基于烧结矿冷却过程余热利用分析
烧结过程余热利用现状及趋势
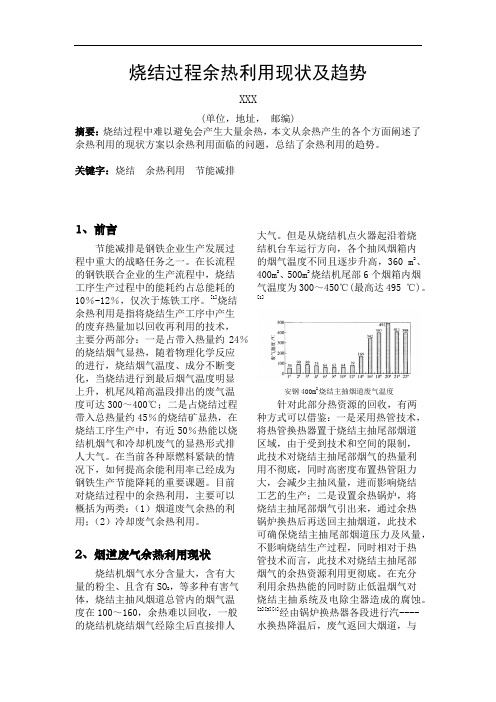
烧结过程余热利用现状及趋势XXX(单位,地址,邮编)摘要:烧结过程中难以避免会产生大量余热,本文从余热产生的各个方面阐述了余热利用的现状方案以余热利用面临的问题,总结了余热利用的趋势。
关键字:烧结余热利用节能减排1、前言节能减排是钢铁企业生产发展过程中重大的战略任务之一。
在长流程的钢铁联合企业的生产流程中,烧结工序生产过程中的能耗约占总能耗的10%-12%,仅次于炼铁工序。
[1]烧结余热利用是指将烧结生产工序中产生的废弃热量加以回收再利用的技术,主要分两部分:一是占带入热量约24%的烧结烟气显热,随着物理化学反应的进行,烧结烟气温度、成分不断变化,当烧结进行到最后烟气温度明显上升,机尾风箱高温段排出的废气温度可达300~400℃;二是占烧结过程带入总热量约45%的烧结矿显热,在烧结工序生产中,有近50%热能以烧结机烟气和冷却机废气的显热形式排人大气。
在当前各种原燃料紧缺的情况下,如何提高余能利用率已经成为钢铁生产节能降耗的重要课题。
目前对烧结过程中的余热利用,主要可以概括为两类:(1)烟道废气余热的利用;(2)冷却废气余热利用。
2、烟道废气余热利用现状烧结机烟气水分含量大,含有大量的粉尘、且含有SO2,等多种有害气体,烧结主抽风烟道总管内的烟气温度在100~160,余热难以回收,一般的烧结机烧结烟气经除尘后直接排人大气。
但是从烧结机点火器起沿着烧结机台车运行方向,各个抽风烟箱内的烟气温度不同且逐步升高,360 m2、400m2、500m2烧结机尾部6个烟箱内烟气温度为300~450℃(最高达495 ℃)。
[1]安钢400m2烧结主抽烟道废气温度针对此部分热资源的回收,有两种方式可以借鉴:一是采用热管技术,将热管换热器置于烧结主抽尾部烟道区域,由于受到技术和空间的限制,此技术对烧结主抽尾部烟气的热量利用不彻底,同时高密度布置热管阻力大,会减少主抽风量,进而影响烧结工艺的生产;二是设置余热锅炉,将烧结主抽尾部烟气引出来,通过余热锅炉换热后再送回主抽烟道,此技术可确保烧结主抽尾部烟道压力及风量,不影响烧结生产过程,同时相对于热管技术而言,此技术对烧结主抽尾部烟气的余热资源利用更彻底。
烧结环冷余温高效利用qc课题

烧结环冷余温高效利用qc课题烧结环冷余温是指烧结过程中所排放出的高温废气中蕴含的热量。
如何高效利用烧结环冷余温,减少能源浪费,是一个重要的课题。
在此,我将从几个方面阐述烧结环冷余温的高效利用。
首先,对于烧结过程中产生的高温废气,可以通过余热回收系统来回收和利用其中的热能。
余热回收系统通过热交换器,将废气中的热量转移到空气或水中。
转移后的热量可以用于加热或提供热水,在工业生产或生活中起到节能的作用。
烧结烟气的高温废气回收和利用是目前比较成熟的余热回收方法之一,可以大大降低能源消耗,并减少对环境的污染。
其次,余温高效利用的另一种方式是通过热能储存技术。
热能储存技术可以将烧结环冷过程中释放的大量热能转化为热能储存介质的热能,以便在需要时进行释放。
常见的热能储存介质包括熔融盐、熔融金属和石墨等。
当产生能量需求时,热能储存介质可以释放蓄积的热能,用于供暖、发电和其他能量应用。
通过热能储存技术,可以更加灵活地利用烧结过程中的余温,实现能量的高效利用,降低能源消耗。
