乙苯的生产工艺组织与实施
乙苯装置工艺流程及生产原理

乙苯装置工艺流程及生产原理第一节催化干气预处理部分生产原理:乙苯烃化催化剂最怕碱性物质,会造成催化剂失活。
而催化干气多采用乙醇胺等碱性物质脱硫技术脱除硫化氢,因此为了防止碱性物质进入烃化反应系统,催化干气首先要经过水洗。
干气中的丙烯会与苯生成丙苯,同时会增加甲苯的生成量,造成苯耗上升增加产品成本,所以需要通过吸收的办法尽可能降低干气中丙烯的含量。
工艺流程叙述:催化干气进装置后进入催化干气水洗罐(D-101)。
该罐具有两个作用,其一是将催化干气进装置时携带的液体除去,另一作用是用水将携带的MEA 除去。
罐内设填料一段,罐底设水洗循环泵(P-101A/B),水洗用水循环使用。
从催化干气水洗罐(D-101)顶部出来的气体依次进入催化干气换热器(E-101)、催化干气过冷器(E-102)与丙烯吸收塔(C-101)塔顶出来的低温催化干气、冷冻水换热,温度降至15℃,从底部进入丙烯吸收塔(C-101)。
吸收剂从丙烯吸收塔顶部进入与催化干气逆向接触,将催化干气中的丙烯绝大部分除去,从丙烯吸收塔顶部出来的催化干气进入催化干气换热器(E-101)与进塔的催化干气换热回收部分冷量后去反应部分。
吸收了丙烯的吸收剂从塔底出来进入贫液-富液换热器(E-103)与贫液换热后进入解吸塔(C-102)。
解吸塔进料进入解吸塔后,塔顶汽相进入解吸塔顶蒸汽发生器(E-106)冷凝冷却,然后进入解吸塔回流罐(D-102),冷凝下来的液体用解吸塔回流泵(P-103A/B)送至解吸塔顶部,未冷凝的气体从解吸塔回流罐顶部出来后依次进入解吸塔顶冷却器(E-107)解吸塔顶气过冷器(E-108)进一步冷凝冷却,然后进入解吸塔顶分液罐(D-103)进行气液分离,冷凝下来的液体用解吸塔顶凝液泵(P-104A/B)送入解吸塔回流罐(D-102),未冷凝的气体出装置。
解吸塔塔底物料用吸收剂循环泵(P-102A/B/C)加压后依次通过贫液-富液换热器(E-103)、贫液过冷器(E-104)冷却,返回丙烯吸收塔塔顶循环使用。
苯烷基化生产乙苯

THANKS
感谢观看
反应过程中,烷基化剂首先与催化剂生成碳正离子,然后碳正离子与苯环发生亲电取代反应,生成乙 苯。
反应条件与催化剂
反应条件
烷基化反应通常在高温、高压下进行, 反应温度一般在200-400℃,反应压力在 1-10MPa之间。反应时间和搅拌速度也 是影响反应效果的重要因素。
VS
催化剂
常用的催化剂有酸性催化剂和金属催化剂 两类。酸性催化剂如硫酸、氢氟酸等,能 够促进碳正离子的生成,从而加速烷基化 反应的进行。金属催化剂如铝、锌等,能 够提高烷基化剂的活性,降低反应活化能 ,促进反应的进行。
在苯烷基化生产乙苯过程中, 会产生多种废弃物,应严格按 照废弃物性质进行分类,确保
各类废弃物得到妥善处理。
污染物排放控制
采用先进的污染处理技术,对生产 过程中产生的废气、废水进行严格 处理,确保污染物排放达到国家及 地方环保标准。
环保设备投入
加大对环保设备的投入,提升环保 设施的处理能力,为降低环境污染 提供有力保障。
03
工艺流程详解
原料准备与预处理
原料选择
生产乙苯的主要原料为苯和乙烯。这两种原 料需要满足一定的纯度要求,以保证反应的 高效进行。
原料预处理
在进料之前,需要对苯和乙烯进行预处理, 如脱水、脱硫等,以去除其中的杂质,防止 对反应造成不良影响。
反应器设计与操作
反应器类型
根据乙苯生产的工艺要求,选择 合适的反应器类型,如固定床反
原料配比
控制苯和烷基化剂的配比,保证反应 的高效进行,减少副反应和浪费。
催化剂管理
选择合适的催化剂,并定期更换或再 生,以保持反应的活性和选择性。
