第10章 主生产计划
生产计划与控制操作指南
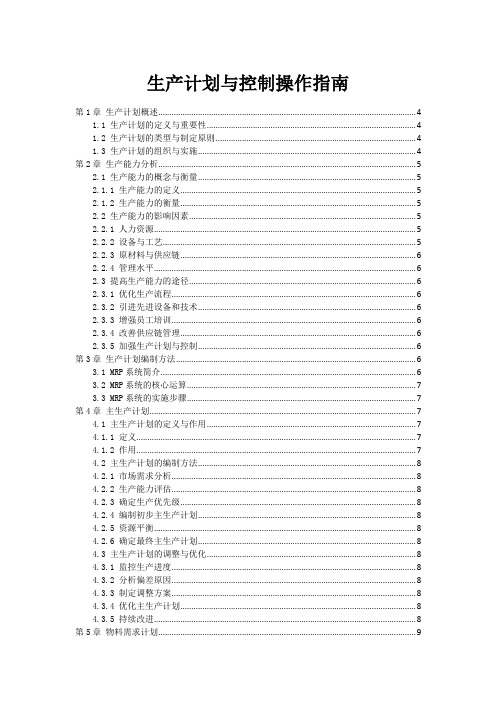
生产计划与控制操作指南第1章生产计划概述 (4)1.1 生产计划的定义与重要性 (4)1.2 生产计划的类型与制定原则 (4)1.3 生产计划的组织与实施 (4)第2章生产能力分析 (5)2.1 生产能力的概念与衡量 (5)2.1.1 生产能力的定义 (5)2.1.2 生产能力的衡量 (5)2.2 生产能力的影响因素 (5)2.2.1 人力资源 (5)2.2.2 设备与工艺 (5)2.2.3 原材料与供应链 (6)2.2.4 管理水平 (6)2.3 提高生产能力的途径 (6)2.3.1 优化生产流程 (6)2.3.2 引进先进设备和技术 (6)2.3.3 增强员工培训 (6)2.3.4 改善供应链管理 (6)2.3.5 加强生产计划与控制 (6)第3章生产计划编制方法 (6)3.1 MRP系统简介 (6)3.2 MRP系统的核心运算 (7)3.3 MRP系统的实施步骤 (7)第4章主生产计划 (7)4.1 主生产计划的定义与作用 (7)4.1.1 定义 (7)4.1.2 作用 (7)4.2 主生产计划的编制方法 (8)4.2.1 市场需求分析 (8)4.2.2 生产能力评估 (8)4.2.3 确定生产优先级 (8)4.2.4 编制初步主生产计划 (8)4.2.5 资源平衡 (8)4.2.6 确定最终主生产计划 (8)4.3 主生产计划的调整与优化 (8)4.3.1 监控生产进度 (8)4.3.2 分析偏差原因 (8)4.3.3 制定调整方案 (8)4.3.4 优化主生产计划 (8)4.3.5 持续改进 (8)第5章物料需求计划 (9)5.2 物料需求计划的编制方法 (9)5.3 物料需求计划的实施与控制 (9)第6章生产作业计划 (10)6.1 生产作业计划的概念与任务 (10)6.1.1 概念 (10)6.1.2 任务 (10)6.2 生产作业计划的编制方法 (10)6.2.1 收集和整理基础数据 (10)6.2.2 确定生产计划指标 (10)6.2.3 制定生产作业计划 (10)6.2.4 编制生产作业指导书 (10)6.3 生产作业计划的执行与控制 (11)6.3.1 生产作业计划的执行 (11)6.3.2 生产作业计划的控制 (11)第7章生产进度控制 (11)7.1 生产进度控制的意义与任务 (11)7.1.1 保证生产计划的有效执行 (11)7.1.2 提高资源利用率 (11)7.1.3 预防和解决生产过程中的问题 (11)7.1.4 提供决策依据 (11)7.2 生产进度控制的方法 (11)7.2.1 甘特图法 (12)7.2.2 关键路径法 (12)7.2.3 看板管理法 (12)7.2.4 生产调度法 (12)7.3 生产进度调整与改善措施 (12)7.3.1 分析原因 (12)7.3.2 制定调整方案 (12)7.3.3 加强沟通与协调 (12)7.3.4 持续改进 (12)7.3.5 建立预警机制 (12)第8章库存管理 (12)8.1 库存的概念与分类 (13)8.1.1 库存的概念 (13)8.1.2 库存的分类 (13)8.2 库存控制策略 (13)8.2.1 定量控制策略 (13)8.2.2 定期控制策略 (13)8.2.3 综合控制策略 (13)8.3 库存优化与供应链管理 (13)8.3.1 库存优化 (13)8.3.2 供应链管理 (13)第9章生产成本控制 (14)9.1.1 直接材料成本 (14)9.1.2 直接人工成本 (14)9.1.3 制造费用 (14)9.2 生产成本控制的方法 (14)9.2.1 目标成本法 (14)9.2.2 标准成本法 (14)9.2.3 作业成本法 (15)9.3 生产成本分析与改进 (15)9.3.1 成本分析的方法 (15)9.3.2 成本改进措施 (15)第10章生产计划与控制信息系统 (15)10.1 信息系统的作用与架构 (15)10.1.1 概述 (15)10.1.2 信息系统在生产计划与控制中的作用 (15)10.1.3 生产计划与控制信息系统的架构设计 (15)10.1.4 信息系统的数据流与信息交互 (15)10.2 生产计划与控制信息系统的功能 (15)10.2.1 生产数据管理 (16)10.2.1.1 生产数据采集与处理 (16)10.2.1.2 生产数据存储与维护 (16)10.2.2 生产计划管理 (16)10.2.2.1 生产计划制定与优化 (16)10.2.2.2 生产计划的监控与调整 (16)10.2.3 生产控制管理 (16)10.2.3.1 生产进度监控 (16)10.2.3.2 生产调度与优化 (16)10.2.3.3 生产异常处理 (16)10.2.4 生产绩效分析 (16)10.2.4.1 生产指标统计与分析 (16)10.2.4.2 生产效益评估与改进 (16)10.3 生产计划与控制信息系统的实施与评估 (16)10.3.1 系统实施准备 (16)10.3.1.1 项目立项与需求分析 (16)10.3.1.2 系统设计与开发 (16)10.3.1.3 系统测试与验收 (16)10.3.2 系统实施策略 (16)10.3.2.1 分阶段实施方法 (16)10.3.2.2 逐步推进与持续改进 (16)10.3.3 系统评估与优化 (16)10.3.3.1 系统功能评估 (16)10.3.3.2 用户满意度调查与反馈 (16)10.3.3.3 系统功能优化与升级 (16)第1章生产计划概述1.1 生产计划的定义与重要性生产计划是企业生产管理的重要组成部分,是指根据市场需求、企业资源状况和生产经营目标,对产品生产进行科学合理的组织和安排。
运营管理第6版习题与参考答案_第10章
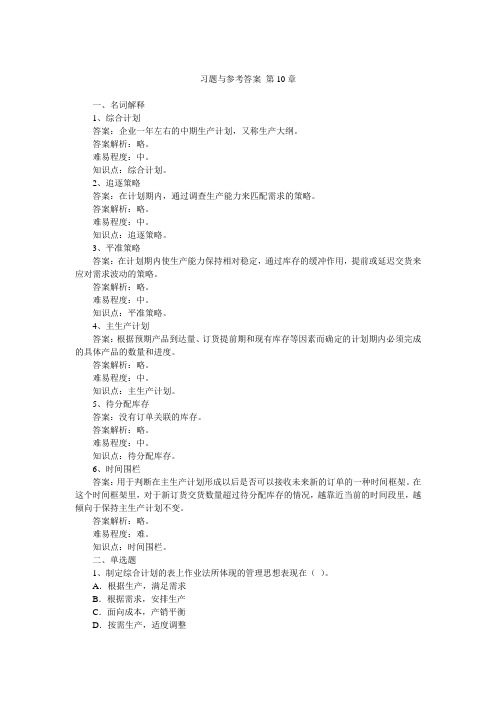
习题与参考答案_第10章一、名词解释1、综合计划答案:企业一年左右的中期生产计划,又称生产大纲。
答案解析:略。
难易程度:中。
知识点:综合计划。
2、追逐策略答案:在计划期内,通过调查生产能力来匹配需求的策略。
答案解析:略。
难易程度:中。
知识点:追逐策略。
3、平准策略答案:在计划期内使生产能力保持相对稳定,通过库存的缓冲作用,提前或延迟交货来应对需求波动的策略。
答案解析:略。
难易程度:中。
知识点:平准策略。
4、主生产计划答案:根据预期产品到达量、订货提前期和现有库存等因素而确定的计划期内必须完成的具体产品的数量和进度。
答案解析:略。
难易程度:中。
知识点:主生产计划。
5、待分配库存答案:没有订单关联的库存。
答案解析:略。
难易程度:中。
知识点:待分配库存。
6、时间围栏答案:用于判断在主生产计划形成以后是否可以接收未来新的订单的一种时间框架。
在这个时间框架里,对于新订货交货数量超过待分配库存的情况,越靠近当前的时间段里,越倾向于保持主生产计划不变。
答案解析:略。
难易程度:难。
知识点:时间围栏。
二、单选题1、制定综合计划的表上作业法所体现的管理思想表现在()。
A.根据生产,满足需求B.根据需求,安排生产C.面向成本,产销平衡D.按需生产,适度调整答案:C。
答案解析:略。
难易程度:中。
知识点:综合计划/生产大纲。
2、制定主生产计划的方法所体现的管理思想表现在()。
A.根据生产,满足需求B.根据需求,安排生产C.面向成本,产销平衡D.按需生产,适度调整答案:D。
答案解析:略。
难易程度:中。
知识点:主生产计划/MPS。
三、多选题无四、判断题无五、填空题1、MPS主要有4个方面的输入,即:()、()、()、()。
答案:最新的市场需求(包括已承诺的订单与预测结果)、预期库存信息、生产能力。
答案解析:略。
难易程度:中。
知识点:MPS的输入。
2、MPS主要有3个方面的输出,即:()、()、()。
答案:预期库存信息、包含量与期的主生产计划、待分配库存。
运营管理(MRP系统)
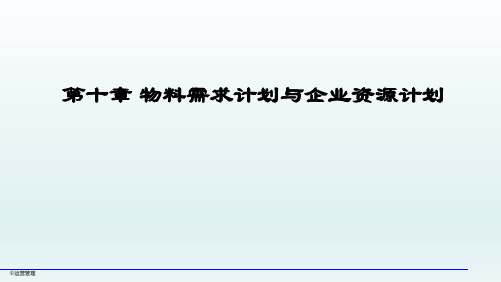
项目
周
12
3
4
次
5
6
7
8
总需要量
100
150
百叶窗 预计到货量
(LT=1) 现有库存数
按需订货 净需要量
100
150
计划发出订货量
100
150
运营管理
❖ 木制板条需求计划
项目
周
1
2
3
4
次
5
6
7
8
总需要量
100
150
百叶窗
(LT=1) 按需订货
预计到货量 现有库存数
净需要量
100
150
总需要量
1
2
框架 (LT=2) 按需订货
预计到货量 现有库存数
净需要量
运营管理
计划发出订货量 200
周
3
4
5
100
100
100
周
3
4
5
200
200 300
次
6
7
8
150
150
150