此外,还可以采用废热发电技术,将烧结过程中的余温转化为电能。
废热发电技术一般采用蒸汽或有机物工质作为传热介质,通过蒸汽轮机或有机朗肯循环机组将余温转化为电能。
这种方法不仅可以高效利用冷余温,还可以降低烧结过程排放的废气对环境的影响,实现能源的可持续利用。
此外,还可以采用余温利用的新型技术,如热泵、热管和燃气废热锅炉等。
热泵利用外部环境的低温热源,将烧结冷余温提升至更高的温度,用于供热或发电。
热管通过利用液体的蒸发和冷凝过程,传导热量和实现热再利用。
燃气废热锅炉则利用烧结过程中产生的高温废气进行热能回收和利用。
这些新型技术在提高冷余温利用效率的同时,还可以降低能源消耗和环境污染。
在最后,值得注意的是,在进行烧结环冷余温高效利用时,需要充分考虑技术成本、环境影响和可行性等因素。
根据具体情况选择适合的余温利用方式,加强技术研发和应用推广,以实现在烧结过程中废气能量的充分利用,减少能源浪费,提高能源利用效率,促进可持续发展。
环冷机烧结矿余热回收性能分析与优化

环冷机烧结矿余热回收性能分析与优化摘要:根据统计表明,我国工业冶金烧结过程的能源消耗至少占整个冶金能耗的10%,而烧结矿在开发过程中排放的余热则占总能耗热的50%左右,由此可见烧结矿在冶金过程中对余热的回收一直都是国家企业重点关注的问题。
在烧结矿冶金过程中采用环冷机能够排放出大量的低温烟气,其产生的热量大约是烧结矿热耗量的30%左右,可以把烧结矿在冷却过程中产生的低温烟气进行余热回收,从而降低热量的大量消耗。
本文对环冷机在烧结矿的使用过程中余热回收的性能和优化进行重点分析讨论,试找出较为合理的解决方式。
关键字:环冷机;烧结矿;余热回收;性能引言:近年来我国烧结余热的利用技术不断发展,工业冶金在烧结余热技术的利用方面取得了较为良好的效果,但和国外成熟的的冶金余热利用技术相比,还有较大的差距。
目前我国烧结矿冶金过程中的平均能耗仍然比国外的指标高,所以通过优化环冷机的性能来提高烧结余热资源的高效利用和回收,增强我国冶金企业未来发展的必然趋势。
这对我国推行保护环境,降低能耗、节能减排也有重要的意义。
一、系统介绍环冷机主要由入端口、平台、台车体、处端口和其他部件组成。
其主要工作流程如下:首先环冷机上的台车在传动装置的驱使下,通过入端口进行接料,接着在平台上进行缓慢的圆形轨迹运动。
这时环冷机底部开始自下而上强制鼓风,底部冷却的介质穿过烧结矿物层发挥冷却作用,使得热量通过对流的方式进行不断的内部循环,导致烧结矿逐渐变得冷却[1]。
这一过程产生的热烟气需要从环冷机的台车顶部出口处排放,但热烟气通过台车顶部设计的一个或者多个集热罩,这些集热罩把热烟气送入余热回收装置进行利用。
环冷机通过以上方式促使内部介质的循环,周而复始地运动,便可以达到制冷的效果。
环冷机在工作的过程中具体余热回收利用系统流程过程如下图一所示:二、环冷机操作参照数对烧结矿冷却过程分析(一)环冷机料层厚度对出口烟气的影响分析利用计算机Matlab软件进行环冷机性能优化实验,控制环冷机的冷却介质风速、冷却介质温度,床层孔隙率和颗粒当量直径为恒定值时,改变料层的厚度,采用1m、1.2m、1.4m和1.6m的料层进行实验,出烟口的烟气温度会因为料层的厚度不同初始温度有所区别,随着冷却时间的变换而降低。
谈谈冷却机余热利用