安全防护
在生产过程中,要注意防止泄漏和火 灾等安全事故的发生,配备相应的安 全设施和应急措施。
乙苯的生产工艺组织与实施

乙苯的生产工艺组织与实施引言乙苯是一种广泛应用于化学工业的重要有机化合物。
它广泛用于生产塑料、纤维、颜料、橡胶等各个领域。
乙苯的生产工艺组织与实施对于提高生产效率、降低生产成本具有重要意义。
本文将介绍乙苯的生产工艺,包括其生产原料、反应条件、反应机制以及工艺参数的优化。
乙苯的原料乙苯的主要原料是乙烯和苯。
乙烯是一种常见的烃类物质,可以通过石油炼制过程中分离得到。
苯则是一种苯环结构的有机化合物,可以从煤焦油或石油中提取得到。
乙烯和苯是乙苯生产的基础原料,其纯度和质量对乙苯的产量和质量具有重要影响。
乙苯的生产工艺Friedel-Crafts芳烃烷基化反应乙苯的主要生产工艺是Friedel-Crafts芳烃烷基化反应。
该反应利用强酸性催化剂,将乙烯与苯发生取代反应,并生成乙苯。
这个反应过程需要在一定的反应条件下进行,包括催化剂的选择、反应温度、反应压力等。
催化剂的选择常用的催化剂有氯化铝、氯化铁等,在催化剂选择方面,需要考虑其催化活性、选择性和稳定性。
催化剂的活性与反应速率有关,选择性则与乙苯的产率和副产物的生成有关,稳定性能够保证催化剂的持久使用。
反应条件的控制Friedel-Crafts芳烃烷基化反应的反应条件对反应的效果具有重要影响。
反应温度一般在120-150摄氏度之间,高温有利于提高反应速率,但同时也会增加副反应的发生;反应压力一般在2-5兆帕之间,过低的压力会降低反应速率,过高的压力则可能导致催化剂失活。
反应机制Friedel-Crafts芳烃烷基化反应的反应机制包括亲电取代和自由基取代两个过程。
在亲电取代过程中,催化剂起到了极大的作用,使得苯环发生亲电进攻,将乙烯加成到苯上形成乙苯;在自由基取代过程中,催化剂使得乙烯自由基发生反应,并将乙烯加成到苯上。
反应机制的理解对于优化工艺参数、提高产量具有重要意义。
工艺参数的优化为了提高乙苯的生产效率和质量,需要进行工艺参数的优化。
常用的优化方法包括反应温度、反应时间、反应物的比例等。
乙苯生产工艺
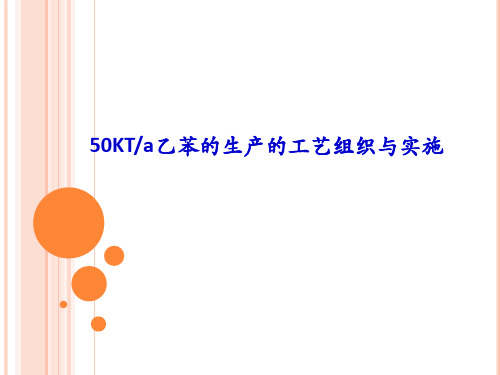
以负载在Al2O3上的BF3为催化剂的反应法
该法以负载在Al2O3上的BF3为催化剂,可用浓度低达8%~10%(质量分数)的 乙烯为原料进行烷基化反应,因此可以用处理后的FCC干气或焦炉尾气为原 料。该反应在100~150°C和2.5~3.5MPa下进行,乙烯和苯的摩尔比控制在 0.15~0.2之间。烷基转移反应在另外的反应器中进行温度为180~230°C。 从两个反应器出来的物料合并后进入提纯系统。 优点:成品的乙苯纯度可达99.9%。该方法主要优点是催化剂活性高、寿 命长、乙苯选择性好、无腐蚀无污染、流程简短、能耗小,可用于低浓度 乙烯的综合利用。 缺点:催化剂制备条件苛刻,费用也较贵,并容易中毒失活。原料在反应前 必须净化,要求H2S、CO2和H2O等杂质的含量小于1×10-6。
生产方法比较分析
乙苯是生产苯乙烯的中间产品,少量的乙苯也用于溶剂、稀释剂以及生 产二乙基苯等。目前在工业生产中,90%以上是在适当催化剂存在下由 苯与乙烯烷基化反应来制取乙苯。
苯和乙烯烷基化是在酸性催化剂存在下进行,若以所用催化剂分类, 可分为三氯化铝(AlCl3)法、BF3—Al2O3法和固体酸法等。液相三 氯化铝法又可分为传统的两相烷基化工艺和单相高温烷基工艺。 AICI3催化剂液相反应法 传统的AlCl3法反应器内反应物和催化剂形成三相,液态芳烃、气态乙 烯和液态的催化剂配合物。催化剂配合物呈红色,与液态芳烃不互溶, 反应时乙烯鼓泡进入含有两个液相的的反应器内,使它们分散混合。 乙烯与苯的摩尔比为0.3~0.35,反应在低于130°C以下及常压进行。