次
6
7
8
300
300
MRP的输出
百叶窗物料需求计划 MRP
自制件木制板条的生产计划
•开始生产时间:第2周、第6周 •需求数量:分别为330件、600件
第十章 物料需求计划与企业资源计划
运营管理
第二节 MRP系统
产品主生产计划
库存状 态文件
MRP
产品物 料清单
外购件需求计划
自制件投入出 产计划
运营管理
例:
生产木制百叶窗的某厂商收到两份百叶窗订单: (1)分别要求第四周交货100个,第八周交货150个。 (2)每个百叶窗包括4个木制板条部分和2个框架。 (3)木制部分由工厂自制,制作过程耗时1周。框架需
生产计划与控制教程与作业指导书

生产计划与控制教程与作业指导书第1章生产计划与控制概述 (4)1.1 生产计划的基本概念 (4)1.1.1 定义 (5)1.1.2 分类 (5)1.1.3 编制原则 (5)1.1.4 编制方法 (5)1.2 生产控制的目的与任务 (5)1.2.1 目的 (5)1.2.2 任务 (6)1.2.3 主要内容 (6)1.3 生产计划与控制的相互关系 (6)第2章生产计划编制方法 (6)2.1 生产计划编制的步骤 (6)2.1.1 确定生产计划的目标 (6)2.1.2 收集和分析数据 (7)2.1.3 制定生产计划方案 (7)2.1.4 评估和选择方案 (7)2.1.5 实施生产计划 (7)2.1.6 生产计划的调整与优化 (7)2.2 MRP系统的原理与应用 (7)2.2.1 MRP系统原理 (7)2.2.2 MRP系统的应用 (7)2.3 MPS的制定与维护 (7)2.3.1 MPS的制定 (8)2.3.2 MPS的维护 (8)第3章生产能力计划 (8)3.1 生产能力的基本概念 (8)3.1.1 生产能力的定义 (8)3.1.2 生产能力的分类 (8)3.1.3 影响生产能力的因素 (8)3.2 综合生产能力的确定 (8)3.2.1 设计生产能力的确定 (8)3.2.2 查定生产能力的确定 (8)3.2.3 计划生产能力的确定 (9)3.2.4 生产能力计算方法 (9)3.3 生产能力计划的调整与优化 (9)3.3.1 生产能力计划调整的必要性 (9)3.3.2 生产能力计划调整的方法 (9)3.3.3 生产能力优化目标 (9)3.3.4 生产能力优化策略 (9)3.3.5 生产能力优化实施 (9)第4章生产作业计划 (9)4.1 生产作业计划的概念与作用 (9)4.1.1 概念 (9)4.1.2 作用 (9)4.2 生产作业计划的编制方法 (10)4.2.1 编制原则 (10)4.2.2 编制步骤 (10)4.2.3 编制方法 (10)4.3 生产作业计划的实施与控制 (10)4.3.1 实施要点 (10)4.3.2 控制措施 (11)第5章库存控制与管理 (11)5.1 库存的基本概念与分类 (11)5.1.1 库存定义 (11)5.1.2 库存的分类 (11)5.2 库存控制策略 (11)5.2.1 订货点法 (11)5.2.2 经济订货量(EOQ)模型 (11)5.2.3 库存动态控制策略 (11)5.3 库存分析与优化 (11)5.3.1 库存分析方法 (11)5.3.2 库存优化方法 (12)第6章生产调度技术 (12)6.1 生产调度的基本概念与原则 (12)6.1.1 基本概念 (12)6.1.2 基本原则 (12)6.2 生产调度方法 (12)6.2.1 手工调度方法 (12)6.2.2 自动化调度方法 (13)6.2.3 智能化调度方法 (13)6.3 生产调度的实践应用 (13)6.3.1 生产调度系统设计 (13)6.3.2 生产调度系统实施 (13)6.3.3 生产调度案例分析 (13)第7章质量控制与管理 (13)7.1 质量的基本概念与质量管理 (13)7.1.1 质量的定义与特征 (13)7.1.2 质量管理的发展历程 (14)7.1.3 质量管理的基本原则 (14)7.1.4 质量管理的常用术语 (14)7.2 质量控制工具与方法 (14)7.2.1 质量控制工具 (14)7.2.2 质量控制方法 (14)7.3 质量管理体系与认证 (15)7.3.1 质量管理体系的概念与结构 (15)7.3.2 质量管理体系标准 (15)7.3.3 质量认证 (15)7.3.4 质量管理体系建立与实施 (15)第8章设备综合效率管理 (15)8.1 