谈谈冷却机余热利用摘要:唐山港陆钢铁有限公司利用200m2烧结环冷机、100m2烧结带冷机冷却烧结矿过程中的废气余热,通过双压余热锅炉产生过热蒸汽发电,并将余热锅炉尾气引回环冷机冷却矿料,提高了成品矿的品质和产量,在有效缓解区域电网供电压力的同时,降低了烧结工序能耗,为企业带来明显的经济效益。
关键词:冷却机;余热;利用1前言粗钢生产主要工序中烧结工序的能耗仅仅逊位于高炉炼铁工序的能耗,而在烧结工序总能耗中,大量的热能变换为烧结烟气和烧结矿的显热及化学热排入大气。
热平衡测试数据表明,烧结机热支出中烧结饼物理热占热收入总量的48.97%,其中冷却烧结矿的废气显热占热收入总量的28.38%、烧结机烟气显热和化学不完全燃烧热占热收入总量的23.06%。
如何有效回收利用冷却废气显热和烧结烟气余热,是烧结工序节能降耗的重中之重。
随着国家节能减排约束性指标的制定,工业企业中低温余热回收利用得到普遍的重视,回收利用技术及设备取得了长足的发展,尤其是钢铁企业中低温余热回收项目的性价比大幅提高,特别是双温双压余热锅炉应用于烧结机余热回收的实践,为烧结工序余热回收展示了良好的前景。
唐山港陆钢铁有限公司借鉴同行业烧结余热回收项目投运的经验,根据本企业的实际情况,将冷却机前部较高温度的废气余热加以回收,利用回收的余热发电供企业内部电网,部分减少了网购电量。
2余热回收利用系统唐山港陆钢铁有限公司现运行的3#、4#烧结机为100m2带式冷却烧结机,5#、6#烧结机为200m2环式冷却烧结机。
环(带)冷却机分为5段冷却烧结矿料,每段各配置1台鼓风机;经鼓风机鼓入的冷风与高温烧结矿料换热后,分别排放150~450℃的“中、低温废气”,废气中还含有一定数量的矿物粉尘。
利用2台烧结机环冷机1#、2#鼓风区段产生的275~450℃的废气各配置1台双温双压余热锅炉,利用2台烧结带冷机1#、2#鼓风区段产生的275~450℃的废气共用1台双温双压余热锅炉,3台锅炉产生的过热蒸汽,同时供1套15MW补汽凝汽式汽轮发电机组发电。
烧结矿竖式冷却工艺的分析与研究
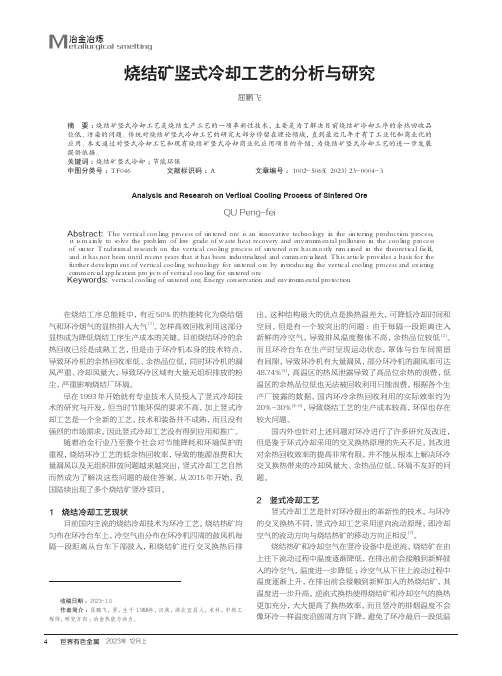
4冶金冶炼M etallurgical smelting烧结矿竖式冷却工艺的分析与研究屈鹏飞[普锐特冶金技术(中国)有限公司,上海 201103]摘 要:烧结矿竖式冷却工艺是烧结生产工艺的一项革新性技术,主要是为了解决目前烧结矿冷却工序的余热回收品位低、污染的问题。
传统对烧结矿竖式冷却工艺的研究大部分停留在理论领域,直到最近几年才有了工业化和商业化的应用。
本文通过对竖式冷却工艺和现有烧结矿竖式冷却商业化应用项目的介绍,为烧结矿竖式冷却工艺的进一步发展提供依据。
关键词:烧结矿竖式冷却;节能环保中图分类号:TF046 文献标识码:A 文章编号:1002-5065(2023)23-0004-3Analysis and Research on Vertical Cooling Process of Sintered OreQU Peng-fei[Primet Metallurgical Technology (China) Co., Ltd,Shanghai 201103,China]Abstract: The vertical cooling process of sintered ore is an innovative technology in the sintering production process, it is