2 乙烯浓度的影响
由表2可知,乙烯浓度对催化精馏过程有影响。干气 中乙烯浓度提高,乙烯的转化率提高,乙苯选择性降低 。这是由于在反应压力一定的情况下,干气中乙烯浓 度增加,乙烯分压增大,有利于乙烯在液相中的溶解吸 收,提高了乙烯的转化率。又由于乙烯在液相中的溶 解度增加,继续烷基化反应速率增大,生成更多的二乙 苯和多烷基苯等,降低了乙苯的选择性
干气制乙苯流程说明

工艺流程说明一干气制乙苯包括脱丙烯、烃化及反烃化反应、吸收及苯回收、乙苯分离等四个工艺过程。
1 脱丙烯:来自界区外的催化干气进入催化干气水洗罐(D-101),通过水洗除去催化干气中可能夹带的脱硫剂乙醇胺,以免造成烃化催化剂中毒失活。
由催化干气水洗罐出来的催化干气经过催化干气换热器(E-101)与丙烯吸收塔(C-101)顶的脱丙烯催化干气换热,再经催化干气过冷器(E-102)冷却到15℃后进入丙烯吸收塔底部。
经过吸收剂吸收丙烯后的脱丙烯催化干气经过催化干气换热器冷却到35℃左右后去烃化反应器(R-101A/B)。
丙烯吸收塔的吸收剂为反烃化料,其主要成分为二乙苯。
丙烯吸收塔底的富吸收剂经过贫液-富液换热器(E-103)后进入解吸塔(C-102)中部第16板,解吸塔底用热载体加热到257℃。
解吸塔釜液由吸收剂循环泵(P-102A/B/C)输送经贫液-富液换热器冷却到40℃,再经贫液过冷器(E-104)过冷到15℃后进入丙烯吸收塔顶部。
解吸塔顶气体经过解吸塔顶蒸汽发生器(E-106)在165℃下部分冷凝进入解吸塔回流罐(D-102),冷凝液由解吸塔回流泵(P-103A/B)输送回流到解吸塔顶部。
由解吸塔回流罐排出的气体经过解吸塔顶气冷却器(E-107)和解吸塔顶气过冷器(E-108)冷却到10℃后进入解吸塔顶气分液罐(D-103),冷凝下的液体由解吸塔顶凝液泵(P-104A/B)送回解吸塔回流罐,不凝的富丙烯催化干气去界区外催化装置或排空管网。
2 烃化及反烃化反应:来自循环苯塔(C-104)11板侧线的循环苯由循环苯塔侧线抽出泵(P-111A/B)输送到循环苯罐(D-105),然后由循环苯泵(P-106A/B)输送一部分进入反烃化反应进料罐(D-106),大部分经过新鲜苯-循环苯换热器(E-115)、反应产物-循环苯换热器(一)(E-111)、反应产物-循环苯换热器(二)(E-110)换热到250℃后进入循环苯加热炉(F-102),循环苯加热炉出来的循环苯达到348℃,进入烃化反应器(R-101A/B)顶部。
乙苯生产工艺流程

乙苯生产工艺流程
《乙苯生产工艺流程》
乙苯是一种重要的有机化合物,广泛用于橡胶、塑料、化妆品等行业。
其生产工艺流程主要分为苯和乙烯的加氢反应,以下是乙苯的生产工艺流程:
1. 原料准备:首先准备苯和乙烯作为生产乙苯的原料,这两种原料通常通过石油提炼或裂解石油得到。
2. 加氢反应:将苯和乙烯送入加氢反应器中,在催化剂的作用下进行加氢反应,生成乙苯。
这个反应需要在一定的温度和压力下进行,控制好反应条件可以提高乙苯的产率。
3. 分离精馏:由于反应生成的产物中可能还含有杂质或未反应的原料,需要进行分离精馏处理。
通过恰当的精馏方法,将乙苯从未反应的原料和其它杂质中分离出来,得到纯净的乙苯产物。
4. 产品脱水:乙苯作为有机溶剂广泛用于化工生产,但其水含量严重影响着产品的质量。
因此,通常需要对乙苯进行脱水处理,降低产品中的水含量。
5. 储存包装:最后将经过处理的乙苯产品进行储存和包装,以便运输到使用场所。