设备综合效率(OEE)的概念 (15)8.1.1 OEE的定义与组成 (16)8.1.2 OEE的计算方法 (16)8.1.3 OEE在生产企业中的应用 (16)8.2 设备故障分析与预防 (16)8.2.1 设备故障分析 (16)8.2.2 设备故障预防策略 (16)8.2.3 设备故障预防实施方法 (16)8.3 设备维护与保养 (16)8.3.1 设备维护与保养内容 (16)8.3.2 设备维护与保养计划 (16)8.3.3 设备维护与保养实施要点 (17)第9章生产计划与控制信息系统 (17)9.1 生产计划与控制信息系统的构成 (17)9.1.1 硬件设施 (17)9.1.2 软件系统 (17)9.1.3 网络通信 (17)9.1.4 数据资源 (17)9.2 生产计划与控制信息系统的功能 (17)9.2.1 生产计划管理 (18)9.2.2 生产过程控制 (18)9.2.3 数据分析与决策支持 (18)9.3 生产计划与控制信息系统的实施 (18)9.3.1 需求分析 (18)9.3.2 系统设计 (18)9.3.3 开发与实施 (18)9.3.4 运行与维护 (19)第10章生产计划与控制作业指导案例分析 (19)10.1 案例一:某制造业企业生产计划与控制实践 (19)10.1.1 背景介绍 (19)10.1.2 生产计划编制 (19)10.1.2.1 市场需求分析 (19)10.1.2.2 生产能力评估 (19)10.1.2.3 主生产计划制定 (19)10.1.2.4 物料需求计划编制 (19)10.1.3 生产控制流程 (19)10.1.3.1 生产进度监控 (19)10.1.3.2 生产异常处理 (19)10.1.3.3 产能调整与优化 (19)10.1.3.4 交货期管理 (19)10.1.4 作业指导 (19)10.1.4.1 生产计划制定步骤 (19)10.1.4.2 生产控制关键环节 (19)10.1.4.3 常见问题与解决方案 (19)10.2 案例二:某家电企业生产计划与控制优化 (19)10.2.1 背景介绍 (19)10.2.2 生产计划与控制现状分析 (19)10.2.2.1 生产计划存在的问题 (19)10.2.2.2 生产控制存在的问题 (19)10.2.3 优化方案 (19)10.2.3.1 生产计划优化 (20)10.2.3.1.1 引入高级预测技术 (20)10.2.3.1.2 优化排产策略 (20)10.2.3.2 生产控制优化 (20)10.2.3.2.1 建立实时监控体系 (20)10.2.3.2.2 引入生产执行系统 (20)10.2.4 作业指导 (20)10.2.4.1 优化方案实施步骤 (20)10.2.4.2 生产计划与控制优化策略 (20)10.2.4.3 注意事项与挑战 (20)10.3 案例三:某汽车制造企业生产计划与控制挑战与对策 (20)10.3.1 背景介绍 (20)10.3.2 生产计划与控制面临的挑战 (20)10.3.2.1 多品种、小批量生产模式 (20)10.3.2.2 供应链协同问题 (20)10.3.2.3 生产过程复杂性 (20)10.3.3 对策与措施 (20)10.3.3.1 精细化生产计划 (20)10.3.3.2 强化供应链协同 (20)10.3.3.3 引入智能制造技术 (20)10.3.4 作业指导 (20)10.3.4.1 针对性对策实施步骤 (20)10.3.4.2 生产计划与控制关键成功因素 (20)10.3.4.3 持续改进与优化方向 (20)第1章生产计划与控制概述1.1 生产计划的基本概念生产计划是企业生产管理的重要组成部分,旨在合理组织和调度企业生产资源,以实现生产目标的高效达成。
第10章转变企业经营机制

市场销售工作的转变
• 通过MRPII/ERP系统,生产 人员和市场人 员能够共同制订长期和短期的市场策略。 • 通过MRPII/ERP系统可以模拟主生产计划的 变化对人力、设备、物料需求以及交货时 间的影响;可以模拟产品配置的变化所产 生的影响等等。 • 从而,以可靠的生产信息为制订正确的市 场策略提供有力的支持 。
3.4 采购管理的转变
• 供应商信息管理 • 供应商计划 • 和供应商建立长期、稳定、双 方受益的合作关系
3.5 财务管理的转变