mainly to solve the problem of low grade of waste heat recovery and environmental pollution in the cooling process of sinter. Traditional research on the vertical cooling process of sintered ore has mostly remained in the theoretical field, and it has not been until recent years that it has been industrialized and commercialized. This article provides a basis for the further development of vertical cooling technology for sintered ore by introducing the vertical cooling process and existing commercial application projects of vertical cooling for sintered ore.Keywords: vertical cooling of sintered ore; Energy conservation and environmental protection收稿日期:2023-10作者简介:屈鹏飞,男,生于1988年,汉族,湖北宜昌人,本科,中级工程师,研究方向:冶金热能与动力。
梅钢烧结矿竖式冷却余热蒸汽利用方案探讨

冷却技术借鉴了干熄焦技术,采用密闭式气固逆 流换热工艺,余 热 回 收 效 率 高 达 8 0 % 以上[54],
引起业内的广泛关注。
梅钢3 号烧结机当前采用环冷方式回收烧结
矿余热回收效果不理想,平均蒸汽产量约l 〇t/h ,
许收相稿波日(期19:2830
17 -
-01 )
-2
,工
2
程
师
;
2
1
0
0
3
Abstract Utilization technologies with steam recovered from sinter vertical cooling that to be built in meishan iron and steel company were discussed. Energy efficiency of two alternatives was calculated and analyzed, from conversion process, transport process and the energy flow consisting of both the two processes. According to the results, compared with power generation, energy efficiency of steam drag ging is 5% higher in conversion process, but 12% lower in the energy flow, due to 64% efficiency in transport process. Power generation is suitable for steam recovered from sinter vertical cooling in meis han, due to its higher efficiency in energy flow. Keywords sinter vertical cooling waste heat recovery steam energy efficiency