这就是乙苯的生产工艺流程,通过严格控制生产过程和加工工
艺可以得到高纯度的乙苯产品,为相关行业的生产提供了稳定的原料支持。
2024年乙苯、苯乙烯安全生产要点(三篇)
2024年乙苯、苯乙烯安全生产要点1工艺简述包括用苯烷基化制取乙苯和用乙苯脱氢法生产苯乙烯。
工艺过程由烷基化、洗涤、乙苯精馏、脱氢、苯乙烯精馏等工序组成。
简要工艺过程是将原料苯干燥使之含水小于10ppm,配入助催化剂无水氯化氢,同乙烯和三氯化铝催化剂络合物进入烷基化/烷基转移反应器,在温度180℃、压力0.91MPa下进行烷基化/烷基转移反应。
反应的物料经闪蒸回收氯化氢,再进入串联的三级洗涤系统,除去三氯化铝和氯化氢。
洗涤后的烷基化液送入精馏系统,烷基液被分离成苯、乙苯、多乙苯和残油。
苯和多乙苯返回烷基化/烷基转移反应器,乙苯产品送贮罐。
将乙苯和初级蒸汽过热后与主蒸汽混合(蒸气:乙苯=1.3:1)进入第一级反应器。
在入口温度628℃、出口压力0.0486MPa和催化剂作用下进行脱氢反应,然后于入口温度631℃、出口压力0.04MPa下在第二级反应器中继续脱氢生成苯乙烯,脱氢混合物经废热锅炉、过热蒸汽降温器、空调器降温、冷凝。
分离器出来的脱氢液进精馏系统,分离苯乙烯、乙苯、苯、甲苯得到苯乙烯产品。
乙苯、苯返回使用。
付产品甲苯送罐区。
本装置生产过程的物料乙苯、苯、苯乙烯、多乙苯、氢气等都具有易燃、易爆、有毒、有害的特性,有些具有强腐蚀性,如氢化氢,催化剂络合物等。
2重点部位2.1烷基化反应系统它是乙苯生产的核心部位。
反应时温度、压力较高,反应条件较苛刻,物料易燃、易爆且有强腐蚀性。
反应器需使用性能良好的防腐隔热衬砖为衬里。
其它设备和阀门、管线均采用特殊防腐材料,但仍存在着跑、冒、滴、漏的危险。
该类装置曾发生反应器被腐蚀而泄漏的事故。
另外,一旦水进入反应器会使催化剂络合物中毒,并造成设备、管线堵塞。
某厂苯乙烯装置因该反应器出料口堵塞而被迫停车。
2.2催化剂络合物配制系统该系统用苯、多乙苯、三氯化铝、无水氯化氢配制催化剂络合物供烷基化/烷基转移反应使用。
物料具强腐蚀性;系统若进水会使催化剂失活并分解产生沉淀堵塞管线,威胁整个烷基化反应。
乙苯初步工艺设计物料衡算
乙苯初步工艺设计物料衡算一、物料清单乙苯:1000 kg硝酸:200 kg硫酸:400 kg水:500 kg二、反应方程式C6H5CH3 + HNO3 → C6H5CH2NO2 + H2OC6H5CH2NO2 + 2H2SO4 → C6H5CH2OH + 2HSO4- + H3O+三、工艺流程1. 原料准备阶段:将乙苯、硝酸、硫酸和水分别称量好,放在不同的容器中备用。
2. 硝化反应阶段:将乙苯和硝酸加入反应釜中,开始加热并搅拌,使其混合均匀。
当温度升至70℃时,开始缓慢加入浓硫酸,同时继续搅拌。
当加完浓硫酸后,继续加热至85℃,并保持反应温度在85-90℃之间。
反应完成后,关闭加热器和搅拌器,放置冷却至室温。
3. 水洗阶段:将冷却后的反应液缓慢倒入大容器中,并加入适量的水进行水洗。
水洗次数根据实际情况而定,一般为3-4次。
每次水洗后,将反应液放置一段时间,使其分层。
然后将上层液体倒掉,留下底层的有机相。
4. 脱色阶段:将底层的有机相加入脱色釜中,并加入适量的活性炭和滤布袋。
开始加热并搅拌,使其混合均匀。
当温度升至80℃时,继续保持反应温度在80-85℃之间,并继续搅拌。
脱色完成后,关闭加热器和搅拌器。
5. 蒸馏阶段:将脱色后的反应液加入蒸馏釜中,并开始加热。
当温度升至110℃时,开始收集馏出物,并记录下不同温度下的收集时间和产量。