• 生产规划数据以及产品成本数据可以作为 经营规划的依据。实际的销售量、生产量 和库存量记录可以作为控制报告,可以用 来检测经营规划的实现情况。 • 将主生产计划按成本折算,可以作为单核算成本即可得出当 前在制品的价值。工时报告和派工单结合在一起, 可以作为工时效率考核的基础。 • 对采购计划进行成本转换可以反映出每个供应商 在何时、分别需要发来多少价值的物料才能满足 预定的计划。 • 将库存余额进行成本转换,很容易得到库存价值。
财务管理的转变
• 按全面质量管理的观点,必须把质量的概念从 产品质量扩展到工作质量。 • ISO9000系列所认证的正是从产品设计开发、 生产到完工检验、发货全过程的工作质量。所 以,ISO9000和MRPII/ERP系统相辅相成。 • 以MRPII/ERP作为通讯工具,使企业中所有的 人都在各自的岗位上井井有条地执行着统一的、 切实可行的计划,产品的质量必然能够得到提 高。
工程计划
• 过程计划的传统方法
– 计划评审法(PERT) – 关键路径法(CPM)
• 可以通过物料清单和工艺路线来做工 程计划并和物料计划结合起来
综上所述,RPII/ERP 系统是企业实现由粗 放经营向集约经营转 变的有效工具
企业资源规划 复习题及详细答案详解

D 模块化物料清单
2、ERP 系统涉及的仓库管理一般有三个方面,下列哪一项不在其中?(D)书 67-68
A 物料的出入库和移动管理
B 库存物料管理信息分析
C 库存盘点
D 物料成本结算
3、主生产计划是确定每个具体产品在每个具体的时间段的生产计划,计划对象一般是(A),有时也可能是
组件,然后再下达装配计划。
4、BOM中的“虚拟件”是指(B)
A 实际存在但可忽略的项目 B 为简化BOM管理而建立的“假”项目
C 提前期不为零的项目
C 需要安排生产计划的项目
5、闭环MRP与基本MRP的明显差异是(C)
A 考虑了物料的价值
B 考虑了人员的数量
C 考虑了能力的约束
D 考虑了材料的需求
6、累计提前期是指(C)(书本 43) A 设计提前期、加工提前期、装配提前期 C 采购提前期、加工提前期、装配提前期
三、判断题 1、MRPⅡ是 MRP 系统的升级版。(×) 2、MRP 系统的正确运行需要有一个切实可行的主生产计划。它除了要反映市场需求和合同订单外,还必须 满足企业的生产能力约束条件。(√) 3、粗能力计划(RCCP)的思想源于约束理论 TOC。(√)书本 55 4、JIT 的要点是找出瓶颈,消除制约因素。(×)书本 42 5、增加价值的同时增加成本的是无效作业。(×) 6、ERP 的主线是计划,它的管理重心在财务上,在企业整个经营运作过程中贯穿了财务成本控制的概念。(√) 7、工作中心是指企业的所有设备(×)书本 42,是生成加工单元的统称 8、MRPII 展开物料需求的计算时不考虑物料的时间特性。(×)
第一章
一、选择
1、哪一家国产 ERP 生产商提出了“ERP 八步实施法”?(D)
第10章 能力需求计划
2. 有限能力方式
优先级计划是按照优先级分配给工作中心负荷,当满负荷时优先 级别低的被推迟。这种方法由于按优先级别分配负荷,不会产生 超负荷,可以不做负荷调整。 有限顺排计划(finite forward scheduling)是在考虑能力的限制下 排负荷,它假定能力是固定不能调整的,因而计划可完全由计算 机自动编排。有限顺排计划通常适用于某种单一的工作中心或较 难调整的能力单元。有时,它也可以用在短期或近期车间作业进 度编排上,作为能力需求计划的补充。有限顺排计划对头道工序 往往是有效的,但对后续工序会增加复杂性,甚至可能影响交货 期。不少软件都设置了有限顺排计划的功能。
按时间周期计算每个工作中心的负荷订货政策零件主计划25252020202030303025lt1周订货政策毛需求25252020202030303025计划接收量38预计可用库存1427计划投入量38406022lt2周订货政策毛需求38406022计划接收量76预计可用库存54343计划投入量112lt1周订货政策固定批量80毛需求38406055计划接收量预计可用库存2222646424244444696969计划投入量808080lt2周订货政策毛需求50504040404060606050计划接收量72预计可用库存3355计划投入量7580120110产品a的mrp输出零件号可用能力排队时运输时间工序后订单数能力负荷生产时3072225265202683031