烧结冷却机余热回收热力计算及应用

烧结冷却机余热回收热力计算及应用烧结冷却机是烧结过程中常用的设备,用于冷却和降温烧结矿石。
烧结冷却机的操作产生大量的余热,如果这些余热得不到回收利用,不仅会造成能源浪费,还会增加环境污染。
因此,对烧结冷却机余热的回收热力计算及应用显得尤为重要。
首先,我们来计算烧结冷却机的余热。
烧结冷却机的工作原理是通过气体或液体对烧结矿石进行冷却,使其从高温状态降至合适的温度。
在这个过程中,烧结气体以及冷却介质都会产生余热。
我们可以通过测量每小时烧结冷却机的燃料消耗量,来计算余热产量。
假设每小时燃料消耗量为Q,烧结冷却机的热效率为η,燃料的热值为H,那么烧结冷却机的余热产量为Q*(1-η)*H。
这个余热的温度通常较高,需要进行进一步的处理和利用。
对于烧结冷却机余热的应用,可以考虑以下几个方面:1.发电:利用余热发电是一种常见的回收方式。
烧结冷却机产生的高温余热可以用来加热工质,通过蒸汽或有机工质驱动发电机组发电。
这种方法可以实现能源的再利用,同时减少对外部电力的需求。
2.热水供应:将余热用于热水供应是另一种常见的应用方式。
可以借助余热设备,将高温余热通过换热器传热给水,提供洗浴、采暖等生活和工业用水。
这种方式可以减少对其他能源的依赖,实现节能环保。
3.废气处理:烧结冷却机在运行过程中会排放大量的烧结气体,这些气体中含有一定的有害物质。
通过余热回收,可以将烧结气体中的热量转运给应用用途,同时降低烧结气体的温度,减少有害物质的排放,保护环境。
4.节能改造:对烧结冷却机进行节能改造也是一种常见的应用方式。
可以利用余热对冷却机进行预热,减少外部能源的投入。
例如,通过在冷却介质进入冷却机前进行预热,可以提高热效率,减少能源消耗。
总结起来,对于烧结冷却机余热的回收热力计算及应用,需要考虑烧结冷却机的燃料消耗量、热效率以及燃料的热值等因素。
根据余热的特点和温度,可以选择合适的应用方式,如发电、热水供应、废气处理和节能改造。
利用余热的回收可以实现能源的再利用,减少环境污染,同时实现节能效益。
烧结机工序的余热回收利用
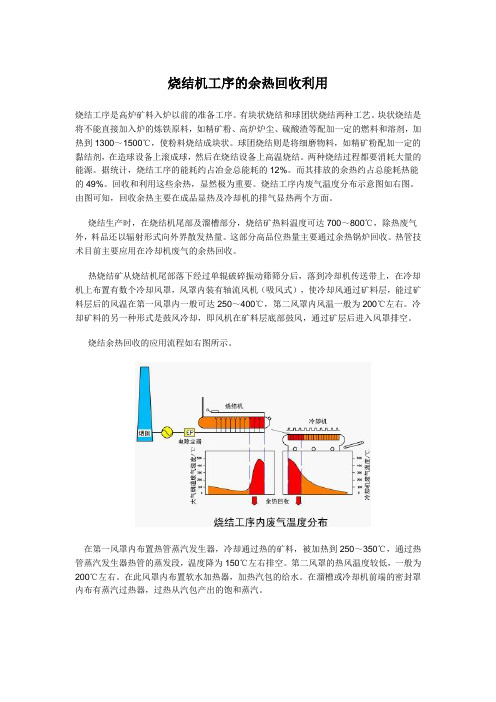
烧结机工序的余热回收利用烧结工序是高炉矿料入炉以前的准备工序。
有块状烧结和球团状烧结两种工艺。
块状烧结是将不能直接加入炉的炼铁原料,如精矿粉、高炉炉尘、硫酸渣等配加一定的燃料和溶剂,加热到1300~1500℃,使粉料烧结成块状。
球团烧结则是将细磨物料,如精矿粉配加一定的黏结剂,在造球设备上滚成球,然后在烧结设备上高温烧结。
两种烧结过程都要消耗大量的能源。
据统计,烧结工序的能耗约占冶金总能耗的12%。
而其排放的余热约占总能耗热能的49%。
回收和利用这些余热,显然极为重要。
烧结工序内废气温度分布示意图如右图。
由图可知,回收余热主要在成品显热及冷却机的排气显热两个方面。