6. 精馏阶段:将收集到的馏出物再次进行精馏处理,以提高纯度。
具体操作方法与蒸馏阶段类似。
7. 包装阶段:将精制后的乙苯装入桶或罐中,并进行标识、封存等处理。
四、安全措施1. 在操作过程中要注意保护眼睛和皮肤,避免接触反应液。
2. 在加入浓硫酸时要缓慢加入,以免产生反应过程中的危险。
3. 在加热和搅拌时要注意防火和爆炸。
4. 操作结束后要及时清理设备,避免残留物对下一次操作产生影响。
五、总结乙苯的制备工艺是一个比较复杂的过程,需要严格控制反应条件和操作技术。
在实际操作中,需要根据具体情况进行调整和改进,以提高产品质量和产量。
乙苯生产技术
3 乙烯浓度旳影响
由表2可知,乙烯浓度对催化精馏过程有 影响。干气中乙烯浓度提升,乙烯旳转化 率提升,乙苯选择性降低。这是因为在反 应压力一定旳情况下,干气中乙烯浓度增 长,乙烯分压增大,有利于乙烯在液相中 旳溶解吸收,提升了乙烯旳转化率。又因 为乙烯在液相中旳溶解度增长,继续烷基 化反应速率增大,生成更多旳二乙苯和多 烷基苯等,降低了乙苯旳选择性
4 催化剂
该工艺采用ZSM-5沸石催化剂,完全防止了 AlCl3催化剂带来旳一系列问题。但因为 ZSM-5催化剂旳活性温度较高,所以反应要 在较高温度下进行。在较高温度下,烷基化 反应速率较快,该催化剂对苯和乙烯旳烃化 反应及多乙苯与苯旳反烃化反应均具有较 强旳催化剂活性和良好旳选择性,可达 99.5%。此工艺催化剂用量少,轻易结焦而 失活,但轻易再生,使用寿命长,生产中不存 在环境污染和设备腐蚀问题。
任务点05 经典设备旳选择
乙苯单元由烷基化反应、烷基转移反应和乙苯精馏部分 构成。烷基化反应部分旳任务是在分子筛催化剂旳作用 下使乙烯和苯烷基化生成乙苯、多乙苯等物质。烷基转 移反应部分旳任务则是在分子筛催化剂旳作用下使苯、 多乙苯发生烷基转移反应,生成乙苯。烷基化反应和烷 基转移反应部分旳出料中具有乙苯、多乙苯、重质物及 未反应旳原料苯,都被送到乙苯精馏预分馏塔。由预分 馏塔、苯塔、乙苯塔、多乙苯塔、脱非芳塔将反应产物 分离成苯、乙苯、多乙苯和重质物。其中回收旳苯返回 到烷基化反应器和烷基转移反应器,多乙苯返回到烷基 转移反应器。脱非芳塔则用于脱除进料和反应过程中生 成旳轻组分和轻非芳烃
• 用旳比较多旳是磁力泵和屏蔽泵 另外还有大功率离心泵 反烃化反 应进料泵是高速齿轮泵。
任务点06 乙苯生产中安全、环境保护、节能 措施
1.1应严格监视反应器旳温度、压力,进料苯和多乙苯 中旳水含量应不大于10ppm。反应器开停车应严格 控制开、降温速度;反应器系统旳联锁必须正常投 入使用,定时校验联锁并有统计。
11苯烷基化合成乙苯的生产工艺
苯烷基化合成乙苯的生产工艺目前在工业生产中, 除极少数乙苯来源于重整轻油C 8芳烃馏份抽提外, 其余90%以上是在适当催化剂存在下由苯与乙烯烷基化反应来制取。
其生产工艺有以下几种。
一、 AlCl 3 法传统的AlC13液相法使用AlC13-HCl 催化剂, AlC13溶解于苯、乙苯和多乙苯的混合物中, 生成络和物。
该络和物在烷基化反应器中与液态苯形成两相反应体系, 同时通入乙烯气体,常压下发生烷基化反应,生成乙苯和多乙苯, 同时多乙苯和乙苯发生烷基转移反应,反应中苯的烷基化反应和多乙苯的烷基转移反应在一台反应器中完成。
均相AlCl 3法通过控制乙烯的投料, 使Alcl 3催化剂的用量减少到处于溶解度范围内, 使反应可以在均一的液相中进行,烷基化和烷基转移反应在两个反应器中进行,乙苯收率高,副产焦油少,Alcl 3用量少(仅为传统法的1/3)。
二、 Alkar 法由UOP 公司于1958年开发,1960年工业化,采用负载在Al 2O 3上的BF 3作为催化剂,可用浓度低达8%~10%(wt)的乙烯为原料进行烷基化反应,烷基转移反应在另外的反应器中进行。
