管道焊接工程施工及验收规范》2.3国标GB50235-97《工业金属管道施工及验收规范》2.4本公司焊接工艺评定报告:HG13焊工3.1焊工应具有“锅炉压力容器压力管道焊工考试规则”规定的焊工考试合格证。
3.2焊工进入现场后应按GB50236-98规定先进行焊接实际操作考试合格,经总包方认可发证后方能担任本项目的焊接工作。
4焊接检验4.1焊接检验人员应熟悉F43C技术文件及有关国标和本工艺。
4.2对管材焊材按规定进行检验、填表验收。
4.3对焊工是否执行本工艺进行全面监督检查,对违反者进行教育帮助得以改正。
对严重违反者或教育不改者有权令其停止焊接工作。
以确保焊接质量。
4.4做好本工艺第7条“焊接后检查和管理工作”。
4.5邀请和欢迎总包方和监理方检查人员检查焊接质量。
5焊前准备5.1.1管材、焊材必须具有符合规定的合格证明,并与实物核对无误。
5.1.2管材型号为304级相当等于我国的0Cr18Ni9规格标准。
按项目图纸规定。
5.1.3 不锈钢焊丝型号规格为:H0Cr20Ni10Ti © 2.5mm © 2.0mm5.1.4 不锈钢电焊条型号规格:A132 © 3.2mm © 2.5mm5.1.5 铈钨电极型号规格:WCe-20 © 2.0mm5.1.6 氩气纯度为99.99 %。
5.2 焊件准备5.2.1焊接口的分布位置必须符合国标GB50235-97和GB50236-98规范的规定。
5.2.2管道为V型坡口,对接接头、组对应符合图1要求:注:间隙3.5〜4mm为焊接时的数据,组对点固焊时,应适当大于此数据,以补收缩图1.焊口组对数据523焊件坡口应用机械或磨光机加工。
不锈钢管道焊接工艺
不锈钢管道焊接工艺1. 引言不锈钢管道作为一种常见的管道材料,具有耐腐蚀、强度高等优点,广泛应用于化工、石油、食品等行业。
而不锈钢管道的焊接工艺是保证管道质量和密封性的关键。
本文将介绍不锈钢管道焊接的常见工艺,包括手工电弧焊接、氩弧焊接和对焊接等,以及各种工艺的特点和适用范围。
同时,还会介绍一些注意事项和常见问题的解决方法,以帮助读者更好地掌握不锈钢管道焊接工艺。
2. 不锈钢管道焊接工艺2.1 手工电弧焊接手工电弧焊接是一种常见的不锈钢管道焊接工艺,适用于一些简单的焊接任务。
其工艺流程如下:1.准备工作:清洁管道表面,确保焊接区域无杂质和油污。
2.安装电弧焊设备:连接电源,安装焊接电极和焊材。
3.打开电源:调节电流和电压,使其适合管道材料和焊接要求。
4.进行焊接:用焊枪在管道连接处进行焊接,形成焊缝。
5.检查焊缝:用目视和尺寸测量工具检查焊缝的质量和尺寸。
手工电弧焊接的优点是操作简便,设备成本低,适用于一些简单的焊接任务。
然而,由于焊接过程中的温度较高,会产生较大的热影响区,可能会导致不锈钢管道的脆化和变形。
2.2 氩弧焊接氩弧焊接是一种常用的不锈钢管道焊接工艺,其工艺流程如下:1.清洁管道表面:确保焊接区域无杂质和油污。
2.安装氩弧焊设备:连接氩气瓶,安装氩弧枪和焊材。
3.打开氩气瓶:调节气体流量,确保焊接区域的保护气体充足。
4.进行焊接:用氩弧枪在管道连接处进行焊接,形成焊缝。
5.检查焊缝:用目视和尺寸测量工具检查焊缝的质量和尺寸。
氩弧焊接的优点是焊接过程中产生的热影响区较小,对管道的变形和脆化影响较小。
同时,氩气可以起到保护作用,防止焊接区域氧化和腐蚀。
2.3 对焊接对焊接是一种将两根管道端连接的不锈钢管道焊接工艺,其工艺流程如下:1.清洁管道表面:确保焊接区域无杂质和油污。
2.安装对焊设备:连接焊接夹具,确保管道端的对称性。