烧结生产时,在烧结机尾部及溜槽部分,烧结矿热料温度可达700~800℃,除热废气外,料品还以辐射形式向外界散发热量。
这部分高品位热量主要通过余热锅炉回收。
热管技术目前主要应用在冷却机废气的余热回收。
热烧结矿从烧结机尾部落下经过单辊破碎振动筛筛分后,落到冷却机传送带上,在冷却机上布置有数个冷却风罩,风罩内装有轴流风机(吸风式),使冷却风通过矿料层,能过矿料层后的风温在第一风罩内一般可达250~400℃,第二风罩内风温一般为200℃左右。
冷却矿料的另一种形式是鼓风冷却,即风机在矿料层底部鼓风,通过矿层后进入风罩排空。
烧结余热回收的应用流程如右图所示。
在第一风罩内布置热管蒸汽发生器,冷却通过热的矿料,被加热到250~350℃,通过热管蒸汽发生器热管的蒸发段,温度降为150℃左右排空。
第二风罩的热风温度较低,一般为200℃左右。
在此风罩内布置软水加热器,加热汽包的给水。
在溜槽或冷却机前端的密封罩内布有蒸汽过热器,过热从汽包产出的饱和蒸汽。
- 1、下载文档前请自行甄别文档内容的完整性,平台不提供额外的编辑、内容补充、找答案等附加服务。
- 2、"仅部分预览"的文档,不可在线预览部分如存在完整性等问题,可反馈申请退款(可完整预览的文档不适用该条件!)。
- 3、如文档侵犯您的权益,请联系客服反馈,我们会尽快为您处理(人工客服工作时间:9:00-18:30)。
基于烧结矿冷却过程余热利用分析
本文采用局部非热平衡双能量方程模型[3,4],即分别对烧结矿和冷却空气建立能量方程。
以上两式中,hv为烧结矿与冷却空气之间的传热系数。
其余参数的选取通过测试及在测试基础上的计算得到,分别是:ρs=1600kg/m3,?=0·4,hv=0·199w/(m3·K),cs=920J/(kg·℃)。
根据烧结矿的冷却过程,研究对象的边界条件为:环冷机台车冷却空气入口边界、环冷机台车壁面、环冷机台车顶部出口。
对于环冷机台车冷却空气入口边界,由于单位时间进入环冷机台车的冷却空气的速度是固定的,所以采用速度入口边界条件,数值以测试值为准。
环冷机台车壁面采用定热流壁面。
对于环冷机台车顶部出口,采用压力出口边界条件。
现场测试方法:结合现场生产条件,利用热电偶测量环冷机余热利用区出口烟气温度,通过对测量位置选取不同的测点,并对不同的测点进行多次测量,取其平均值。
一、各因素对余热利用的影响
在前述建立的物理数学模型的基础上,利用流体动力学计算软件FLUENT 对烧结矿冷却过程进行数值模拟计算,在保持其他参数不变的条件下,考察单一因素对环冷机余热利用的影响。
以下分别对影响环冷机余热回收利用量的五个主要因素进行仿真计算:余热利用区内环冷机台车入口风速、烧结矿料层高度、烧结矿粒径、孔隙率、入口冷却空气温度。
1)环冷机台车入口风速对余热利用的影响:不同环冷机台车入口风速条件下,环冷机出口烟气平均温度随时间变化曲线如图2所示(略)。
由图2可知,随入口风速的增加,出口烟气平均温度逐渐降低。
说明入口风速越大,单位时间内气体带走的热量越多,有效余热利用量增加。
2)烧结矿料层高度:不同烧结矿料层高度下,环冷机出口烟气平均温度随时间的变化曲线如图3所示(略)。
由图3可知,环冷机出口烟气的平均温度随着烧结矿层高度的增加而升高。
由此可知,环冷机出口烟气的平均温度和有效余热利用量随着烧结矿层高度的增加而增大。
因此,在考虑鼓风机动力消耗允许的情况下,应增加料层高度,以提高余热回收率。