其工艺流程如图2。
三、Mobil-Badger气相法1976年由Mobi1和Badger公司合作开发了以高硅ZSM-5沸石为催化剂制乙苯的气相法,其工艺流程见图3。
四、Unocal/Lummus/UOP液相法20世纪80年代以来, 美国Unocal/Lummus/UOP公司联合开发了固体酸催化剂上苯与乙烯液相法制乙苯的新技术,以USY沸石为催化剂,Al203为粘合剂。
烷基化反应器分两段床层,苯与乙烯以液相进行烷基化反应,各床层处于绝热状态。
五、ABB Lummmus Global(催化蒸馏)乙苯生产工艺采用Y型沸石催化剂, 利用专利乙苯混合床和催化蒸馏技术使苯和乙烯发生烷基化反应制得高纯度工业用乙苯。
- 1、下载文档前请自行甄别文档内容的完整性,平台不提供额外的编辑、内容补充、找答案等附加服务。
- 2、"仅部分预览"的文档,不可在线预览部分如存在完整性等问题,可反馈申请退款(可完整预览的文档不适用该条件!)。
- 3、如文档侵犯您的权益,请联系客服反馈,我们会尽快为您处理(人工客服工作时间:9:00-18:30)。
(3)、乙苯 外观与性状:无色液体,有芳香气味。 熔点(℃):-94.9 沸点(℃):136.2 相对密度(水=1):0.87 相对蒸气密度(空气=1):3.66 饱和蒸气压(kPa):1.33(25.9℃) 临界温度(℃):343.1 临界压力(MPa):3.70 闪点(℃):15 引燃温度(℃):432 爆炸上限%(V/V):6.7 爆炸下限%(V/V):1.0
4、原料配比
乙烯与苯的比例对烷基化产 品的组成影响很大。
图中是乙烯与苯的分子比对 产品的影响。由图中可知, 乙苯产率随乙烯与苯比例的 增加而增加,多乙苯的产率 也相应随之提高。当两者比 例超过0.6时,乙苯产率的增 加显著减小,而多乙苯产率 的增加却显著加大。
所以乙烯与苯的摩尔比以 0.5~0.6为宜。
优点: 该工艺可以用浓乙烯为原料,也可用稀乙烯混合气体 为原料,该工艺采用ZSM-5沸石催化剂,完全避免了AlCl3催化 剂带来的一系列问题。该催化剂对苯和乙烯的烃化反应及多 乙苯与苯的反烃化反应均具有较强的催化剂活性和良好的选 择性,可达99.5%。
此工艺催化剂用量少,容易结焦而失活,但容易再生,使用寿命 长,生产中不存在环境污染和设备腐蚀问题。此外,系统排放 的废气和残液均可为装置提供25%的燃料,输入系统的热量和 反应生成的热量中95%可回收。因此,物耗、能耗低。
本项目选用:气相法
理由:该工艺采用ZSM-5沸石催化剂,完全避免
了AlCl3催化剂带来的一系列问题,该催化剂对苯 和乙烯的烃化反应及多乙苯与苯的反烃化反应均 具有较强的催化剂活性和良好的选择性,转化率可 达99.5%。
此工艺催化剂用量少,容易结焦而失活,但容易再生, 使用寿命长,生产中不存在环境污染和设备腐蚀问 题。此外,系统排放的废气和残液均可为装置提供 25%的燃料,输入系统的热量和反应生成的热量中 95%可回收。因此,物耗、能耗低。
典型设备的选择
1、物料性质 (1)、乙烯
健康危害 侵入途径:吸入。 健康危害:具有较强的麻醉作用。
毒理学资料及环境行为 毒性:属低毒类。 急性毒性:LC95000ppm(小鼠吸入) 亚急性和慢性毒性:大鼠吸入11.5g/m3,1年, 生长发育与对照组有差别。
危险特性:易燃,与空气混合能形成爆炸性混 合物。遇明火、高热或与氧化剂接触,有引起 燃烧爆炸的危险。与氟、氯等接触会发生剧烈 的化学反应。
挥发度:挥发度大
(4)、 ZSM-5沸石