3.进行焊接:将两根管道端对接后,使用焊接夹具将其固定在一起。
4.打开焊机:调节焊接电流和电压,确定焊接参数。
不锈钢管道焊接工艺(附示意图)
316L 不锈钢管道焊接工艺焊接工艺(1)焊接方法:由于现场多数为不锈钢管道且大小不一,根据不锈钢的焊接特点,尽可能减小热输入量,故采用手工电弧焊、氩弧焊两种方法,d >Φ159 mm 的采用氩弧焊打底,手工电弧焊盖面。
d ≦Φ159 mm 的全用氩弧焊。
焊机采用手工电弧焊/氩弧焊两用的WS7 一400 逆变式弧焊机。
document.write("");xno = xno+1;(2)焊接材料:奥氏体不锈钢是特殊性能用钢,为满足接头具有相同的性能,应遵循“等成分”原则选择焊接材料,同时为增强接头抗热裂纹和晶间腐蚀能力,使接头中出现少量铁素体,选择HooCr19Ni12Mo2氩弧焊用焊丝,手弧焊用焊条CHSO22 作为填充材料,其成分见表1 和表2。
表1 焊丝HOOCr19Ni12Mo2化学成分(%)(3)焊接参数。
奥氏体不锈钢的突出特点是对过热敏感,故采用小电流、快速焊,多层焊时要严格控制层间温度,使层间温度小于60 ℃ 。
具体参数见表3 。
表3 焊接参数(4 )坡口形式及装配定位焊。
坡口形式采用V 形坡口,由于采用了较小的焊接电流,熔深小,因而坡口的钝边比碳钢小,约为0-0.5 mm,坡口角度比碳钢大,约为65°- 700°,其形式见图l 。
图1 坡口形式因不锈钢热膨胀系数较大,焊接时产生较大的焊接应力,要求采用严格的定位焊。
对于d≦Φ89 mm 的管采用两点定位,d=Φ89-Φ219 mm采用三点定位,d≧219 mm 的采用四点定位;定位焊缝长度6-8 mm。
(5)焊接技术要求:① 手工电弧焊时焊机采用直流反接,氩弧焊时采用直流正接;② 焊前应将焊丝用不锈钢丝刷刷掉表面的氧化皮,并用丙酮清洗;焊条应在200-250 ℃ 烘干1h,随取随用;③ 焊前将工件坡口两侧25 mm 范围内的油污等清理干净,并用丙酮清洗坡口两侧25 mm 范围;④ 氩弧焊时,喷嘴直径Φ2 mm , 钨极为钵钨极,规格Φ2.5 mm ;⑤ 氩弧焊焊接不锈钢时,背面必须充氩气保护,才能保证背面成形。
不锈钢管道焊接施工流程
不锈钢管道焊接施工流程
本文档将介绍不锈钢管道的焊接施工流程。
以下是具体步骤:
准备工作
1. 确定焊接位置和管道走向。
2. 清洁管道表面,确保无油脂、污垢和锈迹。
3. 准备焊接所需的设备和工具,包括焊接机、电极、电源和焊接辅助工具。
进行焊接
1. 将管道对齐,并使用夹具将其固定。
2. 根据焊接类型选择合适的焊接方法,包括手工电弧焊、氩弧焊等。
3. 使用适当的焊接电流和电极直径进行焊接。
4. 焊接时,要保持焊缝的整齐和连续,并确保焊接位置的均匀加热。
5. 检查焊缝的质量,并根据需要进行重新焊接或修复。
完成工作
1. 焊接完成后,将焊接位置清洁干净,确保无焊渣和焊接痕迹。
2. 对焊接部位进行外观检查,确保焊缝质量和美观度。
3. 进行必要的测试和检测,包括压力测试和无损检测,以确保
管道的安全性和可靠性。
4. 如有需要,对焊接部位进行防腐处理,以延长管道的使用寿命。
以上就是不锈钢管道焊接施工的基本流程。
在进行焊接时,务
必遵守相关安全操作规程,并确保焊接操作符合相关法规和标准。
---
*(以上为文档内容,共计334字)*。
- 1、下载文档前请自行甄别文档内容的完整性,平台不提供额外的编辑、内容补充、找答案等附加服务。
- 2、"仅部分预览"的文档,不可在线预览部分如存在完整性等问题,可反馈申请退款(可完整预览的文档不适用该条件!)。