025722302564026860388553582072275635806701209501108801572275121801281201841101701572276207211230381072211213171072280965工序和工序间隔时间工作中心文件工作中心工序间隔时间天排队时间运输时间30零件c计划订单倒序排产图零件c能力需求表零件号工作中wc20wc15能力需求计划表零件号工作中心265265220220220220310310310265工作中心负荷表工作中心10wc30265265220220220220310310310265wc2596513
10第10章企业物流发展态势与管理技术(含案例1个)
10.1快速反应(Quick Response,QR)
快速反应是美国纺织服装业发展起来的一种供应链 管理方法。目的是减少整个供应链上的时间和库存,最 大限度地提高供应链管理的运作效率。 ①快速反应的概念 美国纺织服装联合会对快速反应的定义为:“制造 者为了在精确的数量、质量和时间的条件下为顾客提供 产品,将订货提前期、人力、材料和库存的花费降到最 小;同时,为了满足竞争市场不断变化的要求而强调系 统的柔性”。我国国家标准《物流术语》中对快速反应 的定义为:物流企业面对多品种、小批量的买方市场, 不是储备了“产品”,而是准备了各种要素,在顾客提 出要求时,能以最快速度抽取要素,及时“组装”,提 供所需服务或产品。
案例:在嫁接中提升 —中储物流在线有限公司(1)
商品货物流通意义上的“物流”就一直存在,我们一直在运输、仓储、商品流通 组织在从事“物流”活动。现代物流不是要完全创新一个经济形态,而是要如何 在传统物流资源与现代的物流技术及观念之间进行嫁接,简而言之,就是传统物 流如何现代化。获是物流的信息化。对于中储物流在线公司,在这一方面结合的 比较好。
10.3 物料需求计划
在MRP问世之前,库存计划通常采用订货点法。 但是订货点法只能保证稳定均衡消耗情况下不出现短 缺,不能保证消耗多变情况下不出现短缺,也无法起 到降低库存的作用。为了解决这个矛盾,美国生产管 理和计算机应用专家首先提出了物料需求计划,IBM 公司首先在计算机上实现了MRP处理。 MRP的原理是,由主生产进度计划(Master Production Schedule,MPS)和主产品的层次结构逐 层逐个地求出产品所有零部件的出产时间、出产数量。 以每个物品为计划对象,以定工日期为时间基准倒排 计划,按提前期长短区别各个物品下达计划时间的先 后顺序。其目标是围绕物料转换组织制造资源,实现 按需要的准时生产。如果是自己加工,就形成了加工 任务单,如果是向外采购,就形成了采购任务单。
《ERP原理与应用教程》第3版习题和答案
17. 工作中心是 A. 由 MRP 需求系统定义
6
B. 由生产设施具体限制所决定。 C. 由能力管理所希望达到的控制程度所决定 D. 上面说的都不对 答案:C
18. 物料代码与工作中心的关系通过什么来定义? A. 工艺路线 B. 物料清单 C. 产品 D. 生产订单
答案:A
第 5 章 物料管理----企业运营的基础
1. 从库存投资方面来考虑,最好的生产计划环境是哪一种? A. 面向订单装配 B. JIT C. 面向库存生产 D. 面向订单生产
答案:B
2. 下面那些库存事务应当在计算机中进行处理? A. 当一些物料从一个库位移到另一个库位时 B. 当从某供应商那里接受货物时 C. 当一些物料从一道工序移到下一道工序时 D. 上面说的各种情况
A. A ×C –D = B B. B ×C –A = D C. B ×C –D = A D. A ×B –C = D 答案:D
第 2 章 管理需求推动 ERP 发展
1.以下哪些关于 ERP 发展历史阶段的陈述是正确的? A. ERP 的发展先后经历了订货点法、闭环 MRP、时段式 MRP、MRPII 和 ERP 等阶段 B. ERP 的发展先后经历了 ERP、时段式 MRP、闭环 MRP、MRPII 和订货点法等阶段 C. ERP 的发展先后经历了订货点法、时段式 MRP、闭环 MRP、MRPII 和 ERP 等阶段 D. ERP 的发展先后经历了订货点法、闭环 MRP、MRPII、时段式 MRP、和 ERP 等阶段
答案:D