3)烧结矿粒径在烧结矿粒径:不同的条件下,环冷机出口烟气平均温度随时间的变化曲线如图4(略)。
由图4可知,烧结矿粒径的增大将会导致环冷机台车出口烟气的平均温度降低。
由此可知,环冷机出口烟气平均温度和有效余热利用量随着烧结矿粒径的增大而减小。
4)孔隙率不同孔隙率:的情况下,环冷机出口烟气平均温度随时间变化曲线如图5(略)。
由图5可知,在冷却过程初期阶段(200s之前),随着孔隙率的增加,出口烟气的平均温度增高;在200s之后,则趋势相反。
5)入口冷却空气温度:在入口冷却空气温度不同的条件下,环冷机出口烟
气平均温度随时间的变化曲线如图6。
由图6可知,入口冷却空气温度升高,使得出口烟气的平均温度升高。
说明随着入口冷却空气温度的增加,出口烟气平均温度和有效余热利用量也随之增加。
二、数值仿真结果的验证
在常规工况下,利用origin软件对数值模拟计算所得到的结果进行曲线拟合,图7为环冷机出口烟气平均温度随烧结矿冷却时间的变化曲线。
如图所示,拟合曲线与实测曲线能够理想重合。
由此说明,在工程实际中,可以采用拟合曲线的数学公式对不同冷却时间的出口烟气温度进行预测。
三、正交优化仿真实验
利用正交实验的方法,对影响环冷机上烧结矿余热利用的七个主要运行参数进行优化分析。
七个运行参数分别是:环冷机台车上下层物料高度、上中下层的烧结矿粒径、环冷机台车入口风速、冷却空气入口平均温度。
七个因素之间相互独立,本实验采用标准正交表L18(37)。
优化指标为烧结矿每小时的余热利用量;根据烧结矿进入环冷机的实际温度,将烧结矿的初始温度设定为1023·15K (750℃)。
表1列出了正交实验各工况仿真计算结果。
通过正交实验结果可得到,七个不同运行参数按其对烧结矿余热利用的影响,从强到弱的排序依次为:环冷机台车入口风速、环冷机台车上层烧结矿粒径、环冷机台车中层烧结矿粒径、环冷机台车下层烧结矿粒径、冷却空气入口平均温度、环冷机台车下层物料高度、环冷机台车上层物料高度。
本实验结果表明,实验中的七个不同参数的最优组合为:环冷机台车下层物料高度为0·4m,环冷机台车下层物料粒径大小0·035m;环冷机台车中层物料高度为0·5m,环冷机台车中层物料粒径大小0·025m;环冷机台车上层物料高度为0·5m,环冷机台车上层物料粒径大小0·03m;环冷机台车入口风速为7·65m/s;冷却空气入口平均温度为404K。
在此最优参数组合的工况下,模拟仿真计算得到烧结矿余熱利用量为176783265kJ/h,与正常工况条件下余热回收量相比,提高了25·6%,环冷机出口烟气平均温度为660·86K,比正常工况条件下环冷机出口烟气平均温度提高了49·85K。
结论
1)利用FLUENT软件作为计算平台,采用局部非热力学平衡的双能量方程模型,建立了烧结矿冷却仿真模型。
2)利用数学物理模型进行模拟仿真,在保持其它因素不变的情况下,研究单一因素对环冷机出口烟气温度和环冷机余热利用量的影响。
3)采用origin软件将利用FLUENT软件得到的数值仿真计算结果和在现场实测数据分别进行曲线拟合,得到了环冷机出口烟气平均温度随冷却时间变化的曲线。
经过对比,两条曲线重合理想,所以在工程实际中可以采用拟合曲线的数学公式对不同冷却时间的环冷机出口烟气温度进行预测。
4)利用正交试验方法,对影响烧结矿冷却过程的七个运行参数进行正交试验分析,找出了烧结矿余热利用率最大的参数组合,从而达到提高烧结矿余热利用率的目标。