- 3、如文档侵犯您的权益,请联系客服反馈,我们会尽快为您处理(人工客服工作时间:9:00-18:30)。
不锈钢管道焊接工艺规程Standardization of sany group #QS8QHH-HHGX8Q8-GNHHJ8-HHMHGN#奥氏体不锈钢管道焊接工艺规程1 范围本标准适用于工业管道、公用管道和发电厂奥氏体不锈钢管道焊接施工。
本标准也适用于手工氩弧焊和手工电弧焊作业。
2 规范性引用文件下列文件中的条款通过本标准的引用而成为本标准的条款,凡是注日期的引用文件,其随后的修改单(不包括勘误的内容)或修订版均不适用于标准,然而,鼓励根据本部分达成协议的各方研究是否可使用这些文件的最新版本。
凡是不注日期的引用文件,其最新版本适用于本标准。
GB50235—97 《工业金属管道工程施工及验收规范》GB/T 983—95 《不锈钢焊条》DL/T869-2004 《火力发电厂焊接技术规程》劳人部[1988]1号《锅炉压力容器焊工考试规则》HYDBP006-2004《压力管道安装工程焊接、热处理过程控制程序》HYDBP018-2004《压力管道安装工程焊接材料管理程序》HYDBP013-2004《压力管道安装工程材料设备储存管理程序》HYDBP012-2004《压力管道安装工程材料设备搬运管理程序》HYDBP008-2004《压力管道安装工程计量管理手册》HYDBP007-2004《压力管道安装工程检验和试验控制程序》HYDBP010-2004《压力管道安装工程不合格品控制程序》劳动部发[1996]140号《压力管道安全管理与监察规定》3 先决条件3.1 环境3.1.1 施工环境应符合下列要求:3.1.1.1 风速:手工电弧焊小于8M/S,氩弧焊小于2M/S。
3.1.1.2 焊接电弧在1m范围内的相对湿度小于90%,环境温度大于0℃。
3.1.1.3 非下雨、下雪天气。
3.1.2 当环境条件不符合上述要求时,必须采取挡风、防雨、防寒等有效措施。
3.2 奥氏体不锈钢管道焊接控制流程图见图1。
图1 奥氏体不锈钢管道焊接控制流程图见图1。
Chart 1 Welding control flow chart of austenitic stainless steel pipe3.3 焊接材料3.3.1 奥氏体不锈钢管道焊接材料的采购和入库(一级库)由公司物资部负责,按《物资采购控制程序》和《焊接材料保管程序》执行。
3.3.2 奥氏体不锈钢管道焊接材料入二级库的保管、焊剂、烘干、发放、回收由各项目负责,按《焊接材料保管程序》执行。
3.3.3 氩弧焊所用氩气纯度不低于%。
3.4 焊接设备3.4.1 奥氏体不锈钢管道焊接时的设备可选用逆变焊机和可控硅整流焊机。
施工用焊接、热处理设备由各项目负责,管理按施工机械维护制度执行。
3.4.2 焊接设备、热处理设备所使用的计量仪表应处于正常工作状况,并定期校验,由物资部门负责,按《计量管理手册》执行。
3.5 焊工3.5.1 焊工应经焊接培训中心培训,并按国家劳动人事部颁发的《锅炉压力容器焊工考试规则》经考试合格后取得“锅炉压力容器焊工合格证”,其合格项目满足所承担的奥氏体不锈钢的焊接工作。
3.5.2 焊工持证的合格项目均要求在有效期内。
3.6 技术交底3.6.1 奥氏体不锈钢管道焊接施工前由焊接技术人员向焊工、热处理工、焊接检验员等有关人员进行技术交底,并作好技术交底记录。
3.6.2 技术交底的基本内容3.6.2.1 焊接及焊后热处理工艺、要点及措施。
3.6.2.2 焊接机工具。