纳米ZSM-5分子筛具有较大的外表面积,其吸 附和转化大分子的能力强;其表面原子周围缺 少相邻的原子,有许多悬空键(处于不饱和状 态),即更多更接近的活性中心位,使反应物 分子易于扩散并与活性中心接触引发催化反应, 故具有大的化学活性。其在催化、离子交换吸 附、复合材料方面显示出优异的性能,因而被 更广泛的应用于工业生产中。
3、Unocal/Lummus/ UOP液相法
20 世纪80 年代以来, 美国三个公司联合开发了固体酸催化剂催化苯与 乙烯液相法制乙苯的新技术,以Y-沸石为催化剂, Al2O3为粘合剂。在 232~316℃和2.79~6.99MPa下进行反应, 苯的质量空速2~10/h ,苯/ 乙烯摩尔比4~10。
个阶段 ,即由以
三氯化铝为催化剂的烷基化反应路线,以ZSM-5沸石 分子筛为催化剂的气相烷基化法以及由Y-沸石为催化 剂的液相法制乙苯工艺路线。 近几年来,国内也开展了以沸石为催化剂生产乙苯的研 究,并显示了良好的工业前景。同时,催化蒸馏技术制 乙苯的研究也取得了进展。
5、催化剂
该工艺采用ZSM-5沸石催化剂,完全避免了 AlCl3催化剂带来的一系列问题。但由于 ZSM-5催化剂的活性温度较高,因此反应要 在较高温度下进行。在较高温度下,烷基化 反应速率较快,该催化剂对苯和乙烯的烃化 反应及多乙苯与苯的反烃化反应均具有较 强的催化剂活性和良好的选择性,可达 99.5%。
项目A03:50kt/a乙苯的生产 工艺组织与实施
第二组: 周文仙、孔琴琴、孙敏、吴林飞、马俊、 徐晨、殷斐
目录
A0301生产工艺路线选择 A0302生产工艺条件影响因素分析 A0303典型设备的选择 A0304生产中安全、环保、节能措施
生产工艺路线选择
生产现状 到目前为止,工业上乙苯主要由苯与乙烯的烷基化反应
2、工艺条件
乙苯单元由烷基化反应、烷基转移反应和乙苯精馏部分 构成。
烷基化反应部分的任务是在分子筛催化剂的作用下使乙 烯和苯烷基化生成乙苯、多乙苯等物质。
烷基转移反应部分的任务则是在分子筛催化剂的作用下 使苯、多乙苯发生烷基转移反应,生成乙苯。
烷基化反应和烷基转移反应部分的出料中含有乙苯、多 乙苯、重质物及未反应的原料苯,都被送到乙苯精馏预 分馏塔。
溶解性:不溶于水,可混溶于乙醇、醚等多数 有机溶剂。
主要用途:用于有机合成和用作溶剂。
毒性:有毒
危险特性:易燃,其蒸气与空气可形成爆炸性 混合物,遇明火、高热或与氧化剂接触,有引 起燃烧爆炸的危险。与氧化剂接触猛烈反应。 流速过快,容易产生和积聚静电。其蒸气比空 气重,能在较低处扩散到相当远的地方,遇火 源会着火回燃。
优点:该法不产生污染环境的废料,反应温度低(一 般不超过300°C),乙苯中二甲苯杂质含量仅为 20~40×10-6,远远少于气相法。催化剂的运转周 期可长达一年,对原料纯度要求不高。使用后的催 化剂可以进行器外再生,再生条件缓和,使用寿命可 达3年。
缺点:但该法只能用于浓乙烯的烷基化反应,而不 适合FCC干气或焦炉尾气原料。空速低,催化剂用 量大,反应压力较高,使能耗增加,设备和操作复杂。
缺点:在处理FCC干气或焦炉尾气原料时,为了延长催化剂单 程寿命,需对原料进行严格精制(原料气中丙烯、H2S、O2和 H2O等杂质均需净化至质量分数均为10-15以下)。且该工艺 装置投资和能耗相对较高(苯单耗0.749t/t乙苯,乙烯0.168t/t乙 苯)。产物中二甲苯含量较高(约2×10-3),影响产品的品质。
从动力学方面分析,反应温度低,反应速度低,对反 应进行不利。
适宜的温度随所用催化剂不同而不同。我组选用 ZSM-5催化剂,反应温度主要满足催化剂发挥催化活 性和延长使用寿命的需要,一般为440~445℃,过高的 反应温度同样会发生生成焦油等副反应,结果导致催化 剂因表面结炭而失活。