2. 物料代码的作用是 A. 在工艺路线文件中识别工作中心 B. 物料的惟一标识符 C. 作为产品物料清单的一部分 D. A 和 B
答案:B
3. 在公司中哪个部门应当负责发行新的物料代码和物料清单? A. 生产部门 B. 市场部门 C. 生产控制部门 D. 工程设计部门
生产管理学在线测试题
5、生产过程的均衡性要求________ A、平行作业 B、在相等的时间里完成大体相等的工作量 C、连续作业
D、保持生产负荷均匀
第三题、判断题(每题 1 分,5 道题共 5 分) 1、服务业的兴起使得传统的生产概念得以扩展( ) 正确 错误
C、造纸厂 D、炼油厂
2、下列哪项不是 MRP 的输入( ) A、主生产计划 B、零部件出产计划 C、BOM D、库存状态文件
2、MTO 的需求管理主要包括________ A、获取订单 B、接受或拒绝订单 C、准备工程资源 D、调整工程资源
3、生产计划中表达产品产量时,常用________ A、代表产品 B、假定产品 C、具体产品 D、产品组合
4、下列关于生产能力与生产任务平衡的说法中,错误的是________ A、有多大生产能力就生产多少 B、按最大需求配置生产能力 C、按最低需求配置生产能力 D、寻求最佳生产能力
4、按工艺布置适用于不能移动的加工对象( ) 正确 错误
5、工作地按产品布置通常称为块型布置( ) 正确 错误 生产管理学 第 05 章在线测试
第一题、单项选择题(每题 1 分,5 道题共 5 分) 1、对于预测( ) A、时间长的准 B、时间短的准 C、时间短的不准 D、以上不确定
2、MTO 的订单获取是( ) A、随机的 B、确定的 C、重复的 D、以上不确定
5、以下关于数量价格折扣正确的说法是________ A、一般而言,数量越大价格越低 B、为获得较多的数量价格折扣,购买者乐意加大购买数量 C、用最低价格计算出来的 EOQ 不一定是可行解 D、以不同价格带计算出来的可行 EOQ,一定有一个最优解 第三题、判断题(每题 1 分,5 道题共 5 分) 1、EOQ 模型就是要使订货费用最省 ( ) 正确 错误 2、提高库存系统的服务水平就降低了缺货风险 ( ) 正确 错误
- 1、下载文档前请自行甄别文档内容的完整性,平台不提供额外的编辑、内容补充、找答案等附加服务。
- 2、"仅部分预览"的文档,不可在线预览部分如存在完整性等问题,可反馈申请退款(可完整预览的文档不适用该条件!)。
- 3、如文档侵犯您的权益,请联系客服反馈,我们会尽快为您处理(人工客服工作时间:9:00-18:30)。
§5-2 MPS 的对象
1. 最终产品 生产规划(综合生产计划)所规定的产品系统的具体化后的产品,称 为最终项目(end item)。
2. 独立需求的备品配件 3. 变形产品
也是最终产品,但是系列产品的种种变形组合,难以在最终项目表上 一 一列举。可用系列产品的比例方法确定。 4. 选装件、套件 在模块产品系列中,大量引用选配件、通用件。预测一下各基本件占 总需求量的比例。可从总装计划(Final Assembly Schedule,FAS)规 定。
粗能力计划(rough-cut capacity planning)是一种 计算量小,占用计算机机时较少,比较简单粗略,快速的能 力核定方法,通常只考虑关键工作中心及相关的工艺路线, 关键工作中心文件中定义后,系统会自动计算关键工作中心 的负荷。
1. 规划期(planning horizon)---3时区 从今天往前推算,一般在制造、装配、采购阶段之前。
这是根据合同(定单)、预测想结合定的。在 MRPⅡ是由计算机软件自动计算而确定()一年或 更长),在这一时段,计划可变化,一般,每季调 整一次。 2. 累计提前期---2时区:一般等于或略大于累计提前期。 从3时区进入二时区意味着生产计划开始实行,材料 已购买,资金投入并逐渐进入加工,直至装配,这 时区中如果合同增加,必须由计划员人工录入,系 统只能提供信息。
5. 预计可用库存量(Projected Available Balance,PAB):各时段的可用库存量。
6. 本阶段预计库存量=
7. 求量
本段初结余+本段产出+本段接受量-本段毛需
§5-4 MPS的计算方法
1. 预测需求和合同需求
合同(定单)和预测需求是两种信息。
例如:
项目编号:XB2000 1 2 3
4 56789
预测需求:
16
23 21
27
10