3.6.2.3 焊接质量要求。
3.6.2.4 其他有关奥氏体不锈钢管道焊接工艺的特殊要求、重点和注意事项。
3.7 焊前检查奥氏体不锈钢管道焊接前由焊接检验员会同焊接技术人员和焊工,检查焊接技术交底内容的落实情况,确认符合工艺要求后方可组装、施焊。
4 焊接基本要求4.1 焊接施工程序见图2。
注:虚框表示当要求时。
Chart 2 Welding procedure4.2 对口4.2.1 推荐的坡口形式如下:4.2.1.1 壁厚δ在3<δ≤16mm时,选用V形坡口,其坡口形式见图3。
图3 3<δ≤16mm时, V形坡口坡口形式4.2.1.2 壁厚δ在δ>16mm时,选用U形或V形坡口,坡口形式见图4。
合格不合格返修对口焊接外观检查无损检测质量记录存档充氩气点焊充氩气热处理qualifiedunqualifiedrepaiSpeakalterna weldAppearance checkNDEQualityrecorplace onfileArgonSPotweldingArgonfilleheattreatment图4 δ>16mm时, U形或V形坡口的坡口形式4.2.2 对口质量要求内壁齐平,如有错口,其错口值应符合下列要求:对接单面焊的局部错口值不应超过壁厚的10%,且不大于1mm。
4.2.3 对口应将焊口表面及面侧15mm母材内,外壁的油、漆、垢、及氧化层等清理干净,直至露出金属光泽,并对坡口表面进行检查,不得有裂纹、重皮、毛刷及坡口损伤等缺陷。
若设计有要求时,还应对坡口表面进行渗透探伤。
4.2.4 采用手工电弧焊前,应将焊口坡口两则100mm范围内包上石棉布,以防飞溅污染母材。
4.3 焊接材料选用焊接材料选用按与母材化学成分相同或相近的原则进行,具体按焊接工艺卡的要求执行。
4.4 焊接4.4.1 管径小于60mm或壁厚小于6mm的管道采用全氩弧焊焊接。
4.4.2 管径大于60mm或壁厚大于6mm的管道采用氩弧焊打底,手工电弧焊盖面的焊接工艺。
氩弧焊打底时最好采用摇摆滚动法工艺,确保根层及盖面层的质量。
4.4.3 承插焊或角焊采用手工电弧焊焊接。
4.5 点焊4.5.1 点固焊,其焊接材料、焊接工艺、焊工和预热温度等应与正式施焊相同。
4.5.2 在坡口根部点固焊时,点固焊后应检查各个焊点质量,如有缺陷应立即清除,重新进行点焊。
4.5.3 厚壁大径管若采用填加物方法点固,当去除临时点固物时,不应损伤母材,并将其残留焊疤清除干净,打磨修整。
4.5.4 点焊的焊缝长度、高度及点数,可参照表1的要求执行。
表1 点焊的尺寸要求管径厚度δ(mm)δ≤4 δ>4点焊长度(mm)6-10 10-20点焊高度(mm)<3 ≤δ且≤6点数2-4 4-64.6 因特殊需要焊档板对口时,对口所用的挡板及卡具应与母材相同或相近,其焊接材料、焊接工艺与正式焊接相同,卡具拆除应用砂轮割除。
4.7 工艺要点4.7.1 焊接工艺规范应严格按焊接工艺卡的规定执行。
宜采用小电流、短电弧、小摆动、小线能量的焊接方法。
4.7.2 严禁在被焊件表面引弧、试电流或随意焊接临时支撑物。
4.7.3 采用钨极氩弧焊打底的根层焊缝检查后,经自检合格后,方可焊接次层,直至完成。
4.7.4 氩弧焊时,断弧后应滞后关气,以免焊缝氧化。
4.7.5 氩弧焊打底时薄壁管的次层焊接时,背面应充氩保护,采用可溶纸封堵做成气室。
见图5。
4.7.6 直径大于194mm的管子宜采取二人对称焊,焊前为保证首层氩弧焊道质量,管道内必须充氩气保护,防止合金元素烧损及氧化,大径奥氏体不锈钢管道焊口内充氩装置见图6,为防止氩气从对口间隙中大量泄漏,焊前需在坡口间隙中贴一层高温胶带,焊接过程中随时将妨碍焊接操作的那部分高温胶带撕去,每次撕去的长度视保护情况而定。