2、压力
催化剂、苯、多乙苯循环使用,每吨乙苯副产焦油1.8~2.7kg。
此反应中苯的烷基化反应和多乙苯的烷基转移反应在一台反应器 中完成。为限制多乙苯的生成,必须控制乙烯与苯的比例。工业生 产装置控制乙烯与苯的分子比为0.3~0.4 左右。
催化剂配合物呈红色,与液态芳烃不互溶,反应时乙烯鼓泡进入含有 两个液相的的反应器内,使它们分散混合。
实际生产中,反应器有两种工艺。一是回收的多乙苯进 入同一反应器。另一种是进入另外一个烷基化反应器。
苯在温度为400 ℃左右,压力为1.2~1.6MPa下,以气 相进入顶部床层,进行苯和乙烯的气相烷基化反应,同 时也进行二乙苯和苯的烷基转移反应。苯与乙烯的重 量综合比为18.5 ,乙烯转化率达99.8 %。苯循环,回收 后的多乙苯进入烷基转移反应器进行烷基转移反应。 其操作条件为:压力0.6~0.7MPa ,温度440~445℃, 苯与多乙苯分子比为(1~1. 52) :1 ,苯单程转化率为 15%(Wt ) ,乙苯收率为98%。
由于传统的AlCl3法存在着污染腐蚀严重及反应器内两 个液相等问题,1974年Monsanto/ Lummus公司提出 了均相AlCl3法。
该工艺通过控制乙烯的投料,使AlCl3催化剂的用量减 少到处于溶解度范围内,使反应可以在均一的液相中进 行,提高了乙苯的产率。
反应温度为95 ~ 100℃,压力0.6~0.8MPa ,乙烯与苯 的摩尔比为0.6。均相AlCl3法进料乙烯浓度范围可为 15%~100%。
生产方法
1、 AlCl3法
(1)、 AlCl3液相法 此方法为传统的AlCl3法,使用AlCl3 - HCl催化剂,溶解于苯、乙
苯和多乙苯的混合物中,生成络和物。
该络和物在烷基化反应器中与液态苯形成两相反应体系,同时通 入乙烯气体,在温度130℃以下,常压至0.15MPa下发生烷基化反 应,生成乙苯和多乙苯,同时,多乙苯和乙苯发生烷基转移反应。 反应器中乙烯与苯摩尔比为0.30~0.35 ,乙烯转化率接近100%, 烷基化反应收率为97.5%。
优点:烷基化和烷基转移反应在两个反应器中进行,乙 苯收率高,副产焦油少,AlCl3用量少(仅为传统法的1/3)。
缺点:这种方法也只是使设备腐蚀及环境污染问题有 所缓解,并未从根本上得到解决。
2、Mobil - Badger气相法
1976 年由Mobil 和Badger公司合作开发了以高硅 ZSM - 5沸石为催化剂制乙苯的气相法。1980年在美 国Hoechst公司实现了工业化,年产47.3万吨乙苯。
由表3可以看出,压力对反应的影响十分显著,即 随反应压力的增加,乙烯转化率明显增加。反应 压力增加有利于乙烯在液相中的溶解吸收,而乙 烯在液相中的溶解吸收是整个过程的控制步骤, 所以烷基化反应相应加快,乙烯转化率提高。
3、乙烯浓度
由表2可知,乙烯浓度对催化精馏过程有影响。干气中乙烯 浓度提高,乙烯的转化率提高,乙苯选择性降低。这是由于 在反应压力一定的情况下,干气中乙烯浓度增加,乙烯分压 增大,有利于乙烯在液相中的溶解吸收,提高了乙烯的转化 率。又由于乙烯在液相中的溶解度增加,继续烷基化反应 速率增大,生成更多的二乙苯和多烷基苯等,降低了乙苯的 选择性
优点:乙烯的转化率接近100%,乙苯的收率较高,循环苯和乙 苯的量较小;苯与乙烯的烷基化反应和多乙苯的烷基转移反应 可在同一台反应器中完成。 缺点:反应介质的腐蚀性强,设备造价与维修费用高以及反应 产物有机相经水洗、碱洗后产生大量含有氢氧化铝淤浆的废 水,加上废催化剂,造成了严重的环境污染。