合同需求:
6 4 22
2 56
2. 毛需求量的确定
毛需求量是生产信息,在MRPII中是分时段给 出的。
将合同与预测结合起来,有如下方法:
(1)毛需求量=预测量------ 适合于备货生产 (2)毛需求量=合同量 ----- 适合于定货生产 (3)毛需求量=Max(预测量,合同量)
3. 主生产计划是MRPII的一部分
4 .主生产计划的任务
(1)排出独立需求的、按日、周、月的计划。 (2)对本企业的能力与生产任务进行细的平衡, 以便
确定能力的补充或计划的调整。 (3)根据产量及能力的动态变化,对每周计划做修改. (4)作为配套厂、销售网点、厂内制造部门、库存信息
等的联系枢纽,也是向客户承诺的依据。
第五章
主生产计划
§ 5-1主生产规划的任务和特点
1. 从台份计划到零件计划
传统生产计划(目前大多数国有企业)是台份计划,台份计划的缺点 是: (1)过早,不能适应市场的变化; (2)太粗,造成库存量的增加,资金积压。 MRPII 正是解决这个问题的。
2. 具体到产品的型号及需求的时间(月/周) 综合生产计划只是总的产量(无型号)
56 5 27
89 10
10
预期可用库存 3 7 3 0 -21/19 14 7
计划定单:
20 40
20
定单下达:
20 40
20
20
-3/13 13 20
说明:
1) 预期可用库存在第四周出现-21,故自动 增加定单。
2) 本应在第四周时增工厂生,考虑提前期 两周。
3) 生产批量为20,需求为-21,所以只能2批 40。
------适合于既有合同又有市场需求 (4)毛需求量=合同量:------在需求界内
毛需求量=预测量:------在需求界外
项目编号: (XB2000)
提前期为2周
时间(周)
1 23 4
预测:
16
23 21
合同:
6 4 22 2
MPS毛需求量: 16 4 23 21
计划接受量: 20
567 27
6. MPS 的可行性
传统计划的问题在于它不注意计划的可行性。MRPⅡ可行性与否关 键在于主生产计划。策略是:
(1)主观上要采用客观的数据,而不是把计划看成是“主观愿望”。 可执行才是可信的。
(2)在计划方法上,在编制计划时同时运行粗能力计划。 所以称为“主”( Mater)就是“主控”的意思。
(3)计划要按时间滚动。
主生产计划处理的最终物料(end item) ——独立需求的物料
例:床垫
综合生产 计划 :
月
1
2
产量 900 900
主
周 12345678
生
327 200
400
200 100
产 计
型 号 538
749
划
100 100 100
150
100
200
200
§5-3 MPS的时段概念
1. MPS的变与不变 可实行性的最大挑战是如何适应持续不断的变化。变的因素包 括: 内部:设备故障、质量事故、缺料待料等。 外部:市场需求变化、顾客取消定单。 导致:主生产计划的增加、减少、提前、推后(最终产品)。 时段性解决了这个问题。在MRPⅡ应用计算机轻而易举地调整 计划,可以作到每天调整一次。但调整也会带来损失。通常只 是一周、一月调整一次。
1. 毛需求量(gross demand)
2. 2. 净需求量(net demand)
3. 计划接受量(Scheduled receipt):
计划接受量是指从外部定购的预期到货 数量(正在执行的定单数量)。
4. 计划产出量(Scheduled output):
是指被确认为本厂生产量。有时被归并到 接受量中。
3. 需求时界(demand time fence)DTF: 1、2时区的分界线。提醒计划人员:已 进入机器总装,除特殊情况,一般计划 不能再做调整。
4. 总装期---1时区:进入整机总装阶段 (或略为提前)
5. 计划时界:2时区与3时区之间的分界线 (planning time fence)PTF。提醒:计 划已经确定,采购或生产周期较长的物 料已经备好,资金已投入,能力开始耗 用。变动必须由计划人员手工做。
1. 时段的划分
今天
每周
最后总装
零件制造
每月 采购
每季(可变化)
制造提前期
累计提前期
由计划员控制 (一般不变动)
生产计划 (合同、预测) 由计算机自动提出
1 时区 需求时界
计划时界
2时区 demand time fence
DTF
3时区 Planning time fence
PTF
时段的几个重要的概念