内充氩装置在第一层电焊盖面检查合格后方可撤除。
图5 小径不锈钢管道内充氩装置图6 大径不锈钢管道内充氩装置4.7.7 施焊中,应特别注意接头和收弧的质量,收弧时应将熔池填满。
多层多道焊的接头应错开。
4.7.8 承插焊严禁一次成型,且接头应错开。
4.7.9 施焊过程除工艺和检验上要求分次焊接外,应按层间温度的控制要求进行,当层间温度过高时,应停止焊接。
再焊时,应仔细检查并确认无裂纹后,方可按照工艺要求继续施焊。
4.7.10 对需做检验的隐蔽焊缝,应经检验合格后,方可进行其他工序。
4.7.11 焊口焊完后应进行清理,经自检合格后在焊缝附近用记号笔写上焊工的钢印代号,或其它永久性标记。
4.7.12 层间清理和表面清理采用不锈钢丝刷。
4.8 焊后热处理4.8.1 焊后热处理采用电加热的方法。
4.8.2 热处理的加热宽度,从焊缝中心算起,每侧不小于管子壁厚的3倍,且不小于60mm。
4.8.3 热处理的保温宽度,从焊缝中心算起,每侧不小于管子壁厚的5倍,以减少温度梯度。
4.8.4 焊缝的焊后热处理温度、恒温时间及升降温速度,应严格按照热处理工艺卡的规定执行。
4.8.5 热处理加热时,力求内外壁和焊缝两侧温度均匀,恒温时在加热范围内注意两测点间温差应低于50℃。
4.8.6 进行热处理时,测温点应对称布置在焊缝中心两侧,且不得少于两点,水平管道的测点应上下对称布置。
4.8.7 焊接接头热处理的过程必须有热处理曲线记录图,并填写热处理报告。
4.9 操作注意事项4.9.1 严禁在被焊工件的母材表面引燃电弧、试电流、或随意焊接临时支撑物。
4.9.2 施焊时应特别注意引弧、接头、收弧处的质量,收弧时应把弧坑填满。
4.9.3 多层多道焊的接头应错开,并逐层进行自检合格,方可焊接次层。
4.9.4 管子焊接时,管内应有防止穿膛风的措施。
4.9.5 必须在风、雨、雪的天气焊接时,应有相应的防止措施。
4.9.6 焊接完毕焊工应自检,并标识,焊接施工应做到工完料尽,场地清。
5 质量检验5.1 焊接检验按技术监督部门或合同规定的技术要求进行。
5.2 奥氏体不锈钢管道的焊接也可按相关验收标准和合同规定的技术要求进行。
5.3 外观检验5.3.1 焊工对所有焊缝的表面质量必须作100%的自检,并填写焊工自检记录表。
5.3.2 焊工外观的质量须符合下述要求:5.3.2.1 焊缝表面不允许有裂缝、气孔、未熔合、超规咬边等缺陷。
5.3.2.2 焊缝的外形尺寸应符合设计要求,焊缝边缘应圆滑过渡至母材。
5.3.2.3 焊缝不允许有严重氧化或过烧(指焊缝的正面或反面发黑、起渣等)。
焊接检验员根据技术规程或合同规定的要求进行专检,及时填写焊接“分项工程焊接接头质量检验评定表”。
5.3.3 焊缝或焊接接头的无损检验,硬度、光谱、金相试验、机械性能测试按《检验和试验控制程序》进行。
5.3.4 焊接组装的质量由焊工自检、焊接检验员随机抽查。
5.3.5 施焊时的过程外观检查由质量员进行不定期的抽查,包括焊接工艺参数,外观成形情况、焊缝外观检查等,并做好记录。
6 返修当焊接接头有超标缺陷时必须进行返修,并应遵守下列规定:6.1 不合格项处理按浙江省火电建设公司《不合格品控制程序》进行,或按合同要求处理。
6.2 焊缝返修工艺,应有经评定合格的焊接工艺评定。
6.2.1 经无损检验需返修挖补的焊缝,按返修工艺要求立即进行返修,并填写“焊接返修工艺报批单”。